Martin Petruf , Ján Kolesár
Technical university, Faculty of Aeronautics, Department of Aviation Engineering, Rampová 7, 041 21 Košice, Slovak republik
Correspondence to: Martin Petruf , Technical university, Faculty of Aeronautics, Department of Aviation Engineering, Rampová 7, 041 21 Košice, Slovak republik.
Email: |  |
Copyright © 2012 Scientific & Academic Publishing. All Rights Reserved.
Abstract
Acquisition of the most modern technical systems and their logistical support requires innovative approaches to be adopted in design, manufacturing and providing logistical services for their operation. The article aims to be a contribution to the acquisitional approach termed as CALS, i.e. to a modern, computer-based logistics, which can greatly improve economics of complicated technical systems acquisition. Integrated logistical support provided through electronization of design and operational documentation linked with standardization and continuous upgrade is yielding surprising benefits.
Keywords:
Logistics Support, Production’s Logistics, Continued Acquisition, Life-Cycle, Logistical Management, Simulated Engineering
1. Introduction
Long term aspect of life-cycle at complex and costly systems in aviation and defence industry is necessitating continuous and rapid solutions to economically demanding upgrades, modernization and innovation. All that requires knowledge of steady and more frequent and revolutionary facts from sciences and technology bound to growing need for computer technology, new information and testing technologies, etc. All this is necessary for fast and economic operation and it is much harder to reach demanded quality without this approach.Implementation of computer systems in logistics for modern trends in military and industrial branches is of vital importance, particularly for the purpose of obtaining higher quality (complex quality) from the aspect of system characteristics (readiness, performance, reliability, safety, viability for manufacturing, maintainability, availability, supportability, partial or overall modernization, recycling, etc.... ), both in view of the methods applied (concurrent engineering, limiting the variability of manufacturing and the like).The CALS Initiative (Computer Aided Acquisition and Logistic Support)- was incepted in 1985 and starting with 1994 it has been meant as continuous acquisition and life cycle support as a means of integrated logistical support for complex technical systems[1].
2. The CALS Approach and Product Acquisition
Technologies based on CALS have been originally designed only for information support of logistics. Gradual development, mostly the increasing performance of information technologies caused CALS to transform into the means of informational support for research- manufacturing–operation and modern logistical support of complex technical systems (CTS) in all phases of the product life-cycle, starting with market research and ending with its liquidation. Interconnection of design of complex technical systems and their manufacturing through information technologies, i.e. Computer Aided Design (CAD), Computer Aided Manufacturing (CAM) is affected by rapid changes in modernization, facts that require comprehensive revision of the manufacturing processes and activities related to both acquisition and support of logistics.The fundamental thing in managing CTS is management of logistics in terms of acquisition disciplines, directed in all the phases of the acquisition life-cycle. The complex effort is covered by the notion of integrated logistical support (ILS) and is continuously defining, projecting, upgrading and ensuring a comprehensive readiness support of the CTS throughout its entire life-cycle[2].Fundamental to any engineering design practice is an understanding of the cycle, which the product goes through its life. The life cycle begins at the moment when an idea of a new system is born and finishes when the system is safely disposed. In other words, the life cycle begins with the initial identification of the needs and requirements and extends through planning, research, design, production, evaluation, operation, maintenance, support and its ultimate out[3] ,see illustration in Fig.1.Manufactures who specialise in military hardware will often be approached, either directly or through an advertised “invitation to tender “ to discuss the latest defence requirement. For most other manufacturers, it is generally up to them to identify a / potential / market need and decide whether they can meet that need in a profitable way. The UK MoD approached BAE System to bring together a consortium for an air system that would out-perform all existing offensive systems, both friend and foe, and that would include all of the concepts identified as practical in the URA research project.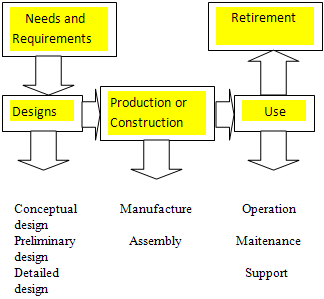 | Figure 1. Life cycle of the system |
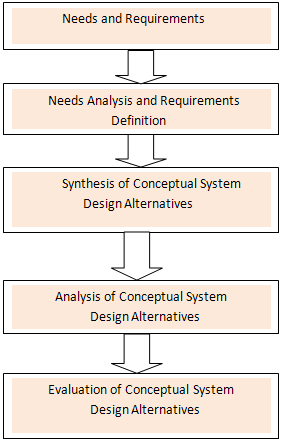 | Figure 2. Conceptual system design process |
The first process then is a set of tasks performed to identify the needs and requirements for a new system and transform them into its technically meaningful definition. The main reason for the need of a new system could be a new function to be performed or a deficiency of the present system. The deficiencies could be in the form :● Functional deficiencies,● Inadequate performance,● Inadequate attributes,● Poor reliability,● High maintenance and support costs,● Low sales figures and hence low profits.The first step in the conceptual design phase is to analyse the functional need or deficiency and translate it into a more specific set of qualitative and quantitative requirements. This analysis would then lead to conceptual system design alternatives. The flow of the conceptual system design process is illustrated in Fig.2.The output from this stage is fed to the preliminary design stage. The conceptual design stage is the best time for incorporating reliability, maintainability and supportability considerations[3].The main task :● during the preliminary design stage are system functional analysis as operation functions, maintenance functions, allocations of performance and effectiveness factors and the allocation of system support requirement,● during the detailed design stage is-Development of system/product design,- Development of system prototype,-System prototype test and evaluation.Design is the most important and crucial stage in the product life cycle. Reliability, maintainability and supportability depend on the design and are the main drivers of the operation availability and costs. It is during this stage that safety, reliability and maintainability demonstrations can be performed and, from these, maintenance and support plan can be decided.● the production/construction process is a set of tasks performed in order to transform the full technical definition of the new system into its physical existence.CALS is aimed to bring revolutionary changes in the fields of collecting, archiving and transfer of digital data as well as unification of information and testing technologies. Computer aided design and manufacturing enables replacement of drawing and copies by data modelling the new product to be manufactured taking the form of an integrated database, which makes it possible to design and plan both manufacturing and logistical support in real time, involving production teams, further contractors and sub-contractors. There is thus an integrated Product Team - the IPT. Such approach is termed as Concurrent Engineering - CE, see illustration in Fig.3.In practice, CALS involves organization of a joint information area supported by automated systems designed to ensure efficient solution of engineering problems and planning of company resources, as well as planning of manufacturing, remote approach to information and on-line solutions of supplier-and-customer relations, prognoses development and tasks of prediction. The joint integrated database features uniform and standard rules of generating, downloading, upgrading, searching and transferring information.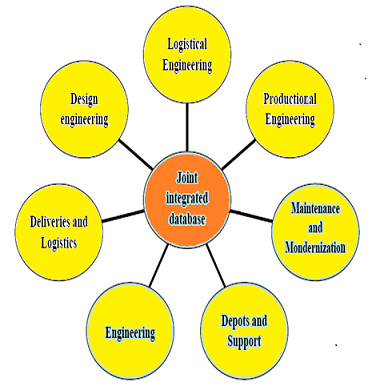 | Figure 3. Acquisition approach of the CALS |
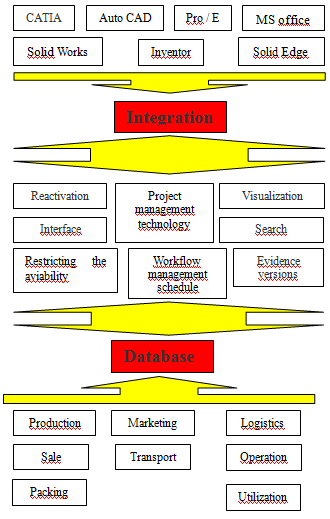 | Figure 4. System Smart Team |
Administration of the joint data base is ensured by a system called PLM (Product Lifecycle Management), either serving as a comprehensive file of computerized systems such as CAE/CAD/CAM/PMD and ERP/CRM/SCM for development, design and integrated logistic support of CTS, or as an information system for a company facilitating interaction with other manufacturers.Currently from the PDM systems is the most famous ENOVIA and Smart Team (Dessault System), Teamcenter(Unigraphics Solutions), Winchill (PTC), my SAP PLM(SAP), Baan PDM (PDM), and Russian system Pilot:PLM(ASCON), PMD Step Suite (MO “Applied logistics), Party Plus (Pilot Software). Dessault Systems Company aprogrambasedon ENOVIA PDM (Product Manager) integration modules CAD/CAM/CAE designed to simulate a product data management, processes and resources at different stages of life cycle – from conceptual design to disposal. The Smart Team is based on Interbase or Oracle with different vizualizer – Fig. 4PLM as a system – illustrated in Fig.5 forms fundaments of integrating the information area of industrial products and, on the basis CALS, it enables interaction of a wide spectrum of manufacturers utilizing computerized systems.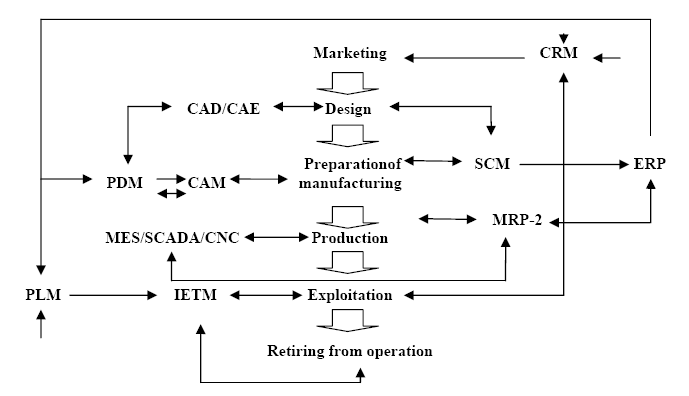 | Figure 5. Life cycle of industrial manufacturing and the computerized systems applied |
Legend:PLM – life-cycle management, PDM – management of system data, CAD –design, CAE – engineering, CAM – technology and manufacturing, CRM – customer data management , SCADA – dispatching management, MES – managing performances, SCM – managing the supply chain, ERP – company planning and management, CNC – computer based control of the machinery, MRP-2 – planning of production resources, ITEM – interactive electronic manuals.The market success of the CTS without the CALS technology would be in these days a mission impossible. Standardized data formats of network servers enable rapid propagation of modern designs avoiding „reinventing the wheel“. Such a modern approach to design and manufacturing of high-tech products consists of:● Applying computer and modern information technology in all phases of the product life-cycle,● Applying a unified methodology to process controlling,● Cooperating with all the participants (manufacturers, contractors, operators ...) in compliance with the requirements set out by international standards regulating such interactions (electronic data exchange).Implementation of the CALS should be integrated into the Contracts on delivery of CTS concluded between the manufacturer, contractor and the customer.Higher level of information integration is known as the „Joint CALS Program and the „ Joint Engineering Data Management of Information Control Systems – JED-MICS“. Both are considered as revolutionary programs identifying a range of functional requirements for the logistical processes of the CTS, such as:● Logistical support analysis / LSA /,● Logistical support analysis recording / LSAR /, etc....,Or supporting the spare parts supply for the equipment repair processes.
3. Logistical Support to Manufacturing and Operation
The introduction of CALS for manufacturing and logistics was of key importance owing to its single and integrated databases equally suitable for the supplier, designer, technical manuals, trainers and logistic specialists as well. Existence of different databases designed and maintained on the part of the supplier and customer raises the need for standardization and cooperation. Then both parts of the logistics, acquisition and maintenance are fused into a single, integrated logistics, which starts before research and ends at retiring the item from operation[4,5]. Most of the life-cycle phases, starting with choosing the suppliers of raw materials and components ending with selling the product requires logistical support, i.e. controlling the supplier chain to increase the value added to the product, to decrease material demand and cut short the time of waiting for the product made ready. The more frequently used approach „ Make or Bay “, particularly at limited manufacturing capacities, or advantages in completion of standard parts. Most of the firms are developing specialized software and hardware for example - commerce and, either they are providing or using a joint information area, to provide services, ensure operation for building, manufacturing or delivery the products on order[5]. Design and manufacturing of CTS directly on or-der with re-defined parameters and specifications, when using CALS technology, enables minimizing time on cost per order. Coordination of the activities of all the partner companies making use of the internet and e-commerce, /electronic data Exchange/ known as the system of data administration /CPC/ integrated information area enables repeated use of identical project documentation in joint projects, an approach that substantially reduces the time of developing a new product, reduces the costs of the entire design and the cycle of manufacturing as well as simplifying functioning of the systems (Fig.6).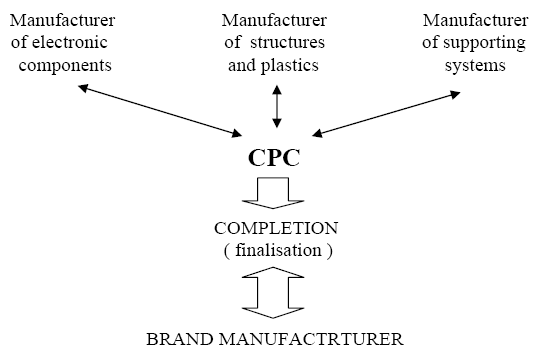 | Figure 6. Virtual company and interaction with subcontractors |
Modern logistic system based on the CALS vision will be a system continuously upgraded and standardized. The standards must be applied in all the participating companies involved in the research, development and manufacturing of the CTS, on the basis of internationally accepted documents for the integrated logistical support. The synergic effect of implementing the CALS is remarkable and some of the sources declare:● 30 - 40% acceleration in implementation of re-search and development,● Up to 30% cuts in cost of purchasing new CTS,● Up to 20% cuts in the time of purchasing and delivering spare parts,● As much as the 9th multiple of reducing time needed for adaptation of projects[1, 6].In view of the manufacturing, substantial in-crease in the quality of products, as much as 50% reduction of the time for development and preparation of manufacturing, increase in productivity by 75%, savings in inventory management by 60%, increasing return of investments by 70% and as high as 50% reduction in the services and stocks[7,8].On introducing CALS, the savings presented can be even higher thanks to its function of maintenance and sub-function of testing, measurement and diagnostics (TDM – Test Measurement Diagnostic), which enable transition from the time-bound maintenance to maintenance by status quo. Furthermore, CALS is providing accelerated research and development of ZTS reducing the periods of 6 up 10 years down to 4 and rapid implementation of top-level technology into manufacturing processes. Research centers of CALS technology – „ Applied logistics „ are in economically developed countries (USA, France, Germany, Russia, UK.....) are intensively dealing with research and implementation of software solutions for high-tech products and their in-formation support. Provision of logistical services for the implementation of solutions is conditioned by the joint approach of the participating companies at creating integrated information products and modern technology-based approaches. Integrated logistical support (ILP) is ensured by a set of Technologies focused on improving operational and technical features of products as well as on cutting life-cycle costs. For example, „ Tupolev “ by developing its operational documentation Tu – 204/214 to the international standard known as the ASD S 1000 D is managing its post-sale service and increasing its product competitiveness. Key component of this technology for monitoring technical status is in creating and maintaining electronic form for aircraft, automated data processing, using RFID components, etc. ..., what in their long run provides excellent reliability of aircraft manufactured and passenger safety. The first Russian aircraft designed by means of the CALS technology, including the digital analysis of logistical support (ALP) is the one known as the SSJ – 100, an aircraft entirely designed in digital environment, making extensive use of the CAD and PDM technologies.
4. Conclusions
Systems-based approach in developing integrated information systems in support of high-tech products and CTS throughout their entire life-cycle, makes it necessary to adopt continuous improvements of concepts, in-depth study and development of CALS technologies. Knowledge of top-level products and procedures of the CALS enables high-speed configuration of the CTS, integrated logistical support and its analysis in all phases of the product life-cycle, re–engineering of company processes in research, manufacturing and operation of high-tech products. The system of PDM data administration plays a decisive role in an integrated in-formation environment and provides, retrieves rationally structured data for product design, technology, manufacturing and operation as well as operation of realization of modern logistical support for complex technical systems. A new standard ASD S 3000 L is being prepared today with participation of world leaders in research of technologies. Certain modules for logistics and safety mostly in aviation technology are object of development conducted by the AVIS, a well established Slovak company.
ACKNOWLEDGEMENTS
This article was written with the support of the project VEGA No.1/1117/11 - Integration of algorithms, automatic flight control and control air turbo compressor engines and project KEGA No.001-010TUKE-4/2010 - The use of intelligent control methods and the modeling of aircraft engines in the educational process.
References
[1] | PETRUF, M.: Logistika OS z pohľadu poznatkov v strojárske praxi špeciálnej techniky, výzbroje a materiálu. Trenčín: Transfér, 2009. 5strán. |
[2] | JAHELKA, K.: Kontinuálna akvizícia a podpora životného cyklu zbraňových systémov. Brno: Zborník VA Brno, 2010. |
[3] | KUMAR, U.D., CROCKER, J., KNEZEVIC, J., EL-HARAM, M.: Reliability, Maintenance and Logistic Support – A Life Cycle Approach. Kluwer Academic Publishers, Massachusetts 02061 USA, 2000. |
[4] | MADARASZ,L.,BUČKO,M.,ANDOGA,R.: Integračnéas-pekty tvorby a prevádzky systémov CIM, TUKE FEI Košice, Elfa s.r.o. 2.vyd. 2011 |
[5] | MADARASZ,L.: Inteligentné technológie a ich aplikácia v zložitých systémoch, TUKE FEI Košice, University Press Elfa, 2010 |
[6] | MALINDŽAK,D.: Výrobná logistika I.,TUKE F BERG Košice, Vydavateľstvo ŠTROFEK Košice, 2.edic. ,2010 |
[7] | KYSEĽOVÁ, K., CEHLÁR, M.: Economic characterization of raw material extration technological processes by com-puter. Košice : Acta Mettallurgica Slovaca, Roč. 9, č.1 (2009), s.55-62, ISSN 1335-1532 |
[8] | PETRUF, M.: Moderná logistická podpora výskumu ,vývoja a prevádzky zložitých technických systémov. 6s. AOS LM 2011, 17. medzinárodná vedecká konferencia „VTPS 2011“ ISBN: 978-80-8040-431-4. |
[9] | www.cals.ru/collaboration/, 2011 |
[10] | ru.wikipedia.org/wiki/CALS-technologie, 2011 |