Ryno van Leeuwen 1, Yoo-Jae Kim 1, 2, Vedaraman Sriraman 1, 2
1Department of Engineering Technology, Texas State University, San Marcos, USA
2Materials Science, Engineering and Commercialization Program, Texas State University, San Marcos, USA
Correspondence to: Yoo-Jae Kim , Department of Engineering Technology, Texas State University, San Marcos, USA.
Email: |  |
Copyright © 2016 Scientific & Academic Publishing. All Rights Reserved.
This work is licensed under the Creative Commons Attribution International License (CC BY).
http://creativecommons.org/licenses/by/4.0/

Abstract
The major environmental impact of concrete comes from CO₂ emissions during cement production. The main goal of this research was to develop an optimized cement replacement in order to reduce energy consumption and CO₂ emissions. This was tested by incorporating limestone powder in concrete to meet construction specifications. This study utilized limestone powders with different particle sizes that replaced a part of Portland cement in different replacement levels to produce concrete. Due to the dilution effect associated with partially replacing cement, there is a reduction in the physical properties of concrete. Conducting a life cycle assessment permitted optimization of the concrete in a way that minimized environmental impact with a minimal reduction in concrete strength. Test results showed that concretes with higher limestone powder content minimized the percentage in strength lost and reduces the shrinkage.
Keywords:
Limestone powder, Fineness, Life cycle assessment, Particle size, Calcium carbonate, Cement replacement
Cite this paper: Ryno van Leeuwen , Yoo-Jae Kim , Vedaraman Sriraman , The Effects of Limestone Powder Particle Size on the Mechanical Properties and the Life Cycle Assessment of Concrete, Journal of Civil Engineering Research, Vol. 6 No. 4, 2016, pp. 104-113. doi: 10.5923/j.jce.20160604.03.
1. Introduction
Concrete is one of the most widely used construction materials and its production impacts the environment in a number of ways. The acquisition and quarrying of large quantities of raw materials and aggregates depletes natural resources in the effort to meet the demand for concrete. Most of the energy and resources are consumed in the cement manufacturing process when a large rotary kiln is fueled by pulverized coal at 1450 degrees Celsius (Neville, 2011). Due primarily to calcination of the limestone, approximately 1.6 metric tons of raw materials are required to make 1 metric ton of cement; which is released as CO₂ (Nisbet, Marceau, & VanGeem, 2002). The manufacturing of cement is not very efficient, and roughly 40% of raw materials are lost in the production process. As the focus on sustainable construction is increasing in North America, replacing a portion of the ordinary Portland cement (OPC) with pozzolanic, or environmentally friendly filler materials, can be used to reduce the effects on the environment. By optimizing the mixture design in concrete, positive effects of one life cycle assessment of concrete can be achieved (Proske, Hainer, Rezvani, & Graubner, 2014). Only in recent years have U.S. standards incorporated the use of inter-ground calcium carbonate (CaCO3), or limestone, in ASTM standards and specifications for Portland cement. The performance of these limestone blended cements with ASTM C150 cements has recently been documented in a study (Hossack, Thomas, Barcelo, Blair, & Delagrave, 2014). Even with ASTM standards allowing the use of Portland limestone cements, the manufacture of these cements is limited and not widely available in the United States. The introduction of limestone to concrete can be done like other pozzolanic materials by incorporating the limestone directly with the mixing design. This is an alternative to inter-grounding the limestone with the cement, and the limestone can then be mixed with the concrete while batching. By replacing part of the cement with limestone, it will provide an additional surface for precipitation of hydration, while also decreasing the amount of water needed to keep the concrete workable (Bonavetti, Donza, Menendez, Cabrera, & Irassar, 2003). Replacing cement with limestone when batching concrete means the limestone and cement are manufactured separately and that their physical properties are different. The particle size, surface area, or distribution of the limestone may differ and, therefore, needs to be controlled. By implementing limestone powder as a replacement for cement, the environmental effect can be reduced. The environmental effects of replacing cement with limestone powder will differ based on the particle size used because finer limestone powder requires additional milling. Using limestone powder with a particle distribution of about 8 µm, generates approximately 54 pounds of CO₂ per ton produced, whereas a finer particle size of about 4.5 µm generates about 200 pounds of CO₂ per ton. (HuberCrete, 2015). That is only 3.4% to 12.5% of the CO₂ emissions compared to manufacturing a ton of cement, making it very sustainable.To investigate how these characteristics affect the performance of the physical properties on concrete and its environmental impacts, different particle sizes of limestone powder are utilized. The level of replacement of cement are also a driving factor that affects the physical properties and the life cycle assessment of the resulting concrete.
1.1. Research Significance
The objective of this study was to experimentally analyze the effect that CaCO3, or limestone powder, has on the fresh and hardened properties, based on the level of replacement of cement and the particle size used in the concrete mix designs. The purpose of this study was to develop information, specifically concerning CaCO3, and the effects it has on the mechanical properties. This will enable the concrete industry to utilize CaCO3 as a cement replacement to offset some of the environmental effects that are associated with cement manufacturing. Separate grinding of the limestone and clinker provides greater opportunity to optimize the particle size distribution, and to ascertain what levels of CaCO3 and particle size used are advantageous for the physical properties and environmental effects.
2. Experimental Procedures
2.1. Materials
In this study, Type I OPC (meeting ASTM C150 specifications) was used and replaced partially with limestone powders that differered in particle size (ASTM C150, 2015). The percentages of limestone replacement were 10%, 20%, and 30% by weight of the cement. The particle sizes were of 4.5 µm, 8 µm, and 15 µm limestone powder and a specific gravity of 2.7. The particle distribution is indicated in Figure 1, and shows the range of particles that are present for each nominal size. The range of the particle sizes are greater in the larger nominal sizes. The concrete mixture consisted of natural river gravel with a specific gravity of 2.57, and river sand with a fineness modulus of 2.68 and a specific gravity of 2.61. The cement to water ratio of 0.40 was maintained in all batches and was calculated from the total amount of cement and limestone used.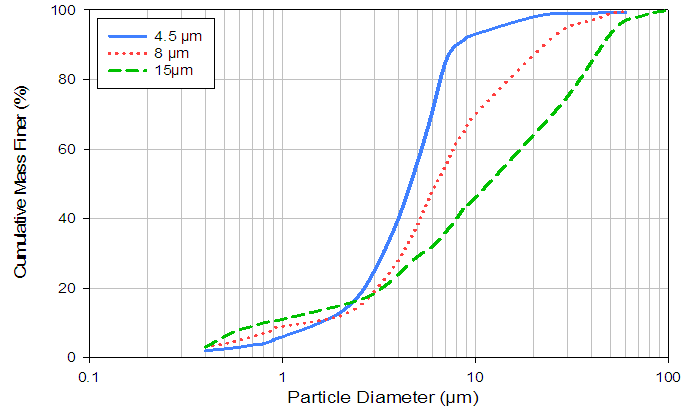 | Figure 1. Limestone powder with a Particle Distribution by Size |
2.2. Mixture Proportions
In each series, 15 specimens of 3” x 6” cylinders were produced. Three different cement intervals and different particle sizes of limestone were introduced (4.5 µm, 8 µm, and 15 µm). The mixture design is shown in Table 1. The concrete was mixed in accordance to ASTM C192, and the limestone powder was added to the drum mixer before adding the cement (ASTM C192, 2015). Once the concrete had been mixed, the fresh concrete was tested for workability, density, temperature, and air content. The concrete mixtures were then cast into 3” x 6” cylinders that were rodded to create uniform specimens for testing. After 1 day of casting, the specimens were de-molded and cured in 100% humidity at 22°C until testing.Table 1. Mix design of concrete with different limestone finesse 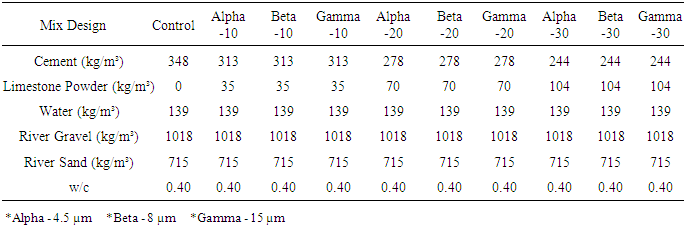 |
| |
|
2.3. Test Specimens
The compressive strength tests were performed at 1 day, 7 days, 14 days, 28 days and 90 days, and the flexural strength test was done at 28 days after batching, in accordance with ASTM C39 (ASTM C39, 2015). Three diameter and length measurements were taken on different positions on the cylinder, then averaged. Using a Test Mark CM-4000 for testing equipment, the cylinders were compressed until failure at a load rate of 0.25 ± 0.05 MPa/s. The maximum load at failure was recorded for each specimen, and the compressive strength was calculated using the average diameter.
3. Test Results
3.1. Fresh Concrete Properties
3.1.1. Temperature
The properties of fresh concrete with limestone powder are considered to be important because of the relation they have with the hydration of the concrete. Table 2 shows the test results for temperature, which ranged from 24.8°C to 25.7°C. The temperature slightly decreased with higher levels of limestone powder present in the concrete, with no significant differences between particle sizes. The slight change in temperature within the different mix designs indicated that no reaction was taking place between the cement and the limestone powder, and that the slight change was due to the lower amount of cement present.Table 2. Fresh properties of concrete with different limestone finesse 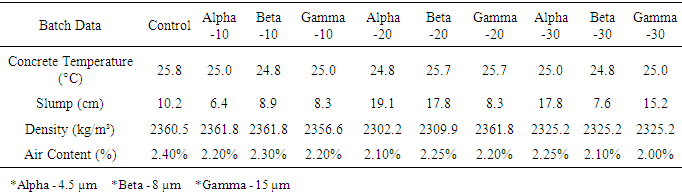 |
| |
|
3.1.2. Workability
The workability of the concrete in the fresh state was measured by conducting a slump test. The results for slump are shown in Table 2. The slump, or workability, slightly increased as a result of limestone powder present in the concrete, most significantly at levels of a 20% replacement. All concrete batches had good workability throughout the process of testing the fresh properties of the concrete and placing it into molds.
3.1.3. Density
Table 2 represents the density of the fresh limestone powder concrete. Fresh density should also be considered when investigating mechanical behaviour, because it affects the material’s elastic modulus and compressive strength. Fresh density in the range 2302.2 kg/m³ to 2361.8 kg/m³ decreased with limestone present in the concrete. The decrease in density depends upon the difference in the specific gravity of cement and limestone powder. Type I OPC has a specific gravity of 3.15, while that of limestone powder is 2.70. Replacing the cement with limestone powder will affect the density, and since the density affects the compressive strength of concrete, it will result in lower strength (Neville, 2011).
3.1.4. Air Content
The air content of fresh concrete containing limestone powder is considered to be important due to the relation it has with durability and porosity. Table 2 shows the test results for air content that has not been modified with any air entraining admixtures, which ranged from 2.3% to 2% with the control mixture at 2.4%. The air content decreased slightly with higher levels of limestone powder present in the concrete. The change in air content within the different mix designs indicated that there was a slight filler effect and efficient particle packing. This indicated that the presence of limestone powder in concrete has positive effects on durability and porosity.
3.2. Hardened Concrete Properties
3.2.1. Compressive Strength
The compressive strength of concrete, commonly considered to be its most important characteristic (especially when limestone powder is used to replace cement because it adversely affects the compressive strength), also gave good overall of the quality of the concrete and the structure of the hydrated cement paste. Table 3 shows the calculated average PSI from 3 specimens at 1 day, 7 days, 14 days, 28 days and 90 days.Table 3. Average Compressive strength of concrete with different limestone finesse 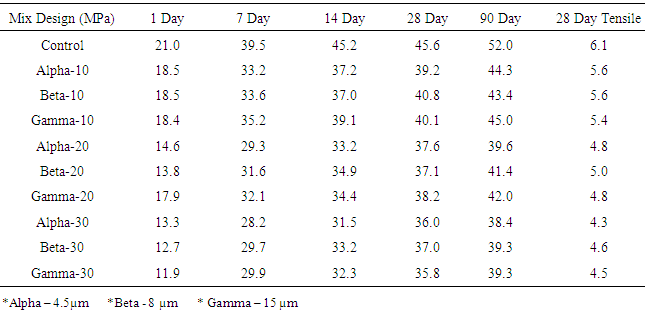 |
| |
|
Figure 2 illustrates the test results of the compressive strength of concrete with a 10% replacement of limestone powder compared to the control that does not contain limestone powder. As expected, the replacement of the limestone adversely affected the compressive strength. A 10% replacement of cement on average reduced compressive strength by 13% at 28 days, and 15% at 90 days, compared to the control. Based on Figure 2, the particle size of the limestone powder did not have a significant effect on the concrete strength ranging from 39.2 to 40.8 MPa at 28 days, and 43.4 to 45.0 MPa at 90 days. 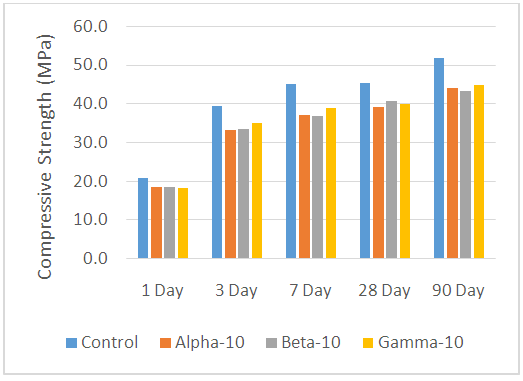 | Figure 2. Effect of Age on Compressive Strength with 10% Limestone |
Figure 3 illustrates the test results with a 20% replacement limestone powder compared to the control. A 20% replacement of cement reduced the compressive strength even more with an average of 19% at 28 days, and 21% at 90 days. The results follow the same pattern as Figure 2, demonstrating that the particle size of the limestone powder had little effect on concrete strength ranging from 37.1 to 38.2 MPa at 28 days, and 39.6 to 42.0 MPa at 90 days.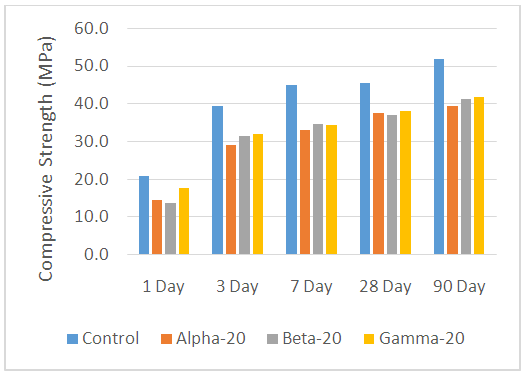 | Figure 3. Effect of Age on Compressive Strength with 20% Limestone |
Figure 4 illustrates the test results of a 30% replacement limestone powder compared to the control. There was an average compressive strength loss of 21% at 28 days, and 25% at 90 days. Particle size of the limestone powder still had little effect on strength, even at a larger volume of limestone powder in the concrete, ranging from 35.8 to 37.0 MPa at 28 days, and 38.4 to 39.3 MPa at 90 days.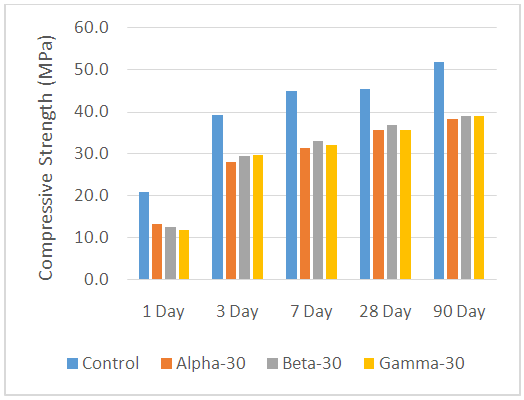 | Figure 4. Effect of Age on Compressive Strength with 30% Limestone |
3.2.2. Flexural Strength
The flexural strength of concrete was tested using the third-point loading test method in accordance with ASTM C78 standard (ASTM C78, 2015). The modulus of rupture for concrete beams was calculated after an aging period of 28 days. Table 3 illustrates the calculated average PSI from three specimens that were tested to failure for flexural strength.Figure 5 illustrates how different levels and particle sizes of limestone powder in concrete affects the flexural strength of concrete. As expected, replacement of the limestone adversely affects the flexural strength. A 10% replacement of cement reduced the flexural strength by 9% to 12%, a 20% replacement reduced the strength by 18% to 21%, and a 25% to 30% reduction was observed with a 30% replacement. As in the case of compressive strength, the particle size of the limestone powder did not have a significant effect on the flexural strength.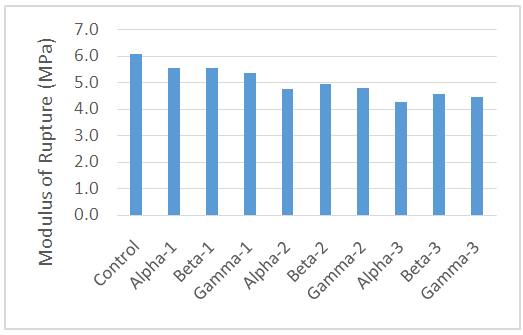 | Figure 5. 28 Day Flexural Strength |
Figure 6 illustrates the relationship between compressive strength and flexural strength. The flexural strength values range from 11% to 13% to that of the compressive strength values. A R² value of 0.86 indicates that a strong correlation was observed between the modulus of rupture and compressive strength of concrete at 28 days.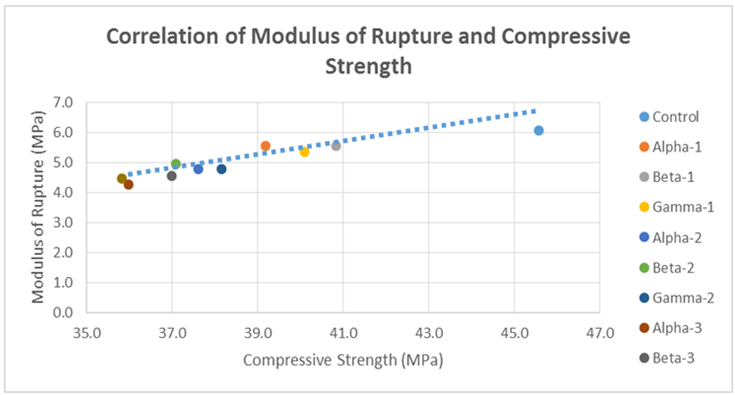 | Figure 6. Correlation of Modulus of Rupture and Compressive Strength |
3.3. Statistically Significance
Data collected on the effect of the particle size of limestone produced with compressive strength at 28 days and 90 days were assessed for statistical significance using analysis of variance (ANOVA). Analysis of variance is used to substantiate whether the measured variation was statistically significant. This inferential statistical method apportions the total variation in the results into that caused by the random variation and that caused by each factor. A conventional level of significance of 0.05 was used for the analysis. This approach can test the hypothesis of whether particle size of limestone affects the concrete strength. Tables 4 and 5 illustrate the analysis of the effect particle size and replacement percentage have on compressive strength.Table 4. Analysis of variance of compressive strength at 28 days 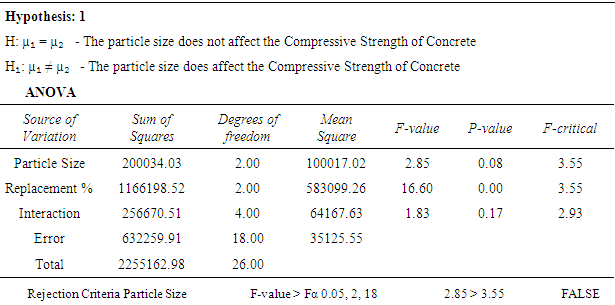 |
| |
|
Table 5. Analysis of variance of compressive strength at 90 days 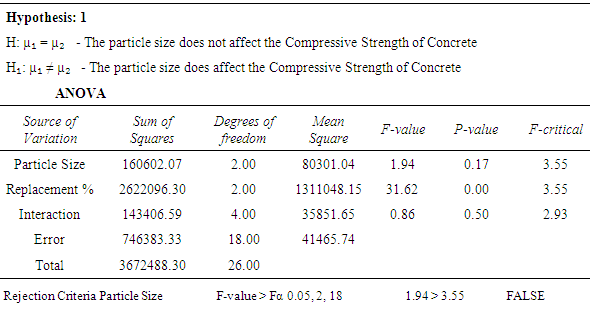 |
| |
|
To test if the effect on compressive strength at 28 days is significant, the null hypothesis, H, is that the particle size does not affect the compressive strength of concrete. The alternative hypothesis, H₁, is that the particle size does affect the compressive strength of concrete. Table 4 represents the F-values, along with p-values for the ANOVA of the concrete strength, at 28 days. Since 2.85 > 3.55, the null hypothesis was not rejected. Thus, the particle size does not significantly affect the compressive strength of concrete at a level of 0.05. Since 16.60 > 3.55, the null hypothesis is rejected. Consequently, the replacement percentage of limestone does significantly affect compressive strength. Test results of the 90 day compressive strength were analyzed with similar hypotheses as before. Table 5 represents the F-values, along with p-values for the ANOVA of the concrete strength at 90 days, and results are the same as the 28 day test. Since 1.94 > 3.55, the null hypothesis is not rejected. Thus, the particle size does not significantly affect the compressive strength of concrete at a level of 0.05. Since 31.62 > 3.55, the null hypothesis is rejected. Consequently, the replacement percentage of limestone does significantly affect compressive strength.
3.4. Shrinkage
Shrinkage is an important mechanical property that effect the structure of concrete and mortar. Shrinkage occurs when the internal humidity in concrete and mortar is lowered, by either the environmental factors or the hydration process. Deformation during the cement hydration process are more significant during early ages. The values in table 6 represent the microstructure of the mortar and its ability to support deformation as the presence of water exchange with the external environment. Calculated average percentage of shrinkage from 3 specimens at 1 day, 7 days, 14 days, and 28 days in accordance with ASTM C596 (ASTM C596, 2015).Table 6. Shrinkage with different limestone finesse 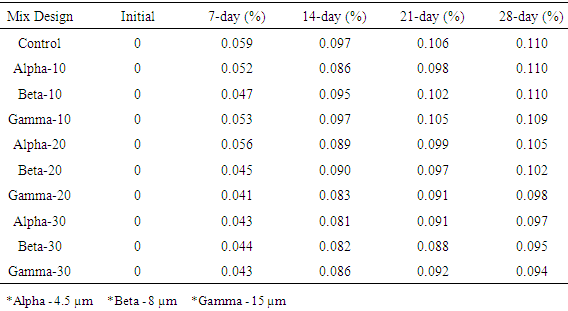 |
| |
|
Figure 7 illustrates the test results of the shrinkage with a 10% replacement of limestone powder compared to the control that does not contain limestone powder. A 10% replacement of cement on average reduced the shrinkage at early ages. At 28 days, there is little to no change in shrinkage compared to the control. Based on Figure 7, the particle size of the limestone powder did not have a significant effect on the shrinkage and is 0.110% that is similar as the control.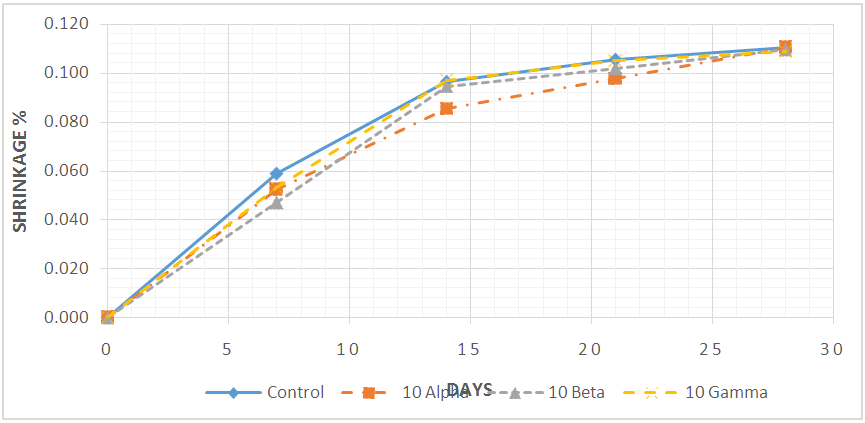 | Figure 7. Effect of Age on Shrinkage with 10% Limestone Powder |
The test results with a 20% replacement limestone powder compared to the control is represented by Figure 8 showing a reduction in the shrinkage in the early stage and at 28 days that is .008% less than the control. The results follow the same pattern as Figure 7 with little variances in shrinkage between the different particle sizes ranging from 0.105% to 0.098% at 28 days.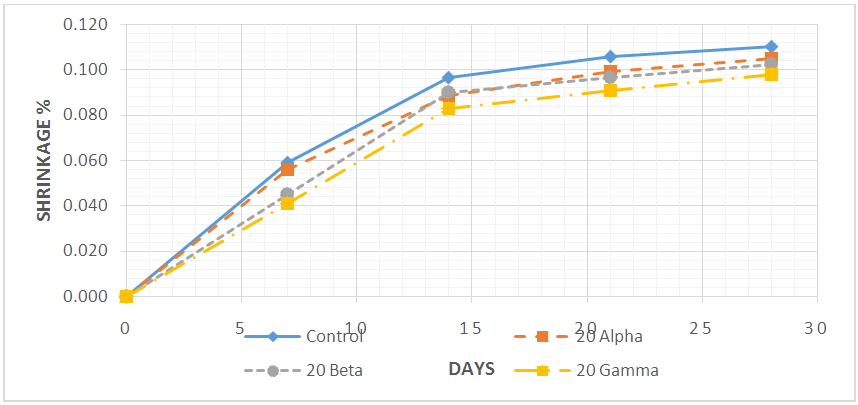 | Figure 8. Effect of Age on Shrinkage with 20% Limestone |
Figure 9 compares the test results of a 30% replacement limestone powder to the control. There was an average reduction in shrinkage by 0.015% at 28 days, and at the early ages of the specimens. Particle size of the limestone powder still had little effect on shrinkage, even at a larger volume of limestone powder used to replace cement. Using less cement in the specimens is the driving factor reducing the shrinkage and agrees with the compressive strength results that the particle size of limestone has little to no effect on the mechanical properties in concrete.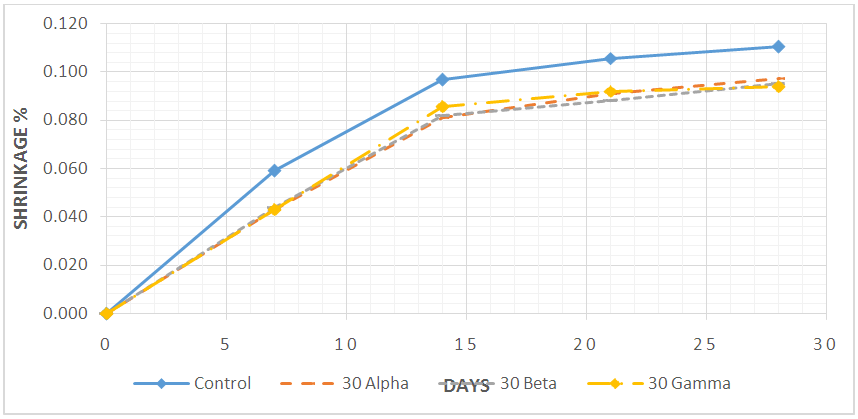 | Figure 9. Effect of Age on Shrinkage with 30% Limestone |
4. Life Cycle Assessment of Limestone Powder in Concrete
Materials from the mix design and emission data from the PCA report were used to conduct a life cycle assessment on the different mix designs (Nisbet, Marceau, & VanGeem, 2002). Data for the production of limestone powder emissions were attained from the manufacturer (HuberCrete, 2015). The environmental impact was assessed based on the carbon dioxide equivalents (CO₂e), found in the U.S. Environmental Protection Agency Tool for the Reduction and Assessment of Chemical and Other Environmental Impacts (TRACI) in order to obtain the emission factors (Bare, Norri, Pennington, & McKone, 2012). There are several benefits of conducting a life cycle assessment, including the ability to evaluate the environmental affect materials and operations have in concrete production, identifying pollution shifts between operations, and providing benchmarks for improvement. This allows for comparison between limestone replacement levels and the different particle sizes and their associated environmental impacts. To accurately conduct a LCA, an inventory of all inputs and outputs are documented with a life cycle inventory.Table 7 illustrates the carbon dioxide equivalents (CO₂e) of environmental impact for each material component, as well as for the transportation and production operations. The table clearly indicates the high degree of environmental impact from cement manufacturing in concrete production. Based on the control mix design, the manufacturing of cement accounts for 91% of the CO₂e emissions, although the concrete contains only 15.7% of cement. The main source of the emission is the operation of the kiln where CO₂ emissions are very high due to the calcination process while driving off CO₂ from CaCO3.Table 7. CO₂e Emission of a yd³ of concrete with transportation and production operations 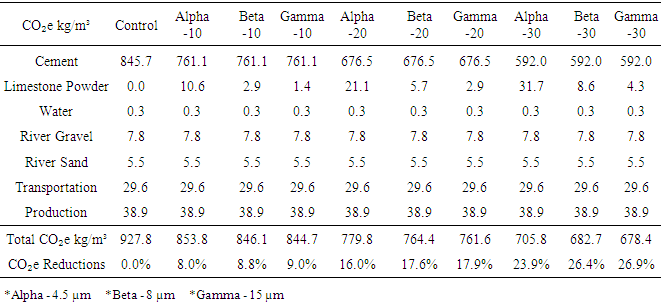 |
| |
|
Figure 10 shows the direct relation CO₂e emission has in the replacement of cement with limestone powder. As the levels of replacement increase and the particle size of the limestone powder increases, the CO₂e emissions of the mix designs decrease. Figure 10 indicates that for every 10% of cement that is replaced with limestone powder, the CO₂e emissions decreased by 8% to 9%, depending on the particle size.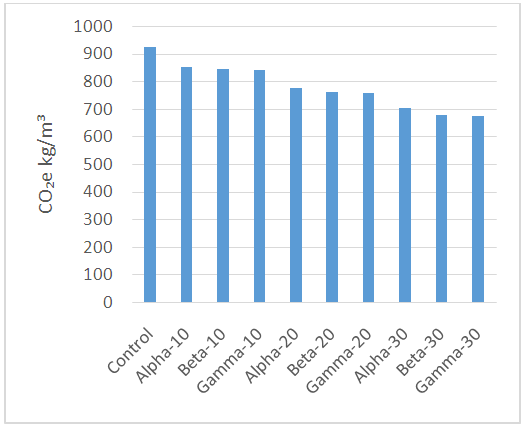 | Figure 10. CO₂e Emission of Concrete Mix Designs |
Higher levels of limestone powder replacement, however, adversely affect the compressive strength of concrete. Figure 11 compares the benefits of the reduction in CO₂e emissions and the adverse effects on the compressive strength. 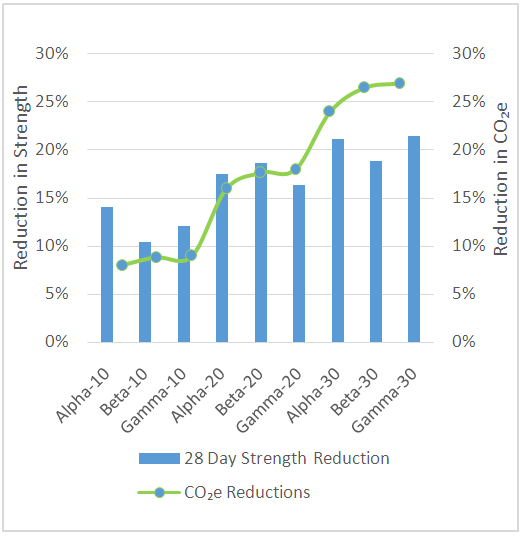 | Figure 11. % CO₂e Reductions Compared to % Strength Reduction. |
Figure 11 also indicates at what level of percentage replacement the benefits of CO₂e emissions are greater than loss of strength. At a 10% replacement of cement, the compressive strength was reduced by an average of 13% at 28 days, and CO₂e emissions by 9.5%. With the loss of strength exceeding the emissions, this percentage of replacement is not very efficient. A 20% replacement of cement has an average of a 17% reduction in compressive strength at 28 days, while CO₂e emissions is reduced by 17.2%. This indicates that at a 20% replacement level of cement, the benefits of the reduction of CO₂e emissions from using limestone powders in concrete starts to surpass the loss in strength. At a 30% replacement, the reduction of CO₂e emissions are greater than the loss of compressive strength, with an average 5.7%, making it the most effective level of cement because the environmental benefits outweigh the reduction of the compressive strength.
5. Conclusions
This study was conducted to evaluate the effects high volume limestone powder with different particle sizes and levels of cement replacement have on the characteristics of concrete when blended during batching. Results from this experiment indicate that introducing limestone powder in high volumes has positive effects on concrete and the environment. Based on the established parameters, concentrations of limestone powders at higher levels are more effective when aspects of environmental effects and properties of strength are considered. However, the use of limestone powder as a cement replacement adversely affects the compressive strength.• The use of limestone as cement replacement in concrete has little effect on the fresh properties. The density and air content of concrete in a fresh state is slightly lower with higher levels of replacement that likely has a more efficient particle distribution. The workability of the concrete does increase with the presence of limestone powder in the concrete, but not significantly.• The level of cement replaced with limestone does effect the compressive strength negatively as levels increase. But at higher levels of limestone powder in concrete, the percentage of strength loss is less significant. • The particle size of limestone used has little or no effect on the compressive strength of concrete at all levels of replacement that were conducted in this study.• The correlation between the modulus of rupture and compressive strength of concrete concludes that that particle size has little effect on flexural strength.• The effectiveness of limestone powder in concrete is higher at higher levels of cement replacement. This is mostly likely due to effective particle packing and efficient particle distribution of the limestone powder in the concrete. • The replacement of cement with limestone powder significantly reduces emissions. This reduction in emissions is directly related to the level of replacement. • The loss of compressive strength at low level replacement is greater than the benefits of emission reductions. But at higher replacement levels, the benefits of emissions reductions outweigh the loss in compressive strength.• The level of cement replaced with limestone does effect the shrinkage positively as levels increase by reducing shrinkage. But the particle size of limestone used has little or no effect on the shrinkage of at all levels of replacement.
References
[1] | ASTM C150. (2015). Standard specification for Portland cement. West Conshohocken, Pennsylvania: ASTM International. |
[2] | ASTM C192. (2015). Standard practice for making and curing concrete test specimens in the laboratory. West Conshohocken, Pennsylvania: ASTM International. |
[3] | ASTM C39. (2015). Standard test method for compressive strength of cylindrical concrete specimens. West Conshohocken, Pennsylvania: ASTM International. |
[4] | ASTM C78. (2015). Standard test method for flexural strength of concrete (using simple beam with third-point loading). West Conshohocken, Pennsylvania: ASTM International. |
[5] | Bonavetti, V., Donza, H., Menendez, G., Cabrera, O., & Irassar, E. (2003). Limestone filler cement in low w/c concrete: A rational use of energy. Cement and Concrete Research, 33(6), 865-871. |
[6] | Hossack, A., Thomas, M. A., Barcelo, L., Blair, B., & Delagrave, A. (2014). Performance of Portland Limestone Cement Concrete Pavements. Concrete International, 36(1), 40-45. |
[7] | HuberCrete. (2015). Let HuberCrete Calcium Carbonate Help You Produce the Brightest White Concrete Building Products Possible. Marble Falls, Texas: Huber Carbonates, LLC. Retrieved from http://www.hubermaterials.com/userfiles/files/PFDocs/Let-HuerCrete-Calcium-Carbonate-Help-You-Produce-the-Brightest-White-Concrete-Building-Products-Possible.pdf. |
[8] | Nisbet, M. A., Marceau, M. L., & VanGeem, M. G. (2002). Environmental Life Cycle Inventory of Portland Cement Concrete. Portland Cement Association, 1-29. |
[9] | Neville, A. (2011). Properties of concrete. Harlow, England; New York: Pearson. |
[10] | J. Padhye, V. Firoiu, and D. Towsley, “A stochastic model of TCP Reno congestion avoidance and control,” Univ. of Massachusetts, Amherst, MA, CMPSCI Tech. Rep. 99-02, 19 |
[11] | Proske, T., Hainer, S., Rezvani, M., & Graubner, C. (2014). Eco-friendly concretes with reduced water and cement content – Mix design principles and application in practice. Construction and Building Materials 67, 413-421. |