J. M. Vion, M. N. Venkatesh, P. S. Gauthami, D. N. Deepak, K. Yathish, K. G. Binu, A. Shetty, Joel D’Mello
Department of Mechanical Engineering, St Joseph Engineering College, Mangaluru, India
Correspondence to: D. N. Deepak, Department of Mechanical Engineering, St Joseph Engineering College, Mangaluru, India.
Email: |  |
Copyright © 2017 Scientific & Academic Publishing. All Rights Reserved.
This work is licensed under the Creative Commons Attribution International License (CC BY).
http://creativecommons.org/licenses/by/4.0/

Abstract
Design and fabrication of arecanut processing unit is presented in this paper. The processing unit consists of four major sub-units i.e. arecanut dehusker, boiler, dryer and sorter, which are designed and fabricated separately and then assembled in one frame. A 3-D printed dehusker peels the arecanut husk and sends peeled nut to the boiler through transfer pipes. The boiled nuts are then sent to dryer equipped with temperature and humidity sensors through rubber conveyers where steam from the boiler is used to dry the nut using a heat exchanger. Then the dried nuts are sorted according to their grades using colour detection camera. The whole unit is designed for 18 kg of raw arecanut, powered by 24 V DC battery and controlled by LabVIEW software. The whole processing unit was tested for its performance and found safe, reliable, and efficient and also reduces the processing time.
Keywords:
Arecanut processing unit, Dehusker, Arecanut dryer, Arecanut sorter
Cite this paper: J. M. Vion, M. N. Venkatesh, P. S. Gauthami, D. N. Deepak, K. Yathish, K. G. Binu, A. Shetty, Joel D’Mello, Design and Fabrication of Arecanut Processiong Unit, Journal of Mechanical Engineering and Automation, Vol. 7 No. 5, 2017, pp. 155-158. doi: 10.5923/j.jmea.20170705.06.
1. Introduction
In recent years, labour scarcity has emerged as one of the foremost challenges in farming. One crop that has been most affected by this is arecanut. Arecanut production is the largest in India according to FAO statistics and according to this, in 2013, Indian production of arecanut counts for 49.74% of the total world production. In India, Karnataka has the highest production percentage of 62.69%. However, in recent years harvesting and processing of arecanut becomes more difficult for farmers as it involves real hard, physical exertion, younger generations of labour are losing interest, with potentially harsh implication for arecanut cultivation. Researchers all around the world are working on developing arecanut processing machines, most of these machines are semi-automatic and requires human interventions [1-8]. Narasimha Bhandari invented an arecanut dehusker machine in 2001 and it was found that the outer surface of arecanut was damaged by sharp blades [9]. Later, in 2002, Vishwanath invented an automatic machine to peel arecanut but production rate was very low compared to manual peeling [10]. The dehusked nut has to be cut, boiled and dried. But no work has been done on developing a single machine which is able to do arecanut dehusking, cutting, boiling and drying. This project work emphasizes on developing an arecanut processing unit. The machine is able to peel the arecanut, cut it in to two halves, boil and dry it to desired hardness in a single pass for two different grades. The design and fabrication of arecanut processing unit was based on arecanut available in the areas of Malenadu. In this work, a safe, reliable and efficient arecanut processing machine is designed and fabricated.
2. Arecanut Processing Unit
The arecanut processing unit consist of four major units. They are, Dehusker, Boiler, Drier and sorter. The different parts of the unit are discussed below.
2.1. Arecanut Slider with Assembly
Individual arecanut is sent to the de-husking unit through the hopper. The diameter of the outlet in set to 50mmm to make sure at a time only one arecanut falls into the slider base. The slider is fabricated using 3-D printer. Above the slider base, there is a pneumatic cylinder arrangement; this cylinder is actuated through sensors and MyRIO as a controller. The piston of the cylinder moves ahead and thus pushes the arecanut from a slide into the holder.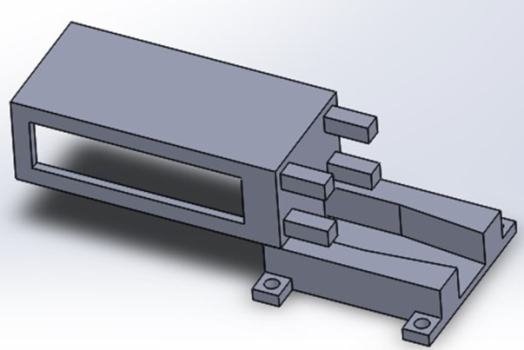 | Figure 1. Solid works model of Slider support assembly |
2.2. Arecanut Holder
The holder is designed to keep arecanut firmly in place during de-husking and easy movement in both axis as required by the system. The arecanut holder is designed in such a way that the rings around the holder will turn into 60° after the first cut for the blade to cut again and peel the husk. This is done three times. Another blade will then cut the nut into two. 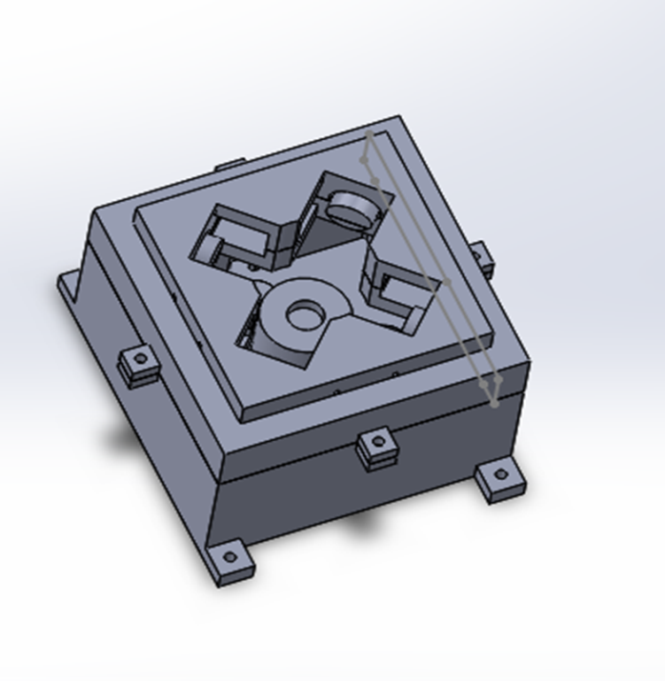 | Figure 2. Solid works model of arecanut holder |
2.3. Cutting Blade
A hardened steel blade is used to peel the areca nut. The inspiration of this blade is the scissor movement. When the areca nut moves into the holder, the blade is used to peel the areca nut. The blade moves along its frame. The blade moves, it pushes the husk apart from each other thus peeling it two ways. Then as the ring turns the holder into 60⁰, the blade moves again and peels of the husk. This is done at three times. 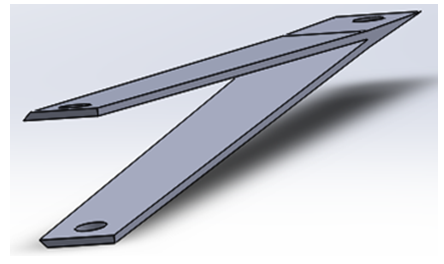 | Figure 3. Solid works model of blade |
2.4. Boiler
A hemispherical base and conical shape on top boiler is used for maximum utilisation of heat. A batch of 20 Kgs arecanut is heated for 30 minutes in this boiler. Arecanut is fed automatically form the hopper and after the process it will be fed to dryer.
2.5. Frame
The frame is made of the cuboidal section with support. This frame mainly holds the dryer, boiler and sorter of the processing unit. Frame also supports the radiator and the conveyors in the cuboidal section which will be the dryer part of the processing unit. The bottom part that will hold boiler and sorter section.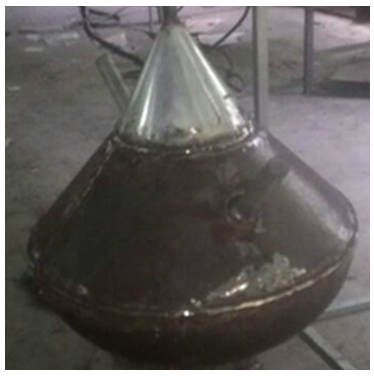 | Figure 4. Boiler |
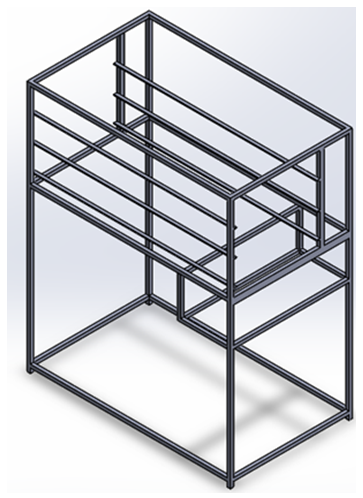 | Figure 5. Solid works model of frame which holds all other units of the processing unit |
2.6. Conveyors
Rubber conveyors are used to transfer the arecanut from boiler to sorter through drier. The conveyor is designed to hold three thousand arecanuts at a time. A servo motor is used to move the conveyors at requires speed.
2.7. Drier
Heat exchanger is used to dry the arecanut. A car radiator is placed in the drier compartment and other sides are covered with plywood. Each arecanut takes 20 minutes to move from boiler to sorter through the drier and moistures will be removed at this time.
2.8. LabVIEW Program for Sensors, Motors, Temperature and Humidity
Give below is the front end of the LabVIEW programming done for the actuating of the motors through sensors. These programs run the servo motor for the rotation of areca nut holder and a stepper motor for the movement of the slider and holder and the blade on the frame. This also includes program that actuates the temperature and humidity sensor used in dryer inlet and outlet.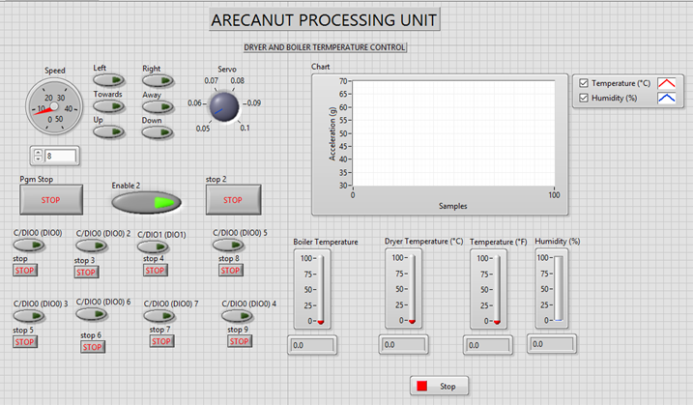 | Figure 6. Programming for the motors, temperature and humidity using LabVIEW |
2.9. Sorter
This unit performs two operations, first one is sorting of arecanut with husks and another one is sorting between the two varieties. First one where there is sorting of arecanut and arecanut husks, when the camera detects arecanut the solenoid valve is actuated and arecanut is pushed into the boiler. When the camera detects husk the conveyor moves it and arecanut is thrown out from the back end.The second one where there is sorting of the varieties when the camera detects one variety the second solenoid valve is actuated and arecanut is pushed to the first outlet. When the second variety is detected the conveyor send the nut to the second outlet. For the sorting, LabVIEW programming is used to actuate the valves and the camera used is HD Webcam.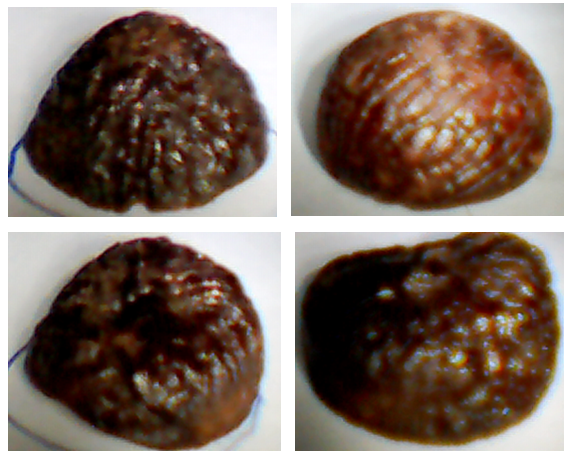 | Figure 7. Different varieties of arecanut samples used for sorting |
3. Working of Arecanut Processing Unit
All the four parts of the whole unit namely De-husker, Boiler, Dryer, and sorter are constructed separately and then assembled in one frame. Each part is connected through belts and conveyors. The main parts of the de-husker is blade that peels of the husk of the nut and holder that holds the nut in place. The hopper sends the nut to arecanut slider. Width of the hopper is to make sure that only one arecanut falls on the slider. The hopper blocking is done by part that pushes arecanut. There is a pneumatic cylinder that pushes the arecanut into the holder. Now blade moves to the arecanut and peels it off. The holder then moves by 60° and the process is repeated. This is done three times for the arecanut to be removed completely. Arecanut is held by grippers and compression springs. The springs are used to push the arecanuts as well. The slider base spring pushes the top of the holder which compresses the base springs. This, in turn, relaxes the gripper spring and the arecanut is pushed out. Once this is done the de-husking part is complete and the seeds of the arecanut are sent for boiling process. The arecanut is sent to the boiler using metal pipes. There is a sorting system, where the camera detects the nuts and sends it to the boiler. In this step, here the nut is boiled in water with the arecanut precipitate that gives the colour to the nut. Once the boiling is done, they are extracted from the boiler without the water and fed to the hopper. This hopper sends the nuts to the dryer for drying. There are three conveyors for equal distribution of all the nuts. At a time through the hopper one line of arecanut falls onto the conveyor, this is moving, thus filling all the arecanut. Here heat exchangers are used and the steam from the boiler used to dry the arecanuts. There are temperature and humidity sensors to make sure that the nuts are drying properly. Once the arecanuts are dried they are sent to the next hopper for sorting. Here, the hopper sends the nuts one by one. The camera detects the nut. The image from the nut is sent to myRIO where the program for colour sorting is coded. This unit detects the grade of the arecanut. If it is the first grade of the arecanut then a solenoid valve is actuated and this pushes the nuts into the first outlet. If the second grade is detected, then the conveyor moves and sends the arecanut to the second outlet. Thus, the nuts are sorting according to the grade of the arecanuts.
4. Results and Conclusions
The design and fabrication of arecanut processing unit is done for 20 Kgs and complete processing time is 8 hrs. The whole unit is powered by 12V DC battery. The unit tested for its performance and found safe, reliable, and efficient and also reduces the human effort. After testing the machine it has been found that,• The design of the dehusker is efficient and desired output has been found. • The cutter, boiler and sorter were working according to the requirement. The design of the drier is efficient and takes less time for the process. • The machine is portable and can be moved to any place and also no skilled labour is required to operate the machine.
ACKNOWLEDGEMENTS
The authors would like to acknowledge the Management, the Principal, and Head of the department, Department of Mechanical Engineering, St Joseph Engineering College, Mangaluru for their support to carry out the project work.
References
[1] | R. Gunaseelan, S. Shanthi, R. Sowmya, and M. Datta, “Areca nut use among rural residents of Sriperambudur Taluk: A qualitative study”, Indian Journal of Dental Re-search, vol. 18, pp. 11-14, 2007. |
[2] | Development of e-courses for B.Sc (Agriculture) by NAIP. |
[3] | Jaysekhars, “Arecanut and Cocoa Production and Marketing Aspects”, 2013. |
[4] | M. Balasubramanian, and J. S. Panwar, “Mechanical properties of arecanut (Areca catechu linn) as related to dehusking”, Journal of Agricultural Engineering (ISAE), pp. 82–88, 1986. |
[5] | B. Baboo, “A device for dehusking arecanut”, Journal of Agricultural Engineering (ISAE), pp. 63–65, 1981. |
[6] | B. Jarimopas, and S. Niamhom, “Development of Dry Betel Nut Fruit shelling Machine”, Kasetsart University Research and Development Institute, Kasetsart University, Bangkok, pp. 46, 2004. |
[7] | S. Niamhom, B. Jarimopas, and A. Sukcharoen, “Testing of the improved betel nut shelling machine”, Proceeding of the International Conference on Agricultural, Food and Biological Engineering & Post Harvest/Production Technology, pp. 21–24, 2007. |
[8] | S. Aaron Hegde, and D. John, “Arecanut farming in southern India: A case study”, International Journal of business and social science, vol. 5, pp. 10, 2014. |
[9] | B. Narasimha, “Arecanut dehusker”, National Grassroot Innovation, 2001. |
[10] | Vishwanath, “Automatic Arecanut Peeler”, V-Tech Engineers, 2006. |