S. Suhaimi1, H. Yusoff1, N. Iswadi1, Sh. Mohd Firdaus1, S. Shuib1, M. K. Abdullah2, A. A. Rashid2
1Faculty of Mechanical Engineering, Universiti Teknologi MARA, Pulau Pinang, Malaysia
2School of Materials and Mineral Resources Engineering, Universiti Sains Malaysia, Penang, Malaysia
Correspondence to: S. Suhaimi, Faculty of Mechanical Engineering, Universiti Teknologi MARA, Pulau Pinang, Malaysia.
Email: |  |
Copyright © 2016 Scientific & Academic Publishing. All Rights Reserved.
This work is licensed under the Creative Commons Attribution International License (CC BY).
http://creativecommons.org/licenses/by/4.0/

Abstract
Part of a larger study on Micro Air Vehicle flapping wing design based on bat wings, this study attempted to fabricate a bat wing skin mimic using natural rubber latex (NRL). The aim of the study was to produce a latex skin that has the closest mechanical properties of a bat wing skin. The study uses three formulas for NRL membrane fabrication; Compound A is filled with Colloidal Silica, Compound B is diluted with 50% TSC, and Compound C contains 5phr extra sulphur. Each compound is also dipped with varying dwell time; 5 seconds, 10 seconds, and 15 seconds. Results from the mechanical properties shown that Compound A produces the highest tensile strength followed by Compound C and Compound B. The results also shown that for each Compound, the tensile strength increases with increasing dwell time. The same can also be said for tensile modulus. Measurements also shown that Compound A and Compound C produces similar membrane thickness and Compound B produces thinner membrane, and longer dwell time also produces thicker membrane. Compound A at dwell time of 15 seconds has the closest properties to a bat wing skin.
Keywords:
Micro Air Vehicle, Bio-Inspired, Bio mimicry, Bat Wing Skin, Natural Rubber
Cite this paper: S. Suhaimi, H. Yusoff, N. Iswadi, Sh. Mohd Firdaus, S. Shuib, M. K. Abdullah, A. A. Rashid, Natural Rubber Latex Fabrication for Bio-Inspired Flapping Wing Skin Based on Bat Wings, Journal of Mechanical Engineering and Automation, Vol. 6 No. 6, 2016, pp. 151-155. doi: 10.5923/j.jmea.20160606.02.
1. Introduction
Micro air vehicle (MAV) is defined as a small Unmanned Arial Vehicle that has a wingspan of 15mm and has a mass of 80g [6]. MAVs main purposes are to fly in small and tight places for the use of reconnaissance and monitoring. This is because of the fact that MAVs are small allows these aerial vehicles to manoeuvre in small places like indoor areas, small pipes or in a jungle, which give rise to several design problems which are the question of manoeuvrability and the question of efficiency. One of the solutions to this problem is by looking into the design of the wing of the MAV. Wings usually are categorized into three categories; fixed wings, which are very efficient and quiet but have lower manoeuvrability. The second is rotary wings, which have higher manoeuvrability but are usually noisy and inefficient. And the third category is the flapping wings, which has better efficiency than rotary wings and more manoeuvrable than fixed wings [7].In this study will focus mainly on the design of a flapping wing since it is a good compromise between fixed wing’s efficiency and rotary wings’ manoeuvrability. Flapping wings also have the greatest design challenge between the three types of wings since it is the least explored between the three. One of the methods of designing a flapping wing is by taking inspiration from some of nature’s best flyers [3]. The reason for taking inspiration from nature’s flyers are, while there are a lot of leaps and bounds in technology made by mankind, there are still areas where technology lacks when compared to nature. In flight, mankind’s fastest plane, the SR 71 Blackbird can travel up to Mach 3, which translates, to travelling 32 of its own body lengths per seconds. Comparing this to the average pigeon, it frequently travels at 75 body lengths per second. While certain species of swifts can travel up to 140 body lengths per seconds. In terms of manoeuvrability, the A-4 Skyhawk (an acrobatic aircraft) have a roll rate of 720 degrees per seconds while a Barn Swallow have a roll rate of 5,000 degrees per seconds [12].This is because of birds and other nature’s flyers have several distinct features that give them advantage. Some of these features are; airflow can be organized and prevented from separating at large incidences die to the birds’ ability to feathering. The birds’ ability to varies its wing during flight and have multiple flight modes also allowed nature’s flyers to be far more manoeuvrable than man made ones. These capabilities are not restricted to birds only. Insects and flying mammals also have features and abilities that can offer lessons to mankind in making better flyers [13]. In this study, the focus will be designing a flyer for indoor missions, which is why this study will focus mainly on the design of a bat wing. This is because of bats have the uncanny ability to fly quietly to catch its prey and bats also are able fly in tight places and even hover [2]. In a previous work done by H. Yusoff, observed that the flexibility of the wing skin has an effect on the lift produced by the wing when flying at a quasi-steady state regime where the more flexible the wing skin is, the higher the lift generated [8, 9]. However, the study did not focus on wing mimicry but instead focused on wing flexibility in general, which does not help in understanding the advantages of an actual bat wing flight. In order to truly understand the flight of a bat wing, this study aims to fabricate a bio-inspired wing skin for a bio-inspired flapping wing design based on the wings of a bat.
2. Methodology
2.1. Rubber Fabrication Methods
In order for the closest mimic of a bat wing skin, this paper will focus on the latex compounding formulation and the dwell time, which is the amount of time which the latex is dipped in to the compound which results in different thickness, as its changing parameters.
2.2. Compounding Formula
This study uses high ammonia (HA) latex where several different ingredients were used for compounding and each of them serves a specific function (Table 1). The solution uses a 10% concentration Calcium nitrate (CaNO3) as a coagulant. For the purposes of this study three formulas that uses different amount of different ingredients in order to achieve different solutions (table 2).Table 1. Compounding solution ingredients and its uses 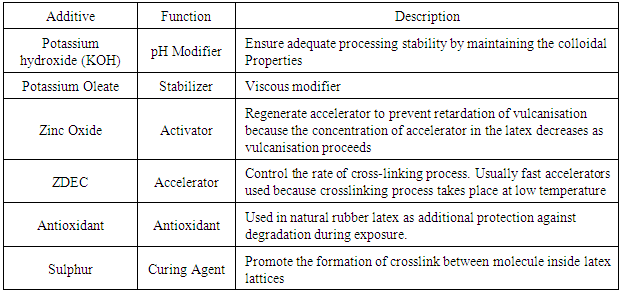 |
| |
|
Table 2. Proposed formulation for NRL membrane fabrication 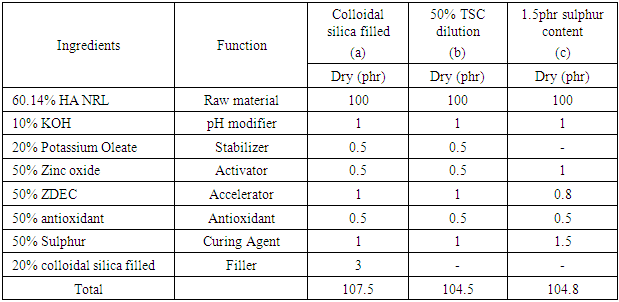 |
| |
|
The process of compounding begins by stirring the latex for 30 minutes before adding the compounding ingredients for 2 hours. The NRL used in this study has a dry rubber content of 60.7% and 61.5% according to ASTM D107610.
2.3. Natural Rubber Latex (NRL) Compound Dipping Process
In this study, the fabrication process for the NRL that was used was the straight dipping process since it is the best process to fabricate a thin, micro scale film. The fabrication process used an aluminium plate former that was roughened, cleaned and oven dried to ensure the film fabricated is as even as possible.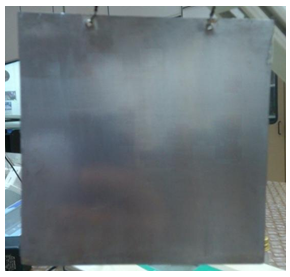 | Figure 1. Aluminium plate former |
The fabrication process begins with the aluminium plate former dipped into a small tank filled with 400 ml of pre-vulcanized compounded latex for 5 seconds. The former plate was then oven dried at 110°C for 5 minutes. Once dried, the plate former was then carefully dipped into the compounded latex formula at different dwell time. These dwell time are 5, 10, and, 15 seconds. The plate was then oven dried at 110°C for 45 minutes and left to dry at room temperature for 24 hours. Once dried, the latex film was striped from the aluminium plate using calcium carbonate as a stripping aid. Overall, 9 films was produce with 3 different compounded latex solution and 3 different dwell time for each formula.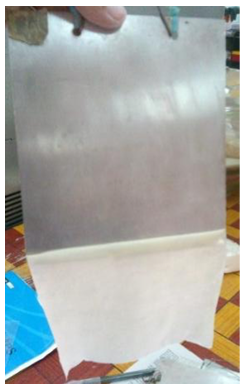 | Figure 2. Stripping process |
2.4. Latex Rubber Quality Check
The quality of the fabricated latex was checked by testing the solid content of the latex with a Total Solid Content (TSC) test using the ISO 124:1992 (E)-Third edition 1192-03-01 standard. The fabricated latexes has a TSC of 60.14% which is close to 61.5%. This means that the fabricated latex is of average quality. In order to test the ability of the latex to withstand colloidal destabilisation, a Mechanical Stability Time (MST) test according to the ISO 35- Third edition 1989-09-15 standard was made. The MST of the fabricated latex was 744s, which is higher than the ISO 35 minimum MST of 630s.
2.5. Characteristics Study
The tensile strength for the different latexes was measured using the ASTM D412 standard tensile test using an Instron machine (Model 3366) with a crosshead speed of 500 mm/min on the 33 ± 2 mm length and 6.3 ± 0.1 mm width dumbbell shaped test latex. The experiments were validated statistically according to the ASTM E1847 through repetition of the different tests.
3. Results and Discussion
3.1. Film Thickness
One of the main factors that effects thickness of the produced film is the dwell time of the dipping process where the longer dwell time will create a thicker film. The compound formula also plays a factor in film thickness where compound A and compound C were able to produce similar thickness of film at 130µm – 153µm. Compound B produced a thinner film than the other where the films has a thickness of 110µm – 123µm.
3.2. Tensile Strength
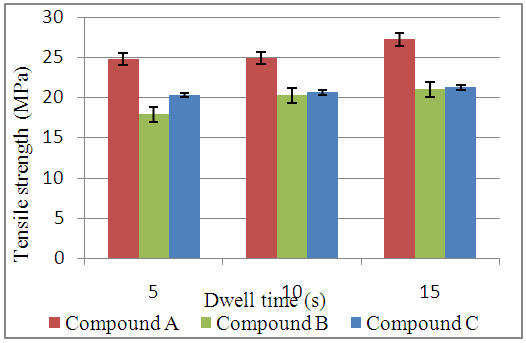 | Figure 3. Tensile strength of different compound and dwell time |
Generally speaking, the results shows that compound A produced a latex with the highest tensile strength which is followed by compound C and compound B. It is also clear that generally, a longer dwell time produces a higher tensile strength. This is true for compound A, which has the its 15s dwell time has the highest tensile strength among all of the other latexes. While this is also true for compound B, but the change in tensile strength is too low. Compound A has the highest tensile strength due to the colloidal silica filler that reinforced the NRL structure lattice by consuming the CH crystals the reducing the CH crystal size and the orientation of CH crystals, which allows for better matrix and fibre interface structure [10]. Compound C however, has a higher tensile strength than compound B because of its higher sulphur content in its formulation, which forms more cross-links in the rubber particle [11].
3.3. Tensile Modulus
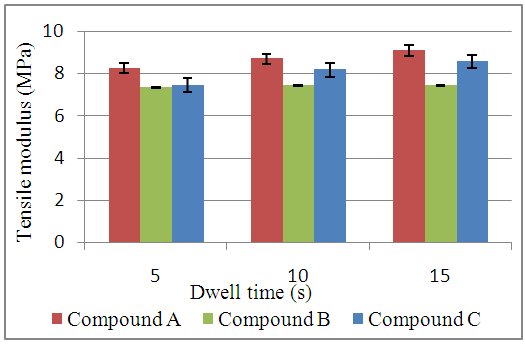 | Figure 4. Tensile modulus of different compound and dwell time |
Similar to the tensile strength, generally speaking, compound A has the highest modulus followed by compound C and compound B. This is true for all dwell time. The reason for this observation is due to the colloidal silica filler in compound A, which has stiffens NRL with increasing modulus of silica filler. Compound C has a higher modulus than compound B because compound C has more crosslink in the latex particles due to the higher sulphur content in the compound’s formula. Generally speaking, higher dwell time will produce a higher modulus value for the latex. This is less true for compound B where the change in dwell time has little change in modulus value. The reason for increase of dwell time allows for higher modulus value is due to crosslinking that formed with longer dwell time, which produces a stiffer product.
3.4. Comparison with Bat Wing Skin
According to S.M. Swartz [5], a bat wing has a tensile strength of 1.14MPa to 26.38Mpa and a Modulus value of 1.02MPa to 250.25MPa. This wide range of tensile strength and Modulus value is due to the wide variations between different bats taxa. However, compound A at 15 seconds of dwell time, with 27.21Mpa has the closest maximum tensile strength of an actual bat wing, which is 26.38Mpa. Since the tensile Modulus of a Bat wing skin varies so much, it is considered that all compounds with all dwell time can be used as a substitute.In terms of thickness however, a bat wing skin has a thickness of 160-260µm. The closest thickness that was produced by each latex compound were compounds A and C that has a thickness range of 130-153mm. This shows that compound A with a dwell time of 15seconds has the highest potential of mimicking a bat wing skin.
3.5. Results Implications
The study is a part of a larger project that aims to develop a MAV inspired by bat flight that have a capability of stable and manoeuvrable flight. The results obtained helps towards development of the MAV wings by mimicking the properties of a bat wing skin. The thin film skin will be used for the wing skin of the MAV.
4. Conclusions
From the results, it is shown that compound A has produced the highest tensile strength and tensile Modulus followed by compound C and then compound B. It is also shown that increasing dwell time also increases the tensile strength and tensile modulus for the same compound. In terms of thickness, compound A and compound C produces the thickest film (153mm), which is the closest to a bat wing skin of 160mm. Compound A with dwell time of 15 seconds dwell time has the closest tensile strength (27.21MPa) of a bat wing skin 26.38MPa. The chosen latex film that will be used for bat wing mimic is compound A that is dwelled at 15 seconds.
ACKNOWLEDGEMENTS
The authors acknowledge technical and financial support from Universiti Teknologi MARA and the government of Malaysia via the sponsorship by the Malaysia Ministry of Higher Education’s Fundamental Research Grant Scheme (600- RMI/FRGS5/3(144/2014)).
References
[1] | M.M. Afiq, A.R. Azura. Effect of sago starch on soil decomposition of Natural Rubber Latex (NRL) composite films mechanical properties. International Biodeterioration & Biodegradation 85 (2013) 139-149. Mayank Suhirid, Kiran B Ladhane, Mahendra Singh, Vishwas A Sawant, "Lateral Load Capacity of Rock Socketed Piers Using Finite Difference Approach", Scientific & Academic Publishing, Journal of Civil Engineering Research, vol.1, no.1, pp.1-8, 2011. |
[2] | T. Y. Hubel, N. I. Hristov, S. M. Swartz, K. S. Breuer. Change in kinematics and aerodynamics over a range of speeds in Tadarida brasiliensis, the Brazilian free-tailed bat. Journal of The Royal Society Interface (2012) 9; 1120-1130.A. Karnik, "Performance of TCP congestion control with rate feedback: TCP/ABR and rate adaptive TCP/IP", M. Eng. thesis, Indian Institute of Science, India, 1999. |
[3] | J. H. Evers. Biological Inspiration for Agile Autonomous Air Vehicles. Biological Inspiration for Agile Autonomous Air Vehicles. In Platform Innovations and System Integration for Unmanned Air, Land and Sea Vehicles (AVT-SCI Joint Symposium) (2007) (pp. 15-1 – 15-14).Wireless LAN Medium Access Control (MAC) and Physical Layer (PHY) Specification, IEEE Std. 802.11, 1997. |
[4] | T. Renner, L. Pék. Comparing Strength Properties Of Natural And Synthetic Rubber Mixtures. Sustainable Construction and Design (2001), pp. 134-141. |
[5] | S. M. Swartz, M. S. Groves, H. D. Kim, W. R. Walsh. Mechanical Properties of Bat Wing Membrane Skin. Journal of Zoological Society of London (1996) 239, 357-378. |
[6] | T. J. Mueller, J. D. DeLaurier. Aerodynamics of Small Vehicles. Annual Review of Fluid Mechanics (2003) 35, pp 89-111. |
[7] | K. V. Rozhdestvensky, V.A. Ryzhov. Aerohydrodynamics of flapping-wing propulsors. Progress in Aerospace Sciences 39 (2003) pp 585-633. |
[8] | H. Yusoff, M.Z. Abdullah, K.A. Ahmad, M.K Abdullah, S. Suhaimi. Experimental Study on the Effect of Skin Flexiblility on Aerodunamic Performance of Flapping Wings for Micro Air Vehicles. Applied Mechanics and Materials Vol. 629, pp 18-23. |
[9] | H. Yusoff, N. Iswadi, A.H. Zulkifly, Sh. M. Firdaus, M.Z. Abdullah, M.K. Abdullah, S. Suhaimi. Lift Performance of A Cambered Wing for Aerodynaimc Performance Enhancement of The Flapping Wing. Jurnal Teknologi (Sciences & Engineering) 75:8 (2015) 43-47. |
[10] | Santos, S.F. Sergio Francisco Rodrigues, José De Anchieta Tonoli, Gustavo Henrique, Denzin Almeida, Alessandra Etuko, Feuzicana De Souza Savastano, Holmer., 2014. Effect of colloidal silica on the mechanical properties of fiber–cement reinforced with cellulosic fibers. Journal of Materials Science, 49(21), pp.7497–7506. |
[11] | Blackley, David Charles. Polymer latices. Vol. 2. Springer Science & Business Media, 1997. |
[12] | Wei Shyy, Mats Berg, Daniel Ljungqvist. Flapping and fleexible wings for biological and micro air vehicles. Progress in Aerospace Sciences 35 (1999) 455-505. |
[13] | Kirill V. Rozhdestvensky, Vladimir A. Ryzhov. aerohydrodynamics of flapping-wing propulsors. Progress im aerospace Sciences 39 (2003) 585-633. |