Oluwole O. O. , Adio M. A.
Department of Mechanical Engineering,University of Ibadan, Nigeria
Correspondence to: Oluwole O. O. , Department of Mechanical Engineering,University of Ibadan, Nigeria.
Email: |  |
Copyright © 2012 Scientific & Academic Publishing. All Rights Reserved.
Abstract
This work focused on the design and construction of a batch cassava peeling machine able to handle one diametric size of cassava tubers. The principle of abrasive peeling using a stationary outer abrasive drum and a rotating inner abrasive drum was used based on a batch capacity of 8.5 kg and cut tuber lengths of 200mm and diameters of 90mm. An average peeling efficiency recorded was 70.45 percent while the average flesh loss was 5.09 percent. Percentage of broken cassava was estimated as 2%.
Keywords:
Design, Construction, Machine, Cassava, Peeling, Peeling Efficiency
Cite this paper: Oluwole O. O. , Adio M. A. , Design and Construction of a Batch Cassava Peeling Machine, Journal of Mechanical Engineering and Automation, Vol. 3 No. 1, 2013, pp. 16-21. doi: 10.5923/j.jmea.20130301.03.
1. Introduction
Cassava, Manihotesculantacrantz, a dicotyledonous perennial plant belonging to the botananical family Euphorbiaceae is of importance in many developing tropical economies such as the tropical parts of Africa, West India, Brazil, Malagasy, Indonesia, Philippines, Malay, Thailand and China[1]. In tropical Africa, cassava and other tubers like yam form the most staple food crops which are the main source of carbohydrate in the diets of this region[2]. Its high yield in poor soil and the ability to stay in the soil for long periods after maturity make cassava an important food- security crop in low-income countries.Olukunle[3] reported that as a result of development in technologies, cassava production was needed in several areas in order to boost its utilization in oil and gas sector, for enhanced food security, means of foreign exchange and tool for rapid industrialization. However, the drudgery in post-harvest processing can be minimised or eliminated through adequate mechanised processing.Although, the cassava crop has relatively few problems in production, its problem seems to multiply at the post-harvest stage. Storage of fresh tuber, mechanization of harvesting and mechanised processing are sticking areas. The processing of cassava tubersfor industrial or human use involves different operations of which peeling is a major one. The efficiency of peeling affects the quality of the resultant product especially as regards unwanted contents. In some cases, especially when the cassava is being used for animal feed, peeling may be unnecessary[2].Cassava peeling has been practiced as far back as when cassava came into existence, but the instrument for peeling has evolved from stone and wooden flight into simple household knifes. This makes the peeling of a large quantity of cassava a drudgery[2].According to Adetan et al.[4], the cassava peel has two layers; the outer layer called periderm and the inner layer called cortex.The problems encountered in peeling cassava root tuber arise from the fact that cassava roots exhibit appreciable differences in weight, size and shape. There are also differences in the properties of the cassava peel which varies in thickness, texture and strength of adhesion to the root flesh. Thus, it is difficult to design a cassava peeling machine that is capable of efficiently peeling all roots due to the wide differences in properties of roots from various sources.This present effort is the beginning of a process to design a machine capable of peeling different sizes of cut-to-size cassava tubers. This research effort therefore seeks an uncomplicated design to make it cheap to produce and easy to use (ergometry) for post harvest workers just like the grinding machines are easy to operate for end users. Thus, this effort was focused on designing and construction of a machine that can peel a particular size of cut-to-size cassava tubers. The next effort would add–on the adjustable module for peeling various sizes.
2. Literature Review
2.1. Manual Peeling
In this method, a knife is used to manually remove the peel. It is the most common method of peeling cassava roots tuber today. However, it is rather tedius, labour consuming and still wasteful in terms of flesh loss. A manual cassava root tuber peeling rate of about 21.8kg/h has been reported[5].
2.2. Chemical Peeling
This method is the most widely used for peeling sweet potatoes in processing industries. It makes use of a hot solution of sodium hydroxide (Lye) to loosen and soften the skin of the potatoes. Igbeka[2] argued that this would not be suited to cassava peeling because a) It may require higher concentration of sodium hydroxide, higher temperature, more immersion time and operation pressure for cassava roots that have peels that are tougher than those of potatoesb) When concentration of the Caustic Soda (NaOH) is high, tuber may need to be immersed in acid solution to neutralize residual Caustic soda. This implies an addition running cost and food poisoning cannot be ruled out.c) If the cassava is to be used for garri or industrial starch production, the method will be ruled out for it results in the formation of objectionable heat ring (Dark colour) on the surface of root flesh and the gelatinization of starch.
2.3. Mechanical(Machine) Peeling
Adetan et al[4]critically and carefully designed a spring loaded cassava peeling machine with five spring-loading points ,equally spaced at 140mm intervals, were located along the length of the knife assembly with a spring rate 2.193N/mm. The cassava was then introduced in various sizes and the average height of the bed respectively to suit various tuber sizes. The result however obtained indicated that, there were 15% of broken tubers with peeling efficiency of 98.8%.In the design work carried out Odigboh[5] he designed three models of cassava peeling machine (models I, II and III. In model I an oil drum was punched about two-third millimetre diameter holes per square cm of its surface and eccentrically mounted on a shaft with a 200mmby 150mmopening to load cassava inside the drum. Cassava tubers and a predetermined quantity of some inert materials, such as quartziferous pebbles or pieces of 3.2-4.8 mm hard quarry stone are loaded into the drum which is then rotated at 40rpm. The rubbing action removed the peels from the cassava tubers, leading eventually to the complete and uniform peeling. Water is sprayed to wash away the finely abraded peels to prevent fouling and dulling of the abrasive surface. In model II balls of expanded metals were used to replace pebbles. Model III had four abrasive cylinders of expanded metal mounted inside the main peeling drum driven by a planetary gear arrangement to rotate about their axes at four times the r.p.m of the main drum, in addition to balls of expanded metals also loaded into the drumwhich is then rotated at 40 rpm.
3. Methodology
Based on a batch process with a designed capacity of 8.5 kg and cut tuber lengths of 200mm and diameters of 90mm, a cassava peeling machine having an inner peeling drum wasof 12cm diameter, 520cm long and the outer drum 30 cm diameter, 550 cm long was designed and constructed. This means six cut tubers would be peeled at a batch, two cut lengths per row and three rows. The outer peeling drum was fixed, while the inner peeling drum was made to rotate. The power requirement was calculated as 0.89 horse power. At a rotationalspeed of 364 rpm and 394 rpm were used for the trial runs. The average peeling efficiencies were recorded. The full design considerations are as follows:
3.1. Design Considerations
3.1.1. Capacity Design
The machine was designed to accommodate 6 cut tubers of yam with each the cut yam length=200 mm and cut yam diameter =90mm and each cut yam tuber weighing approximately 1.4 kg.Total Weight= 1.4 *6=8.5 kg
3.1.2. Power Requirement to Peel Cassava
Power to peel cassava is the power required to drive the inner drum
Where P= power to turn the inner drum and v, the speed
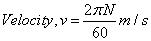
Having a factor of safety of 2 gives 0.894hp. A 1hp motor would be used.
3.1.3. Belt Design
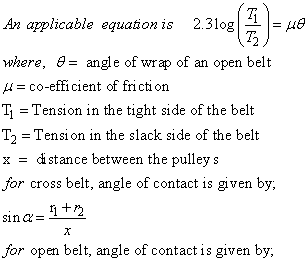
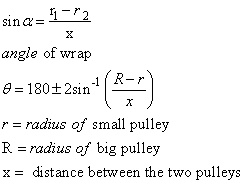
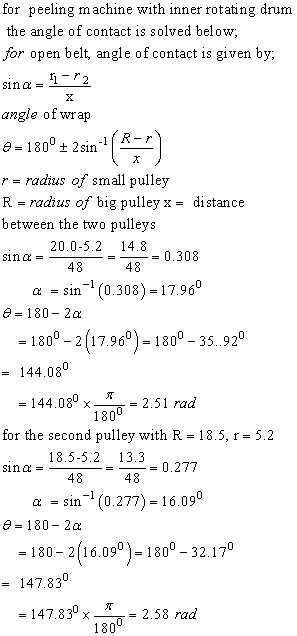
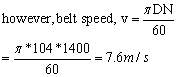
where, P = belt power (W); V = belt speed (m/s)T1 and T2 are tensions on the tight and slack sides respectively (N)
Using belt ratio for an open belt;
Where, μ = coefficient of friction between belt and pulley.For mild steel pulley and rubber belt, μ= 0.30 (khurmi and Gupta[6]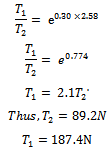
3.1.4. Shaft Design
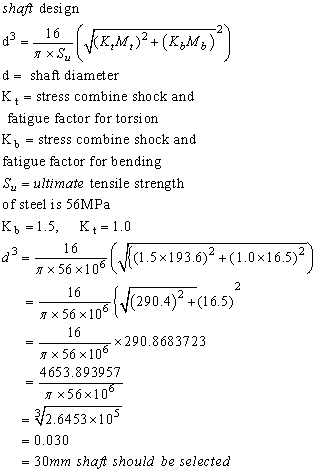
3.1.5. Velocity Ratios for Belt Drive
It is the ratio between the velocities of the driver and the follower (driven). It may be expressed mathematically as: 
Length of the belt that passes over the driver in one minute is given by
Similarly, length of belt that passes over the follower in one minute is
Since the belt that passes over the driver in one minute is equal to the length of the belt that passes over the follower in one minute.Therefore, 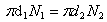


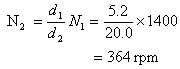

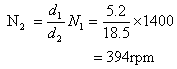
3.2. Equations Used in Trial Runs
Calculations used in the trial runs are as follows;(i) Percentage weight of peel(%)
(ii) Peeling efficiency (P.E %)
Where total weight of peels =% weight of peels
weight of unpeeled tubers
(iii) Percentage flesh loss of tubers (% F.L.)
(iv) Machine through put capacity (M.T.C )
(v) Percentage of broken cassava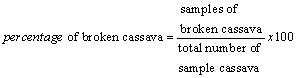
4. Results and Discussions
The results obtained from table 1 indicate manual peeling. The weight of peels and flesh are as indicated from five different weight samples carried out adjudging the machine is manned by a man. This was done for reproducibility. The result indicated that the mean weight of peels is about 16.3 percent of the total weight of the cassava and weight of flesh, 83.7 percent.The manual peeling gave an idea of the percentageweight of peels and that of peeled tubers. This is used in obtaining an assumed weight of peels and tuber in the mechanical peeling and hence the flesh loss.Table 2 presents the results for mechanical peeling using the designed peeling machine. For the two shelling speeds, time of peeling remained 5 minutes. It showed peeling efficiency decreased with increased peeling speed. The table also showed that flesh loss increased with increased peeling speed. When the inner peeling drum rotates at 364 revolutions per minutes the flesh loss was 5.07% while at 394 revolution per minutes the flesh loss was 5.97%. Which is an indication that amount or percentage of useful flesh loss with the peels, increased with an increase in speed of rotation. This is probably due to the fact that an increase in the speed of rotation increases the rate of contact of the abrasive surfaces rubbing against the cassava such that, same side of the cassava were peeled over and over until the prescribed time elapsed. The peeling efficiency could not be raised higher without further loss of fless and so it seemed a sort of compromise must be reached between peeling time and flesh loss because of the undulating nature of the cassava topography. However, it is recommended that cutting of the tubers should be made at regions where there are very close diametric dimensions to facilitate better peeling and minimise manual finishing.Table 1. Manual peeling of cassava  |
| |
|
Table 2. Mechanical Peeling of cassava tubers 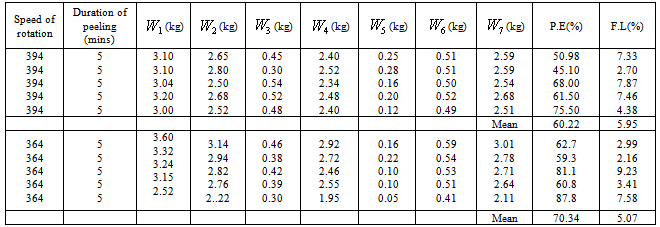 |
| |
|
Where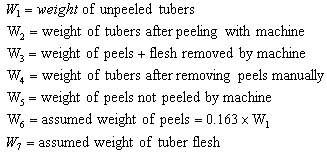
5. Conclusions
The fabricated cassava peeling machine at the speed of 364 revolution per minute had an average peeling efficiency of 70.34 per cent and an average flesh loss of 5.09 percent. However,when the speed was raisedto 394 revolution per minutes there was an average peeling efficiency of 60.22 and an average flesh loss of 5.95 percent. Hence, low speed of rotation of the peeling machine will increase the peeling efficiency and decrease percentage flesh loss and the peeling process is easier to control. A simple cassava peeling machine has been designed and constructed able to peel cut to size tubers up to a peeling efficiency of 70.34 with the trial runs performed on it. However, this design will not peel all sizes of cassava tubers. In the next stage of the design, the module to accommodate different sizes of cassava will be introduced in other to handle the peeling of all sizes of cassava tubers.
Appendix
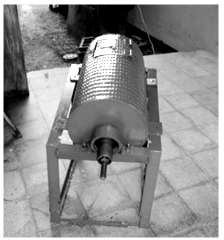 | Figure 1. Cassava peeling machine with fixed outer peeling drum |
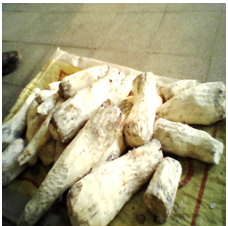 | Figure 2. Peeled cassava after mechanical and manual peeling has been done |
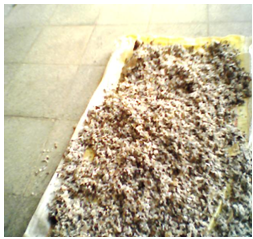 | Figure 3. Peels removed by peeling machine |
References
[1] | Ajibola O.O. (2000) “Adding value to the farmer’s harvest”ObafemiAwolowo University Lecture Series No 145. |
[2] | Igbeka, J.C. (1985) “Mechanization of tuber (cassava) peeling. |
[3] | Olukunle O.J.(2007) ‘Development of a cassava peeling machine for cottage industries. Conference on International Agricultural Research for Development. University of Kassel- Witzenhausen and University of Gottingen, October 9-11. |
[4] | Adetan D.A., Adekoya,L.,O., Aluko, O.B. and Mankanjuola,G.A. (2005) “An experimental mechanical cassava tubers peeling Machine. Journal of Agriculture Engineering and Technology’ (JAET) VOL 13. |
[5] | Odigbo, E.U. (1983) – Model III batch process cassava peeling machine presented at International Conference of Agricultureal Engineering Paper No 88.406 |
[6] | Khurmi, R.J and Gupta, J.K., (2005) A textbook of machine design, New Delhi – 110055, Eurasia Publishing House. |