Solomon C. Udensi 1, Lebe. A. Nnanna 2
1Department of Physics, Federal University of Technology Owerri, Owerri, Imo State, P.M.B. 1526, Nigeria
2Department of Physics/Electronics, Abia State Polytechnics Aba, Abia State, P. M. B. 7166, Nigeria
Correspondence to: Solomon C. Udensi , Department of Physics, Federal University of Technology Owerri, Owerri, Imo State, P.M.B. 1526, Nigeria.
Email: |  |
Copyright © 2012 Scientific & Academic Publishing. All Rights Reserved.
Abstract
Expanded graphite/Acrylonitrile/methyl methacrylate nanocomposites of different weight contents (0 to 5 wt. %) of Expanded Graphite (EG) were prepared via polymerization and examined for their yield and failure behaviours under uniaxial stress state. The failure mechanism shows transitions from sheared to crazed states as the volume contents of EG were increased. SEM photomicrographs also confirmed the brittle to ductile microstructural transitions of the nanocomposites. The toughness of the nanocomposite with 3 wt. % EG was optimum, and the process of crack growth which led to this high toughness could be seen. The decisive parameter which influenced the fracture data of EG/AN/MMA nanocomposites was found to be volume fraction of EG and interfacial adhesion of AN/MMA matrix and EG particles.
Keywords:
Expanded Graphite (EG), Nanocomposites, Sheared Stress, Crazed Stress, Deformation
Cite this paper:
Solomon C. Udensi , Lebe. A. Nnanna , "Sem Studies of Tensile Fractured Surfaces of Expanded Graphite/Acrylonitrile/Methyl Methacrylate Nanocomposites Prepared via in-Situ Polymerization", American Journal of Materials Science, Vol. 1 No. 2, 2011, pp. 123-127. doi: 10.5923/j.materials.20110102.20.
1. Introduction
Polymeric nanocomposites are multi-phased solids, where one of the phases has one, two, or three dimensions less than 100 nm[1]. That is to say that the solid (nanocomposite) is derived from a bulk matrix of polymer and nano-dimensional materials/phases, which exhibit dissimilar properties, as a result of there dissimilar chemical compositions. These dissimilarities explain to a large extent, the differences observed in mechanical, electrical, optical, thermal, etc properties of nanocomposites when compared to those of the component materials. One of such nano-dimensional materials used as filler is graphite nanoplatelets. Graphite nanoplatelets have grown in prominence[2,3] because of there ability to easily expand and/or exfoliate with the application of heat within its heat resistant range of -200 to 3000℃ [4]. There are very few literatures, to my knowledge, which have reported any result(s) on the effect of included stress sites on the mechanical properties of in situ prepared polymeric nanocomposites.This study is propitious, if the longevity of our light weight nanocomposites is to be guaranteed and applied in fields such as aviation, windmill, audio industries etc. where mechanical strength, toughness, etc of materials are pre- requisite for performance. One useful characterization tool which has been of help to scientists in studying the effect of minuscule cracks, voids and other tiny defects is the scanning electron microscope (SEM). The aim therefore, is to report the results as observed using SEM to study the two main deformation mechanisms- shear yielding and crazing[5] in (EG/AN/MMA) nanocomposites prepared via in-situ polymerization.
2. Experimental
2.1. Materials
Graphite power (SP-1 grade) from Bay carbon Incorporated containing 1 ppm of Silicon. Sulphuric acid and concentrated nitric acid from Sigma Aldrich were used as intercalants in the graphite powder, in order to aid exfoliation. Other materials from Sigma Aldrich include: anhydrous ethanol (99.9% vol.), methyl methacrylate (MMA) monomer (lot no. 180882) and acrylonitrile (≥ 99.0%) monomer (lot no. 110213). Monomers MMA (density 0.936g/mL) and AN (density 0.8g/mL) were mixed in the ratio of 1:1. 1 wt % of expanded graphite (EG) was added to the mixture, which was maintained at 65℃ and stirred for about 3 mins, in order to achieve good dispersion of EG. 2.5 wt % Benzoyl Peroxide (BPO), an initiator was then added to the mixture and the beaker covered with parafilm material. The stirring was continued for another 3mins, during which the liquid mixture started coagulating. The thermosetting mixture was then cast into an iron mould with cavities measuring 50mm x 5mm x 2.02mm, kept overnight in an oven, at a temperature of 50℃. Polymerization was allowed to run to completion for another 18 hrs in this oven, at this temperature (50℃).The “dog-bone” shaped samples obtained from these moulds were then prepared for scanning electron microscope (SEM) and tensile testing, in order to investigate the microstructure of our new composite (EG/AN/MMA) with that of 0 wt% EG/AN/ MMA nanocomposite.Also 2 wt%, 3 wt%, 4 wt%, and 5 wt% EG were added to the 1:1 MMA, AN and BPO mixture. The same procedure was followed to obtain samples for testing and comparison. The tensile tests were performed at room temperature to conform with ISO 527-1 standard for measuring rigid plastics using Zwick Z100 static testing machine with in-built ( testXpert® II ) software and a digital clip-on extensometer. After these tests, fracture analyses of the faces of the fragmented specimens were done using Zeiss scanning electron microscope (ultra high resolution). The surfaces of the sample were gold plated to aid the SEM analysis. The failure mechanisms of the samples were studied by direct observation of the structures of the tensile fractured surfaces.The gauge lengths, widths and thicknesses of the samples were measured using callipers and recorded (i.e. 50mm x 5mm x 2.02mm). In order to make the samples insensitive to transverse forces, a 5KN load cell whose operation is based on the principle of axial/rotational symmetry, and most suitable for measuring plastics, was attached to the Zwick Z100 static testing machine for this work. Five different tests, for each sample/composite was carried out for this study.
3. Results and Discussion
It is a well-known fact that the mechanical properties of nanocomposites are dependent on the type of filler used, in our case expanded graphite. The factors that must be emphasized upon are the filler- to - EG-AN/MMA) interfacial adhesion and orientation[6]. Also the surface area/volume ratio of the filler is another vital property of reinforcements (fillers)[7-11].Low strength usually results from weak interfacial regions, consequently leading to reduced efficiency in stress transfer and ultimately a premature failure of the material under test. Therefore, addition of fillers to any given polymer matrix usually does not necessarily result in increased tensile properties of the composite. Factors that determine the quality of interfacial bond include; filler/fibre aspect ratio, nature of filler and polymer matrix, and processing technique applied during treatment of fibre and/or polymer[12]. Figures' 1 and 2 show the tensile properties of the composite- that is the tensile strength and the ultimate elongations. Addition of 1 wt. % to 4 wt. % EG improved the tensile properties of the matrix. The composite with 3 wt % showed the highest strength and ultimate elongation. Composites with 2 wt % and 4 wt. % EG in them showed approximately same strength but different ultimate elongation, because in 2 wt % the matrix is not well saturated and so possesses points which constituted dislocation sites. In the composite with 4 wt % EG, the property that accounted for more elongation was the proper alignment of the EG in the matrix. However, increment to 5 wt % led to least adhesion between EG and AN/MMA matrix, thereby lowering the original tensile properties of the matrix with any EG. This is also attributed to horizontal orientation of EG in the matrix, compared to the line of tension.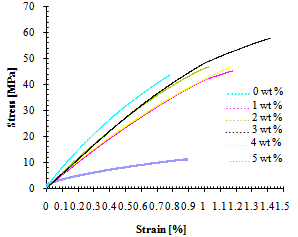 | Figure 1a. Stress versus strain curve for various weight percent EG in AN/MMA matrix |
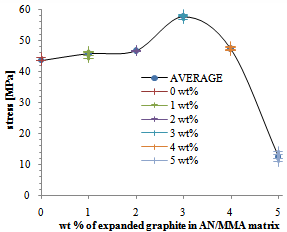 | Figure 1b. Stress versus weight percent EG in AN/MMA matrix |
Fig. 2 shows the strain against wt % of EG in the AN/MMA matrix for five different tests. The least deviation in 3 wt % EG shows that within the limit of experimental errors that the tensile properties were greatly improved because of good adhesion and alignment AN/MMA, but worst in 5 wt % EG.The SEM photomicrographs are shown in figures 3a to 3f. These give reliable insights of how well the expanded graphites are dispersed in the AN/MMA matrix, or whether the fiber and matrix are in isostrain or isostress condition. Another usefulness of SEM photomicrographs is the unveiling of the exfoliation rate of the fillers (expanded graphite)[13]. As can be seen for the images, the shear forces from the stirrer are needed to break-down the EG agglomerates into smaller tactoids for faster and proper polymer intercalation within the matrix[14]. The glassy nature of AN/MMA matrix accounts for the brittle failure observed in figure 3a and shown in the tensile graphs above. This may have arisen due to poor conducting property of the matrix, so much so that the cooling was non-uniform. The outer walls of the composite in the mould cooled faster because of its contact with the surrounding air, but nevertheless acted as an insulating material for the still molten interior, which then cooled in small pockets with different orientations. 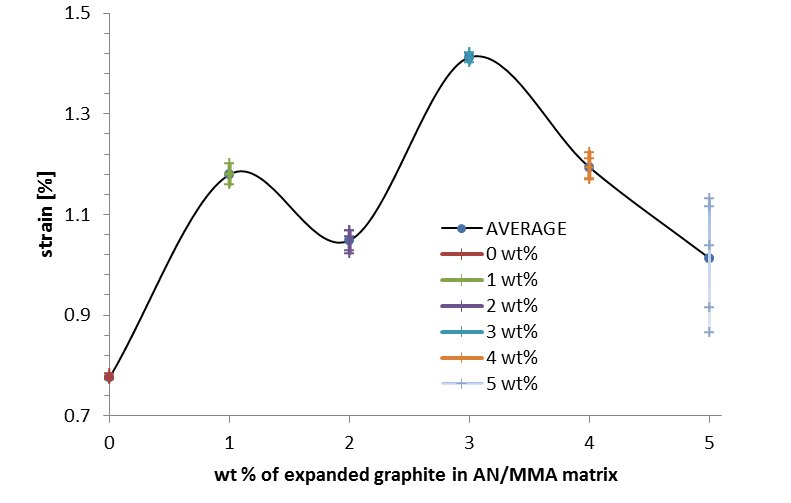 | Figure 2. Strain versus weight percent EG in AN/MMA matrix |
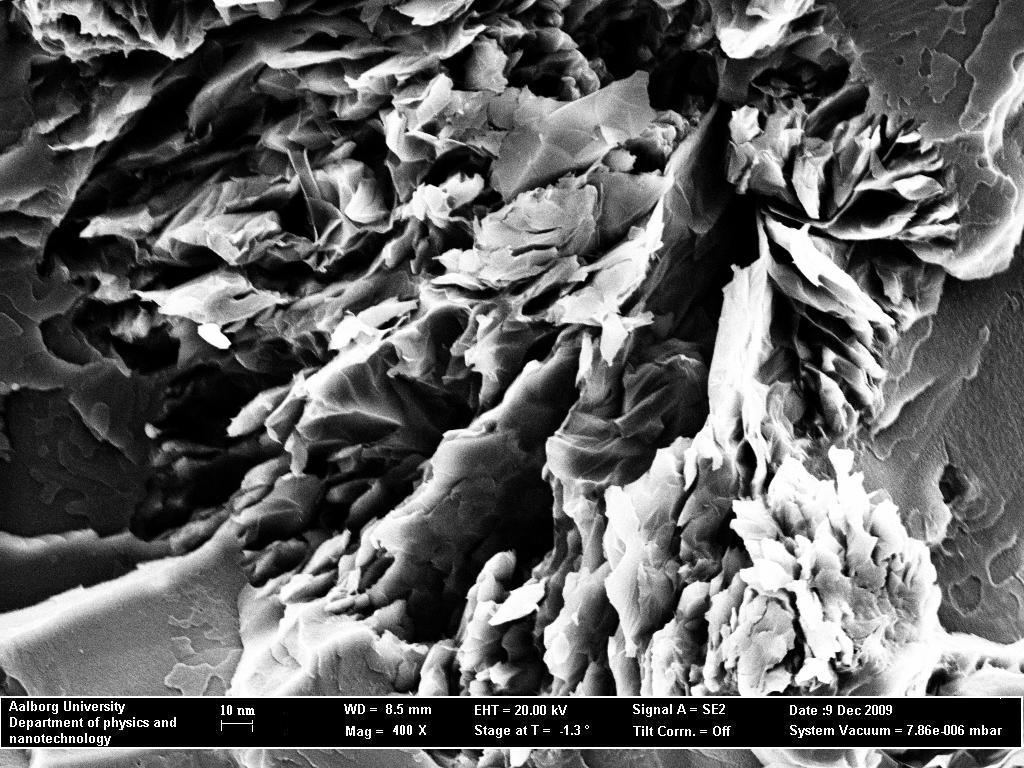 | Figure 3a. 0 wt. % |
The ductility nature of this matrix was improved by the addition of 1wt. % to 5wt. % EG. Another important property introduced to the matrix on addition of different weight percent EG is the competition between sheared and crazed regions. Sheared regions arose because of the processing technique used, whereas crazed regions are highly stressed regions[15] originating from the inclusion of tiny flaws, like voids, which grow into cracks and eventually fail[16,17] when tension is applied. Crazes are normal yield stresses that enhance the fracture toughness of AN/MMA/EG by absorbing the energy through the process of crack growth.The maximum craze condition occurred in 3wt. % EG and AN/MMA composite. This accounts for the high yield stress as shown by the tensile graphs. The SEM shows the highly stressed regions (crazed regions) where the inclusion of tiny flaws, such as voids grew into cracks and ultimately failed on application of tension. Crazes increase the fracture toughness during tension by absorbing the fracture energy through craze growth. The alignment of the 4wt. % and 5wt. % EG in AN/MMA matrix accounted for their lower tensile properties than that of 3wt. % EG in AN/MMA. The volume contents of EG in both cases were higher than in other situations that most EG did not have time and space to align themselves in the line of tension. The two photomicrographs show horizontal cleavage of EG in AN/MMA matrix, due to the formation of clusters of EG.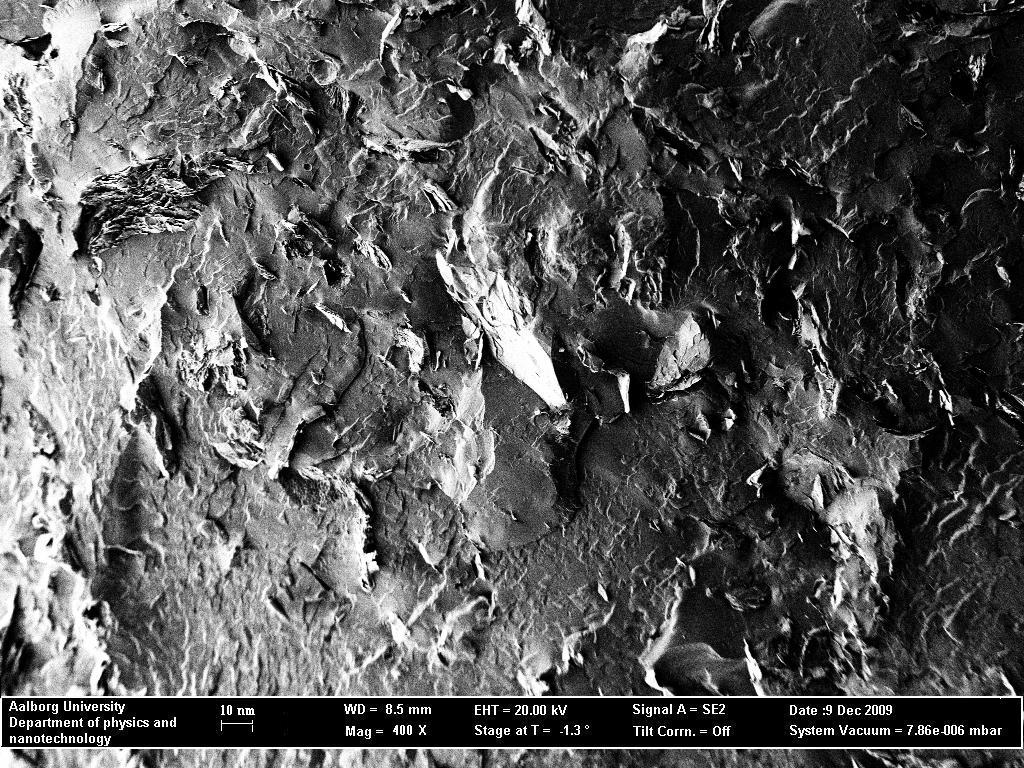 | Figure 3b. 1wt. % |
At these sites, AN/MMA found it difficult to make their way into the expanded and exfoliated parts of the graphite. This difficulty is thought to be due to the cohesion forces holding the polymer molecules together and the capillary action through the opening in the exfoliated graphite.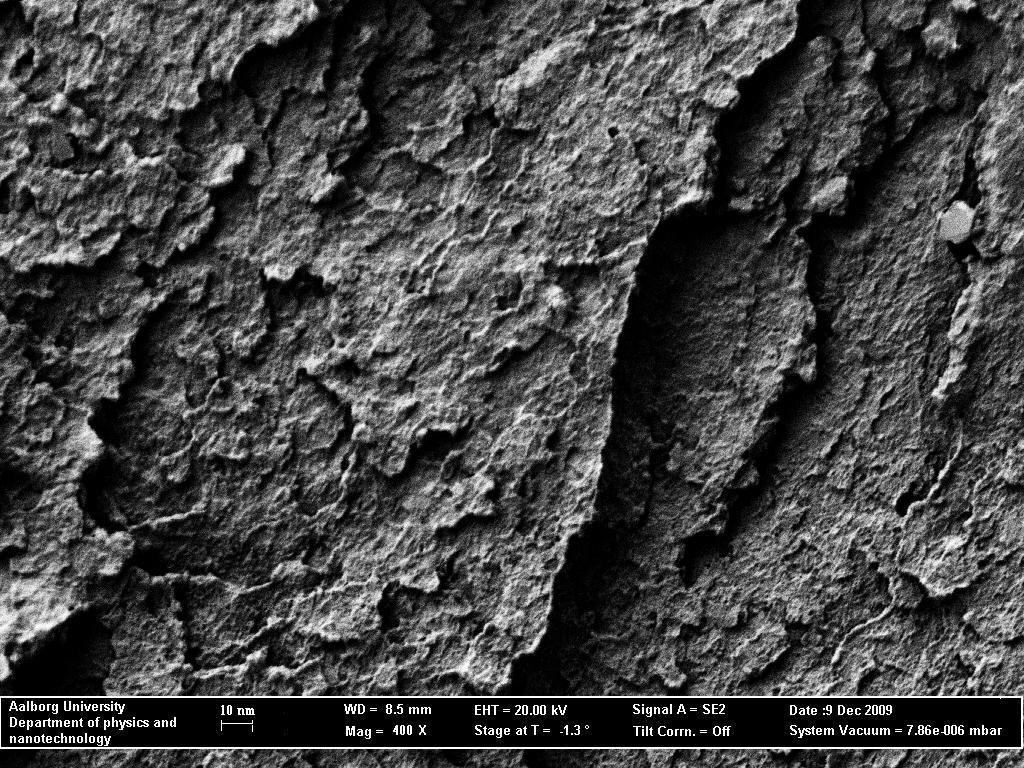 | Figure 3c. 2 wt.% |
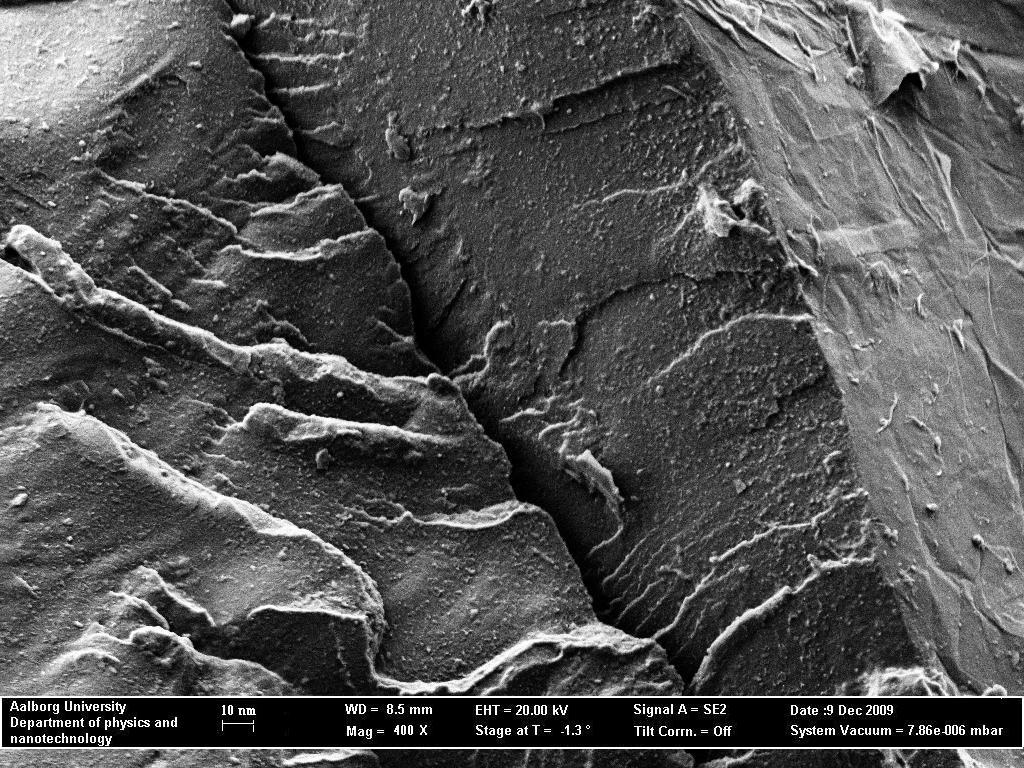 | Figure 3d. 3wt.% |
 | Figure 3e. 4wt.% |
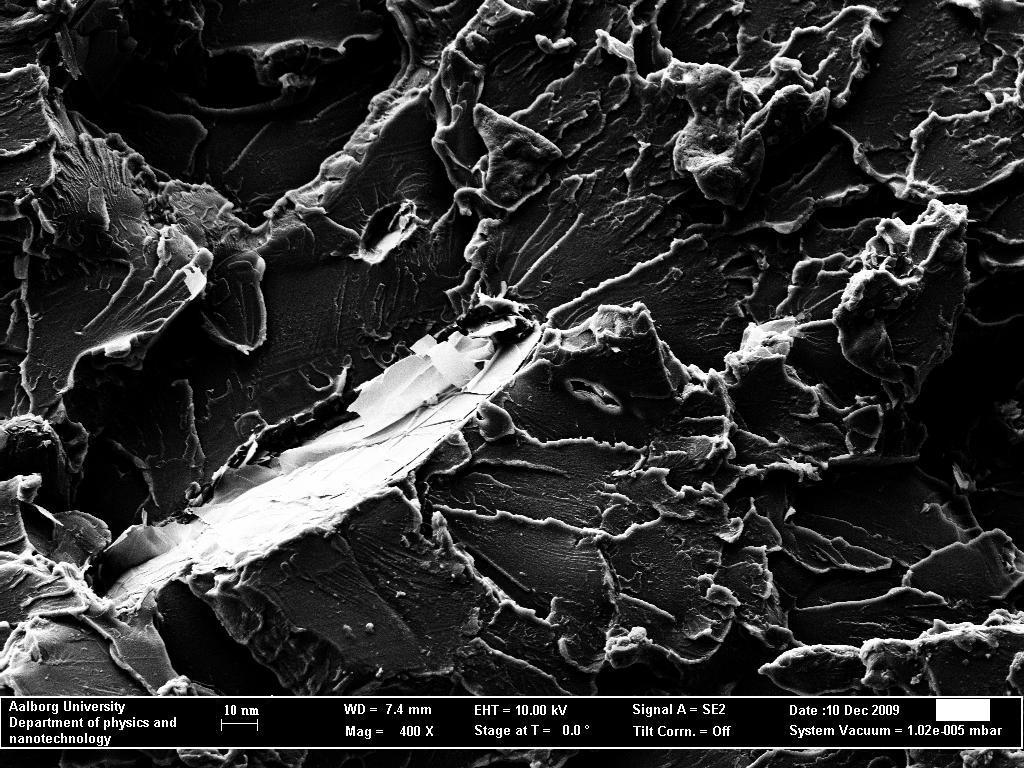 | Figure 3f. 5wt. % |
4. Conclusions
In this paper, the study of fractured tensile surface of in situ prepared EG/AN/MMA composite is reported. We found out that• The SEM image of the fractured surface of 3 wt% EG/AN/MMA nano-composites showed that the high ultimate tensile strength, toughness and the high fracture strength were as a result of good filler-to-matrix (i.e. EG-to-AN/MMA) adhesion, dispersion, and strength of graphite nanoplatelets. This imparted into the composite a good matrix to filler load transfer. This image also showed increased shear regions thought to improve the ductility of the matrix (AN/MMA). It also supported the views that both shear stress and hydrostatic stress exist in polymers, and could transit from one stress state to another.• There was a transition from the glassy matrix to a somewhat ductile nanocomposite, with maximum ductility occurring on addition of 3 wt % EG.• Overloading of our matrix with more than 3 wt % EG resulted on misalignment and different orientation of EG in the matrix (see figs 3e and 3f). This reduced the matrix- to- filler load transfer of the specimens’ 4- and 5 wt %.
ACKNOWLEGDEMENTS
The authors are grateful to the department of Physics and nanotechnology, Aalborg University Denmark, for the characterization of our sample and to Prof Donghung Yu of the Chemistry department of the same University for some insightful sessions we had together.
References
[1] | P. M. Ajayan, L. S. Schadler, and P.V. Braun; Nanocomposite Science and technology, copyright (2003) Wiley-VCH Verlag GmbH Co KGaA Weinheim. ISBN: 3-527-30359-6 |
[2] | A. Yasmin, I. M. Daniel; Mechanical and thermal properties of graphite platelets/epoxy composites, Polymer 45(24), 8211- 8219 (2004) |
[3] | A. Yasmin, Jyi-Jiin Luo, I. M. Daniel; Processing of expanded graphite reinforced polymer nanocomposites, Composites Science and Technology 66(9), 1182- 1189 (2006) |
[4] | M. Inagaki, R. Tashiro, Yu-iti Washino and M. Toyoda; Exfoliation process of graphite via intercalation compounds with sulphuric acid, Journal of Physics and Chemistry of Solids, vol.65 (2-3), 133-137, 2004 |
[5] | S. S. Sternstein and L. Ongchin; Yield criteria for plastic deformation of glassy high polymers in general stress fields. ACS Polym. Prep. 10(1969), 1117-1124 |
[6] | C. L. Wei, M. Q. Zhang, M. Z. Rang, K. Friedrich; Tensile performance improvement of low nanoparticles filled- polypropylene composites, Compos Sci. technol 62, 1327- 1340, (2002) |
[7] | Kin-tak Lau, Man-Wai Ho, Chun-Ki Lam, D. H. L. Ng, and D. Hui; Mechanical properties of epoxy-based composites using nanoclays, Composites 75(1-4), 415-421 (2006) |
[8] | M. Xanthos, Neung Hyun Kim, and S. V. Malhotra; Modification of cationic nanoclays with ionic liquids, micrporous and Mesoporous Materials, 96, 29-35 (2006) |
[9] | Quyuan Zhou, and M. Xanthos; Nanosized clay effects on the kinetics of thermal degradation of polylactides, Polymer Degradation and Stability 94, 327-338 (2009) |
[10] | R. S. Rajeev, E. Harkin-Jones, K. Soon, T. McNally, C. G. Armstrong, and P. J. Martin; Studies on the effect of equi-biaxial stretching on the exfoliation of nanoclays in polyethylene terephthalate, European Polymer Journal, 45, 332-340 (2009) |
[11] | S. Tzavalas, and V. G. Gregoriou; Infrared spectroscopy as a tool to monitor the extent of intercalation and exfoliation in polymer clay nanocomposites, Vibrational Spectroscopy, 51, 39-43 (2009) |
[12] | L. Vaisman, H. D. Wagner and G. Marom;The role of surfactants in dispersion of carbon nanotubes, Adv Colloid Interface Sci 128-130; 37-46 (2006) |
[13] | P. Magagnini, S. Filippi, Elena Mameli, and C. Marazzato; comparison of solution- blending and melt-intercalation for poly (ethylene-co-acrylic acid)-organoclay nanocoomposites, European Polymer Journal, vol.43, 1645-1659, 2007 |
[14] | R. A. Vaia, and E.P. Giannelis; lattice model of polymer melt intercalation in organically- modified layered silicates, Macromolecules 30, 7990-7999, (1997) |
[15] | H. A. Hristov, A. F. Yee, and D. W. Gidley; Fatigue craze initiation in polycarbonate: study by transmission electron microscopy. Polymer 35(17), 3604-3611 (1994) |
[16] | Wenbo Luo, and Wenxian Liu; Incubation time to crazing in stressed poly (methyl methacrylate). Polymer Testing 26(3), 413- 418 (2007) |
[17] | R. P. Singh, M. Zhang, D. Chang;Toughening of a brittle thermosetting polymer: Effects of reinforcement particle size and volume fraction, Journal of Materials science, 37, 781- 788, (2002) |