Ahad Molaei1, Ramin Tabatabaei Mirhosseini2
1MSc, Civil Engineering Department, Besat Institute of Higher Education, Kerman, Iran
2Civil Engineering Department, Islamic Azad University, Kerman Branch, Kerman, Iran
Correspondence to: Ramin Tabatabaei Mirhosseini, Civil Engineering Department, Islamic Azad University, Kerman Branch, Kerman, Iran.
Email: |  |
Copyright © 2025 The Author(s). Published by Scientific & Academic Publishing.
This work is licensed under the Creative Commons Attribution International License (CC BY).
http://creativecommons.org/licenses/by/4.0/

Abstract
In this paper, the effect of Volcanic pumice (VP) on the rheological and mechanical properties of light weight concrete is investigated. In this study, by replacing 4.5, 6.75 and 9 kg/m3 of VP particles in the mentioned mixing design for concrete was used. All concrete samples made in this study were light weight. The results show that addition of particles reduces the flow and filling properties of concrete. The largest decrease is observed in the concrete floor design containing 2%. Moreover, the addition of VP particles has little effect on the compressive strength and even in cases of more consumption of these particles will lead to a slight reduction in compressive strength. Adding every three percent of VP particles increases the tensile strength, so that the greatest improvement has been observed in concrete floor containing 2% of VP particles. Also, the relationship between tensile strength and compressive strength for conventional concrete flooring and all three types of light weight concrete containing different percentages of VP particles is in the range proposed by CEB-FIP-2010 for normal concrete. Furthermore, The use of VP particles improves the flexural strength of conventional concrete; this improvement is more noticeable in concrete flooring containing 2% of VP particles. Next, the failure mode of concrete flooring samples containing VP particles under compressive, tensile and flexural tensile strength tests is different from conventional (particle-free) concrete flooring samples and is soft and gradual. Therefore, the presence of VP particles on the speed of ultrasonic waves in concrete floors is not normal. The speed of ultrasonic waves of light weight concretes both without particles and containing particles, increases with each age in each design. Finally, VP particles affect the mechanical properties of concrete and increase tensile and flexural strength and have little effect on compressive strength.
Keywords:
Light weight concrete, Volcanic pumice, Tensile strength, Flexural strength
Cite this paper: Ahad Molaei, Ramin Tabatabaei Mirhosseini, Effect of Local VPM on Mechanical Behavior of Light Weight Concrete Pavements, Journal of Civil Engineering Research, Vol. 15 No. 1, 2025, pp. 1-9. doi: 10.5923/j.jce.20251501.01.
1. Introduction
Concrete flooring is usually in the form of solid blocks that are paired together and placed on the final surface of the pavement. Concrete flooring can be divided according to production method or type of use. The flooring is mainly divided into the following two groups based on the production method: A. Vibrating and B. Pressing. On the other hand, flooring can be divided into the following two types based on the amount of load and the type of use: A- flooring and B- Non-flooring. According to the studies performed, press floors are recommended for use in container environments of port docks [1]. Concrete flooring is usually produced by dry pressing method with low water to cement ratio and is compacted in the production stage using pressure and vibration applied to the mixture. Applying pressure and vibration simultaneously during the production stage causes high resistance of the flooring Which gives it the ability to withstand heavy loads [2]. These floors have a strong and durable surface and show good resistance to heavy loads and aggressive environments. In addition, the block has a wide range of colors, textures and different layout patterns, which is very flexible and practical in terms of diversity in beauty. The structure of concrete flooring includes two surface surfaces and the bed surface. The surface is visible when using the floor and because it is exposed to abrasion; It uses fine-grained materials. But the surface of the bed, which is under the top layer and is in contact with the ground after laying the floor, is not visible; Coarser aggregates are used [3]. To find out to what extent concrete floors can meet the requirements of container docks; The experiences of previous pavements should be examined from three perspectives: technological, environmental and economic. From a technological point of view, asphalt pavement is the main type of pavement that has been used in the construction of container yards so far; Cannot be used immediately after execution. Also, the asphalt surface gradually subsides, which is a negative factor in paving ports where heavy point loads such as the load from the base of containers have to stay in place for a long time, While this problem will be solved by using concrete floors [1,3]. From an economic point of view, it should be noted that asphalt is one of the derivatives of the oil industry, which due to the high price of oil and its derivatives, many countries are taking steps to reduce the consumption of oil derivatives. More to other pavements, especially concrete floors. From an environmental point of view, it should be noted that in the process of asphalt production, bitumen needs to be heated, which causes air pollution and adverse effects on the environment. While using concrete flooring, not only is there no air pollution; Rather, it has the ability to purify surface water from dust and oily substances, drain it and transfer it to groundwater [4]. The use of concrete flooring in paving port and container areas has the following advantages:- Concrete floors are resistant to melt and frost conditions and also have high abrasion and head resistance [5].- After the implementation of this type of pavement, can be passed over it immediately [2].- The presence of gaps and executive joints between the floors is used as a tool to transfer load and cracks due to stress and non-uniformity are minimized [1]. - Considering that it is possible to repair and replace damaged floors without creating a new surface; As a result, maintenance costs in this type of pavement are reduced. Damaged floors can sometimes even be reused for minor repairs with a slight modification, resulting in a reduction in material waste [1].- Concrete flooring due to its diversity in texture and structure, patterns and colors, bring a unique beauty that in comparison with other forms of paving, has the ability to combine and harmonize significantly with its surroundings. So far, many researchers have been done on the methods of making concrete flooring and pavements, and at the same time, several researches have been done on the application of VP particles in ordinary concretes. In order to industrialize the results of the researches, in this research, we intend to produce green and environmentally friendly concrete floors that have a suitable capability for use in paving port areas [6]. In developing countries, especially in East African countries, most construction and demolition waste generation is from construction renovation. This results in environmental impacts and various natural resource pollution due to dust emissions from C & C&D wastes and scarcity of lands due to C&D debris massive accumulation to the environment [4]. Composite construction and demolition trash contained a lot of waste types and categories. Most of it includes the soil, aggregate, and sand lest overs. These waste materials can be completely recyclable and reusable in many cases [7]. Next to these categories, wood waste materials have significant parts in C&D debris groupings [8]. The applications of recycled aggregates from C&D debris in construction project work need the right and current information on these materials’ performance levels to damage the strength of the structures that contain recycled aggregate materials as a substitute for conventional aggregate materials. Based on the current recycling process in India’s capital city, Delhi, the study focused on the realization of the cases always questioned by engineering professionals and stakeholders in construction industries [3]. Identification of the fundamental behaviors of recycled aggregate materials from C&D debris encourages using such materials in existing and ongoing civil engineering and construction projects. The C&D waste contains various waste groups that need identification in the segregation process while recycling these wastes. Concrete, Insulation materials (ceilings), and brick demolition wastes are also significant contributors to the C&D debris. These categories of C&D waste exceed 20% of all the waste groups. The recycling process considers all these leftovers while producing recycled aggregate materials from them. Not only the fundamental properties of recycled aggregate materials, but the current investigation also includes the production mechanisms and current trends in the manufacturing process of recycled aggregate materials from C&D debris [9]. This way, the recycling of construction and demolition debris can add value to the area’s knowledge in recycling and recovering such waste materials [10]. And better understanding concerning recycled aggregate materials will reduce risks while using these materials in various projects works as a replacement for virgin aggregate materials [11-14].
2. Methods and Materials
In this experiment, after selecting the optimal mixing design for the production of zero slump concrete and replacing VP particles with percentages of 3, 5 and 10, the weight of coarse aggregate in the zero control slump concrete mixing design, by German MASA batching and weighing machine and mixer Up to e-Pan was prepared for the construction of concrete floors. Then, after placing the zero slump concrete inside the mold with dimensions of 80 × 100 × 200, it was produced by pressing machine in two layers of surface and bed. During the production process, the concrete floors were subjected to a compressive force of 100 bar and a frequency of 3600 Hz with a compression time of 3.5 seconds and then by a conveyor and intelligent robots into the steam room for 48 hours to process the initial steam Were transferred. After 48 hours of laying the floors in the water pool, they were wet treated until the test date.
2.1. Laboratory Program
Laboratory research is needed to make zero slip concrete that can meet the specified limitations for the properties of concrete flooring. Therefore, determining the constituent ratios of concrete floor mix, including coarse, fine-grained, water-to-cement ratios, and the required amounts of filler and superplasticizer are significant. In this research, while introducing the specifications of materials used in the manufacture of zero slump concrete, several mixing schemes are introduced to achieve a mixing scheme that meets the limitations of fresh concrete tests. Also, the optimal amount of VP particles in the construction of concrete flooring after measuring the properties of fresh concrete and hardened concrete tests are performed on the constructed samples.
2.2. Specifications of Consumable Materials
COARSE GRAIN (GRAVEL)According to the recommendations of the regulations, the maximum allowable nominal size of sand used in the manufacture of concrete flooring is 12.5 mm. (Crossing 1.2 inch sieve) The coarse grains used in this research are natural and broken. For granulation of sand used using standard sieves, the weight percentage remaining on each sieve is calculated and passed by calculating the cumulative percentage, the granulation of sand is obtained. The granulation curve is shown in Figure 1. The range of passing percentage of consumed sand corresponds to the passing range of ASTM 33 standard and Iranian national standard number 302. Therefore, according to the restrictions considered for the maximum consumption of coarse grain, it is suitable for making concrete flooring.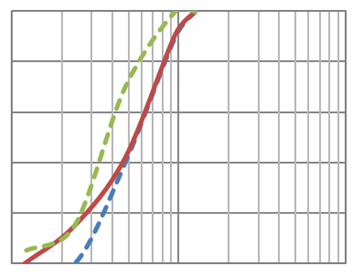 | Figure 1. Grading curve of consumed sand |
FINE-GRAINED (SAND)Since all types of fine aggregates are allowed to be used in concrete flooring, in this study, sand with a nominal size (0-6 mm) was used according to Figure 2. The range of passing percentage of consumed sand corresponds to the passing range of ASTM 33 standard and Iranian national standard number 302.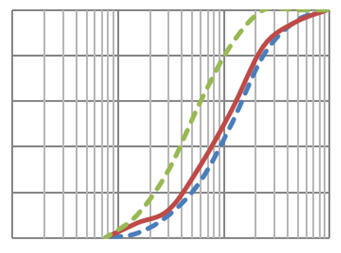 | Figure 2. Consumption curve of sand |
CEMENTThe cement used in this research is of Portland type 2 produced, which has a specific mass of 33150 kg / m and a specific surface area of 3160 cm2 / gr.WATERThe water used in the construction and processing of concrete is drinking water from kerman city, which is not a problem due to its drinking consumption for making concrete [15]. (ASTM C1602)MICRO SILICAMicro silica used as a filler. The chemical characteristics of the consumed micro silica are given in Table 1.Table 1. Chemical characteristics of consumed microsilica 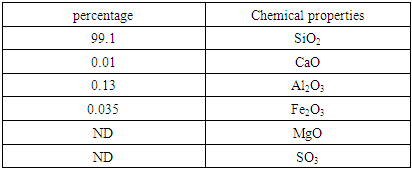 |
| |
|
VP PARTICLESIn general, all non-powdered mixed particles such as fibers, polymer and VP particles reduce the permeability and flowability of concrete. Due to this fact, the optimal amount of particles to achieve the characteristics of fresh and hardened concrete. In this research, VP particles have been physically crushed. The particles are shown in Figure 3.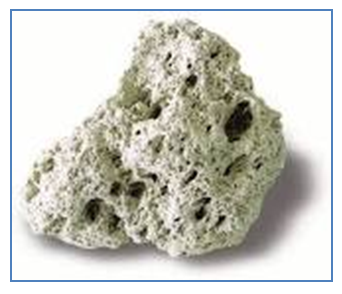 | Figure 3. Appearance of VP particles |
Table 2. Ratios of initial mixing plan of concrete flooring 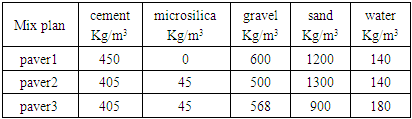 |
| |
|
2.3. Mixing Plan
Concrete floor mixing design is selected according to the concrete performance criteria for the properties of fresh and hardened concrete. The basic components for mixing ratios of concrete flooring are similar to normal concrete, but for achieving the properties of concrete flooring, the amount of fine-grained is high. The filler used in slump concrete is usually zero microsilica. In this study, for the design of concrete mixing, according to the existing criteria of the mixing design, three initial designs were considered. From all mixtures, VB slump test was performed. From the concretes that the amount of VB is in the desired range, finally a mixing plan, the results of tests of fresh concrete in the desired range, was selected as the mixing plan for concrete flooring (Control). The ratios of the three initial mixing schemes are collected in Table 2. To determine the optimal amount of VP particles to strengthen zero slump concrete, for VP particles, five values (3%, 5%, 10%, 15%, 20%) per cubic meter were added to the final mixing plan of concrete flooring. Finally, among each of the concrete floor mixing designs, the mixing design with the results of their fresh concrete tests in the desired ranges was considered as the final concrete floor mix (as control concrete). The paver3 mixing design was selected as the preferred design to start the experiment and then the percentages of VP particles replacement instead of aggregate were applied in this mixing design.
2.4. Making Concrete without Slump
To make concrete without slump, first different ratios of mixing materials were determined for a certain amount of concrete. Then, by replacing VP particles instead of aggregate in 3, 5, 10, 15 and 20 percent, concrete production began. The slump was zero and the necessary studies were performed on them. Fresh concrete tests were performed immediately after this step for each of the mixing designs. After making the concrete according to the above pattern, sampling operations were performed to check the mechanical properties and after filling the molds, the samples were kept at 24°C in the laboratory for 24 hours and after this time and open Molding The samples were subjected to steam and moisture treatment in a water bath in the laboratory processing room until the experiment.
2.5. Concrete Processing
In this dissertation, concrete samples made from concrete floor mixing designs and modified concrete flooring with VP particles were kept in accordance with the standard for 48 hours in the steam room and then placed in a pool of water until the test date.
3. Results
Investigation of mechanical properties of concrete flooring by performing tests of compressive strength, tensile strength, flexural strength and speed of ultrasonic waves, water absorption, wear percentage and frost resistance on concrete flooring samples with dimensions of 200 × 100 × 80 mm and was determined.
3.1. Compressive Strength Test Results
Compressive strength test was performed after storage in wet conditions at the ages of 3 to 28 days. Comparison of compressive strength of samples of concrete flooring (Control) and concrete flooring modified with VP particles is shown in Figure 5.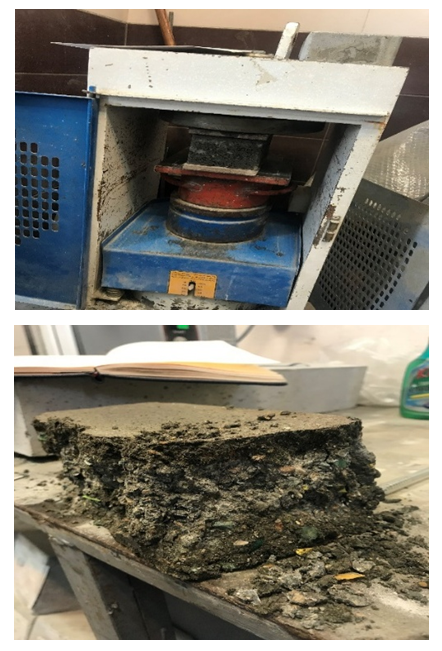 | Figure 4. Sample after compressive strength test |
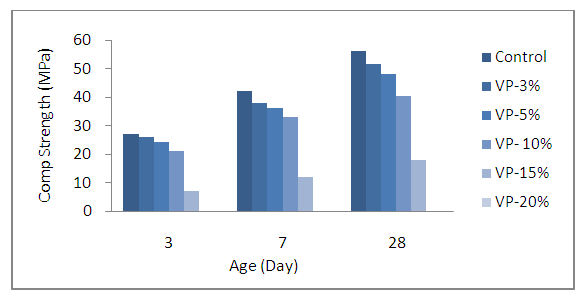 | Figure 5. Comparison of compressive strength of concrete flooring and concrete flooring containing VP particles with different percentages |
The results show that the presence of VP particles will not have much effect on compressive strength and sometimes at high doses will cause a slight decrease in compressive strength, which is more noticeable at older ages of concrete and with increasing amount of VP particles. This reduction in compressive strength may be due to the fact that the use of VP particles in the concrete floor reduces the compressibility of the concrete, which may cause weaknesses in the concrete texture (due to localized porosity due to the infiltration of air bubbles) and As a result, it provides a reduction in compressive strength. On the other hand, because VP particles have hydrophobic properties (water absorption of these particles is less than 0.15%.) They prevent the passage of water through these particles and penetration into the concrete structure to perform the hydration process. All concrete samples containing VP particles have changed their nature from brittle (sudden) failure to soft and gradual failure during compressive loading.
3.2. Results of Tensile Strength Test
Tensile strength test was performed to determine the tensile strength of concrete by halving the concrete samples tested at 3 to 28 days of age under steam and wet processing conditions. Tensile strength for each design, under the same storage conditions at the ages of 3 to 28 days, as well as their comparison are shown in Figure 7. The results show that the presence of VP particles in low percentages (3 and 5%) increases the tensile strength and as the amount of these particles increases (10 and 15%) due to the lack of proper compressibility of these VP particles, the amount of tensile strength decreases. For example, the percentage of increase in tensile strength of concrete flooring design containing VP particles by 3% by weight of aggregate compared to the control design at the age of 28 days is about 7%. The failure pattern of concrete samples containing VP particles in the tensile test is different from that of concrete flooring samples and has changed from brittle (sudden) to soft and gradual state. What happens when the tensile strength increases as a result of the use of particles can be explained by the fact that, the particles have a larger tensile strain when they split between the split parts of the matrix, by transferring stresses from the matrix to the particles. As a result, an increase in tensile strength is observed.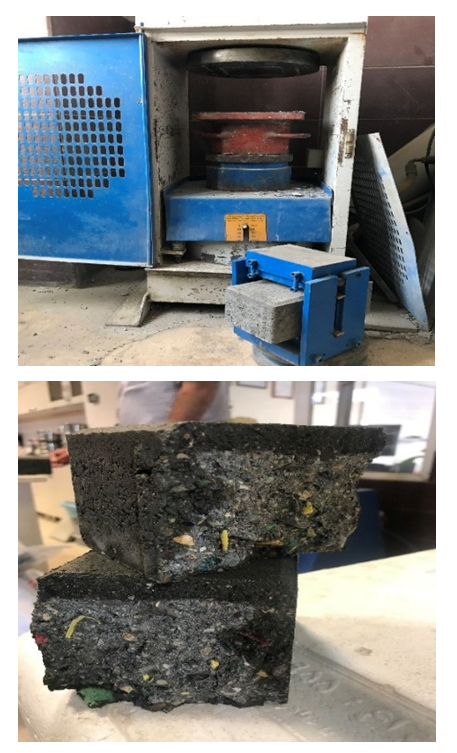 | Figure 6. Tensile strength test machine and Brazilian enclosure and flooring sample after performing tensile strength test |
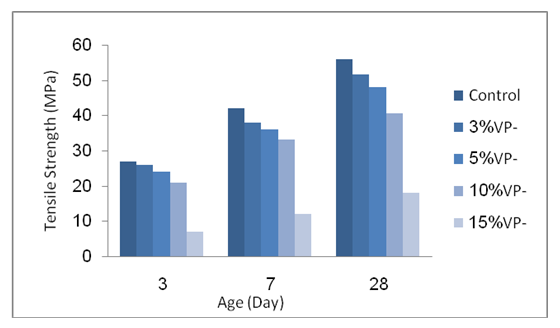 | Figure 7. Comparison of tensile strength of concrete flooring with different percentages |
3.3. Results of Flexural Strength Test
The rupture modulus test was performed by loading in the middle of the concrete floor in accordance with Regulation BS-6717. The samples were treated with steam and moisture until the test and were tested at the ages of 3, 7 and 28 days.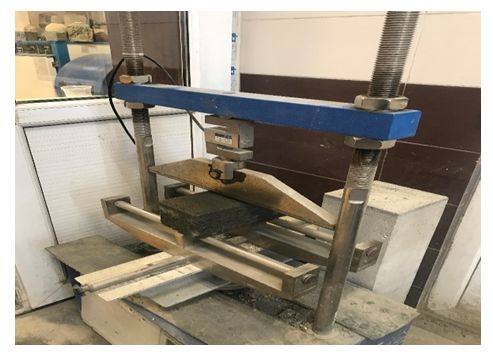 | Figure 8. Flooring under flexural strength test |
The results show that the addition of VP particles improves the flexural strength of concrete in low percentages (3 and 5%) and the higher the amount of these particles, the less effective it is in increasing the flexural strength. VP particles with 3.5 ratios, about 5 and 13 percent less than the design without particles at the age of 28 days and about 20 and 60 percent for 10 and 15 percent of designs containing VP particles.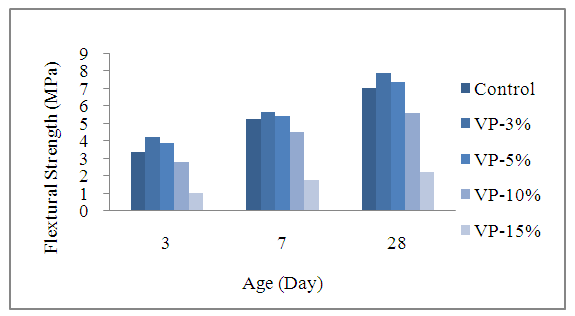 | Figure 9. Comparison of flexural strength of concrete flooring (without particles) and concrete |
In samples containing VP particles with different percentages, the use of VP particles prevents the samples from splitting brittle and after increasing the load, the rupture is not accompanied by a complete halving of the samples. The mechanism of increasing the flexural strength due to the use of particles can be explained as follows: The use of particles means a very wide connection and a short distance of particles, so after applying the load and the appearance of very small cracks in the concrete texture (microscopic cracks ), The particles will be able to prevent the cracks from spreading to macroscopic cracks and reduce the amount of stress at the crack tips by transferring stress between the edges of the cracks, thereby increasing the width of the cracks and turning the microscopic cracks into Prevent macroscopic.
3.4. Ultrasonic Wave Velocity Test Results
Ultrasonic wave velocity measurement on concrete containing VP particles with dimensions of 200 × 100 × 80 mm and at the age of 28 days, has been subjected to steam and moisture processing. This test is used to collect information about estimating the density and uniformity of concrete samples.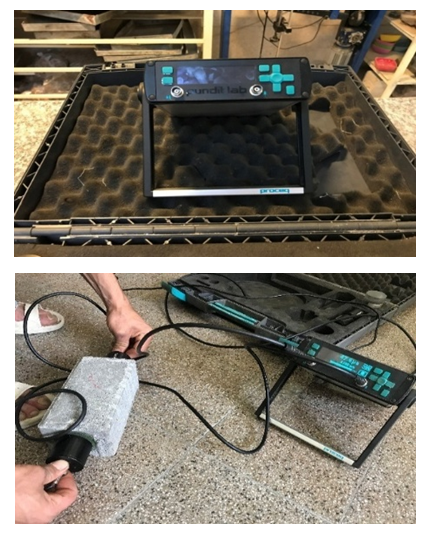 | Figure 10. Ultrasonic test device |
As can be seen from Figure 11, with increasing age of concrete specimens, the speed of ultrasonic waves in each design increases, but in general the presence of VP particles will have a slight decrease in the wave velocity, which decreases with increasing amount of VP particles. It is more tangible. This reduction in wave velocity or in other words an increase in porosity in concrete may be due to the fact that the use of VP particles in concrete flooring reduces the compressibility of concrete, which is due to weaknesses in the concrete texture (due to localized porosity). Caused by the penetration of air bubbles) and thus provide a reduction in the velocity of the waves.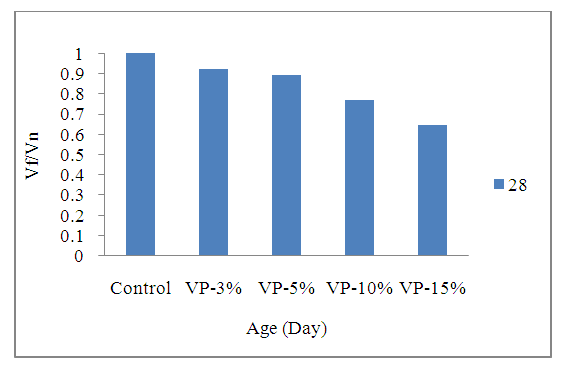 | Figure 11. Comparison of the ultrasonic wave speed ratio of concrete flooring containing VP particles (Vf) to concrete flooring (Vn) at different ages |
As can be seen from the figure above, the presence of VP particles with 3% by weight does not have a significant effect on the speed of ultrasonic waves, but the use of higher percentages has somewhat reduced the speed of ultrasonic waves.
3.5. Abrasion Resistance Results
Abrasion resistance test of concrete flooring was performed at the age of 28 days after curing by steam and moisture and with the percentage of replacement patches 3, 5, 10, with dimensions of 80 × 100 × 200 mm. Selected and tested, the amount of concrete wear was determined by grinding the surface according to EN1338 standard.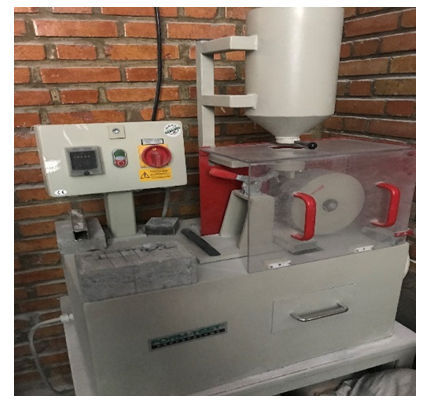 | Figure 12. Wide wheel abrasion tester with sample |
In this test, a sample of concrete flooring was placed inside an abrasion measuring device with a Fe690 steel wheel with a diameter of 20 cm and a width of 7 cm. The device also has a funnel into which abrasive material is poured. With a particle size of 80 microns and according to the FEPa42F 1984 standard. A horizontal axis drawn in the middle of the groove is drawn vertically (one completely in the middle and the other two at a distance of 10 mm from both ends of the groove). The maximum value of these lines with an accuracy of 0.5 mm is reported as the amount of wear. It should be noted that the concrete floors in category 4 are considered abrasion resistance classes that according to the standard, the results of wear of their individual samples should be less than or equal to 20 mm according to the wide wheel method. The abrasion test results are shown in Figure 13.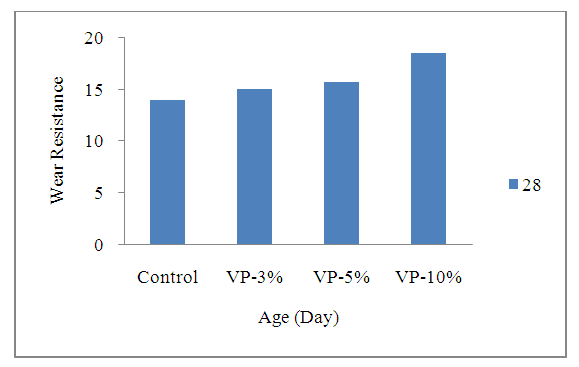 | Figure 13. Comparison of wear resistance of floors containing VP particles |
The results show that the use VP particles will not have much effect on the abrasion resistance of concrete floors and this is due to the structure of the floors because as mentioned earlier, concrete floors from Two layers of Face and main are formed and in this research, VP particles have been used only in the main layer, and since approximately 1.5 cm on the floors is made of Face layer materials and abrasion resistance test on the surface of the floor (surface) of the floor And low percentages of VP replacement (3% and 5%) no significant change compared to the control sample of flooring. However, with the increase of VP particles replacement instead of aggregate in high percentages (20,15,10), it was observed that due to VP shapes and also the presence of parts with larger dimensions than the allowable grain size in concrete floors and also elasticity. On top of the particles, by applying pressure to compact the floors during production, some particles have been observed on the surface after loading and unloading operations, and this will weaken the face layer and the results will go beyond the allowable amount of wear, which led to experiments. Abrasion percentage for floors replacing VP with high percentages of 15 and 20 percent due to not meeting the apparent requirements of concrete floors.
3.6. Total Water Absorption
The test for determining the water absorption of concrete flooring was performed at the age of 28 days after curing by steam and moisture with the percentage of alternative VP particles 3, 5, 10, 15 in the dimensions of 80 × 100 × 200.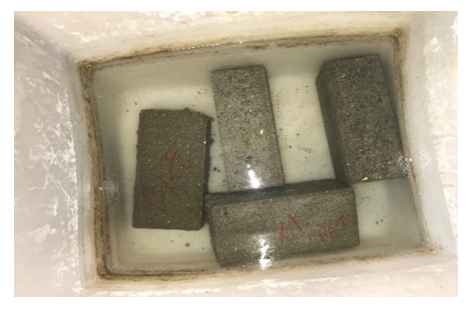 | Figure 14. Test to determine the water absorption of the entire concrete floor containing VP particles |
The amount of water absorption of concrete is determined by changing the weight of the sample in the saturated and dry state so that after preparing the test at a temperature of 20 degrees Celsius, it is submerged in water until it reaches a constant mass and then until We dry the fixed mass in the greenhouse, the mass drop is calculated and shown in terms of the percentage of dry mass. The results of the water absorption test are shown in Figure 15.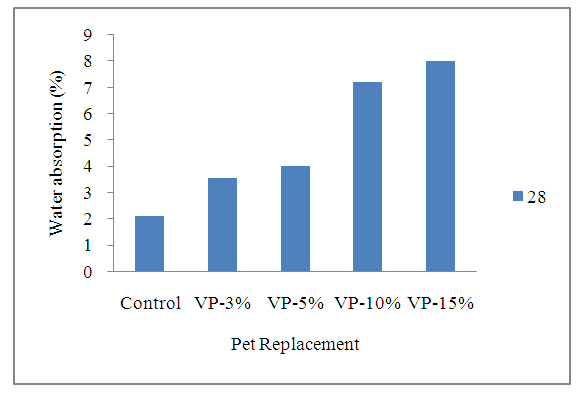 | Figure 15. Comparison of water absorption results of concrete floors containing VP particles |
According to Regulation BS-6717, the average water absorption of floors should be less than or equal to 6 on average. The results show that with increasing the amount of alternative plastic in floors, the amount of water absorption increases. This happens while VP particles have water absorption, it seems that water absorption, it is placed between empty and porous spaces and the heterogeneous shape of particles increases these empty spaces in flooring. However, with the replacement of VP in low percentages of 3% and 5%, there is no noticeable change in the results of water absorption with the control sample, but with increasing the percentage of VP, the water absorption of the samples gradually increases.
3.7. Results of Resistance to Frost and Thawing with Defrosting Salts
Melting and frost resistance test of concrete flooring was performed at the age of 28 days after curing by steam and moisture and with replacement percentages of 3 and 5 VP particles with dimensions of 80 * 100 * 200 mm, to determine the amount of frost resistance Melting with defrosting salts is done according to BS1338 standard.In this test, a sample of concrete flooring is prepared and then, while its surface is covered with 3% sodium chloride solution, it is exposed to 28 cycles of freezing and thawing at a temperature of 20°C, and after testing the materials removed from the surface. It is collected and weighed and the result is reported in kilograms per square meter. The results should be on average less than or equal to one and individually less than or equal to 1.5. The results of the ice test are shown in Figure 17.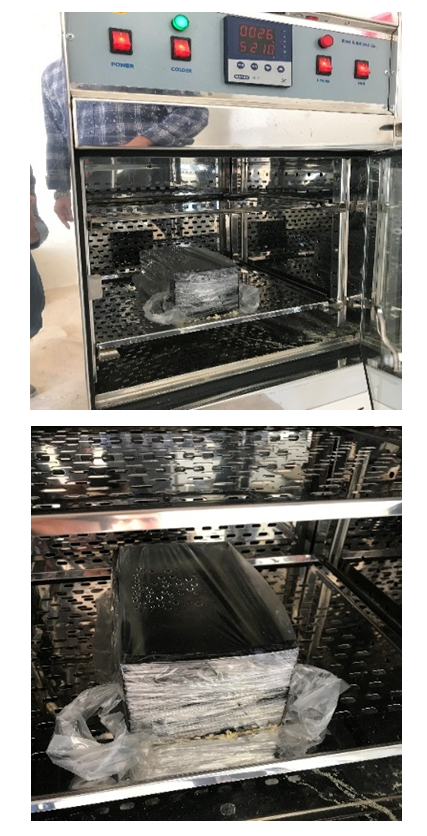 | Figure 16. Melting and ice test of concrete floor containing VP particles |
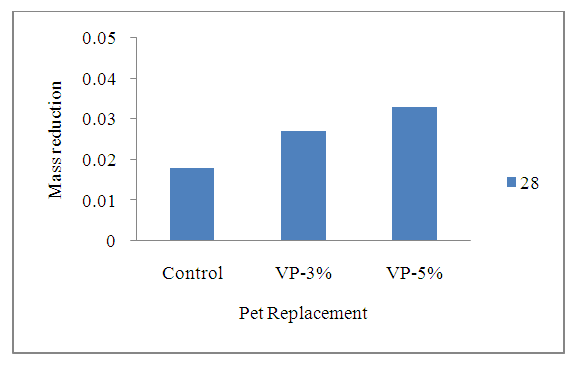 | Figure 17. Comparison of melting and ice test results of concrete floor containing VP particles |
According to the previous results obtained from experiments performed on the mechanical characteristics of concrete flooring, the use of VP particles in high percentages (10 and 15) caused the floor to become porous and the appearance requirements of the flooring to be met, so only test and valuation of floors with a low percentage of alternative VP instead of aggregate is discussed in this experiment. The results show that the use VP with a low percentage (3 and 5%) will not have much effect on the frost resistance of concrete floors, this is due to the structure of the floors because as It was mentioned at the beginning that concrete floors consist of two layers, Face and main, and in this experiment, the salt solution is only in contact with the surface of the sample, which has low permeability, but it is predicted that the results will increase with the percentage of VP. The reduced result is out of the range defined in the regulations.
4. Conclusions
In this study, in order to investigate the effect of using VP particles on the engineering specifications of concrete flooring containing VP particles, after determining the optimal amount of particles and mixing ratios to strengthen light weight concrete, necessary tests were performed on fresh and hardened concrete. According to the experiments, the following results have been obtained.• Addition of particles reduces the flow and filling properties of concrete. The largest decrease is observed in the concrete floor design containing 2%.• The addition of VP particles has little effect on the compressive strength and even in cases of more consumption of these particles will lead to a slight reduction in compressive strength. • Adding every three percent of VP particles increases the tensile strength, so that the greatest improvement has been observed in concrete floor containing 2% of VP particles. • The relationship between tensile strength and compressive strength for conventional concrete flooring and all three types of light weight concrete containing different percentages of VP particles is in the range proposed by CEB-FIP-2010 [16] for normal concrete.• The use of VP particles improves the flexural strength of conventional concrete; this improvement is more noticeable in concrete flooring containing 2% of VP particles. • The failure mode of concrete flooring samples containing VP particles under compressive, tensile and flexural tensile strength tests is different from conventional (particle-free) concrete flooring samples and is soft and gradual.• The presence of VP particles on the speed of ultrasonic waves in concrete floors is not normal. The speed of ultrasonic waves of light weight concretes both without particles and containing particles, increases with each age in each design. • VP particles affect the mechanical properties of concrete and increase tensile and flexural strength and have little effect on compressive strength. The recommendations and possibilities for further studies include (1) Studying deeply and analyzing the impacts of VP in a regular concrete mixture thoroughly. (2) More studies about the environmental impacts and economic aspects of utilizing VP. (3) Studying more characteristics and conducting tests like split tensile strength, modulus of elasticity, shrinkage and toughness tests.
References
[1] | R. J. Burak and P. Eng, “Segmental concrete pavements for municipal and heavy use industrial or port applications,” in Second Material Specialty Conference of the Canadian Society for Civil Engineering, Montréal, Québec, 2002b. CANADIAN STANDARDS ASSOCIATION–CSA, 2002. |
[2] | G. Garber, Design and construction of concrete floors. CRC Press, 2006. |
[3] | C. Clark, J. Jambeck, and T. Townsend, “A review of construction and demolition debris regulations in the United States,” Crit. Rev. Environ. Sci. Technol., vol. 36, no. 2, pp. 141–186, 2006. |
[4] | A. M. Wagih, H. Z. El-Karmoty, M. Ebid, and S. H. Okba, “Recycled construction and demolition concrete waste as aggregate for structural concrete,” HBRC J., vol. 9, no. 3, pp. 193–200, 2013. |
[5] | J. Nilimaa and V. Zhaka, “Material and environmental aspects of concrete flooring in cold climate,” Constr. Mater., vol. 3, no. 2, pp. 180–201, 2023. |
[6] | Uoyo Jin, Hongping Yuan, Qian Chen, Science mapping approach to assisting the review of construction and demolition waste management research published between 2009 and 2018, Resour. Conserv. Recycl. (2019). |
[7] | M. Vijayalakshmi, A. S. S. Sekar, M. Sivabharathy, and G. Ganesh Prabhu, “Utilization of granite powder waste in concrete production,” in Defect and Diffusion Forum, Trans Tech Publ, 2012, pp. 49–61. |
[8] | A. Gagan, “Sumit.(2015). Recycled Aggregates: A Sustainable Solution of Construction and Demolished Waste,” IOSR J. Mech. Civ. Eng., pp. 1684–2278. |
[9] | A. K. Padmini, K. Ramamurthy, and M. S. Mathews, “Influence of parent concrete on the properties of recycled aggregate concrete,” Constr. Build. Mater., vol. 23, no. 2, pp. 829–836, 2009. |
[10] | G. Andreu and E. Miren, “Experimental analysis of properties of high performance recycled aggregate concrete,” Constr. Build. Mater., vol. 52, pp. 227–235, 2014. |
[11] | M. Fadadu, N. Vadher, V. Trivedi, M. Mungule, and K. K. R. Iyer, “A comparative study on stress-strain response and associated hysteresis for conventional and PET macro-reinforced concrete,” Constr. Build. Mater., vol. 264, p. 120534, 2020. |
[12] | G. O. Bamigboye, K. Tarverdi, A. Umoren, D. E. Bassey, U. Okorie, and J. Adediran, “Evaluation of eco-friendly concrete having waste PET as fine aggregates,” Clean. Mater., vol. 2, p. 100026, 2021. |
[13] | O. K. Ali, A. I. Al-Hadithi, and A. T. Noaman, “Flexural performance of layered PET fiber reinforced concrete beams,” in Structures, Elsevier, 2022, pp. 55–67. |
[14] | S. Salhotra, R. K. Khitoliya, and S. K. Arora, “Assessing the enhanced concrete-properties induced by sugarcane bagasse ash-coated PET-fibers,” Mater. Today Proc., vol. 48, pp. 994–1000, 2022. |
[15] | J. S. Pierce, “Mixing and curing water for concrete,” in Significance of Tests and Properties of Concrete and Concrete-Making Materials, ASTM International, 2006. |
[16] | M. A. Chiorino, “Napoli P., Mola F., and Koprna M., CEB Design Manual on Structural Effects of Time-dependent Behaviour of Concrete, CEB Bulletin d’Information № 142-142 Bis, Georgi Publishing Co.,” 1984. |