Belachew Asteray1, 2, Walter Oyawa3, Stanley Shitote4
1Civil Engineering Department, Pan African University Institute for Basic Science, Technology and Innovation Hosted at Jomo Kenyatta University, Nairobi, Kenya
2Addis Ababa Science and Technology University, Addis Ababa, Ethiopia
3Commission for University Education, Nairobi, Kenya
4Civil and Structural Engineering Department, Moi University, Eldorate, Kenya
Correspondence to: Belachew Asteray, Civil Engineering Department, Pan African University Institute for Basic Science, Technology and Innovation Hosted at Jomo Kenyatta University, Nairobi, Kenya.
Email: |  |
Copyright © 2017 Scientific & Academic Publishing. All Rights Reserved.
This work is licensed under the Creative Commons Attribution International License (CC BY).
http://creativecommons.org/licenses/by/4.0/

Abstract
Currently, innovations on sustainable materials has been encouraged as a result of continual accumulation of different local wastes and their consequent environmental complications due to urbanization, population growth, global energy need and excess biomass raw materials use. The objective of this experimental investigation is to develop Recycled Reactive Powder Concrete (RRPC) by utilization of local wastes for structural applications. The conventional reactive powder concrete is a mixture of water, Portland cement, silica fume, fine sand, quartz powder, superplasticizer and steel fibers produced using stem curing at high temperature. In this study, finely dispersed waste ceramic powder was utilized to replace Quartz powder fully. Moreover, rice husk ash and finely dispersed waste glass powder were used in three different percentages (at 80-20%, 50-50% and 25-75%) as a raw material from waste stream to replace silica fume fully for the development of RRPC. The performances of the developed concrete were appraised in terms of compressive strengths at 7, 14 and 28 days standard curing. The experimental results indicated that development of RRPC using hand mixing at standard curing from local wastes in this study was an interesting approach to solve raw material shortage for the current generation structural concrete and to reduce waste disposal cost and related environmental issues in Africa among others. In this study, RRPC with an average compressive strength of 57.3 MPa were developed at 28 days standard curing by replacing silica fume fully with 80% finely dispersed local waste glass powder and 20% rice husk ash. Compared to the control mix, an eco-friendly concrete with 9.5% larger compressive strength can be produced from these local wastes.
Keywords:
Local Wastes, Recycled Reactive Powder Concrete, Compressive Strength, Sustainable Construction
Cite this paper: Belachew Asteray, Walter Oyawa, Stanley Shitote, Experimental Investigation on Compressive Strength of Recycled Reactive Powder Concrete Containing Glass Powder and Rice Husk Ash, Journal of Civil Engineering Research, Vol. 7 No. 4, 2017, pp. 124-129. doi: 10.5923/j.jce.20170704.03.
1. Introduction
Today, the main emphasis of materials science in sustainable civil engineering world is on enhancing the performance and functionality of conventional materials in environmentally friendly way using recent technologies and local waste materials. As a prime composite construction material in Civil Engineering, the rapid rise in concrete raw materials has led to serious environmental effects such as economical unbalances, resource shortage, biodiversity loss, habitat destruction, and desertification. Moreover, it is also a challenge to produce high performance concrete for structural applications from locally recycled waste materials since less costly components of conventional concrete are eliminated by more expensive elements (such as silica fume) to produce newly emerging concretes called reactive powder concrete. In addition to this, waste disposal from different sources (industrial, agricultural areas, mining, households, etc.) in Africa have continued to be a complex challenge for the society, both environmentally and economically. In view of rising raw material prices in the construction and threats of global climate change, waste management in the future needs efficient technologies. As per the African Development Bank, surveys of waste management are essential for any future investments in equipment and technology to be sustainable [1]. Globally, 90 billion tons of solid wastes are expected to be generated annually by the year 2025 [2]. Likewise, based on the urban community consumption, the composition of wastes generated in East African urban centers is mainly decomposable solid waste materials [3]. However, as a major opportunity, there is a market demand for sustainable eco-friendly materials and design concepts using recycled wastes which require little energy to process; and enabling the reuse of these waste materials in a continuous cycle.In recent times, a new generation concrete called reactive powder concrete is under development as an ultra-dense mixture of water, Portland cement, silica fume, fine quartz sand, quartz powder, superplasticizer and steel fibers [4-6]. However, it is noticed that high silica fume content is one of the characteristics of reactive powder concretes which is uneconomical for local constructions. Chan and Chu (2004) [7] also examines the effect of silica fume on steel fiber bond characteristics in RPC and investigates that the optimal silica fume content is between 20% and 30% in which this quantity within the mix may lead to uneconomical mix. In most African Countries including the East African countries where this study focuses, silica fume for local concrete work is imported from Middle East, Asian and other foreign suppliers which are too expensive and time-taking. Beside its availability problems, usage of silica fume highly affects the concrete production costs. Furthermore, application of reactive powder concrete for local construction activities has limitations due to its energy-consumption during the heat curing process and the milling of quartz sand [8]. Thus, the magnitude and nature of waste generated across the world have prompted the need for innovative way of changing the environment and using its resources in a better way [9]. Presently, reusing and recycling of wastes by proper management for conservation of natural resources in environmentally and economically sustainable ways is becoming one of the principal strategies for waste management [10]. Hence, by utilizing local wastes, one can attain an innovative strategy for multidimensional advantages in the construction industry. Moreover, it helps to address the environmental as well as cost-related problems and to encourage innovations on sustainable waste materials.There is not much information available on the type and volume of waste that is generated in the construction industry [18]. However, the nature of local wastes can be either biodegradable or non-biodegradable materials depending on their source. This may affect the quality of the end product. One of the basic features of a sustainable material is its reusability, recyclability and biodegradability. Reusability is a function of the age and durability of a material. Very durable materials may have many useful years of service left when the building in which they are installed is decommissioned, and may be easily extracted and reinstalled in a new site. Recyclability measures a material’s capacity to be used as a resource in the creation of new products. Many building materials that cannot be reused in their entirety can be broken down into recyclable components. The biodegradability of a material refers to its potential to naturally decompose when discarded. Organic materials can return to the earth rapidly, while others, like steel, take a long time [16].Different scholars were investigated the nature of waste materials and their effect on concrete property. As per A. Halicka et. al. (2013) [15], ceramic waste is one of the industrial wastes under non-biodegradable waste since its biodegradation period is very long (up to 4 thousand years). It substitutes traditional natural aggregate even if poorly affects concrete strength parameters [15]. On the other hand, using waste/recycled plastics will reduce municipal solid wastes being landfilled and is an alternative to pressure-treated lumber that leaches toxic chemicals into water [17].Moreover, rice husk is also one of the abundant agricultural wastes which can serve as a source of silica by burning and forming ash. However, the excessive amount of husks generated during rice processing produces a serious environmental problem due to their slow biodegradation which can reduce the quality of products. But, as per N. S. Suharty et al. (2014), by making composites with recycled polypropylene, we can enhance the tensile strength to an optimum value [19]. In this study, finely dispersed waste glass powder as well as waste ceramic powder from construction sites; and rice husk ash from factories were proposed as a result of continual accumulation of wastes in the East African region to develop recycled reactive powder concrete. The proposed local wastes were utilized as full replacements of silica fume through experimental investigations as ecofriendly material for future Civil Engineering projects.
2. Materials and Methods
2.1. Materials
In this study, Portland cement (CEM I 42.5 N Power PLUS), fine sand (600µm), waste ceramic powder (300µm), finely dispersed waste glass powder (150µm), rice husk ash, steel fibers, superplasticiser and water available around Nairobi area were used for the development of RRPC mix and for the entire tests. To develop the control mix, MasterRoc MS 610 type densified Silica fume was used from BASF East Africa LTD in Nairobi. The rice husk ash was collected from Mwea Irrigation Scheme in Kenya.The cement was from Bamburi Cement Limited in Nairobi fulfilling the criteria for the European Norm Standard EN 197-1 (Table 4). Fine sands obtained from Meru, Kenya and passing 600µm standard sieve size were used in all the mixtures and used in dry condition. The grading of fine sand, used for the entire mixtures, is shown in Table 3. Additionally, locally available waved wire steel fibres of 50 mm length with 0.22 mm thickness from Steel Wall Africa Nairobi branch were used for development of RRPC. Commercially available superplasticiser supplied by SIKA® Company Kenya Limited in Nairobi under the commercial name Sika Viscocrete-10 were used to attain workability. The ordinary drinking water was also used for preparation of the desired concrete mix. Experimental results are presented comparatively with the control mix. To develop the control mix, MasterRoc MS 610 type densified Silica fume (Table 2) was used from BASF East Africa LTD in Nairobi.Waste ceramics and waste glass were collected from construction sites and crushed with a sledge hammer using manpower. Then, the crushed products were taken to the crushing machine in Jomo Kenyatta University Engineering Workshop to make them very fine and to produce pozzolanic powder. After getting finely grained powder products, the products were sieved using 150µm standard sieve to get finely dispersed glass powder and 300µm standard sieve to get ceramic powder. Table 1 describes the chemical composition of ingredients in this study. The overall chemical composition of a pozzolan is considered as one of the parameters governing long-term performance (e.g. compressive strength) of the blended cement binder, ASTM C618 prescribes that a pozzolan should contain SiO2 + Al2O3 + Fe2O3 ≥ 70 wt.%. In this study, the results of the chemical analysis for local waste materials proposed in this study were compared with the minimum requirement for a standard pozzolana quality as per ASTM C618.Table 1. Chemical Composition of materials in this study 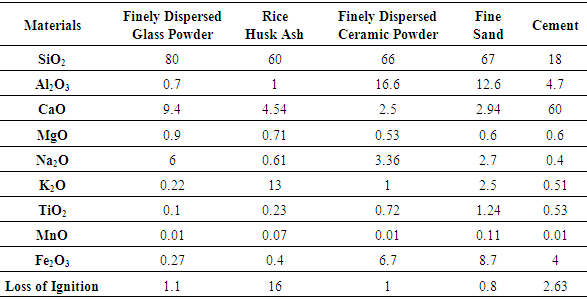 |
| |
|
Table 2. Technical Data for Densified Silica fume 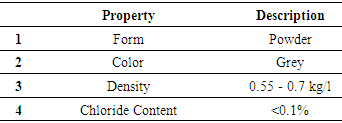 |
| |
|
Table 3. Fine Sand Grading 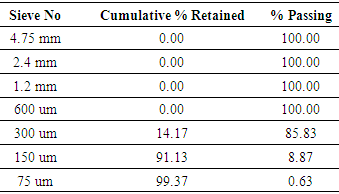 |
| |
|
Table 4. Properties of Cement 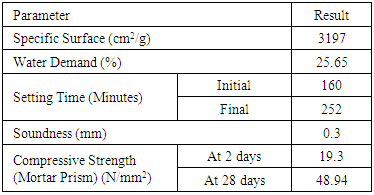 |
| |
|
2.2. Mix Design of RRPC Mixtures
In this study, RRPC was developed through preliminary tests based on the existing mix proportions by replacing the silica fume and quartz powder in full version by local waste materials [11]. Finely dispersed waste glasses and rice husk ash were proposed to replace silica fume fully. Additionally, quartz powder was replaced by finely dispersed local waste ceramic powder. Since the mix design was employed using this three local waste materials together with other core raw materials, the name “Recycled Reactive Powder Concrete” was given for the concrete mixture. The mix proportion for this study was summarized in Table 5. For all mixes, hand mixing, standard water curing and uniform water-binder ratio of 0.216 were used.Table 5. Mix Proportions for 0.009 [M3] 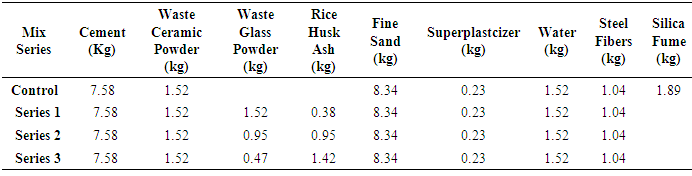 |
| |
|
2.3. Mixing Procedure, Specimen Preparation and Curing Procedure
For this study, watertight and non-absorbent 100X100X100 mm3 cube moulds conforming BS EN 12390-1:2000 [12] were prepared. Then, specimens were prepared based on BS EN 12390-2:2000 [13], the methods for making and curing test specimens for strength tests. Hand mixing was employed throughout the entire specimen preparations. After removal of specimens from the mould, standard curing of the test specimens was done until testing days in water at a temperature of 20°C ± 2°C instead of steam curing at high temperature in conventional RPC. The standard curing temperature was proposed to save energy consumption used by the conventional method and to solve sustainability issues.In order to prepare specimens, dry mixing of ingredients was done for 3 minutes. After that, wet mixing was done by adding 80% of the water and all of superplasticicer into the mixed dry materials and was mixed for another 7 minutes. Then, the remaining water was added and mixing was done again until a visually acceptable mix was obtained. Hand mixing was employed throughout the entire specimen preparations. After getting a uniform mix and placing layer by layer on moulds, compaction was employed in two layers by steel compacting rod of circular cross-section having 16 mm diameter and length 600 mm with rounded ends. Once leveling of the surface was made with steel floats, the specimens were leave in the moulds for one day till getting dry. After removal of specimens from the mould, the specimens were marked without damaging the specimen. Then, standard curing of the test specimens were done till testing days for 7, 14 and 28 days in water at a temperature of 20°C ± 2°C instead of steam curing at high temperature in conventional RPC.
2.4. Testing of Specimens
After 7, 14 and 28 days standard curing in water, the compressive strength of the cube specimens (100x100mm) was determined following BS EN 12390-3:2002 [14] by automatically controlled universal testing machine at constant rate of loading (rate of 0.500 KN/Sec and start load of 0.250 KN with 15% stopping load) in Jomo Kenyatta University of Agriculture and Technology (JKUAT). The mean of three specimens produced from four categories (including control mix) were taken to evaluate the compressive strength of RRPC.
3. Results and Discussions
3.1. Pozzolanic Property of Proposed Waste Materials
Fig. 1 shows the chemical compositions (silica, alumina and iron oxide content) of selected local wastes in this study after X-ray fluorescence (XRF) analysis in Kenya Ministry of Mining. As evaluation criteria, the sum of the three mineral components (silica, alumina and iron oxide content) in each local waste should be compared with the requirement of ASTM C618 as a pozzolana.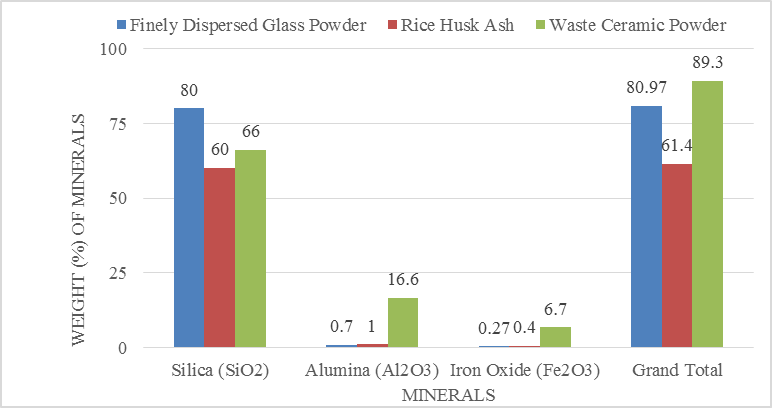 | Figure 1. Pozzolanic property of Waste materials in the study |
Accordingly, finely dispersed glass powder contains 80.97%; rice husk ash contains 61.4% and waste ceramic powder contains 89.3% by weight. Except rice husk ash, the chemical compositions are greater than 70 (by weight %). Hence, the local waste materials used in this study specifically finely dispersed glass powder and waste ceramic powder were revealed a wonderful pozzolanic property that can greatly affect the long-term performance of the concrete product.
3.2. The Effect of Glass Powder and Rice Husk Ash on Compressive Strength of RRPC
One of the major parameters to identify the long term mechanical performance of the produced recycled reactive powder concrete is compressive strength. In this study, the compressive strength was evaluated by replacing different percentages of the proposed waste materials. The mean compressive strengths of three specimens produced from four categories (including control mix) were as presented in Fig. 2.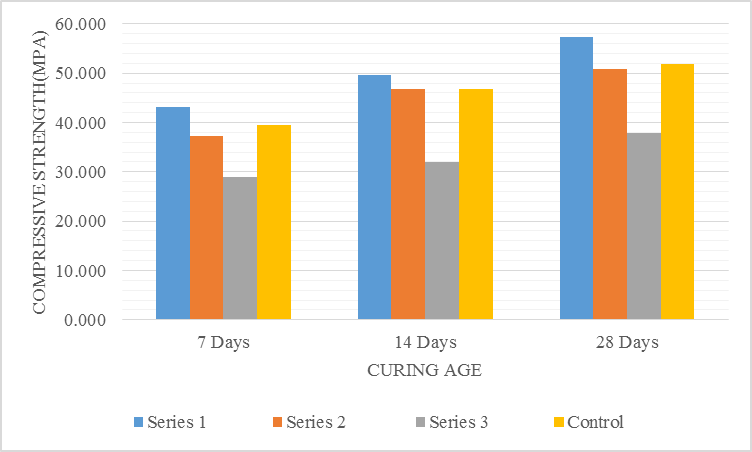 | Figure 2. Mean Compressive Strength at standard curing Ages |
Fig. 2 shows the average compressive strength of different series of RRPC mix developed by replacing the silica fume fully with glass powder and rice husk ash. In all curing ages, mix series 1 gives the maximum average compressive strength using 20% rice husk ash and 80% finely dispersed glass powder. At 7 days standard curing, in mix series 1, the compressive strength raises by 13.7%, 32.9% and 8.4% compared to series 2, series 3 and the control mix respectively. Likewise, there is also an increment of compressive strength by 5.7%, 35.6% and 6% at 14 days standard curing. Additionally, at 28 days, series 1 also produced a maximum compressive strength of 57.3 MPa. Compared to other mix series, the strength gained in mix series 1 was very high due to the pozzolanic reaction of low rice husk ash and high glass powder content with the other ingredients in the mix. This shows that low rice husk ash and high glass powder in the mix were produced a concrete with high compressive strength at all standard curing ages. Fig. 3 shows the comparison of mean compressive strength of different mix Series with the control mix at 28 days standard curing. Compared to the control mix, higher compressive strengths were attributed in the first and second mix series. In this regard, 9.5% rise of compressive strength was observed in the first mix series compared to the control mix.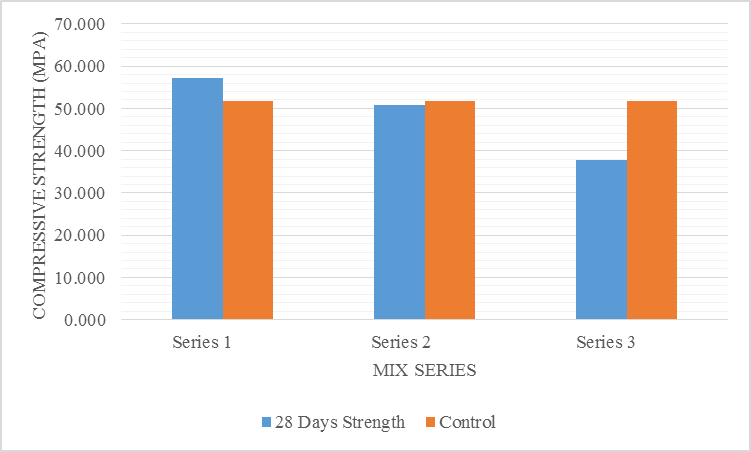 | Figure 3. Comparison of Mean Compressive Strength of Mix Series with the control Mix at 28 days standard curing |
The compressive strength variation at each series of RRPC mix is due to the percentages of rice husk ash and glass powder in each mix series. However, this compressive strength was very low compared to the conventional Reactive Powder concrete that was produced by Silica fume, quartz powder, very fine steel fibres using machine mixing and stem curing at high temperature. As shown in the previous study [11], by introducing 10%, 20% and 30% of glass powder to replace quartz powder, a reactive powder concrete with 97.4 MPa, 136.1 MPa and 83.9 MPa compressive strength were produced respectively after 14 days of stem curing. Hence, compared to the three percentages, maximum strength was obtained using 20% glass powder content.The result obtained by the above scholar is also true for this study with respect to the ratio of glass powder. There will be higher compressive strength with respect to using higher amount of finely dispersed glass powder.
4. Conclusions
Based on the experimental results, the following conclusions can be drawn.i. As a waste material and reuse for current generation concrete production, finely dispersed glass powder and waste ceramic powder revealed a wonderful pozzolanic property that can greatly affect the long-term performance of RRPC product;ii. In the proposed mix proportion series for getting higher compressive strength, the optimal values for waste glass powder is 80% and for rice husk ash is 20%.iii. A maximum mean compressive strength of 49.695MPa at 14th days curing age can be produced using 20% rice husk ash and 80% finely dispersed glass powder combinations. iv. Higher mean compressive strength can be observed by using high finely dispersed waste glass powder and low rice husk ash within the desired mix. In general, from this study, one can realize that a culture of using local waste raw materials in the African construction sector will be an interesting approach to solve raw material shortage, to fulfil the market demand of eco-friendly concrete products, to reduce waste disposal cost and related environmental issues in Africa.
ACKNOWLEDGEMENTS
The authors are grateful to African Union Commission for the support under the flagship program of Pan African University Institute for Basic Science, Technology and Innovation (PAUSTI) in this study.
References
[1] | Palczynski RJ., Study on Solid Waste Management Options for Africa by African Development Bank. 2002. p. 131. |
[2] | Ajnavi S., Bioconversion of Cellulosic Agricultural Wastes. Masters Technol Diss Dep Biotechnol Environ Sci Thapar Univ. 2008; (60601011). |
[3] | Okot-okumu J., Solid Waste Management in African Cities – East Africa. 2012. p 3-20. |
[4] | Cheyrezy M, Maret V, Frouin L., Microstructural Analysis of RPC (Reactive Powder Concrete), Cem Concr Res. 1995; 25(7): 1491–500. |
[5] | Bayard O, Plé O. Fracture mechanics of reactive powder concrete: Material modelling and experimental investigations. Eng Fract Mech. 2003; 70(7–8): 839–51. |
[6] | Ahmad S, Zubair A, Maslehuddin M., Effect of key mixture Parameters on Flow and Mechanical Properties of Reactive Powder Concrete. Constr Build Mater. 2015; 99: 73–81. |
[7] | Chan YW, Chu Sh., Effect of silica fume on steel fiber bond characteristics in reactive powder concrete. Cem Concr Res. 2004; 34(7):1167–72. |
[8] | Gu CP, Ye G, Sun W., Ultrahigh performance concrete-properties, applications and perspectives. Sci China Technol Sci. 2015; 58(4): 587–99. |
[9] | Adebayo OS, Kabbashi N a., Alam MZ, Mirghani MS., Recycling of organic wastes using locally isolated lignocellulolytic strains and sustainable technology. J Mater Cycles Waste Manag. 2014; 17(4):769–80. |
[10] | Safiuddin M, Jumaat MZ, Salam M a, Islam MS, Hashim R., Utilization of solid wastes in construction materials. Int J Phys Sci. 2010; 5(13):1952–63. |
[11] | Kushartomo W, Bali I, Sulaiman B., Mechanical behavior of reactive powder concrete with glass powder substitute. Procedia Eng. 2015; 125: 617–22. |
[12] | BS EN 12390-1 (2000). British Standard for Testing hardened concrete — Part 1: Shape, dimensions and other requirements for specimens and moulds. BSI, London. |
[13] | BS EN 12390-2 (2000). British Standard for Testing hardened concrete — Part 2: Making and curing specimens for strength tests. BSI, London. |
[14] | BS EN 12390-3 (2002). British Standard for Testing hardened concrete — Part 3: Compressive strength of test specimens. BSI, London. |
[15] | A. Halicka, P. Ogrodnik, and B. Zegardlo, “Using ceramic sanitary ware waste as concrete aggregate,” Constr. Build. Mater., vol. 48, no. May, pp. 295–305, 2013. |
[16] | J. Kim and B. Rigdon, “Qualities, Use, and Examples of Sustainable Building Materials,” in Sustainable Architecture Module, no. December 1998, 1998. |
[17] | R. Siddique, J. Khatib, and I. Kaur, “Use of recycled plastic in concrete: A review,” Waste Manag., vol. 28, no. 10, pp. 1835–1852, 2008. |
[18] | M. Yeheyis, K. Hewage, M. S. Alam, C. Eskicioglu, and R. Sadiq, “An overview of construction and demolition waste management in Canada: A lifecycle analysis approach to sustainability,” Clean Technol. Environ. Policy, vol. 15, no. 1, pp. 81–91, 2013. |
[19] | N. S. Suharty, M. Mathialagan, H. Ismai, B. Wirjosentono, M. Firdaus, and G. K. Wardani, “Tensile properties and biodegradability of rice husk powder-filled recycled polypropylene composites: Effect of crude palm oil and trimethylolpropane triacrylate,” J. Phys. Sci., vol. 25, no. 2, pp. 55–71, 2014. |