Hsing-I Hsiang 1, Wei-Sheng Chen 1, 2, Yu-Lun Chang 1, Fu-Chi Hsu 1, Fu-Su Yen 1
1Particulate Materials Research Center, Department of Resources Engineering, National Cheng Kung University, 70101, Tainan, Taiwan, R.O.C
2Sustainable Environment Research Center, National Cheng Kung University, 70101, Tainan, Taiwan, R.O.C
Correspondence to: Hsing-I Hsiang , Particulate Materials Research Center, Department of Resources Engineering, National Cheng Kung University, 70101, Tainan, Taiwan, R.O.C.
Email: |  |
Copyright © 2012 Scientific & Academic Publishing. All Rights Reserved.
Abstract
This study investigates the ferrite load effects on the thermo-mechanical and electromagnetic properties of NiZn ferrite powder- epoxy resin coatings. It was observed that the Young's modulus and glass transition temperature of the composites decreased as the ferrite load increased from 30 to 50wt% and increased as the ferrite load was further increased above 70wt%. The dielectric constants and initial permeability both increased with increasing ferrite load. The thermal decomposition offset temperature for composites with ferrite loading was shifted toward higher temperatures compared to the neat epoxy.
Keywords:
NiZn Ferrite,Composites, Dielectric Property, Magnetic Property, Dynamic Mechanical Property
Cite this paper:
Hsing-I Hsiang , Wei-Sheng Chen , Yu-Lun Chang , Fu-Chi Hsu , Fu-Su Yen , "Ferrite Load Effects on the Mechanical and Electromagnetic Properties of NiZn Ferrite Powders-epoxy Resin Coatings", American Journal of Materials Science, Vol. 1 No. 1, 2011, pp. 40-44. doi: 10.5923/j.materials.20110101.06.
1. Introduction
Ferrite powder-polymer composites have been used extensively in the suppression of electro-magnetic noise and embedded inductor components due to their superior electro-magnetic properties 1-3. Epoxy resins are widely used in many applications due to their superior adhesion, high strength, and resistance to creep, heat and chemicals. NiZn ferrites have also been used widely because of their high permeability in the RF region, high electrical resistivity and environmental stability4. Therefore, some investigations on the NiZn ferrite-epoxy composites have been reported5-8. These studies focused mainly on the permeability or permittivity of NiZn ferrite-epoxy composites, however, very few studies have investigated the dynamic mechanical properties.During ferrite powder-polymer resin slurry preparation the ferrite particles tend to hold together. The particles form agglomerates because of the strong magnetic interactions between the ferrite particles. Moreover, the NiZn ferrite particles are hydrophilic and cannot be dispersed homogeneously in organic resins. The agglomerates and inhomogeneous ferrite powders mixed in organic resins generally lead to the formation of micro-structural defects in the ferrite powder-polymer coatings. These defects affect the quality of magnetic devices. Ferrite powder surface modification using a coupling agent in epoxy resin formulations can offer superior performance, such as improved dispersibility, increased compatibility between the ferrites and epoxy resin and adhesion strength between the ferrite particles and polymer matrix because the coupling agent grafts onto the ferrite powder surface6. In general, these composites are prepared by mixing 20–50vol% ferrite powders with epoxy resin. Epoxy resins are widely used in many applications due to their superior adhesion, high strength, and resistance to creep, heat and chemicals. However, these materials are rather brittle and exhibit poor toughness. The ferrite powder-epoxy composite are often modified with a carboxyl terminated butadiene-acrylonitrile liquid rubber (CTBN) to improve the toughness.This study investigates the ferrite load effects on the thermo-mechanical and electromagnetic properties of NiZn ferrite powder- epoxy thick film prepared using titanate coupling agent surface modified NiZn ferrite powder and CTBN modified epoxy resin as the raw materials.
2. Experimental
2.1. Materials
The Ni0.5Zn0.5Fe2O4 ferrite powders were prepared from reagent-grade NiO, ZnO and Fe2O3, which were mixed and then calcined at 1100℃ for 6 h. The calcined powder was used as the raw material and milled for 6 h using Y-TZP balls using ethanol as the medium. The specific surface area (BET) value of the ball-milled Ni0.5Zn0.5Fe2O4 ferrite powder was about 1.24m2/g. The Titanate coupling agent, tri(dioctyl) pyro-phosphato titanate-Lica 38 (Kenrich Petrochemicals Inc., USA) was used without further purification. The epoxy resin used was brominated epichloro hydrin-bisphenol A (NPEB450A80, Nan Ya Plastics Co., Taiwan), with a weight per epoxy equivalent of 425-455g. Dicyanodiamide (DICY) and 2-methyl imidazole (2-MI), purchased from Acros Chemical (Geel, Belgium), were used as the hardener and accelerator, respectively. The carboxyl-terminated butadiene-acrylonitrile liquid rubber (CTBN) (Hypro 1300x13, Emerald Performance Materials LLC, USA) was used to improve the toughness of the epoxy resin. Aceton, toluene and dimethyl fumarate (DMF) were used as solvents without further purification. Aceton and toluene were used as the solvent and prepared in a 75:25 ratio before use.
2.2. Experimental Procedure
Prior to surface modification, the NiZn ferrite powders were dried in an oven to remove moisture. The NiZn ferrite powders were added with 2wt% Lica 38 and aceton. This mixture was ball-mixed in polyethylene bottles for 6 h. After ball-mixing, the surface modified NiZn ferrite powders were subsequently washed 3 times with aceton to remove the non-adsorbed Lica 38. The slurry was then dried at 80℃ for 24 h. NiZn ferrite powder-epoxy resin composite coatings were prepared as follows. Epoxy resin was mixed with 15 phr CTBN and a proper amount of acetone. The surface modified Ni-Zn ferrite powder (30, 50, and 70wt%) was added to the above CTBN-epoxy resin mixture, diluted with a proper amount of acetone / toluene (75/25) binary solvent. The appropriate amount of DICY and 2-MI dissolved in DMF were then added quantitatively to the NiZn ferrite powder-epoxy resin slurry. The mixture was then stirred using a rotary evaporator under reduced pressure to remove the excess solvent and obtain a suspension with a proper viscosity for casting. The wet coatings (about 50μm) were prepared from the suspension onto transparent PET films. Coated samples were aged under ambient conditions for 24 h and then baked at 160℃ for 1 h. Scanning electron microscopy (SEM) was used to observe the NiZn ferrite powder-epoxy resin composite film micro-structure. Tensile properties were determined from stress–strain curves obtained with a Shimadzu AG-SI universal testing machine at a strain rate of 5mm/minute at room temperature. The composite specimens were 100mm long, 15mm wide, and 0.1mm thick. The dynamic thermal mechanical analysis (DTMA) of composites was determined using a Dynamic Mechanical Analyzer (Pekin Elmer, Diamond). The thermal stability was analyzed with a thermo-gravimetric analyzer (Netzch, STA409) at a heating rate of 10℃/minute under air. The dielectric properties of the NiZn ferrite powder-epoxy resin composites were measured over the range of 20Hz to 1MHz using a HP 4284A impedance analyzer at room temperature. The magnetic properties of the NiZn ferrite powder-epoxy resin composites were measured over the range of 1 MHz to 1.8 GHz using a HP 4291B material analyzer at room temperature.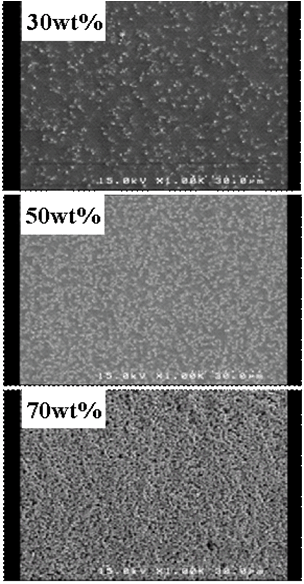 | Figure 1. SEM micrographs of the as-received surfaces of NiZn ferrite powders-epoxy resin coatings with different ferrite loads. |
3. Results and Discussion
SEM micrographs of the as-received and fracture surfaces of NiZn ferrite powders-epoxy resin coatings with different ferrite loads are shown in Figures.1 and 2, respectively. The as-received surfaces of the samples with ferrite powders below 50wt% show that the epoxy resin constitutes a continuous phase and the ferrite particles are dispersed in the epoxy matrix. However, for the sample with the ferrite load of 70wt%, the ferrite particles are highly packed and the epoxy resin is coated onto the ferrite surfaces or filled into the ferrite particle voids. The fracture surfaces of the samples with a ferrite load of 30wt% reveal a brittle behavior characterized by a smooth and flat surface. For the sample with the ferrite load of 50wt%, excellent dispersion of the NiZn ferrite particles in the epoxy matrix was observed on the fracture surfaces. This indicates that the crack developed mainly through the ferrite particles as a result of the interaction between the titanate coupling agent modified NiZn ferrite particles and the matrix. Note that the ferrite particle size increased and the shape of ferrite particle became obscure on the fracture surface as the ferrite load increased from 50wt% to 70wt%. This may be caused by the aggregation of NiZn ferrite powders as the ferrite load was above 70wt%. The occurrence of the dispersed ferrite particles in the epoxy matrix could enhance the toughness of the composite coatings for the sample with a ferrite load of 50wt%. This results in coating fracture in a way more similar to ductile materials than in the case of the samples with ferrite loads of 30 and 70wt%. 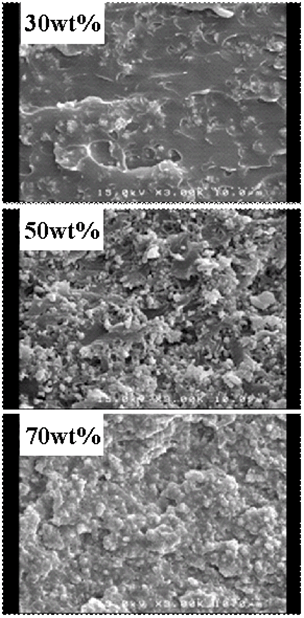 | Figure 2. SEM micrographs of the fracture surfaces of NiZn ferrite powders-epoxy resin coatings with different ferrite loads. |
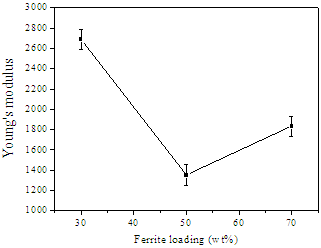 | Figure 3. Variation in Young's modulus of the composite film with different ferrite loads. |
Figure 3 shows the variation in Young's modulus of the composite film with different ferrite loads. It can be clearly observed that the Young's modulus decreased with the ferrite addition and reached a minimum at 50wt%. However, as the ferrite load was increased above 70wt%, the Young's modulus increased. Figure 4 shows the temperature dependence of tanδ for the samples with various ferrite loads. The glass transition temperature (Tg) can be determined from the peak temperature of tanδ. It indicates that Tg decreased from 127℃ to 120℃ as the ferrite load increased from 30wt% to 50wt% and then increased to 131℃ at a ferrite load of 70wt%. These results are not in good agreement with the literature on Young’s modulus and Tg values of inorganic filler/polymer composites. Biernholtz et al.[8] investigated the mechanical properties of ferrite-polymer composites and observed that the elastic modulus of the composites increased with increasing filler load. In this study, at ferrite loads of 30 and 50wt%, the epoxy resin constituted a continuous matrix and the ferrite particles dispersed homogeneously in the epoxy matrix. Therefore, the thermo-mechanical behaviors of the ferrite powder-epoxy composites at ferrite loads of 30 and 50wt% can be explained by the relationship among the chain cross-linking, the chain mobility of thermosetting epoxy resin. The cross linking of epoxy resin occurs during the curing reaction, forming a 3D network bonding molecular chains through covalent links. As the number of cross linking points decreases, the mobility of the chains increases, accompanied by increasing a certain amount of free volume, which leads to a decrease in Tg. As the ferrite load added in the epoxy matrix reaches the 30wt% to 50wt% range, the dispersed ferrite particles hinder the growth and cross linking of epoxy chains, thus producing a glass transition shift to lower temperatures. However, for the sample with a ferrite load of 70wt%, the ferrite particles are highly packed and the epoxy resin is coated onto the ferrite surface or filled into the ferrite particle voids, which leads to chain mobility in the cross linked epoxy being strongly restricted by the presence of ferrite particles. This leads to overall increased Young’s modulus and Tg.Figure 5 shows the dependence of the storage modulus for the samples with various ferrite loads on the temperature. The storage modulus slightly increased as the ferrite load increases from 30wt% to 50wt% and then increases steeply as the ferrite load is further increased to 70wt%.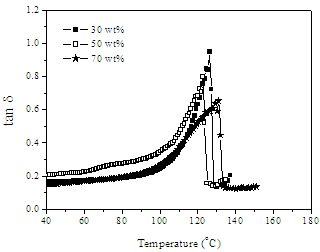 | Figure 4. Temperature dependence of tanδ for the samples with various ferrite loads. |
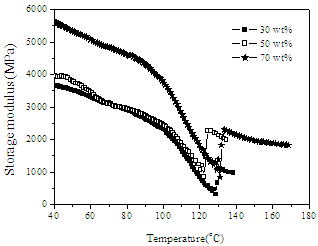 | Figure 5. Dependence of the storage modulus for the samples with various ferrite loads on the temperature. |
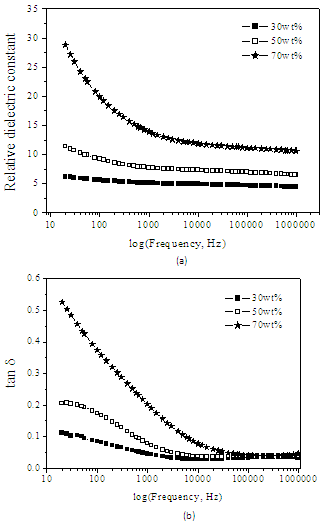 | Figure 6. Variations in (a) dielectric constant and (b) dielectric loss (tanδ) for samples. |
The variations in dielectric constant and dielectric loss (tanδ) for samples with various ferrite loads as a function of the frequency are shown in Figure. 6. For all samples, the dielectric constant and tanδ decreased rapidly with increasing frequency up to 1 kHz and beyond that remained constant. A barrier-layer structure with higher conducting areas encircled by insulating layers can be used to explain the large dielectric constant of ferrite powder-epoxy resin composites at low frequency. This behavior is characterized by the space charge polarization arising from differences between the conductivity of the various phases. At low frequency, electron hopping may occur between Fe3+ and Fe2+ on the octahedral sites9 for NiZn ferrites. The electrons reach the phase boundary between the NiZn ferrites and epoxy resin through hopping and are piled up at the phase boundaries, which results in interfacial polarization. However, as the frequency is increased, the probability of electrons reaching the phase boundary decreases, which results in a decrease in interfacial polarization. Therefore, the dielectric constant decreases with increasing frequency. Note that the relative dielectric constant and tanδat low frequency (below 1 kHz) increased with increasing ferrite load. This is due to the amount of dispersed ferrite particles within the epoxy matrix increasing with increased ferrite load. This increases the phase boundary between the NiZn ferrite powders and epoxy resin, thereby increasing the space charge polarization.In the 1 kHz-1 MHz frequency range the dipolar polarization becomes dominate. The dielectric constant of the samples increased with increasing ferrite load in the 1 kHz-1 MHz frequency range due to the NiZn ferrite phase having a much higher dielectric constant than the epoxy resin.The initial permeabilities of samples with ferrite loads of 30 and 50wt% are shown in Figure.7. The initial permeability remained almost unchanged below 1GHz, and increased from 1.35 to 1.75 as the ferrite load was increased from 30 to 50wt%.Figure 8 shows the thermo-gravimetric analysis curves for the neat epoxy and the samples with ferrite loads of 30 and 50wt%. The weight loss of neat epoxy can be divided into two stages and occurs at 315℃ and 530℃, respectively. Compared with the neat epoxy, the onset temperature of the first thermal decomposition stage for the composites with ferrite loads of 30 and 50wt% was shifted toward lower temperature, which may be caused by the decrease in cross linking of the epoxy resin. However, the offset temperature of the second thermal decomposition for the composites with ferrite loads of 30 and 50wt% was shifted toward higher temperatures compared to the neat epoxy, which may be because the titanate coupling agent modified NiZn ferrite powders had a greater interfacial adhesion with the epoxy matrix, which inhibited the thermal decomposition.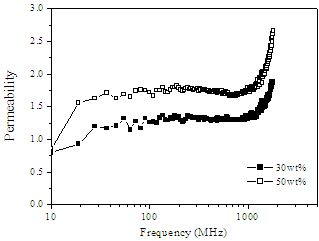 | Figure 7. Initial permeabilities of samples with ferrite loads of 30 and 50wt%. |
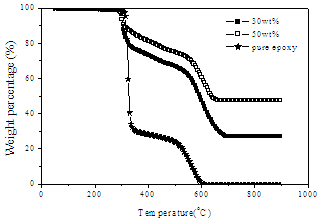 | Figure 8. Thermo-gravimetric analysis curves for the neat epoxy and the samples with ferrite loads of 30 and 50wt%. |
4. Conclusions
1. The Young's modulus and Tg of the composites decreased as the ferrite load increased from 30 to 50wt% and increased as ferrite load further increased above 70wt%.2. The dielectric constants increased with increasing ferrite load at low frequency (below 1 kHz) due to the increase in the phase boundary between the NiZn ferrite powders and epoxy resin. This led to the increase in space charge polarization. The dielectric constant of the samples increased with increasing ferrite load in the 1 kHz-1 MHz frequency range because the NiZn ferrite phase has a much higher dielectric constant than the epoxy resin.3. The initial permeability remained almost unchanged below 1GHz, and increased from 1.35 to 1.75 as the ferrite load was increased from 30 to 50wt%.4. The offset temperature of the thermal decomposition for the composites with ferrite loads of 30 and 50wt% was shifted toward higher temperatures compared to the neat epoxy.
ACKNOWLEDGEMENTS
The authors would like to express their thanks to the Ministry of Economic Affairs of the Republic of China through contract (98-EC-17-A-08-S1-023) and National Science Council of the Republic of China (NSC 98-2221-E-006 -077 -MY3) for financially supporting this project.
References
[1] | Moon K. S., Wong C. P., Kim S. H., Choi H. D., Han S., Yoon H. G., and Suh K. S., Ferrite polymer composites for improving the electromagnetic compatibility of semiconductor packaging, J. Electron. Mater., 36 (2007) 1711 |
[2] | Verma A., Saxena A. K., Dube D. C., Microwave permittivity and permeability of ferrite-polymer thick films, J. Magn. Magn. Mater., 263 (2003) 228 |
[3] | Chung D. D. L., Polymer-matrix composites for microelectronic, Polym. Polym. Composites, 8 (2000) 219 |
[4] | E. C. Snelling, A. D. Giles, Ferrites for Inductors and Transformers, Research Studies Press, England (1986) |
[5] | R. Dosoudil, M. Usakova, J. Franek, J. Slama, V. Olah, RF electromagnetic wave absorbing properties of ferrite polymer composite materials, J. Magn. Magn. Mater.304 (2006) e755 |
[6] | M. R. Anantharaman, S. Sindhu, S. Jagatheesan, K. A. Malini, P. Kurian, Dielectric properties of rubber ferrite composites containing mixed ferrite, J. Phys. D: Appl. Phys. 32 (1999) 1801 |
[7] | K. C. Han, H. D. Choi, T. J. Moon, W. S. Kim, K. Y. Kim, Dispersion characteristics of the complex permeability-permittivity of Ni-Zn ferrite-epoxy composites, J. Mater. Sci. 30 (1995) 3567 |
[8] | H. Biernholtz, S. Kenig, H. Dodiuk, Dielectric, magnetic and mechanical properties of ferrite composites, Polym. Adv. Tech. 3 (1992) 125 |
[9] | Kingery W. D., Bowen H. K., Uhlmann D. R. Introduction to ceramics. 2nd ed. John Wiley & Sons (1976) |