Enamur R. Latifee
Department of Civil Engineering, Ahsanullah University of Engineering and Technology, Dhaka, Bangladesh
Correspondence to: Enamur R. Latifee, Department of Civil Engineering, Ahsanullah University of Engineering and Technology, Dhaka, Bangladesh.
Email: |  |
Copyright © 2012 Scientific & Academic Publishing. All Rights Reserved.
Abstract
Alkali-silica reaction (ASR)in concrete has been studied extensively after it was first recognized by Stanton in the late 1930s as a source of deterioration. This article presents the influence of pore solution alkalinity and cement alkalinity(Na2Oeq %) in the concrete mix on the expansive nature of ASR expansion. MCPT – a new test method of assessing aggregate reactivity in 56-days was used throughout the experiment. This MCPT method has excellent correlation with the CPT 2-year expansion results. The Spratt limestone, a well-known reactive aggregate from Ontario, Canada was used in the experiment. The specimens were kept in a soak solution matching the predicted pore solution. The aim of the research was to find out the influence of pore solution alkalinity and cement alkalinity on the ASR expansion.It was also aimed to see if the correlation between pore solution alkalinity (also cement alkalinity) and ASR expansion is linear or not. Good linear correlation was established forpore solution alkalinity and ASR expansion at early stages (within one month) and similarly for cement alkalinity (Na2Oeq%) andASR expansion. However, the later age expansions showed that ASR expansion is more influenced by high alkaline environment than low alkaline environment and they are not proportional. This also confirms the fact that ASR distress becomes critical at high alkaline environment in the early age of the concrete structure.
Keywords:
Alkali-silica Reaction, Concrete, Cement, Alkali
Cite this paper: Enamur R. Latifee, Influence of Pore Solution and Cement Alkalinity on ASR-Expansion Behavior, Journal of Civil Engineering Research, Vol. 3 No. 5, 2013, pp. 143-147. doi: 10.5923/j.jce.20130305.01.
1. Introduction
Alkali-silica reaction (ASR) is a chemical reaction between reactive silica (SiO2) in certain aggregates (e.g.: chert, quartzite, opal, strained quartz crystals) andalkali hydroxides in the concrete pore solution. The pore solution alkalinity comes from the cement alkalinity (expressed as Na2Oeq%). The alkali-silica reaction (ASR) in concrete was first recognized by Stanton in the late 1930s as a source of deterioration[1, 2]. Researchers have shown that alkali content in the cement greater than 0.60% causes the ASR[1, 2]. However, even with the low alkali cement, ASR can happen with highly reactive aggregates. The reaction (between reactive silica and alkali in the pore solution) produces a hydrous alkali-silica gel, often referred to as ASR gel. Formation of the ASR gel alone does not cause cracking, however when the gel absorbs water it shows significant potential to swell. The resulting expansion often results in pressures greater than what the concrete can withstand, which in turncauses cracks in the concrete.The reaction process can be viewed as a two- step process: Step 1:Silica + Alkali = Alkali-Silica-gel SiO2+2NaOH+H2O = Na2SiO3.2H2O (2KOH can replace 2 NaOH)Step 2:Gel Reaction Product + water = ExpansionEven though cement alkali content contributes to pore solution alkalinity, it is not fully investigated how the pore solution affects the ASR expansion. This research investigates the influence of pore solution alkalinity on ASR expansion. Low alkali and high alkali cement based concrete- pore solution was matched by soak solution alkalinity.
2. Experimental Investigation
2.1. Materials
Aggregates: A well-known reactive aggregates was selected in the investigation: Siliceous Limestone from the Spratt Quarry in Ontario, Canada; The reference non-reactive aggregates used in this study Siliceous sand from the South Carolina (Fine Aggregate) [Table 1].Table 1. Material properties used in the investigation  |
| |
|
Cement: A high-alkali (alkali content of the cement was measured at 0.82% Na2Oeq) Type I cement from Lehigh Cement Company and one low-alkali (alkali content of the cement was measured at 0.49% Na2Oeq) from Argos Cement Companywere selected for this study [Table 2].Table 2. Chemical Composition of High-Alkali and Low-Alkali Cement  |
| |
|
NaOH: A reagent grade sodium hydroxide was used to boost the alkali level of concrete to 1.25% Na2Oeq by the weight of the cement for one particular case and NaOH was also used in the soak solution matching pore solution alkalinity.
2.2. MCPT Method
In the MCPT method, concrete prisms of dimensions 50 mm x 50 mm x 285 mmare used. In this method, a cement content of 420 kg/m3 is used with the cement alkalis raised to 1.25% Na2Oeq. The test specimens are demolded 24 hours after casting. After taking the initial length reading, the prisms are submerged in water at 140°F (60℃) for an additional 24 hours. At the end of 48 hours from the time of casting, the zero-day length change reading is taken, before the prisms are transferred to 1N NaOH soak solution that has already been preconditioned to 140°F (60℃) temperature. Subsequent length change readings are periodically taken at 3, 7, 10, 14, 21, 28, 42, 56, 70 and 84 days. The details of the test method can be found in the references[3]. The length-change measurements of the test specimens followed the procedure of ASTM C157/157M[4].
2.3. Pore Solution Calculation
The pore solution composition of the concrete mixtures was predicted based on the equation developed by Helmuth and Diamond[5]:[OH-] = 0.339 Na20%/(w/c) + 0.022 +/- 0.06 mol/LThe pore solution concentration of the job concrete mixture is predicted based on the assumption that the cementitious materials content is entirely composed of portland cement alone. This will likely overpredict the pore solution alkalinity, (even in case of a mixture with SCM) to produce a conservative estimate on the effectiveness of the job concrete mixture.Based on the predictive equation, with a constant w/c of 0.45 used in all cases, for low-alkali cement mixtures (alkali content of the cement was measured at 0.49% Na2Oeq), a pore solution composition of 0.45 M NaOH was determined, while for the high-alkali cement (alkali content of the cement was measured at 0.82% Na2Oeq) a pore solution composition of 0.70 M NaOH solution was established. It can be noted that Chen and Brouwers[6] reported a method for alkali concentration only for slag cement.Research conducted by Rivard et al.[7] showed that in the CPT(ASTM C 1293) the pore solution alkalinity decreased over time which could be attributed to leaching. However, in the MCPT the specimens are kept in soak solution, therefore the alkalinity lost can easily be replenished by the surrounding soak solution.
3. Results and Discussions
3.1. Expansion Results Analysis of Different Alkali Cements and Soak-solutions
Three set of tests were conducted with different cement alkali content in the mix. The concrete prisms made of Spratt limestone were submerged in soak solution matching pore solution alkalinity at 60 degree Celsius. Three concrete prisms were made in each batch.The three tests conditions are as follows-1. Cement alkali boosted to 1.25% Na2Oeq and 1 N NaOH soak solution matching pore solution2. Cement alkali of 0.82% Na2Oeq and 0.7 N NaOH soak solution matching pore solution3. Cement alkali of 0.49% Na2Oeq and 0.45 N NaOH soak solution matching pore solutionThe expansion curves (% expansion due to ASR vs. Age in days), until 84 days, are shown in Figure 1. The % expansion is highest for Cement alkali (boosted) of 1.25% Na2Oeq and 1 N NaOH soak solution matching pore solution and lowest for Cement alkali of 0.49% Na2Oeq and 0.45 N NaOH soak-solution matching pore-solution, which is expected.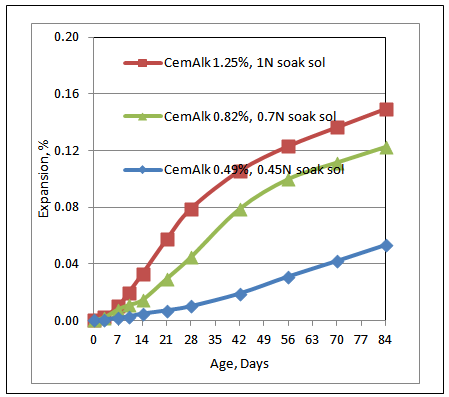 | Figure 1. Expansion curves of different cement alkalinity and soak solution alkalinity concrete prisms in the MCPT |
However, plotting the 28-day and 56-day % expansion vs. Soak solution alkalinity reveals that there is higher correlation between 28-day % expansion and Soak solution alkalinity than 56 day % expansion and Soak solution alkalinity as shown in Figures 2 and 3. 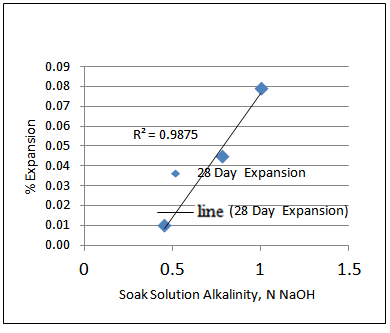 | Figure 2. 28-day % expansion vs. Soak solution alkalinity |
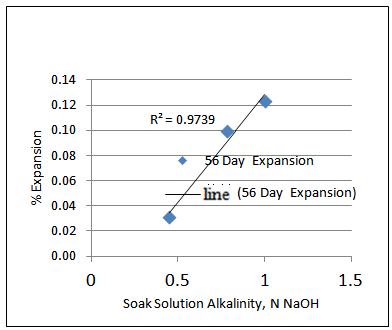 | Figure 3. 56-day % expansion vs. Soak solution alkalinity |
The other way to look into it is to compare the cement alkalinity in the mix and the % expansion. Plotting the 28-day and 56-day % expansion vs. cement alkalinity reveals that there is higher correlation between 28-day % expansion and cement alkalinity than 56 day % expansion and cement alkalinity as shown in Figures 4 and 5. Note that, the correlation is almost perfectly linear for 28-day % expansion and cement alkalinity (R2= 0.9938).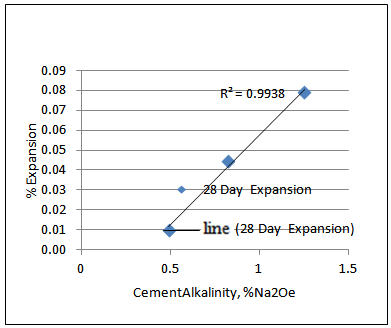 | Figure 4. 28-day % expansion vs. CementAlkalinity, %Na2Oe |
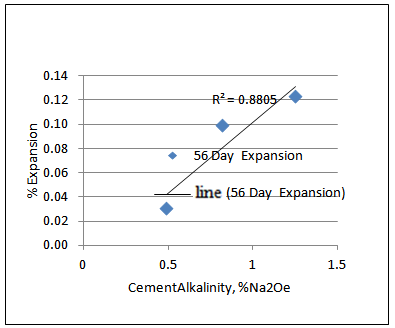 | Figure 5. 56-day % expansion vs. CementAlkalinity, % Na2Oe |
The early age (28-day) linear behaviour or correlation between pore solution (also cement alkalinity) and ASR expansion can be attributed to the fact that the ASR gel formation becomes a function of pore solution and cement alkalinity. At later stage, 56-day, the overall expansion in the high alkaline environment is much higher than low alkaline environment. This can be due to the fact that the average rate of expansion for high alkaline situation during the test period is much higher than the low alkaline situation. However, it is worth to note that at the age from 56-84 days the slope of expansion curve (rate of expansion) for low alkaline environment is increasing and for high alkaline environment it is decreasing. This suggests that even with low alkali cement, sufficient source of alkali can cause ASR problems in the field at later ages.The relationship can be expressed as a linear form for 28-day and as exponential form for 56-day. | (1) |
 | (2) |
Where, x=Pore soln. AlkalinityOr, =0.2024x2 +0.4732x-0.1523, x=Cement AlkalinityNow, using the limit of 0.04% at 56-days and solving for cement alkalinity yields, x =0.51 (% Na2Oe), using Spratt limestone reactive aggregate (a moderately reactive aggregate). Now, it is important to remember depending on the mineralogy of the reactive aggregate it would be different for different aggregate.
3.2. SEM Analysis
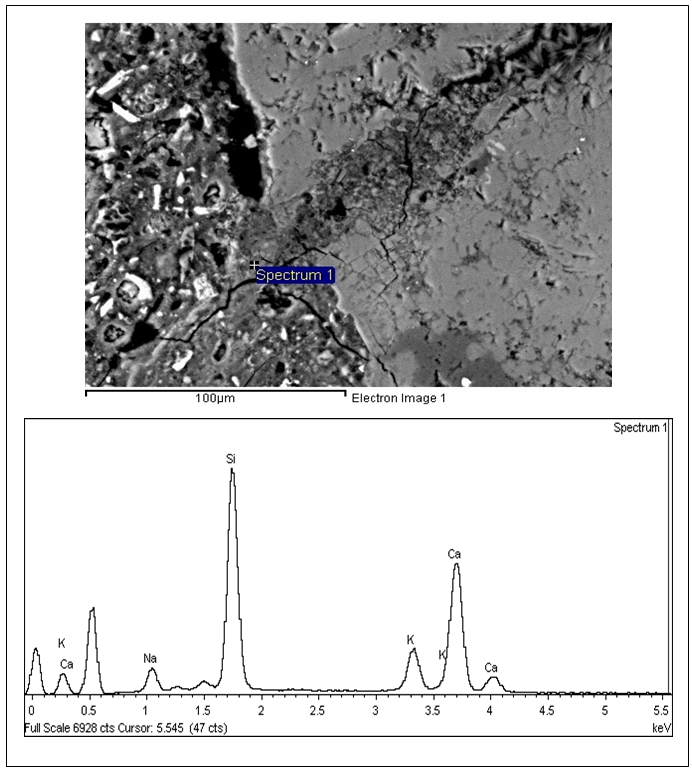 | Figure 6. SEM analysis and EDX fro Spratt MCPT specimen |
Scanning electron(SEM) and EDX (Energy-dispersive X-ray spectroscopy) analysis was done with the test specimen to verify the presence of ASR gel. The K+ and Na+ ions present in the matrix essentially showed the presence of ASR gel.
4. Conclusions
The experiment showed that the ASR related expansion in concrete is correlated with pore solution alkalinity and cement alkalinity. If we consider cement alkalinity the correlation is almost linear (R2=0.99) at early ages (28-day expansion). The variation starts at later ages (56-days) which indicate that pore solution/cement alkalinity effect is linear within first month and non-linear at later age. Percent expansion of concrete prisms can be predicted based on cement alkalinity, given that the aggregate reactivity of the field matches closely with the one tested in the laboratory.Increasing the temperature in general increases the ASR expansion. The 60℃ for the experiment was chosen to accelerate the expansion process and in some cases in hot weather conditions the concrete pavement temperature can reach 60℃. The influence of humidity is important in ASR (some researchers reported 80% RH needed for ASR reaction). In this experiment, the concrete specimens were submerged in alkaline solution so as to avoid storage condition variation and the soak solution could replenish the lost alkalinity in the pore solution.
References
[1] | Stanton, T. E.,1940, Expansion of Concrete through Reaction between Cement and Aggregate,Proceedings, American Society of Civil Engineers, pp. 1781-1811. (Reprinted with discussion and closure in Transaction, ASCE, V. 107, pp. 54-126. |
[2] | Stanton, T. E., 1942, California Experience with the Expansion of Concrete through Reaction between Cement and Aggregate,ACI Journal, Proceedings, V. 38, pp. 209. |
[3] | Rangaraju, P.R. 2011, “Development ofarapidlaboratory test method for assessing alkali-silica reactivity of aggregates”, interim report, Federal Highway Administration, Solicitation No. DTFH61-08-R-00010, pp. 1-19 |
[4] | ASTM C157/157M- 08 Standard Test Method for Length Change of Hardened Hydraulic-Cement Mortar and Concrete, Annual Book of ASTM Standards 2008, Vol. 04.02. |
[5] | HelmuthStark, R., Diamond, S., 1993, Alkali-Silica Reactivity: An Overview of Research,SHRP-C-342, Strategic Highway Research Program, National Research Council, Washington, D.C., pp. 13-14 |
[6] | W. Chen, H. J. H. Brouwers ,"A method for predicting the alkali concentrations in pore solution of hydrated slag cement paste", Journal of Materials Science, May 2011, Vol. 46, Issue 10, pp. 3622-3631 |
[7] | P. Rivard, M. A. Berrube, J. P. Ollivier, G. Ballivy, 2007,“Decrrease of pore solution alkalinity in concrete tested for alkali-silica reaction”,Materials and Structures,V. 40, pp.909–921. |