Melese Yohannes
Addis Ababa University, Addis Ababa, Ethiopia
Correspondence to: Melese Yohannes, Addis Ababa University, Addis Ababa, Ethiopia.
Email: |  |
Copyright © 2015 Scientific & Academic Publishing. All Rights Reserved.
Abstract
This paper presents the use of Ethiopian pumice and scoria aggregates for lightweight concrete in ribbed slab construction. Experimental and theoretical investigations were conducted to study the strength and deformation characteristics of ribbed-slabs with 60 mm topping. The experimental program was dedicated to the study of mix design for the production of all-lightweight structural concrete and full size ribbed slab testing. Theoretical investigations were conducted parallel to the experimental investigations. Mixtures developed with scoria aggregates have attained required strength and density to be accepted as structural lightweight concrete; however, pumice cannot be used as structural concrete. Experimental investigations showed that ribbed-slabs can be constructed using scoria aggregates with 40 - 47% fine content, 1.6 – 1.8 A/C ratio and 0.4 W/C in range of normal cement content.
Keywords:
Scoria, Pumice, Lightweight Aggregates, Lightweight Concrete, Ribbed-Slab, Mix Design, Density, Strength
Cite this paper: Melese Yohannes, Investigation on the Suitability of Pumice and Scoria Aggregates in Ribbed-Slab Construction, Journal of Civil Engineering Research, Vol. 5 No. 4, 2015, pp. 75-82. doi: 10.5923/j.jce.20150504.01.
1. Introduction
1.1. Background of the Problem
Reinforced concrete as the major building material is playing the biggest role in almost all kinds of construction in Ethiopia. It can be cast to almost any practical shape while it is still fresh. It is also fire and weather resistance after it has hardened.However, the use of crushed aggregate in web and topping construction of ribbed-slab incurred a significant cost increase as it requires: crushing equipments, sufficient quarry sites, blasting chemicals and intensive skilled labour [1].
2. Objective
Researches have been conducted worldwide on a large number of natural and artificial lightweight aggregates to manufacture mortar and concrete. Natural lightweight aggregates include diatomite, pumice, scoria, sawdust, oil palm shells, bottom ash, and starch-based aggregates. Artificial aggregates include expanded shale, slate, perlite, sintered fly ash, bonded fly ash, solidified blast furnace slug, and vermiculite. Use of natural lightweight aggregates instead of processed artificial aggregates can significantly reduce the cost of such concretes [2].Following Italy, Chile, and Ecuador; Ethiopia is the 4th leading producer of pumice and scoria aggregates in the world [2]. Hence, it is essential to investigate ribbed-slab properties with the aim of using these locally available low cost lightweight materials and thereby minimizing the cost of construction. This study was undertaken to investigate the suitability of pumice and scoria aggregates in ribbed-slab construction. The study also presents the results of experimental investigation studying mix design, strength and density characteristics of pumice and scoria concretes. Theoretical and experimental investigations are carried out to determine the strength and deformation characteristics of ribbed slab.
3. Lightweight Concrete Using Pumice / Scoria Aggregates for Ribbed Slab Construction
3.1. Materials
The cement used is Portland Pozzolana Cement (PPC) from Mugar Cement Factory and ordinary tap water was employed for all mixes.Pumice and scoria aggregates obtained from Dire near Debrezeit sources consisted of lumps of various sizes ranging from 1 mm to 40 mm but bigger blocks were also available. Both coarse and fine pumice and scoria aggregates of various grading could be produced from these sources by sieving. In this study, scoria was used as both coarse and fine aggregate in the manufacture of scoria-scoria concrete (ScScC). Pumice was used as only fine aggregate in the manufacture of scoria pumice concrete (ScPC). Figure 1 shows non-graded pumice and scoria aggregates. The maximum size of coarse aggregates was 19.5 mm and that of fine aggregates was 4.75 mm. 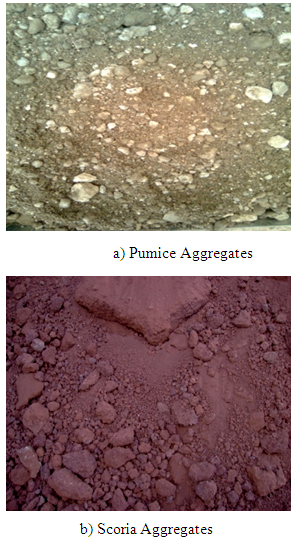 | Figure 1. Pumice and Scoria Aggregates |
3.2. Grading of Aggregates
The aggregates obtained from the quarry are blended to satisfy code requirements. 45% of the sample mass with size of 12.5 mm finer and 9.5 mm coarser scoria aggregates was added during coarse scoria aggregate blending. Similarly, 47% by mass of the sample passing 1.18 mm sieve is added during fine scoria aggregate blending. The particle size distributions of the aggregates are performed according to ASTM C 136 [3] and presented in Table 1.Table 1. Grading of Aggregates 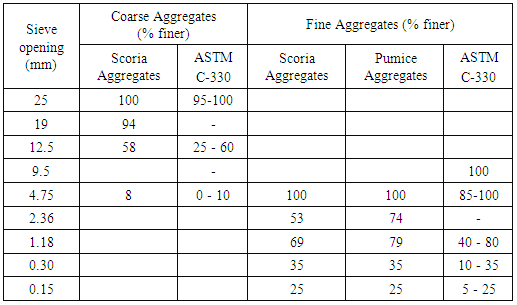 |
| |
|
3.3. Specimen Preparation, Testing and Test Results
Graded coarse and fine aggregates were soaked in water for 24 hours and measurements were taken to determine the free moisture before mixing them with other ingredients. The concrete production was made using a pan mixer of 0.16m3 capacity. The mixes were mixed dry in the mixer for 2 minutes. The specified quantity of water was then added, and the mixture subsequently mixed for another 4 minutes. Concrete from the mixer was fed directly in to the cube moulds and compacted by vibration for slumps less than 75mm and by tamping for slumps greater than 75mm.
3.4. Mix Design
After many trial mixes, suitable ones were selected as shown in Table 2. With each mix type, six 150 mm cube and one 152 mm x 305 mm cylindrical specimens were cast. The cubes were then cured in a water tank at laboratory conditions and tested for strength at 7 and 28 days. The cylinder specimens were kept in oven at 105℃ for 72 hours to determine the oven dried unit weight.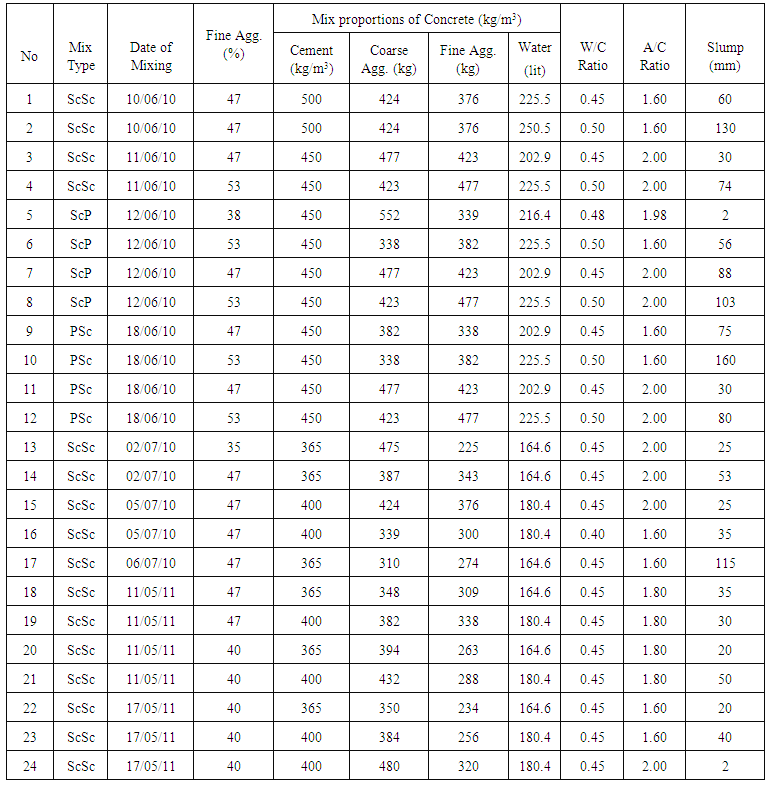 | Table 2. Mix Design for Structural Concrete |
It was observed in the experiment that both pumice and scoria aggregates crush before the cement mortar reaches ultimate value.As expected the fracture path travels through, rather than around, lightweight aggregate particles. 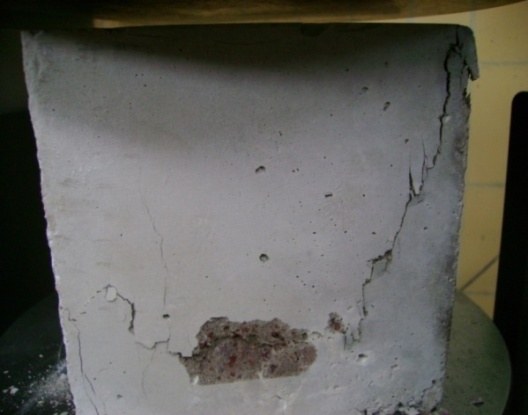 | Figure 1. Cube specimen under load |
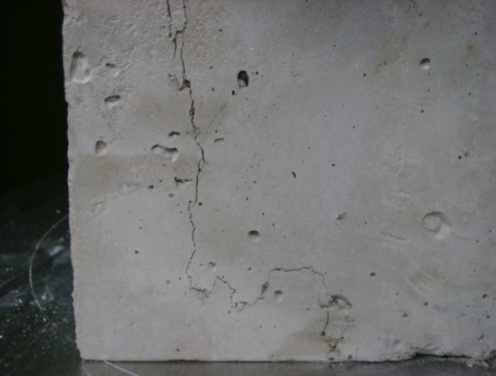 | Figure 2. Fracture Path in concrete specimens |
The mean value of strength test results of scoria and pumice concrete specimens are shown in Tables 3 and 4.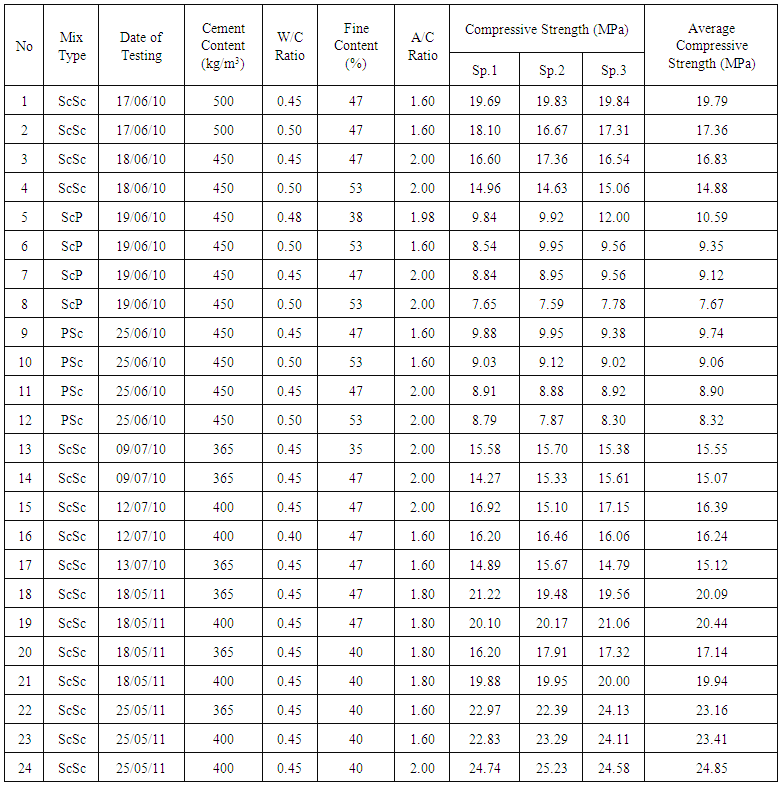 | Table 3. Strength test results at the age of 7 days |
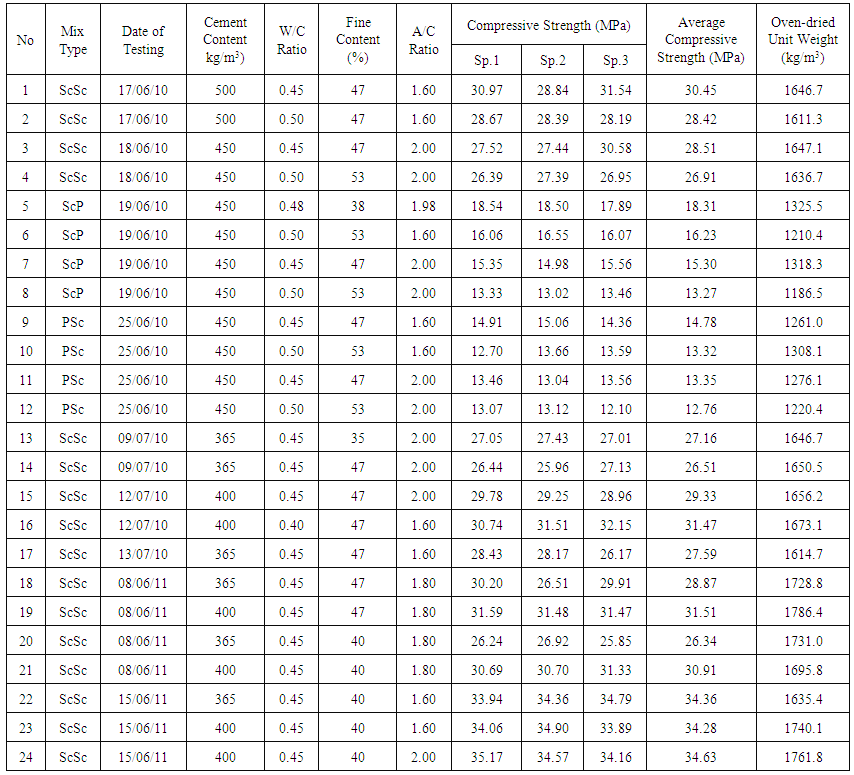 | Table 4. Strength test results at the age of 28 days and Oven-dried Unit Weight |
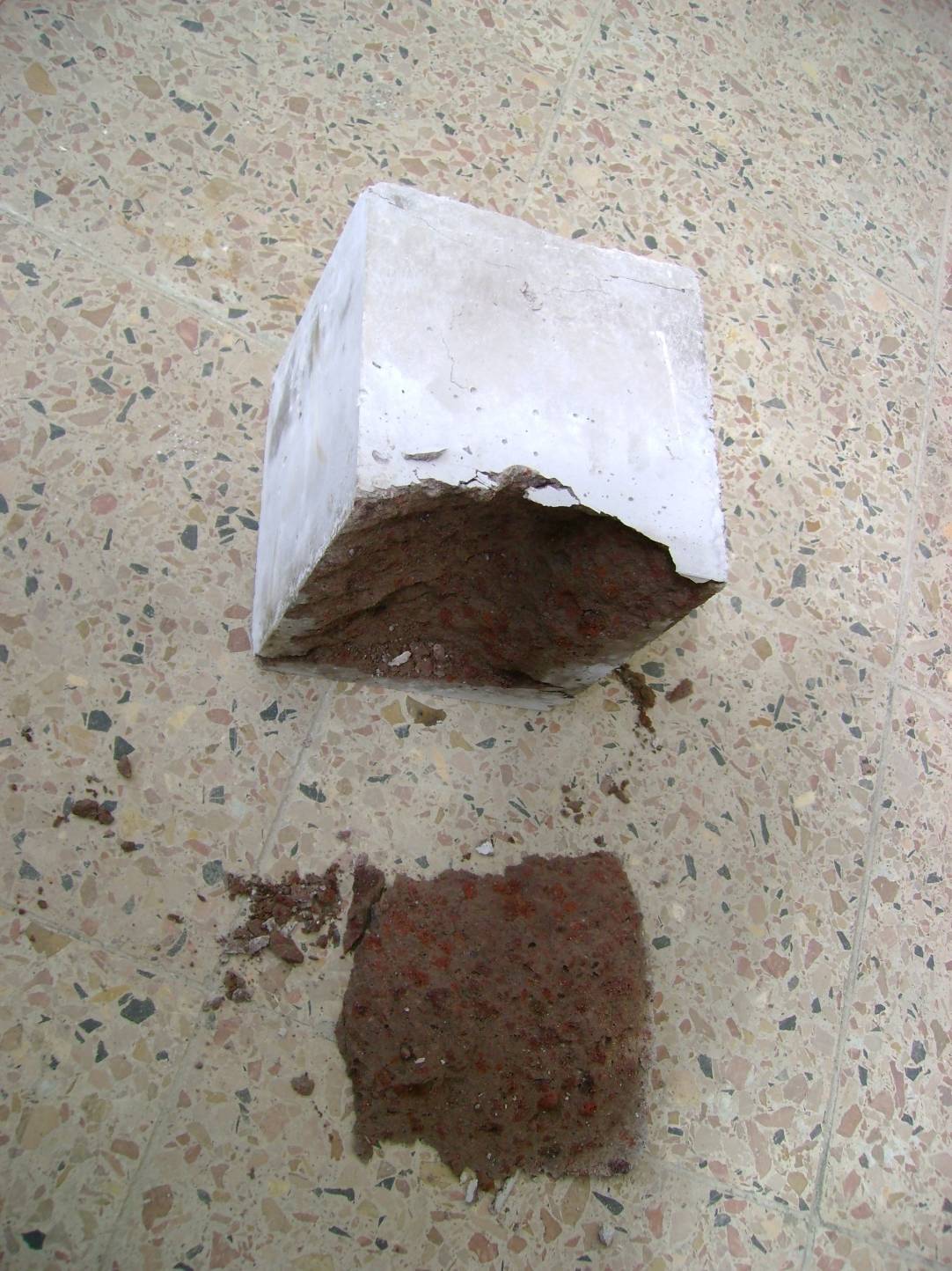 | Figure 3. Scoria Aggregates Crushing |
4. Theoretical Strength Determination and Test Results of Ribbed Slab
4.1. General
Full-size ribbed slabs spanning 3.0 m and 3.5 m were constructed to investigate the strength and deformation characteristics under service and ultimate loads. The predicted ultimate loads of the slab are calculated using the idealized parabolic-rectangular stress block for concrete and elastic-perfectly plastic relationship for reinforcement.The theoretical yield moment capacities of the interior and edge beams are presented. The yield capacities of the cross sections were chosen in lieu of the ultimate capacities for strength comparison purposes because of the physical limitations with regard to deflection measurements after yielding of the reinforcement.The mean compressive strength of the control cubes at the age of 28 days and the mean yield strength of the reinforcing bars were found to be 28 MPa and 373 MPa respectively.
4.2. Experiments on Actual Size of Ribbed-Slabs
One ribbed slab spanning 3.0 m and two ribbed slabs spanning 3.5 m were constructed and loaded until the reinforcements started yielding. The specimen and test setup are shown in Figures 4 - 7. 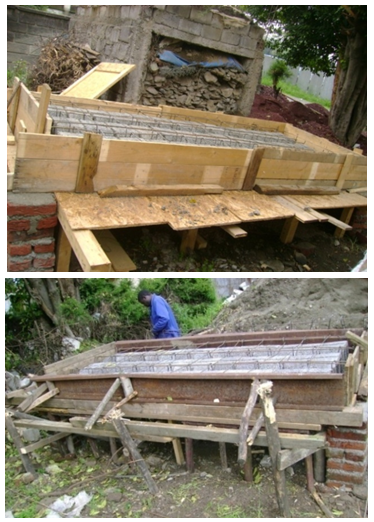 | Figure 4. Formwork for ribbed-slabs |
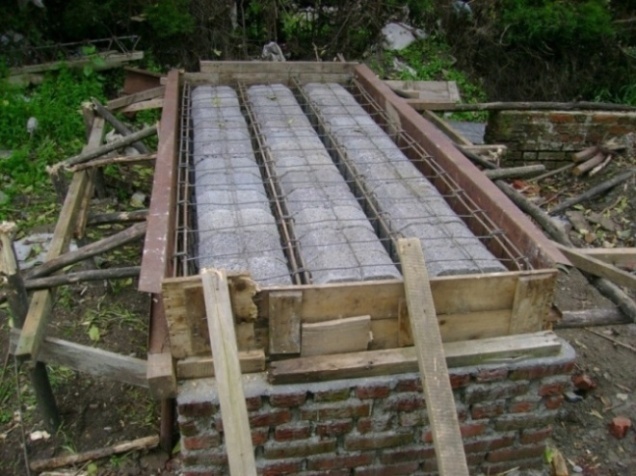 | Figure 5. Placing of HCB, Reinforcement layout, Supporting System |
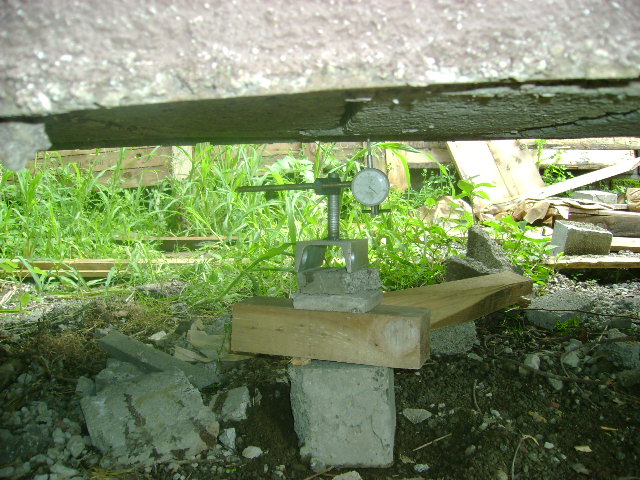 | Figure 6. Ribbed-Slab, experimental setup with gauges |
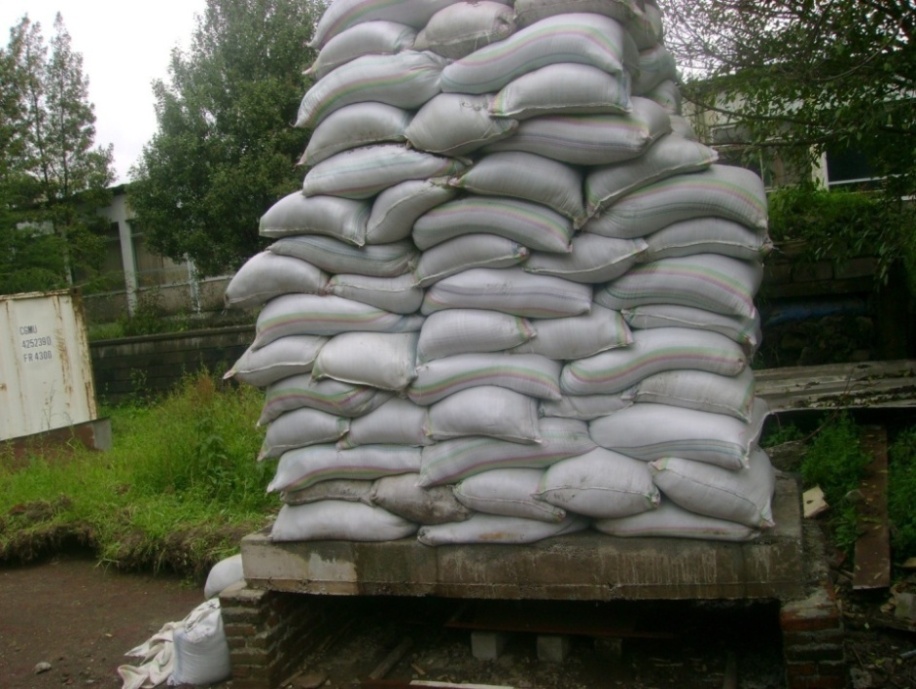 | Figure 7a. Ribbed-Slab1 under load |
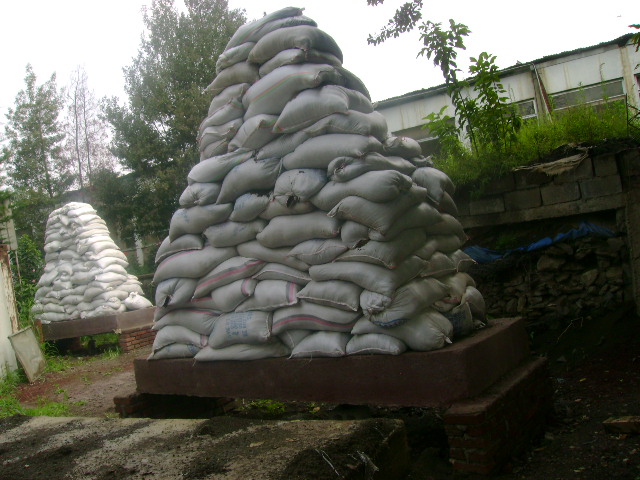 | Figure 7b. Ribbed-Slabs 2 and 3 under load |
The uniformly distributed load (sacks filled with sand) was applied over the middle portion of the slabs to avoid dispersion of load directly to the supporting brick piers. The loading was gradually increased until the reinforcement had started yielding. This stage of load was characterized by rapid increase in deflection at which time the dial gauges were removed and the load increment was almost simultaneously stopped. The load corresponding to the yielding of the slab is taken from the load versus mid span deflection curve shown in Figure 8-10. The yielding loads plus self weight for the ribbed slab-1 was 1050kg. The yielding load plus the self weight of ribbed slabs-2 and 3 are 915 kg and 920 kg. Deflection reading corresponding to further increase in loading was recorded as long as the physical limitations of approximately maximum dial readings allowed.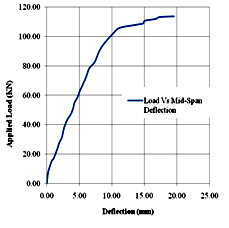 | Figure 8. Load versus mid-span deflection of ribbed slab 1 |
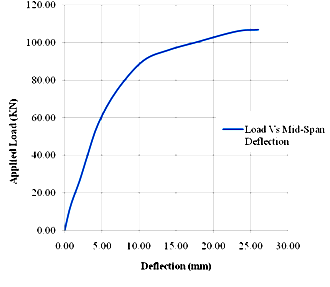 | Figure 9. Load versus mid-span deflection of ribbed slab 2 |
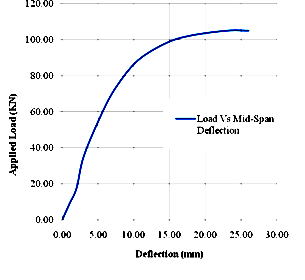 | Figure 10. Load versus mid-span deflection of ribbed slab 3 |
4.3. Comparison of the Results and Discussion
In the following sections, the internal yield moments for the interior and edge beams of the test ribbed slabs subjected to loading that corresponds to the yielding of the reinforcement will be determined.Comparisons of moment capacities of the beams at yield from experimental and analytical results are shown in Table 5. Table 5. Theoretical versus experimental yield moment capacities 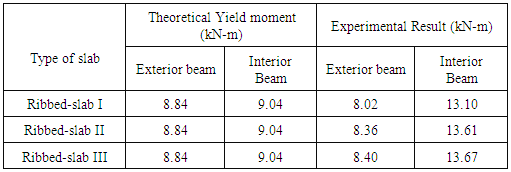 |
| |
|
Experimental and theoretical yield moment capacities of exterior beams compare quite well. On the other hand, the experimental yield moment capacities of the interior beams are greater than that found analytically.References [5-7] are used for the analysis of the experiment ribbed slabs and slab sections. Details of the cross section analysis based on Ethiopian codes are available in references [1].In all the experiment slabs, tension cracks were formed first due to flexural stress. Figures 11-13 show the cracking pattern in the experiment slabs. The width and length of the cracks were well controlled and uniform because of the presence of shear reinforcement.However, in experiment ribbed slab-1 diagonal tension crack near the face of support was observed and this crack extended deep in to the compression zone.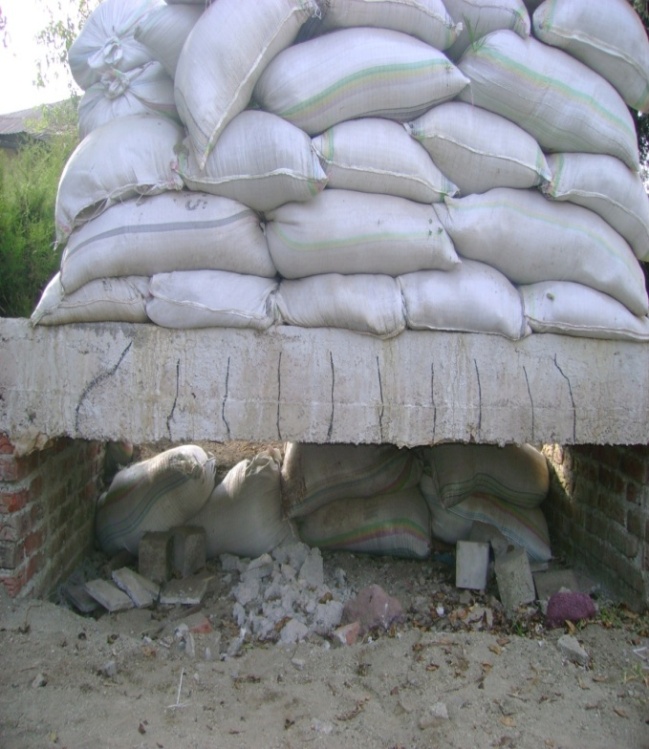 | Figure 11. Crack pattern in experiment slab 1 |
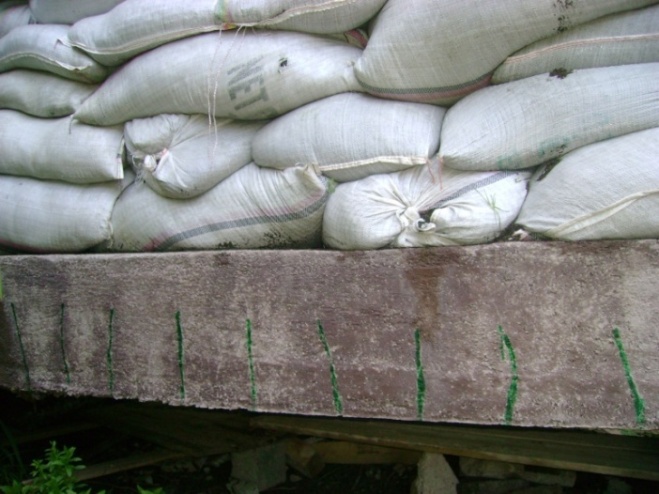 | Figure 12. Crack pattern in experiment slab 2 |
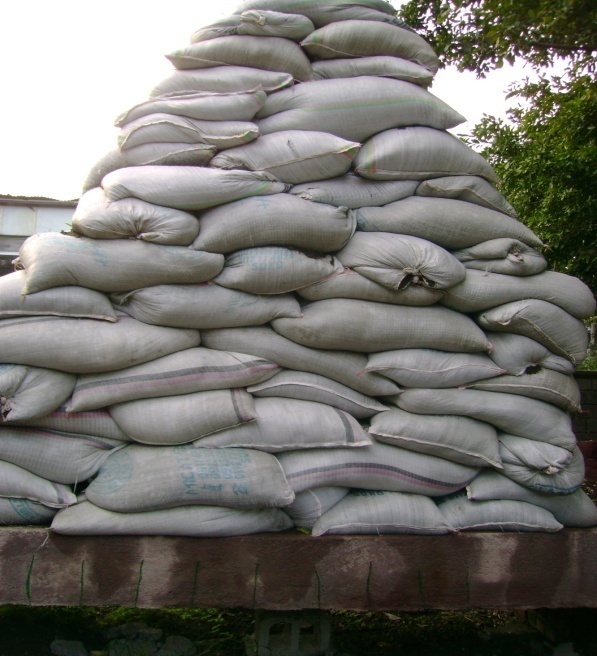 | Figure 13. Crack pattern in experiment slab 3 |
At the instant the diagonal tension crack develops, the simultaneous bending stress combines with the shear stress to increase the diagonal tension stress further [1].The beams of the experiment slab, although reinforced with longitudinal reinforcement, are not provided with any other reinforcement to offset the effects of diagonal cracking. This made the diagonal crack to be much more decisive in the strength and performance of the ribbed-slab beam than the flexural tension cracks.Therefore, the failure mode of the experiment ribbed slab 1 was due to flexural shear crack. To avoid this mode of failure, experiment ribbed slabs-2 and 3 were cast with 3.5 m span and shear reinforcement in external beams were placed at 10 cm distance, hence their mode of failure was flexural.
5. Conclusions and Recommendations
The use of widely available natural volcanic materials; pumice and scoria for the construction of ribbed-slab has been studied.Based on laboratory test results and experimental investigation of ribbed-slab produced using all-scoria lightweight concrete, the following recommendations and conclusions can be drawn:1) Structural scoria lightweight concrete can be produced up to strength of 30 MPa by using locally available well-graded scoria coarse and fine aggregates with cement content of 360 kg/m3 and above.2) Structural concrete to be used in ribbed slabs and other reinforced concrete structures cannot be produced with both coarse and fine pumice aggregates within the normal cement contents (200 to 450 kg/m3).3) Unlike crushed gravel aggregates, the water absorption of pumice and scoria aggregates are significantly affected by weather conditions. Therefore, great care should be exercised during addition of water. 4) Sometimes the pumice aggregates obtained from quarries might be used without grading; nevertheless, grading of both coarse and fine scoria aggregates is necessary before using the aggregates in the mix design.5) Mix proportions of scoria coarse aggregates with scoria fine aggregates possessed a desirable quality with regard to strength; therefore, scoria concrete with 40 - 47% fine content, 0.45 water cement ratio and 400 kg/m3 of cement content can be used for ribbed slab construction.6) Basic mechanics of reinforced concrete can be used for the design and analysis of ribbed slab systems with Ethiopian scoria aggregates.7) In almost all the trial-mixes the oven-dried unit weight is less than 18kN/m3. Therefore, this type of construction becomes suitable for the desired purpose of reducing the size of structural elements, the amount of reinforcement and with it the overall cost of the structure.
References
[1] | Melese Yohannes, Investigation on Suitability of Pumice and Scoria Aggregates in Ribbed-Slab Construction, MSc Thesis, Addis Ababa University, Addis Ababa, 2010. |
[2] | Hossain, Khandaker MA, Lachemi, The Mixture Design, Strength, Durability, and Fire Resistance of Lightweight Pumice Concrete, Canada, 2007. |
[3] | ASTM C 136 Standard Test Method for Sieve Analysis of Fine and Coarse Aggregates, 2001. |
[4] | ASTM C 330 Standard Specification for Lightweight Aggregates for Structural Concrete, 2000. |
[5] | Girma Zerayohannes and Adil Zekaria, Experimental and Theoretical Study of Precast Beam-Slab Construction, Addis Ababa University, 2008. |
[6] | Girma Zerayohannes, Ethiopian Building Code Standard, EBCS 2 - Part 2, Design Aids for Reinforced Concrete Sections Based on EBCS 2-Part 1, Ministry of Works & Urban Development, 1995. |
[7] | Ethiopian Building Code Standard, EBCS 2 - Part 1, Structural Use of Concrete, Ministry of Works & Urban Development, 1995. |
[8] | Daniel Abebayehu, Studies on Pumice Blocks and Scoria Bricks as the basis of Standardization, Addis Ababa University, Addis Ababa, 1998. |
[9] | Satish C. and Lief B., Lightweight Aggregate Concrete, Chalmers University of Technology Göteborg, Sweden, 2002. |
[10] | Mikyas Abayneh, Concrete making properties of Lightweight Aggregate Concrete made with Ethiopian Pumice and Scoria, Msc. Thesis for Israel Institute of Technology, Haifa, 1970. |
[11] | Clarke J.L., Structural Lightweight Aggregate Concrete, Blackie Academic & Professional, London, 2005. |
[12] | ACI Committee 213, Guide for Structural Lightweight-Aggregate Concrete, American Concrete Institute, Farmington Hills, 2003. |
[13] | ASTM, Annual book of American Society for Testing and Materials, 1999. |
[14] | Clarke J.L., Structural Lightweight Aggregate Concrete, Blackie Academic & Professional, London, 2005. |
[15] | Khandaker M. Anwar Hossain, Blended cement and lightweight concrete using scoria: mix design, strength, durability and heat insulation characteristics, Ryerson University, Toronto, Canada, 2006. |
[16] | Lightweight Concrete Mix Design, DOE method, Department of Environment, UK. |
[17] | Abebe Dinku, The Need for Standardization of Aggregates For Concrete Production in Ethiopian Construction Industry, Addis Ababa, 2005. |
[18] | Ethiopian Standards, Cement and Cement Products, 1990. |