Michael Ateyire1, Peter Paa kofi Yalley2, Asubey Yakubu1
1Department of Technical and Vocational, St. John Bosco’s College of Education, Navrongo, Ghana
2Department of Wood and Construction Technology, Akenten Appiah-Menka University of Skills Training and Entrepreneurial Development, Kumasi, Ghana
Correspondence to: Michael Ateyire, Department of Technical and Vocational, St. John Bosco’s College of Education, Navrongo, Ghana.
Email: |  |
Copyright © 2023 The Author(s). Published by Scientific & Academic Publishing.
This work is licensed under the Creative Commons Attribution International License (CC BY).
http://creativecommons.org/licenses/by/4.0/

Abstract
This research investigates the effect of replacing Pozzo-mix Content with OPC for earth blocks production. The batching for Pozzo-mix cement alone was 5% (P5/0), 9% (P9/0), and 12% (P12/0). In the other batch were Pozzo-mix cement and OPC mixed stabilizers fractions in the ratio 3% Pozzo-mix: 2% OPC(P3/2), 6% Pozzo-mix: 3% OPC(P6/3), 8% Pozzo-mix: 4% OPC (P8/4). The engineering characteristics of the soil from the Bernatech campus, Navrongo revealed that soil fines and coarse fractions constitute about 46.8% and 53.2% respectively, and therefore suitable for brick production. The total number of bricks selected for the tests was Eighty-five (85) and they were 230mm x110mm x 90mm in size. Also, hand-made bricks' strength and durability criteria were investigated after 28 days of curing. The Regression analysis showed that Pozzo-mix contributed the most (71%) to the density of earth bricks. Again, all the stabilized earth bricks saw a steady increase in dry compressive strength between 2.06N/mm2, to 4.73N/mm2. The control and the 5% Pozzo-mix specimens did not perform well in wet compressive strength. The entire specimens responded negatively to water intake with the specimens P8/4 recording an impressive 0.096g/cm2/min reduction. The abrasion test values were within acceptable range with batch P8/4 again resisting abrasion the most with a record of 11cm2/g. Generally, the brick specimens saw an improvement when the percentages of the stabilizers increased. It is appropriate to conclude that the use of Pozzo-mix with OPC will improve significantly the strength and durability properties of compressed earth bricks. The use of Pozzo-mix cement alone should be used sparingly especially in lower percentages and in poor soils.
Keywords:
Abrasion, Compressive Strength, Dry density, Earth Blocks, Initial Rate of Water absorption, OPC, Pozzo-mix, Stabilizer
Cite this paper: Michael Ateyire, Peter Paa kofi Yalley, Asubey Yakubu, Investigating the Properties of Pozzo-mix Stabilized Earth Blocks with OPC Additive for Sustainable Construction, Journal of Civil Engineering Research, Vol. 13 No. 2, 2023, pp. 49-59. doi: 10.5923/j.jce.20231302.02.
1. Introduction
The increase in human population has brought about higher demands for housing provision in Developing countries all over the world. This rapid population growth has resulted in a huge housing deficit. The 2021 Ghana Population and housing census revealed that the housing shortfall stands at 1.8 million [1]. Despite the 33 percent reduction over the previous 2.8 million in 2010, the reduction is not significant to offset the population.The escalating price of conventional building materials accounts mainly for the short supply of housing [2] [3], explained that building materials are the key factors that contribute to the limited supply of housing and revealed that they account for between 50 to 70% of the cost of buildings.It has therefore become necessary that alternative sustainable building materials are sort for. Alternative building materials are generated through the modification of conventional materials or improvement in traditional materials which are acceptable for housing [4]. Building and Road Research Institute (BRRI) of the Centre for Scientific and Industrial Research (CSIR) Ghana in 2012 explained that the use of local materials could save the country at least $80 million annually. Some of the alternative building materials which are sustainable according to [5] include Bamboo, Straws, and Manufactured sand ferrock. Numerous stabilizers have been used in many studies all over the world. Some of these well-known stabilizers are blast furnace granulated slag (GGBS), Portland cement, fly ash, Pozzo-mix cement, lime, and natural fibers. Most of the research on cement stabilization has been heuristic and the reasons for successful or unsuccessful experiments have not been effectively investigated. Earth stands out as a suitable and sustainable construction material. Rammed earth became particularly well-known and widely used around the French Revolution thanks to the architect François Cointeraux [6].Application of materials in buildings now comes along with the challenge to meet the global environmental stake. This challenge concerns every sector, especially construction which is nowadays responsible for more than 40% of the global energy consumption, and for over one-third of the greenhouse gas emission in the world [7]. Apart from the architectural design choices directly affecting the energy demand in buildings, this high energy consumption level is due to the utilization of materials having an important embodied energy [8].The sensitivity of earth-based buildings to moisture with the resultant effects of cracks on drying, erosion, and structural collapse, however, has been the major setbacks of the earth as building materials [9].The BRRI built a small, prototype plant to produce clay Pozzo-mix from clay deposits at Mfensi (North-West of Kumasi), which is currently producing thousands of cements and sold at an affordable price. This material is an innovative product developed by CSIR-BRRI after over 30 years of research, which replaces up to 35% of ordinary Portland cement (OPC) to obtain Portland Pozzo-mix cement (PPC) for both concrete and general construction.[10] concluded in their study that higher percentages (30%) of Pozzo-mix cement can improve the strength of SEB but recommended a waterproof admixture be added to further improve the water resistance properties of the blocks.[11] used Locust bean pot ash, (a Pozzolana material) with OPC in specified percentages in producing concrete mixtures and to investigate the strength properties. After 28 days of curing the specimens with 60% pozzolanic material recording increased strength values of 38.2N/mm2.The treatment of the earth with the combination of lime-natural Pozzo-mix results in an overall improvement of the durability of the clayey soil blocks [12].[13] in their study combined Pozzo-mix cement and OPC in varied proportions to determine the optimum contents required to treat clay for the best resistance against dispersion or erosion. However, this may not necessarily be the best against physical stress.Some studies have been carried out on using clay Pozzo-mix as the main stabilizer without any admixture or lime as admixture. Studies that have attempted using other form of Pozzo-mix with OPC as admixture carried out the studies on concrete. This studies therefore critically investigate the strength and durability properties of Pozzo-mix and OPC as composite stabilizers in SEB for sustainable construction.The target compressive strength for earth material used as a structural element is 2 MPa. This value can be improved by adding Stabilizer like cement or by implementing fibers into the soil mixture.
2. Materials and Methods
2.1. Experimental Materials
The main experimental materials used for the study were Earths (soil), Pozzo-mix cement, ordinary Portland cement and water.EarthAll block samples were made using soil of a fixed composition. In this way the effect of varying the stabilizer type and content on the properties of the blocks could then be easily monitored. The earth for brick production was typically sourced from Bernatech Campus, Navrongo at a depth of 1m to 1.5m using the method of disturbed sampling and air dried for three months. CementOrdinary Portland cement type CEM I 32.5R manufactured by GHACEM a subsidiary of Heidelberg Cement Group used as an admixture.Pozzo-mixPortland Pozzo-mix cement type CEM II/13.0CLASS 32.5N manufactured by CSIR at Fumesua-Kumasi in the Ashanti region which meets Ghana and International Standards i.e., GS 964 and [14] specifications.WaterWater from the laboratory tap was used for mixing; it was ensured that it was fit for drinking, free from contaminants either dissolved or in suspension. These raw materials used for the preparation of samples as well as the variables in the raw mix are shown in Figure 1, Figure 2 and Figure 3.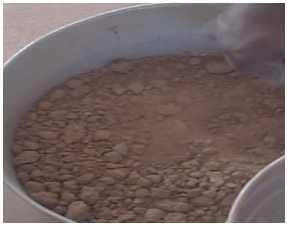 | Figure 1. Earth |
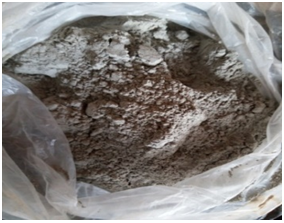 | Figure 2. OPC |
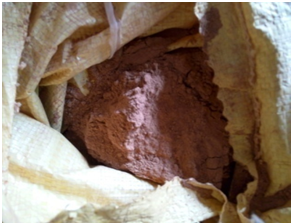 | Figure 3. Pozzo-mix Cement |
2.2. Methods
2.2.1. Earth Characterization and Preparation
Initial tests on the soil used for making the blocks were evaluated first for the purpose of classifying and identifying the types of soil. The tests performed were as follows: Soil Particle Size Test, Moisture Content Test, Specific Gravity Tests, the Atterberg Limits Tests, linear shrinkage and Compaction Test in accordance with [15].
2.3. Main Experiment
2.3.1. Preparation of Stabilized Earth Block Samples
Preparation of blocks samples followed, after the soil had undergone testing to determine its suitability for earth blocks production. This was carried out in accordance with [16]. The process outlined in Figure 4. 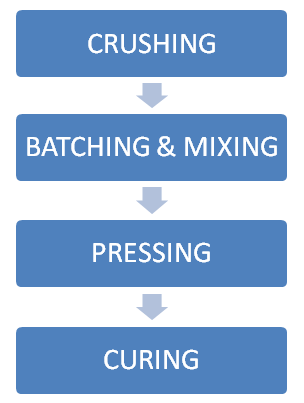 | Figure 4. Block Specimen Making Process |
Crushing of the soil sample was done manually in the laboratory. The researcher ensured that the maximum size of soil lumps passed the 20mm test sieve by crushing on a flat surface as shown in figure 5.Mixing of Pozzo-mix cement and ordinary Portland cement, in soil was done manually by hand in a wheelbarrow in a dry state. The stabilizers were calculated and weighed out in three quantities. The controlled samples were made of raw earth with no stabilizer and denoted by S0, the Pozzo-mix cement samples denoted by (Px), where ‘x’ is percentage Pozzo-mix, thus P5, P9 and P12. Research suggests that optimal levels of stabilization occur when the bricks contain between 3% and 18% of cement content by weight. [17] in their studies established that cement stabilization of 5%, 9% and 12% increased the characteristics of SEB significantly. The second for stabilization was the combination of ordinary Portland cement and Pozzo-mix cement denoted by
where X represents Pozzo-mix percentage and Y represents OPC percentage (OPC was used as an admixture), thus Pozzo-mix to OPC ratio (3%-2%), (6%-3%), (8%-4%) respectively. Figure 6 shows the mixing of samples.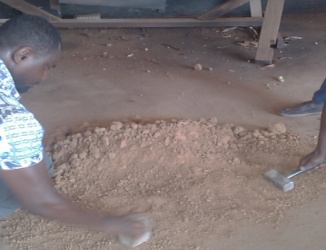 | Figure 5. Crushing of Soil |
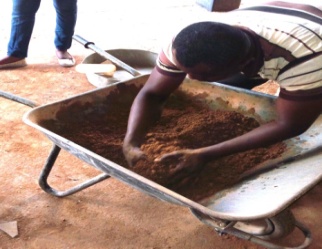 | Figure 6. Mixing |
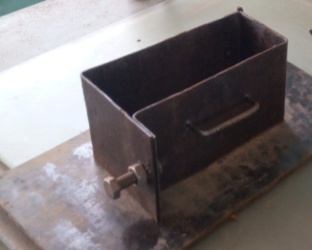 | Figure 7. Block press |
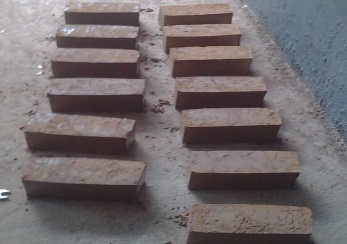 | Figure 8. Curing |
Bricks were made with an improvised manually operated press similar to “Balram” Block press “artifact GmbH Glucksburg. The press has internal nominal dimensions of 230mm (length) 110mm (width) and 90mm (height). Figure 7 shows the block press adopted for brick making.The bricks were demolded under a shed to ensure that they were not affected by the excessive sunlight. The bricks were air dried for 28 days before being tested. Figure 8. Shows the curing of SEBs.
2.4. Testing of Brick Samples
For this research work Four engineering properties were selected to investigate the strength and Durability properties of the stabilized brick samples after 28 days of manufacturing. The main approach adopted was to compare the properties and performance of three categories of blocks, namely: traditional blocks (unsterilized blocks), improved blocks (Pozzo-mix stabilized) and improved blocks (OPC stabilized). These properties are as follows: Wet and Dry Compressive Strength, Abrasion Resistance and Rate of Water absorption.
2.4.1. Dry Block Density
Test is to determine the effect of soil type, stabilizer, moisture content and compaction effort on the density of the bricks. This density
is known to be the ratio of measured block mass (m) to volume (v) i.e.,
. The mass of the bricks was taken after drying in a ventilated oven for 24 hours at a temperature of 105°C in accordance with [18]. The volumes of the bricks were calculated. Averages of the densities of five blocks from each batch were calculated.
2.4.2. Wet and Dry Compressive Strength Test
One durability challenge of compressed earth bricks is resistance to water. After SEB has been exposed to dampness its compressive strength is undermined. This test was conducted to find out whether or not the SEB has improved in strength in damp condition after it has been stabilized with the selected stabilizer. Wet and Dry compressive strength tests was conducted in accordance with [19]. five specimens were selected and placed on a supportive steel block in the lower platen. This lifted the brick within the ambient range of operation of the compressive machine. The specimens were first of all wiped clean of loose materials and dried in an oven before placing in an orientation where the bed faces of the brick rested on the platen, which was the same orientation of the compaction pressure during brick production as shown below in Figure 9. The failure loads for each of the blocks were taken.
2.4.3. Initial Rate of Water Absorption
This test was conducted in accordance with BS 3921. A set of five blocks per sample of SCEB specimen were wiped clean of loose materials and preventively dried in an oven after 28 days curing, till a constant weight was obtained. The cooled bricks were immersed in a 5mm depth of water for 10min. The test setup is as shown in Figure 10. The water absorption coefficient Cb of each block is by convention expressed by the formula:
Where: Mso = Mass after absorption (g), Mdry = Mass before absorption (g)As = Area of exposed face (mm2), T = time (sec), Cws = initial rate of water absorption
2.4.4. Abrasion Resistance (Wire Brush Test)
This test was conducted to determine the minimum amount of selected stabilizer in the soil to achieve a degree of hardness adequate to resist field weathering. BS 3921 and CraTarre (personal communication Vincent Rigassi) modification of [20] procedures were followed. The test was used to determine the surface hardness of the soil brick and thus their resistance to wear. A stiff wire brush made of 50 of 16mm flat 26-gauge wire bristles was used to brush the blocks cyclically. five oven dried bricks were used to average one block. The entire face of the bricks was subjected to mechanical erosion by brushing with a metal brush at a constant pressure over 60 cycles. The brushed faces were gently wiped with a soft cloth to remove all loose materials. The mass of the detached (loose) matter was weighed from which the abrasion coefficient (Cu) was calculated as follows:
Where A=Area of brushed surface. (cm2), m1=mass of brick before brushing (g).m2=mass of brick after brushing (g).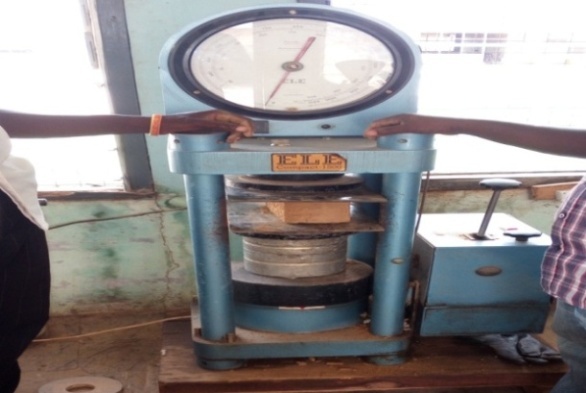 | Figure 9. Crushing of Bricks |
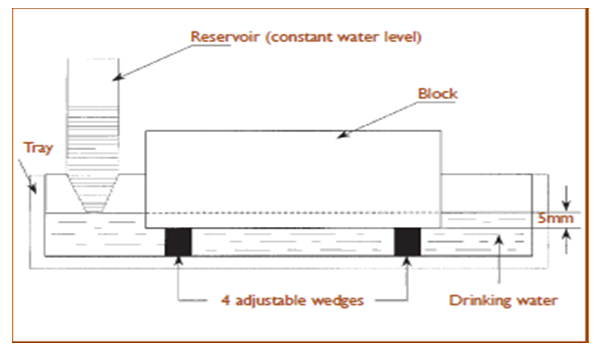 | Figure 10. Setup of Water Absorption Test |
3. Results and Discussions
3.1. Particle Size Distribution
The particle size distribution revealed a 0.09% grain size retained on 4.75mm sieve in the sample sieved. Again, size limit passing the 0.075mm sieve was 46.85%. 53.15% represent the percentage of soil fraction retained between BS. Sieves 4.75 to 0.075. The high sand fraction in the soil formed the stable constituent, though they lack cohesion when dry, but have a high degree of internal friction between the particles which make them up.
3.2. Optimum Moisture Content
Optimum moisture content after 28 days air dried specimen was recorded at 13% water addition with a dry density of 2173kg/m3. The 14% water addition recorded dry density value of 1956kg/m3 which is higher than that of 12% water addition (1998kg/m3). From Table 1 it is clear that increasing the water content beyond the 13% water content will reduce the dry density of the brick specimen. Table 2 presents a summary of clay soil characteristics.Table 1. Results of Optimum Moisture Content Test 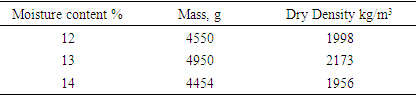 |
| |
|
Table 2. Summary of Characteristics of the Clay Soil 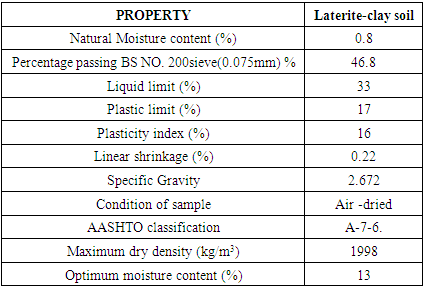 |
| |
|
3.3. Characteristics of Earth Bricks
3.3.1. Density of Specimens
From the results presented in Table 3, it is noticed that density steadily increased as Pozzo-mix- OPC content increases. Expected densities commonly range between 1700kgm3 and 2200kg/m3 [21]. [22] used bricks of densities within the range of 1500- 2400 as specifies by BS 6073 for a dense aggregate masonry unit. Densities of individual bricks specimen in a batch varied slightly possibly because of variation in the amount of mix fed into the block press. The errors were minimized else accumulation could affect the durability of the bricks [23]. It was clear that the addition of OPC in the batch effected a significant increase in density. The outcome of the results suggests that increasing the percentage of Pozzo-mix –OPC beyond 8% Pozzo-mix + 4% OPC will not cause any significant increase in density compared to the density of specimens with 12% Pozzo-mix + 0% OPC. From the regression analysis in Table 5 it is clear that variation in ordinary Portland cement quality and amount can drastically affect its properties and behavior more than any other input variables [24]. The pozzolanic action has a particularly stabilizing effect because it binds soil particles together as various cementitious compounds are formed.Table 3. Results of Dry Density of Pozzo-mix- OPC Stabilized Earth Bricks  |
| |
|
Table 4 presents the correlation among the study variables which indicates that, Pozzo-mix used for producing bricks strongly correlates significantly at the 5% level of significance with density of earth bricks (r=0.721, p<0.05). Ordinary Portland cement (OPC) was found to positively correlate with density of bricks specimen but insignificant (r=0.583, p>0.05).Table 4. Correlation among Pozzo-mix, OPC and Density 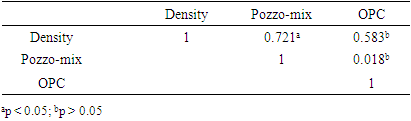 |
| |
|
The experimental correlation between density, Pozzo-mix and OPC levels is outlined in Table 5. The best fit represented in equation (1) shows a strong linear correlation (R2=0.846), represented in the equation:  | (1) |
Y= Density of specimens Where x1 is percentage Pozzo-mix content.x2 is percentage OPC content.The coefficient of determination value suggests that the percentage replacement of Pozzo-mix and OPC content explains about 77% of the variation in density of the earth brick specimen (Adjusted R2 = 0.769). As it would appear to be expected, Pozzo-mix and OPC content is associated with higher density. The result of the ANOVA test on the density of Pozzo-mix and OPC Stabilized bricks specimens indicates a significant prediction using the model developed (F = 10.981, p<0.05). The unstandardized coefficient suggests that, an increase in Pozzo-mix and OPC content by one percent will increase the density by 1581kg/m3 (t= 3.624, p<0.05) and 2959kg/m3 (t= 2.907, p<0.05) respectively when all other variables remain constant. Also, when all other variables remain constant the beta value suggests that an increase in the percentages of Pozzo-mix and OPC by one standard deviation will increase the density on the average by 0.711kg/m3 and 0.571kg/m3 respectively. Again, this stipulates that Pozzo-mix contributes the highest of about 71% to the density while OPC contributes to about 57% of the density of Stabilized earth blocks.
3.3.2. Dry Compressive Strength of Specimen
From Table 6 Pozzo-mix replacement from 5% to 12% saw an increase in dry compressive strength from 12% to 30.1% over the control group. Comparing Stabilized composition, it can be observed that specimens with 3%Pozzo-mix+ 2% OPC increased about 19.5% over brick specimens with 5% Pozzo-mix+0% OPC content. The results of dry compressive strength values recorded conforms with the minimum dry compressive strength recommended by (BS 5628: Part 1, 1978). Table 7 presents correlation between Dry compressive strength, ordinary Portland cement (OPC) and Pozzo-mix content. The relationship depicts that, Pozzo-mix used for producing bricks have a weak correlation with dry compressive strength of earth bricks (r=0.322, p>0.05) at 5% significant level. Ordinary Portland cement (OPC) used for the earth bricks fabrication was found to significantly correlate strongly with Dry compressive strength of bricks specimen (r=0.891, p<0.01).Table 5. Regression Analysis of Density of Specimens 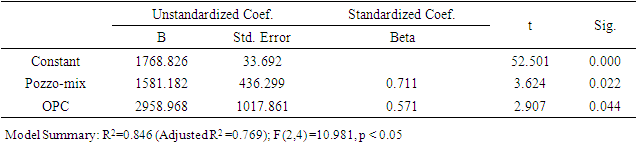 |
| |
|
Table 6. Results of Dry Compressive Strength of Pozzo-mix- OPC Stabilized Earth Bricks 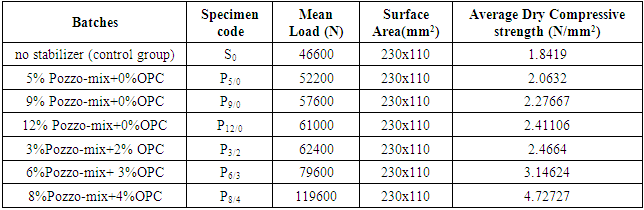 |
| |
|
Table 7. Correlation Between Pozzo-mix, OPC and Dry compressive Strength 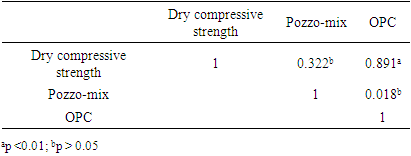 |
| |
|
Table 8. presents regression analysis of Stabilized earth bricks Stabilized with Pozzo-mix and OPC contents which depicts a significant prediction using the model developed (F =15.977, p < 0.05) as obtained by computing ANOVA. The best fit shows a strong linear correlation (R2=0.889) as shown in equation (2) | (2) |
The coefficient of determination value suggests that the percentage replacement of Pozzo-mix and OPC content explains about 83% of the variation in dry compressive strength of the earth brick specimen (Adjusted R2 = 0.833). The unstandardized coefficient suggests that, an increase in Pozzo-mix by one percent will increase the dry compressive strength by 7.56N/mm2 (t=1.838, p>0.05) while an increase in OPC content by one percent will increase the strength by 50.98N/mm2 (t= 5.312, p<0.01). Also, the beta value suggests that an increase in the percentages of Pozzo-mix and OPC by one standard deviation will increase the density on the average by 0.307N/mm2 and 0.886N/m2 respectively when all other variables remain constant. Again, this stipulates that Pozzo-mix contributes to about 30.7% to the dry compressive strength while OPC contributes to about 89% to the dry compressive strength of Stabilized earth blocks. This implies that ordinary Portland cement contributes the most in the strength of the Stabilized earth bricks.Table 8. Regression Analysis of Dry Compressive Strength of Specimens 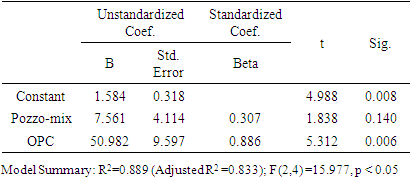 |
| |
|
3.3.3. Wet Compressive Strength of Specimen
Again, the results presented in Table 9, shows a clear increase in wet compressive strength with increase in levels of Pozzo-mix from 5% to 12%. The strength values ranged from 1.02N/mm2 to 1.83N/mm2. The trend shows that, increasing Pozzo-mix content from 5% to 12% increases the wet compressive strength from 148% to 346% over the un-Stabilized brick specimens. Again adding 4% Pozzo-mix+ 2% OPC, 6% Pozzo-mix+ 3% OPC and 8% Pozzo-mix+ 4% OPC improved the earth bricks by 203.8%, 319% and 417% respectively over the control specimens. The specimens maintained a good and recommended wet compressive strength except the un-Stabilized bricks and the 5% Pozzo-mix brick specimens.Table 9. Results of Wet Compressive Strength of Pozzo-mix- OPC Stabilized Earth Bricks 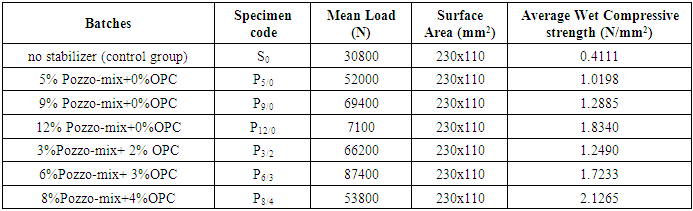 |
| |
|
Table 10 depicts the correlation between wet compressive strength, ordinary Portland cement (OPC) and Pozzo-mix cement. There is a positive association between Pozzo-mix cement for brick production and wet compressive strength. The correlation suggests a strong relationship between Pozzo-mix and wet compressive strength of earth bricks (r=0.768, p<0.05). Ordinary Portland cement (OPC) used for the earth brick stabilization was found to correlate with wet compressive strength of bricks specimen but insignificant (r=0.642, p>0.05).Table 10. Correlation Between Pozzo-mix, OPC and Wet Compressive Strength 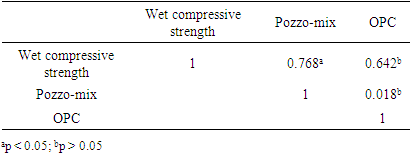 |
| |
|
The experimental correlation between wet compressive strength and Pozzo-mix and OPC levels is outlined in Table 11. The line of best fit shows a strong linear correlation (R2=0.984), represented by equation (3): | (3) |
werey= wet compressive strengthx1 is Pozzo-mix content x2 OPC content. The coefficient of determination value suggests that the percentage replacement of Pozzo-mix and OPC explains about 98% of the variation in the wet compressive strength of the earth bricks specimen (Adjusted R2 =0.976). As it would appear to be expected, higher Pozzo-mix and OPC contents is associated with higher wet compressive strength. The results of the ANOVA test on the Wet compressive strength of Pozzo-mix and OPC stabilized bricks indicates a significant prediction using the model developed (F = 123.195, p < 0.01). The unstandardized coefficient suggests that, an increase in Pozzo-mix and OPC content by one percent will increase the wet compressive strength by 10.92N/mm2 (t=11.973, p<0.01) and 21.15N/mm2 (t=9.939, p<0.01) respectively. Also, the beta value suggests that a percentage increase in Pozzo-mix and OPC by one standard deviation will increase the dry compressive strength on the average by 0.757N/mm2 and 0.628N/mm2 respectively. Again, this stipulates that Pozzo-mix and OPC content contribute to about 76% and 63% respectively to the wet compressive strength of stabilized earth blocks, which meant that Pozzo-mix cement as a Stabilized in earth bricks can resist water intake thereby retaining its strength.Table 11. Regression Analysis of Wet Compressive Strength of Specimens 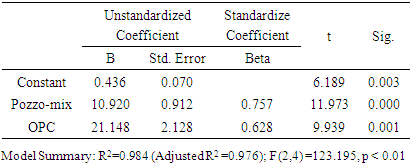 |
| |
|
3.3.4. Initial Rate of Water Absorption of Specimens
From Table 12, it can be observed that all the earth bricks absorbed some amount of water due to capillary action. Significantly the amount of water absorbed saw a gradual declines as the amount of Pozzo-mix- OPC replaced increased. It is clear that adding 4% OPC to 8%Pozzo-mix can reduce water intake in earth bricks tremendously. Generally, all the earth bricks had IRA within recommended limits.Table 12. Results of Initial Rate of Water Absorption of Pozzo-mix- OPC Stabilised Earth Bricks 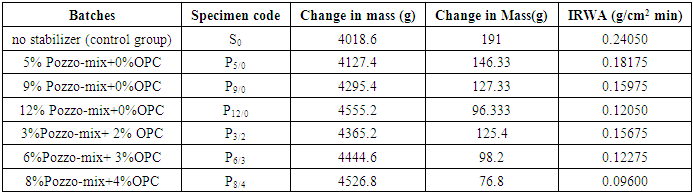 |
| |
|
Table 13, presents the correlation metrixs between initial rate of water absorption, ordinary Portland cement (OPC) and Pozzo-mix cement. There is a negative association between Pozzo-mix cement for brick production and initial rate of water absorption. The correlation suggests a strong significant relationship between Pozzo-mix content and water absorption of earth bricks (r= - 0.749, p<0.05). Ordinary Portland cement (OPC) used for the earth brick stabilisation was found to correlate negatively with water absorption of bricks specimen but insignificantly. (r= - 0.653, p>0.05).Table 13. Correlation Between Pozzo-mix, OPC and Initial Rate of Water Absorption (IRWA) 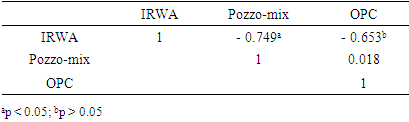 |
| |
|
The experimental correlation between initial rate of water absorption and Pozzo-mix and OPC levels is outlined in Table 14. The best fit shows a strong linear correlation (R2=0.970) as shown in equation 4 | (4) |
werex1 is Pozzo-mix content,x2 OPC contenty = initial rate of water absorption. The coefficient of determination value suggests that the percentage replacement of Pozzo-mix and OPC explains about 96% of the variation in the initial rate of water absorption of the earth bricks specimen (Adjusted R2 =0.955). As it would appear to be expected, higher Pozzo-mix and OPC content is associated with higher initial rate of water absorption. The results of the ANOVA test on the initial rate of water absorption of Pozzo-mix and OPC stabilized bricks indicates a significant prediction using the model developed (F =64.011, p < 0.001). The unstandardized coefficient suggests that, an increase in Pozzo-mix by one percent will reduce the water absorption by 0.886g/cm2 min (t= -8.473, p<0.01) and an increase in OPC by one percent will reduce the water absorption by 1.793.g/cm2 min (t= -7.349, p<0.01). Also, the beta value suggests that a percentage increase in Pozzo-mix and OPC by one standard deviation will reduce the water absorption on the average by 0.738g/cm2 min and 0.640g/cm2 min respectively. This suggests that Pozzo-mix and OPC content contribute to about 74% and 64% respectively to the initial rate of water absorption of stabilized earth blocks. This prediction meant that Pozzo-mix cement has a higher water repellant ability than OPC.Table 14. Regression Analysis of Initial rate of water absorption of Specimens 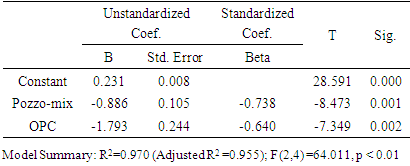 |
| |
|
3.3.5. Abrasion Resistance on Specimens
The results presented in Table 15 show a clear increase in abrasion resistance as the amount of Pozzo-mix- OPC content increases. Comparing batches, it is clear that specimens with 3% Pozzo-mix+2%OPC saw an improvement of 33.7% over specimens with 5% Pozzo-mix+0%OPC content. there was a significant improvement of 28.92% in surface abrasion for bricks specimens with 6% Pozzo-mix+3%OPC replacement over specimens with 9% Pozzo-mix+0%OPC. Again, the batch with 8% Pozzo-mix+4%OPC addition recorded an increase in resistance to surface wearing of about 18.15% over specimens with 12% Pozzo-mix+0%OPC.Table 16, shows the correlation between abrasion resistance, OPC and Pozzo-mix cement. There is a positive association between Pozzo-mix cement for brick production and abrasion resistance. The correlation suggests a strong significant relationship between Pozzo-mix and abrasion resistance of earth bricks (r=0.783, p<0.05). Ordinary Portland cement (OPC) used for the earth brick stabilization was found to correlate with wet compressive strength of bricks specimen but insignificant (r=0.560, p>0.05).Table 15. Results of Abrasion Resistance of Pozzo-mix- OPC Stabilized Earth Bricks 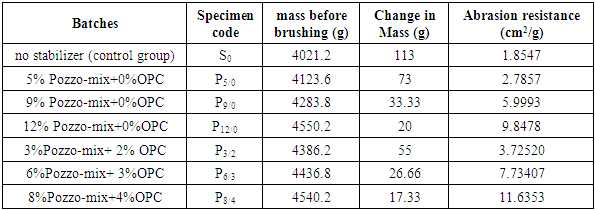 |
| |
|
Table 16. Correlation Between Pozzo-mix, OPC and Abrasion Resistance 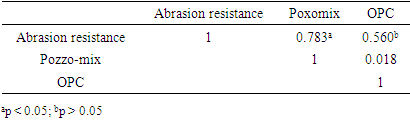 |
| |
|
The experimental correlation between abrasion resistance and Pozzo-mix and OPC levels is outlined in Table 17 shows a strong linear correlation (R2=0.912), represented in the equation: | (5) |
where y= Abrasion resistancex1 is Pozzo-mix contentx2 OPC content. The coefficient of determination value suggests that the percentage replacement of Pozzo-mix and OPC explains about 87% of the variation in the abrasion resistnce of the earth bricks specimen (Adjusted R2 =0.868). the outcome revealed that higher Pozzo-mix and OPC content is associated with higher abrasion resistance. The results of the ANOVA test on the abrasion resistance of Pozzo-mix and OPC stabilized bricks indicates a significant prediction using the model developed (F =20.750, p < 0.01). The unstandardized coefficient suggests that, an increase in Pozzo-mix and OPC content by one percent will increase the abrasion resistance by 71.890cm2/g (t=5.218, p<0.01) and 118.474cm2/g (t=3.686, p<0.05) respectively. Also, the beta value suggests that a percentage increase in Pozzo-mix and OPC by one standard deviation will increase the dry compressive strength on the average by 0.774cm2/g and 0.547cm2/g respectively. Again, this depicts that Pozzo-mix and OPC content contribute to about 77% and 55% respectively to the abrasion resistance of stabilized earth blocks which means that Pozzo-mix cement as a stabiliser in earth bricks contributes the most in wearing resistance of specimens.Table 17. Regression Analysis of Abrasion Resistance of Specimens 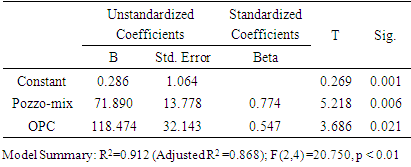 |
| |
|
4. Conclusions
The principal objective of this studies was to investigate the strength and durability properties of stabilized earth blocks for affordable housing. In the light of the results of the experimental test reported in this study it can be concluded that:Earth can be used as an alternative material to replace conventional building materials such as concrete and mortar. Pozzo-mix cement can contribute to the density of earth bricks. There exist a relationship between the dry density and compressive strength of earth blocks. The dry compressive strength values obtained in the study were within specified limits and suitable for single storey dwellings. Increasing Pozzo-mix and OPC content in earth block production can significantly increase the strength and durability criteria of SEBs. It was obvious that OPC as admixture can significantly improve the wet and dry compressive strength of soil blocks, therefore making them suitable as masonry wall units. Higher percentages of the composite stabilizer materials showed significant resistance to water absorption and abrasion, which are mostly the setbacks of earth blocks. It is worth noting that the use of Pozzo-mix cement alone should be used cautiously especially lower percentages and in poor soils. Earth blocks are of cultural significance to most African and Asian countries however its weak structural integrity has been the major setback, there is the need to improve on its properties by way of stabilization before adoption. It is recommended that the curing duration should be extended longer than the 28 days used for the study for Pozzo -mix to cure properly. With Pozzo- mix and OPC combined stabilizer, there could be wide range adoption of this building material in low- and middle-income countries.
ACKNOWLEDGEMENTS
This work was supported by Ghana High way Authority Material Lab and St. John Boscos College of Education research Grant.
References
[1] | Ghana Statistical Service. (2021). Ghana 2021 Population and Housing Census General Report. |
[2] | Ogunsemi D. R., (2010) "The use of enough quality and quantity materials for building a durable edifice," in A Lecture delivered at Campus Transformation Network, Akure, Nigeria. |
[3] | Danso, H., & Manu, D. (2013). High Cost of Materials and Land Acquisition Problems in the Construction Industry in Ghana. IJREAS International Journal of Research in Engineering & Applied Sciences International Journal of Research in Engineering & Applied Sciences, 3(19), 18–33. http://www.euroasiapub.org. |
[4] | Anigbogu, N. A. (1999). Economic of Alternative Construction Materials: Some Conceptual Issues. |
[5] | Josiah Marut, J., ALAEZI, J. O., & OBEKA, I. C. (2020). A Review of Alternative Building Materials for Sustainable Construction Towards Sustainable Development. Journal of Modern Materials, 7(1), 68–78. https://doi.org/10.21467/jmm.7.1.68-78. |
[6] | Garric, J. P., Baridon, L., & Richaud, G. (2016). Les publications de François Cointeraux, dans le contexte contemporain des publications sur l’architecture rurale. |
[7] | Data and Statistics. (2020). Retrieved from International Energy Agency: https://www.iea.org. |
[8] | Elizondo, M. F., Guerrero, L. F., & Mendoza, L. A. (2011). Environmental impact: Comparison between earthen architecture and conventional construction. WIT Transactions on the Built Environment, 118, 475–484. https://doi.org/10.2495/STR110391. |
[9] | Zami, M. (2008). Using earth as a building material for sustainable low cost housing in Zimbabwe. The Built and Human Environment Review, 1, 40–55. |
[10] | Danso, H. (2019). Characterization of Compressed Earth Blocks Stabilized with Clay Pozzolana Journal of Civil & Environmental Characterization of Compressed Earth Blocks Stabilized with Clay Pozzolana. 9(1), 1–6. |
[11] | Yalley, P. . (2019). High volume of Pozzolana Mechanical and Durability Properties of Engineered Cementitious Composite Containing High Volume of Pozzolanic admixture. American Journal of Engineering Research, 8(4), 229–235. www.ajer.org. |
[12] | Harichane, K. (2010). Effect of Combination of Natural Pozzolana on the Durability of the Clayey Soils. Electrical Journal of Geotechnical Engineering, 15, 1194-1210. |
[13] | Vakili, A. H., Selamat, M. R., & Moayedi, H. (2013). Effects of using pozzolan and portland cement in the treatment of dispersive clay. The Scientific World Journal, 2013(1977). https://doi.org/10.1155/2013/547615. |
[14] | ASTM C618-19 (2019) Standard Specification for Coal Fly Ash and Raw or Calcined Natural Pozzolan for Use in Concrete. ASTM International, West Conshohocken. |
[15] | BS1377, Part 2. (1990). British Standard Methods of Test for Soils for Civil Engineering Purposes, Part 2: Classification tests. British Standards Institution, London. |
[16] | BS 1924-2 (1990). Stabilizer materials for civil engineering purposes – Part 2 Methods and lime-stabilized materials. BSI London. |
[17] | Namango, S. S., & Madara, D. S. (2014). Compressed earth blocks reinforced with sisal fibres. Journal of Agricultural Pure Applied Science and Technology, 19, 10-22. |
[18] | BS1880, (1990). Code of Practice for earth, Part 1 British Standard Institution, London: British Standard. |
[19] | BS EN 12390-3 (2002) Testing Concrete. Method for Determination of Compressive Strength of Concrete Cubes. British Standards Institution. |
[20] | ASTM 1944, D559-44, Wetting and Drying Test of Compacted Soil-Cement Mixtures. |
[21] | Rigassi, V. (1995). Compressed earth blocks: Manual of production. De Autsches Zentrum fur Entwicklungs technologien-GATE. |
[22] | Yalley P.P., & Adogla, F. & Arkoh, M. (2022). Improving Compressed Laterite Bricks using Powdered Eggshells Improving Compressed Laterite Bricks using Powdered Eggshells. 71-75. |
[23] | Lunt, M.G. (1980). Stabilised Soil Blocks for Building. Overseas Building NoteNo. 184. Building Research Establishment. February 1980. Garston, England. |
[24] | Gooding, D.E.M. (1994). Improved Processes for the Production Soil-Cement Building Blocks. PhD Thesis. University of Warwick. Coventry, England. |