Sharun Mendonca, Khalid Mohammad Zulqurnain, K. M. Abdul Razack, Mohammed Zohair, Rolwin Wilston Carlo
Department of Mechanical Engineering, St Joseph Engineering College, Vamanjoor, India
Correspondence to: Khalid Mohammad Zulqurnain, Department of Mechanical Engineering, St Joseph Engineering College, Vamanjoor, India.
Email: |  |
Copyright © 2017 Scientific & Academic Publishing. All Rights Reserved.
This work is licensed under the Creative Commons Attribution International License (CC BY).
http://creativecommons.org/licenses/by/4.0/

Abstract
Robotics has become very useful in medicine, education, military, research and mostly, in the world of manufacturing. It has become popular, useful, and has achieved great success in several fields of humanity. In this project, work is carried out on the robotic arm which is controlled using an Arduino ATMEGA-328 micro-controller via android app. Servomotors are used for the link movements and DC motors are used for the base movement. The benefits of this work are visual movement of the device, text-to-speech recognition, compact in size and economical. The prototype developed is more user friendly and less costlier. It will perform the desired operation very smoothly. The system can be controlled within a range of 15 meters using any android smart phone, which will be more applicable in applications such as bomb defusing, remote pick and place, cleaning applications.
Keywords:
Arduino ATMEGA-328, Servomotors, DC motors, Android App
Cite this paper: Sharun Mendonca, Khalid Mohammad Zulqurnain, K. M. Abdul Razack, Mohammed Zohair, Rolwin Wilston Carlo, Multi Functional Android Controlled Robotic Arm for Drilling, Cutting and Cleaning Application, Journal of Mechanical Engineering and Automation, Vol. 7 No. 3, 2017, pp. 89-93. doi: 10.5923/j.jmea.20170703.06.
1. Introduction
In the modern world, Robotics has become popular, useful, and has achieved great success in several fields of humanity. Robotics has become very useful in medicine, education, military, research and mostly, in the world of manufacturing. It is a term that has since been used to refer to a machine that performs work to assist people or work that humans find difficult or undesirable. [1]Robots which could be destructive or non destructive, performs tasks that would have been very tedious for human beings to perform. They are capable of performing repetitive tasks more quickly, cheaply, and accurately than humans [9]. Robotics involves the integration of many different disciplines, among them kinematics, signal analysis, information theory, artificial intelligence, and probability theory. These disciplines when applied suitably, lead to the design of a successful robotic arm. The most common types of robot technology that have evolved for different purposes are Robotic Arms. The Robotic arms are mechanically controlled devices designed to replicate the movement of a human arm. These are used for lifting heavy objects and carrying out tasks that require extreme concentration and expert accuracy. The design of a robot arm can vary depending on what it is intended to do. The Robotic Arm is programmable in nature and it can be manipulated. A robot control language defines the actions that a robot manipulator needs to perform in order to complete some task. There are different programming languages like Variable Assembly Language (VAL), Motion Control Language (MCL), WAVE, Interactive Reader Language (IRL), Arc Macro Language (AML) etc. [2]The equipments used in automation are effective to produce at faster rates and with better quality. Automation is made by using different machines like CNC (Computer Numerical Control), putting conveyors for transfer systems. All these systems require PLC (Programmable Logic Controller). Also most of the automobile industries use robots. Robots are used for making spot welding, painting, assembly, water jet cutting, dispensing, handling parts. By using robots work is completed faster. Accuracy of work increases because robot works as per the program stored in it. There is no deviation in the position from programmed points. As software used in the robot is advanced the diagnosis is also very easy and faster. [4] In this project, work is carried out on the robotic arm which is controlled using an Arduino micro-controller through a android app. It is applicable for drilling, pick and place, cutting and cleaning applications. The benefits of this work are visual movement of the device, text-to-speech recognition, compact in size and economical. It is also capable of carrying out operations which are difficult for the humans to perform.
2. Literature Survey
A self sufficient robotic arm is fabricated by using components like micro-controllers and motors. This increases their speed of operation and reduces the complexity. It also brings about an increase in productivity which makes it easy to shift to hazardous materials. In the implementation process, the necessary components of structure ICs, blocks and power supply are all assembled on the PCB. The Robotic Arm is designed using the Microcontroller i.e. ATMEGA8 Micro-controller using Arduino programming. This process works on the principle of interfacing servos and potentiometers. This task is achieved by using Arduino board. Potentiometers play an important role. The remote is fitted with potentiometers and the servos are attached to the body of the robotic arm. The potentiometer converts the mechanical motion into electrical motion. Hence, on the motion of the remote the potentiometers produce the electrical pulses, which are en route for the arduino board. The board then processes the signals received from the potentiometers and finally, converts them into requisite digital pulses that are then sent to the servomotors. This servo will respond with regards to the pulses which results in the moment of the arm. [6].At present, the main interest is to protect nuclear workers in highly contaminated areas or hostile environments, robots can be used in nuclear power plants to reduce human exposure not only to radiation, but also to hot, humid and oxygen-deficient atmosphere researchers in the field of robotics are proposing a great variety of robots configurations and functional capabilities to be used in nuclear power plants. Wheeled robots and tracked vehicles are the common configurations for mobile robots. [3].The robotic arm was designed with four degrees of freedom and programmed to accomplish accurately simple light material lifting task to assist in the production line in any industry. 3D printing method is used in this project to fabricate the components of the robotic arm. Therefore, it provided more precise dimensions and huge time and cost-saving in fabrication. The robotic arm is equipped with 4 servo motors to link the parts and bring arm movement. Arduino, an open-source computer hardware and software is applied to control the robotic arm by driving servo motors to be capable to modify the position. [7]. The performance of the micro-robotic system has the potential to have an important role in such applications with reference to the transportation, handling and storage of micro objects. For that, has developed an automated system consisting of multiple drilling micro-robots. [8]
2.1. Objectives
The objective of this project is to • Automate the process of drilling, cutting and cleaning using robotic arm.• Use of robotic arm in small areas of work.• Synchronizing robotic technology and android system.
3. Part Description
The robotic arm consists of several parts. They are Links, Servo Motors, DC Motors, Wheeled Base, Micro-Controller, Bluetooth Module.
3.1. Arduino Uno
The Arduino Uno is a microcontroller board based on the ATmega328. It has 14 digital input/output pins (of which 6 can be used as PWM outputs), 6 analog inputs, a 16 MHz crystal oscillator, a USB connection, a power jack, an ICSP header, and a reset button. It contains everything needed to support the microcontroller; simply connect it to a computer with a USB cable or power it with a AC-to-DC adapter or battery to get started. 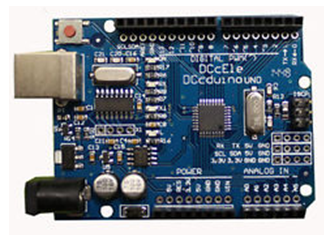 | Figure 1. Arduino Uno |
3.2. Bluetooth HC 05 Module
The HC-05 module is a Bluetooth SPP (Serial Port Protocol) module, which means it communicates with the Arduino via the Serial Communication.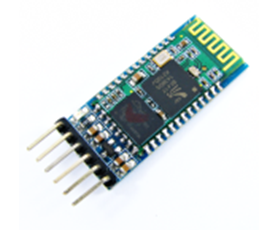 | Figure 2. Bluetooth Module |
3.3. L298n Motor Driver Dual H Bridge
The L298N driver module , using ST’s L298N chip can directly drive two 3-30V DC motor and provides a 5V output interface can 5V single chip circuitry to supply , support 3.3VMCU control, you can easily control the DC motor speed and direction.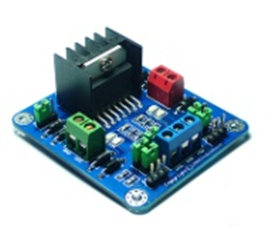 | Figure 3. L298n Driver |
3.4. Tower Pro M995 Metal Gear Servo Motor
This is the most famous servo made by Tower Pro. MG995 is a digital metal gear high torque servo for airplane, helicopter, RC-cars from 10 to 6-th scale buggy and monster and many RC models.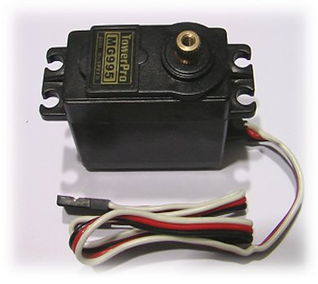 | Figure 4. Tower Pro M995 Metal Gear Servo Motor |
3.5. Mini Drill
The end effector of the robotic arm consists of a mini drill which is constructed using a DC motor enclosed inside a PVC pipe.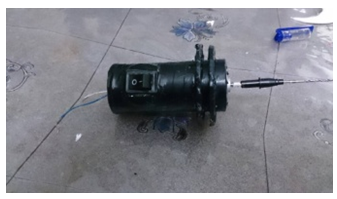 | Figure 5. Mini Drill |
3.6. Links
The material used for the main body of the robotic arm is Acrylic Perspex sheets of 1000 x 1000 x 3mm. The links of specific dimensions are cut by laser cutting operation.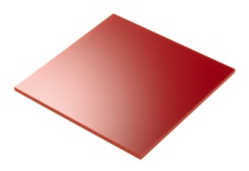 | Figure 6. Acrylic Perspex Sheets |
4. Design and Calculations
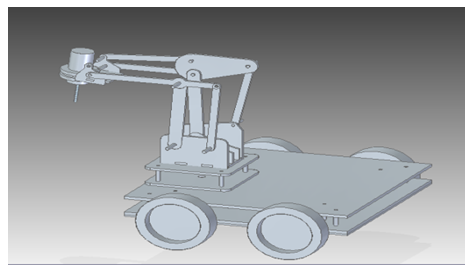 | Figure 7. 3D Design Model |
4.1. Calculations
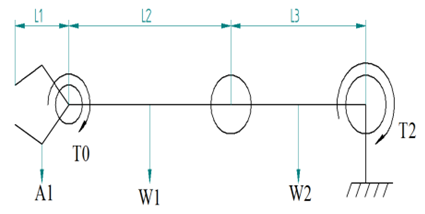 | Figure 8. Line Diagram Representing the Weights of the Links |
4.1.1. Torque Required At Each Joint
Weights of the links
Length of the links
Torque valuesT0 = A1 * L1/2T0 = 1.962 * 35 = 68.67 Nmm.T2 = A1 * (L1 /2 + L2 + L3) + W1 * (L2/2 + L3) + W2 * L3/2T2 = 1.962 * (35+ 140 + 120) + 0.981*(70 + 120) + 2.453*60 = 912.36 Nmm.
4.1.2. Kinematic Structure
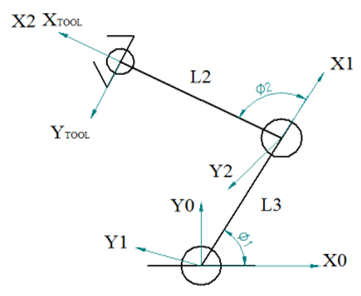 | Figure 9. Line Diagram Representing the Frames |
The DH parameter of the robotic arm is:
To provide the position and orientation of the end effector with respect to the base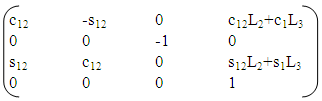
4.2. Block Diagram
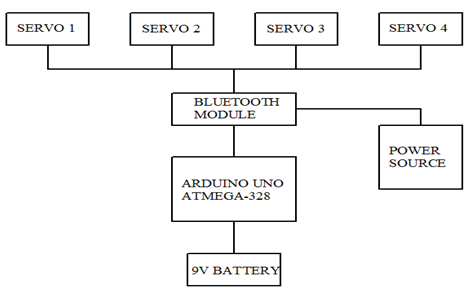 | Figure 10. Block Diagram for the Link Movement |
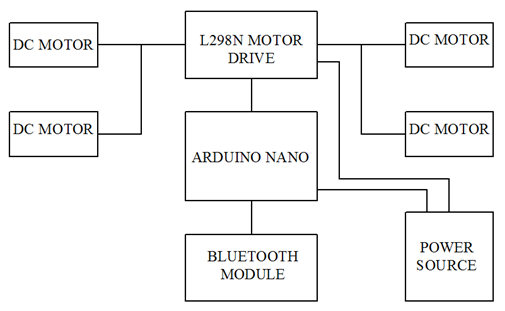 | Figure 11. Block Diagram for the Base Movement |
4.3. Programming and Controlling the Arduino System
The entire system is controlled through an android smart phone using two apps, namely Arduino Control Car and Multiple Servo Control. The Arduino Control Car app is used for the movement of the wheel base while the Multiple Servo Control is used for the movement of the links. These apps are connected to the Arduino system via Bluetooth module and it can control the movements.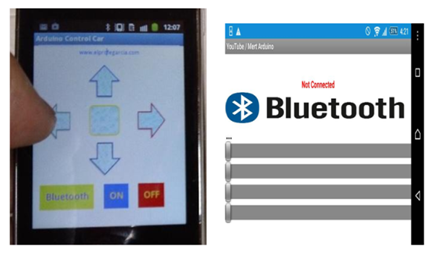 | Figure 12. Arduino Control Car and Multiple Servo Control App |
5. Conclusions
Nowadays robotic technology has a major role in the advancement of technology. Most of the workers are moving towards the service sector and not to the industrial sector. As a result there exists a scope for automating all the operations carried out by the workers in industries.The prototype developed is more user friendly and less costlier. It will perform the desired operation very smoothly. The system can be controlled within a range of 15 meters using any android smart phone, which will be more applicable in applications such as bomb defusing, remote pick and place, cleaning applications.In the further development, the robotic arm can be designed for other applications like in gardening, agricultural applications etc. Different sensors can be used to detect the position of the objects and the whole process can be automated and it can also communicate with user through networking.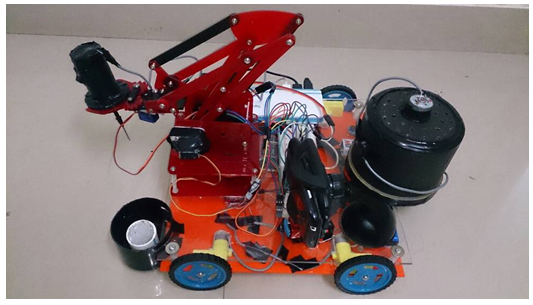 | Figure 13. Final prototype |
ACKNOWLEDGEMENTS
The authors extend heartfelt thanks and appreciations to Director and Principal of St Joseph Engineering College, Mangaluru for their continuous support and encouragement during project work.
References
[1] | Puran Singh, Anil Kumar, Mahesh Vashisth, Design of a Robotic Arm with Gripper & End Effector for Spot Welding, Universal Journal of Mechanical Engineering 1(3): 92-97, 2013. |
[2] | K. Manoj Kumar & Ch. Sambaiah, Modelling And Study of Motion Control System for Motorized Robot Arm Using Mat Lab And Analysis of The Arm By Using Ansys, International Journal of Mechanical and Industrial Engineering (IJMIE), ISSN No. 2231 –6477, Vol-2, Issue-1, 2012. |
[3] | Goldy Katal, Saahil Gupta, Shitij Kakkar, Design And Operation of Synchronized Robotic Arm, IJRET: International Journal of Research in Engineering and Technology E-ISSN: 2319-1163 | P-ISSN: 2321-7308. |
[4] | Marco Piccigallo, Umberto Scarfogliero, Claudio Quaglia, Gianluigi Petroni, Design of a Novel Bimanual Robotic System for Single-Port Laparoscopy, IEEE/ASME Transactions On Mechatronics, Vol. 15, No. 6, December 2010. |
[5] | Sebastian Klug, Bernhard Möhl, Oskar von Stryk and Oliver Barth, Design and Application of a 3 DOF Bionic Robot Arm, Proc. AMAM 2005, Illmenau, Germany, September 25-30, 2005. |
[6] | A.N.W.Q, K. L. Voon, M. A. Ismail, N. Mustaffa, M. H. Ismail, Design and Development of a Mechanism of Robotic Arm for Lifting, 2nd Integrated Design Project Conference (IDPC) 2015. |
[7] | Matt Blackmore, Jacob Furniss, Shaun Ochsner, 5 DOF Robotic Arm, ECE 478/578 Embedded Robotics, Fall 2009. |
[8] | Sajid Ghuffar, Javaid Iqbal, Usman Mehmood And Muhammad Zubair, Design and Fabrication of a Programmable 5-DOF Autonomous Robotic Arm, 6th WSEAS Int. Conf. on Systems Theory & Scientific Computation, Elounda, Greece, August 21-23, 2006 (pp167-173). |
[9] | Paul Ciprian Patic, Mihaita Ardeleanu, Florin Popa, Micro-robots used in control of automatic drilling operations, WSEAS Transactions on Circuits and Systems, ISSN: 1109-2734, Issue 6, Volume 9, June 2010. |
[10] | S. Pachaiyappan, M. Micheal Balraj, T. Sridhar, Design And Analysis of an Articulated Robot Arm for Various Industrial Applications, IOSR Journal of Mechanical and Civil Engineering (IOSR-JMCE) E- ISSN: 2278-1684, P-ISSN : 2320–334x Pp 42-53. |