Karthik Madhyastha
Department Mechanical Engineering, St Joseph Engineering College, Mangalore, India
Correspondence to: Karthik Madhyastha, Department Mechanical Engineering, St Joseph Engineering College, Mangalore, India.
Email: |  |
Copyright © 2017 Scientific & Academic Publishing. All Rights Reserved.
This work is licensed under the Creative Commons Attribution International License (CC BY).
http://creativecommons.org/licenses/by/4.0/

Abstract
Agriculture is the backbone of India’s economy. Application of technological innovation to improve the productivity in agricultural activities is a continuous process. Nowadays, agriculture related engineering projects have gained a lot of scope because of the need and usefulness in uplifting the quality of work. Pepper separator machine is an agriculture related project for facilitating efficient separation of pepper berries from its spikes. There are many problems associated with existing design of pepper separator machine like high cost, low efficiency, low capacity and more processing time. One of the main disadvantages of the existing machines is that they damage the berries because of the use of metallic parts in them. To address this problem an attempt was made to replace some of the metallic parts by rubber and automate the separation of pepper. Thus, pepper would get threshed between the stationary and rotary rubber bushes and get separated without damage.
Keywords:
Piper nigrum, Pepper Separator Machine, Threshing
Cite this paper: Karthik Madhyastha, Design and Fabrication of Pepper Separator Machine, Journal of Mechanical Engineering and Automation, Vol. 7 No. 3, 2017, pp. 82-84. doi: 10.5923/j.jmea.20170703.04.
1. Introduction
Pepper has been used as a spice since prehistoric times. It is popularly known as “King of All Spices”. It is the whole dried fruit of the vine Piper nigrum, a native crop of tropical region. In India, it is extensively cultivated in the western ghat region and has always reigned supreme in the production and export of this most exotic and sought-after spice. The crop is harvested mainly in the months of December and January at proper maturity of the berries, as it greatly influences the quality of the final product [1].Harvesting is followed by threshing for separation of the berries from spikes. The traditional method used for this has been by trampling with legs, which is crude, tedious, labour intensive and unhygienic [1]. To overcome this problem several types of mechanical pepper threshers have been designed. Over the past few years, many individual plantations have developed varieties of pepper threshers for their usage and most of these machines make use of rotating metallic drum technique of threshing. The disadvantage of this technique is that the usage of metallic parts causes damage to the berries. Therefore, it was necessary to develop a pepper thresher which would overcome all the drawbacks mentioned above.
2. Objective and Working Principle
The current project was carried out with the objective of designing and fabricating a cost effective mechanical pepper separator machine which would reduce the berry damage during threshing process and automate the separation process. The set up consisted of a vertical rotating cylinder with rubber bushes on its periphery and powered by an electric motor. It was surrounded by a stationery drum which also had rubber bushes on its inner walls. Pepper spikes with berries were fed into the machine through the hopper. Pepper would get threshed between the stationary and rotary bushes thereby separating the berries from spikes. The bottom of the drum was provided with the mesh plate through which only pepper seeds would pass and the spikes would remain over it. After separation pepper seeds would be collected from the two outlets. A brush connected to the shaft just above the base, would push out all the spikes through another outlet.
3. Design and Fabrication
3.1. Shaft Speed
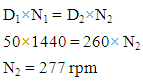 | (1) |
Where D1, D2= Pulley diametersN1, N2= Shaft speeds
3.2. Power Requirement
Depending on the free volume of space inside the drum, the weight of the pepper berries and spikes that can be fed into it at a time was found to be = 1.5Kg*9.81= 14.715NMaximum threshing force per spike = 0.735NAverage weight of spike = 12gm = 0.1177NForce required for threshing 1.5 kg of pepper stalk
Torque produced  | (2) |
Power required for threshing  | (3) |
Based on the power value, a 0.75HP electric motor was selected.
3.3. Selection of Belt Drive
V-belt drive was selected to transmit power from the motor to the machine shaft. Depending on the power from the motor two V-belts of type A were selected.
3.4. CAD Models and Assembly
The CAD models in Figure 1 and 2 show the stationary drum and the rotating cylinder with rubber bushes respectively. Figure 3 shows the assembly. The actual fabricated pepper thresher equipment is shown in figure 4.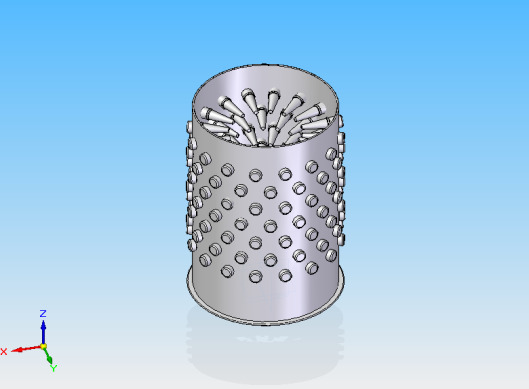 | Figure 1. CAD model of stationary drum with bushes |
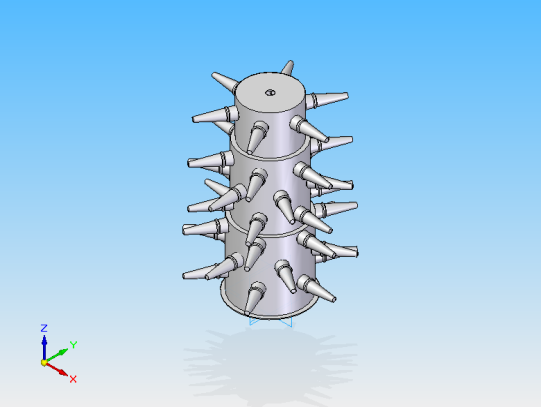 | Figure 2. CAD model of rotating cylinder with bushes |
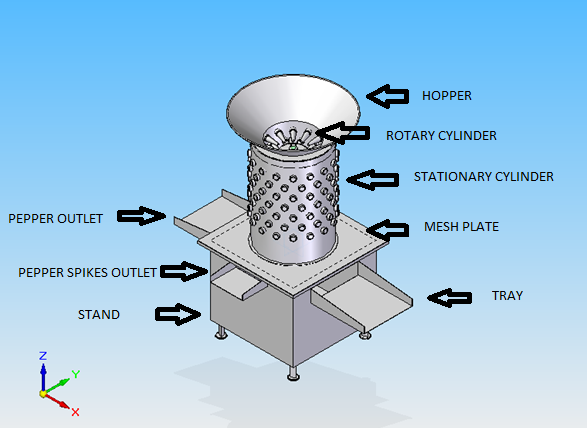 | Figure 3. Assembly |
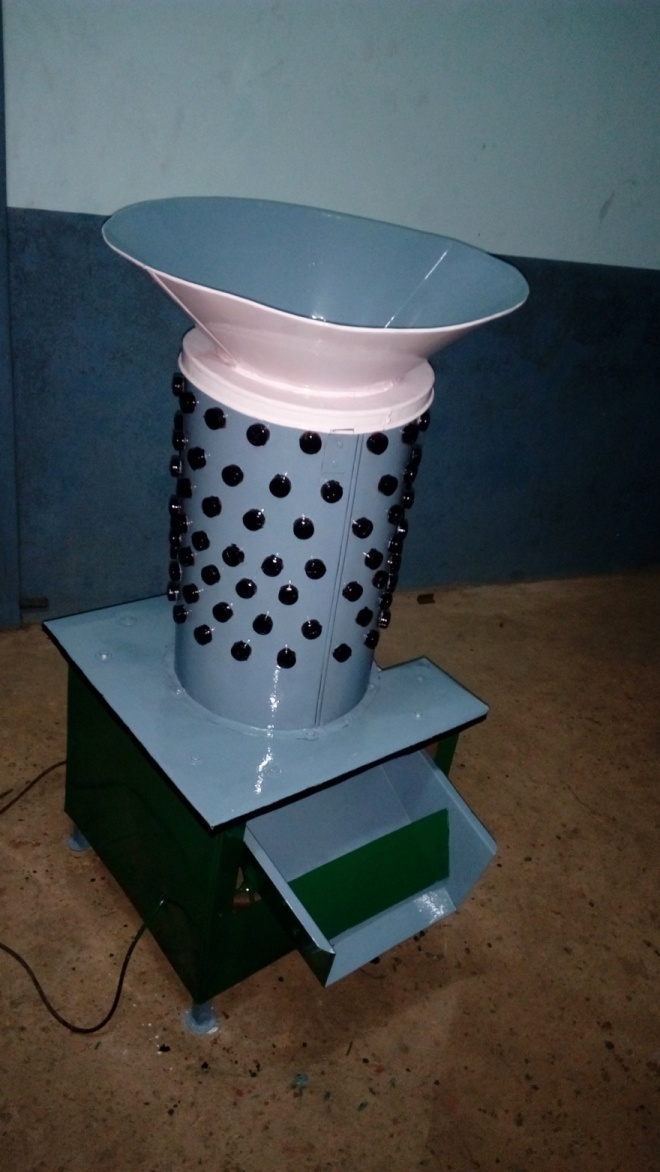 | Figure 4. Fabricated Pepper Threshing machine |
4. Testing for Efficiency
The fabricated model was tested for efficiency. It was found that during the test, on supplying 2 kg of pepper spikes into the machine which contained around half kg of pepper berries, an output of 470 grams was obtained which amounted to an efficiency of 94%. Similar results were obtained for different weights of pepper spikes fed into the hopper.
5. Conclusions
The fabricated model was found to be efficient upon testing. Also, it was possible to fabricate the machine at a reasonable cost which could further be reduced during mass production. Above all, the berries were not damaged during threshing which was the major objective of the project.
References
[1] | P Heartwin Amala Dhas and V S Korikanthimath, 2003, Processing and quality of black pepper- a review, Journals of spices and Auromatic crops, Vol. 12(1), 1-13. |
[2] | R S Khurmi and J K Gupta, A textbook on Machine Design, 2nd ed., S. Chand publisher, 1979. |
[3] | K. Mahadevan, K Balaveera Reddy, Design Data Hand Book, 2nd ed., CBS Publishers, 2013. |