Turdikulov Tolmas Nurulloyevich1, Doniyarov Giyas Tilavovich2, Bahramov Hasan Kayumovich3, Kadyrov Hassan Irgashevich4
1Base Doctoral Student, Tashkent Chemical-Technological Institute, Department of "Basic Organic Synthesis", Tashkent, Republic of Uzbekistan
2PhD., Tashkent Chemical-Technological Institute Yangiyer Branch, Yangiyer City, Republic of Uzbekistan
3PhD, Bukhara State Medical Institute, Head of the Department of "Medical Chemistry", Bukhara, Republic of Uzbekistan
4Doctor of Technical Sciences, Professor of the department of Basic Organic Synthesis, Tashkent Institute of Chemical Technology, Tashkent, Republic of Uzbekistan
Correspondence to: Turdikulov Tolmas Nurulloyevich, Base Doctoral Student, Tashkent Chemical-Technological Institute, Department of "Basic Organic Synthesis", Tashkent, Republic of Uzbekistan.
Email: |  |
Copyright © 2025 The Author(s). Published by Scientific & Academic Publishing.
This work is licensed under the Creative Commons Attribution International License (CC BY).
http://creativecommons.org/licenses/by/4.0/

Abstract
This study presents a comprehensive thermodynamic analysis of the sulfonation reactions of linear, isostructured, and unsaturated C7–C18 alkylbenzenes with sulfur trioxide (SO₃), aimed at optimizing the production of alkylbenzene sulfonic acids (ABSA)—precursors for surfactant synthesis. Utilizing the DFT method in the Gauss computational package, standard thermodynamic parameters (ΔG, ΔH, ΔS) for various target and side reactions were calculated. Results demonstrated that the sulfonation of alkylbenzenes is thermodynamically favorable across all studied substituent lengths, with Gibbs free energy values ranging from approximately –185 to –235 kJ/mol depending on the molecular structure. It was found that para-substitution is preferred due to steric and electronic effects, and the formation of by-products such as pyrosulfonic acids and sulfones is also feasible under industrial conditions. A mathematical model of the sulfonation reactor was proposed, integrating mass and heat transfer dynamics as well as operational cycles. The model confirmed that optimizing process parameters enables nearly complete conversion of raw materials while mitigating high-viscosity by-product formation. These findings support the development of more efficient and sustainable industrial sulfonation processes for surfactant production.
Keywords:
Pyrolysis distillate, Fractional distillation, Arenes, Sulfonation, Alkanolamines, Ammonium salts, Surfactants
Cite this paper: Turdikulov Tolmas Nurulloyevich, Doniyarov Giyas Tilavovich, Bahramov Hasan Kayumovich, Kadyrov Hassan Irgashevich, Thermodynamic Analysis of the Reactions of the Sulfonation Process of C7-C18 Alkylbenzenes with Sulfuric Anhydride, International Journal of Virology and Molecular Biology, Vol. 14 No. 3, 2025, pp. 35-42. doi: 10.5923/j.ijvmb.20251403.03.
1. Introduction
In many countries, the deep processing of products formed during the pyrolysis process has also been established, in which various valuable reagents are obtained. For example, in this article, the authors studied the yield of naphthalene by thermal treatment of heavy pyrolysis resin. In the work, distillate fractions and cubic residue were obtained by atmospheric-vacuum distillation by treating heavy pyrolysis resin in a reactor with a stirrer at a temperature range of 250-270°C for 6-8 hours. The distillate was separated by distillation into fractions in a short temperature range: main fraction (up to 200°C), naphthalene fraction (200 - 230°C), methylnaphthalene fraction (230 - 245°C), residual fraction (245 - 340°C).As a result of the thermal treatment carried out by the authors, an increase in the naphthalene fraction and the content of naphthalene in it was observed, while a decrease in the content of mono- and bicyclic alkenes and dienes, vinyl aromatic hydrocarbons, indene and its homologues, dihydronaphthalenes in the product was observed [1].Oil-polymer resins with targeted complex properties, used as a functional additive to polymer compositions with a high yield under certain conditions of thermal processing of heavy pyrolysis resins, as well as commercially pure naphthalene, can be isolated without expensive additional processing.To date, known methods for utilizing liquid pyrolysis products are mainly aimed at isolating technical hydrogenation products of certain fractions, as well as individual products (benzene, toluene, xylene, dicylopentadiene, naphthalene, etc.) for further use. In addition, liquid pyrolysis products are also utilized in the direction of producing low molecular weight "oil polymer resins" [2].
2. Materials and Methods
Study Design and ParticipantsThis study employed a computational and theoretical design to simulate the sulfonation reactions of C7–C18 alkylbenzenes under industrial conditions. Conducted during 2024–2025, the research did not involve human or biological participants but focused on modeling molecular behavior through thermodynamic and quantum-chemical approaches. No sampling or sample size calculations were required in the classical empirical sense. The study considered various classes of alkylbenzenes—linear, isostructured, and unsaturated—across different carbon chain lengths (C9–C14) for comparative analysis. The selection criteria for these molecules were based on industrial relevance, availability in pyrolysis products, and variation in side-chain structure, while no specific exclusion criteria were applied due to the theoretical nature of the study.Data Collection InstrumentsThe main instruments utilized for data collection and computational modeling were advanced quantum-chemical simulation tools. Thermodynamic properties—Gibbs free energy (ΔG), enthalpy (ΔH), and entropy (ΔS)—were calculated using the Gaussian (Gauss) software package based on Density Functional Theory (DFT). The simulation relied on parameterized molecular descriptors, and geometry optimization was conducted to ensure the stability of molecular structures. The DFT method was selected due to its balance between accuracy and computational efficiency. Validity of the data was ensured through cross-validation with known literature values, and reliability was supported by repeated calculations under varying conditions, all yielding consistent thermodynamic trends.ProceduresThe research procedure did not require participant access or questionnaire-based settings. Instead, alkylbenzene molecules were designed and structurally optimized using computational chemistry environments. The setting was a controlled digital laboratory involving energy minimization routines and quantum mechanical calculations. Raw data in the form of molecular energies and spatial configurations were input into the Gauss software, which performed the DFT-based simulations. All computational runs were performed using standardized reaction conditions (303 K, 110 kPa) mimicking industrial reactor environments. The generated outputs, including reaction energies and equilibrium conditions, were collected and tabulated for analysis. No physical materials or chemical reagents were handled during the study.Data AnalysisAll data analyses were performed using the Gauss software suite and supplemented with Excel for statistical tabulation and graph generation. Thermodynamic parameters were derived by calculating energy differences between reactants and products, as well as transition states where applicable. The DFT method was specifically chosen for its effectiveness in evaluating electron density distributions and predicting thermochemical behavior. Multiple reaction pathways, including para-substitution, sulfonation into side chains, and by-product formation (e.g., sulfones, pyrosulfonic acids), were analyzed. The justification for using DFT lies in its widespread acceptance for modeling chemical reactivity and its ability to incorporate electron correlation effects. Summary statistics (mean, range) were computed across different molecule classes to assess consistency and reaction favorability.
3. Results
Foreign companies currently produce 30-40 types of petroleum polymer resins of various nature and applications [3], and in our country, the products of the pyrolysis process are still used as fuel.Heavy pyrolysis resin is a liquid secondary product of the pyrolysis process. It contains aromatic compounds C8+, resins, asphaltenes, which are formed as a result of the condensation and condensation reaction of aromatic rings [4]. It has been established that the content of naphthalene and methylnaphthalene exceeds 25% [5,6]. In modern pyrolysis plants, heavy pyrolysis resin is not considered the main product, it does not have a stable composition, physicochemical properties, which change depending on the composition of the initial raw material and the technological regime. The use of heavier raw materials for the pyrolysis process leads to an increase in the content of naphthalene and its homologues (more than 25%) in the heavy pyrolysis resin [7]. The modern use of heavy pyrolysis resin has quite broad directions, but it has not solved the problem of its full utilization (1-table).It is known that the chemical composition of heavy pyrolysis resin is complex and in many cases, it is impossible to identify the composition under production conditions. Heavy pyrolysis resin is a by-product of the process, its analysis methods are expensive and not always feasible, therefore it is mainly used as a raw material component in various processes (1-table).Table 1. Possibilities of application and processing of heavy pyrolysis resins 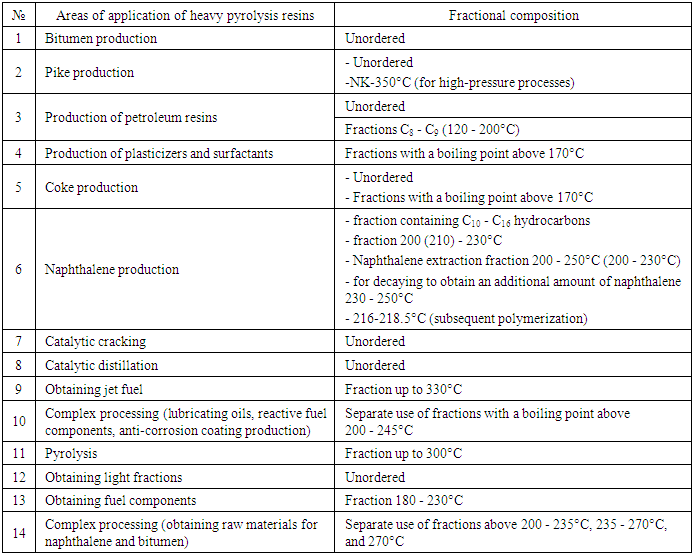 |
| |
|
Moreover, the different raw material base of the pyrolysis process significantly affects the component composition of the primary and secondary products of the process, and the lack of information on the composition of heavy pyrolysis oil does not allow for a high degree of reliability in determining the direction of its target application. At the same time, the chemical composition of the pyrolysis process raw material does not significantly affect the content of the main component of the heavy pyrolysis resin - naphthalene and its homologues. Thus, the possibility of extracting a naphthalene concentrate as an individual component from the composition of heavy pyrolysis resin is a relatively promising direction for its processing [8].According to the results of some studies [9], in 2022, the ABSA market has changed significantly compared to previous years. Over the next five years, the average annual growth rate of revenues in the ABSA market will be 1.9%. The volume of the global ABSA market is expected to increase from $4598.8 million in 2020 to $5263.1 million by 2027.The increasing use of ABS in detergents, emulsifiers, binders, etc. leads to the continuous growth of the ABS market worldwide.Currently, due to growing demand in China and Europe, they are the main consumer regions. These two regions together account for 34% of global consumption.Currently, regions such as Europe, North and South America, Africa, the Middle East, and the Asia-Pacific region are expected to dominate the ABSA market. Currently, the industrial sulfonation process is carried out at the following enterprises, which are presented in Table 2.Table 2. Enterprises carrying out the sulfonation process 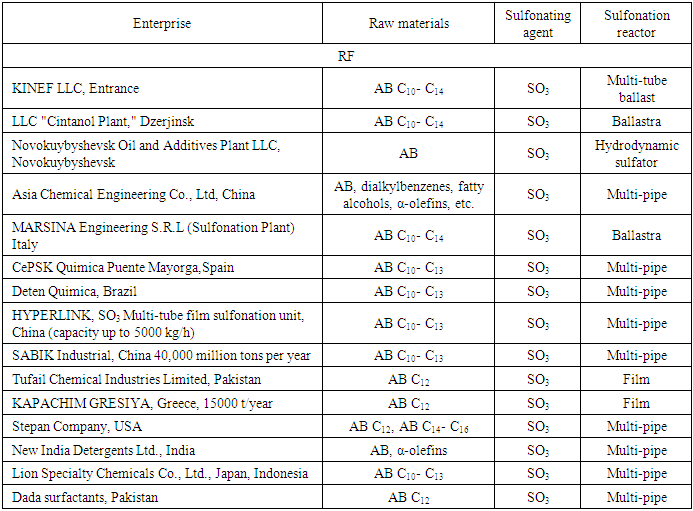 |
| |
|
Other important producers of sulfonic acids are Sasol, Fogla Group, ISU Chemical, Solvay, Huntsman, Kao, Hansa Group, Miwon Chemical, NCSP, FUCC, Ho Tung, Nanjing Gige.The obtained results and their analysis. Most ABSK manufacturers use alkylbenzenes sulfonation technology in a multi-tube film reactor. This design allows for a significant reduction in the formation of a viscous component in the reaction medium with the correct selection of raw material consumption.Based on the analysis of literature sources and the composition of the raw material, a list of reactions occurring during the sulfonation of alkylbenzene with sulfur trioxide was compiled:1. Targeted reaction for formation of ABSAR – С6Н5 + SO3 → R – С6Н4 – SO3H1. Formation of sulfonsR – С6Н5 + R – С6Н4 – SO3H → R – C6H4 – SO2 – C6H4 – R' + H2O2. Formation of sulfoanhydride2R – С6Н4 – SO3Н + 3SO3 ↔ R – С6Н4 – SO2-О-SO2–С6Н4 – R + H2SO43. Formation of PSAR – С6Н5 + 2SO3 → R – C6H4 – SO2-O-SO3H4. Interaction of PCP with residual blood pressure to form ABSA.R – C6H4 – SO2-O-SO3H+ R – С6Н5 → 2R – С6Н4 – SO3H5. Hydrolysis of sulfuric acid anhydride to form ABSKR – С6Н4 – SO2-О-SO2 – С6Н4 – R + Н2О → 2R – С6Н4 – SO3Н6. Sulfonation of AB with an unsaturated hydrocarbon radical into the side chainR – С6Н5 + SO3 → R(SO3H) – С6Н5The sulfons formed as a result of side reactions enter the unsulfurized part, i.e., they are highly viscous components that are located on the walls of the reactor tubes and disrupt the hydrodynamic regime of the organic fluid flow.The last two decades have been characterized by the widespread introduction of quantum-chemical methods into the practice of chemical research to calculate the molecular structure and properties of molecules. The rapid development in the field of computer technology, primarily in manuals for personal computers, the emergence of mass-available quantum-chemical complexes and modern visualization tools have revolutionized quantum chemistry in terms of its application in various fields of chemistry [10].Predicting various properties of molecules, as well as the characteristics of reactions based on quantum chemistry and molecular dynamics methods, is carried out in many software products, including the Gauss software package, which uses modern electron structure theory.The structure and chemical activity of molecules are calculated based on the optimization of energies, energy properties, and geometry of individual molecular structures.There are two approaches to calculating quantum-chemical properties:Molecular mechanics models that use classical physics laws to determine the structure and properties of molecules. These methods are included in the algorithms of computer programs such as MM3 (3-digit molecular mechanics), HyperChem, ADF (Amsterdam functional density), Quanta, Spartan, Sybyl, HONDO.2. Electronic structure methods, which often use the laws of quantum mechanics, which determine the energy and other properties of molecules by solving the Schrödinger equation [11].From the point of view of the approach to solving the Schrödinger equation, semi-empirical and non-empirical methods are not distinguished. Semi-empirics are characterized by the same general calculation scheme. The same applies to the methods of абинитио. The difference is that each calculation stage is simplified [12].Another way to derive the Schrödinger equation is to apply the transition to classical mechanics to the boundary.There are two classes of methods for calculating the electronic structure of molecules:- Semi-empirical, such as AM1 (Ostin's model l), MINDO/3 (modified interval neglect of differential similarity), and PM3 (parameterized model number 3), used in programs such as MOPAC, AMPAC, HyperChem, GAUSSIAN, GAMESS, and others. To simplify calculations in these methods, parameters derived from experimental data are used.- do not use non-empirical or ab-initio methods, experimentally obtained parameters in calculations. Aboriginal calculations are based solely on the laws of quantum mechanics, providing high accuracy using only a limited set of physical constants.Methods based on the functional density theory (DFT) are newer considering the influence of electron correlation. Additionally, calculations using this method require the same time and computer power as calculations using Hartree-Fock. In the functional density method (DFT), it is considered that the potential acting on each electron from all other electrons in the molecule or crystal depends only on the electron density and its gradient.In this work, the thermodynamic characteristics of the transient state were calculated using the Gauss software package using the DFT method.Alkylbenzenes with a side chain length of 9 to 14 carbon atoms undergo sulfonation. In addition, the raw material may contain unsaturated and isostructured alkylbenzenes with side chains. Using the Gauss program, the thermodynamic parameters of the target and side reactions were calculated depending on the hydrocarbon chain length of alkylbenzenes and their structure.The electron-donating alkyl group has ortho- and para-orientation. However, steric factors also have a great influence on the sulfonation of alkylbenzenes with a side chain length of 9-14 carbon atoms, and the sulfonation occurs mainly in the para-position.Targeted ABSA formation reaction
where R - is a linear hydrocarbon substituent with a chain length of 9-14 carbon atoms.Table 3. Calculated thermodynamic parameters of sulfonation reactions of alkylbenzenes with linear hydrocarbon chains 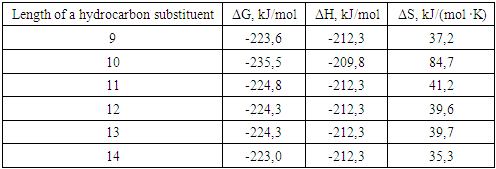 |
| |
|
As can be seen from Table 3, the rate of chemical changes does not increase with increasing substituent chain length. This is because in this case, the transfer force of electron density from the substituent to the benzene ring does not change significantly with the growth of the side chain. The average Gibbs energy of the reaction is DG=-225.9 kJ/mol.To determine the structure of the hydrocarbon chain, the Gibbs energy of the methyl radical in various positions relative to the hydrocarbon chain was calculated. The calculation results are presented in Figure 1.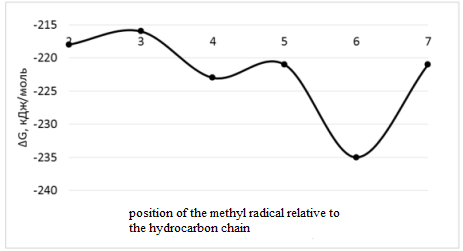 | Figure 1. Dependence of the Gibbs energy value on the position of the methyl radical relative to the hydrocarbon chain |
As can be seen from Figure 1, the highest Gibbs energy value in the meta-position during the sulfonation process, equal to -234.66 kJ/mol, corresponds to the moment when the methyl radical is located at the sixth carbon atom in the hydrocarbon chain. In this regard, we assume that the greatest value of Gibbs energy will be at the location of the methyl radical at the sixth carbon atom, regardless of the length of the hydrocarbon chain.
where R- is an isostructured hydrocarbon substituent with a chain length of 9-14 carbon atomsTable 4. Calculated thermodynamic parameters of sulfonation reactions of alkylbenzenes with isostructured hydrocarbon substituents 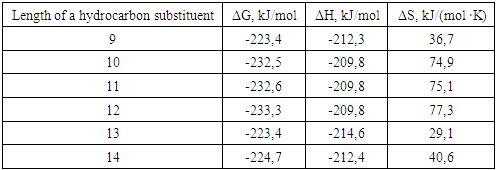 |
| |
|
The sulfonation reaction of alkylbenzenes with an isostructure side hydrocarbon chain is also thermodynamically possible and practically independent of the side chain length (Table 4). The average Gibbs energy of the reaction is DG= -228.3 kJ/mol.Sulfonation of alkylbenzenes C9-C14 with an unconjugated hydrocarbon substituent proceeds according to the following reaction:
where R - is an unsaturated hydrocarbon with a chain length of 9-14 carbon atoms, at the sixth carbon atom.Table 5. Calculated thermodynamic parameters of the sulfonation reaction of alkylbenzenes with unconjugated hydrocarbon substituents 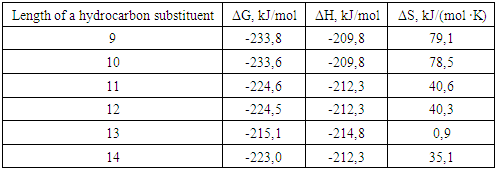 |
| |
|
The presence of a double bond also does not significantly affect the change in Gibbs energy (Table 5. The average Gibbs energy ΔG=-225.7 kJ/mol.Sulfonation of alkylbenzenes into the side chain by an unsaturated hydrocarbon substituent is carried out according to the following reaction:
where R - is a hydrocarbon substituent containing an unsaturated structural double bond with a chain length of 10-13 carbon atoms, located on the sixth carbon atom, SO3 - on the sixth carbon atom.Table 6. Calculated thermodynamic parameters of the reaction of sulfonation of alkylbenzenes into a side chain with an unsaturated hydrocarbon substituent  |
| |
|
The Gibbs energy for sulfonation of alkylbenzenes into a side chain (SO3H at the sixth carbon atom of the side chain) is approximately -184 kJ/mol (Table 6). The reactions of sulfonation of unsaturated alkylbenzenes in the side chain are less than the reactions of sulfonation of unsaturated alkylbenzenes in the para-state (ΔG = -232 kJ/mol).The formation of PSC occurs according to the following reaction:
where R- is an unsaturated structural hydrocarbon substituent with a chain length of 10-13 carbon atoms.Table 7. Calculated thermodynamic parameters of pyrosulfonic acid formation reactions 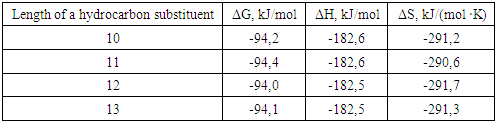 |
| |
|
The occurrence of a side reaction of PCC formation is thermodynamically possible and practically does not depend on the length of the hydrocarbon chain and averages ΔG ≈ -94.2 kJ/mol (Table 7).The formation of sulfons occurs according to the following reaction:
where R - is an unsaturated structural hydrocarbon substituent with a chain length of 10-13 carbon atoms.Table 8. Calculated thermodynamic parameters of sulfonation reactions (vaporization) 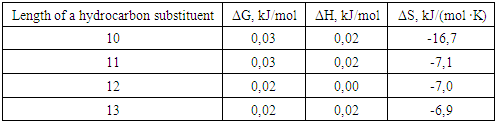 |
| |
|
The fact that the Gibbs energy of sulfonation reactions is close to zero indicates that these reactions are in equilibrium (8-table).Thus, thermodynamic calculations confirm the formation of both iso- and unsaturated structural ABSАs, as well as the formation of by-products such as PSАs and sulfons.The fact that the length and structure of the side chain of alkylbenzenes have little effect on the thermodynamic parameters of the ongoing reactions leads to the unification of these processes into one reaction.Due to the inexpediency of isolating the specific components included in the unsulfurized part of the ABSA, along with sulfons, the following substances formed in small quantities are combined into the pseudocomponent "Non-sulfurized Compounds": ethers, alcohols, sulfons, and SA.It was established that under the conditions of the industrial process of sulfonation of alkylbenzenes with sulfur anhydride in the reactor (temperature 303 K, pressure 110 kPa), reversible sulfonation reactions (∆G≈0 kJ/mol) occur, as well as additional products included in the composition contain unsulfonated residues, which is confirmed by the Gibbs energy change values of the reactions located in the range from (-94.2) to 0 kJ/mol. Mathematical model of a sulfonation reactor filled with a reaction medium activity parameter, which depends on the concentration of a high-viscosity component and takes into account heat and mass transfer, reactor washing periods, depending on the technological parameters of the interprocess and the composition of the raw material. The effectiveness of maintaining optimal values of the technological operating mode of the sulfonation reactor has been proven. If these conditions are met, it is possible to achieve an increase in the conversion rate of raw materials by almost 100%.
4. Discussion
The thermodynamic modeling conducted in this study has provided valuable insights into the sulfonation behavior of C7–C18 alkylbenzenes under industrial conditions. The use of quantum-chemical simulations based on Density Functional Theory (DFT) has proven highly effective for evaluating the feasibility, stability, and reaction pathways of these compounds, which are essential intermediates in the production of surfactants such as alkylbenzene sulfonic acids (ABSA).A key finding is the relative independence of sulfonation thermodynamics from the length of the hydrocarbon side chain. Despite variations in chain length (C9 to C14), the Gibbs free energy (ΔG) for the sulfonation reactions remained consistently within a narrow range, averaging around –225 to –228 kJ/mol for linear and isostructured alkylbenzenes. This indicates a broadly favorable thermodynamic profile across this class of compounds and suggests high adaptability in the choice of raw materials for industrial ABSA production.An important implication of this result is the feasibility of unifying the industrial sulfonation process for a broader range of feedstocks, including unsaturated and branched alkylbenzenes, without substantial alterations in reaction conditions. Notably, even the sulfonation of unsaturated alkylbenzenes showed only a moderate thermodynamic deviation, supporting their inclusion in process streams. However, the slightly reduced ΔG for side-chain sulfonation compared to para-substitution underscores the preference for the latter due to steric and electronic stabilization, aligning with previous experimental data on electrophilic aromatic substitution.The study also confirms the thermodynamic plausibility of side reactions such as the formation of sulfones and pyrosulfonic acids. These by-products, while less favorable than the main sulfonation pathways, can accumulate under certain process conditions and contribute to high-viscosity residues that impair reactor hydrodynamics. The close-to-zero Gibbs energy observed for sulfone formation highlights the potential equilibrium nature of such reactions, reinforcing the necessity of precise process control to minimize their occurrence.Furthermore, the modeling of reactor behavior through activity coefficients and the inclusion of heat and mass transfer variables allowed the development of a refined mathematical model of the sulfonation reactor. This approach not only quantifies the conversion efficiency but also offers practical guidance for adjusting operational parameters such as washing intervals and raw material throughput, thus enabling nearly complete conversion of feedstocks while suppressing undesirable side reactions.Comparing these findings with global industrial practices—such as those of KINEF (Russia), Stepan Company (USA), and MARSINA (Italy)—it is evident that the adoption of multi-tube film reactors and accurate raw material metering, as modeled in this study, are critical for optimizing yields and ensuring sustainability. The study provides scientific validation for current technological trends and lays a theoretical foundation for their further refinement.This thermodynamic analysis confirms the high efficiency and robustness of the industrial sulfonation of alkylbenzenes. The minimal influence of side chain variations on the overall thermodynamic favorability supports the expansion of raw material diversity, while the accurate prediction of by-product formation offers routes to better reactor design and process optimization. These findings have practical significance for surfactant manufacturing industries aiming to enhance conversion rates, reduce waste, and maintain product quality under varying feedstock conditions.
5. Conclusions
This study has demonstrated that the sulfonation of C7–C18 alkylbenzenes with sulfur trioxide is thermodynamically favorable across a wide range of molecular structures, including linear, isostructured, and unsaturated variants. The application of quantum-chemical methods, particularly Density Functional Theory (DFT) using the Gauss software package, allowed for accurate calculation of key thermodynamic parameters (ΔG, ΔH, ΔS), which consistently indicated strong reaction feasibility.The results confirm that para-substitution is the most energetically preferred sulfonation pathway, primarily due to favorable electronic and steric effects. While side-chain sulfonation and by-product formation (e.g., pyrosulfonic acids and sulfones) are also thermodynamically possible, their occurrence can be minimized through precise control of reactor conditions. The near-constant Gibbs energy values across different alkyl chain lengths support the standardization of industrial processes, enabling flexibility in raw material selection without compromising reaction efficiency.Moreover, the developed mathematical model of the sulfonation reactor provides a practical tool for optimizing operational parameters, improving conversion rates, and reducing the accumulation of high-viscosity by-products. Overall, this work offers both theoretical insight and practical value for enhancing the sustainability and performance of industrial surfactant production systems.
References
[1] | Yusevich, A. I., Trusov, K. I., & Osipyenok, E. M. (2022). The influence of thermal treatment of heavy pyrolysis tar on the yield and quality of naphthalene. Journal Name, 95(5), 646–655. |
[2] | Dumskiy, Y. V., & Butov, G. M. (1999). Chemistry and technology of petroleum polymer resins. Moscow: Khimiya. |
[3] | Zander, M., Mildenberg, R., & Collin, G. (1997). Hydrocarbon resins. New York, Basel, Cambridge, Tokyo: VCH Publishers. |
[4] | Prosochkina, T. R., Nikitina, A. P., Trapeznikova, E. F., et al. (2020). Hydrocarbon pyrolysis process [Protsess piroliza uglevodorodov]. Ufa: USPTU Publishing. |
[5] | Majer, Ye. A. (2014). Effective practice of deep processing of gas raw materials into chemical products at the enterprises of JSC SIBUR Holding and the technological processes used [Effektivnaya praktika glubokoy pererabotki gazovogo syr'ya...]. Tomsk: Tomsk State University Publishing. |
[6] | Kitonov, G. A., & Doshlov, O. I. (2015). Environmental problems with the use of heavy steam cracking tar at JSC "Angarsk Polymer Plant". New Science: Current State and Ways of Development, (6-3), 172–174. |
[7] | Sadygov, F. M., Magerramova, Z. Yu., Gadzhiev, G. N., Gejdarly, N. I., Gasan-zade, G. G., Mamedova, I. G., & Sadygova, N. S. (2016). Combination of technological mode of steam cracking and high-quality composition of heavy tar. Azerbaijan Chemical Journal, (4), 60–63. |
[8] | Lebedeva, M. A., Kolesnik, V. D., Mashukov, V. I., & Egorov, A. V. (2010). Chromatographic determination of the chemical composition of heavy steam cracking tars. Bulletin of the Tomsk Polytechnic University, 316(3), 102–105. |
[9] | Kantarci, N., Borak, F., & Ulgen, K. O. (2005). Bubble column reactors. Process Biochemistry, 40, 2263–2283. https://www.360researchreports.com/thankyou/request-sample/18719221. |
[10] | Poleshchuk, O. Kh., & Kizhner, D. M. (2006). Chemical studies by methods of molecular electronic structure calculation. Tomsk: TPU Publishing. |
[11] | Blatov, V. A., Shevchenko, A. P., & Peresypkina, E. V. (2005). Semi-empirical computational methods of quantum chemistry. Samara: Univer-Group. |
[12] | Ivashkina, E. N. (2012). Development and application of modeling systems for multistage petrochemical processes in industrial reactors (Doctoral dissertation abstract). Tomsk. |