Fawziea M. Hussein1, Johain J. Faraj2, Raed J. Kareem1
1Mechanical Engineering, Technical College of Baghdad, Middle Technical University, Baghdad, Iraq
2Chemical Engineering, Technical College of Baghdad, Middle Technical University, Baghdad, Iraq
Correspondence to: Raed J. Kareem, Mechanical Engineering, Technical College of Baghdad, Middle Technical University, Baghdad, Iraq.
Email: |  |
Copyright © 2018 Scientific & Academic Publishing. All Rights Reserved.
This work is licensed under the Creative Commons Attribution International License (CC BY).
http://creativecommons.org/licenses/by/4.0/

Abstract
This work presents an experimental investigation of The effects of adding Nano-particles to the paraffin wax (as a PCM). A fixed quantity of PCM (5 kg) which produced by Al-dora oil refinery was selected. A heat-exchanger was used to exchange the heat between HTF (water) and PCM for the PCM charging process, also between PCM and HTF (room air) for the discharging process. The effect of adding Nano-particles on charging and discharging process time was studied. Adding (Al2O3) to the PCM can reduce charging time by 2.1, 5, and 6.4% after adding the Nano-particles by 0.1, 0.2 and 0.3% wt concentration, respectively. And adding (CuO) to the PCM can reduce charging time by 2.7, 6.25, and 8.8% after adding the Nano-particles by 0.1, 0.2 and 0.3% wt concentration, respectively. The paraffin wax shows a good response towards adding Nano-particles. Using Copper (II) oxide (CuO) Nano-particles was better than Alumina (Al2O3) Nano-particles because the PCM thermal conductivity is showing good response after adding Copper (II) oxide.
Keywords:
PCM, Phase change materials, PCM for space heating, Nano-particles
Cite this paper: Fawziea M. Hussein, Johain J. Faraj, Raed J. Kareem, Experimental Investigation of Adding Nano-Particles to PCM for Heating Applications, Journal of Mechanical Engineering and Automation, Vol. 8 No. 1, 2018, pp. 32-37. doi: 10.5923/j.jmea.20180801.03.
1. Introduction
This Many mountainous, nomadic and marshlands in Iraq are missing reliable grid utility service, rendering those areas populaces to follow some kind of primitive to satisfy-their needs. Since the conventional air conditioning equipment has to be powered by a grid which is not efficiently available in these areas and that impede the process of their life style enhancement, unfortunately such luxury cannot be available at the present constraints. When the solar collectors are used to heat domestic hot water, the storage also matches different powers of the solar collector field, which collects the energy over many hours of the day, to meet the request of a hot bath that is filled in only several minutes. For example in hot water heat storages, sensible heat storage is used or in the floor structure under floor for heating. An alternative method is changing the phase of a material. The best -known examples are ice and snow storage. The storage of thermal energy in the form of latent heat in phase change materials (PCMs) represents an attractive option for low and medium temperature range energy applications. Wide ranges of PCMs have been investigated, such as paraffin wax.Many researcher has been studied the effect of adding Nano-particles to the PCM like Arasu et al. [1] studied the effects of Nano-particle volume fraction on both the melting and-solidification rates of paraffin wax the study analyzed and compared for Al2O3 and CuO Nano-particles confirmed that the thermal performance of paraffin wax is improved only marginally with the dispersion of Al2O3 and CuO Nano-particles. A numerical solution using Comsol software was performed by Afif [2], to investigate the effect of using phase change materials to decrease the heating/cooling loads for-buildings. A Numerical analysis of PCM melting in a single shell-and-tube LHTES unit was presented by Sciacovelli et al. [3]. Harikrishnan and Kalaiselvam [4] observed that complete melting times of palmitic acid with Nano-particles with 0.1, 0.2 and 0.3 wt% of TiO2 Nano-particles were decreased by 6.43, 14.62 and 21.05% respectively, than the palmitic acid. Also, complete solidification times of Nano-fluids with 0.1, 0.2 and 0.3 wt% of TiO2 Nano-particles were decreased by 6.18, 12.37 and 20.11% respectively, than-the palmitic acid. Chaichan et al. [5] improve the thermal conductivity of the paraffin wax by adding Nano-particles, which-is having a high thermal conductivity and using two types of the Alumina Nano-particles (Al2O3) and TiO2 Nano-particles. A numerical study on variations of thermo-physical properties of Phase Change Material (PCM) due to dispersion of Nano-particles investigated by Auriemma and Iazzetta [6]. Three different metal oxide Alumina (Al2O3), Copper Oxide (CuO) and Zinc Oxide (ZnO) were used, that was heated from one side of rectangular enclosure of dimensions of 25 mm × 75 mm. The integrated simulation system ANSYS Workbench 15.0 was used. It was founded that the thermal-conductivity of nPCM is greater than the simple PCM and Dynamic viscosity of nPCM increases with the increasing in the volumetric concentration of Nano-particles. While the other researcher has been used a diifrent type of additives like Bugaje [7] found that the thermal response of paraffin wax was improved by the use of metal matrices embedded within the body of wax. Significant decreases in melting and freezing times were obtained by the use of aluminum sheet metal. Fukai et al. [8, 9] modeled and tested the use of Carbon-fiber combined with n-Octadecane. Carbon fibers were added to improve the thermal-conductivities of phase-change materials packed around heat-transfer tubes. The transient thermal responses enhanced as the volume fraction of the fibers and the brush diameter-increased. Hamada et al. [10] compared numerically and experimentally the thermal behavior of carbon chip and carbon brush. The carbon-fiber chips are efficient for improving the heat-transfer-rate in PCMs. Zhang et al. [11] tried to improve the thermal conductivity of (PCMs) by introducing the-same mass fraction of several kinds of additives, among which, exfoliated graphite was found-to be most effective. The thermal conductivity increased with the mass fraction of exfoliated graphite, through the mechanical properties reduced. Mattawee and Assassa [12] placed aluminum powder in the (PCM) for a compact (PCM) solar-collector. Solar energy was stored in (PCM) and discharged to cold water-flowing in pipe located inside the (PCM). The propagation of melting and freezing fronts was studied during the charging discharging process. Tavaranan et al. [13] proposed a study for using PCM with photovoltaic (PV) panels and thermoelectric modules (TEMs) in the design of a portable vaccine-refrigerator for remote villages with no grid electricity. TEMs, which transfer heat from electrical-energy via the Peltier effect, represent good alternatives for environmentally friendly cooling applications, especially for relatively low cooling loads and when size is a key factor. For water heating, Gu et al. [14] developed a heat recovery system using PCM to recover the rejected-heat and produce low temperature hot water for washing and bathing. Sharma et al. [15] developed a solar cooker based on Evacuated Tube Solar Collector (ETSC) with PCM storage with a closed loop-pumping line-containing water as Heat Transfer Fluid (HTF) in a stainless steel tubing heat exchanger. For cooling electronic devices, Takakuwa et al. [16] designed an electronic module intended for cooling electronic-equipment, including paraffin as the PCM and measured-its transient temperature rise. The effect of the diameter of pin fins and heat dissipation values were investigated as design parameters.
2. Experimental Work
An The outdoor experimental study was conducted in Iraq-Wasit province on the roof of a house with a latitude and longitude 32.5° north and 45.8° east respectively, the experiment done with an environmental condition about 8 to 15°C. Figure (1) shows the schematic diagram of the experimental rig.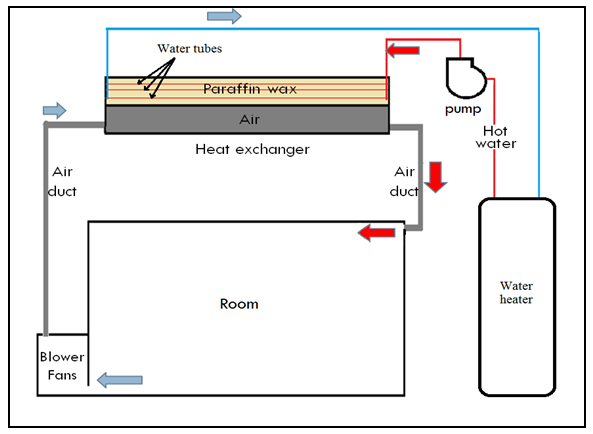 | Figure (1). Schematic view of the system |
2.1. Room Model Design
The chosen wood to build the room model was an MDF wood having a thickness of 18 mm and its thermal conductivity about
A suitable scale factor is considered the dimensions of the model are assumed to be 5:1. The prototype for this study was a room in Technical College of Baghdad with dimensions of (7.5 m
3.87 m
3.21 m). Since the scale factor is 3 then the dimension of model is (1.5
0.774
0.642) m. With one inlet at the top of the wall and one outlet in front of the inlet wall but the outlet point at the bottom of the wall. The inlet and the outlet port is considered to be along the wall so as to make the calculation more easier as well as this inlet and outlet port having the following dimensions (4 mm) height and (77.4 cm). The reduced scale model used in this study was made of wood 18mm thickness with a thermal conductivity about 
this type of wood was the nearest to the calculated value
The overall heat transfer coefficient for the model was calculated with the selected wood thermal conductivity and its value was 
2.2. Design of Heat-Exchanger Model
The design of heat exchanger assumption is to contain three fluids which are water, PCM and air, everyone of these fluids should be worked separately from the others, so the heat exchanger will be divided into three parts, as shown in figure (2). The PCM container is made from a galvanized iron with a thickness of a 0.6 mm and thermal conductivity (72)
As well as that the all of the heat exchanger is surrounded by wood with a thickness of 18 mm and its thermal conductivity about
The wood used to give a suitable support as well as that the wood is considered as a good insulation so as to decrease the dissipated heat to the surroundings. The PCM container and the HTF passages are sealed by the wood.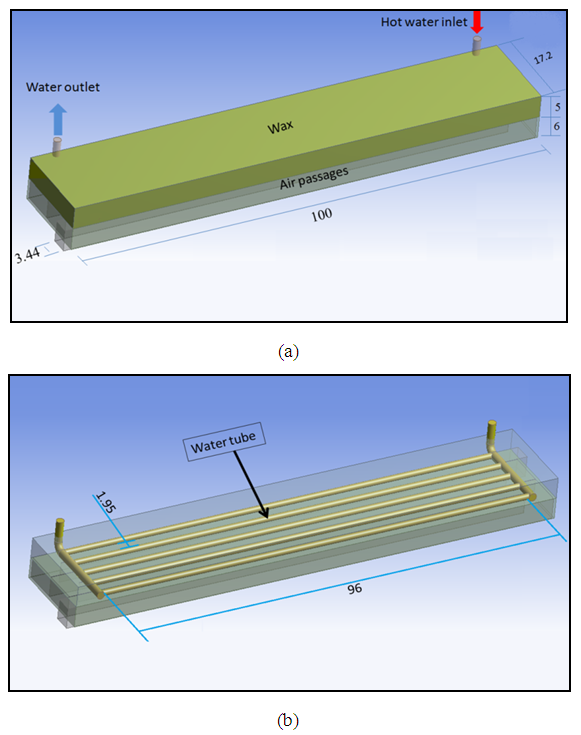 | Figure (2). Schematic view for the heat exchanger and it`s passages as shown at the bottom (all dimensions in centimetres) |
2.3. PCM
The phase change material that used is (5) kg of an Iraqi local paraffin wax grade (A) from Al-Dora oil refinery with the following properties as shown below in table (1):Table (1). Paraffin wax properties 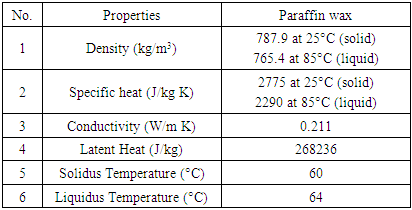 |
| |
|
2.4. Nano-particles
The used Nano-particles is (Al2O3) and (CuO), as shown in table (2):Table (2). Nano-particles properties 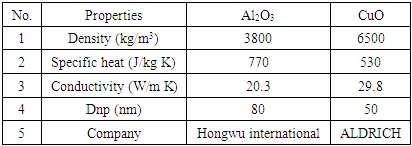 |
| |
|
3. The Procedures of Study Work
The effect of mixing Nano-particles to the phase change materials (PCM) during the heating modes was studied. The test of phase change material for the heat exchanger model containing (PCMs) and room model has been taken two months to achieve these results. The following procedures are used to achieve the work:
3.1. Mixing Process
1. Pouring the paraffin wax (PCM) to the heat exchanger.2. Adding 0.1, 0.2 and 0.3 %wt of (Al2O3) to the PCMs for every case of studied, respectively.3. Replacing the phase change materials (paraffin wax) with a pure one of it.4. Adding 0.1, 0.2 and 0.3%wt of (CuO) to the PCMs for every case of studied, respectively.
3.2. Charging Process
1. Water heater system turned was on until reaching steady state.2. The pump was turn on to circulate the water to the heat exchanger.3. The water got in the heat exchanger with a high thermal energy through the copper tube.4. The water leaved the heat exchanger after losing a part of its thermal energy.5. The water heater and the pump was turn off after all the PCM temperature reach to 70°C.
3.3. Charging Process
1. The air was moved and circulated between room model and heat exchanger, which it’s a closed circulation.2. The cooled air started to draw from the room model through the outlet port of the room model by a centrifugal fan.3. After moving the air inside the heat exchanger and gaining thermal energy, air leaved the heat exchanger through the outlet port and returned to the room model.
4. Temperature Measurement
A (12) thermocouples of type “K” in the range of -100 to 1300°C are used to measure the temperature as shown in figure (3). The thermocouple junctions distributed at selected locations in the room model, air duct, heat exchanger, bottom of the separated plate, water inlet and outlet and as well as ambient. | Figure (3). BTM-4208SD Data logger with 12 channels |
5. Results and Discussions
The effect of adding nano particles to the PCM for both cases of solid and liquid PCM as it shown in figure (4- a and b).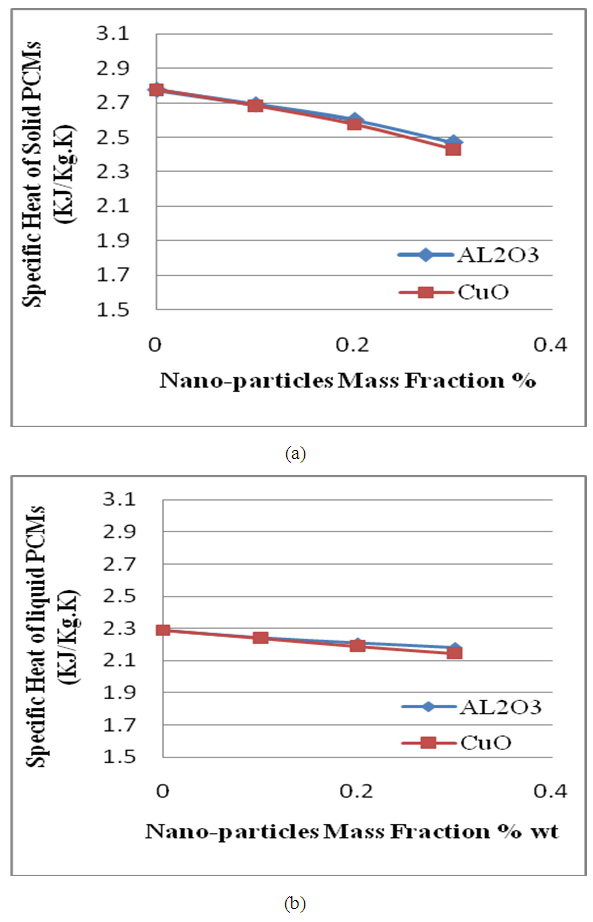 | Figure (4). Effect of adding Nano-particles on: (a) Specific heat of solid PCM. (b) Specific heat of liquid PCM |
The effect of adding Nano-particles to the PCM on the latent heat of fusion as it seen in figure (5).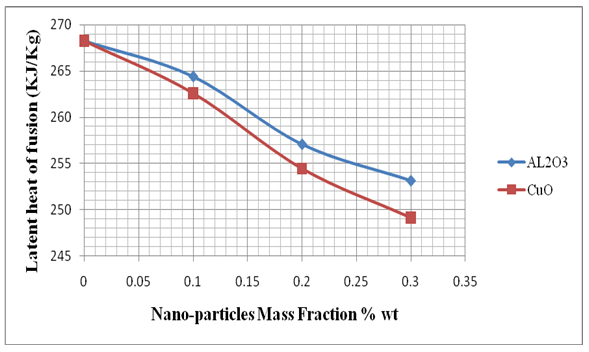 | Figure (5). Effect of adding Nano-particles on the latent heat of fusion |
The thermal conductivity will be affected relative to the percentages of additive the thermal conductivity will be incrcreased relative to the increment of Nano-particles concentration in the PCM as it shown in figure (6).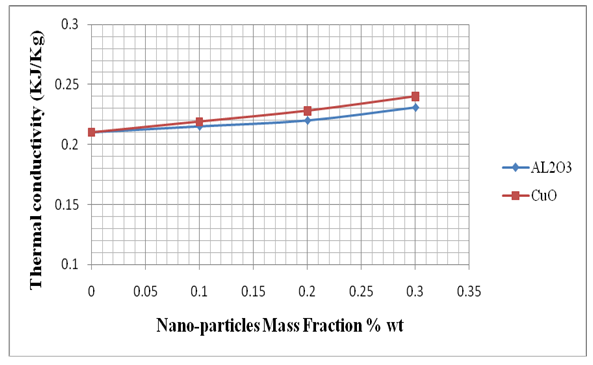 | Figure (6). Effect of adding Nano-particles on the thermal conductivity |
Figures (7- a, b and c) below is showing the results of charging process for each percent of additives which they are (0.1, 0.2 and 0.3% wt), respectively. As it noticed at these figures that the time was decreased after each time adding Nano-particles to the PCM also it’s noticed that the nPCM composite charging time will be decreased relative to the Nano-particles concentration increment in the PCM.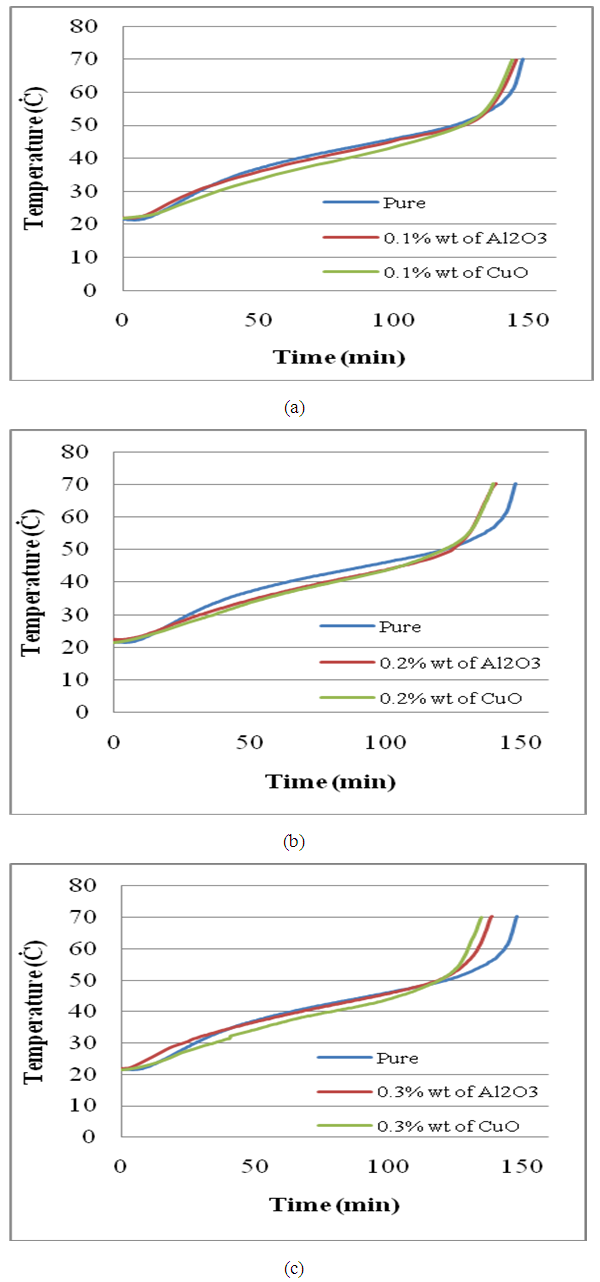 | Figure (7). Comparison for different percentages of additives (a) 0.1% wt (b) 0.2% wt (c) 0.3% wt |
6. Conclusions
These two additives having its own thermo-physical properties so as to make some differences between the pure PCM and PCM composite. The discharging process time was longer than charging process time about 4 times, because the charging process was done by water as a HTF while discharging was done by air as a HTF. The charging was faster than discharging because the water having high specific relative to the air, so that water HTF having ability to absorb and release heat from the water heater to the PCM more than air. The findings in this research according to the type of additives is explained in the following:1. Using Copper (II) oxide (CuO) Nano-particles better than Alumina (Al2O3) Nano-particles because the PCM’s thermal conductivity is showing good response after adding Copper (II) oxide.2. Adding (Al2O3) to the PCM will reduce charging time 2.1, 5, and 6.4% after adding the Nano-particles 0.1, 0.2 and 0.3% wt concentration, respectively.3. Adding (CuO) to the PCM will reduce charging time 2.7, 6.25, and 8.8% after adding the Nano-particles 0.1, 0.2 and 0.3% wt concentration, respectively.
ACKNOWLEDGEMENTS
Many thanks to the technical colleges of Baghdad to provide us with the necessary equipment and special thanks to the people who supported us to write and work in the fields.
References
[1] | Arasu, Amirtham, Agus Sasmito, and Arun Mujumdar. "Thermal performance enhancement of paraffin wax with Al2O3 and CuO nanoparticles–a numerical study." Frontiers in Heat and Mass Transfer (FHMT) 2, no. 4 (2012). |
[2] | Hanan Afif Khamis. "Solar energy storage in buildings using composite pcm containing nanoparticales." University of Jordan, MSc thesis, 2012. |
[3] | Sciacovelli, Adriano, Francesco Colella, and Vittorio Verda. "Melting of PCM in a thermal energy storage unit: Numerical investigation and effect of nanoparticle enhancement." International Journal of Energy Research 37, no. 13 (2013): 1610-1623. |
[4] | Harikrishnan, S., and S. Kalaiselvam. "Experimental investigation of solidification and melting characteristics of nanofluid as PCM for solar water heating systems." International Journal of Emerging Technology and Advanced Engineering 3 (2013): 628-635. |
[5] | Chaichan, Miqdam T., Shaimaa H. Kamel, and A. N. M. Al-Ajeely. "Thermal conductivity enhancement by using nano-material in phase change material for latent heat thermal energy storage Systems." SAUSSUREA 5, no. 6 (2015): 48-55. |
[6] | Auriemma, M., and A. Iazzetta. "Numerical Analysis of Melting of Paraffin Wax with Al2O3, ZnO and CuO Nanoparticles in Rectangular Enclosure."Indian Journal of Science and Technology 9, no. 3 (2016). |
[7] | Bugaje I.M., "Enhancing the thermal response of latent heat storage systems", international journal of energy research, vol. 21, 759-766, 1997. |
[8] | Fukai J., Hamada Y., Morozumi Y. and Miyatake O., "Effect of carbon fiber brushes on conductive heat transfer in phase change materials", international journal of heat and mass transfer, vol. 45, 4781-4792, 2002. |
[9] | Fukai J., Hamada Y., Morozumi Y. and Miyatake O., "Improvement of thermal characteristics of latent heat thermal energy storage units using carbon fiber brushes; experiments and modeling", international journal of heat and mass transfer, vol. 46, 4513-4525, 2003. |
[10] | Hamada Y. Ohtsu W. and Fukai J., "Thermal response in thermal energy storage material around heat transfer tubes; effect of additives on heat transfer rate", solar energy materials and solar cells, vol. 75, 317-328, 2003. |
[11] | Zhang Z. and X. Fang, "Study on Paraffin/Exfoliated Graphite Composite Phase Change Material", Energy Conversion and Management, Vol.47, 303-310, 2006. |
[12] | K. Mattawee and M. Assassa, "Solar energy storage using phase change materials", Renewable and Sustainable Energy Reviews, Vol.9, 1913-1965, 2007. |
[13] | Tavaranan, S., Das, A., Aurora, P., Trelles, J.P., "Design of a standalone portable solar powered thermoelectric vaccine refrigerator using phase change material as thermal backup", solar engineering program, university of massachusetts lowell, usa 2002. |
[14] | Gu Z., Liu H., Li Y., "Thermal energy recovery heat recovery system calculation and phase change material development", applied thermal engineering, vol. 24, 2411-2426, 2004. |
[15] | Sharma, S.D. And Sagara, K., "Solar cooker for evening cooking using latent heat storage material based on evacuated tube solar collector", iea, eces ia annex 17, advanced thermal energy storage through phase change materials and chemical reactions - feasibility studies and demonstration projects. 6th workshop, arvika, Sweden, 2004. |
[16] | Takakuwa S., Ishizuka M., Nakagawa S. and Takagi K., "Application of a thermal network method to thermal analysis of electronic devices using phase change materials", asme, 471-477, 2010. |