Choochart Phayom, Artit Ridluan
Department of Production Technology, Faculty of Industrial Technology, Surindra Rajabhat University, Surin, Thailand
Correspondence to: Artit Ridluan, Department of Production Technology, Faculty of Industrial Technology, Surindra Rajabhat University, Surin, Thailand.
Email: |  |
Copyright © 2015 Scientific & Academic Publishing. All Rights Reserved.
Abstract
This paper presented the performance investigation of the silk reeling machine powered by solar energy compared with traditional silk reeling one. The aim of this study is determine the optimum rotation speed of spinning wheel for silk reeling. The rotation speed of spinning wheel as 6, 22, 38, 54, 70, 86 and 102 rpm were tested. In this study, 3 species of silk cocoons, Nang Lai, Leung Surin and Sum Rong, were used. The silk reeling machine powered by solar energy was applied to silk reeling. It was found that the highest silk reeling rate is obtained at the rotational speed of the spinning wheel about 54 rpm. The average silk reeling rate of Nang Lai, Leung Surin, and Sum Rong is 116.2, 112.3, and 101.85 g/h, respectively. Also, it was increased from the hand silk reeling as 100.33, 96.43 and 86.23 g/h, respectively. The silk reeling rate given the solar silk reeling machine is higher than the handed silk reeling.
Keywords:
Silk reeling machine, Solar energy, Silk cocoon
Cite this paper: Choochart Phayom, Artit Ridluan, The Investigation of the Silk Reeling Machine Performance Powered by Solar Energy, Journal of Mechanical Engineering and Automation, Vol. 5 No. 1, 2015, pp. 29-32. doi: 10.5923/j.jmea.20150501.04.
1. Introduction
The origins of sericulture and silk production are closely associated with the emergence of China as one of the great civilizations. It is believed that sericulture evolved gradually and by the middle of the third millennium BC was already being used by humanity.In Thailand, there is evidence that the origin of sericulture and silk production was discovered at Udon Thani, more than 3000 years ago. And it was first developed by specialist from Japan in 1890. At presently, the northeast of Thailand is the importance region for sericulture and silk production. Silk reeling is the process by which a number of cocoons are reeled together to produce a single thread. This is achieved by unwinding filaments collectively from a group of cooked cocoons at one end in a warm water bath and winding the resultant thread onto a fast moving reel. Silk reeling may be classified into two types according to silk reeling machines in use. Hand spinning wheel, show in Figure 1, this primitive spinning apparatus is operated by two hands, one to drive the wheel and the other to feed in cocoons. One end of the reeling thread is wound onto each wheel, while cocoons are boiled in a separate pot.Silk reeling machine mechanizes the processes of groping ends, picking ends; cocoon feeding to reeling thread and separation of dropped end cocoons during the reeling process. Silk reeling machine was shown in Figure 2. It was driven by electric motor. 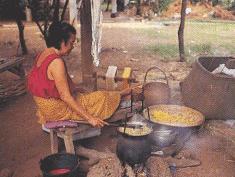 | Figure 1. Hand silk reeling |
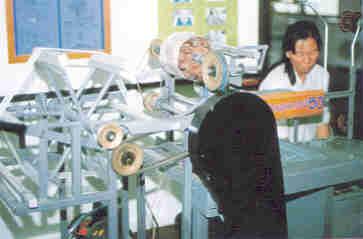 | Figure 2. UB2 silk reeling machine |
In India, Sanjay Mande, B.R. Pai and V.V.N. Kishore investigates the performance of the stoves used in the silk-reeling industry for the cocoon-cooking operation, in order to identify bottlenecks in achieving higher fuel efficiency and the ways and means to overcome these. The results show that the useful energy required for the present cooking technique/practice is about 5440 and 3660 kJ/kg cocoon for cooking in the charka and the cottage basin oven, respectively [1]. Sunil Dhingra, Sanjay Mande, P. Raman, S.N. Srinivas and V.V.N. Kishore present the technology intervention to improve the energy efficiency and productivity of silk reeling sector [2]. This technology can reduce the wood consumption of gasifier based cottage basin system for cocoon cooking in silk reeling process.Generally, the silk reeling machine was powered by electricity. It is caused by increasing the electrical consumption. Some researcher such as Panna Lal Singh investigates the silk cocoons drying with a force convection type solar dryer. It was found that a force convection type solar dryer suitable for drying silk cocoons. The air temperature in the drying chamber was 50–80C and drying time for a batch of raw cocoons was 16–19 hour depending upon intensity of sun and ambient temperature [3]. In this study, the aim of this study is design and constructs the prototype of silk reeling machine powered by solar energy.
2. Apparatus and Materials
2.1. Apparatus
The silk reeling machine powered by solar energy (show in Figure 3) consists of solar cell, silk reeling machine and boiler. The boiler was powered by Liquefied Petroleum Gas (LPG), show in Figure 4. The charger was shown in Figure 5, it was used to charge the rechargeable battery (Dry cell). The dry cell was shown in Figure 6. The spinning wheel was shown in Figure 7, it was used to spin a silk. And it was powered by the DC motor. The DC motor was shown in Figure 8. Solar cell was shown in Figure 9, it was used to produce direct current electricity from the sun light.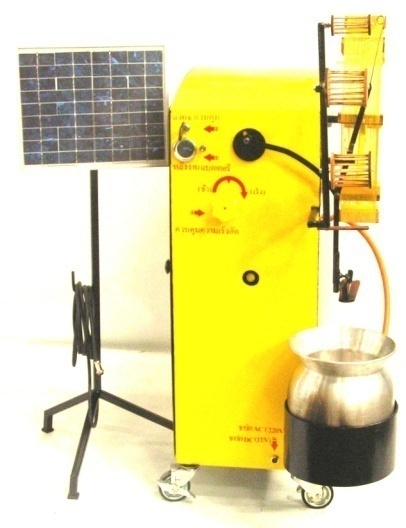 | Figure 3. Silk reeling machine powered by solar energy |
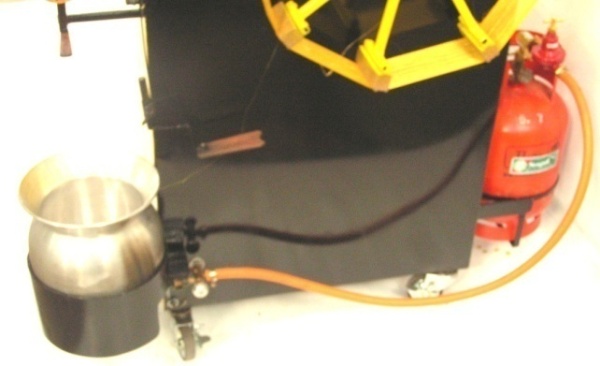 | Figure 4. Boiler |
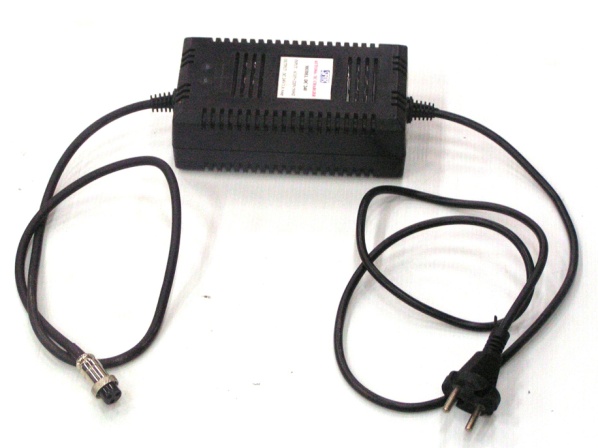 | Figure 5. Charger |
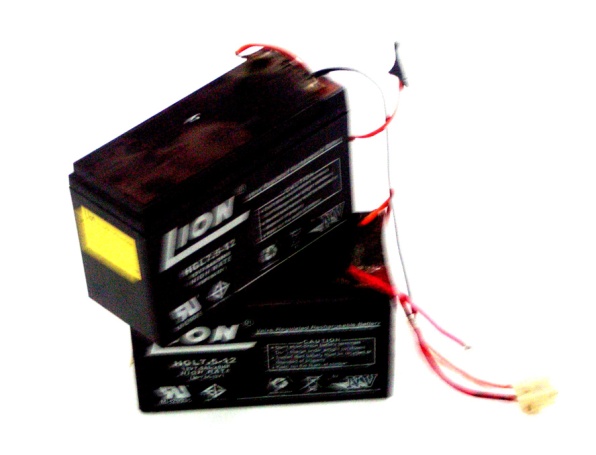 | Figure 6. Dry cell |
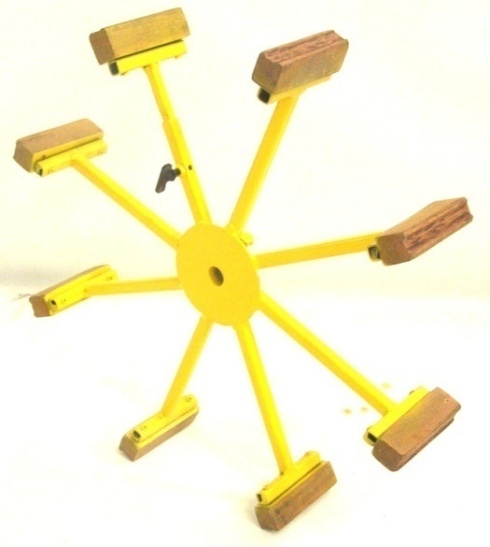 | Figure 7. Spinning wheel |
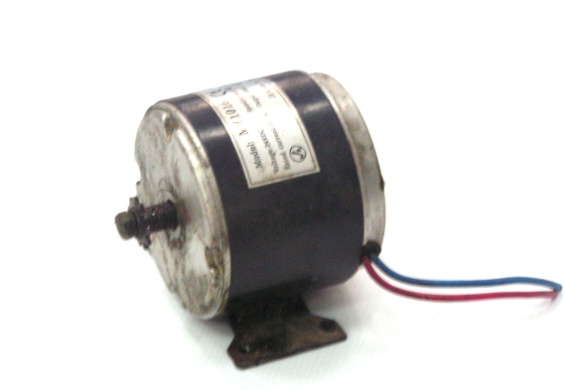 | Figure 8. DC motor |
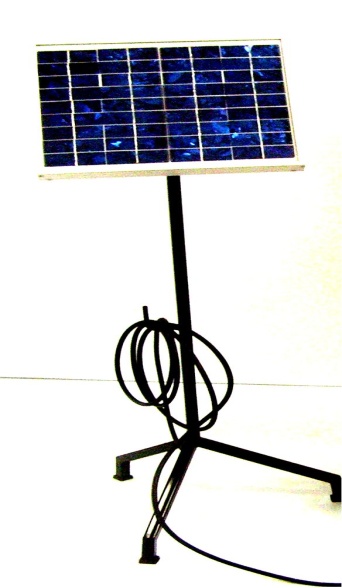 | Figure 9. Solar cell |
2.2. Raw Materials
In this study, 3 species of silk cocoon, Nang Lai, Leung Surin and Sum Rong, were used. The properties of silk cocoons were shown in Table 1. The silk cocoons were dried to protect its qualities and prepare the condition before reeling. Table 1. Properties of cocoons 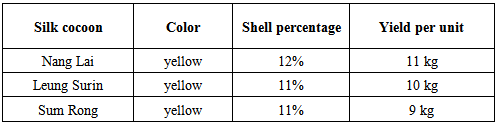 |
| |
|
3. Experimental Methodology
The silk reeling machine powered by solar energy was used to reeling the silk cocoons. 3 species of silk cocoon, Nang Lai, Leung Surin and Sum Rong, were used. For each test, 1500 g of dry silk cocoons was tested. And the silk cocoons were boiled at 75C. The boiler was powered by Liquefied Petroleum Gas (LPG). The rotation speed of spinning wheel were varied at 6, 22, 38, 54, 70, 86 and 102 rpm. It was controlled by DC motor. The performance of silk reeling machine, rotation speed of spinning wheel and silk reeling rate, were investigated and compared with the hand silk reeling.
4. Results and Discussion
Table 2 shows the performance of reeling machine powered by solar energy. In this case, Nang Lai silk cocoon was used. It was found that the optimum rotation speed of spinning wheel is 54 rpm.Table 2. Performance of reeling machine powered by solar energy (Nang Lai) 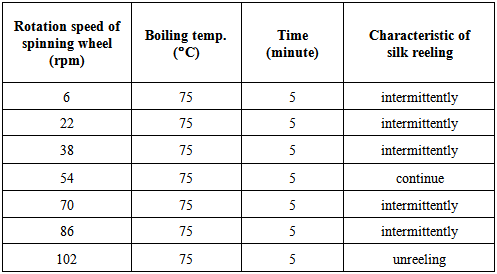 |
| |
|
The reeling machine does not applicable, at rotation speed of spinning wheel as 102 rpm. Table 3 shows the performance of reeling machine powered by solar energy. In this case, Leung Surin silk cocoon was used. It was found that the optimum rotation speed of spinning wheel is 54 rpm.Table 3. Performance of reeling machine powered by solar energy (Leung Surin) 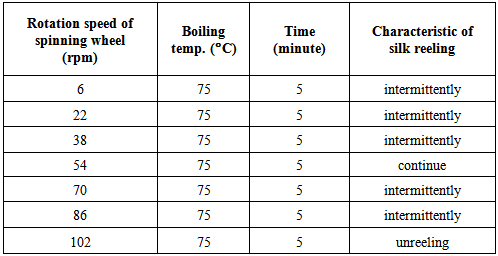 |
| |
|
The reeling machine does not applicable, at rotation speed of spinning wheel as 102 rpm. Table 4 shows the performance of reeling machine powered by solar energy. In this case, Sum Rong silk cocoon was used. It was found that the optimum rotation speed of spinning wheel is 54 rpm.Table 4. Performance of reeling machine powered by solar energy (Sum Rong) 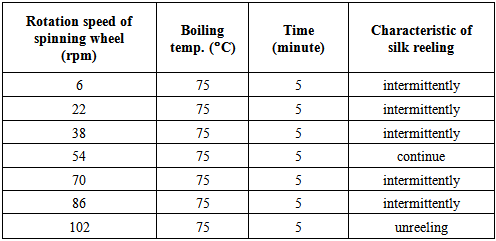 |
| |
|
The reeling machine does not applicable, at rotation speed of spinning wheel as 102 rpm.Table 5 shows the performance of the silk reeling machine powered by solar energy compare with hand silk reeling. The silk reeling rate from the silk reeling machine is higher than hand silk reeling. Table 5. Performance of the silk reeling machine powered by solar energy compare with hand silk reeling 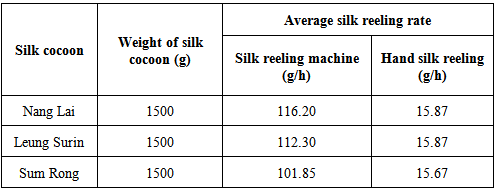 |
| |
|
For Nang Lai case, when silk reeling by using silk reeling machine, the average silk reeling rate is 116.20 g/h. But silk reeling with hand silk reeling, the average silk reeling rate as 15.87 g/h. The average silk reeling rate from silk reeling machine is increase from hand silk reeling as 100.33 g/h. For Leung Surin case, when silk reeling by using silk reeling machine, the average silk reeling rate is 112.30 g/h. But silk reeling with hand silk reeling, the average silk reeling rate as 15.87 g/h. The average silk reeling rate from silk reeling machine is increase from hand silk reeling as 96.43 g/h.For Sum Rong case, when silk reeling by using silk reeling machine, the average silk reeling rate is 101.85 g/h. But silk reeling with hand silk reeling, the average silk reeling rate as 15.67 g/h. The average silk reeling rate from silk reeling machine is increase from hand silk reeling as 86.23 g/h.
5. Conclusions
This study investigates the performance of the silk reeling machine powered by solar energy compare with hand silk reeling. 3 species of silk cocoons, Nang Lai, Leung Surin and Sum Rong, were used to test. The importance parameters used to describe the performance of the silk reeling machine are rotation speed of spinning wheel and silk reeling rate. The rotation speed of spinning wheel as 6, 22, 38, 54, 70, 86 and 102 rpm were tested. It was found that, when used the silk reeling machine, the optimum rotation speed of spinning wheel was 54 rpm. The average silk reeling rate of Nang Lai, Leung Surin and Sum Rong is 116.2, 112.3 and 101.85 g/h respectively. And it was increased from the hand silk reeling as 100.33, 96.43 and 86.23 g/h respectively. The silk reeling rate from the silk reeling machine is higher than the hand silk reeling.
ACKNOWLEDGMENTS
The author would like to thank Surindra Rajabhat University, Thailand for supporting by grand fund.
References
[1] | Sanjay Mande, B.R. Pai, V.V.N. Kishore. (2000). Study of stoves used in the silk-reeling industry. Biomass and Bioenergy, 19, 51–61. |
[2] | Sunil Dhingra, Sanjay Mande, P. Raman, S.N. Srinivas, V.V.N. Kishore. (2004). Technology intervention to improve the energy eciency and productivity of silk reeling sector. Biomass and Bioenergy, 26, 195 – 203. |
[3] | Panna Lal Singh. (2011). Silk cocoon drying in forced convection type solar dryer. Applied Energy, 88, 1720–1726. |