Noel Deepak Shiri, Joshua Fernandes, Gilson Fernandes, Glen Pinto, Brendan Gonsalves, Deekshitha
Department of Mechanical Engineering, St. Joseph Engineering College, Mangaluru, India
Correspondence to: Noel Deepak Shiri, Department of Mechanical Engineering, St. Joseph Engineering College, Mangaluru, India.
Email: |  |
Copyright © 2017 Scientific & Academic Publishing. All Rights Reserved.
This work is licensed under the Creative Commons Attribution International License (CC BY).
http://creativecommons.org/licenses/by/4.0/

Abstract
The prime objective of this work is to develop an efficient method to convert low value plastic wastes i.e. Commingled Waste Plastics into useable plastic lumber as a product, and to realize the concept of Upcycling, where the transformation of old mixed waste plastic materials into a useable plastic lumber product of higher quality or value greater than the original raw material is achieved. A big percentage of waste plastic comes in the form of soft plastics, which are the neglected section of waste plastics in general. Plastic packaging such as food wrappers, packets, carry bags and other packaging made from PE, PP, PS, multilayered plastics and laminates etc. are not being regularly recycled due to its low market value. The processing method selected for manufacturing the plastic lumber is “Two-stage extrusion–injection molding”. In this method, the cleaned and shredded low value commingled waste plastics is first melted using a plastic extruder and transferred into a separate accumulation chamber for injection into rectangular shaped moulds and the plastic lumber is obtained. The properties of plastic lumber are close to that of wood in terms of mechanical properties. The plastic lumber produced using this machine can be used for outdoor furniture, walkways, decking application etc. The Extrusion – Injection Molding Machine developed is used to manufacture plastic lumber along with the Waste Plastic Washing and Shredding Machine in a waste processing facility.
Keywords:
Commingled (Mixed) Waste Plastics, Plastic Extrusion, Plastic Injection Moulding, Plastic Lumber, Upcycling, Recycling
Cite this paper: Noel Deepak Shiri, Joshua Fernandes, Gilson Fernandes, Glen Pinto, Brendan Gonsalves, Deekshitha, Development of a Two-stage Extruder-Injection Molding Machine for Manufacturing of Plastic Lumber Using Commingled Waste Plastics, Journal of Mechanical Engineering and Automation, Vol. 7 No. 4, 2017, pp. 124-129. doi: 10.5923/j.jmea.20170704.08.
1. Introduction
Plastics have become a major waste component in today's scenario as there is a lot of plastic waste produced by industries, households and by every human being on an everyday scale. Plastic products have become an integral part of our daily life. It is produced on a massive scale worldwide and its production crosses 150 million tonnes per year globally [1]. In India, approximately 8 Million tonnes of plastic products are consumed every year according to 2008 survey [1]. Its broad range of applications are in films, wrapping materials, shopping bags and garbage bags, fluid containers, clothing, toys, household and industrial products, and building materials. It is a fact that plastics will never degrade and remains on landscape for years to come. The recycling of a virgin plastic material can be done 2-3 times only, because after every recycling, the plastic material is deteriorated due to thermal pressure [1]. Disposal of plastic waste can be done by biodegradation, pyrolysis, incineration, sanitary landfill and recycling. Among them Recycling is the only method which permits the conservation of raw materials and at the same time provide an opportunity for commercial profit [2]. The conventional forms of recycling are not applicable to mixed plastic waste; that is, plastic waste containing more than one polymer; nor are they applicable to heavily contaminated waste. The equipment used for the recycling of homogeneous scrap is basically similar to normal plastic processing equipment and is unsuitable for the homogenization of mixtures of polymers. It is also unsuitable for handling large amounts of contamination unless the material is first cleaned. The recycling of mixed plastics waste involves the homogenization of the various polymers, the dispersion in the plastics mass of the contaminants (i.e., non-thermoplastic materials), and the conversion of the mass directly into products which do not resemble the products from which the waste arose. The types of recycling machines at present on the market is limited to five types: The Reverser, designed by Mitsubishi Petrochemical Co. in Japan; the Remaker, built by Kleindienst in Germany; the Flita, designed by Flita GmbH in Germany, the Klobbie, built by Rehsif S.A. in Belgium, and a machine built by Fabrique Nationale Herstal in Belgium. All five machines are different from each other in the means employed to homogenize the mixture of polymers [3]. Recycling of mixed wastes is difficult for technical and commercial reasons: (1) Each component has a different melting behaviour, rheology and thermal stability. At a given processing temperature some components may be melted, others remain solid, and others still decompose thermally. (2) Polymer mixtures are generally mutually insoluble, even after thorough mixing they still consist of discrete phases, dispersed in a continuous phase. Unless there is sufficient adherence between the different phases, the mechanical properties of such a mixture are quite poor [4].The manufacture of flow moulded linear profiles, or plastic lumber as it is commonly referred to, has received a great deal of attention as a solution to using mixed plastics waste because minimal separation of the mixed plastic is necessary to produce this type of product. It is viewed as a method to utilize plastic containers and films altogether which could not otherwise be collected in significant quantity to justify separation. Although the manufacture of plastic lumber from mixed plastics without separation has large potential as a solution to mixed plastics in general and along with associated problems. It may also be necessary to separate plastics to obtain a desired colour or appearance of the finished lumber product, or to attain a product with reasonable quality standards. While dark brown, black and gray colors are possible with mixed plastic wastes, lighter colors such as blue, yellow and light gray are not possible without using separated clear and white HDPE/LDPE [5]. Plastic Lumber offers superior resistance to degradation and weathering in outdoors application. In general, there are transportation, industrial, marine and agricultural applications for plastic lumber products. Materials that can be used to develop Plastic Lumbers are LDPE, LLDPE, HDPE, PP, PVC, PS, PET, ABS, Nylon etc [5].Batch processing of plastic lumber is a relatively simple operation, but it takes time to complete a cycle. The plastic is first extruded into the moulds. Chilled cooling water is circulated round the jacket of the mould until the plastic has solidified. The mould is opened, the post removed and the cycle is repeated. Fillers, chemicals and pigments can all be added at the point where the shredded plastic or pre-prepared pellets are fed into the extruder. Fillers significantly alter the engineering properties of the resultant material, but can extend the costlier plastic over a greater number of products [6]. The addition of chemicals such as plasticisers, compatiblisers, stabilisers, UV blockers and fire retardants all add cost to what may well be a low value final product. Pigments also add cost so their use should be minimised. Fillers can be used to extend or alter the characteristics of any plastic. Their use with mixed plastic waste to produce plastic lumber has proven popular in the USA [6]. The unusable plastic can be used to bond the filler and un-melted shredded plastics. Since there may be no chemical bonding between the plastic and filler, the mix may resemble the honeycomb created by blowing agents, but with filler in the spaces rather than gas. Fillers are usually in the form of “flour” or finely ground material such as talc, calcium carbonate, fibreglass, mica and wood flour. Large particles are likely to reduce the strength of the mix if there is no bond between filler and the polymer used [6].Using a waste plastic extruder, a method for effectively converting waste plastics into building materials like bricks and interlocks have been studied and the plastic brick obtained was shown to have a compressive strength twice that of a traditional clay brick [7]. The maximum compressive load sustained by the polypropylene-rubber composite brick was found to be 17.06 tons whereas a clay brick sustained only 9.03 tons. Bricks made from waste plastic sustain a higher load and compressive strength compared to normal clay brick [7]. Study has been performed to optimize the waste plastic-rubber composite materials using the Taguchi’s Design of Experiment Methodology [8]. Moreover, an investigation has been carried to find out the effect of various parameters such as waste plastic mix, rubber powder, and filler materials (calcium carbonate and fly ash) on the compressive strength of the developed material [8]. The study was performed to reutilize the waste plastics into developing plastic-rubber composite materials. It is evident from the results that all the selected parameters like waste plastic, rubber powder, fly ash and calcium carbonate are having significant effect on the compressive strength of the material under study. Experimental results of compressive strength for optimum values of waste plastic-rubber composite material in comparison with clay brick revealed that it is 3 times stronger than the normal clay brick [8].
2. Design Procedure and Machine Parts
The design of the extruder-injection molding machine consists of the following:a) Maximum volume of the melt plastic needed to fill the mould to produce Plastic Lumber considering the shrinkage. This involves dimensions of the mould like length, breadth, height, solid density (ρs) and melt density (ρm) of the plastic material and melt mass (m) to be filled inside the mould etc;b) Design of Extruder screw and Extruder barrel, which involves the length of the screw conveyor (L), diameter of the barrel (D), pitch of the screw (p), helix angle (Φ), L/D Ratio of the Screw and Barrel.c) Torque and power calculations for running the Hydraulic Pump to operate the hydraulic components of the machinery.d) Volume of hydraulic oil to be filled inside hydraulic piston cylinder to achieve forward stroke and return stroke. e) Power calculations for Hydromotor.f) Volume of Hopper and mass of plastic that can be contained inside the hopper. While the machine setup has the following units:1) The Extruder unit comprises of the barrel, screw, hopper, ceramic band heaters, J Type Thermocouples, cooling water jacket, bearing housing, gear coupling, hydromotor, Extruder barrel-Injection barrel connector tube and insulation ceramic blanket etc.2) The Injection Unit consists of Accumulation chamber / Injection Barrel, plunger with plunger rod and hydraulic cylinder for injecting plastic, Injection Nozzle, tie bars and support platens along with base supports. 3) The Toggle joint consists of hydraulic cylinder, toggle mechanisms, mounting table, tie bars etc.4) The electrical digital temperature control panel comprises of digital temperature controller panel, Ammeters, contactors and toggle switches etc.5) The Hydraulic control panel consists of Hydraulic cylinders and hydromotor control switches, On/Off indicators and emergency control switches, Voltmeters, Motor starter, contactors and toggle switches etc. 6) Hydraulic unit consists of Hydraulic oil tank, Hydraulic gear pump, oil filters, hydromotor, gear couplings, two hydraulic cylinders, hydraulic hose and tubing, hydraulic control solenoid valves, flow control valves, pressure relief valve, pressure gauge, couplings etc.
3. Objective and Working Method
The main objective of this work was to develop a waste plastic processing two-stage extruder-injection moulding machine for processing of commingled waste plastics into plastic lumber. The target size of the Plastic Lumber to be manufactured with this machine is 100mm × 30mm × 1200mm. This machine has basically two stages, Extruder-Injection moulding system wherein the hopper conveys the cleaned and shredded commingled waste plastics into the extruder. Inside the extruder screw the melting and blending of the plastics takes place. From the extruder, the molten plastic is conveyed to the accumulating chamber. This chamber consists of a plunger which is powered by means of hydraulic piston cylinder and hydraulic power pack and facilitates in the injection of the plastic melt into the mould. The mould is kept in the mould table and with the help of toggle mechanism the mould is pushed into the injection nozzle and the molten plastic is injected into the mould to produce the Plastic lumber of the required size. This machine can effectively process waste plastics coming from used thin film bags, Packaging plastics, Post consumer film plastics, Agricultural films etc. The block diagram of the process inside the Extruder-Injection moulding machine is shown in figure 1.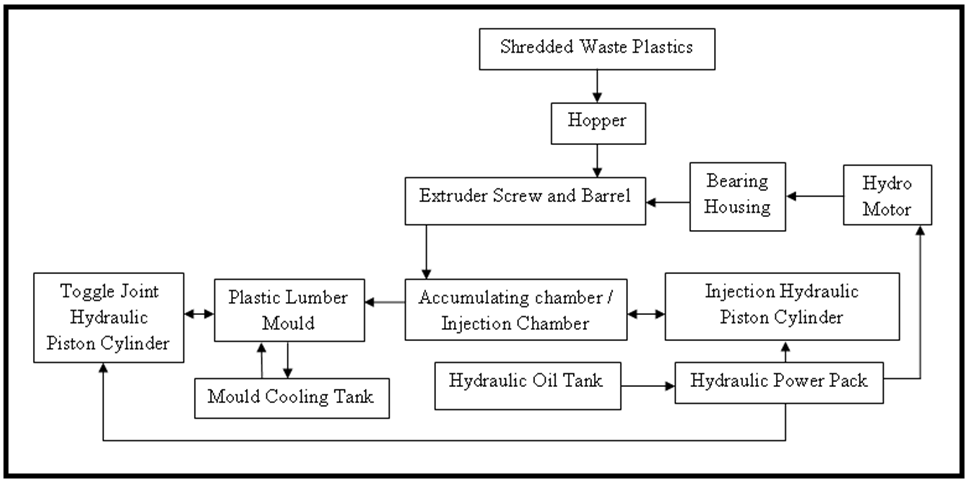 | Figure 1. Block diagram of the process inside the Extruder-Injection molding machine |
3.1. Working Method
Shredded and cleaned soft plastics like LDPE, LLDPE, PP, PVC and multilayered plastics and laminates is fed into the hopper. The extruder screw rotates at a lower speed of around 80 rpm. The extruder screw rotates and conveys the melted plastic material with the compression ratio (C.R) of 1.8:1 from the one end of the screw to the other end by mixing all the different types of plastics and blending them together inside the screw and the mixer part of the screw which is in the front portion of the screw is used to obtain uniformly blended plastic material as output at the front of barrel. The screw is powered by a constant pressure motor (hydro motor) where the motor speed can be altered by controlling the flow of the hydraulic fluid into the motor with maintaining constant pressure. The temperature maintained in the three heating zones in the extruder to achieve the melting of wide variety mixed plastics is 180°C at the first zone (hopper end or feed zone), 200°C at the second zone (transition zone) and 220°C at the third zone (metering zone). The material is further conveyed through a connecting tube to the accumulating chamber. The Accumulating Chamber / Injection Barrel is the fourth zone (nozzle end) and it is maintained at a temperature of 250°C to facilitate the injection of the uniformly blended plastic material into the mould to develop the Plastic Lumber. Once the molten plastic material is filled completely into the accumulating chamber using the help of plastic extruder, the plastic material is then continuously pressurized using the plunger inside the Injection barrel using the hydraulic cylinder to increase the pressure of the plastic melt while injecting the plastic into the mould. This method reduces the problems of shrinkage and other defects which can develop inside the plastic lumber which is the final product to be produced from the developed moulds. The diagram of Two-stage Extruder-Injection moulding machine is shown in figure 2. As the whole system is being powered by means of hydraulic system by using a three way single power pack, it is easy to control the overall system which consists of Hydromotor to rotate the extruder screw, Injection hydraulic cylinder to inject plastic into mould and the Toggle mechanism operating hydraulic cylinder to clamp the mould into the nozzle etc, the whole system consumes less power by using the single power source and is highly capable of doing multiple operations using the hydraulics. The screw is designed to give minimum throughput of 60kg/hr. To achieve this the screw of 18:1 length to diameter ratio (L/D Ratio) is selected with the inner diameter of 77 mm and flighted length of screw is 1300mm. For the smooth flow of molten plastic inside the screw a square pitch of 17.66° helix angle is selected with a pitch of 60mm. The total length of the screw is divided into three sections namely feed section, compression section, and metering section with a compression ratio of 1.8:1. The Hydraulic control panel and temperature control panel is placed on two separate panels and it is easy and efficient for a single person to operate the overall system. Figure 3 shows the photograph of the final assembled Two-stage Extruder-Injection molding machine. The Plastic lumber is developed with mixed Waste Plastics, Rubber Powder and with filler materials like Fly Ash and Calcium Carbonate. Once the moulds are filled with plastic and reinforcement materials, for the efficient and faster cooling the moulds are lifted from the table and completely immersed into the cooling water tank using the compound pulley system for the plastic lumber to be cooled at a rapid rate to reduce the shrinkage defect in the final product. 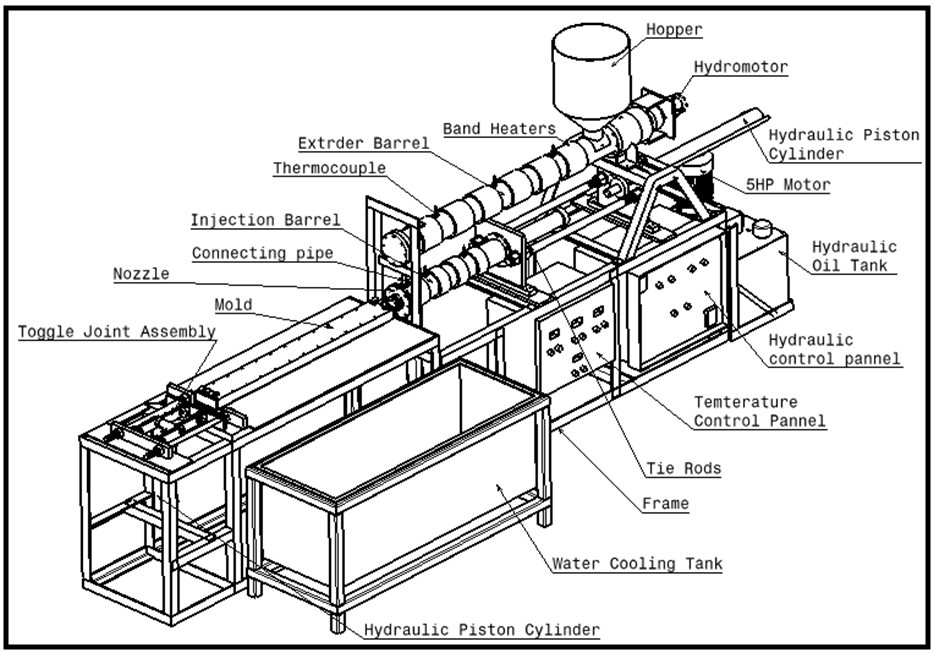 | Figure 2. Diagram of Two-stage Extruder-Injection molding machine |
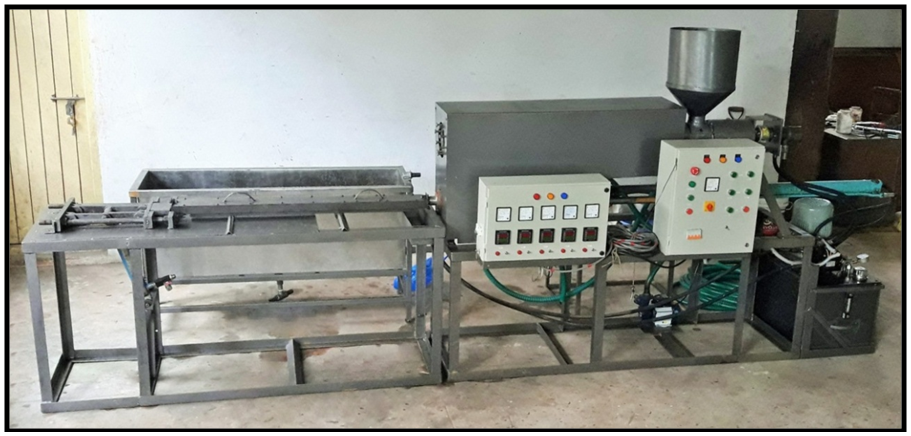 | Figure 3. Photograph of the final assembled Two-stage Extruder-Injection molding machine |
3.2. Applications of this Machine and the Variety of Plastic Lumber Products that can be Developed Using this Machine
1) This machine helps in upcycling the waste plastics into a new type of a product like Plastic lumber which can be used for outdoor application.2) Wide variety of mixed waste plastic materials can be effectively processed in this machine. Effective recycling of soft plastics like LDPE, LLDPE, HDPE PP, PS, multilayered plastics and laminates which helps in curbing pollution and reducing landfills.3) The Plastic lumber is an effective replacement for Wood and metal in many applications.4) This machine can be used to manufacture plastic lumber products like public benches, park benches, tables, public walkways, outdoor furniture, park walkways, decking application and plastic furniture, planks, profiles, railway sleepers, fence posts, pilings, pallets, drainage gutters and street furniture etc. 5) Plastic lumber products can be used in other applications like Protective Posts, Guardrail Offset Blocks, Guardrail Posts, Sign Blanks, Sign Supports, Sign poles, Barricades, Flexible Posts, Barriers etc.6) The Upcycled plastic lumber products has the following important attributes like the material is water proof, durable, having good insulation properties and not vulnerable to insect infestation and it does not decompose and has Low Carbon Footprint while manufacturing the material and the plastic lumber material is 100% recyclable. 7) The plastic lumber product can also be assembled with other materials like metals and wood with the help of nails, screws, nuts and bolts etc.
4. Conclusions
In the extrusion-injection molding machine, the shredded waste plastic is first melted using a plastic extruder and transferred into a separate accumulation chamber for injection into rectangular shaped moulds and the plastic plumber is obtained after cooling the moulds in cooling tank. The properties of plastic lumber is close to that of wood in terms of mechanical properties. The plastic lumber which is the end product produced using this machine can be used for wide range of useful applications like outdoor furniture, park walkways, decking application, public benches and plastic furniture to mention a few. It can play a significant role in efficient management of waste plastics namely soft plastics which are less recycled as compared to hard plastics. The Extrusion – Injection molding machine developed is to be used along with the Waste Plastic Washing and Shredding Machine for use in waste processing facility named "Eco Hub" under the “The Eco Gram Project” of T.A.I.C.T in Bengaluru.
Funding Organization
We are extremely grateful to Ms Myriam Shankar Krafft, Trustee, The Anonymous Indian Charitable Trust (T.A.I.C.T), Bengaluru and Co-founder of Solid Waste Management Round Table (S.W.M.R.T), Bengaluru and Mr Wolfram Thurm, Product Designer, Bauhaus University in Weimar, Dresden, Germany for providing the necessary financial support for developing this machine for the benefit of society in dealing with problems of waste plastics.
ACKNOWLEDGEMENTS
The authors are exceptionally thankful to Mr Robinson Furtado for his invaluable suggestions and comments that gave us direction for the successful completion of this work. We thank Mr P. Varun Kajava, Mr Ranjan H. V, Mr Nikhil Lloyd Pais, Mr Vikhyat M. Naik, alumni of St Joseph Engineering College, Mangaluru for developing an award winning Waste Plastic Extruder which was the foundation for this work. Sincere thanks to Mr Jayakara Shettigar, C.E.O, and Mr Gurucharan Shettigar, C.O.O, and Mr Ashok Devadiga, Technical Manager, from Gurucharan Industries, Baikampady Industrial Area, Mangaluru for the useful interactions and for helping with the fabrication of many key machinery components. We would like to express our gratitude to Chrisage Engineering Company, Baikampady Industrial Area, Mangaluru for helping with the fabrication and completion of the machine. We appreciate the staff of Hebich Technical Training Institute, Balmatta, Mangaluru for developing the machine components. We are indebted to the Management of St. Joseph Engineering College, Vamanjoor, Mangaluru for providing the work space and the constant support and encouragement during the research work.
References
[1] | "Material on Plastic Waste Management", Central Pollution Control Board (CPCB), Delhi, June 2012, pp. 1-22. |
[2] | H. Verity Smith, "Some Criteria For The Successful Commercial Recycling of Heterogeneous Plastics Wastes", Conservation and Recycling, Vol. 2, No. 2, Pergamon Press Ltd.,1978, pp. 197-201. |
[3] | H. Verity Smith, "The Recycling of Mixed Thermoplastics Waste", Polymer-Plastics Technology and Engineering, 12:2, 1979, pp. 141-147. |
[4] | A. G. Buekens, "Some Observations On The Recycling of Plastics And Rubber", Conservation & Recycling, Vol. I, Pergamon Press Ltd., 1977, pp. 247-271. |
[5] | Bruce A. Hegberg, Gary R. Brenniman, William H. Hallenbeck, "Mixed Plastics Recycling Technology", Noyes Data Corporation, Park Ridge, New Jersey, U.S.A. ISBN: O-8155-1297-X, pp. 110 - 116. |
[6] | R T Pringle, M B Barker, "Starting a Waste Plastics Recycling Business", Report Prepared For Aberdeen Forward and Aberdeenshire Council, Napier University - March 2004, pp. 49-50. |
[7] | Noel Deepak Shiri, P. Varun Kajava, Ranjan H. V., Nikhil Lloyd Pais, Vikhyat M. Naik, "Processing of Waste Plastics into Building Materials Using a Plastic Extruder and Compression Testing of Plastic Bricks", Journal of Mechanical Engineering and Automation, 2015, Vol.5(3B), pp. 39 - 42. |
[8] | Noel Deepak Shiri, Shreeranga Bhat, Babisha K C, Krishna M Moger, Minal Patricia D’almeida, Clyde Jofan Menezes, " Taguchi Analysis on the Compressive Strength behaviour of Waste Plastic-Rubber Composite Materials ", American Journal of Materials Science 2016, Vol. 6 (4A), pp. 88-93. |