Shreeranga Bhat, Nishchith H., Akshay Kumar U. R., Ramith Raj, Naveen M. V., Jishnumohan Damodaran Nair
Department of Mechanical Engineering, St. Joseph Engineering College, Mangaluru, India
Correspondence to: Shreeranga Bhat, Department of Mechanical Engineering, St. Joseph Engineering College, Mangaluru, India.
Email: |  |
Copyright © 2017 Scientific & Academic Publishing. All Rights Reserved.
This work is licensed under the Creative Commons Attribution International License (CC BY).
http://creativecommons.org/licenses/by/4.0/

Abstract
The construction industry has a long Turn Around Time (TAT) due to human- based work environment. Further, lack of skilled labour, increase in labour cost, and technological advances are forcing rapid changes in building construction, which mainly consists of commercial infrastructure and residential building, where plastering work is must. The introduction of a new automated plastering machine can help to reduce the TAT in the construction field. The present work developed a model of a wall plastering machine. The proposed machine consists of an AC motor, gear box, wire rope mechanism, pulley, hopper-tray, guide ways, etc. The model has been fabricated considering a normal constructed brick wall, and further validated through testing in real-time environment.
Keywords:
Plastering Machine, Construction Industry, Turn Around Time
Cite this paper: Shreeranga Bhat, Nishchith H., Akshay Kumar U. R., Ramith Raj, Naveen M. V., Jishnumohan Damodaran Nair, Design and Fabrication of Wall Plastering Machine, Journal of Mechanical Engineering and Automation, Vol. 7 No. 5, 2017, pp. 159-163. doi: 10.5923/j.jmea.20170705.07.
1. Introduction
1.1. General
The construction revolution of today has made the contractors to equip their construction so as to perform the highest output with minimum construction cost. In order to have highest output, parameters like accuracy, precision, quality, and cycle time have to be optimized. This is possible either by having skilled manpower or by automating the system [1].With the constant increase in the demand of construction, contractors are forced to increase their construction and also the quality of the construction to remain in the competitive market. The construction industry in most countries amounts to 10–20% of the GNP [2], making it the largest economic employing sector. It is still labour dependent and most of the work involved is repetitive. The growth of any country is dependent on the construction industry; hence, it is of prime economic significance to many industrial sectors. Intense competition, shortage of skilled labour, and technological advances are forcing rapid changes in the construction industry, thus encouraging its automation. The construction of buildings, apartments, complex, shops, and homes are basic requirements of human being. In this construction area, plastering is necessary for decorating the wall. Plastering work or plastering refers to the construction or ornamentation done with plaster [3], such as a layer of plaster on an interior wall or plaster decorative mouldings on ceilings or walls. The tools and materials for this include trowels, floats, hammers, screeds, a hawk, scratching tools, utility knives, laths, lath nails, lime, sand, plaster of Paris, a variety of cements, and various ingredients to form colour washes.
1.2. Objective
Automation is one in every of the numerous and evolving disciplines among all technologies. Our aim is to render the plaster on the walls mechanically. This concept aims at reducing the work of a trained worker. It is possible, light-weight, cheap and easy structure scrutiny to the present machine. This innovative method keeps up with the ever-changing world of building automation. • It is used to reduce human work, especially the work of plasterers.• It is the machine, instead of handmade in construction plastering area.• Very easy and simple to operate.• It is inexpensive compare with the traditional method.• Simple structure, light weight, small cubage, and easy to operate.• Saving more than 20% raw material (cement and sand).
2. Literature Review
In general, the growth of a country is mainly dependent on the infrastructure, agriculture, and industry. Hence the constructional sector is of prime economic significance to many countries. In most countries, 10–20% of the GNP is for the construction industries [2], thereby making it one of the largest economic employment sectors. Plastering is construction or ornamentation work done with plasters or cement mortar over the walls [3]. Failing to allow the plastering to fully cure can lead to excess shrinkage and cracking after the walls have been plastered [4]. The various types of surface finish are as follows:a) Smooth finish, which can be obtained by using a wooden float, rather than a steel trowel;b) Roughcast finish is for rural or coastal areas, and is splashed on to the surface as a wet mix and left rough. The maximum size of sand and crushed stone or gravel may vary from 12.5 mm to 6.3 mm; c) Pebbledash finish is the most durable of all finishes and is generally free from effects. It gives a rough texture to the wall and is obtained by means of small pebbles or crushed stone, graded from 12.5 mm to 6.3 mm being splashed on to a fresh coat of and left exposed; and d) Textured finishes of different designs are now becoming very popular and can be obtained in a variety of ways. Special effects can be obtained by scraping the surface of the rendering with a straight edge hacksaw blade or with the edge of a steel trowel. Apart from this, commercial wall plastering machines are also available [5]. But these machines do not have self-alignment capability, which is essential for flat and smooth plastering of the wall. Also, these types of wall plastering machines are used to plaster the entire wall and cannot be used to re-plaster patches and damaged plastered walls.1. Design and Fabrication of Automatic Wall Plastering Machine Author Name: Mahesha P.K. and Sree RajendraJournal Name: IOSR Journal of Mechanical and Technology Result: This work includes applying mortar into the wall and additionally pressuring mortar with creating a surface level. The model was developed and tested successfully. With this development, two major downsides to the construction industries were reduced, namely, labor shortage and quality within construction method with less wastage. During the trials, it was noted that the machine was more productive compared with labour in relation to rendering the work, and additionally, the standard achieved was admirable.2. Automatic Plastering Machine Author Name: Arivazhagan B. Journal Name: International Journal of Advanced analysis in Physics, Communication & Instrumentation Engineering and Development.Result: Machine-driven rendering machine is exclusive and maybe one reasonably machine-driven rendering machinery is ideally appropriate for the construction/building business. Machine-driven rendering machine works with typical cement mortar that brings it to a swish, flat end with variable and adjustable thickness to suit every application. It makes rendering easier, faster, and easy compared with manual application. This concept also can additional increased by interfacing liquid crystal display & computer keyboard for creating the method while not external supply. This point and cash saving machine, keeps up with the ever dynamic world of building automation. 3. Automation and Robotics in Construction: Opportunities and ChallengesAuthor Name: S.M.S. ElattarJournal Name: Emirates Journal for Engineering Analysis Result: Robots square measure progressively concerned in construction operations to take care of extremely correct actions and to scale back venturous risks achieving improved management and safety. Machine-driven constructions are often developed to include: design, engineering, and maintenance of existing and planned structures. Several analysis works counsel extremely autonomous robotic system for the development performance. The “Sense-and-Act” could become a reality with the development of a lot of advanced robotic systems for construction applications. Efforts should be made to persuade professionals in building management to integrate AI and building automation enhance the standard of services of contemporary intelligent buildings. All new concepts for automation or robotizing on the vacant lot need to be generated by a mix of recent designs, new forms, and new materials that meet the requirements for building in a very metropolis. However, many of the problems in construction engineering cannot be absolutely addressed through improvement and computation. With intelligence activities reminiscent of generalization, analysis and decision-making for multi-objectives, there are often a higher understanding of the development engineering downside.
3. Design of Machine Components
3.1. Loads on Hopper
Plastering Width = 2ft = 0.6096mPlastering height = 6ft =1.8288mPlastering thickness = 1cm = 0.01mMortar mixing proportions:1:4 (normally)Density of wet mortar,
Plastering Volume, 
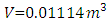
 | (1) |
Total weight on hopper including cement mixture=25KgMaximum force acting on rope is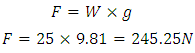 | (2) |
3.2. Rope Design
Approximate weight on hopper =25kgAxial load acting on rope=25KgSelect rope material as steel wire.Take F.O.S. for steel wire is (lifting) =3.5Nominal breaking strength of rope
Allowable Stress | (3) |
We know that,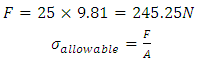 | (4) |
Where, 
Selecting diameter
mm safe for design.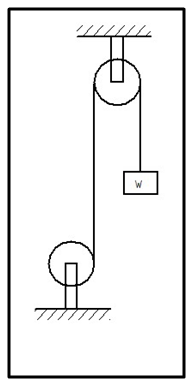 | Figure 1. Rope and Pulley Arrangement |
3.3. Gear Design
Motor used =3 phase, 0.5 HP ACMotor speed
=1330rpmPulley diameter
=25mmAnother pulley diameter
=160mm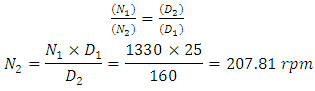 | (5) |
Then, speed
Assuming speed reduction gear box of 40:1
3.4. Design of Column
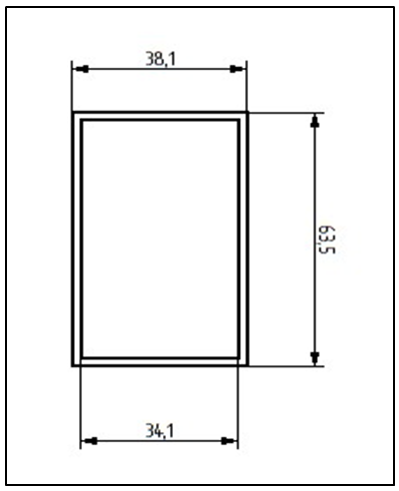 | Figure 2. Cross-section of Hollow Column |
Material used – Mild Steel
Young’s modulus =210 GpaMoment of inertia of cross-section,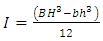 | (6) |


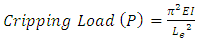 | (7) |


3.5. Chain and Sprocket Calculations
We assume, Front sprocket teeth
Rear sprocket teeth
0.5 HP 3 Phase Motor,Rated Power=0.373 KW | (8) |
We know that,Design power = Rated power × Service factor (K S) [6]The service factor (KS) is the product of various factors
and
The values of these factors are taken as follows: [Tables 14.3(B) & 14.35]Load factor
for variable load with heavy shock=1.9 Lubrication factor
for drop lubrication=1Rating factor
for 16 hours per day=1.5
From table, 08B chain number selected, [14.39(a)]
We know that pitch circle diameter of the smaller sprocket or pinion, | (9) |
Pitch circle diameter of the larger sprocket or gear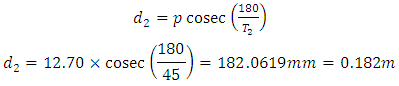 | (10) |
Pitch line velocity of the smaller sprocket,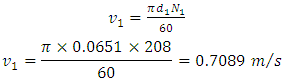 | (11) |
Therefore, | (12) |
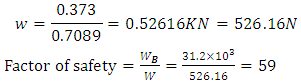 | (13) |
The minimum centre distance between the smaller and larger sprockets should be 30 to 50 times the pitch.Let us take it as 30 times the pitch.
distance between the sprockets, 
In order to accommodate the initial sag in the chain, the value of centre distance is reduced by 2 to 5 mm.
We know that the number of chain links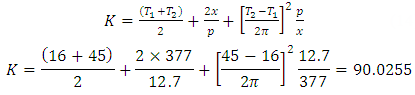 | (14) |


4. Fabrication of Machine
The structure was fabricated using required necessary components like steel frame, sheet metal, metal bars, lead screw, AC/DC motors, wheels, and nuts and bolts. All these were well- assembled for the requirement to be controlled through the control toggle switch. 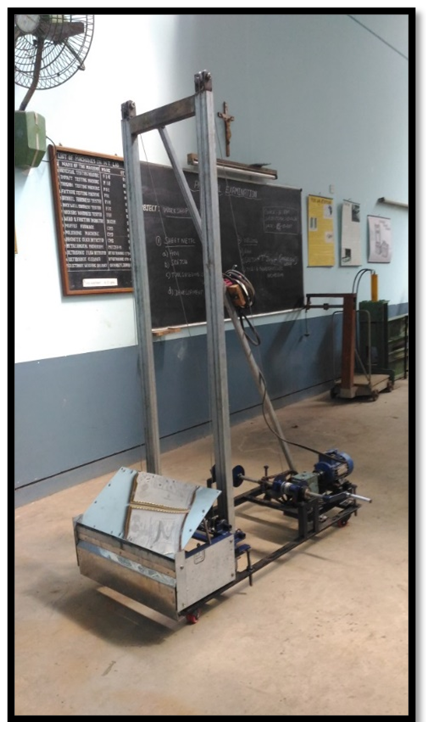 | Figure 3. Wall Plastering Machine |
5. Working of the Machine
Initially, the machine should be brought close to the wall to be plastered and positioned using hooks. Then, the mortar of cement and sand roughly in the proportion of 1:4 is poured into the hopper-tray, which is lifted by means of a rope coupled to the motor. The mortar flows downwards due to gravitational force. The wedge plate applies pressure on to the cement mixture so that the cement adheres to the wall. The clearance between the wall and machine can be adjusted as per the thickness of the plaster. When the carriage moves upward, the mortar gets applied, and the downward movement sees that the finishing of the plaster is done.
6. Advantages
The thickness of the mortar onto the wall achieved manually would vary between 0.5 to 1 inch at different wall conditions, whereas the machine can achieve any thickness constantly and uniformly. It was observed that the wastage was reduced by 0%, while increased mortar thickness increased wastage and also depended on the skill of the labour.• It is time and money saving.• It is more reliable than conventional operation.• It keeps up with the ever changing world of automation. • It increases productivity.• It saves labour and other related cost. • The working conditions, preparation, and raw objects work with are similar to manual rendering. • It is portable, and easy to operate and maintain.
7. Disadvantages
7.1. Breakdowns
All automated and electronics devices are bound to break down at one time or another. When this happens, a delay towards finishing the job can prove costly and might cause a domino effect on pending jobs. Unlike the basic plastering tools and equipments, which are usually simple one piece manual tools which when damaged can easily be replaced.
7.2. Loss of Art
It is said that manual labour enhances the expertise and attention to detail of an individual. Some people may say that plastering is more of an art, with plasterers producing magnificent works of art. Being too dependent on automated tools may deter a creative mind and cause loss of interest in the art of plastering.
8. Comparison
Table 1. Comparison between Automatic and Manual Work 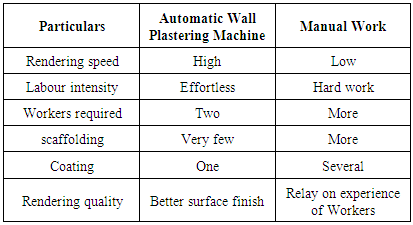 |
| |
|
9. Scope for Future Development
Loading the mortar needs to be automated. The present machine has been developed to plaster straight walls and it is suitable only for buildings, which have large walls. Hence, it requires upgrading to handle walls which are curved.
10. Conclusions
The present work includes applying mortar into the wall and also pressuring mortar to make a surface level. The model has been developed and tested successfully. With this development, two major problems currently faced by the construction industries can be reduced, namely, skilled labour shortage and quality in the construction process with less wastage. During the trials it was noted that the machine is more productive compared with labour regarding the the plastering work and also the quality achieved is almost equivalent to that of manual labour.
References
[1] | Mahesha P.K, and Sree Rajendra, Design and Fabrication of Automatic Wall Plastering Machine Prototype, IOSR Journal of Mechanical and Civil Engineering, 11(4) 2014, 1-6. |
[2] | Elattar S.M.S., Automation and robotics in construction: opportunities and challenges, Emirates Journal for Engineering Research, 13 (2) 2008, 21-26. |
[3] | Quang Ha et al., Robotic Excavation in Construction Automation, IEEE Robotics and Automation Magazine, 2002, 20-28. |
[4] | Ruchi H., Shortage of Skilled Workers: A Paradox of the Indian Economy, SKOPE Research Paper, 111 2012, 1-30. |
[5] | Ernesto G., Robotics and Automation in Construction, IEEE Robotics and Automation Magazine, 2002, 4-6. |
[6] | Khurmi R.S. and Gupta J.K., Machine Design, Eurasia Publishing House Pvt. Ltd., 2005. |
[7] | Mahadevan K. and Balaveera Reddy K., Design Data Handbook for mechanical engineering, CBS Publishers & Distributors, 2003. |