Hoang Quoc Vu, Thuy Ninh Nguyen
Building Materials Lab., Faculty of Civil Engineering, Ho Chi Minh City University of Technology, Viet Nam
Correspondence to: Hoang Quoc Vu, Building Materials Lab., Faculty of Civil Engineering, Ho Chi Minh City University of Technology, Viet Nam.
Email: |  |
Copyright © 2017 Scientific & Academic Publishing. All Rights Reserved.
This work is licensed under the Creative Commons Attribution International License (CC BY).
http://creativecommons.org/licenses/by/4.0/

Abstract
Autoclaved aerated concrete (AAC) is a high-rise market in Vietnam and it has a very significant potential to thrive in the future. The application of advanced technologies and methods such as use of new and recycled materials, improve technical properties... is essential in developing of this type of construction materials. Similar to the method used to fabricate concrete using dune sand, this study was performed to evaluate the applicability of using dune sand in another construction material, such as AAC brick. Then, in order to increase the applicability of AAC in civil construction, the property of water absorption of AAC is studied as a very important aspect of this research. Final results may point to some possible measures to improve this feature and give preliminary data for more intensive studies on the properties of AAC and its application.
Keywords:
AAC, non-AAC, Dune sand, Fine aggregate, Admixture
Cite this paper: Hoang Quoc Vu, Thuy Ninh Nguyen, The Influence of Admixtures on Properties of AAC Using Dune Sand as the Fine Aggregate, Journal of Civil Engineering Research, Vol. 7 No. 1, 2017, pp. 1-8. doi: 10.5923/j.jce.20170701.01.
1. Introduction
Similar to the method which is used to fabricate concrete using dune sand, this study was performed to evaluate the applicability of using dune sand in another construction material, such as AAC brick. The research on the applicability of the dune sand in the construction products have been conducted in several countries also had some researches on this field in Vietnam.A. S. Al-Harthy and M. Abdel Halim [1] carried out a research on the properties of concrete using dune sand as a replacement of normal sand. Then V. Q. Hoang et al. [2] also have replaced normal sand by dune sand in the concrete fabrication in Vietnam and the result also showed similarities. Also, Salim Guettala and Bouzidi Mezghiche [3] had a study of the influence of the dune sand to the properties of the mortar. In Vietnam, V. Q. Hoang’s group is also conducting a study on the application of dune sand in manufacturing dried- mortar.The latest study in 2012 led by Alhozaimy [4] also focuses on effects of white dune sand and normal dune sand in properties of concrete in both standard and autoclave curing. Besides, the study by Yothin Ungkoon and Chadchart Sittipunt [5] about micro structure of AAC and study led by Norifumi Isu [6] in Japan about properties of AAC with variable seize of quartz particles can be considered as important references to carry out this study.Using of dune sand in the construction also contribute significantly to reduce the exploitation of normal sand and prevent desertification in the central coastal region. The problems that this study wishes to solve include:1. Can dune sand replace crushed sand in the production of AAC or not?2. Which component in the traditional materials of AAC can cause adverse reactions when interacting with dune sand?3. The influence of the dune sand to the properties of AAC brick.4. How much dune sand can be used (if possible to) to balance between economic factors and technical characteristics of AAC bricks.Besides, the AAC brick also has downside made it has not been widely applied in the construction. The major problem of AAC brick related to its interaction with water, including the high water absorption, and the decrease in its compressive resistance when the water met. The intensity of absorbing water of the AAC brick caused the inconveniences such as:1. The difficulty in preservation, especially considered outdoor.2. Using in the positions frequently exposed to water such as toilet, kitchen area, aquarium, the exterior surfaces.3. Significantly increase in its weight when watered.So, besides studies of improving aggregate proportion such as adding dune sand, finding solutions to reduce the water absorption of bricks is very necessary. In fact, the contractor has used a number of methods to AAC brick for waterproofing, mainly covering a layer of waterproofing on the surface of the bricks. This insulating layer can be removed over time or does not guarantee absolutely snugly sealed, the water can still seep into cracks.To avoid the disadvantages of surface coating measures, currently waterproofing additives are often used in combination with the components to create products with the waterproofing capability by itself. This idea has been done in this study and pointed to some results of waterproofing of AAC brick use additives, which have a high heat resistance and are not affected by the process of autoclaving.The methodology of this research is to design a sample proportion; then, dune sand is used to replace normal sand content in the proportion by the weight to take the samples with levels of dune sand ascending to 100%. With the control samples and the samples added the dune sand; researchers will perform experiments to define the basic properties of the samples from which to give conclusions and recommendations.
2. Materials and Testing Methods
2.1. Standard Aggregates Proportion
Basic materials of manufacturing AAC bricks include crushed sand, cement and water which are parts of making concrete. Besides, aerated concrete requires components to create bore holes; specifically here is a mix of lime and aluminium powder. Finally, a quantity of gypsum is added to the mixture for the purpose of increasing the viscosity of silicate concrete and avoiding stratification of the mixture and gas from escaping. Thus, manufacturing materials include crushed sand, cement, lime, aluminium powder, gypsum and water. Physical and chemical properties as well as the technical characteristics of these components are determined according to current standards. In detail:The properties of the cement are listed in Table 1 with the application of standards as in Vietnamese Standard (abbreviated as TCVN hereafter) named TCVN 4030: 2003, TCVN 6017: 1995, TCVN 6016: 2011.Table 1. The properties of the cement 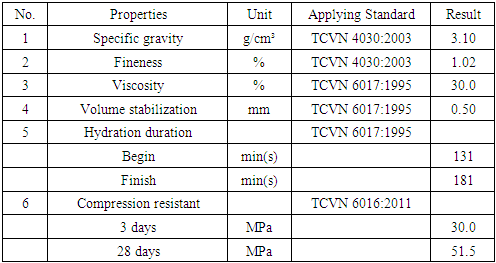 |
| |
|
Crushed sand used in this study was provided by a company (in Viet Nam) with specs provided in Table 2.Table 2. The specs of the crushed sand from the plant  |
| |
|
The main object of this study is the dune sand. Dune sand in this research comes from sand hills of Phan Thiet, Binh Thuan Province.In Table 3 are the results of statistical analysis of the chemical composition of the dune sand used in this study, compared to crushed sand at the plant.Table 3. The chemical composition of crushed sand and dune sand 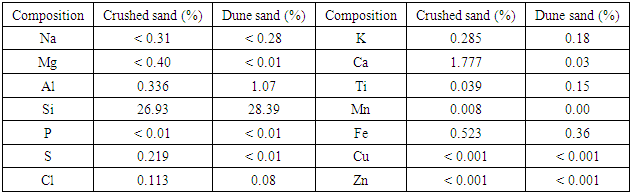 |
| |
|
In the chemical composition, the higher proportion of SiO2 is the better quality of the sand. In addition, the total amount of aluminium oxide (Al2O3) and iron oxide (Fe2O3) must less than 5% and 3%, respectively.The physical and chemical properties of the dune sand is also determined according to TCVN 7572: 2006, including specific gravity, grading size, bulk gravity and moisture, as shown in Table 4.Table 4. The properties of dune sand 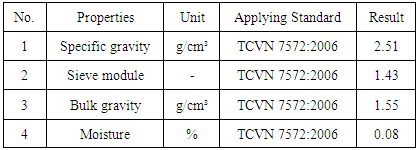 |
| |
|
Table 5. Statistical table of sieve test result for dune sand 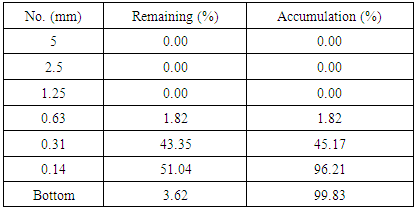 |
| |
|
The experimental results and chart of grading size curve also show that the dune sand is composed mainly of fine grained particles, for detail, the accumulation is only 1.82% on 0.63 mm screening, there is no larger particle grades.A preliminary assessment is this kind of sand may be suitable for manufacturing of aerated concrete. However, if the fineness of the sand particles is not enough to satisfied fabrication requirements, it can combine conventional measures such as crushing or simply screening to remove coarse particles for saving crushing cost.Possibility of alkali - aggregate reaction is also an issue to be considered in the use of sand derived from the sea or containing salt. This reaction occurs in high alkaline and pH environment, the products swell out and cause volume destabilization and destroy concrete structures.From the data in Table 3 alkali content found in the dune sand (mostly original Na+ and Ca2+) is lower than in the crushed sand at the factory and both of them are suitable for making AAC. The quality of lime was evaluated by the total MgO and CaO content. This value was determined by titration with liquid of 0.1 N HCl. It also needs to determine the temperature and duration of the reaction between lime and water. These values were recorded Table 6.Table 6. Properties of lime 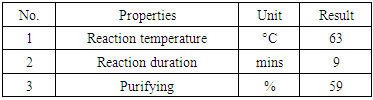 |
| |
|
Aluminium used is aluminium powder paste with appropriate technical requirements. This study surveyed the groups of sample of autoclaved aerated concrete also non-autoclaved aerated concrete. The purposes of the experiment on two kind of aerated concrete sample are based on two things:1. The first thing is to assess the effectiveness of the autoclaved process on aerated concrete and the influence of the dune sand to the product in this process.2. The second one is to evaluate the interaction between the dune sand and other components in aerated concrete when producing the conventional aerated concrete product without performing the autoclaved process.It can also compare the change in properties of AAC and non-autoclaved aerated concrete (hereafter referred to as the non-AAC) with the same content of dune sand in composition. And then it can give some recommendations of the use of dune sand generally in producing aerated concrete products rather than just focus on AAC.
2.2. The Mechanism of Waterproofing Additive
The structure of concrete and cement slurry are mostly calcium hydroxide crystal, a small part of calcium silicate hydrogen gel (C-S-H) and pore holes. There are many types of voids in the structure of AAC brick: Pores between the crystalline gels, capillary between the aggregates or cement.Those microscope holes primarily affect the properties of concrete such as reducing waterproofing and resistance. Waterproofing depend on the ratio of polymer-per-cement, type of addictive and coating condition. While the surface covered approaches deal with large scale holes, mixing Polymer admixtures with the aggregates solve problems relating to permeability at the micro scale. | Figure 1. Connections between the Polymer and Ca2+, and between Polymer layers [10] |
In general, the Polymer added to the mixture will disperse and bind up the particles, then it constantly form membranes tightly connect aggregates together. In the process of hydration, the voids are filled by the Polymer strings. When the water gradually evaporate, those Polymer layers also gradually form along with other materials to produce a Polymer-Carboxylate bond in which Oxygen link with Ca2+ to create connection between Polymer and the aggregates. The model is depicted in the picture above.Additives are used to improve waterproofing properties of the AAC brick in this study is the Polymer additives grouped into Styrene-Butadiene. This additive works as the agglomeration mechanism described. The optimal amount of Polymer used to improve the properties of the mixture is usually from 5 to 20 percent of the weight of cement to ensure the economical usage. The low proportion of Polymer led to insufficient amount of adhesive on the surface of particles lead to low-performance of additive.Also in excess of additive, then the existence of Polymer will limit the hydration process and leads to the lack of strong crystals which set the quality of the concrete down. Below is the chemical structure of Styrene-Butadiene Polymer which is used in this study.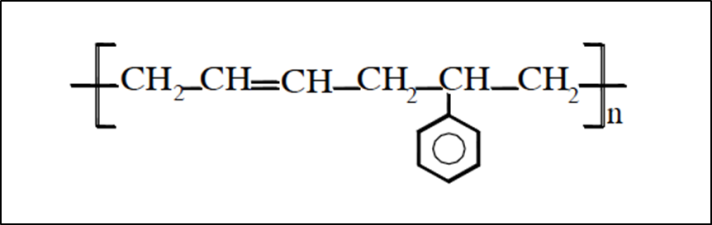 | Figure 2. Chemical scheme of Polymer additives |
The AAC and non-AAC in this study were made in the same conditions, with the same dune sand proportion, the difference is that the AAC will be put in Autoclave at 180 ~ 190°C with the pressure of 8 ~ 12 bar during 12 hours or longer while the non-AAC after removing the specimens will be stored in neutral curing conditions.Besides, the waterproofing additives will be added only to autoclaved samples, so that the water absorption will be considered between AAC samples with and without Polymer admixture. The basic result of this study is about properties of non-AAC and AAC brick using dune sand. Then, the results in water absorption were presented as additional information about properties of AAC when adding Polymer.The criteria of the AAC and non-AAC are defined in accordance with TCVN 7959:2011 related to the dried gravity; the compression strength is also defined as in TCVN 3118:1993, the water absorption was also determined as in TCVN 248:1986.It can identify the dry shrinkage of non-AAC based on TCVN 9029:2011 and TCVN 9030:2011. The characteristics which will be defined are in the statistics Table 7 below.Table 7. Criteria of the AAC and non-AAC should be determined 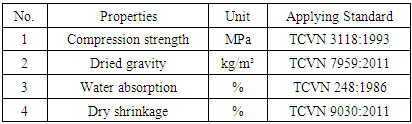 |
| |
|
The samples are cast in the Construction Materials Laboratory, at the Ho Chi Minh City University of Technology. Then the non-AAC samples were curing here while the AAC samples are sent to the factory of Vuong Hai JSC., Dong Nai province to conduct autoclaved process in Autoclave.
3. Results and Discussion
The proportion of AAC and non-AAC mixtures in this research is preliminarily calculated from the tables and charts in guidebook then adjusted by using experimental method.Two groups of control sample including samples use 100% crushed sand (which mean none dune sand in content) and will be put in the Autoclave and others also use no dune sand but take the standard curing process are denoted AAC-0 and non-AAC, respectively.The specific gravity of the AAC often range from 400 to 1200 kg/m³. In this study, the controlling proportion was designed for the products with the gravity about 700 kg/m³. This grade of specific gravity is quite popular for the AAC brick and other products used in many civil building.With each type of mix, AAC or non-AAC, a set of 6 samples is fabricated with dune sand replace for 10%, 20%, 30%, 50%, 80% and 100% of crushed sand by mass in proportion. So, for a set of samples, there are totally 7 samples including a control sample and 6 mixtures which have been added dune sand in its content.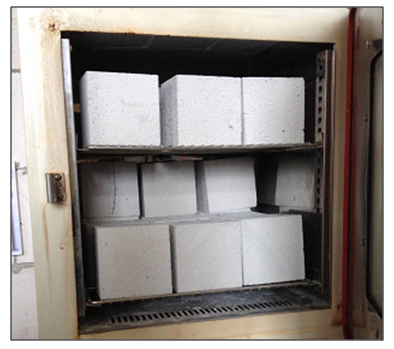 | Figure 3. AAC brick samples after autoclaving process in Autoclave |
In Table 8 below is the standard contents for 1 m³ of aerated concrete both controlling and samples with dune sand. With each group of AAC samples, an additional proportion of additives were added to provide new comparing samples.Table 8. Content of samples (kg/m³) for 1 m³ of concrete 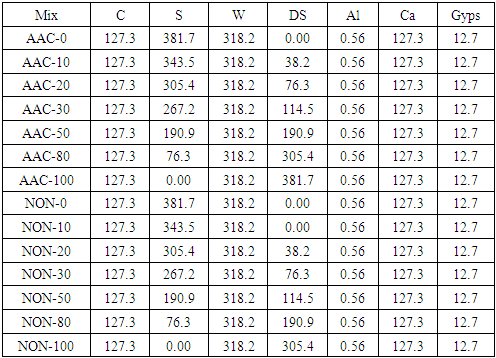 |
| |
|
The percentage were respectively 0%, 1%, 2%, 3%, 5%, 8%, and 10% for samples named ADD-0, ADD-10, ADD-20, ADD-30, ADD-50, ADD-80, ADD-100. In the name of the sample, ADD stand for ACC with additive, and the number stand for its percentage of dune sand, the proportion of admixture is always considered as one tenth of dune sand percentage.About the notation, as explained above, the prefix AAC stand for the AAC samples, NON represent the non-AAC, and ADD stand for AAC samples with additive; the following number represents the percentage of dune sand in the mixing content, the proportion of additive is always by one tenth of dune sand percent.For example, AAC-30 is AAC samples with 30% of the dune sand or NON-10 is non-AAC samples with 10% crushed sand was replaced by dune sand, and the ADD-80 may represent AAC samples with 80% of dune sand and 8% of additive.In the table above, the symbol C means of Cement, Sand and Water is S and W, DS is the Dune Sand, Al is Aluminium, Ca is Lime and Gyps means Gypsum. The unit used in the table is kg for aggregates and litter for the water. Note that all the samples were in the form of cube has the edge by 10 cm.The autoclaved process has been carried out with the saturated vapour pressure varied from 9 to 16 atm and the temperature ranged from 170 to 190 Celsius degree constantly in 12 hours. Particularly, this process occurred as 3 stages: The first stage is the process of raising the pressure and the temperature. In the second stage, the temperature and the pressure in the Autoclave remained their peak values. Lastly, the temperature and the pressure come down to zero in the final stage.Within this research, the samples have been cured in the Autoclave of the Vuong Hai JSC. The detail information about the temperature and the pressure of the autoclaved process has been recorded in the chart below.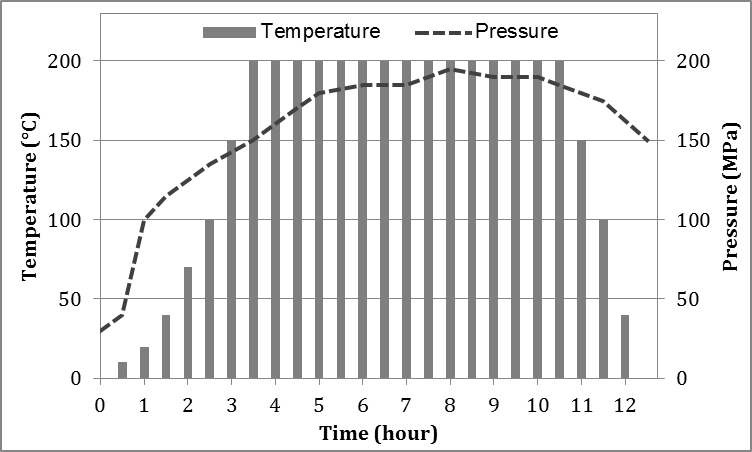 | Figure 4. The condition of the temperature (°C) and the pressure (MPa) during the autoclaved process |
3.1. The Influence of Dune Sand and Admixture to Compressive Strength
The results of compressive resistance of AAC, non-AAC, and AAC with additive mixes are presented in the form of the graph in Figure 5. With the AAC, when dune sand content exceeds 30%, its strength down dramatically, reach 23.95% with ACC-50 and peak to 41.23% with AAC-100.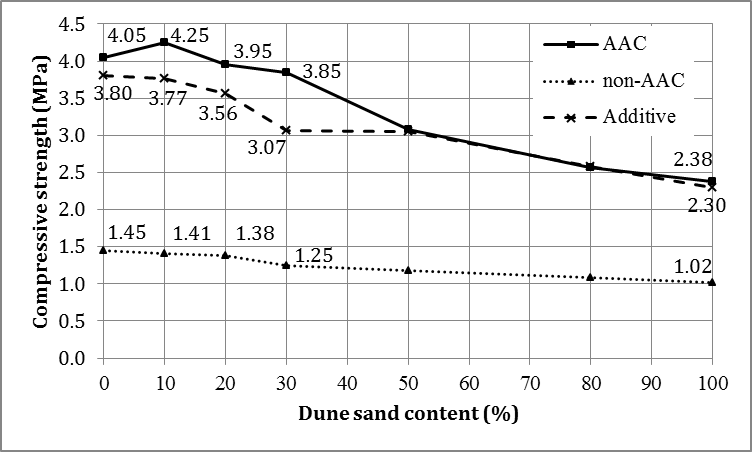 | Figure 5. Compression strength (MPa) of the AAC, non-AAC and AAC with additive samples |
In contrast, the decrease of strength in NON-30 approximately 15% but when the content of dune sand up, the non-AAC has less decrease, it down gradually and meet the greatest value at 29.66% with samples of NON-100.The AAC mixes use mixtures have the similar compressive strength with the AAC mixes without it, and its variation is gradual. It could consider that the Polymer additive hardly not affect the compressive strength of samples, it is just under the effect of the dune sand proportion.It can conclude that adding dune sand at the rate of 30% or less is hardly reduces the intensity of AAC, with the non-AAC then the intensity decrease about 15% but still remain in allowance.After that, the reduction of AAC sample’s strength is greater as we continue to add more dune sand into while non-AAC then decreases steadily in intensity. It can predict the cause of this change is due to the separation between the crushed sand and dune sand layer. In the lower content of dune sand, that separation is not yet significantly, but when increasing the dune sand, it turn into more remarkable.In addition, the dune sand with more coarse particle than crushed sand which had been processed also contribute to the reduction of quality of the materials drag by the decrease in the strength of samples.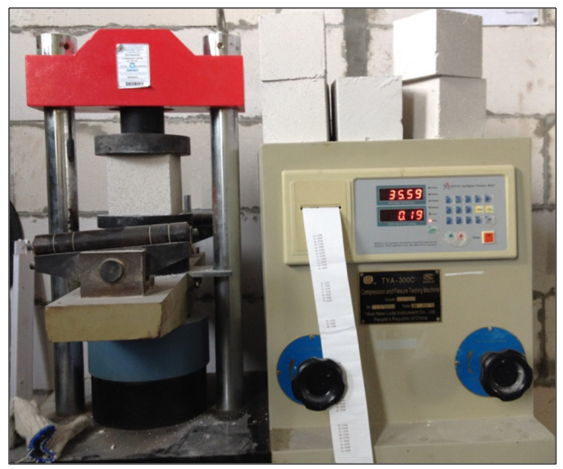 | Figure 6. Compressive strength test |
3.2. The Influence of Dune Sand and Admixture to the Dried Gravity
The variation of the dried gravity of types of mixes is recorded as in Figure 7. In general, the dried gravity of aerated concrete gradually in-creases when adding dune sand into the mix aggregates.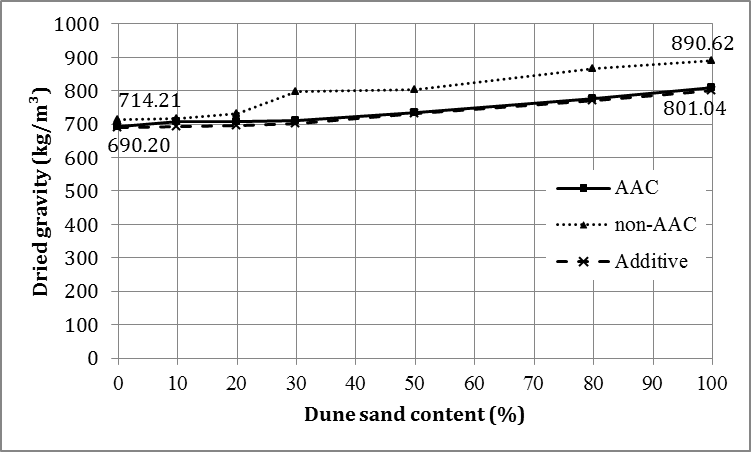 | Figure 7. Chart of dried gravity (kg/m³) of samples |
The biggest growth for the AAC group was recorded in AAC-100 with the value increase 16.97%, while NON-100 sample has the dried gravity rose 24.70%.Among the alternative mixes with dune sand under 30%, the dried gravity rose insignificantly, only 2.66% with AAC-30 and 11.76% with samples of NON-30. The difference between AAC samples use Polymer additive and others is very small to evaluate that there is any variation.The Polymer in mixes may cause its gravity drop very slightly because of its lightweight but it is unnoticeable.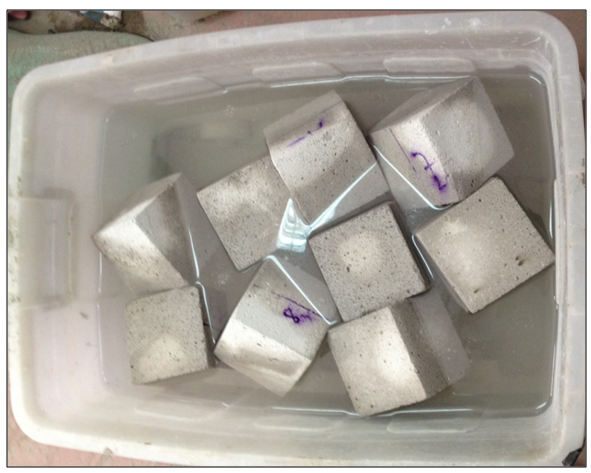 | Figure 8. Water absorption test carried out according to TCVN 248:1986 |
Comparison of experiment’s results of three kinds of mixes can show that: The non-AAC has the increasing in dried gravity more than other AAC samples.Base on the high water absorption of dune sand, it can be explained this water evaporated after autoclaved process while it still exist in non-AAC. Gravity increasing of types of samples is mainly due to dune sand’s particle gravity is greater than the crushed sand’s at the factory.The dried gravity of the aerated concrete is much lighter than conventional products. Adding dune sand on the mixture has increased the gravity of samples but this increase is small and acceptable.So, the dune sand does not affect the advantage of the light weight of the aerated concrete brick and it still ensures the dominant of the products.However, the aerated concrete has high water absorption, adding the dune sand on may cause these properties to be more detrimental, resulting in wet gravity increases. This property should be carefully studied and evaluated.
3.3. The Influence of Dune Sand and Admixture to the Water Absorption
The results of water absorption (after 60 minutes in water) of two kinds of AAC and other non-AAC are presented in Table 9 and Figure 9. In the table, W stand for Water Absorption (in %) and V stand for Variation (in %).Table 9. Water absorption (%) and its variation (%) of groups of sample 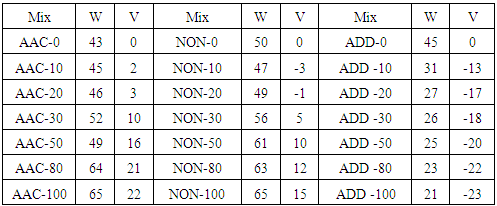 |
| |
|
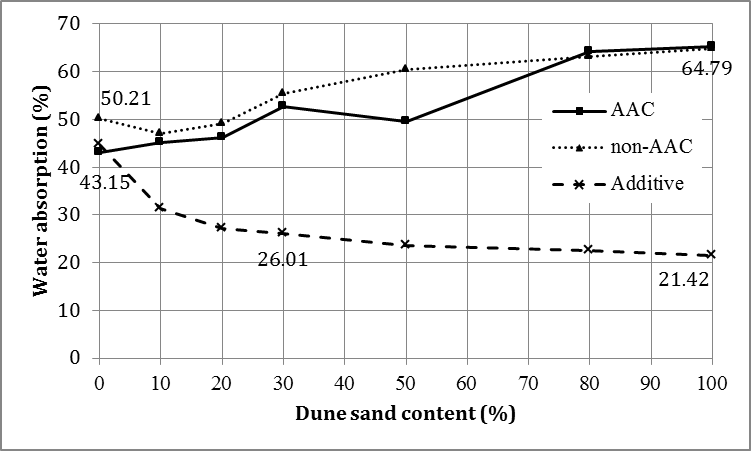 | Figure 9. Water absorption curves (in %) of three kinds of sample |
From results of the experiment, it can clearly see that the water absorption of AAC samples is lower than non-AAC. This is the result of the autoclaved process of AAC samples. In both groups of sample, when replacing the dune sand in concentration less than 30%, the water absorption has no major upheaval, namely the difference between AAC-0 and AAC-30 is 10% while NON-30 is 5% more than NON-0.When continuously replacing the crushed sand by dune sand, then the water absorption continues to increase. The maximum result of two types of mixes is nearly at the same level of 65% with samples only use dune sand. While the water absorption of the sample NON-0 is higher than AAC-0, when replacing the dune sand, the non-AAC increases the water absorption slower than AAC, and the maximum value of two types is mostly equal.When adding dune sand to the mixture, it will generally cause adverse effects. One of the effects is that the separation and increasing the possibility of generating micro cracking in the product. This influence has led to the increase in water absorption of when adding more dune sand. The AAC through the autoclave process has a lower water absorption compare to non-AAC but when using only dune sand, it is almost equal.Another result may be very crucial is that when adding Polymer admixture to the mixture, the water absorption continuously drop down from 45% at 0% of additive to about 26% at 3% of additive and 30% of dune sand. The water absorption reached its lowest point at 21% when adding 10% of Polymer to the mixture.When adding more admixtures, the water absorption keeps decreasing, but with the proportion of additive over 5%, the decrease is not significant as before. Compare with AAC samples with the percentage of dune sand raise from 0% to 100%, the water absorption increases dramatically, but it can reduce a lot when using additives, no matter how much dune sand were added.Water absorption of aerated concrete in general is said higher than the conventional products. Adding dune sand on makes the water absorption increases and causes more harmful to the product.From the study, it can conclude that the amount of dune sand added at fewer than 30% will restrict the water absorption’s variation and ensure the economic aspect. In the future, it is potential to study to combine solutions to reduce the water absorption of the aerated concrete such as the use of additives.In addition, the amount of admixture used in the proportion should be considered under 5% because the higher amount could not turn into remarkable improvement in AAC properties.
4. Conclusions
1. The AAC has superior characteristics than non-AAC. This is a result of the autoclaved process; it helps the products have higher intensities such as the smaller gravity and lower water absorption. These advantages of the AAC remain even when replacing the crushed sand with the dune sand.2. For the AAC without the additive, the compressive strength does not change significantly when the replacement of the normal sand by the dune sand is fewer than 30%. On the contrary, a drastic reduction in the strength was observed when replacing the crushed sand with the dune sand in higher than 30% proportions.3. The water absorption of the AAC can be reduced significantly by the Polymer admixture, the effect of additives keeps expanding when increasing its proportion. In general, the amount of additives should vary between 5 and 20 percent of the amount of cement. Particularly, this work pointed out that the optimal content of admixtures is properly from 3 to 5 percent to ensure the optimal usage also the economic aspect.4. It could consider that the AAC products with Polymer admixture can meet the expectation of standards for the AAC using in civil building. The AAC brick using admixtures can be used in areas which have high requirements of waterproof and expose to water for a period such as exterior wall, water closet areas, etc.
5. Recommendations
1. It is needed more extensive surveys on the properties of the dune sand in sand hills in central coastal region to evaluate whether dune sand is suitable for using in the production of aerated concrete as well as other products or not. In some cases, the dune sand have not yet reached the required fineness, which means some particles are bigger than the limit, it can implement measures such as crushing or simply screening to remove the coarse part.2. Within the scope of this study, dune sand taken from Phan Thiet, Binh Thuan province is entirely satisfied to use in the manufacturing of aerated concrete. Generally, the findings presented in this study validated the properties of AAC products used the particular kind of dune sand as shown. However, it has a high potential that the results are probably similar for the AAC products which use other kinds of dune sand as a part of fine aggregate.3. The use of dune sand in AAC fabrication not only settles unused dune sand but also reduces using normal sand and effects on the environment, especially on the watersheds. It could take advantages of the local materials in place and also reduce the cost for the crushing process.4. Experimental works showed that Polymer admixture can stay in the AAC brick after the autoclave process. However, it still needs further researches about the heat resistance property of this admixture to ensure that Polymer additive works truly stable over the autoclave process.
ACKNOWLEDGEMENTS
This research is funded by Ho Chi Minh City University of Technology, a member of Vietnam National Unversity of Ho Chi Minh City, under the grant number T-KTXD-2016-79.
References
[1] | A. S. Al-Harthy, M. Abdel Halim, R. Tara and K. S. Al-Jabri, “The properties of concrete made with fine dune sand,” Construction and Building Materials, vol. 21(8), pp. 1803-1808, 2007. |
[2] | N. N. Thuy, V. Q. Hoang and N. V. H. Giang, “The study using dune sand as the fine aggregate of concrete,” Review of Ministry of Construction, vol. 10/2015, 14.10, 2015, in Vietnamese. |
[3] | Salim Guettala and Bouzidi Mezghiche, “Compressive strength and hydration with age of cement pastes containing dune sand powder,” Construction and Building Materials, vol. 25(3), pp. 1263-1269, 2011. |
[4] | Alhozaimy and M. S. Jaafar, “Properties of high strength concrete using white and dune sands under normal and autoclaved curing,” Construction and Building Materials, vol. 27(1), pp. 218-222, 2012. |
[5] | Yothin Ungkoon and Chadchart Sittipunt, “Analysis of Microstructure and Properties of Autoclaved Aerated Concrete Wall Construction Materials,” Journal of Ind. Eng. Chem., vol. 13, pp. 1103-1108, 2007. |
[6] | Norifumi Isu, “Influence of Quartz particle size on the chemical and mechanical properties of autoclaved aerated concrete (AAC) (I) Tobermorite formation” and “(II) Fracture toughness strength and micropore,” Cement and Concrete Research, vol. 25, pp. 243-254, 1995. |
[7] | N. Narayanan and K. Ramamurthy, “Structure and properties of aerated concrete: a review,” Cement and Concrete Composites, Vol. 22, pp. 321-329, Oct 2000. |
[8] | Ioannis Ioannou, Andrea Hamilton and Christopher Hall, “Capillary absorption of water and n-decane by autoclaved aerated concrete,” Cement and Concrete Research, Vol. 38, pp. 766-771, Jun 2008. |
[9] | Roger Rixom and Noel Mailvaganam, Chemical Admixture for concrete – 3rd ed., 1999. |
[10] | V. S. Ramachandran, Concrete Ads. Handbook, 2nd ed., 1995. |