Somil Nishar
Engineering, Colorado State University Pueblo, 2200 Bonforte Blvd, Pueblo, Colorado, United States
Correspondence to: Somil Nishar, Engineering, Colorado State University Pueblo, 2200 Bonforte Blvd, Pueblo, Colorado, United States.
Email: |  |
Copyright © 2023 The Author(s). Published by Scientific & Academic Publishing.
This work is licensed under the Creative Commons Attribution International License (CC BY).
http://creativecommons.org/licenses/by/4.0/

Abstract
This introductory section highlights the importance of effective manufacture and supply of wind towers in light of the rising worldwide demand for wind power as a renewable energy source. As technology has progressed, several designs have emerged to accommodate a wide range of environments, wind speeds, and climates. However, logistical issues arise when manufacturing and transporting wind tower parts on a big scale. Avoiding expensive recalls or maintenance calls requires prioritizing quality assurance and achieving demanding standards at high production speeds. Cellular manufacturing, which has its origins in lean manufacturing concepts, proposes a solution by setting up isolated work areas, or cells, in which all of the necessary tools and materials are located in close proximity to one another. This method shortens the lengths that parts have to travel, which boosts productivity and decreases the likelihood of human mistake.
Keywords:
Cellular Manufacturing, Wind Tower Manufacturing, Lean Manufacturing, Supply Chain Management, Logistics Management, Productivity Improvement
Cite this paper: Somil Nishar, Enhancing Efficiency and Supply Chain Management in Wind Tower Fabrication through Cellular Manufacturing, Journal of Logistics Management, Vol. 11 No. 1, 2023, pp. 1-5. doi: 10.5923/j.logistics.20231101.01.
1. Introduction
Wind power has really stood out as a beacon of hope especially at a time the drive towards renewable energy sources is intensifying globally and there, increasing its demand. The global demand being experienced is not just a statistical upswing but also a reflection of a world that is changing and appreciating more eco-friendly power solutions [1]. This growth in demand is one factor that has pushed manufacturers to meet large-scale and even urgent demands and although the need is global, production facility tends to be localized therefore creating an imbalance on between supply and demand in some regions [2].Advancements in technology have however changed the designs of wind towers over time. The drive for efficiency has led to the creation of varied models suited for different terrains, wind speeds, and climatic conditions. Each design variation adds a layer of complexity to the production process with modern wind towers especially those designed for offshore locations requiring specialized materials that would offer durability against harsh environmental conditions. For large-scale production, securing consistent and quality material supplies is a challenge and also transporting massive components from the manufacturing facility to installation sites presents logistical challenges and causes delays. Given the critical role of wind towers in energy production and the significant investment they represent, there is zero tolerance for defects [3]. Ensuring each tower meets stringent quality criteria while trying to speed up production is a delicate balancing act since any mistakes can lead to costly recalls or maintenance work. For instance, onshore and offshore wind turbine sizes are expected to change by 2035, compared to the 2019 average, as revealed in a research of turbine sizing and designs intended to improve wind generation. Respondents were asked to predict the typical turbine size for brand-new development projects by 2035 [4]. In contrast to the typical turbine sizes of the project built in 2019, the outcomes for the typical respondent are shown in figure 1.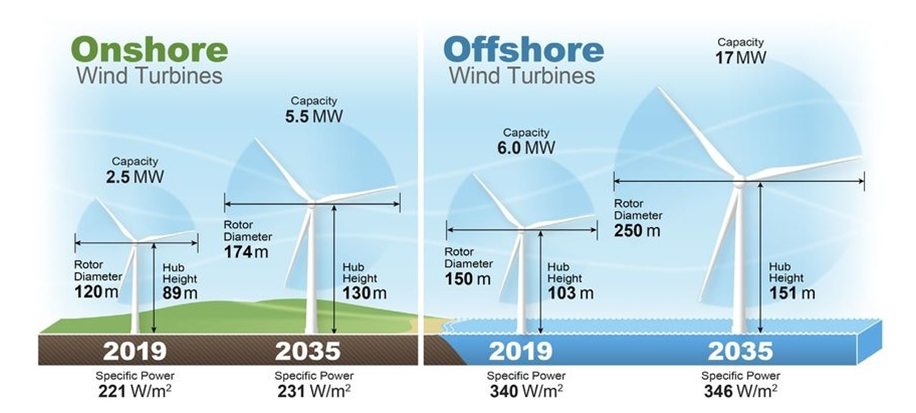 | Figure 1. The need for taller wind turbines in the future. Source: (Wiser et al., 2021) |
Aims and ObjectivesThe study aims to delve into the utility of the cellular manufacturing approach in the fabrication of wind towers and its capacity to overcome logistical hurdles while amplifying productivity. It is therefore imperative to enhance the efficiency of manufacturing and supply chains for wind towers considering the upsurge in global demand for wind energy. The research will illuminate the logistical challenges inherent in large-scale manufacturing and transportation of wind tower components. By tracing its roots to lean manufacturing principles, cellular manufacturing can be seen as a strategy that minimizes distances traveled by parts and thereby improving productivity and diminishing human errors. Such an approach offers distinct advantages to wind tower production including streamlined processes, lessened transit times and also superior quality control. A case study further substantiates these claims by showcasing tangible enhancements in lead time and overall productivity following the adoption of cellular manufacturing. The method proves invaluable by fostering greater efficiency, offering flexibility for diverse tower blueprints and paving the way for potential cost reductions in the wind tower sector. The study will culminate by endorsing cellular manufacturing as a transformative force for the wind tower manufacturing realm and positioning it as a front-runner in an ever-evolving industry.Understanding Cellular ManufacturingHaving worked at the tower manufacturing facility, I can attest that batch processing was still in use. However, the benefits of using cellular manufacturing technique was rarely discussed. Following a presentation in the form of an experiment on the efficiency of cellular manufacturing, it was evident that the new method would save time and offer better results than batch processing for Wind tower manufacturing. As a result of the studies, the industry was persuaded and it adopted the cellular manufacturing method in to manufacturing of wind towers. Following the successful implementation of the cellular manufacturing method, I was compelled to share the information in form of writing.The concept of cellular manufacturing emerged as a groundbreaking approach to manufacturing systems, stemming from the lean manufacturing philosophy which prioritizes the elimination of waste in all its forms. Rooted in principles of efficiency, adaptability, and continuous improvement, cellular manufacturing has reshaped how products are produced in various industries. At the heart of cellular manufacturing is the creation of ’cells’. A cell is essentially a dedicated space or unit where all the equipment and resources needed to produce a particular product or component are closely grouped. These cells are custom-designed to suit specific product families or those with similar production processes. One of the core advantages of cellular manufacturing is its emphasis on workflow. Traditionally, products might move across vast distances within a factory, leading to inefficiencies and delays. In a cellular setup, the distance traveled by components is minimized. Each machine and workstation in a cell are organized to mirror the logical sequence of the production process. This not only speeds up production but also reduces the chances of errors or mishandling [3].Actual Case StudyBy implementing a cellular process in our wind tower manufacturing, we have really streamlined our operations since we have been able to reduce inefficiencies and wasted time. We began by organizing our plate cutting station into a U-shape and this helped decrease the movement of materials. This U-shaped layout ensured that materials are introduced on one side, processed in the center, and then removed from the opposite side to reduce unnecessary transportation time. Our rolling station was then set right beside to our cutting station. This minimized transportation times. To expedite the movement of plates from cutting to rolling, we employed roller conveyors and sliding tables followed by a strategically placed linear welding station that enabled our rolled plates to be moved swiftly to welding. We utilized specific jigs and fixtures to hold plates in position so as to ensure consistency in our welding processes.After the linear welding was completed, we moved the sections directly to circular welding. It was vital for us to ensure that circular welding followed linear welding in quick succession. This approach ensured our sections were ready for the next stages of production without any undue delays. For the post-welding, the sections were directed to our sandblasting and painting stations where we managed to have them either in the same cell so as to maintain the momentum. We also opted for quick-drying paint techniques that minimized wait times in a bid to expedite the process further. Our final assembly station was then set up in such a manner that the freshly painted sections could be rapidly moved for assembly. Here, we relied on cranes and other heavy lifting equipment and this greatly facilitated this phase. The process is as shown in the below figure 2.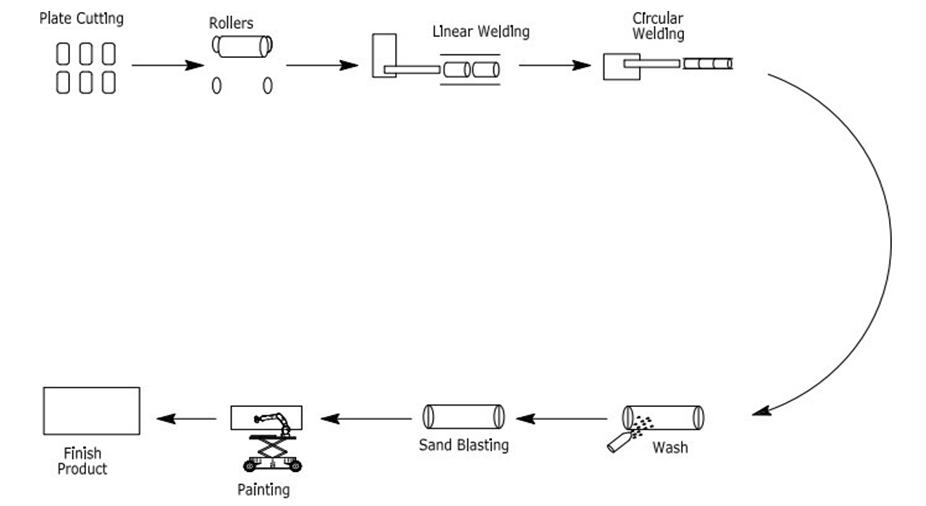 | Figure 2. Cellular Manufacturing process for wind tower fabrication |
Initially, before our cellular implementation, the lead time to produce one wind tower stood at 10 days. This meant we could manufacture about 3 towers in a month of 30 days. However, after implementing the cellular process, we managed to reduce this lead time by 30% thanks to more efficient flow and reduced waiting times. Our new lead time now stands at 7 days, allowing us to produce approximately 4.3 towers in a month. This translates to a 30% reduction in lead time and a remarkable 43.33% increase in our monthly productivity.• Lead time for producing one wind tower = 10 days• Number of wind towers produced in a month (30 days) = 3 towers After Cellular Implementation:• Lead time reduced by 30% due to efficient process flow and reduced waiting time.• New lead time = 0.7 * 10 days = 7 days• Number of wind towers produced in a month = 30 days / 7 days = ~4.3 towers• Improvement in Lead Time = (Old lead time - New lead time) / Old lead time = (10 days - 7 days) / 10 days = 30%• Increase in Monthly Productivity = (New monthly output - Old monthly output) /Old monthly output = (4.3 towers - 3 towers) / 3 towers = 43.33%Key Benefits of Cellular Manufacturing to Wind TowerGenerally, wind tower manufacturing entails a sequential series of processes and by integrating cellular manufacturing, we can break down the process into activities like plate cutting, rolling, welding, sandblasting, painting, and assembly. This not only facilitates a streamlined production flow but also significantly reduces transportation time and the associated risks of moving hefty components. Further, the U-shape configuration enhances this efficiency as a staple in cellular manufacturing. It is designed for materials to enter from one side, undergo processing in the center, and get offloaded from the opposite end and this epitomizes the process optimization. Another key benefit is the noticeable reduction in Work-in-Progress (WIP). The expedited movement of materials through the system drastically cuts down WIP and this liberates floor space and minimizes the capital invested in unfinished goods. Also, cellular manufacturing is a game-changer from a quality perspective. With each cell equipped with its quality control measures it becomes more straightforward to monitor and so, quality-related issues can be swiftly traced back to their respective cells. This ensures prompt rectifications and reduces the likelihood of defective parts progressing to subsequent stages [5].Further, the system’s inherent design ensures shorter lead times due to minimized movement and enhanced process coordination. The ability to provide rapid feedback during anomalies ensures that any arising issues are promptly addressed. Another outstanding advantage in wind tower manufacturing is the enhanced flexibility offered by the cellular setup. It is significantly simpler to reconfigure a particular cell in line with varying tower designs or specifications without causing disruptions in the overarching production line. This adaptability becomes paramount considering the frequent customization requirements intrinsic to specific wind tower projects. From a human resources perspective, cellular manufacturing also amplifies employees’ morale and productivity. It endows workers with a lucid understanding of their roles within the grander production scheme. The potential for cross-training within the cell adds a layer of versatility to their skillset and this mitigates the repercussions of potential absenteeism or worker shortages. This model also fosters a heightened sense of ownership and accountability leading to elevated job satisfaction and productivity levels. Lastly, the cost benefits are undeniable due to the substantial reduction in transportation and handling costs that ultimately means cost savings. Additionally, the optimized flow and minimized WIP lead to less storage demands and so, reduced inventory costs [5].
2. Literature Review
It is evident that by using the novel concept of VCM in a study by Bansee and Chowdary [6] on a new concept of cell production, namely Virtual Cell Manufacturing (VCM). Average wait times and total uptime both fell by 41% and 59%, respectively, in their study. As a result, there was a 30% improvement in task execution time, which went from 1,266.80 to 893.75 minutes. As a result of this structure, setup time is significantly reduced after their initial portion has been processed on the machine. Additionally, it will take less time to reassemble components to create other parts groups. There is deep analysis of studies on decision assistance applications in the textile supply chain by analyzing 77 publications that appeared in the 35 journals between 1994 and 2009. Information about the use of intelligent systems and decision support at various points in the textile supply chain, together with pertinent references for researchers and practitioners [7]. Also, there is a mathematical model that can be used in building a cell production system with uncertain parameters in a manufacturing model. In the model, the processing time is a random variable that behaves as per a normal probability distribution, and the requirement is a random variable that behaves as per a normal probability distribution. Minimized intercellular mobility and perforation of the bottleneck wound [8].Further, another analysis on increasing wind turbine tower heights reveals three main insight. First, the U.S. possesses ample wind resources at higher altitudes and this justifies technologies for taller turbine hub heights. Secondly, tubular steel towers emerge as the most viable tall tower technologies and therefore gaining significant industry traction in recent years following the soft-soft design criteria and finally hub heights between 110 m and 140 m could offer cost savings between $5/MWh and $10/MWh over current turbines especially if future innovations further enhance their economic appeal. However, there are inherent uncertainties in these findings that demand more detailed cost estimations for validation. From the analysis, the benefits appear to taper off beyond 140 m hub heights and regions with high estimated LCOEs might not see wind deployments solely based on economic merits for taller hubs [9]. Beyond mere wind resource benefits other motivating factors for taller turbines could arise from land availability challenges or the aim to accommodate larger rotors and therefore ensure they remain clear of the ground. Another relevant analysis presents an overview of response patterns and sustainability issues in recent work from 2015 to 2022. The review focuses on key issues related to recent industry developments such as Industry 4.0, big data, digital twins and energy consumption [10]. Mobile manufacturing systems will be able to use the additional insights provided by the integration of Industry 4.0, digital twins and big data to improve response and reconfiguration capabilities to Continuously adapt to industry changes. According to the assessment, the continued increase in energy production from renewable sources requires companies to use new energy management models and not only reduce energy consumption but also integrate energy sources different quantities.
3. Conclusions
The global push towards sustainable energy solutions, especially wind power, has high- lighted the significance of efficient and quality-driven manufacturing processes. As the demand for wind towers surges, so does the need for production methodologies that can address both scale and precision. For instance, it’s evident that transitioning to cellular manufacturing reduced our wind tower production lead time from 10 to 7 days and this increased the monthly output from 3 to 4.3 towers and therefore exemplifying cellular manufacturing’s transformative efficiency in the industry. In this context, cellular manufacturing emerges as more than just a method since it represents a pivotal shift in the paradigm of production for the wind tower industry. As the wind tower production sector grapples with the challenges of scale, complexity, and global demand, cellular manufacturing offers a beacon of efficiency, quality, and adaptability. For manufacturers looking to the future, moving to cellular manufacturing isn’t merely a strategic choice but also a fundamental shift to ensure continued competitiveness and success in a rapidly evolving industry landscape.
References
[1] | Chen, J. and Kim, M.H. (2021), “Review of recent offshore wind turbine research and optimization methodologies in their design”, Journal of Marine Science and Engineering, Vol. 10 No. 1. |
[2] | Kumar, A., Pal, D., Kar, S.K., Mishra, S.K. and Bansal, R. (2022), URL https://doi.org/10.1007/s10098-021-02248-z. |
[3] | Bošnjaković, M., Katinić, M., Santa, R. and Marić, D. (2022), “Wind turbine technology trends”, Applied Sciences, Vol. 12 No. 17, pp. 8653–8653. |
[4] | Wiser, R., Rand, J., Seel, J., Beiter, P., Baker, E., Lantz, E. and Gilman, P. (2021), “Expert elicitation survey predicts 37% to 49% declines in wind energy costs by 2050”, Nature Energy, Vol. 6 No. 5, pp. 555–565. |
[5] | Jureczko, M.E.Z.Y.K., Pawlak, M. and Mężyk, A. (2005), “Optimisation of wind turbine blades”, Journal of materials processing technology, Vol. 167 No. 2-3, pp. 463–471. |
[6] | Bansee, J. and Chowdary, B.V. (2007), “A new concept of cellular manufacturing: a case study”, in “Fifth LACCEI international Latin American and Caribbean conference for engineering and technology”, LACCEI, pp. 1–10. |
[7] | Ngai, E.W.T., Peng, S., Alexander, P. and Moon, K.K. (2014), “Decision support and intelligent systems in the textile and apparel supply chain: An academic review of research articles”, Expert Systems with Applications, Vol. 41 No. 1, pp. 81–91. |
[8] | Salarian, R., Fazlollahtabar, H. and Mahdavi, I. (2014), “Inter-cell movement minimisation in a cellular manufacturing system having stochastic parameters”, International Journal of Services and Operations Management, Vol. 17 No. 1, pp. 67–87. |
[9] | Lantz, E.J., Roberts, J.O., Nunemaker, J., Demeo, E., Dykes, K.L. and Scott, G.N. (2019), URL https://www.nrel.gov/docs/fy19osti/73629.pdf. |
[10] | Renna, P., Materi, S. and Ambrico, M. (2023), “Review of Responsiveness and Sustainable Concepts in Cellular Manufacturing Systems”, Applied Sciences, Vol. 13 No. 2, pp. 1125–1125. |