Miskir Gebrehiwot, Robi Diriba
Department of Civil Engineering, Assosa University, Assosa, Ethiopia
Correspondence to: Miskir Gebrehiwot, Department of Civil Engineering, Assosa University, Assosa, Ethiopia.
Email: |  |
Copyright © 2020 The Author(s). Published by Scientific & Academic Publishing.
This work is licensed under the Creative Commons Attribution International License (CC BY).
http://creativecommons.org/licenses/by/4.0/

Abstract
Construction industry involves the application of different construction materials and equipment that makes the industry to consume big capital budget. Concrete is one of the construction materials which is the composition of cement, coarse aggregate, fine aggregate and water. Among the production processes of concrete, curing is a vital process to give the concrete it’s final strength. To attain the required final strength of concrete suitable amount and quality of water should be applied. Curing usually conducted by application of enough water on the casted structure for the required days of curing. But the application of the usual watering method for the areas like Assosa town is very difficult since there is a high scarcity of water in the town. The main objective of this study is to compare the compressive strength of C25 concrete cured by water curing and shrinkage reducing admixture (Polyethylene glycol 4000). And specifically to determine the physical properties of ingredients used in mix designing process, to determine compressive strength of C25 concrete cured by water immersion (CCWI), cured by water sprinkling (CCWS) and cured by self-curing admixture (Polyethylene glycol 4000) (CCS) and finally to compare the curing capacity of CCWI, CCWS and CCS, C25 concretes based on the determined compressive strength results. Based on the 28th day mean compressive strength results, CCWI, CCWS and CCS samples attained 33.53Mpa, 28.8Mpa and 34.37Mpa compressive strength results respectively. According to the observed change in compressive strength from the 7th to 14th to 28th days of curing CCS samples shows higher increment in compressive strength than both CCWI and CCWS samples which indicates better curing capacity.
Keywords:
Compressive strength, Curing, Polyethylene glycol 4000, Properties of ingredients
Cite this paper: Miskir Gebrehiwot, Robi Diriba, Comparative Study on the Compressive Strength of C-25 Concrete Cured by Water Curing and Self-Curing Methods; A Case Study in Assosa, Ethiopia, Journal of Civil Engineering Research, Vol. 10 No. 2, 2020, pp. 47-52. doi: 10.5923/j.jce.20201002.03.
1. Introduction
Curing is the name given to the process used for promoting the hydration of the cement. It controls temperature and moisture movement from and into the concrete. Curing allows continuous hydration and strength gain. Once curing stops strength gain of the concrete also stops. Proper moisture conditions are critical because the hydration of the cement virtually ceases when the relative humidity within the capillaries drops below 80% (ACI, 2009). If the water applied for curing is insufficient, the hydration in the cement paste will not proceed and the resulting concrete may not possess the desired strength and impermeability. Additionally, durability problem may arise due to the entrance of deleterious agents caused by the continuous pore structure formed on the near surface. More over due to early drying, micro-cracks or shrinkage cracks would develop on the surface of the concrete (C. Selvamony et al., 2010). Application of Unclean water for curing results quality problems on the concrete. Suitable Water for making concrete should also be used for curing purpose. Waters containing impurities that leading to stains is intolerable. When concrete is subjected to prolonged wetting, even a very low concentration of iron and organic matter may cause staining (S.K. Duggale, 2008).Since there is a higher scarcity of water in Assosa town, application of clean water for curing will be difficult. So to overcome this problem another alternative method of curing should be applied. These study focused on Self -curing concrete by the application of shrinkage reducing admixtures. Self –curing is very important from the point of view that saving of water is a necessity every day. One cubic meter of concrete requires 3m3 of water in construction and most of which is used for curing (Dayalan j and Buellah, 2014).The general objective of this study is to compare the compressive strength of C25 concrete by applying water curing and shrinkage reducing admixture (Polyethylene glycol 4000) curing. The specific objectives of this study are to determine the physical properties of concrete ingredients, to determine compressive strength of both watering and admixture cured C25 concretes and to compare curing capacity of both water cured and admixture cured C25 concretes at different ages of curing.
1.1. Curing of Concrete
The rate and extent of moisture loss from concrete during cement hydration is controlled by curing. The hydration of cement take time, days, and even weeks rather than hours.There are two major methods of internal curing currently available. The first method uses saturated porous lightweight aggregate (LWA) in order to supply an internal source of water, which can replace the water consumed by chemical shrinkage during cement hydration. The second method uses poly-ethylene glycol (PEG) which reduces the evaporation of water from the surface of concrete and also helps in water retention. Self-Curing concrete is the newly emerging trend in the construction industry (Patel Manish Kumar, 2014). To achieve potential strength and durability requirements of the concrete, curing must be undertaken for a reasonable period of time. The cement hydration also controlled by curing. The curing period may depend on the properties of concrete, the purpose for which it is to be used, and the ambient conditions of the surrounding atmosphere. Curing is designed primarily to keep the concrete moist, by preventing the loss of moisture from the concrete during the period in which it is gaining strength. Curing may be applied in a number of ways and the most appropriate means of curing may be dictated by the site or the construction method (Bentiz D., 2002).One of the modern concrete type immerged is self-curing concrete. Self-curing concrete cures itself by retaining water (moisture). Self-curing or internal curing is technique that can be used to provide additional moisture in concrete for more effective hydration of cement and reduced self- dehydration (Patel Manish Kumar, 2014).Polyethylene glycol is a condensation polymer of ethylene oxide and water with general formula H(OCH2CH2)nOH where “n" is the average number of repeating Oxethylene groups typically from 4 to about 180. The abbreviation (PEG) is termed in combination with a numeric suffix which indicates the average molecular weights. One common feature of PEG appears to be the water-soluble nature. Polyethylene glycol is non-toxic, odourless, neutral, and lubricating (M.V. Jagannadha et al., 2012).Polyethylene glycols (PEGs) are family of water soluble linear polymers formed by the additional reaction of Ethylene oxide (EO) with Mono ethylene glycol (MEG) or Diethylene glycol. Though the increase in strengths were very small, it was observed that PEG involves complete internal curing of the concrete and helps to achieve a strength very nearer to the full strength of conventional reference mix (SR. Thiruchelve et al., 2017). Babitha Rani, et al., (2017) on their study on self-curing concrete with the addition of polyethylene glycol -4000, concluded that that PEG 4000 help in self-curing by giving strength on par with conventional curing. It was also found that 1% of PEG 4000 by weight of cement was optimum for M20 grade concretes for achieving maximum strength without compromising workability.The mechanism of self-curing can be explained that, the polymer added in the mix mainly form hydrogen bonds with water molecules and reduce the chemical potential of the molecules which in turn reduces the vapour pressure. This reduces the rate of evaporation from the surface. (N. Gowripalan et. al. 2001).
1.2. Types of Concrete Curing
1.2.1. Dry Air Curing
Dry curing is a curing of concrete cubes by letting them to cure at room temperature in open air. Dry-air curing produced 15.2% in compressive strength, 6.59% in dynamic modulus of elasticity and 3.36% in ultrasonic pulse velocity reduction. This results early drying of concrete which virtually ceased hydration of the cement which resulted due to the relative humidity within capillaries dropped below 80%. Also, it caused 12.4% and 46.53% increase in initial surface absorption after 10 and 120 minutes respectively. This might be due to micro cracks or shrinkage cracks resulting from the early drying out of the concrete. Experimental results indicate that Dry-curing is not an efficient method to achieve good hardened properties of concrete (Fauzi, 1995).
1.2.2. Water Curing
Water curing is carried out by supplying water to the surface of concrete to keep it moist. The water used for this purpose should not be more than about 5°C cooler than the concrete surface. Spraying warm concrete with cold water may give rise to ‘thermal shock’ that may cause or contribute to cracking. Alternate wetting and drying of the concrete must also be avoided as this causes volume changes that may also contribute to surface crazing and cracking (Nirav R., 2013).
1.2.3. Wet Coverings
Wet coverings curing is done by Fabrics such as hessian, or materials such as sand, to maintain water on the surface of the concrete. On flat areas, fabrics may need to be weighed down. Wet coverings should be placed as soon as the concrete has hardened sufficiently to prevent surface damage. They should not be allowed to dry out as they can act as a wick and effectively draw water out of the concrete. Fabrics may be particularly useful on vertical surfaces since they help distribute water evenly over the surface and even where not in contact with it, will reduce the rate of surface evaporation (Md. Safuddin et al., 1991).
1.2.4. Membrane-Forming Curing Compounds
These method of curing processed by retarding or reducing moisture from concrete by applying Liquid membrane forming -forming compounds consisting of waxes, resins, chlorinated rubber, and other materials. They are the most practical and most widely used method for curing not only freshly placed concrete but also for extending curing of concrete after removal of forms or after initial moist curing. Curing compounds should be able to maintain the relative humidity of the concrete surface above 80% for seven days to sustain cement hydration (NirR., 2013).
1.2.5. Internal Moist Curing
Internal moist curing refers to methods of curing by providing moisture within the concrete as opposed to outside the concrete. This water should not affect the initial water to cement ratio of the fresh concrete. Lightweight (low-density) fine aggregate or absorbent polymer particles with an ability to retain a significant amount of water may provide additional moisture for concretes prone to self-desiccation. (Nirav R., 2013).Internal curing (IC) is a method to provide the water to hydrate all the cement, accomplishing what the mixing water alone cannot do. It Provides water to keep the relative humidity (RH) high, keeping self-desiccation from occurring. And also self-curing method eliminates largely autogenous shrinkage and Maintains the strengths of mortar/concrete at the early age (12 to 72 hrs.) above the level where internally & externally induced strains can cause cracking. It Can make up for some of the deficiencies of external curing, both human related (critical period when curing is required in the first 12 to 72 hours) and hydration. (M.V. Jagannadha et al., 2012).
2. Materials and Methods
2.1. Types of Concrete Curing
The materials used in this study are cement, coarse aggregate, fine aggregate, water and self -curing Admixture (Polyethylene glycol 4000). The selection of self-curing admixture was based on its availability in the market. The sources of materials used in this study are; Ø Dangote OPC cement 42.5 -from marketØ Coarse aggregate- from Benshangul Gumuz region Ø Fine aggregate - from Benshangul Gumuz region Ø Water- from tap water system and Ø Self-curing admixture (polyethylene glycol 4000)- from market
2.2. Sampling Techniques and Sample Size
Selection of samples for this study was purposive sample selection. For the determination of the properties of the ingredients, the amount of materials was taken as per the requirements of the test methods. For compressive strength test of C25 concrete 3 cubes for each testing days (7days, 14 days and 28 days) was casted for CCWI, CCWS and CCS concrete types as per the mix design determined before. CCWI stands for concrete cured by water immersion method for 7, 14 and 28 consecutive days. CCWS is concrete sample refers to concrete cured by water sprinkling for 7, 14 and 28 consecutive days. Method of curing applied for this sample were by using sprinkling of water twice a day. These method of curing is the usual method applied on different building constructions in the study area. CCS stands for concrete cured by PEG-4000.Table 1. Test Samples for Compressive Strength Test 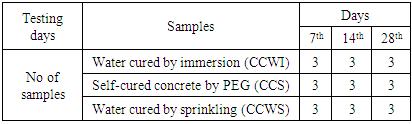 |
| |
|
Table 2. Material Proportion 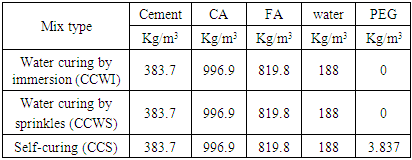 |
| |
|
The quantity of PEG applied was 1% of the cement content which is the optimum content (Babitha Rani, et al., (2017).
2.3. Data Analysis
Primary data for this study was collected form the results of laboratory experiments. Properties of ingredient that affect the mix design of the concrete were determined in BDU construction materials laboratory. The collected data was analysed by comparing the results with ASTM standard to insure the suitability of the materials. Compressive strength test results were also collected from laboratory. For the three (CCWI, CCWS and CCS) samples a total of 27 cubes were tested. The data obtained was analysed by comparing the average compressive strength result of each sample for 7th, 14th and 28th days of curing and the result is presented by charts and tables.
3. Result and Discussion
The general objective of this study is to compare the compressive strength of C-25 concrete cured by water curing and self-curing methods. Specifically, this study was also aimed to determine the physical properties of concrete ingredients, to determine the compressive strength of water cured and self- cured C-25 concrete and finally to compare the curing capacity of both types of concretes.
3.1. Properties of Ingredients
The result of the physical properties of ingredients determined in this study were summarized on the Table 3 below. Table 3. Properties of Ingredients 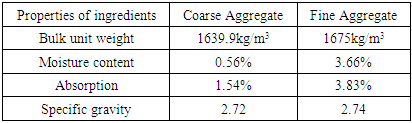 |
| |
|
The properties of ingredients were according to ASTM test procedures. According to the result obtained the minimum requirement was fulfilled.Gradation for both fine and coarse aggregate was conducted. As shown on the gradation curve both fine and coarse aggregates used in this study has full filled the minimum requirement. 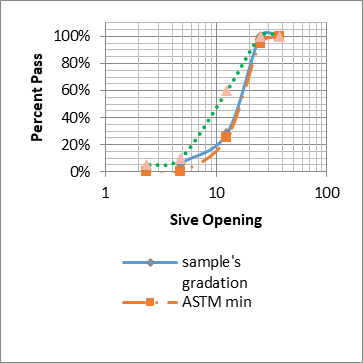 | Figure 1. Gradation curve for coarse aggregate |
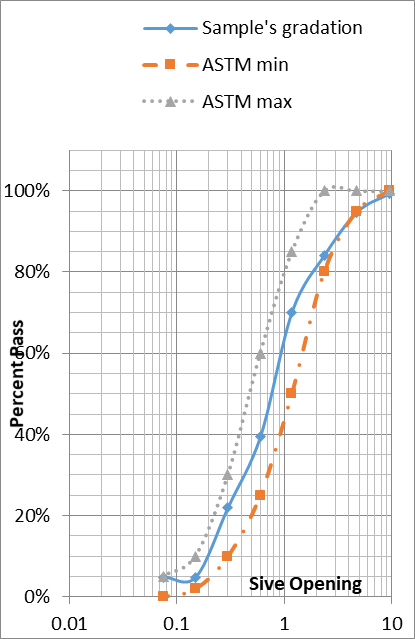 | Figure 2. Gradation curve for fine aggregate |
3.2. Compressive Strength Results
The average compressive strength test results of CCWI at the 7th, 14th and 28th days of curing were 13.83Mpa, 26.1Mpa and 33.53Mpa respectively.The average compressive strength test results of CCWS at the 7th, 14th and 28th days of curing were 12.8Mpa, 21.9Mpa and 28.8Mpa respectively. The average compressive strength test results CCS at the 7th, 14th and 28th days of curing were 16.4Mpa, 28.87Mpa and 34.37Mpa respectively. 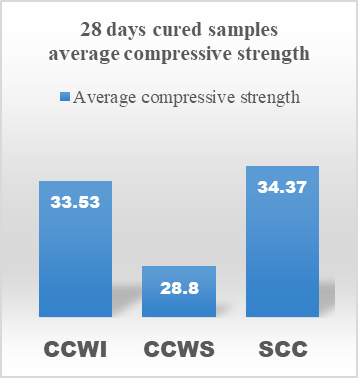 | Figure 3. Average 28th day compressive strength results |
The concrete samples cured by the self-curing method by the application of polyethylene glycol (SCC) admixture, attained the better strength than CCWI and CCWS samples and. On the other hand, the concrete samples cured by water sprinkling method twice a day (CCWS) has relatively the smallest average compressive strength result. Since all the ingredients (cement, sand and water) used in the three different samples have the same qualities and quantities except the addition of the polyethylene glycol for the self-curing concrete samples, the key factor that will mainly affect their strength is the different methods of curing.The self-curing, by the application of admixture is better than the method of curing by water immersion and water sprinkling methods.
3.3. Curing Capacity
As it is illustrated on Figure 4. the compressive strength results of CCWI samples attained better compressive strength at all ages of curing than the CCWS concrete samples. This indicates that the conventional method of curing which is curing by immersion process is better for laboratory testing of samples. The average compressive strength value of CCWI increased by 12.27Mpa from the 7th days of curing to the 14th days of curing. Whereas the average compressive strength of CCWS sample increased by 9.1Mpa. This indicates that from the 7th to 14th days of curing days the concrete samples cured by immersion shows better curing capacity than the samples cured by water sprinkling method. The average compressive strength of CCWI concrete samples compressive strength value increased by 7.43Mpa from 14th to 28th days of curing. Whereas for the CCWS concrete samples it increased by 6.9Mpa. This also indicates that from the 14th to 28th days of curing the concrete samples cured by immersion shows better curing capacity than the samples cured by water sprinkling method. 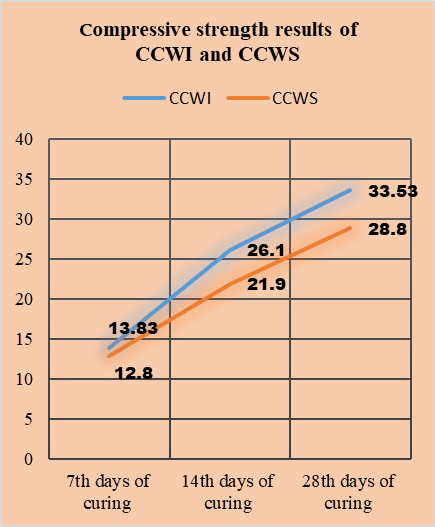 | Figure 4. Average compressive strength results of CCWI and CCWS |
Figure 5 shows the relation of the average compressive strength of CCWI and CCS at the 7th, 14th and 28th days of curing. As its clearly shown, the concrete samples attained better strength for all days of curing for concrete samples cured by self-curing method than the water immersion method. When we see the tendency of curing the average compressive strength value of CCWI increased by 12.27Mpa from the 7th days of curing to the 14th days of curing and the average compressive strength value of CCS increased by 12.47Mpa from the 7th days of curing to the 14th days of curing. This indicates that the self-cured concrete sample has attained better curing than the CCWI sample. The average compressive strength of CCWI concrete samples compressive strength value increased by 7.43Mpa from 14th to 28th days of curing. Whereas for the CCS concrete samples it increased by 7.6Mpa. This also shows that the concrete samples cured by self-curing admixture have shown better curing capacity than the concrete samples cured by water immersion method. As the chart on Figure 6 illustrates, the average compressive strength of CCS increased by 12.47Mpa and the CCWS sample increased by 9.1Mpa from the 7th to 14 days of curing. This shows CCS concrete samples has cured than CCWS. When we consider the increment of compressive strength from 14th to 28th days of curing CCS sample average compressive strength increased by 7.6Mpa. Compressive strength amount CCWS increased by 6.9Mpa. This also indicates the tendency of the compressive strength increment is greater for the self-cured concrete samples than the water sprinkling cured samples. 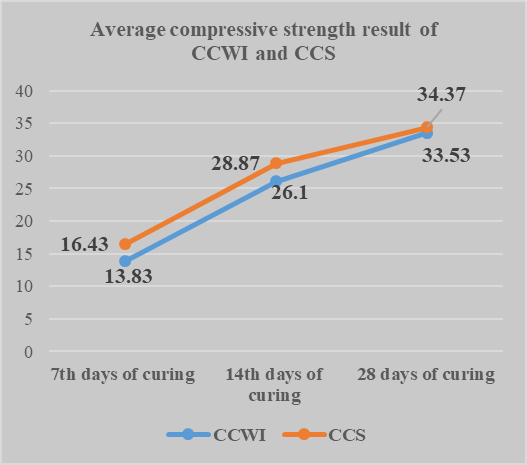 | Figure 5. Average compressive strength results of CCWI and CCS |
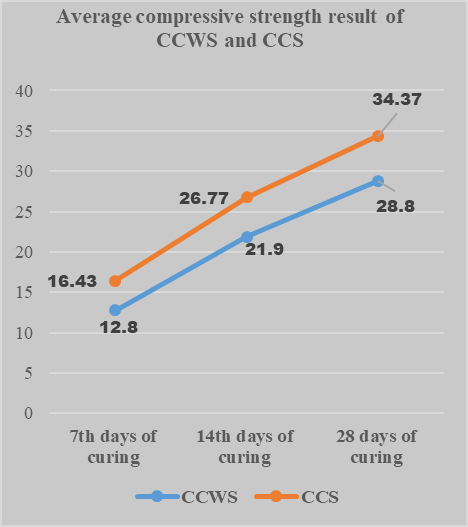 | Figure 6. Average compressive strength results of CCWS and CCS samples at different ages of curing |
4. Conclusions
Ø The compressive strength of self-curing concrete samples cured by polyethylene glycol (PEG 4000) admixture (SCC) was better at all ages of curing than the concrete samples cured by water immersion (CCWI) and water sprinkling(CCWS) methods. Ø The compressive strength of concrete samples cured by water immersion method (CCWI) has attained better compressive strength than the samples cured by sprinkling method applied twice a day (CCWS). Ø The 28th day mean compressive strength results are 33.53Mpa, 28.8Mpa and 34.37Mpa for CCWI, CCWS and CCS concrete samples respectively. Ø According to the ACI mix design procedure the minimum 28th mean compressive strength required for C-25 concrete is 33.33Mpa. Therefore, CCS and CCWI concrete samples of this study has fulfil the minimum compressive strength requirement but the CCWS samples doesn’t attain minimum compressive strength requirement.Ø Based on the change in compressive strength from the 7th to 14th to 28th days of curing CCS samples shows higher increment of compressive strength than both CCWI and CCWS.
References
[1] | ACI Committee 305R-99, (2009). Hot Weather Concreting, Reported by ACI. |
[2] | American Society for Testing and Materials (ASTM C 125), (2000). Standard terminology related to concrete and concrete aggregates. |
[3] | American Society for Testing and Materials (ASTM C 127), (1988). Standard Test Method for Specific Gravity and Absorption of Coarse Aggregate. |
[4] | Babitha Rani H., Shivakumar, Dushyanth Veerendra Babu, Kunal Kothari, Sindhu S., Harish J., (2017). Studies on Self Curing Concrete With the Addition of Polythylene Glycol- 4000, International journal of Innovative Reasearch in Science Engineering and Technology. 4(9). |
[5] | Bentz, D.P., (2002). Influence of Curing Conditions on Water Loss and Hydration in Cement Pastes with and without fly ash substitution, U.S. Dept. Commerce. |
[6] | C. Selvamony, M. S. Ravi Kumar, S. U. Kannan and S. Basil Gnanappa, (2010). Investigations On Self-Compacted Self-Curing Concrete Using Limestone Powder and Clinkers, ARPN Journal of Engineering and Applied Sciences 5(3): pp155-176. |
[7] | Dayalan J. and Buellah M., (2014). Internal curing of concrete using pre wetted light weight aggregates, International Journal of Innovative Research in Science, Engineering and Technology. 3(2): pp1554-1560. |
[8] | Fauzi, M., (1995). The Study on the Physical Properties of Surface Layer Concrete under the Influence of Medium Temperature Environments. Ph.D. Thesis, Kyushu University, Japan. |
[9] | Hans W. Reinhardt and Silvia Weber, (1998). Self-Cured High Performance Concrete, journal of materials in civil engineering. 3(2): pp 564-571. |
[10] | International Conference on Innovations in Engineering and Technology, (2013). Effects of Super Plasticizing and Retarding Admixtures on Properties of Concrete, Bangkok (Thailand). |
[11] | Kosmatka, Steven H.; Kerkhoff, Beatrix; and Panarese, William C., (2003). Design and Control of Concrete Mixtures, EB001, 14th edition, Portland Cement Association, Skokie, Illinois, USA. |
[12] | M. V. Jagannadha Kumar, M. Srikanth, K. Jagannadharao, (2012). Strength Characteristics of Self Curing Cocrete, IJRET. 1(1). |
[13] | Md. Safuddin, S.N. Raman and M.F.M. Zain, (2007). Effect of Different Curing |
[14] | Methods on the Properties of Micro Silica Concrete, Australian Journal of Basic and Applied Sciences, 1(2): pp87-95. |
[15] | Michaels M. and John P. Zaniewski, (2006). Materials for Civil and Construction Engineers. Second Edition. Upper Saddle River, New Jersey Pearson Education, Inc. |
[16] | N. Gowripalan, R Marks and R Sun, (2001). Early age properties of self-cured concrete, Proceedings of Concrete, Institute of Australia, pp 655-662. |
[17] | Neville, A.M., (1998). Properties of Concrete. 4th. Ed., New York, NY: John Wiley & Sons, Inc. |
[18] | Nirav R Kholia, Prof. Binita A Vyas, Prof. T. G. Tank Kholia, (2013). Effect On Concrete by Different Curing Method and Efficiency of Curing Compounds, International Journal of Advanced Engineering Technology. 4(2): pp57-60. |
[19] | Patel Manish and Jayesh kumar, (2014). Introducing the Self-Curing Concrete in Construction Industry, International Journal of Engineering Research & Technologyn (IJERT). 3(3): pp1286-1289. |
[20] | Patel Manish and Prof. Jayesh kumar R. Pitroda, (2013). Self-Curing Concrete: New Technique for Concrete Curing, Journal of International Academic Research for Multidisciplinary, Impact Factor. 1(9): pp393-399. |
[21] | SR. Thiru chelve, S. Sivakumar, M Rajkumar, G. Shanmugaraja, M. Nallathambi Vishnue pryan, (2017). Effect of Polyethylene Glycol as Internal Curing Agent in Concrete, International journal of Innovative Reasearch in Science Engineering and Technology. 6(3). |