Ravindrapal M. Joshi
Department of Electronics, M. B. Patel Science College, Anand-388 001, Gujarat
Correspondence to: Ravindrapal M. Joshi, Department of Electronics, M. B. Patel Science College, Anand-388 001, Gujarat.
Email: |  |
Copyright © 2014 Scientific & Academic Publishing. All Rights Reserved.
Abstract
A low cost simple and versatile Seebeck coefficient ‘S’ measurement setup is fabricated. The fabricated setup can measure values of Seebeck coefficient ‘S’ with variation in temperature. The temperature can be varied from 25°C to 300°C. The setup can measure the value of S in the said temperature range for small samples. The compact setup has two heaters to raise overall temperature of the sample from 25°C to 300°C. The auxiliary heaters maintain the temperature gradient. The set overall sample temperature and temperature gradient is maintained by controller circuit and other ancillary circuits. To reduce error in Seebeck measurements, the temperature gradient ΔT can be varied from 1 to ± 10°C. The measured Seebeck coefficient ‘S’ variation with temperature for four single crystal samples using the fabricated setup is presented.
Keywords:
Differential temperature controller, Seebeck coefficient, Semiconductors
Cite this paper: Ravindrapal M. Joshi, Differential Temperature Controller for the Measurement of Thermoelectric Power on Small Samples, International Journal of Instrumentation Science, Vol. 3 No. 1, 2014, pp. 8-11. doi: 10.5923/j.instrument.20140301.02.
1. Introduction
The measurement of Seebeck coefficient as a function of temperature is one of the most significant methods for investigating electronics properties of solids. In fundamental, the Seebeck coefficient ‘S’ provides useful information about the mechanisms of electrical transport. The quantity S can be used to determine the mobility ratio, the concentration of majority carriers, the position of Fermi level, scattering mechanism, etc, and it has been used for the study of electrical transport properties of samples by many investigators [1-4]. The polarity of S indicates the types of dominant carriers or the type of dominant electric conduction.The author has developed a simple instrument: differential temperature controller, to undertake measurements of Seebeck coefficient in the temperature range 25°C to 300°C. The controller controls not only the overall temperature but also maintains the temperature gradient (0°C to 10°C) between the two ends of the sample. The instrument is very compact, low power and easy to operate.
2. Operating Technique
The sketch of the experimental setup is shown in Figure 1. It consists of two blocks. Block – 1: Sample holder with heaters and pick up probes and Block – 2: electronic circuits controlling temperature and temperature gradient across the sample. The sample holder consists of two low power heaters A and B (15W each). Temperature T of the heater A is measured by thermocouple TC1 and the temperature difference ΔT between A and B is measured by differential temperature sensor (TC2). Both the thermocouples are of K type. The sample under investigation is mounted directly on the heaters and is held by two pick up probes which are of copper (or stainless steel). The probes are made of copper or stainless steel so that they are a good conductor of electricity and measures the developed electrical signals at the sample surface where the junction if formed between the probe and the sample. Thus these probes measures the Seebeck voltage developed across the two ends of the sample.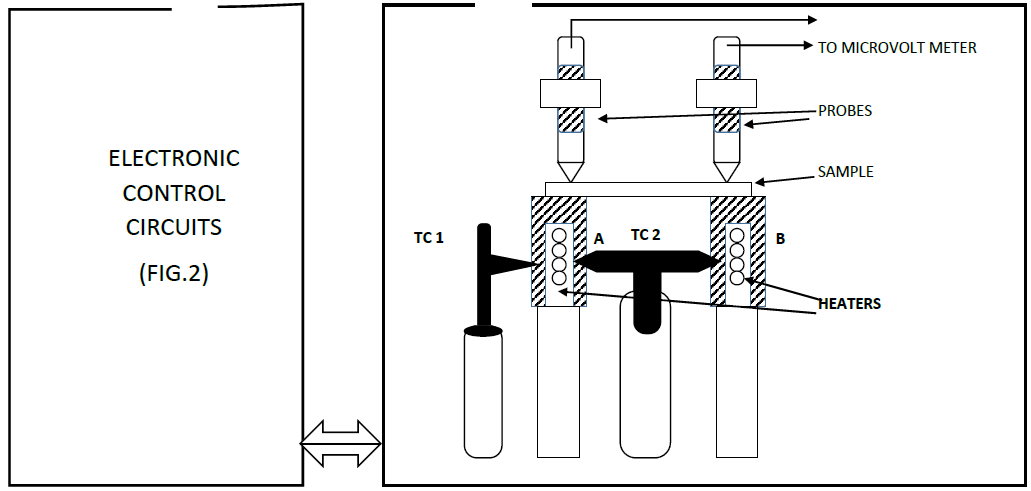 | Figure 1. Experimental system |
The Figure 2 shows the details of the Block 2 of the setup. The Block 2 consists of temperature indicator, proportional controller and two heater control circuits which drives the two heaters A and B. Error amplifier A generates a signal corresponding to the temperature difference between T and set T. Similarly error amplifier generates a signal corresponding to the desired temperature gradient (ΔT), Err-2 can be selected to be –ve or +ve depending upon the desired direction of temperature gradient. Two independent control circuits drive two heaters A and B. Signal corresponding to Err-1 after proper manipulation is given simultaneously to both the heater control circuits. However signal corresponding to Err-2 is added in only one of the adders, automatically as decided by two diodes D1and D2, in only one of the adders. This action generates difference in the power to be given to the two heaters, generating a stable temperature gradient between the two heaters. Using this circuit the temperature T, can be controlled from 25° to 300 °C and ΔT from 1 to ± 10°C simultaneously with better than ± 1°C stability.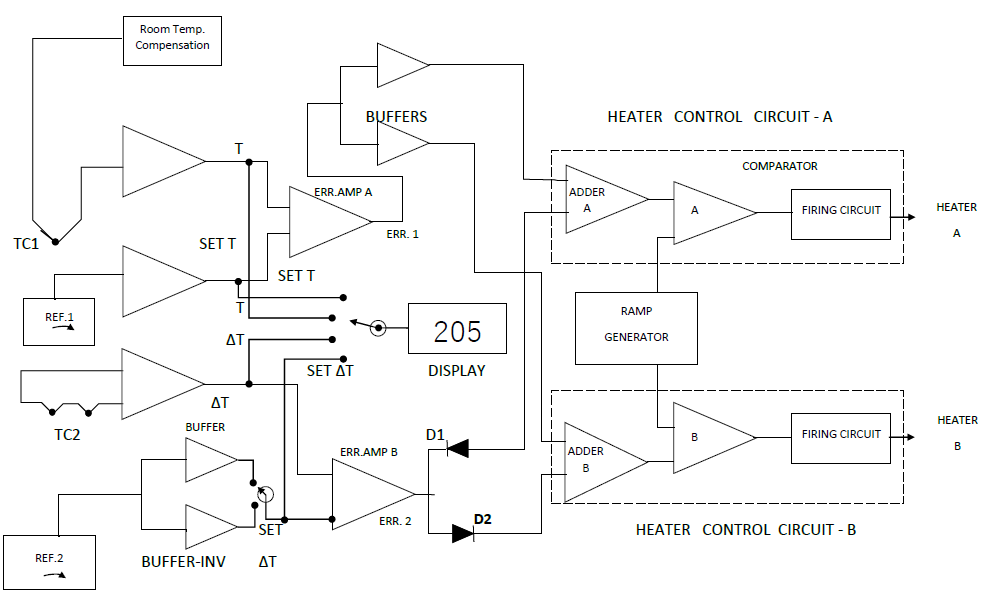 | Figure 2. Block diagram of the control circuit |
3. Results and Conclusions
As a test case of the fabricated setup, Seebeck coefficient S measurements were carried out on two samples, tin monoselenide (SnSe) and Cadmium doped copper indium disulphide (CulnS2) single crystals. The developed voltage across the probes was measured using digital voltmeter (Meco) connected externally. The results are shown in Figures 3 and 4. The brief of the samples employed, experimental conditions maintained and the obtained results are tabulated in Table 1.Table 1. The Seebeck coefficient conditions and values obtained on different samples 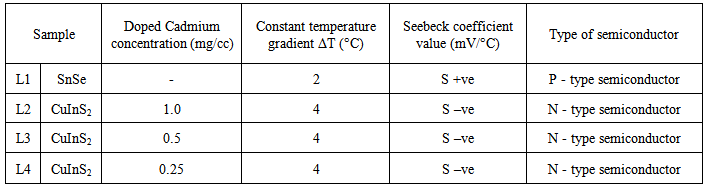 |
| |
|
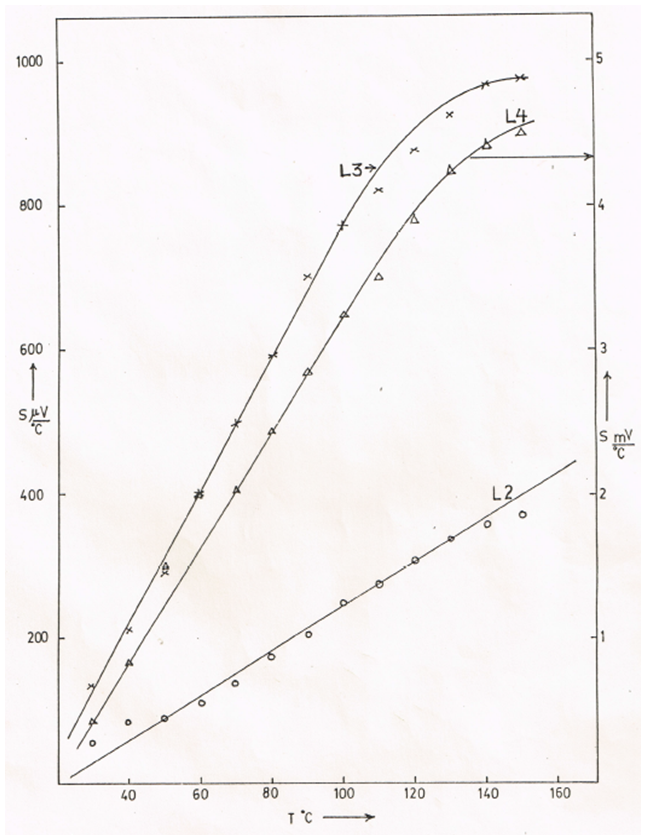 | Figure 3. Seebeck coefficient verses temperature in Cd doped CuInS2 crystals |
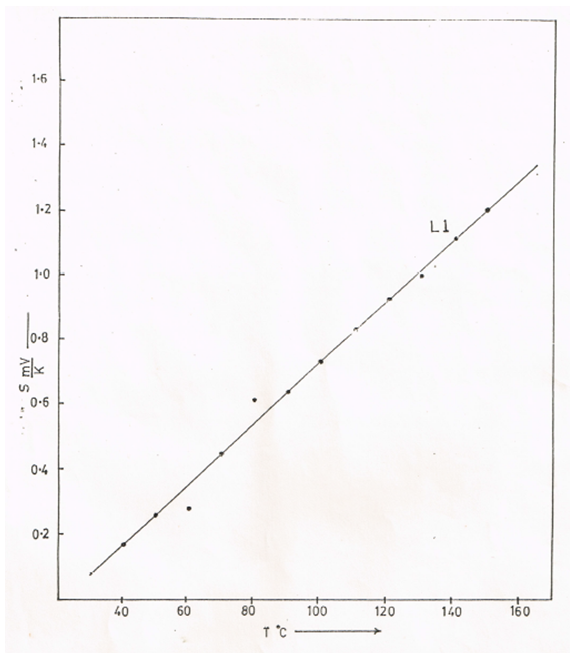 | Figure 4. Seebeck coefficient vs temperature in SnSe single crystal |
The problem usually encountered in making thermopower measurements are stray thermal e.m.f.s. In the present instrument these are eliminated by providing choice of selection of temperature gradient in the range between 1°C to 10°C.The sample holder and the electronic circuits are integrated into one unit. Use of low power heaters and electronic controller make the operations very easy. This simple and economic instrument could be used to understand and study the concepts of thermoelectric power, by introducing an experiment at the masters’ level studies.
4. Future Scope for Improvements
The fabricated setup has future scope of improvement. The following are some of the improvements possible.1. The complete setup can be enclosed in a transparent case so that external atmospheric variation does not affect the measurements.2. In the present setup for reducing the stray thermopower variation in the temperature gradient from 1°C to 10°C is possible. Even further accuracy in measurement and reduction in the stray thermopower, change in the sign of the temperature gradient ΔT should be made.
References
[1] | Kwan C. Kao & Wei Hwang, Electrical Transport in Solids, Pergamon Press, 14 (1981) 42. |
[2] | M. Cutler, The thermoelectric behaviour of disordered systems, Phil. Mag. 25(1972) 173. |
[3] | M. Cutler & N. F. Mott, Observation& Anderson localization in an electron gas, Phys. Rev. 181(1969) 1336. |
[4] | V.A. Johnson, “Seebeck effect in Semiconductors” In progress in semiconductors, Heywood (LONDON), 1(1956) 63. |
[5] | Operational Amplifier and Linear Integrated Circuits Robert Francis Coughlin, Fredrick Francis Driscoll, Prentice Hall PTR, 2001. |
[6] | Operational Amplifier and Linear Integrated Circuits, Ramakant A Gayakwad, PHI Learning Private Limited, 2013. |