Onuorah L. O.1, Nwozor K. K.2
1Department of Physical and Geosciences, Godfrey Okoye University, Ugwu-omu Nike, Nigeria
2Department of Geology, Anambra State University, Uli, Nigeria
Correspondence to: Onuorah L. O., Department of Physical and Geosciences, Godfrey Okoye University, Ugwu-omu Nike, Nigeria.
Email: |  |
Copyright © 2014 Scientific & Academic Publishing. All Rights Reserved.
Abstract
This work demonstrates the design and implementation of a 3, 6, 9, 12 and 24 Volts switching mode power supply system that replaces battery as a major source of direct current (DC) voltage for electronic equipment that can be used to energize electrodes, in geophysics field work that involves electrical resistivity surveys, seismographic and magneto-telluric surveys. The switching mode output of a variable power supply system produces direct voltages of 3, 6, 9, 12, and 24 Volts that are selected by a multi-output switch. These voltages are stepped down from a 220 Volt alternating current (AC) main terminal by an auto (variable taps) transformer and thereafter rectified and smoothened. This smoothing process by a bridge rectifier converts AC to direct current (DC) and filters off the associated impurities and ripples. The capacitor used for each stage has the rating of 2200microfarad (µf) and 35Volts.
Keywords:
Direct current, Alternating current, Multi-output switching, Voltage and capacitive filters
Cite this paper: Onuorah L. O., Nwozor K. K., Instrumentation Geophysics: Design and Construction of a DC Variable Power Supply, International Journal of Instrumentation Science, Vol. 3 No. 2, 2014, pp. 13-16. doi: 10.5923/j.instrument.20140302.01.
1. Introduction
As discussed in the sequel, a regulated power supply is indispensable in powering or precision equipment operations. Joshua DuBois [4] defined electrical current as the time rate of change of charge flow in a circuit. Williams, O. A., [6] suggested that since the energy from the wall outlet is practically unlimited, it can be converted from its alternating current (AC) to direct or steady current (DC), and tailored to provide the voltage suitable for electronic equipment. This can be achieved in a DC power supply unit (PSU), and the PSU used in the laboratory for experiments is termed a laboratory bench supply. It can be designed as a variable power supply unit that can supply either a uni-polar or bi-polar power to the load (Shoewu et al., [5]). In most countries the electricity from the power grid to homes, industries and laboratories is transmitted and distributed in AC form, while most electronic equipment directly use the suitable means of converting the alternating supply to direct current therefore becomes indispensable. An alternating current is a current that varies in magnitude and direction with time (Fig. 1a) and a direct current is a current that maintains a constant magnitude as it flows through a wire without change in direction with time (Fig. 1b).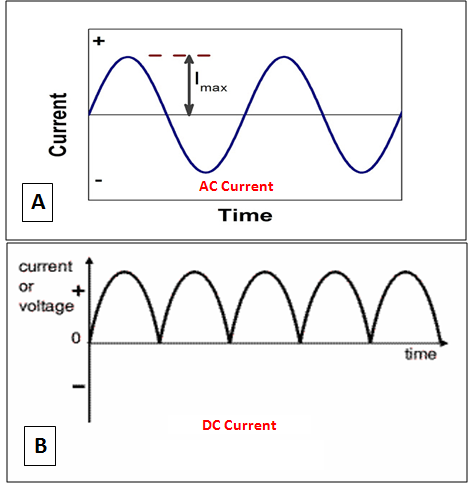 | Figure 1. Schematic representation of AC (A) and DC (B) Currents (Source: Williams, 1995) |
The primary characteristics that need to be considered in the design of a regulated power supply are the output dc voltage (Vdc), maximum current (Imax) required by the load, the tolerance level and the percentage regulation (%Reg) allowable (Berkowitz, S. [1], Horowitz, P. and Hill, W. [3]). There are various ways of designing regulated power supply units. The most commonly used are the linear regulated power supply, mostly used in low power application and the switching mode regulated power supply which this work is mainly concerned with is mostly used in high power applications. Moreover, the use of a battery as a source of DC voltage for electronic circuits has several short comings. These include, relatively short life-time, relatively low circuits that can be continuously supplied without battery recharging, and relatively large volume requirement.
2. Design and Construction
The switching mode power supply is made up of a number of stages. These stages are the transformer, the voltage selector, full-wave bridge rectifier and finally the filtering and smoothening circuit. The transformer operation consists of step-up and step-down modes. The step-up mode utilizes a high voltage secondary and low voltage primary. On the other hand, the step-down mode which this project is concerned with uses a low-voltage secondary and high voltage primary as illustrated in Fig. 2. 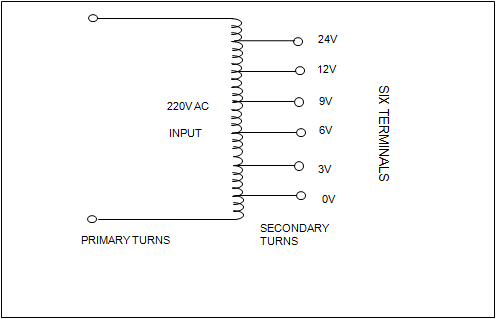 | Figure 2. Design of a variable auto-transformer |
The step-down transformer converts the mains voltage from 220V to the required DC at the output terminals for 3V, 6V, 9V, 12V, and 24V. These secondary winding outputs are AC which has not been rectified to give DC outputs.Figure 3 shows the second stage, the voltage selector or selecting switch. Switches used to open and close circuits are the start mechanism that sets an electrical process in motion. The switch in this design has 6 terminals A, B, C, D, E and F for selecting the required voltage, including an off-position F. G is the output selector operated by the knob. This second stage feeds the output alternating voltage to the input of the third (rectifier-bridge) stage (Fig. 4).The nonlinear characteristics of a diode are used to convert AC into unidirectional, but pulsating current in the process called rectification. The transformer AC voltage is rectified using a full-wave bridge rectifier to give equal positive direct voltages during the positive and the negative half-wave AC inputs. The output is DC in the sense that it does not change polarity, but it has periodic variations in voltage about a steady value that depends on the values of the R and C components shown. The variations are called ripples (Hammed, O.S. and Ademola, A.K. [2]). As shown in Figure 4, on one half of the cycle, when A is positive relative to B, only the diodes D1 conduct. On the other half of the same cycle, only the diodes D2 conduct. In both cases, the current goes through the load resistor (RL) in the same direction. This arrangement was used for the circuit under discussion. The diodes D1, D2 being the IN 4001. 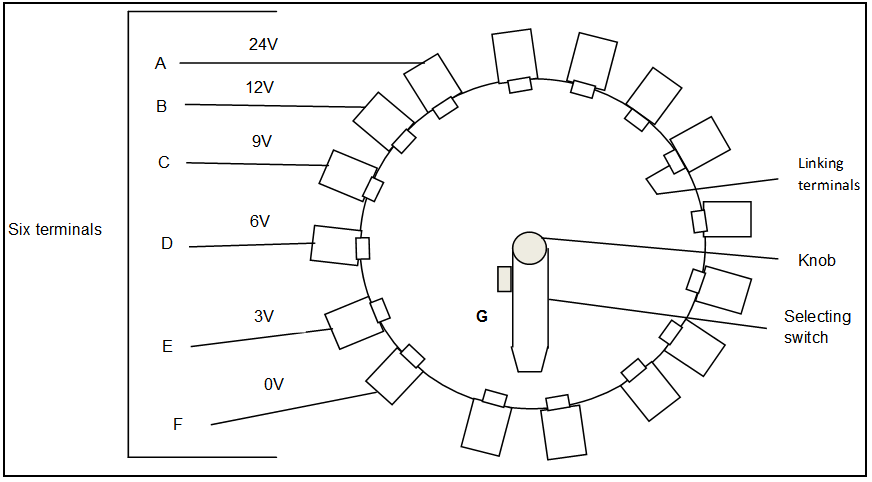 | Figure 3. Switch arrangement |
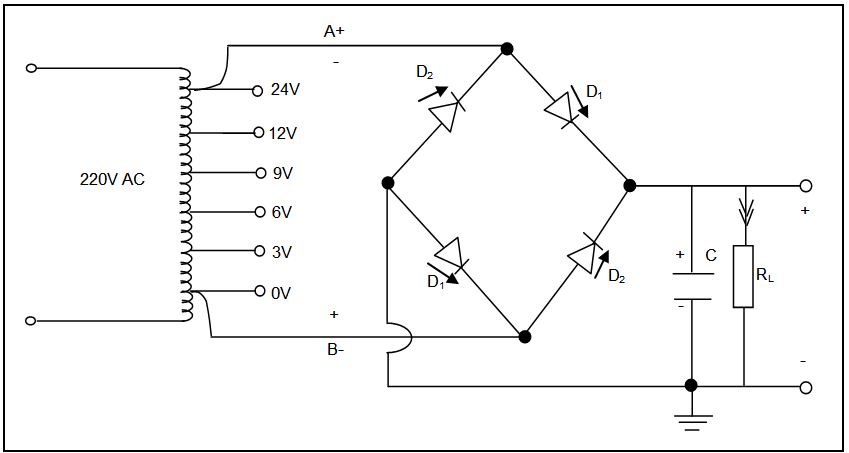 | Figure 4. Full-wave bridge rectifier and smoothening circuit |
The fourth and final stage is the filtering or smoothing circuit which is used here to minimize the ripple content of the rectifier output. A filter is a circuit that by design suppresses certain frequency outputs in favour of others, including zero frequency or DC. The simplest filter is a capacitor. A capacitor can be an assembly of two conducting plates separated by an insulator that is used to store an electric charge, or simply it is a device used to store electrostatic energy. The way to get a good filtering is to use a very high value of capacitance in combination with a low parallel resistance, which will lower the load impedance. This also means that it will take longer for the capacitor to discharge. The ratio of the charge (Q) on the positive plate of a capacitor to the potential difference (V) between the plates is called its capacitance (C). Mathematically,
The S.I units of capacitance, charge and potential difference are the farad (f), Coulomb (C) and Volts (V), respectively. The voltage rating of the capacitor must be much greater than the output voltage; else the voltage will rupture the capacitor. Also, the bigger the capacitance of the capacitor the better the result hence the capacitor used in the project is rated 2200 microfarad (µf) and 35V. Figure 4 shows the capacitor placed in parallel with the load resistor, RL. The power supply filter stores energy when the current is high and gives it up when the current is low. This results in smoothing out the variations in current and as a result provides almost steady state DC that maintains a steady flow of power. The rectification and filtering stages were taken care of by a good combination of bridge rectifier and capacitor as shown in Fig. 4. The complete circuit diagram is shown in Fig. 5. 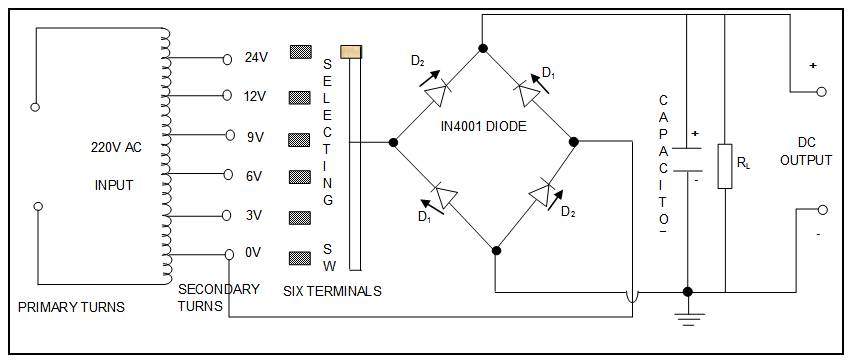 | Figure 5. Complete circuit diagram for the power supply system |
3. Conclusions
This work has successfully presented a switching mode of a variable power supply system. It produces DC voltages of (3, 6, 9, 12 and 24) Volts that replace battery as its major source for electronic equipment used in the field, industries, laboratories and houses. The step-down transformer function is to steps down the mains voltages from 220V to the required DC outputs terminals 3, 6, 9, 12 and 24 Volts (fig. 2). Figure 3 shows the switch as the terminals selector. An important function of a rectifier diode is to convert an alternating current (AC) into a direct current (DC) by a process known as rectification. It allows the passage of electric current in one direction and blocks from the other (fig. 4). The significant of a capacitor in rectification is to block DC while permitting AC to pass through and to smooth the top of the rectified DC output. This variable power supply system is very simple in design with few components and can be built with ease into a complete circuit diagram for the power supply system of any desired appliance.
References
[1] | Berkowitz, S. 2003. Powering Digital Circuits and Systems. Orbit Educational Book Publishers: Toronto, Canada. |
[2] | Hammed, O.S. and Ademola, A.K. 2008.”Design and Construction of an Emergency Rechargeable Lamp Incorporated with a Battery Overcharging Preventer Circuit”. Medwell Journal of Engineering and Applied Sciences. 3(9):684-687. |
[3] | Horowitz, P. and Hill, W. 1980. Art of Electronics. Cambridge Press: Cambridge, UK. |
[4] | Joshua DuBois. 2009. ECE 480.Team 6 – BorgWarner Fan Clutch. |
[5] | Shoewu, O., Olaniyi, O.M. and Ogunleye, O.M., 2011. Design and Development of an Intelligent Variable Power Supply Device. The Pacific Journal of Science and Technology Volume 12. Number 1. |
[6] | Williams, O.A. 1995. Design and Construction of a Regulated Power Supply Unit. Cambridge Press: Cambridge, UK. |