Neil Vaz, Binu K. G., Pruthivi Serrao, Hemanth M. P., Jeffin Jacob, Nirmal Roy, Eric Dias
Department Mechanical Engineering, St Joseph Engineering College, Mangaluru, India (Affiliated to VTU)
Correspondence to: Neil Vaz, Department Mechanical Engineering, St Joseph Engineering College, Mangaluru, India (Affiliated to VTU).
Email: |  |
Copyright © 2017 Scientific & Academic Publishing. All Rights Reserved.
This work is licensed under the Creative Commons Attribution International License (CC BY).
http://creativecommons.org/licenses/by/4.0/

Abstract
Variations in frictional force developed in the journal bearing lubricated with Magnetorheological (MR) fluid was investigated. Also, a comparative study was conducted between MR fluids and SAE15W40 grade engine oil on the performance characteristics. A test bearing set-up was developed to accommodate MR fluid film with provision for varying magnetic field. MR Fluid was formulated by dispersing electrolytic grade micron sized iron particles in silicon oil base fluid in 0.3 volume fraction. The results of the experimental testing indicated an increase in frictional force with increasing excitation current in the electromagnetic cores of journal bearing for similar loads and speeds in comparison to plain engine oil; the presence of MR fluid causes an increase in viscosity in comparison to plain engine oil and thus holds a great potential to increase the load carrying capacity of the journal bearing.
Keywords:
Journal bearings, Magnetorheological fluids (MRFs), Hydrodynamic lubrication
Cite this paper: Neil Vaz, Binu K. G., Pruthivi Serrao, Hemanth M. P., Jeffin Jacob, Nirmal Roy, Eric Dias, Experimental Investigation of Frictional Force in a Hydrodynamic Journal Bearing Lubricated with Magnetorheological Fluid, Journal of Mechanical Engineering and Automation, Vol. 7 No. 5, 2017, pp. 131-134. doi: 10.5923/j.jmea.20170705.01.
1. Introduction
In rotating machinery, the dynamic stiffness and damping of the structure which supports the rotating shaft has a significant effect on the machine vibration. In particular it affects the machine critical speeds, the vibration in between critical speeds and the forces. In rotating machinery, the dynamic stiffness and damping of the structure which supports the rotating shaft has a significant effect on the machine vibration. In particular it affects the machine critical speeds, the vibration in between critical speeds and the forces voltage rapidly transforms these fluids from Newtonian to pseudo-plastic materials with higher apparent viscosity. The phenomenon of electro-rheology was first reported by Winslow and occasionally bears his name, i.e. Winslow effect. It appears as an increased resistance in flow, and in some cases, the fluid converts itself to a solid when an increase of the electric field takes place.Magnetorheological fluid (MRF) is a manageable fluid that exhibits drastic changes in rheological properties which is adjustable and interchangeable to the applied magnetic field strength. The MRFs behave like the normal fluids having normal viscosity in the absence of an external magnetic field, but in the presence of a strong magnetic field it solidifies immediately to a grease state. Hence, the fluid is potentially advantageous to be employed as a replacement to conventional journal bearings particularly for high speed applications.Controllable bearings using smart fluidsAnother category of controllable bearings seeks to incorporate “active” or “smart” fluids into bearing applications to introduce “smart” behavior. These smart fluids usually exhibit field dependent properties that could be altered by external physical fields. Typical kinds of these materials used in fluid film bearings are the electrorheological and magnetorheological fluids (ERF & MRF). Typical structures of these two fluids are similar, ingredients of both including one carrier fluid and active particles that react to external electric or magnetic fields. The external field (electric or magnetic) will induce the so-called yield stress [1, 2] in the fluid, increasing the apparent viscosities of the fluids, which will then alter the behaviour of the bearings. Hesselbach and Guldbakke [3, 4] firstly applied the MRF into hydrostatic bearings. Using MRF as lubricant, their hydrostatic thrust bearing maintained a constant bearing gap under different payloads. And quicker response to the change of payloads was also observed in the bearing with MRF than with conventional valve based systems. Based on the experimental results, they concluded that in closed loop control, the bearing would achieve quasi- infinite stiffness. The MRF is categorized as a non-Newtonian fluid, or rather, the Bingham fluid, which behaves like a rigid solid at low stresses but flows like a viscous fluid at high stress. In hydrodynamic lubrication, therefore, the Bingham model is generally used to describe the lubricating behavior of the MRF. Wada et al. [5] and Tichy [6] incorporated the Bingham model into fluid momentum equations to describe the core formation in the oil film of Bingham fluids. Urreta et al. [7] tested a journal bearing lubricated with MRF or ferrofluid, concluding that the MRF is more suitable in journal bearing control than the ferrofluid. In the application of MRF, a phenomenon called shear-thinning effect has been observed by researchers [8, 9]. When external magnetic field is applied, microstructure of the MRF would change, i.e. randomly distributed particles would form chains and pillars. This is basically the mechanism of the smart behavior of the MRF. When boundary shear is high, however, these chain and pillar structure will break and performance of the MRF is then reduced. In the hydrodynamic bearing, since surface speed of the rotor is high and clearance between the rotor surface and bearing inner surface is small, shear rate in the lubricant film this effect is the main issue to be considered when applying MRF to bearings as lubricant.
2. Experimental Setup
The experimental setup consists of bearing assembly with winding, shaft, two plummer blocks, frame, loading system.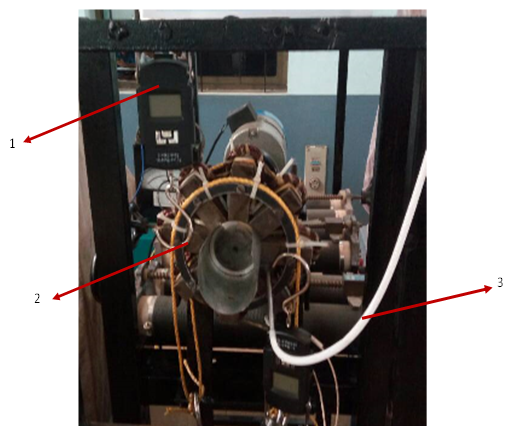 | Figure 1. Bearing assembly in the rig |
Figure 1 represents the bearing assembly in the rig ,which consists of bearing and core assembly (2), digital weighing scale (1) to measure the frictional force acting during the operation, oil inlet feed pipe (3) to feed the lubricate into the bearing and there is also provision made to collect the lubricant from the bearing using sheet metal. In order to energize the MR fluid the current flowing through the coils has to be varied. Figure 2 shows the bearing assembly with rheostat used to control the current. (1) motor, (2) bearing assembly, (3) frame, (4) weighing pan, (5) speed regulator, (6) ammeter with range 0-30A, (7) rheostat (10 Ω).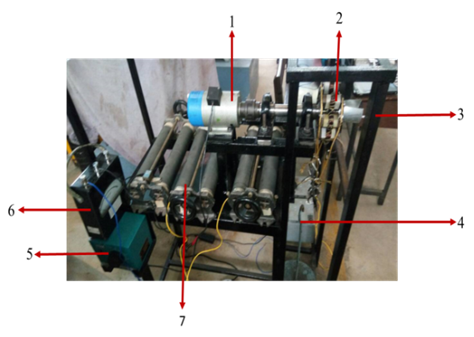 | Figure 2. Bearing assembly with rheostat and ammeter |
3. Results and Discussions
The frictional force measurement was done using the apparatus for both engine oil (15W40) and MR fluid. Table 1 indicates the variation of frictional force at different speeds using engine oil as the lubricant.Table 1. Variation of friction force for different speeds with SAE 15W40 engine oil 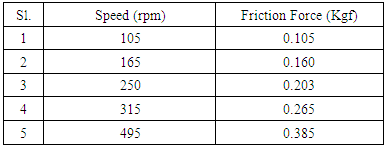 |
| |
|
From the above table, it can be seen that the frictional force generated by rotation of the shaft increases with increase in speed of the shaft. Table 2 indicates the variation of frictional force in the bearing using MR fluid as the lubricant, at different speeds.Table 2. Variation of friction force for different speeds with MR fluid as lubricant 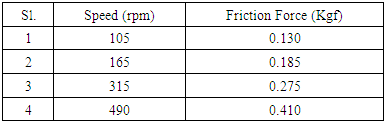 |
| |
|
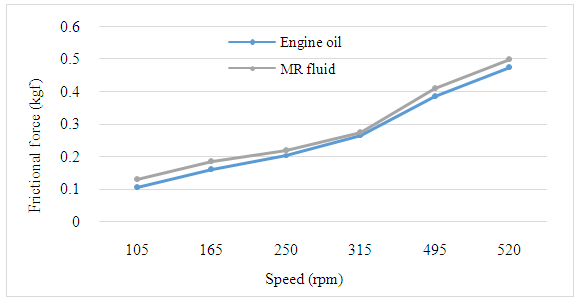 | Figure 3. Comparison of the variation of frictional force using MR fluid and Engine oil |
The influence of volume concentration of ferromagnetic particles in lubricants without the application of current can be seen in Figure 3. It shows that increase in viscosity of the lubricant by addition of ferromagnetic particles has a profound effect on the friction force developed at the surface of the bearing.
3.1. Magnetization Effect
The magnetization effect on the friction force was studied for volume fraction 0.3. Table 3 shows the variation of frictional force for different speeds of shaft with variation of current in the coils. The frictional force generated at the bearing increases with increase in the value of current. As the speed of the shaft increase the frictional force also increase.Table 3. Variation of frictional force in the bearing using MR fluid as the lubricant by varying the current 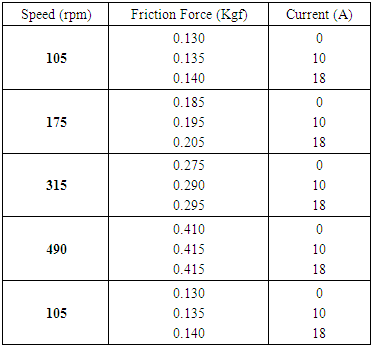 |
| |
|
Table 4 represents the comparison of the frictional force in case of engine oil and MR fluid at 490 rpm and with the application of 10A. It was observed that the friction force was increased by 6.5%, showing that the shear force between the layers has been increased due to the presence of magnetic particles in the lubricant.Table 4. Comparison of the frictional force in case of engine oil and MR fluid at 490 rpm and with the application of 10A  |
| |
|
Figure 4 shows the variation of frictional force with respect to speed when MR fluid is used as the lubricant. From the Fig. 4, it can be clearly seen that when the current increases the frictional forces generated for varying speeds increases marginally. It is also observed that the effect of friction force on the bearing at higher speeds is negligible.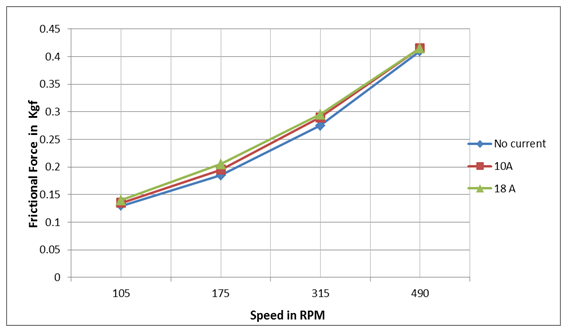 | Figure 4. Variation of frictional force for different speeds and different currents with MR fluids |
4. Conclusions
The following conclusions were derived from the study:1. The results of the experimental testing indicated that, an increase in frictional force of journal bearing for similar loads and speeds in comparison to plain engine oil. 2. The frictional force was also observed to increase with excitation current in the electromagnetic cores. 3. Frictional force in a journal bearing is manifested due to the shearing stress within the hydrodynamic lubricant film. The shear stress is developed due to the viscous shear of the film. It is therefore, concluded that, the presence of MR fluids causes an increase in viscosity in comparison to plain engine oil. 4. The load bearing capacity of journal bearing being a function of viscosity of lubricant, it is concluded that addition of MR fluid holds potential to increase the load carrying capacity of the journal bearing.5. The feasibility of using MR Fluid as lubricant is proved in this project. Issues related to blockage of lubricant supply due to magnetic field were overcome.
References
[1] | Stanway R, Sproston JL, El-Wahed a K. Applications of electro-rheological fluids in vibration control: a survey. Smart Mater Struct 1999; 5: 464–82. |
[2] | Bossis G, Lacis S, Meunier a, Volkova O. Magnetorheological fluids. J Magn Magn Mater 2002; 252: 224–8. |
[3] | Hesselbach J, Abel-Keilhack C. Active hydrostatic bearing with magnetorheological fluid. J Appl Phys 2003; 93: 8441–3. |
[4] | Guldbakke JM, Hesselbach J. Development of bearings and a damper based on magnetically controllable fluids. J Phys Condens Matter 2006; 18: S2959–72. |
[5] | Wada S, Hayashi H, Haga K. Behavior of a Bingham solid in hydrodynamic lubrication. BullJSME 1973; 16: 422–31. |
[6] | Tichy J. Hydrodynamic lubrication theory for the Bingham plastic flow model. J Rheol (N Y) 1991; 35: 477–96. |
[7] | Urreta H, Leicht Z, Sanchez A, Agirre A, Kuzhir P, Magnac G, et al. Hydrodynamic Bearing Lubricated with Magnetic Fluids. J Intell Mater Syst Struct 2010; 21: 1491–9. |
[8] | Becnel AC, Hu W, Wereley NM. Measurement of Magnetorheological Fluid Properties at Shear Rates of up to 25000s-1. IEEE Trans Magn 2012; 48: 3525–8. |
[9] | See H. Field dependence of the response of a magnetorheological suspension under steady shear flow and squeezing flow. Rheol Acta 2003; 42: 86–92. |