Mukhtar M. A. Morad, Jasem Alrajhi
Department of Automotive, And Marine Engineering Technology, College of Technological – PAAET, Studies, Kuwait
Correspondence to: Mukhtar M. A. Morad, Department of Automotive, And Marine Engineering Technology, College of Technological – PAAET, Studies, Kuwait.
Email: |  |
Copyright © 2014 Scientific & Academic Publishing. All Rights Reserved.
Abstract
There are a number of things that can go wrong with vehicles cooling system, causing the engine to run warmer than it should. Most engines today are designed to operate within a normal temperature range of about 90-115 degree℃. relatively constant operating temperature is absolutely essential for proper emissions control, good fuel economy and performance.
Keywords:
Engine Performance, Kuwait Temperature
Cite this paper: Mukhtar M. A. Morad, Jasem Alrajhi, The Effect of High Temperature on Engine Performance in Kuwait Conditions, Journal of Mechanical Engineering and Automation, Vol. 4 No. 2, 2014, pp. 55-62. doi: 10.5923/j.jmea.20140402.02.
1. Introduction
The demands on engine cooling systems have risen dramatically over the past two decades. Factors that have driven this rising demand are an increase in the number of the fluids that need cooling, a push for higher power output, and the implementation of stricter emission regulations. However internal combustion engines run on heat to produce energy in a mechanical form due to conversion chemical energy to heat energy. Thus all heat engines need cooling to operate, and remove energy fast enough to keep temperatures low so the engine can survive, the basic concept of the liquid cooling system is generally understood, that there is excess heat generated in the engine that must be expelled through the radiator, and that heat is carried from the engine to the radiator by the flowing liquid inside.
2. Cooling System Theory
An Internal Combustion engine is very good at converting chemical energy to heat energy. When gasoline and air is burned with proper mixture ratio, about 14.5 parts of air for each of fuel by mass, the result is very near to 100% efficiency of the conversion in making all possible heat with minimal fuel remaining. Unfortunately the same internal combustion engine is not so good at converting heat energy into mechanical energy. Typical thermal to mechanical conversion efficiency is in the range of 25% to 35% with 50% being to the current world record (but not in a car engine). The remaining 65% or more of the available heat which is not converted to mechanical output has to be expelled or disposed of in some manner. Much of it goes out the tail pipe as heated exhaust gas. Some of it is radiated away from the exhaust system and other engine parts as infrared energy, while some more is carried away by thermal conduction to surrounding air.The science of heat transfer provides the basis for cooling system as
Whereq= heat transferredm= massΔT=difference in temperaturecp= specific heatThe amount of heat that can be transferred from one part to another is directly proportional to the difference in temperature between the two parts. (ΔT). For the radiators, as the difference between ambient air and engine coolant temperature increases, the volume of air required to cool the fluid decrease. This law has a dramatic effect on air flow requirements as the temperature of the air approach the temperature of the fluids being cooled by radiator. The heat transfer formula from above can be re-written to apply directly to a radiator. As
Cfmr = the required airflow generated by the cooling fan Q= the required amount of heat rejected into the air to maintain proper engine temperature.
Mechanic Of Airflow The energy required to move something varies with the square of the speed with which it moves. The formula that describes this relationship can be written as
Where e=energym=massv= velocityThe implication of this relationship on airflow through a radiator is straight forward.It is necessary to move more air through a radiator, it is necessary to increase the speed of the air since the effective area of the radiator remains static.Power Requirements of Airflow:The empirical relationship between airflow and the power required to generate that airflow is displayed by a well-known Fan Law, Written as
Where hp1= power draw of the existing airflow hp2=power draw of the desired airflowcfm1 =the existing airflowcfm2=the desired airflow The implications of the above formula are far-reaching. The power draw to an increase in airflow is directly proportional to the cube of the ratio of airflow increase. Therefore, in order to increase the airflow through a radiator by 2 times, an increase in power of 8 times will be required.Impact of Fan Diameter:By increasing the diameter of the cooling fan, the same amount of airflow can be generated at a lower velocity. Since area varies with the square of diameter, velocity varies with the square of diameter, and as earlier stated, energy varies with the square of velocity. Therefore, it follows that the fan power varies inversely with the diameter to the fourth power. This relationship is expressed as
Where hp1= power draw of the existing fanhp2= power draw of the desired fan
= the diameter of the existing fan
= the diameter of the desired fanThis means 10% larger fan/radiator will use 32% less horse power to move the same volume of air. It is important to use the largest radiator and fan arrangement that design constraints will allow.
3. Engine Overheating Causes
Understand that overheating problems may be caused by a low cooling level, the radiator being plugged, the thermostat may be stuck, or other related common cooling system problems. Overheating can be caused by decreases the cooling system’s ability to absorb, transport and dissipate heat. Poor heat conductivity inside the engine because of accumulated deposits in the water jackets, a defective thermostat that does not open, poor airflow through the radiator, a slipping fan clutch, an in operative electric cooling fan, a collapsed radiator hoses, an eroded or loose water pump impeller, or even a detective radiator cap. High ambient temperature, driving at high thermal load causes consequences of overheating. The first phenomenon if gasoline engine operates at high temperature engine will start to detonate, and start to lose power under load as the combustion of heat and pressure exceed the octane rating of the fuel. Overheating can also cause pre ignition. Hot spots develop inside the combination chamber that becomes a source of ignition for the fuel. This will leads to auto-ignition even without the electric spark.
4. Test Rig and Experimentation
The test rig as shown in Fig (1) was further developed and commissioned. The values of thermal conductivity for different compositions of radiator liquid (a mixture of Ethylene Glycol and water) were obtained by empirical relations and the liquid tested on the rig, so the function of the liquid cooling system as a whole is to precisely control and expel only the exact amount of heat, necessary to keep the engine operating in thermal equilibrium, at or near a fixed desired temperature, this temperature control function is performed by the thermostat.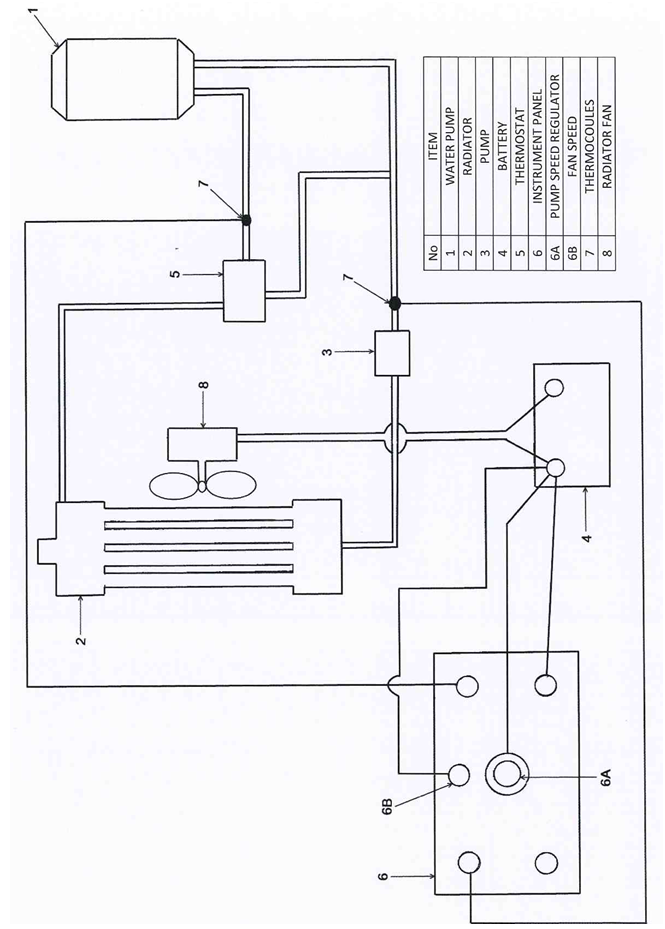 | Figure (1). The Test Rig |
The testing comprised the following. A thermex water heater (1) was used for heating the radiator cooling liquid by electricity to selected temperature that simulated the working temperature in an engine. The cooling liquid was pumped to the radiator (2) by an electric pump (3) for re-cooling. A conventional water pump, different from the pump in car engines, was used so as run at different speeds through a speed regulator. A fan (8) which was powered by a 12 volt battery (4) provides a smooth airflow the radiator fins whenever required. Thermostat (5) controls the coolant temperature due to varying load and speed, which inserted between the outlet of the radiator and the inlet of the water heater so as to allow excess cooling liquid flow through the radiator when the temperature in the water heater exceeded the rated temperature of the thermostat. The instrument panel (6) comprised the temperature measurement by two thermocouples (7) which were at the inlet of the water pump and exit of the thermostat, the switches for the fan (6a) and battery, and the speed regulator. For the pump (6b). The test procedures will be carried out at different cooling liquid concentration ratios, and different cooling fan speed and diameters, radiators larger and thicker will be used to improve cooling capacity. In additional replacing radiator cap with higher pressure capability will be used to increase poiling temperature. The above main components will describe in the following sections.
5. Radiators
A radiator is basically a heat transfer core to transfer waste heat from cooling media to the atmosphere through fins. Radiator types:Fig (2) shows the two main types of radiators 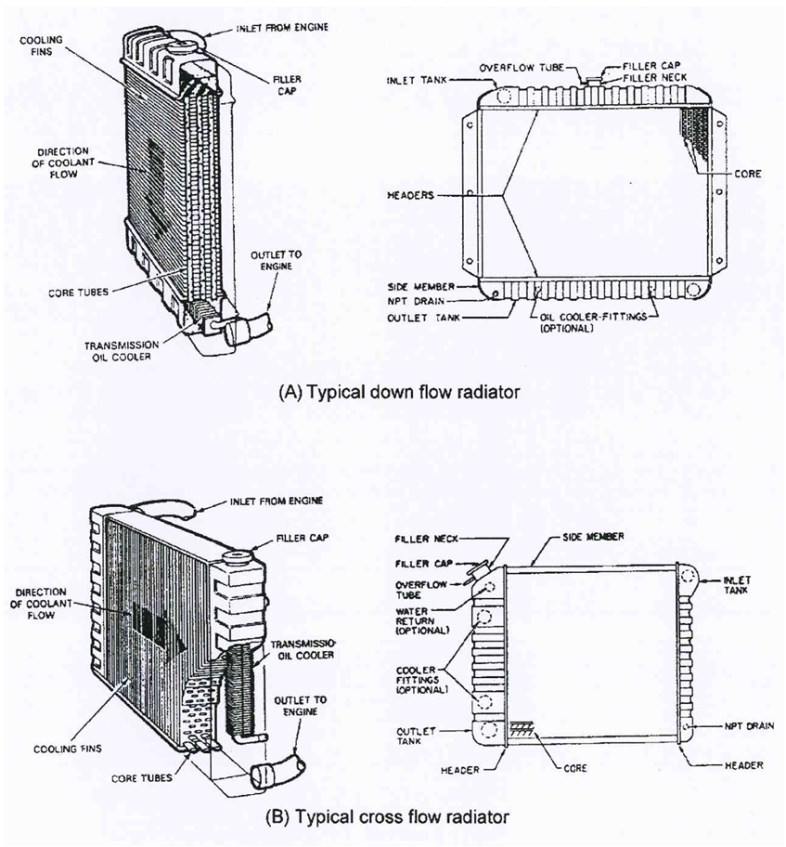 | Figure (2). Two types of radiators |
Down flow radiator:This refer to the direction of the coolant through the radiator for this tanks are on the top and bottom and the core tubes are vertically. The coolant from the engine enters the top tank. The coolant flows downward through the core tubes. After cooling, coolant flows out the lower tank and back into the engine. Cross flow radiator:This is a more modern design that has its tank on the sides of the core. The core tubes are arranged for horizontal coolant flow. The tank with the radiator cap is normally the outlet tank. This type can be shorter allowing for lower law load.Law flow radiator:This is normally a down flow type where only a small portion of the engine coolant flow is passed through the radiator even under fully open thermostat condition.Split Flow Radiator:It has a single coolant tank and dual flow type used on some high power engine applications. The low flow portion of the system provides a large coolant temperature drop in combination with a higher coolant flow portion of the system.Folder radiator:A self- cleaning care with multiple narrow width (Sectional) core, arrange to form a series of vertical vee’s is provided.Core Materials:The commonly used material has been copper fins and brass tubes bonded together by a low temperature solder. In severe environmental cores have solder coated steel fins, solder borded to brass tubes. Aluminum tubes expanded into Aluminum fins have also been used when weight saving and cost is of important. For some special applications, copper round tubes are expanded into copper or aluminum fins, often when higher pressure are require. Core types:Basically there are of these types normally, tube type and cellular type.Oval tube and plate fin:As used in practice to heavy duty vehicles, construction and farm vehiclesOval tube serpentine fin:This is the most common type of automotive care by nature of its ability to be automated in production.Round tube and plate fin:This may be used in smaller, lower power, passenger cars. Removable type:For severe conditions, the core consists of individually heavy walled round tubes that are flattened in the area between headers. Corrugated heavy fins are borded to the tubes. The rawdes tube ends are sealed coolant tight into the heades by means of a rubber – like grommet each tube can be individually removed.Silicone headerFor locomotives are severe off- highway services core are made using a composite header consisting of a silicone compound that bonds together a steel header reinforcement with short brass tubes arrangers, as match the core tube pattern. The use of silicone allows the core to be isolated from severe vehicle vibration. Fans:A fan a volume of air through its radiator core to remove heat from the coolant. This flow of air also provides cooling of the engine. The fan provides most of the air flow through the radiator at low travel speeds when the forward motion of the vehicle forces comparatively little air through the core. Fan shrouds direct the flow of air, reduces recirculation of air around the tips of the fan blades, provides more uniform distribution of the air through radiator and thereby improves fan efficiency for more effective cooling.Fan types:Flex FanThis has thin, flexible blades that alter in flow with engine speed. At low speeds, the fan blades remain curved and pull air through the radiator. At higher engine speeds, the blades flex until they are almost straight. This reduces the fan action and saves engine power.Viscous fluid coupling “Fan Clutch”This is designed to slip at higher engine speeds. It performs the same function as flex fan. The clutch is filled with silicone based fluid.Electric-motor-drive fan:It uses an electric motor and a thermostatic switch to provide cooling action. As electric motor spins the fan only when it is needed. The switch controls the fan automatically. Normally such a fan does not operate at cruising speeds.Thermostatic Fan Clutch:This has a temperature sensitive bimetallic spring that controls the fan action. The spring controls oil flow in the fan clutch. When it is cold the spring causes the clutch to slip speeding engine worm up. After reaching operating temperatures, it allow the clutch, providing forced- air circulation.Thermostats:A thermostat is a self contained, heat operated; flow modulating is or diverting type of valve assembly that is actuated by a temperature sensitive power element, this element expands during the heating cycle while moves the valve off its seat and allow coolant flow through radiator. During the cooling cycle as the power element controls, the valve is mechanically returned to its seat by a spring. A thermostat is typically located between the engine outlet and radiator. Some systems may place it between the radiator outlet and the engine inlet.
6. Results and Discussion
In order to select the suitable coolant mixture g Ethylene- glycol and water were considered. Liquid Ethylene- Glycol has greater density than water and is performed for it's anti-freeze and anti corrosion properties. Fig (3) gives the values of thermal conductivity of the mixtures that were obtained empirically (12). It is seem from this figure that the thermal conductivity decreases with the increase in the percentage of Ethylene- Glycol with a compromise to attaining abetter anti-corrosion - anti- freeze properties and thermal conductivity, a mixture of 25% Ethylene-Glycol and 75% water is recommended for use. Although the use of propylene Glycol is becoming promising (6.8), yet it has been popular so far in Kuwait. The temperature were obtained by means of two thermocouples which were located at the inlet of the inlet of water pump and the exit of the thermostat as show in fig (1). Thus the temperature difference, ΔT, for that coolant was measured under different conditions. The inlet temperature of a mean increase of 90℃ was drived by heating the water in the boiler. The increased temperature difference could be interpreted as the increase in engine load. These different types of radiators, fans and thermostats were employed there were.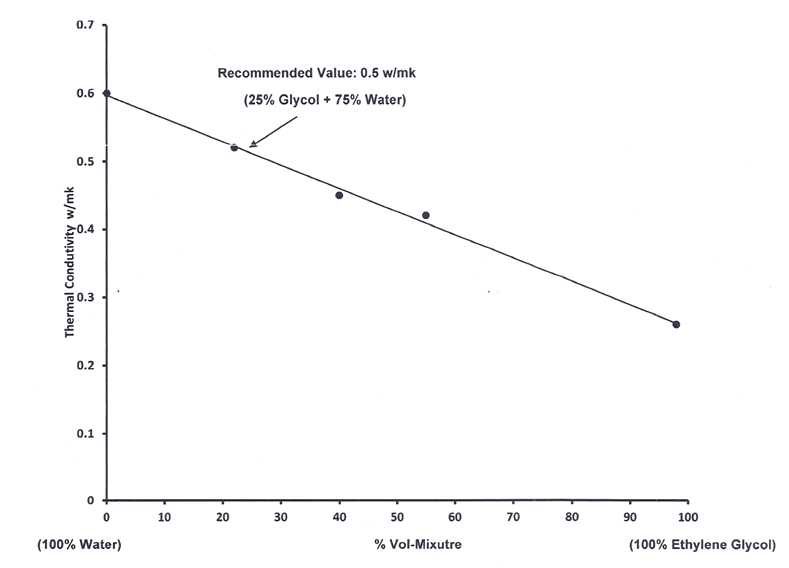 | Figure (3). Values of thermal conductivity for different coolant compositions |
Radiators as shown in figuresType 1, Type 2, Type 3, Fans, Type A, Type B, Type CThermostat: Figure (4) shows a typical relationship between the temperature difference, ΔT. and fan speeds for radiator type 1. At an inlet temperature of 90℃. These cooling conditions were found satisfactory by performing series of tests for different combinations. It is seem from the figure that as the fan speed increases the cooling becomes effective i.e. ΔT increases. So the fan of type A seems suitable.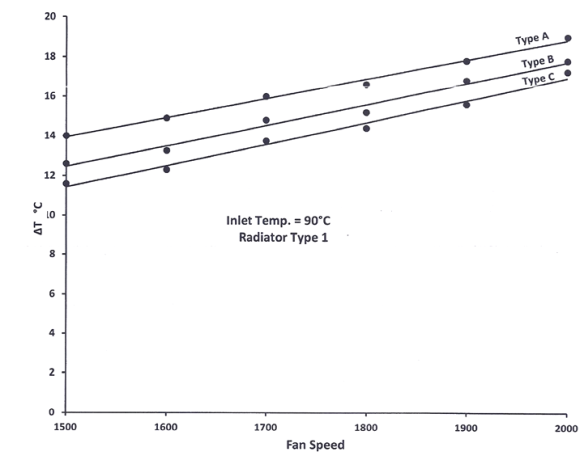 | Figure (4). Temperature Differences Against Fan Speed For Different Fans |
Figure (5) gives the typical relationship for the temperature, difference, ΔT, and the temperature at the radiator inlet for fan of type A at a speed of 2000 r.p.m for the three radiators types used. Radiator, type 1 gave a significant temperature differential and it's therefore recommended.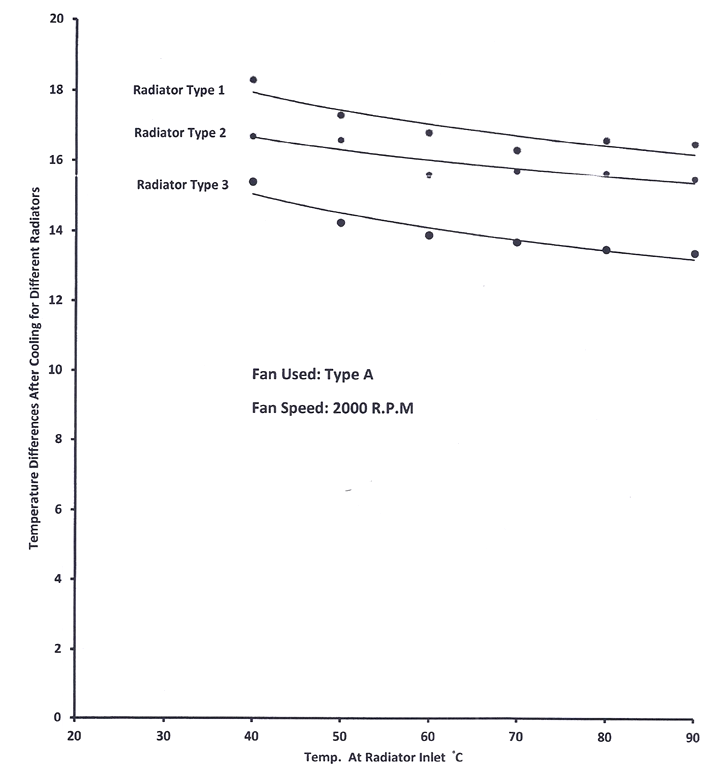 | Figure (5). Temperature Differences Against Temperature At Radiator Inlet For Different Radiators |
As was observed that the three different types of thermostats did not provide any significant effect on the cooling at different conditions. It might be that all the thermostat are mechanically operated by a spring, and the temperature difference attained in the present tests could not exhibit a clear difference in the use of the three types of thermostats.The performance test on the car engine test bed with the recommended coolant, radiation and fan could not be performed due to time limitation and non availability of a propertestrig. As intended but was not possible to use the air-conditions gas from evaporator to the compressor of the air conditioning system to study the cooling effect by this method, through this was out of scope of the present work.
7. Conclusions
A Suitable coolant, 25% Ethylene- Glycol and 75% water has been selected on the basis of it's thermal conductivity and anti-freeze properties and tested for these different types of radiators, fans and thermostats.Fan of type A. seems to be provide effective cooling of the coolant and with this fan in use, radiator of type 1, is recommended for use under Kuwait condition.Different types of thermostats do not seem to show significant effect in the cooling process. It would be worthwhile to conduct test on car engine test bed to achieve, the cooling performance with the recommends coolant, and components such as radiator and fan.
References
[1] | H Couetoux and D. Gentile 'Cooling system control in Automotive Engine" SAE paper 920788, SP-918, Feb, 1992. |
[2] | M. Hochkonig and M. Rauser "Cooling system lany-out for higher performance Cars" SAE Paper 920789, SP-918, Feb 1992. |
[3] | H Takashahietal. "Experimental Analysis for the Improvement of Radiater Cooling air- intate and Discharge" SAE Paper 920782 SP- 988 Feb 1992. |
[4] | D.A. Washington et al., "Performance of organic Baced coolant in Heavy Duty Applications SAE Paper 960644 SP-1162, Feb 1996. |
[5] | Effect of coolant miature Compositio on Engine Heat Release Rate, SAE Paper 960275, SP-1175. |
[6] | Dynamic control of the coolant Temperature for a Reduction g fuel consumption and Hydrocarbon Eroission, SAE paper 960271, SP-1175. |
[7] | Comparative Performance of Ethylene Glycol/water and Propylene-Glycol/water coolant SIN Automotive Radiator" SAE Paper 960372, SP-1175. |
[8] | Comparison of Performance g Ethylene Glycol and Propylene Glycol coolants in Heavy Duty vehicles. SAE Paper 961039, SP 11 162. |
[9] | "SAE Vehil Cooling Systems Standards Manual" SAE 175-4040, 1996 Edition. |
[10] | W.K. Taboladt et al., Automotive Encyclopedia" Good heart Wilcox 1989. |
[11] | R. B. Ltathaway and J. R. Lird back, Comprehensive Auto Mechanics". |
[12] | Wright, K.P & Czeisler, C, A Relationship between alertness, performance, and body temperature in Humans. American journal of physiology. 283, R1370-R1377 (2002). |