Blaise Ngwem Bayiha1, Fabien Kenmogne1, Benjamin Bahel2, Nnuka A. Biabag1, Emmanuel Yamb1
1Department of Civil Engineering, Advanced Teacher's Training College of the Technical Education, University of Douala, Douala Cameroon
2Laboratory of Energy Modeling Materials and Methods (E3M), National Higher Polytechnic School of Douala, The University of Douala, Douala, Cameroon
Correspondence to: Blaise Ngwem Bayiha, Department of Civil Engineering, Advanced Teacher's Training College of the Technical Education, University of Douala, Douala Cameroon.
Email: |  |
Copyright © 2023 The Author(s). Published by Scientific & Academic Publishing.
This work is licensed under the Creative Commons Attribution International License (CC BY).
http://creativecommons.org/licenses/by/4.0/

Abstract
The mud bricks are stabilized with a natural base (rice hull ash) in this study. To do this the raw materials used are clay: rice husks, caustic soda and water. The stabilizing solution used was obtained by mixing rice husk ash with caustic soda. Tests of measurements of physical characteristics such as natural water content, specific weight, particle size analysis, Atterberg limits, Proctor test, CBR were carried out. Mechanical tests such as simple compression and three-point bending were performed. The percentages used in the mechanical stabilization tests were 02%, 04%, 05%, 06%, and 08%. Three stabilization formulations were produced, the first 50% soda + 50% ash, the second 30% soda + 70% ash, and the third 20% soda + 80% ash. The water absorption for the hardness test was performed, and the results obtained give for the natural water content 17.5% and 18.1%, the specific weight 2.425
and 2.433
, the particle size analysis 0.6% and 1% of gravel, 58.5% and 71.4% of sand, 4% and 6% silt, 22% and 36.5% clay, the Atterberg limits give 57.6% and 58.7% liquid limit, 34.8% and 31.8% plastic limit, 22.7% and 26.9% plasticity index, the Proctor trial gives 18.8% and 19% of optimum water content, 1.801
and 1.806
of maximum dry density, the CBR gives 7.1 and 7.8 of plasticity index. The results found for the mechanical tests give a compressive strength at 28 days of 2.70MPa, 4.10MPa, and 6.28 MPa, the flexural strength of 1.98MPa and 2MPa. All bricks are tested for compression as well as bending at 7 days, 14 days and 28 days. The results obtained show that the dosage at 5% of the mixture is optimal; it gives a compressive strength of 2.5MPa at 7 days, 3.68MPa at 14 days and 6.68 MPa at 28 days. For the immersion test, bricks without sodium silicate will dissolve after a few minutes, while those containing this mixture will not dissolve and have no defects. Also, it should be noted the low water absorption of the brick containing sodium silicate during their immersion compared to the brick without sodium silicate.
Keywords:
Stabilized brick, Rice husk ash, Caustic soda, Compressive strength, Flexural strength, Immersion
Cite this paper: Blaise Ngwem Bayiha, Fabien Kenmogne, Benjamin Bahel, Nnuka A. Biabag, Emmanuel Yamb, Physico-Mechanical Characterization of an Earth Brick Stabilized with Sodium Silicate and the Rice Husks Ash, Journal of Civil Engineering Research, Vol. 13 No. 2, 2023, pp. 60-70. doi: 10.5923/j.jce.20231302.03.
1. Introduction
Earth is the oldest natural material that humans use to build their homes. It is available almost everywhere in the world and its operation does not require special effort or extensive knowledge. Human use of clay, mainly in the production of building materials, dates back centuries. Therefore, clay is considered as the raw material in the production of earthen bricks [1]. Clay is an abundant material with several qualities. It is estimated that a third of the world's population lives under roofs constructed from clay. About half of the population of developing countries and at least 20% of city dwellers live in earthen constructions [2].The construction materials sector in Cameroon remains dominated by materials imported or manufactured locally but the cost continues to increase. Thus, sustainable development in Cameroon goes through the valuation of local materials given their ease of obtaining. The use of materials derived from concrete and its derivatives has gradually become necessary for reasons of properties and modernity compared to local materials, especially in Central Africa. However, point out that the construction of concrete habitats is expensive in developing countries and has a strong environmental impact [3]. Materials such as cement blocks are generally used in Cameroon as part of building construction projects and more specifically in rural areas. However, at this level, the use of stabilized or unstabilized compressed earth blocks is less used, while the development of local secondary natural resources, often considered as waste, is a field of research for the development of eco-friendly materials construction [4]. The compressed stabilized earth brick gives the vision of energy efficient buildings, at reduced costs and respectful of the environment in materials, globally contributing to sustainable development [5].Although earthen construction is generally profitable, its economic benefits depend on the nature and amount of binder used in the stabilization process [6]. The downside is that, when raw, this material does not always stand up to the elements. Thus, the research results have shown that the use of local building materials (BTC, adobes) gives the possibility of obtaining better thermal performance of the building compared to modern materials [7,8]. Thus, the durability of the structures built is feared. Many mud buildings (adobe) and particularly those built with materials without any associated treatment are doomed to serious problems of stability, progressive wear and even crumbling in the presence of a high level of humidity, especially in countries with high rainfall. The same phenomena are also observed in some buildings of stabilized earth bricks, especially when no surface treatment has been considered [9].Thus, scientific studies have been carried out on the stabilization of raw earth by mineral binders (cement and lime) for the most part [10]. However, the use of these mineral binders in high proportions can call into question the ecological character of the material [11]. At the same time, certain traditional practices, particularly in developing countries, and some recent scientific studies have shown that the use of organic binders of natural origin could be a more virtuous alternative from an environmental point of view to mineral binders [12]. These organic products have very great diversity and therefore a significant potential for scientific study, like the variety of practices depending on the location of the globe [13].We then find an interest in the use of materials of natural origin such as plants (wood, straw, hemp, flax, rice husks, etc.) which are renewable, recyclable and sustainable and can contribute to significantly limit greenhouse gas emissions thanks to their ability to trap CO2 [14]. Each year after the harvest, the rice husks are either thrown away or burned for lack of recycling, posing thus a threat to the environment. The objective of our study is to perform the physical and mechanical characterizations of an earth brick stabilized with sodium silicate from the ash of rice husks. To achieve this objective, the identification tests of the physical and mechanical properties will be carried out.
2. Material and Experimental Procedure
2.1. Materials Used in the Study
The materials used in this research are: Earth (sandy clay), rice hull ash, caustic soda and tap water.
2.1.1. Soil
The soil used, as shown in Fig. 1 comes from the coastal region (Cameroon), it is chosen on the basis of its availability and abundance in the region. We took four soil samples at a place called Nkolbon just after the Chinese base located in Yassa by Douala 3rd.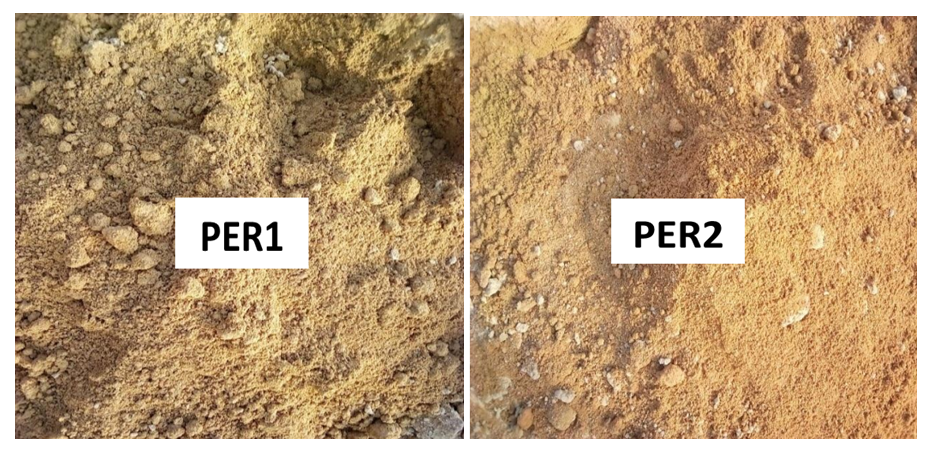 | Figure 1. PER1, PER2 soil samples |
2.1.2. Study Area
The localization map, as shown in Fig. 2, which is obtained using an electronic GPS gives us: 60 meters altitude and for the geographical coordinates 04°0'44.0856 ’North latitude and 09°48'34.90884’ East longitude.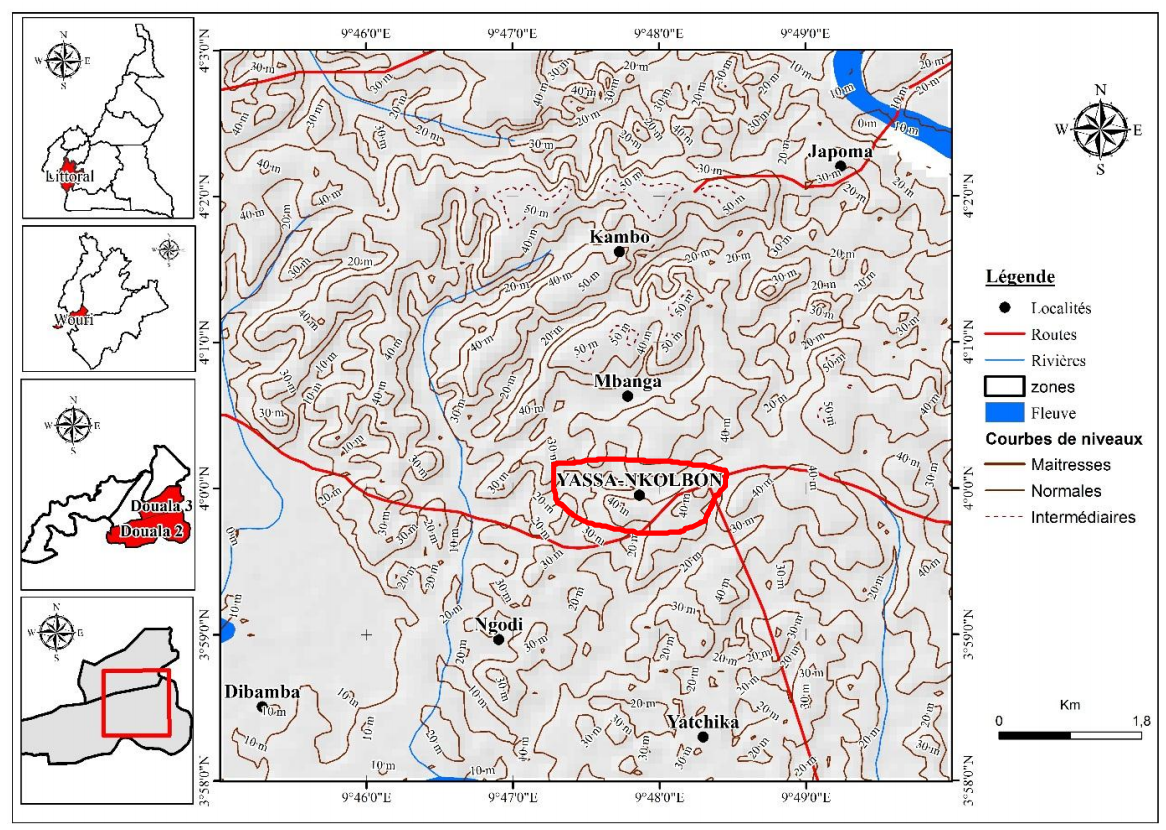 | Figure 2. Location map of the sample collection site |
2.1.3. Rice Husks
The rice husks used throughout this research were calcined at a temperature of 700°C for six hours to obtain ash [14]. Figures 3 and 4 shows the balls.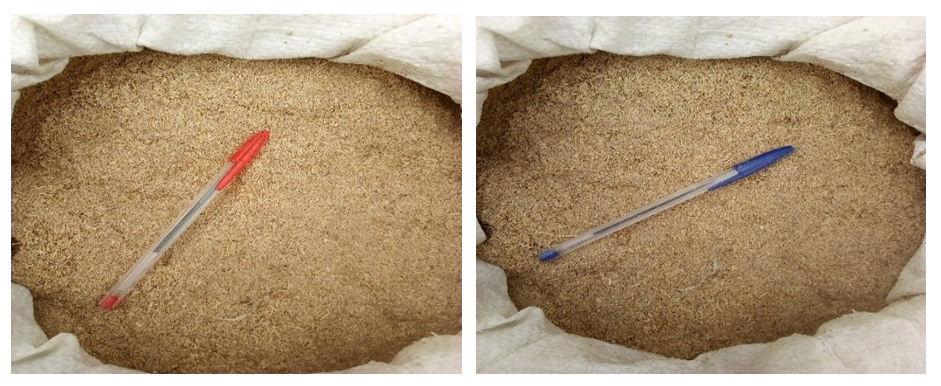 | Figure 3. Rice husks |
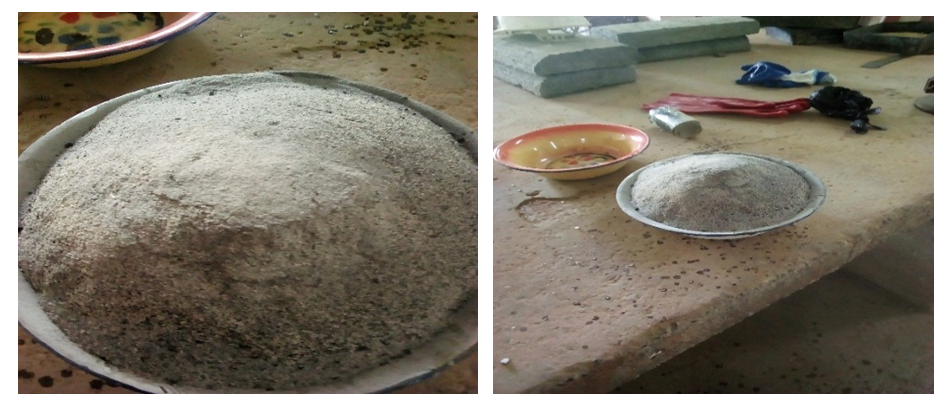 | Figure 4. Rice husk ash |
2.1.4. Caustic Soda
Caustic soda, also called sodium hydroxide, is an odourless white solid. Sodium hydroxide will be used throughout this research associated with the ash of rice husks to stabilize (BTC). Figure 5 shows caustic soda.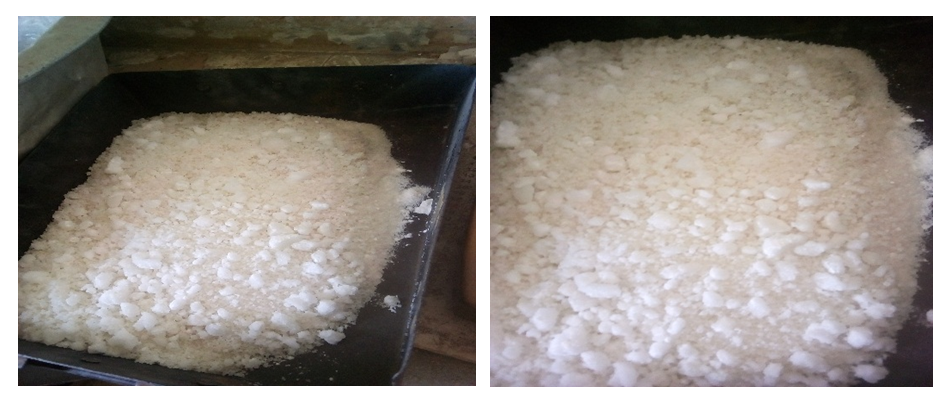 | Figure 5. Caustic soda |
2.2. Composition of Caustic Soda and Rice Husk Ash
To continue this research in order to stabilize the earth bricks, the following different percentages are used: 02%, 04%, 05%, 6% and 08% of sodium silicate. This formulation was made in order to analyze and assess the optimal value to be used for making quality bricks.• Sodium silicate: Sodium silicate is made by mixing caustic soda and the ash of rice husks.• Mixture of caustic soda and rice husk ash: in order to bring out the sodium silicate solution, this work was done in three different formulations, a composition of 50% caustic soda and 50% rice hull ash , a composition of 30% caustic soda and 70% rice husk ash, a composition of 20% caustic soda and 80% rice husk ash. These compositions were made with the aim of finding the optimal formulation of the stabilizer (sodium silicate).This composition will be put into practice during the making of stabilized earth bricks while respecting the dosage parameters defined. Heat is observed when water is added to the mixture. Figure 6 shows the texture of the caustic soda (left) and rice husk center mixture (right).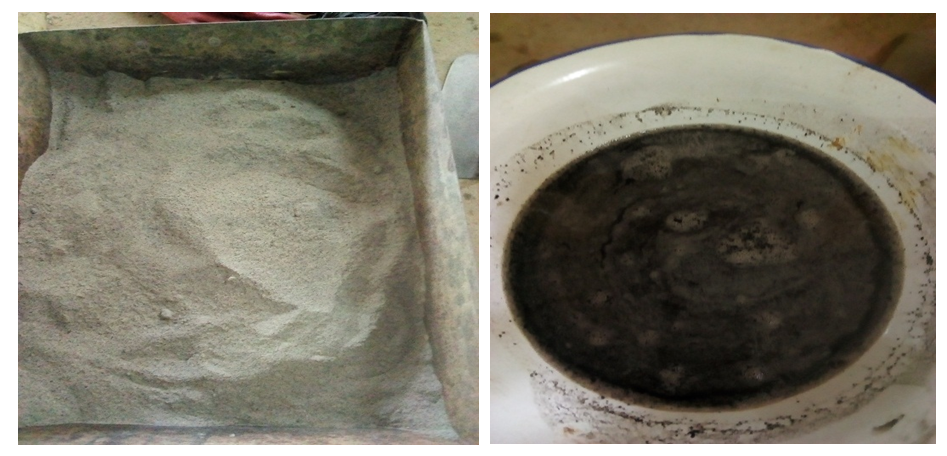 | Figure 6. Texture of caustic soda and rice husk ash |
2.3. Characterization of Raw Materials
Due to their significant heterogeneity, clay materials have been characterized in order to ensure their suitability for the production of stabilized earth bricks [15]. This characterization concerns the identification of terrestrial materials by physical tests experienced in the laboratory. Table 1 shows the summary of the physical properties of the soil samples taken in the laboratory such as: natural water content, specific gravity, particle size analysis, Atterberg limits, proctor test, and CBR test.Table 1. Physical properties of the soil samples under consideration 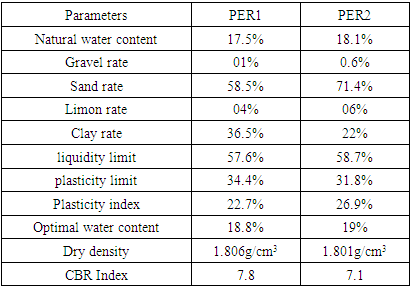 |
| |
|
2.4. Preparation of Compressed Stabilized Earth Block Samples
The manufacture of stabilized earth bricks is based on the principle of clay-sandy compaction, optimized matrices according to the water content and the grain size of the mixture [16].It is carried out in 3 stages: preparation of the soil material (see Figs. 7 and 8) from which the samples were extracted by surface excavation, compression of the mixture introduced into a 22 × 10 × 5 cm3 mould and hardening for flexion tests, and into cylindrical mould for compression tests. Referring to previous studies conducted with straw as stabilizers for clay bricks; indicate that the presence of these straws will prevent the shrinkage and swelling responsible for cracks, thus improving the physical properties and mechanical resistance [17]. In soil preparation, it must be given an appropriate compressive load to obtain the best results after the mixture is placed in the mould [5].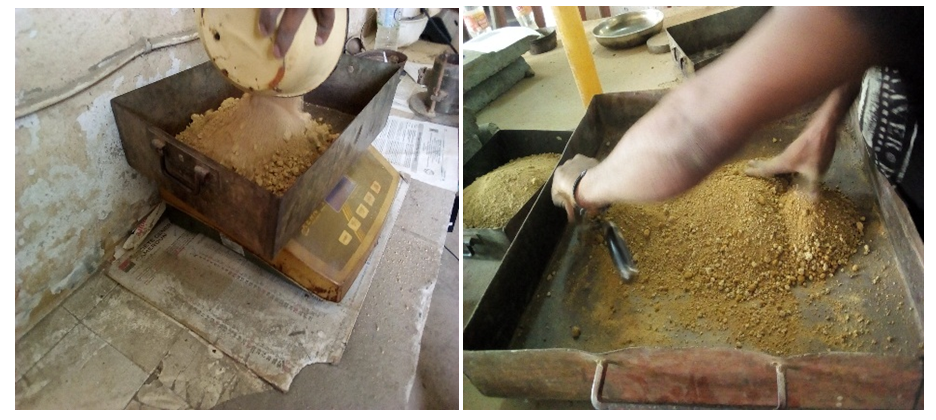 | Figure 7. Weighing and mixing the soil |
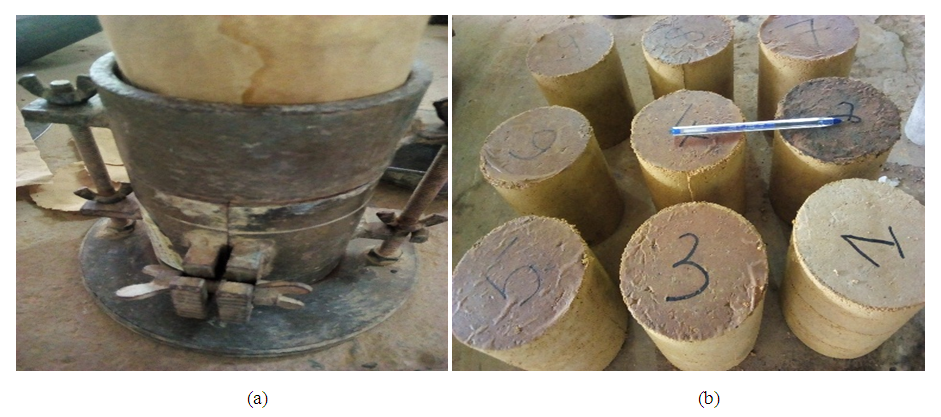 | Figure 8. Preparations of test pieces (a). Test pieces produced and put to drying (b) |
In order to achieve the BTCs, static compaction was applied to the mixtures, according to the centre for development of enterprise (C.D.E) method, applied in literature [18]. This is done by applying a uniform load to the mixture to optimize the use of the properties of compressed earth bricks based on the result of the standard Proctor test. Compression of the mixture was necessary to achieve preferred properties and to limit production costs in order to extend the use of stabilized bricks to all types of bricks [19].
2.5. Preparation of Test Specimens
Paper and plastic are placed inside the mould to prevent the clay from sticking to the wall. Compaction starts by dropping the ram on the material up to 25 times per layer (Figure 8a). Once the compaction of three layers is complete, the test piece will be removed from the mould, weighed (Fig.9 a), then placed on a bench for drying in the open air or in an oven at 105°C until a constant dry mass is obtained (Figure 9 b). A total of 60 test tubes were made and crushed at different ages. Details are given in Tab. 2.Table 2. Preparation of specimens for mechanical characterizations 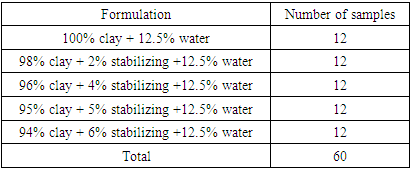 |
| |
|
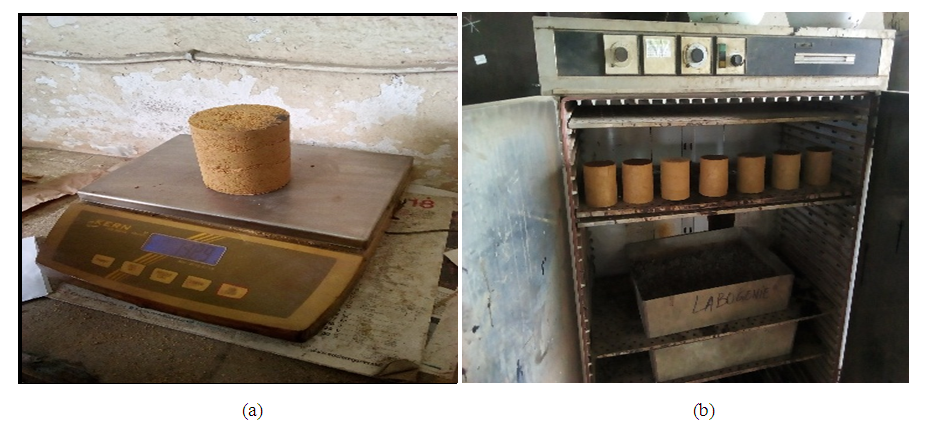 | Figure 9. Weighing of the test piece (a). Test pieces produced and put to drying (b) |
2.6. Mechanical Testing
The mechanical study of bricks is made by simple compression and bending by three bridges.
2.6.1. Simple Compression Test [20] (NF P 94-077)
In this test, the compressive strength of unstabilized and stabilized raw earth bricks is carried out in order to check their quality and resistance to compression (see Fig. 10). The compressive strength will be measured during crushing of the test pieces after a period of 7 days, 14 days and 28 days for this work. The test consists of subjecting the specimen or brick to a continuous and progressive load using an electro-hydraulic press of the FORM TEST type until it is crushed. Compressive strength is the ratio of the breaking load to the cross section of the specimen. Designating by S
the surface of the parallelepipedal specimen and by F
the maximum load it supports until failure. Hence the compressive strength expressed in (Mpa) is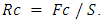 | (1) |
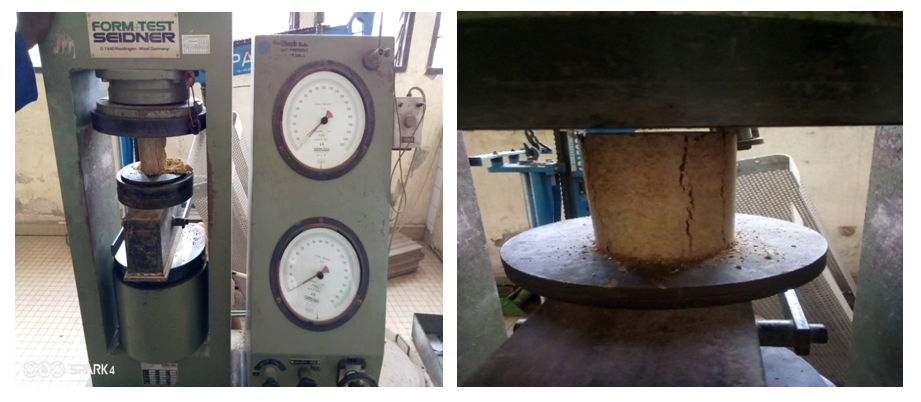 | Figure 10. Compression test apparatus |
2.6.2. Three-point bending test [21] (NF B 51-008)
Bending strength tests are carried out on blocks of dimensions 1604040 mm3 using an electro-hydraulic press as shown in Fig. 11. The test piece is placed on two metal rods 50 mm apart on the lower plate of the machine; A third rod, on which pressure will be exerted, is then placed on top of the test tube. At failure, the maximum tensile stress due to bending is calculated from the equation below: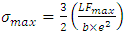 | (2) |
With,
(MPa) the flexural strength at three points;
(N): the breaking force; L (mm): the length of the BTC; b (mm): the width of the BTC; and e (mm): the thickness of the BTC.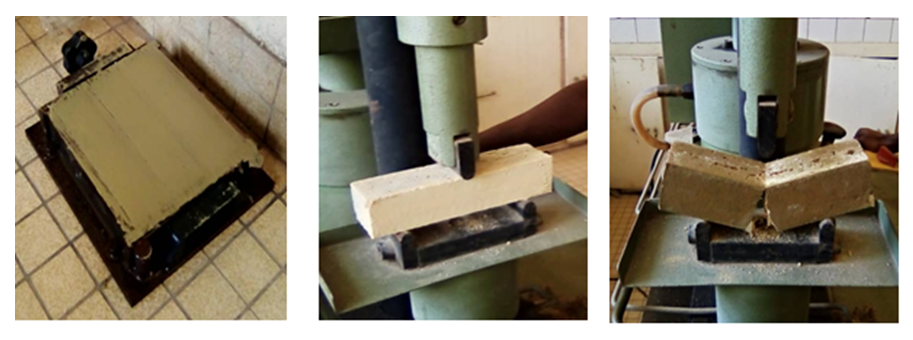 | Figure 11. Bending test device |
2.6.3. Water Absorption Test
Water absorption by immersion is the result of capillary movements in the pores of the brick which are open to the surrounding environment. Being a picture of porosity, water absorption is therefore used as one of the important indicators of the quality of the brick. The operations are performed in the following order during our work:- Immersion in a water tank for a minimum of 48 hours or until constant wet mass. Before weighing to the nearest gram, the test pieces are carefully wiped with a cloth absorbing all surface water;- Drying for a minimum of 72 hours or to a constant dry mass in a ventilated oven, the temperature of which is maintained at 105°C;- The mass is considered constant when two successive weighings 24 hours apart do not give significant difference, not more than 0.1%;- The water absorption rate by immersion (Ta%) is the percentage of the dry mass calculated by the following relationship:  | (3) |
With
The constant wet mass of the test specimen after immersion;
The constant dry mass of the test piece after drying in an oven.
3. Results and Discussions
In this section, the results obtained from the tests described in the previous section are presented.
3.1. Compression Test
The results of the compression test for different admixture are shown in Fig. 12 for 50% soda and 50% ash, in Fig. 13 for 30% soda and 70% ash, and in Fig. 14 for 20% soda and 80% ash. From these figures, it is obvious that the compression strength found from the admixture of 50% soda and 50% ash are lower than that of 30% soda and 70% ash. however, the results of the dosage of (20% soda and 80% ash) are improved compared to the two other cases. The first formulation gives an optimal result at 28 days of 2.70 MPa which corresponds to (05% and 06%); The second gives an optimal result of 4.10 MPa at 28 days which also corresponds to 05%; however the third formulation gives an optimal result at 28 days of 6.68 MPa for the proportions of (05% and 06%). Following these different results, the third formulation could be adopted because the dosage at 5% gives the improved values. Thus, the dosage adopted for making quality bricks is 5%. One also notices that, the more the percentage of sodium silicate increases and the more the resistance decreases from 8%, this is justified by the appearing of cracks on the bricks of 8% before crushing from 21 days and a deformation of the brick. Taken together, these results suggest that sodium silicate appears to be the essential element in the optimization of formulations and, therefore, it contributes to improving the mechanical performance of mud bricks in compression. However, the mechanical characteristics obtained on the stabilization of clay by Arabic gum gave a resistance from 1.67 MPa to 3.25 MPa [2]. These results are similar to those obtained with the second formulation; with a compressive strength at 28 days from 2.91 to 4.10 MPa. In addition, the results of the third formulation are improved even, giving a compressive strength of 6.68 MPa at 28 days, which are better as compared to result found in [9] for earthen brick stabilized using sugar cane molasses, which gave a compressive strength at 28 days between 4.65 and 4.85 MPa. The results found in [9] for 8% of sodium silicate at 28 days gave the compressive strength of 4.45 MPa. The mechanical characteristics of bricks in compressed sand and laterite mortars stabilized with cement gave 2.55 MPa and 7.90 MPa. The results found here remain acceptable at 28 days of 6.68 MPa as compared to the latter [22]. Moreover, undertaken work of the fly-ashes - lime used to stabilize the lateral soil blocks subjected to alternating cycles of wetting and drying gave resistances of 3.12 and 3.04 MPa [23], which is small as compared to result found here at 28 days. The results found here offer better compression strength as compared to several works carried out in the literature [24,25].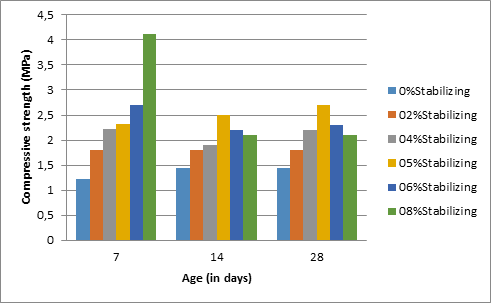 | Figure 12. Compressive strength for the admixture of (50% soda and 50% ash) |
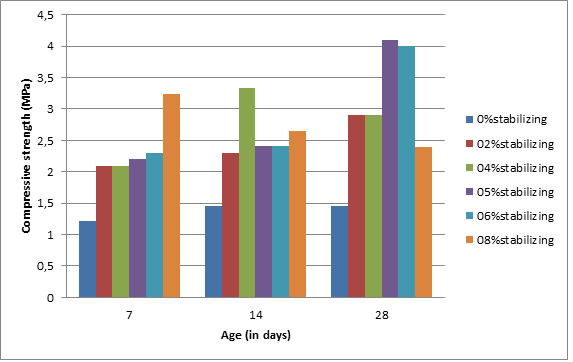 | Figure 13. Compressive strength for the admixture of (30% soda and 70% ash) |
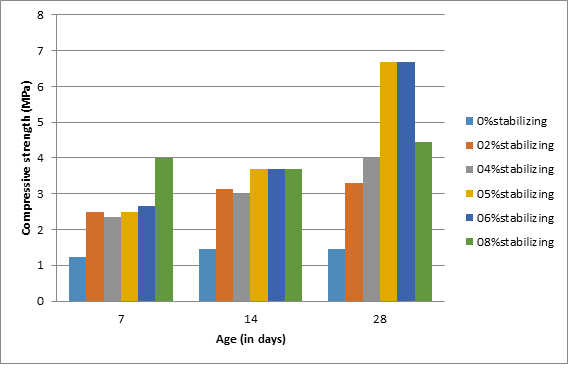 | Figure 14. Compressive strength for the admixture of (20% soda and 80% ash) |
3.2. Bending Test
The results of the bending test as shown in Fig.15 give values in the order of 25% to 30% compared to the results obtained in compression. These values are justified by the fact that bricks resist better in compression than in bending. It should be noted that the earthen brick stabilized with sodium silicate has a maximum which varies between 1.90 and 2 MPa at 28 days, respectively for the dosages of 5% and 6%. The results of the bending test are similar to those found in [28], in what concern the effect of length and content of bamboo fibers on the physico-mechanical and hygroscopic properties of compressed earth blocks (BTC) used in construction, in which the bending strength at 28 days was 2 Mpa. Other studies made on the mechanical and thermal characterization of compact blocks in clayey soil with the addition of wood ash gave a bending strength at 28 days of 2.6 MPa which is comparable with the best value of flexural strength, which is 2 MPa obtained at 28 days [25].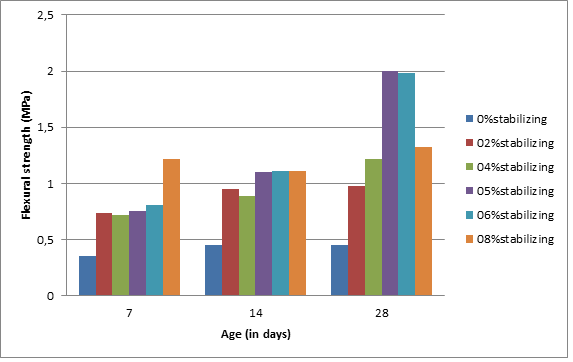 | Figure 15. Flexural strength |
3.3. Water Absorption
The results of the water absorption rate (Fig. 16) show a change in the water content over time. It is noted that stabilized earth bricks have a low water absorption rate compared to unstabilized earth bricks. The amount of water absorbed by capillary action decreases as the sodium silicate content is increased. The unstabilized brick has a water absorption rate of 12.8%, while the stabilized brick has a water absorption rate that varies between 5% and 10%. Note that the mud brick stabilized at 06% at a water absorption rate of 5%, while the one stabilized at 08% at a water absorption rate of 7.4%. Following these results, we can notice that the percentage of sodium silicate from 06% is optimal because beyond 05% and 06% the water absorption rate begins to increase. However, we note that the water absorption rate of 8% is higher than the contents of 05% and 06%, so from 05% we can ensure quality bricks. We also note that, for treated earth bricks, the water absorption rate is practically constant beyond sodium silicate content of the order of 05% and 06%. It can be seen in Figure 16 that for a sodium silicate content varying from 04 to 06%, the water absorption rate drops sharply. For all exposure times, this water absorption rate is practically stable when the silicate content is in the range 04 to 06%. The quantity of water absorbed by capillarity is then very low between (0.8 and 1.2%), which suggests a better durability for a material with a sodium silicate content in the range (05 - 06%), constituting l building envelope capable of receiving rainwater. We can therefore observe that the addition of sodium silicate decreases the absorption rate of BTC. We observe that 0% of sodium silicate corresponds to 12.5% of absorption rate, 2% of sodium silicate corresponds to 11% of absorption rate, i.e. a decrease of 1%, value which is within the acceptable range of water absorption which is 10% to 20%, and therefore, meets the minimum requirements for use in construction [27].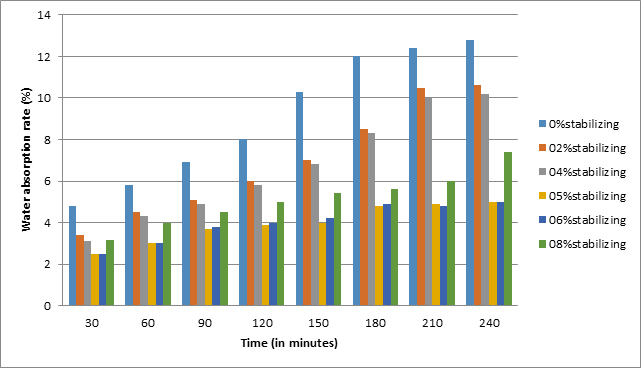 | Figure 16. Water absorption rate as a function of time (min) |
4. Conclusions
The objective of this study was the stabilizing of the earth bricks by incorporating sodium silicate and rice husk ash. The samples for this study were taken in the city of Douala (economic capital of Cameroon), specifically in Yassa at a place called Nkolbon in the third district of Douala. The samples were taken at two points called here PER1 and PER2, 200 m apart at a depth of 1m and 1.5m. These samples after collection were immediately brought to LABOGENIE in Douala for various tests. Fieldwork shows that raw materials for bricks do not have a prior study from which the samples are analyzed in the laboratory. Laboratory tests were performed on measurements of the physical characteristics of soil samples, mechanical, and water absorption hardness tests. Laboratory tests on samples show natural water contents of 17.5% and 18.1%. The specific weight gives 2.424 T/m3 and 2.427 T/m3. Particle size analysis showed that the samples consist of gravel, sand, clay, silt in proportions of (0.6% -01%) for gravel, (58.5% -71.4%) for sand, (04% -06%) for silt and (22% -36.5%) for clay. The Atterberg limit tests allowed us to define the liquidity limit of the samples (57.6% -58.7%), the plasticity limit (31.8% -34.8%), and the plasticity index (22.7% -26.9%). Through the Casagrande apparatus we have carried out a classification of samples which present a character of very plastic loamy soils. The PROCTOR test gives an optimum water content of (18.8% -19%), the maximum dry density is (1.801 g/cm3-1.806 g/cm3). The CBR test gives the index of (7.1 and 7.8). The mechanical tests were the subject of this work on stabilization insofar as we made three formulations (50% soda - 50% ash), (30% soda - 70% ash), (20% soda - 80 % Ash) to find the improved results for quality bricks. The rates used for stabilization were 02%, 04%, 05%, 06%, and 08%. Thus, the compressive strength for this work was optimal on the formulation of (20% soda and 80% ash) with the results of 2.50 MPa, 3.68 MPa and 6.68MPa respectively at 7 days, 14 days and 28 days of age for a rarte of 5% stabilizer. The flexural strength gives 0.75MPa, 1.10MPa, 2.00 MPa at 7 days, 14 days and 28 days of age with 5% stabilizer. Water absorption consisted of evaluating the ability of the bricks to absorb water after 28 days of age. The amount of water absorbed by capillary action decreases with the increasing of sodium silicate content. The unstabilized brick has a water absorption rate of 12.8%, while the stabilized brick has a water absorption rate that varies between 05% and 10%.Note, sodium silicate stabilization dramatically improves strength and reduces total immersion water absorption which is much lower in the case of high percentage bricks than in the low percentage case. For the future works, it should be interesting to better characterize this type of brick; by carrying out other tests such as: shrinkage and swelling, thermal study, impact resistance, as well as erosion.
References
[1] | Djaouyang Djonga Parfait (2016). Impact de prélèvement de la matière première argileuse sur la qualité finale des briques cuites à l’usine de Nkolbisson. Memoire de fin d’etudes en vue de l’obtention du diplôme d’ingénieur de conception en traitement des matériaux, architecture et habitat. Université de Maroua Cameroun. |
[2] | Abakar Ali et al. Caractéristiques mécaniques de l’argile de Ndjamena stabilisée par la gomme arabique. Université Henri Poincaré. Afrique SCIENCE 13(5) (2017) 330 - 341 http://www.afriquescience.info. |
[3] | Ouedraogoa, M., et al. (2019) Physical, Thermal and Mechanical Properties of Adobes Stabilized with Fonio (Digitaria exilis) Straw. Journal of Building Engineering, 23, 250-258. https://doi.org/10.1016/j.jobe.2019.02.005. |
[4] | Malbila, E., Delvoie, S., Toguyeni, D., Attia, S. and Courard, L. (2020) An Experimental Study on the Use of Fonio Straw and Shea Butter Residue for Improving the Thermophysical and Mechanical Properties of Compressed Earth Blocks. Journal of Minerals and Materials Characterization and Engineering, 8, 107-132. https://www.scirp.org/journal/jmmce. |
[5] | Riza, F.V., Rahman, I.A., Mujahid, A. and Zaidi, A. (2010) A Brief Review of Compressed Stabilized Earth Brick (CSEB). CSSR 2010 International Conference on Science and Social Research, Kuala Lumpur, 5-7 December 2010, 999-1004. |
[6] | Pacheco-Torgal, F. and Jalali, S. (2012) Earth Construction: Lessons from the Past for Future Eco-Efficient Construction. Construction and Building Materials, 29, 512-519. https://doi.org/10.1016/j.conbuildmat.2011.10.054. |
[7] | Laborel-Préneron, A., Aubert, J.E., Magniont, C., Tribout, C. and Bertron, A. (2016) Plant Aggregates and Straw in Earth Construction Materials: A Review. Construction and Building Materials, 111, 719-734. https://doi.org/10.1016/j.conbuildmat.2016.02.119. |
[8] | Compaore, A., Ouedraogo, B., Guengane, H., Malbila, E. and Bathiebo, D.J. (2017) Role of Local Building Materials on the Energy Behaviour of Habitats in Ouagadougou. International Journal of Applied Science, 8, 63-72. https://doi.org/10.21013/jas.v8.n2.p3. |
[9] | Narcisse Malanda, Paul Louzolo Kimbembe, Yannick Destin Tamba Nsemi (2017). Etude des caractéristiques mécaniques d’une brique en terre stabilisée à l’aide de la mélasse de canne à sucre. Revue du CAMES Sciences Appliquées et de l’Ingénieur, Vol. 2(2) ISSN 2312-8712. http://publication.lecames.org/. |
[10] | Danso, H., Martinson, B., Ali, M., Mant, C., 2015. Performance characteristics of enhanced soil blocks: a quantitative review. Build. Res. Inf. 43, 253–262. https://doi.org/10.1080/09613218.2014.933293. |
[11] | Van Damme, H., Houben, H., 2017. Earth concrete. Stabilization revisited. Cem. Concr. Res. https://doi.org/10.1016/j.cemconres.2017.02.035. |
[12] | Vissac, A., Bourgès, A., Gandreau, D., Anger, R., Fontaine, L., 2017. Argiles biopolymères les stabilisants naturels pour la construction en terre 81. |
[13] | Anger, R., Fontaine, L., 2013. Interactions argiles/biopolymères: Patrimoine architectural en terre et stabilisants naturels d’origine animale et végétale, Craterre‐ ENSAG. ed. |
[14] | Edem CHABI et al. Formulation du béton de balles de riz: étude du comportement au cisaillement et au poinçonnement-flexion. Afrique SCIENCE 12(5) (2016) 114 – 124 ISSN 1813-548X, http://www.afriquescience.info. |
[15] | Ezbakhe, H., et al. (2001) Comportement thermique de la terre stabilisée au ciment. Revue Française de Génie Civil, 5, 505-515. https://doi.org/10.1080/12795119.2001.9692320. |
[16] | Gélard, D. (2005) Identification et caractérisation de la cohésion interne du matériau terre dans ses conditions naturelles de conservation. Institut National Polytechnique de Grenoble. |
[17] | Christine, D.A., Séraphin, D.A., Olivier, B.M. and Edjikémé, E. (2018) Effet de l’addition de fibres de coco traitées à la potasse sur les propriétés mécaniques des matériaux de construction à base d’argile-ciment. European Scientific Journal, 14, 104-116. https://doi.org/10.19044/esj.2018.v14n36p104. |
[18] | Taallah, B. and Guettala, A. (2016) The Mechanical and Physical Properties of Compressed Earth Block Stabilized with Lime and Filled with Untreated and Alkali-Treated Date Palm Straw. Construction and Building Materials, 104, 52-62. https://doi.org/10.1016/j.conbuildmat.2015.12.007. |
[19] | Patil, A.D. and Attar, A.C. (2015) Compressed Stabilized Earth Blocks by Using Lime. International Journal of Engineering Research & Technology, 4, 116-120. https://doi.org/10.17577/IJERTV4IS090204. |
[20] | NF P94-077 Mai 1997. Sols: Reconnaissance et essais – essai de compression uni axiale. |
[21] | ISO 1209-2 détermination des propriétés de flexion (essai simple de flexion). |
[22] | Bozabe Renonet Karka 2020. Comparative Study of the Mechanical Characteristics of Sand Mortar and Compressed Lateritic Bricks Stabilized with Cement. International Journal of Innovation and Applied Studies ISSN 2028-9324 Vol. 28 No. 2 Jan. 2020, pp. 438-451 © 2020 Innovative Space of Scientific Research Journals http://www.ijias.issr-journals.org/. |
[23] | Jijo JAMES et Rajasekaran SARASWATHY, (2020). performance of fly ash - lime stabilized lateritic soil blocks subjected to alternate cycles of wetting and drying, |
[24] | Shetty, T. S. - RAO, K. B. - PAI, B. J.: A Feasibility Study on the Compressive Strength of Flyash and Lime Stabilized Laterite Soil Blocks. International Journal of Innovative Research in Science, Engineering and Technology, 5(9 (Spl)), 2016, pp. 73–80. |
[25] | Gbénondé Sèna Gladys Milohin et al., (2020). Mechanical and thermal characterization of compact blocks made of clayey earth with wood ashes addition, MATEC Web of Conferences 307, 01030 (2020) https://doi.org/10.1051/matecconf/202030701030 ICOME’17 and ICOME’18. |
[26] | Dieudonné Abessolo et al. (2020). Effets de la longueur et de la teneur des fibres de bambou sur les propriétés physicomécaniques et hygroscopiques des Blocs de Terre Comprimée (BTC) utilisés dans la construction, Afrique Science 16(4) (2020) 13 - 22 13 ISSN 1813-548X, http://www.afriquescience.net. |
[27] | M. Saidi, A. S. Cherif, E. Sediki and B. Zeghmati, Etude comparative de la capacité de sorption des matériaux de construction à base de terre Abstract, 2019 (2019) 1 - 10 p. |