Santhosh H., Manjunath B. A., Rahul Kumar
Department of Mechanical Engineering, St. Joseph Engineering College, Mangaluru, India
Correspondence to: Santhosh H., Department of Mechanical Engineering, St. Joseph Engineering College, Mangaluru, India.
Email: |  |
Copyright © 2017 Scientific & Academic Publishing. All Rights Reserved.
This work is licensed under the Creative Commons Attribution International License (CC BY).
http://creativecommons.org/licenses/by/4.0/

Abstract
Productivity improvement is a continuous process and an important technique to achieve both individual as well as organizational growth. Connecting rod manufacturing done in BEML machine shop engine division, Mysuru consists of 28 operations in different work centres. In some of the work centres, the components have to be passed 2 to 3 times, thereby increasing the waiting time of the components in the production line. This reduces the flexibility of line leading to line imbalance thereby less output from the line. In this project, an attempt was made to avoid machine waiting and line imbalance; the operations were combined using MAG HMC 1000 using suitable fixture design and program in order to increase the productivity of the connecting rod with reduction in set-up and labour time. Twelve components were accommodated in a single set-up, which would increase productivity by 18.54%.
Keywords:
Connecting Rod, MAG HMC 1000, Fixture
Cite this paper: Santhosh H., Manjunath B. A., Rahul Kumar, Productivity Improvement of 170 Series Connecting Rod Using MAG HMC 1000 CNC Machine, Journal of Mechanical Engineering and Automation, Vol. 7 No. 4, 2017, pp. 103-108. doi: 10.5923/j.jmea.20170704.03.
1. Introduction
The connecting rod or conrod connects the piston to the crank or crankshaft. Together with the crank, they form a simple mechanism that converts reciprocating motion into rotating motion. Connecting rods that function in internal combustion engines are subjected to high cyclic loads comprised of dynamic tensile and compressive loads. They must be capable of transmitting axial tension and compression loads, as well as sustain bending stresses caused by the thrust and pull on the piston and by the centrifugal force of the rotating crankshaft [1].Connecting rods are manufactured by casting, forging, and powdered (sintered) metal processes. Forged connecting rods have been used for years and have a thick parting line along the length of the rod. They are mostly used in high performance engines and are generally used in heavy-duty engines. The cost of cast rods is lower than that of forged rods, both in the initial casting and in the machining. Cast rods can be identified by a thin parting line along the length of the rod. Generally, the forging method produces lighter weight and stronger, but more expensive connecting rods.The function of connecting rod is to transmit the thrust of the piston to the crankshaft. Connecting rods are widely used in variety of engines such as, in-line engines, V-engine, opposed cylinder engines, radial engines, and opposed-piston engines. Table 1 shows the Chemical Composition of Boron Steel used as work piece.Table 1. Chemical Composition of Boron Steel  |
| |
|
The manufacture of connecting rods involves a number of operations that must be routed to different machining centres. Figure 1 shows a connecting rod that consists of a rod and a cap and involves a variety of operations such as milling, boring, grinding, chamfering, drilling, reaming, honing, and assembling.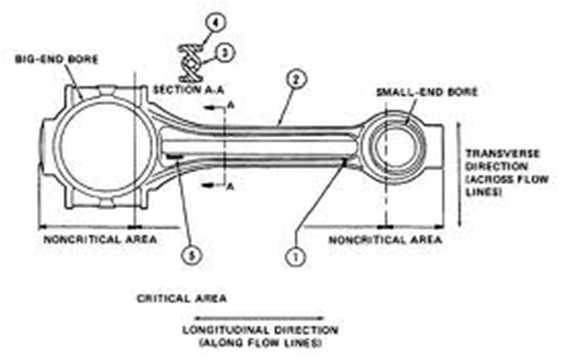 | Figure 1. Connecting Rod |
1.1. Problem Definition
The 170 series connecting rod is manufactured in the BEML machine shop engine division, and consists of 28 operations in different work centres. In some of these work centres, the components have to be passed 2 to 3 times, thereby increasing the waiting time of the components. This reduces the flexibility of the line leading to line imbalance, and thereby less output from the line. This also increases the waiting time, set- up time, and labour time. This results in reduction of the production of the connecting rods.
1.2. Objective
In order to avoid machine waiting and line imbalance, the operations should be combined and automated so that some of the operations are implemented into the latest machining centre MAG HMC 1000, with advanced features, better and consistent in- built quality by using suitable fixture design and program in order to increase the productivity of the connecting rod.• In the same fixture, 5 operations should carried out for a single component in a single set-up.• 12 components can accommodated for a single set-up.
2. MAG HMC 1000 CNC Machine
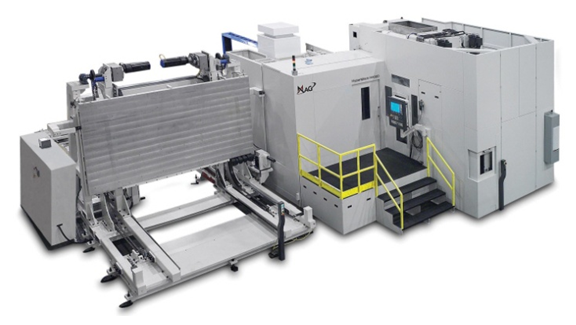 | Figure 2. MAG HMC 1000 CNC Machine |
Table 2. Specification of the MAG HMC CNC Machine 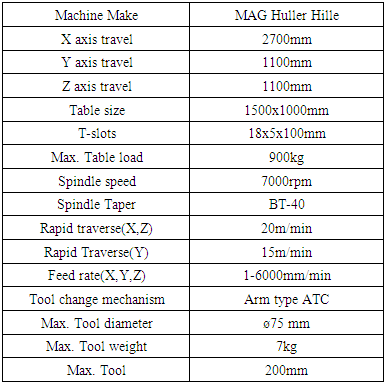 |
| |
|
The MAG HMC 1000 adopts an impressionable casting with scrapping skill, high rigidity structure, and precision axial feed rates to assure high precision machining capacity. It uses a box way mechanism with a worktable of dimension 1500x1000mm and the X, Y, Z axes travel 2700x1100x1100mm. It is a multi- pallet system with a tool magazine capacity of 190 tools and costs < 19.89 crores.
3. Literature Survey
Improving Productivity of Manufacturing Division by using Lean Concepts and Development of Material Gravity Feeder- A Case StudyK. Hemanand et al. carried out as a case study in an automotive industry. They made efforts to reduce motion waste in the shop floor. The problems were identified and analyzed in the current layout through simulation and the results were compared, which resulted in productivity improvement of 11.95%. Motion waste was decreased by developing a new material handling system.Implementation of Productivity Improvement Strategies in a Small Scale CompanyA. Gunasekaran et al. presented a few of their experiences in implementing the latest productivity development strategies in a small company. The objective of the project was to improve productivity in the 2 cells of the manufacture of the head lamp cleaning systems through three aspects to be implemented.Improving Productivity of Connecting Rods by Doe MethodVashim I. Kureshi et al. carried out their work in reducing the rejection rate of connecting rods. The rejection of the connecting rod was taking place due to the assembly of rod and cap tight bolts Using DESIGN OF EXPERIMENTS as tool and by considering four different types of control parameters there was a reduction in the rejection rate by 3%.Improving Productivity for Engine Crank Case Machining Line Using TPS Techniques and SimulationV. N. Borikar et al. used the Toyota Production System (TPS) techniques to optimize the machining line of the Engine Crankcase, where multiple machines were operated by a single operator. It used simulation modelling using ARENA software to verify the on- hand as well as the proposed results.To Improve Productivity for Casting Technology by Reducing Weight of the Gating SystemShashank V. Gulhane et al. tried to discover the problem related with the gating system for the production of ginning dead weight. Casting defects were recognized with % of defect and rejection of around 25-30%.
4. Fixture Details
Fixture is a work holding device that positions the work, but does not guide the tool or position the cutting tool. A fixture can be used for any operation that requires precise relationship in the positioning of a tool to a work piece.
4.1. Fixture Requirements for Connecting Rod
The proper holding of a connecting rod in a particular machine requires a special designed fixture. Here the proposed fixture designed for the MAG HMC 1000 is presented. The advantage of the proposed fixture is that it can hold 12 components at a time and perform 6 different operations. The material for the fixture should have enough strength to allow the 12 component to be placed in the fixture and also the supporting pads, which rest on the connecting rod.
4.2. Selection of Fixture
4.2.1. Fixture Material
Mild steel is used for making fixtures such as base plate, big end boring plate, and front and rear end plates, while C-45 is used for supporting the fixture plates.Table 3. Composition of Mild Steel 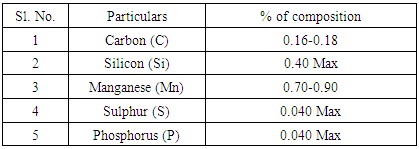 |
| |
|
Table 4. Composition of C-45 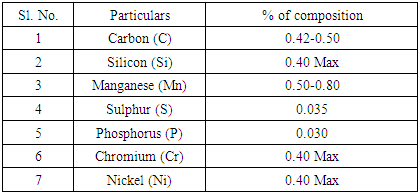 |
| |
|
4.2.2. Fixture Design
The designing of a suitable fixture for the production of connecting rod consists of 3 plates, viz,Ø Base plateØ Big end boring plateØ Front and rear end plateBase PlateThe base plate is the main plate, which is connected to a work table of length 1000mm, width 1000mm, and thickness 63mm. Fig. 3 shows the base plate.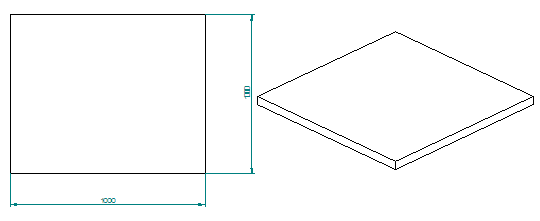 | Figure 3. Base Plate |
Big End Boring PlateThe big end boring plate is placed between the front and rear end plate. This plate is of length 250mm, width 800mm, and thickness 36mm. It is made to accommodate 12 components to carry out the operation of big end boring. Fig. 4 shows the big end boring plate.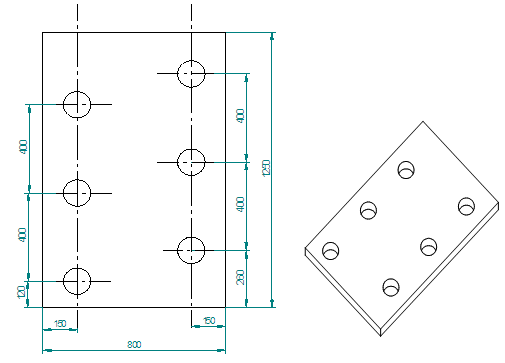 | Figure 4. Big End Boring Plate |
Front and Rear End PlateThe front and rear end plate is mounted on the base plate and connected to the big end boring plate in inverted c shape. This plate is of length 1250mm, width 800mm, and thickness 36mm. It is used to carry out operations such as top and rough milling, top and bottom rough grinding, small end rough boring, small end chamfering and boring, and side end bolt seat milling. Fig. 5 shows the front and rear end plate.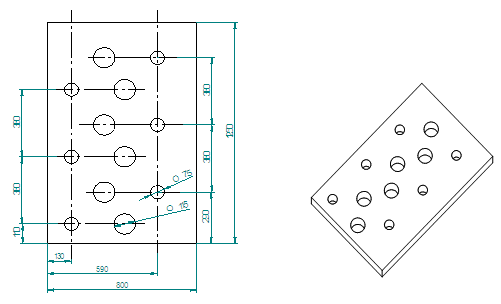 | Figure 5. Front and Rear End Plate |
4.2.3. Fixture Processing
The processing starts with the selection of raw material for the fixture plates. A base plate of 70mm is taken and its thickness is reduced to 63mm by the milling operation. Then, mild steel for the big end boring and front and rear end plate is taken. It is also milled to the desired dimensions and certain operations are carried out on that plate such as• Marking• Drilling• TappingThe resting pads required for supporting the fixture plates are made of C-45 material and are milled to respective dimensions, and marking, drilling, and tapping operations are carried out. The resting pads are connected to the main fixture plates through permanent fasteners.
4.2.4. Hardening
Hardening is a metallurgical and metalworking process used to increase the hardness of a metal. The hardness of a metal is directly proportional to the uniaxial yield stress at the location of the imposed strain. Quenching and tempering are heat-treatment methods used for high-quality heavy plates.
4.2.5. Assembly
The big end boring plate and the front and rear plate is connecting to the base plate by welding in inverted c shape. The welding is done at four points on the fixture plate and carried out in 2 layers. Fig. 6 shows the assembly of the fixture plates from different perspectives.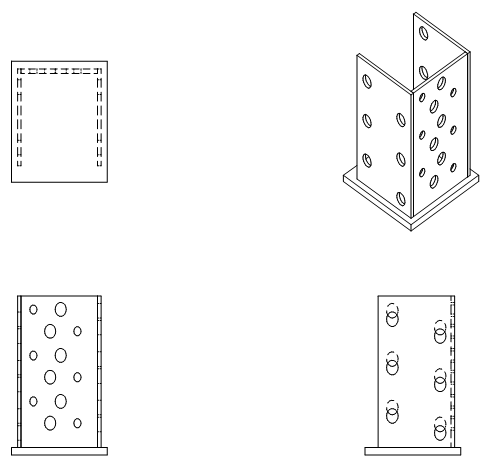 | Figure 6. Different Views of the Assembly of Fixture Plates |
5. Theoretical Analysis
The manufacture of connecting rods done in the Machine Shop Engine Division of BEML Limited, Mysuru. BEML produces 4 series of connecting rods that are used for various applications. They are 170 series 145 series 125 series 105 seriesThis project is mainly concerned with the manufacture of the 170 series connecting rod used in large trucks and earth movers. The operations carried out in the respective machines for the conventional production of connecting rods are shown in Table 5.Table 5. Operations on Respective Conventional Machines 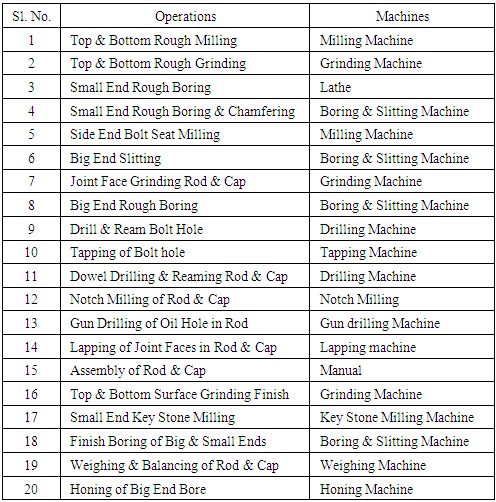 |
| |
|
The total time taken by conventional machines to complete the operations to produce the connecting rod is 8hrs and the set- up time required to produce the 170 series connecting rod is 13hrs.
5.1. Comparison between Conventional and Proposed Methods
The comparison of conventional and proposed method is presented in Table 6.Table 6. Comparison between Conventional and Proposed Methods 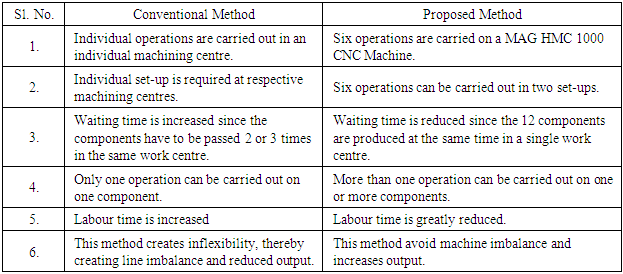 |
| |
|
6. Results and Discussions
The first six main operations are implemented into the MAG HMC 1000 machine. The operations that are implemented and their respective set-up time and labour time in conventional machine are shown in Table 7.Table 7. Operations with their Set-up and Labour Times in Conventional Machines 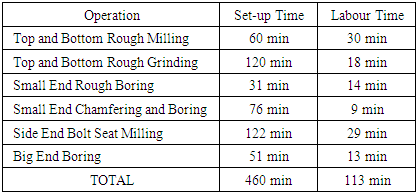 |
| |
|
The results obtained after the trail run of the component on the MAG HMC 1000 CNC Machine is shown in Table 8.Table 8. Operations conducted on MAG HMC 1000 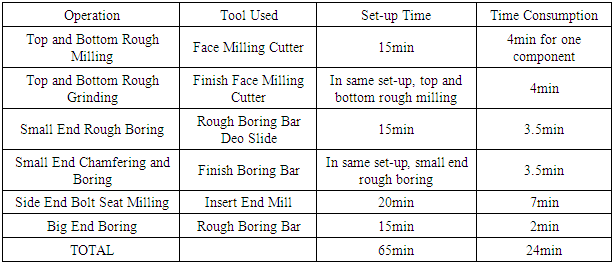 |
| |
|
The first five operations were carried out in a single set- up, which required fixture set-up time of 1hr. And another operation, the big end boring was carried out in another set –up, which required fixture set-up time of 1hr.With this new fixture design and programming capability, the time taken by the MAG HMC1000 CNC Machine for the operations is reduced. The time taken by respective machining centres to carry out these six operations is 113min per component, whereas the time taken by this new fixture design is about 24min for a single component. This new fixture design can perform machining operations for 12 components at a time. It takes around 290min to complete the machining operations for 12 components in this fixture design, whereas it takes 3 shifts by employees to complete these machining operations in respective convention machines.In the same fixture, slots are made to accommodate three different positions of the component. More than one operation can be carried out or two components can be accommodated in a single operation.
7. Conclusions
In this project, an attempt has been made to present the implementation process of productivity improvement method in a company.By the implementation of this new fixture design and program, the productivity is increased to around 30%. The overtime allocated to workers for the completion of orders gets reduced. The waiting period of machines for the arrival of the components at the different machining centres is reduced. Better quality of connecting rods can be produced. The set-up time and cycle time for production is also reduced.
References
[1] | Danielle Visser, “A Comparison of Manufacturing Technologies in the Connecting Rod Industry”, Department of Metallurgical and Materials Engineering, CO 80401. |
[2] | K. Hemanand, D. Amuthuselvan, S. Chidambararaja, & G. Sundararaja, “Improving Productivity of Manufacturing Division by using Lean Concepts and Development of Material Gravity Feeder- A Case Study”, Volume 3, Issue 2 (December 2012). |
[3] | A. Gunasekaran & P. Cecille, “Implementation of Productivity Improvement Strategies in a Small Scale Company”, Department of Manufacturing and Engineering Systems, Brunel University, UK. |
[4] | Vashim I. Kureshi & Ankit B. Sidhpara. “Improve Productivity of Connecting Rod by Doe Method”, Final year student of M.E. Mechanical, Marwadi Engineering College, Rajkot. |
[5] | V. N. Borikar & Dr. K. H. Inamdar, “Improving Productivity for Engine Crank Case Machining Line Using TPS Techniques and Simulation”, Walchand College of Engineering, Sangli, Maharashtra, India. |
[6] | Shashank V. Gulhane & Rahul M. Dahekar, “To Improve Productivity for Casting Technology By Reducing Weight of Gating System”, Assistant Professor in Mechanical Engineering Department, G.W.C.E.T, Nagpur. |