Yunchan Shin1, Gwanghyun Im1, Honghyun Cho2
1Graduate School of Mechanical Engineering, Chosun University, South Korea
2Department of Mechanical Engineering, Chosun University, South Korea
Correspondence to: Honghyun Cho, Department of Mechanical Engineering, Chosun University, South Korea.
Email: |  |
Copyright © 2016 Scientific & Academic Publishing. All Rights Reserved.
This work is licensed under the Creative Commons Attribution International License (CC BY).
http://creativecommons.org/licenses/by/4.0/

Abstract
Oil pump can reduce the weight by using the Al material. In addition, it is possible to make a low noise, high efficiency, and high power. In this study, the analytical study on the performance characteristics of power steering oil pump was carried out theoretically by using PUMPLINX. As a result, at the 1000 RPM which is idle state, the discharge flow rate and driving torque are very low. As the rotational speed increases, the fluctuation of discharge pressure increases and the total efficiency decreases. When the rotation speed is 1000, 2000, 3000 rpm, the volumetric efficiency is 62.7%, 56.8%, 47.6% and torque efficiency is 24.2%, 22.8%, 22.5, respectively. Total efficiency is 15.16%, 12.96%, and 10.7%, respectively.
Keywords:
Oil pump, Discharge flow rate, Volumetric efficiency, Torque efficiency, Total efficiency
Cite this paper: Yunchan Shin, Gwanghyun Im, Honghyun Cho, Performance Analysis of Power Steering Oil Pump Applying Al Material, Journal of Mechanical Engineering and Automation, Vol. 6 No. 4, 2016, pp. 75-77. doi: 10.5923/j.jmea.20160604.01.
1. Introduction
Recently, there is a rising interest on the problem for decreasing weight of commercial vehicle. Oil pump can reduce the weight by using the Al material. In addition, it is possible to make a low noise, high efficiency, and high power. Power steering can reduce the force needed to turn the steering wheels of automotive. Also, it is mainly equipped into the midsize and full size car in order to improve steering ability. The hydraulic device is more complicated structure than the electric device and is about 4~5 kg heavier than that. However, the hydraulic device is superior on steering ability and it can make a high power.Hydraulic power steering system consists of a pressure balanced vane pump, steering gear and pulsation damping hydraulic hoses. Vane pump supplying hydraulic in power source transports the working fluid to the discharge from suction. The chamber between a cam ring, vanes and rotor causes periodically volume change due to rotational motion of rotor. Some study of oil pump using Al material has been carried out, but it is so insufficient. Especially, there has been carried out a little study for oil pump applying hydraulic power steering and discharge pressure of high pressure.In this study, the analytical study on the performance characteristics of power steering oil pump was carried out theoretically by using PUMPLINX. The result of this study is intended to provide required basic data for designing high efficiency power steering vane pump.
2. Analysis Modeling and Method
In this study, the performance characteristic of a power steering oil pump was analyzed theoretically by extracting the flow field of the vane pump. The vane tip gap of the simulation was used with the real vane value in order to ensure the reliable result. Grid number was formed by131,793 totally and the flow field was shown in Fig. 1.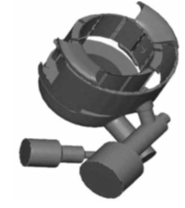 | Figure 1. Schematic of a balanced vane pump |
The analytical study on the performance characteristics of a power steering oil pump was carried out theoretically by using PUMPLINX and the simulation condition was shown in Table 1. Inlet pressure is assumed as atmospheric pressure. The performance characteristic of a vane pump was analyzed according to rotational speed from 1000 to 3000 rpm in the step of 1000 rpm. Working fluid used DEXRON-3 properties of general oil.As the rotation speed increases, a local low pressure area is presented inside of inlet port. Accordingly, density change is occurred rapidly. This phenomenon is called the cavitation. Cavitation is collapsed rapidly at the outlet with high pressure which causes a lot of noise and vibration. Therefore, analysis and protection for cavitation generation is very important.Table 1. Simulation conditions 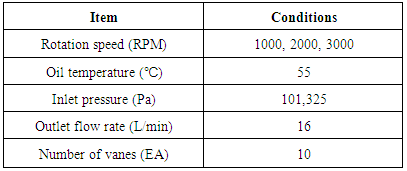 |
| |
|
In this study, Full cavitation model was used to simulate the system in order to consider one dimensional factor of cavitation. It includes some concepts like below. 1) Creation and transport of vapor bubbles2) Fluctuations caused by turbulent of pressure and velocity3) Size of non-condensable gasCreation and transport of vapor bubble are designed Raleigh plesset’s equation (1-3). And Ce and Cc of phase change rate factor are 0.02 and 0.01, respectively [1]. | (1) |
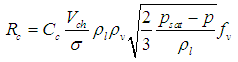 | (2) |
 | (3) |
Fluctuation caused by turbulent of velocity was used approximately. Fluctuation of pressure was simulated to increase pressure influencing the phase change. | (4) |
 | (5) |
Mass fraction of non-condensable gas has constant value. Mass faction, density, volume fraction of non-condensable gas is calculated by equation (6-8). | (6) |
 | (7) |
 | (8) |
3. Results and Discussion
Fig. 2 shows the pressure ripple, driving torque and chamber volume according to vane angle for variable rotor speeding. Pressure ripple and torque curve are not changed when rotation speed increases from 1000 rpm to 2000 rpm, while it is rapidly changed when it increases from 2000 to 3000 rpm. It can be found, as the compression starts, the pressure increases significantly. The reason for pressure drop in middle angle of compression is because of the back flow effect at the outlet [2]. Driving torque increases where vane is located and then was decreases. This tendency is repeated periodically. The average torque increases linearly with rotation speed as the rotating speed increases. Besides, the frequency of pressure increases significantly.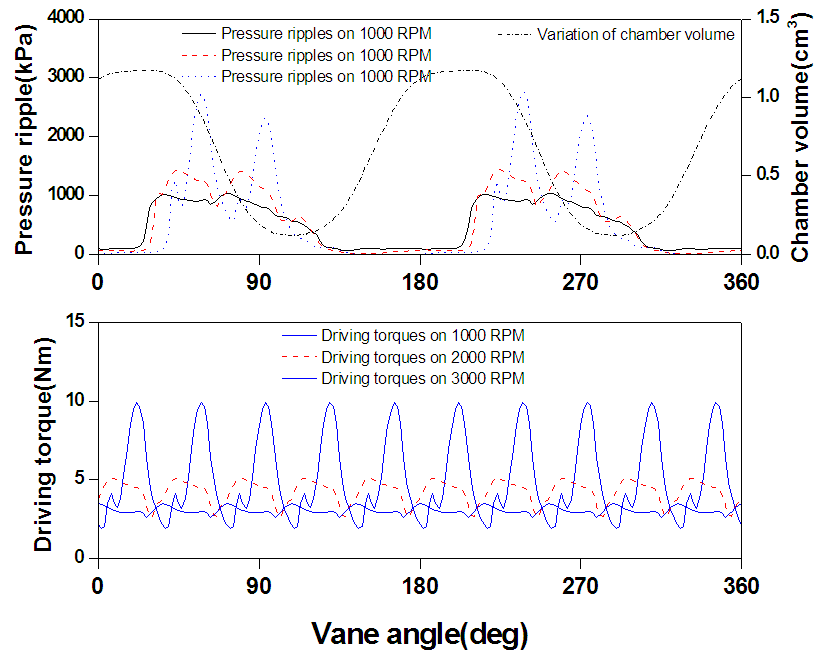 | Figure 2. Pressure ripple and driving torque in chamber with variation of vane angle and chamber volume |
Fig. 3 shows the volumetric, torque and total efficiency according to rotation speed. Volume efficiency decreases continually as rotation speed increases. It is because the cavitation in the chamber increases. In case that rotation speed is 1000, 2000, and 3000 rpm, the volume efficiency is 62.7%, 56.8%, and 47.6%, respectively. In addition, torque efficiency is 24.18%, 22.81%, 22.45%, respectively. Total efficiency is 15.16%, 12.96%, 10.7% respectively. Reduction rate of torque efficiency is relatively small. The reduction of total efficiency is mainly due to the decrease of volume efficiency by generating much cavitation.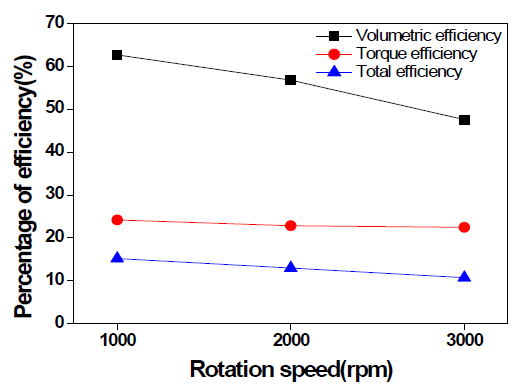 | Figure 3. Volumetric, torque and total efficiency with variation of rotation speed |
4. Conclusions
The analytical study on the performance characteristics of a power steering oil pump was carried out, and the detail results obtained through this study are as follows.1) Pressure ripple and torque curve are not changed when rotation speed increases from 1000 rpm to 2000 rpm, while it is rapidly changed when it increases from 2000 to 3000 rpm. It can be found, as the compression starts, the pressure increases significantly. The reason for pressure drop in middle angle of compression is because of the back flow effect at the outlet. 2) Volume efficiency decreases continually as rotation speed increases. It is because the cavitation in the chamber increases. In case that rotation speed is 1000, 2000, and 3000 rpm, the volume efficiency is 62.7%, 56.8%, and 47.6%, respectively. In addition, torque efficiency is 24.18%, 22.81%, 22.45%, respectively. Total efficiency is 15.16%, 12.96%, 10.7% respectively.
ACKNOWLEDGMENTS
This work (Grants No. 2014-0506) was supported by Business for Academic-industrial Cooperative establishments funded Korea Small and Medium Business Administration in 2014.
References
[1] | Brennen. C. E., 1995, Cavitation and Bubble Dynamics, Oxford University Press, 47-50. |
[2] | Ha. J. H., 2011. Latest Hydraulic Engineering, Cheongmoongak Co. Korea, 126-144. |