Pavana Kumara B., Krisantha Alexandra Pais, Roger Michael Pereira, Mohammed Ashish Sahil, Varun S. Mallya
Department of Mechanical Engineering, St. Joseph Engineering College, Mangalore, India
Correspondence to: Roger Michael Pereira, Department of Mechanical Engineering, St. Joseph Engineering College, Mangalore, India.
Email: |  |
Copyright © 2017 Scientific & Academic Publishing. All Rights Reserved.
This work is licensed under the Creative Commons Attribution International License (CC BY).
http://creativecommons.org/licenses/by/4.0/

Abstract
The future of technology lies significantly in the field of R&D. With extensive research and the desire to obtain abilities beyond the human capability, the concept of anthropomorphic equipment came into being. The thirst for indomitable power was quenched by the development of the “Human Exoskeleton.” A Human Exoskeleton also known as Powered Armour, Exoframe, Hardsuit, or Exosuit, is a wearable mobile machine that can be powered by a system of motors, pneumatics, levers, or hydraulics that amplifies the force of the operator and enables them to possess superhuman strength. This concept has a wide scope for improvement and is a tantalizing topic for research. With the dawn of this advanced technology, the term ‘weakness’ can be eliminated from the human perception. This project aims to empower the physically weak individuals by helping them harness the power of pneumatics to amplify the strength of their arm. By incorporating a pneumatic cylinder in the system, it is possible to significantly reduce the amount of muscle effort required, by an individual, while lifting loads up to twenty-five kilograms. The design has been realised for one arm but can be extended to the other arm as well. The exoskeleton arm is a subassembly of an entire portable suit, and it permits the transfer of external loads to the stronger sections of the body by means of accurately placed linkages and joints. The arm is intended to be an auxiliary source of strength for any person willing to exercise themselves back to fitness or just perform arduous domestic tasks.
Keywords:
Exoskeleton, Pneumatic, Strength, Anthropomorphic, Auxiliary, Rehabilitation
Cite this paper: Pavana Kumara B., Krisantha Alexandra Pais, Roger Michael Pereira, Mohammed Ashish Sahil, Varun S. Mallya, Design and Fabrication of a Pneumatically Powered Human Exoskeleton Arm, Journal of Mechanical Engineering and Automation, Vol. 7 No. 3, 2017, pp. 85-88. doi: 10.5923/j.jmea.20170703.05.
1. Introduction
The world today is spellbound by the surreal realm of superheroes and their ability to defy the laws of physics. Although they are fictitious, they have inspired the modern homo-sapiens to incorporate certain concepts of superhuman abilities into current technology. This idea conceived by the humans has been realised with the birth of the “Human Exoskeleton.” The term “Exoskeleton” refers to an external wearable robot that is worn by the user to extend muscle strength and enhance body stability. It is designed in a skeletal manner i.e., the joints of the exoskeleton line up correspondingly with the joints of the human limb on which it is worn. The force exerted by the exoskeleton is thus exerted on the joints of the human to create power-augmented motion. In recent years, there has been an increasing interest in the development of different kinds of exoskeletons. This is made possible now by many technological advancements: some including reduction in sizes of actuators such that exoskeletons can be worn by a human user, improvements in reduction of size of power supplies and lifetime, better control techniques, etc. The exoskeleton is a classification under wearable robots that describes a robotic field which studies the interaction between the human body and robotics. In these systems, a mechatronics structure is attached to different members of the human body, and while the wearer commands the mechanical system using physical signals (like electronic simulation produced by the orders of the brain, or the movements of the body generated by muscles) the mechanical system does the hard work, like carrying heavier objects or helping the movement of handicapped members of the body. Since its conception in the sixties, the bibliography written by Crawshaw speaks about two models of wearable robots - the prosthetics and the orthotics. The first group replaces the lost body members, while the second one assists the body movements or enhances the body capabilities.
2. Objectives
1. To design and fabricate a pneumatically powered human exoskeleton for one arm (can be extended to both arms) to assist the physically weak (at the upper limb) individuals.2. To ensure that the arm is cost effective and available to the general masses.3. To manufacture an economic, portable, reliable, stable and ergonomic human exoskeleton arm.4. To apply the concepts of engineering learnt at the undergraduate level to the real world.
3. Development of the Exoskeleton Arm
3.1. Failure Mode and Effect Analysis of the Arm
To ensure quality control, a Failure Mode and Effect Analysis (FMEA) of the system was undertaken and it showed that the forearm is crucial, especially the forearm rib, and hence is more susceptible to failure. This is shown in Table 1 below.Table 1. Failure Mode and Effect Analysis of the Exoskeleton Arm 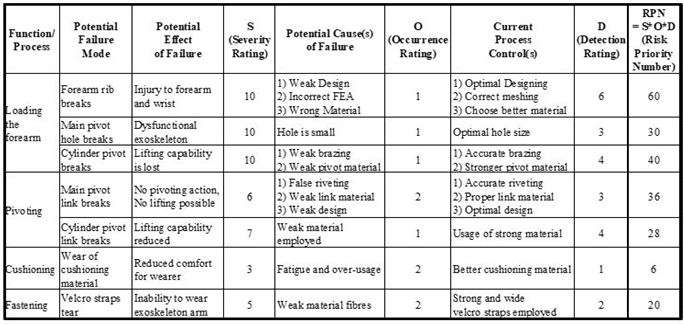 |
| |
|
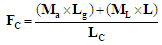 | (1) |
3.2. Design Calculations
By considering the moment about the “Elbow Pivot” as shown in Figure 1, we obtain,Where, FC - Force acting on the cylinder (Newton)Ma - Mass of the arm = 3 kgLg - Distance of the centre of gravity of the forearm (meter)ML - Mass of the load to be lifted = 25 kgL - Length of the forearm = 0.3048 meterLc - Eccentricity from the elbow = 0.0508 meter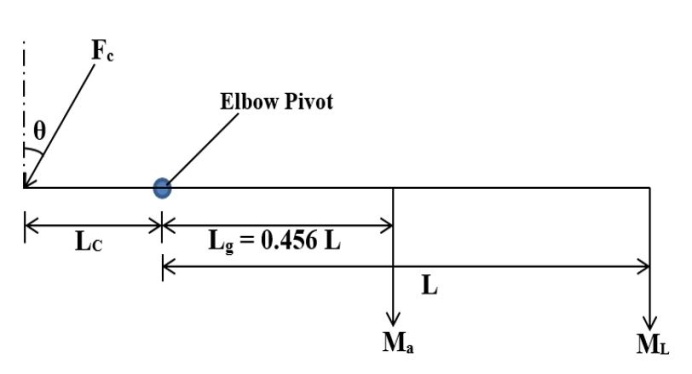 | Figure 1. Free Body Diagram of the Forearm Frame |
For Forearm Length of 12 inches (0.3048 m):Using the formula given by Equation (1), we get,
Considering a Factor of Safety (FOS) Margin of 5% (1.05 FOS):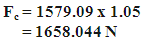
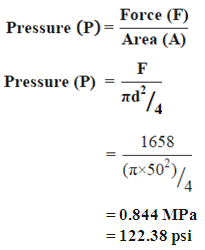 | (2) |
3.3. Design of the Arm
After performing the required the calculations, the next goal was to conceptualise a design for the exoskeleton arm. A licensed version of the NX 10 PLM (CAD/CAM/CAE) Software was used to cater to the needs. After multiple heuristic analysis, the most optimal designs of the Forearm frame, Bicep frame and Forearm rib were chosen.A survey was initially conducted to acquire the dimensions of the forearm and bicep (Circumference and Length). CAD Modelling of the aforementioned components was done using the dimensions obtained from the survey, taking into account tolerance values wherever necessary.The Failure Mode and Effect Analysis (FMEA) of the system inferred that the forearm is more prone to failure and hence an optimal design of the forearm rib was designed as shown in Figure 2 below.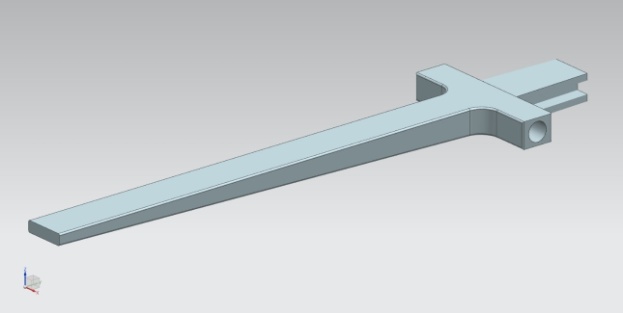 | Figure 2. The Forearm Rib (Carrying Main Pivot and Cylinder Pivot) |
3.4. Analysis of the Arm
For analysing the arm, the CAE function of the NX 10 software was employed. The Forearm rib was analysed using 1 mm, 3-D Tetrahedral (C-4) Meshing and was found to be safe with a Factor of Safety equal to 1.46. The loading and constraint (pinned) was applied as displayed in Figure 3 below.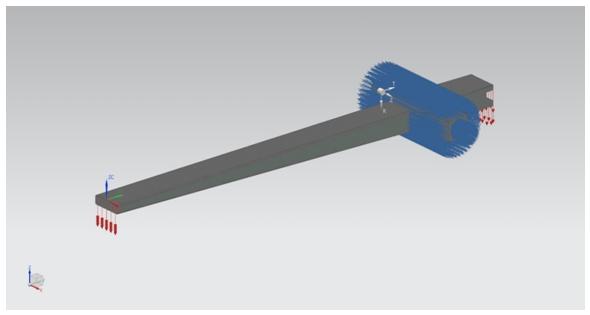 | Figure 3. Loading and Pinned Constraint Application (For Upward Motion of Arm) |
4. Working Procedure of the Pneumatically Powered Exoskeleton Arm
The entire working of the exoskeleton arm is summarised in the form of a block diagram as shown in Figure 4 below.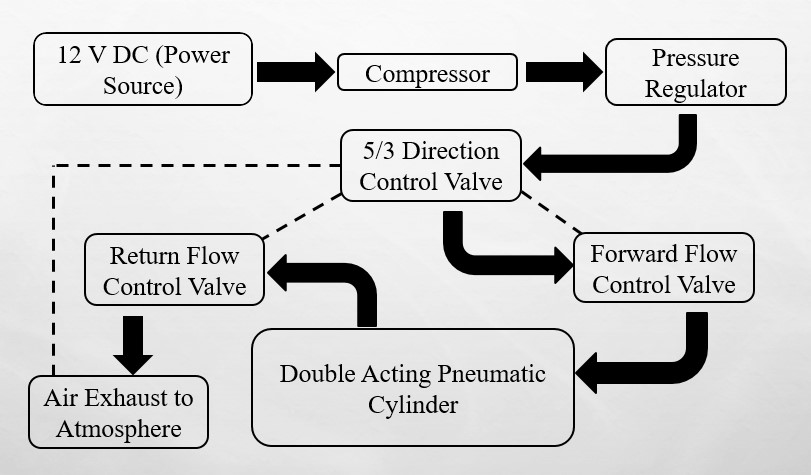 | Figure 4. Working Procedure of the Exoskeleton Arm |
The lifting action is achieved using a Double Acting Pneumatic Cylinder which upon extension raises the forearm and amplifies the power output. This facilitates easy lifting of heavy loads. The magnitude of effort by the arm depends on the efficiency of the cylinder used.
5. Applications
The exoskeleton arm is found to be useful in diverse situations as mentioned below:• Disabled people can regain the use of their limbs using the exoskeleton.• The exoskeleton can be used as a means of rehabilitation.• Industrial workers, dock workers and loaders who are engaged in jobs which entail lifting of heavy loads on a daily basis are empowered by the exoskeleton.• Nurses who have to carry heavy patients can effectively do so with the exoskeleton.• Exoskeletons have become widely popular in the military field as well, helping soldiers to carry armaments over challenging terrain.
6. Conclusions
• The Forearm frame, bicep frame and forearm rib were designed and analysed using Siemens NX 10 PLM Package Software. • The frames were designed keeping in mind the average dimensions obtained from a survey of various human upper limb sizes. • The Pneumatically Powered Human Exoskeleton Arm was fabricated successfully as per the predefined metrics. • The Prime material used for fabrication of the exoskeleton is Aluminium Alloy (6061), which reduced the overall weight of the assembly.• Slots machined on the Forearm and Bicep frames helped to further reduce the overall weight and to facilitate ventilation. • With nearly 130 psi pressure applied on the Pneumatic cylinder, which is the power house of the exoskeleton, the muscle effort was considerably reduced and loads up to 25 kg could be lifted with ease.• The amount of muscle effort depends on the overall efficiency of the pneumatic cylinder.• The fabricated pneumatically powered Human Exoskeleton arm is economical (costing under Rs. 12,000), aesthetic, reliable, portable and ergonomic.• The exoskeleton arm proves to be an excellent assist tool for the physically weak individuals.• The exoskeleton arm is just the beginning of a potential power enhancing exoskeleton suit which is the technology of the future.• The exoskeleton arm (by incorporating pneumatics) is the first step to the advancement of mankind’s perception of technology.
References
[1] | Abdulla Almomani, Faisal Miqdadi, Mustafa Hassanin, Mustafa Samy, and Mohammed Awadallah, “The 1st Pneumatic Fluidic Muscles Based Exoskeleton Suit in The U.A.E,” IEEE, 2014. |
[2] | Kwok-Hong Chay, Jer-Vui Lee, Yea-Dat Chuah and Yu-Zheng Chong, “Upper Extremity Robotics Exoskeleton: Application Structure and Actuation,” International Journal of Biomedical Engineering and Science (IJBES), Vol. 1, Issue No. 1, pp 35-45, April 2014. |
[3] | Joel C. Perry, Jacob Rosen and Stephen Burns, “Upper-Limb Powered Exoskeleton Design,” IEEE/ASME Transactions on Mechatronics, Vol. 12, Issue No. 4, pp 408-417, August 2007, Publisher: IEEE. |
[4] | Boris Jobbágy, Dušan Šimšík, Jiří Marek, Ján Karchňák and Daniela Onofrejová, “Robotic Exoskeleton for Rehabilitation of the Upper Limb,” American Journal of Mechanical Engineering, Vol. 2, Issue No. 7, pp 299-302, 2014, Publisher: Science and Education Publishing. |
[5] | Gregory Clark Henderson and Jun Ueda, “Pneumatically-Powered Robotic Exoskeleton to Exercise Specific Lower Extremity Muscle Groups in Humans,” Biomedical Robotics and Biomechatronics (BioRob), 4th IEEE RAS & EMBS International Conference on IEEE, pp 1506-1511, 2012, Publisher: IEEE. |
[6] | Younkoo Jeong, Yongseon Lee, Kyunghwan Kim, Yeh-Sun Hong and Jong-Oh Park, “A 7 DOF Wearable Robotic Arm Using Pneumatic Actuators,” Proceedings of the 32nd ISR (International Symposium on Robotics), Vol. 19, pp 21, April 2001. |
[7] | Zhichuan Tang, Kejun Zhang, Shouqian Sun, Zenggui Gao, Lekai Zhang and Zhongliang Yang, “An Upper-Limb Power-Assist Exoskeleton Using Proportional Myoelectric Control,” Sensors, Vol. 14, Issue No. 4, pp 6677-6694; DOI: 10.3390/s140406677, Publisher: Multidisciplinary Digital Publishing Institute, 2014. |
[8] | Hugh Herr, “Exoskeletons and orthoses: classification, design challenges and future directions,” Journal of Neuroengineering and Rehabilitation, Vol. 6, Issue No. 1, pp 21, DOI: 10.1186/1743-0003-6-21, Publisher: BioMed Central, 2009. |
[9] | Evangelos Papadopoulos and Georgios Patsianis, “Design of an Exoskeleton Mechanism for the Shoulder Joint,” 12th IFToMM World Congress, Besançon (France), pp 18-21, 2007. |
[10] | Md. Sadiur Rahman, Md. Tanjil Rashid Avi, “Exoskeleton Arm - The First Step of Real Life Iron Suit,” School of Engineering and Computer Science BRAC University, Publisher: BRAC University, 2015. |
[11] | Arjun Kurunji and Team, “Project Report on Design and Fabrication of Exoskeleton Arm,” St. Joseph Engineering College, Mangalore, Karnataka, 2014. |