E. V. Slivinsky1, S. Y. Radin2
1Prof., doctor of technical science, Mechanical Technological Faculty, Elets State University I.A. Bunin, Elets, 399770, Russia
2Associate prof., candidate of technical science, Mechanical Technological Faculty, Elets State University I.A. Bunin, Elets, 399770, Russia
Correspondence to: E. V. Slivinsky, Prof., doctor of technical science, Mechanical Technological Faculty, Elets State University I.A. Bunin, Elets, 399770, Russia.
Email: |  |
Copyright © 2012 Scientific & Academic Publishing. All Rights Reserved.
Abstract
This article presents the material relating to the development of advanced designs devices, excluding folding units train braking. In developing such technological solutions analyzed numerous, both domestic and foreign literature and patent sources allowed to create at 3 inventions efficient designs allowing to exclude folding units of heavy trucks when braking. On the basis of such devices developed computational scheme allows to assess the main rational kinematic and geometric parameters ensuring efficiency of the proposed design meets the requirements of the safety requirements of heavy trucks. The proposed development is recommended for both domestic and foreign research and industrial structures in the automotive industry for the purpose of further study and possible implementation in practice.
Keywords:
Semi-trailer, Tractor, Saddle device, Spring, Boot, Pneumatic cylinder, Frame, Compound axis, Rigidity, Folding
Cite this paper: E. V. Slivinsky, S. Y. Radin, The Device Excluding Folding of Links of the Heavy-Load Road Train at Braking, International Journal of Traffic and Transportation Engineering, Vol. 3 No. 1, 2014, pp. 8-19. doi: 10.5923/j.ijtte.20140301.02.
1. Introduction
One of the most effective ways to improve vehicle performance, quality and safety of transported goods, as well as reducing the cost of road transport is the use of articulated vehicles consisting of a tractor and trailer units, the main ones are the trailers and semi-trailers[1,2,3].Transport semi-trailers, both general and special purpose intended for the carriage of general, piece, bulk, liquid bulk cargo, as well as various agricultural products, and depending on the capacity of their perform uniaxial, biaxial, triaxial, etc. For the preparation of trains are equipped with the towing vehicle saddle device couplings, which are based on the ledges frame trailers. In addition, the units are equipped with terminals for connection of the brake system and electrical equipment for underwater towing vehicle systems.Fig. 1 shows a general view of train consisting of a towing vehicle and trailer used for transport of cargo[2]. It can be seen that the semi-trailer is a train link, which also performs the basic functions of the technological transportation process.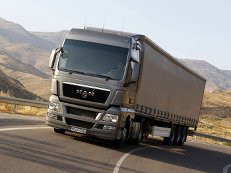 | Figure 1. General view of the heavy trains |
Frame made a ledge with a reference sheet and the kingpin, interacting with the truck towing the car. The frame consists of a spar rigidly interconnected cross members, which is different accessories. In the back of the frame is placed Suspension wheel axle, which is usually performed in a semi-elliptic leaf springs primary and secondary, which reduces the dynamic loads transmitted to the trailer frame and thereby increase the smooth running trains.All car trailers are made of welded frames, which are the basis for the platforms and bodies[1,2,4,7]. In front of the frame is made with a reference sheet ledge and kingpin, interacting with the truck towing the car. The frame consists of a spar rigidly interconnected cross members, which is different accessories. In the back of the frame is placed Suspension wheel axle, which is usually performed in a semi-elliptic leaf springs primary and secondary, which reduces the dynamic loads transmitted to the trailer frame and thereby increase the smooth running trains.The frame of a semi-trailer and the rear wheels on the suspension placed braking equipment, which includes air brake system connected to the air brake system of a car - truck. In the rear of the trailer to his frame usually tightly connected safety board, which is designed to protect the rear suspension components from damage in case of emergency, when the truck is in reverse, or when a tractor-trailer strikes at high speed, overtaking his car.Analysis of the structures described semi-train components, shows that one of the features is their tendency to folding, ie rapid change in the relative position of the car - truck and trailer units is generally in the braking mode. By contrast, modern construction trucks do not have these devices that would prevent the process of folding their links, and so the conditions often caused by the nature of the various emergency situations that entail not only in the subsequent significant costs for repair and restoration techniques, but injuries and people and, in some cases, death.One of the most important indicators of cars are their operational properties, which are characterized by the use of performance under certain conditions, allow us to estimate the extent to which the design is in these conditions[4,5]. This figure can not be obtained without the knowledge and use of the theory of motion of individual cars and trucks on the basis of which they can create new types and models. In theory, a single vehicle performance characteristics considered directly related to the movement of the car and the last ones are - dynamic, fuel economy, handling, stability, permeability and smoothness. Under the dynamic vehicle realize his property to transport cargo and passengers with the highest possible average speed, and the higher dynamism, the higher the performance. Dynamism of a single cars and trucks, above all, depends on their traction and braking characteristics. It is known[15] that the main driving force is the pulling force applied to the drive wheels of the car, and it arises from the interaction of the engine and the drive wheels and the road. For the resistance forces include friction in the transmission, the power of resistance of the road, the braking force and drag force. Evaluation traction usually produced by mechanical
and
. The resultant of all the forces exerted by the road on the vehicle wheel in the contact associated with the concept of road reaction which may be represented by three parts: normal Rz (it is the vector perpendicular to the road), the tangent Rx (its current vector in the plane of the road and the wheel plane ) and the transverse Ry in-plane perpendicular to the road wheel. The rotation of the wheel and move it on the road has also been associated with the concept of traction, which is determined depending on
, where MT - the torque on the wheel of the engine, r - the radius of the wheel. On the driven wheel traction is not PT = 0. On the side of the road impede the movement of the wheel rolling resistance force
and the resistance force of the road
, where i - the slope of the road. Typically, the expression in parentheses is called the coefficient of resistance of the road and represent ψ, then
, where G - the load on the wheel. In practical calculations to determine the nature of the vehicle at any time using the equation of the vehicle as follows:
where: PИ - inertia, PИ = -ma;PB - aerodynamic drag force.It is also known[3] that the safety of vehicular movement is closely linked with its braking equipment. In the event of failure of the braking equipment car loses its stability, and as he continues to move, it is clear that the traction and braking its properties are closely related. If we consider the case of braking only when exposed to the brake system (engine braking is possible), then the equation of motion it will become:РТОР + РД – РИ = 0,or as a result, this equation can be written as:φх G + ψG – δврmаз=0,where, m - mass of the vehicle;φx - the coefficient of traction;ψ - the drag coefficient of the road;аз - acceleration deceleration of the vehicle;G - dead weight of the vehicle;δвр -factor has been rotating mass of a car.The most important parameters of a mode of braking are time of braking and a brake way which can be determined respectively by dependences:tтор=V / аз(мах) – 0,5 ty; Sтор= V2 / 2 аз(мах),where ty - time during which the deceleration increases from zero (start of the brakes) to a maximum value;V - speed at which there is a braking beginning.Even more adverse picture of movement is stability loss when braking road train. As usually when braking the trailer is rolled on the car – the tractor, in the coupling device there is pushing force directed in case of drift of any of two links of the road train at an angle ξ to its longitudinal axis. This force creates the additional moment developing the road train, bringing to its folding.It is known that kinematic and power interaction of links of road trains and transfer of traction effort to semi-trailers is carried out via the basic coupling devices which details are mounted both on the car - the tractor, and on the semi-trailer[2,15].Basic coupling devices are applied to transportation of semi-trailers and are devices which perceive not only longitudinal loadings, but also vertical from a body weight of semi-trailers, carrying out at the same time functions of the rotary mechanism.Under the influence of dynamic loadings in details of basic coupling devices there is considerable tension in size which carry as strength, and fatigue character. The valid nature of dynamic interaction of links of the road train depends on many circumstances, to consider which fully it is impossible. In this regard at analytical researches of power loading of basic coupling devices use a number of the assumptions, allowing to concretize and simplify the solution of an objective. So, for example, for studying of dynamic interaction of the tractor with the semi-trailer by Schukin M. M.[15] offered the settlement scheme (fig. 2) and the mathematical model of a look is developed: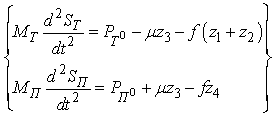 | (1) |
where,
and
- district traction forces on tractor and semi-trailer wheels;z1,z2,z4 - basic reactions on road train axes; z3 - vertical reaction in the basic coupling device;µ and f sliding friction respectively a coefficient in the basic coupling device and in a zone of contact of wheels the road.Analyzing the above it is visible that development of the technical means excluding folding of links of road trains at braking, and also calculation of their design data is an actual task.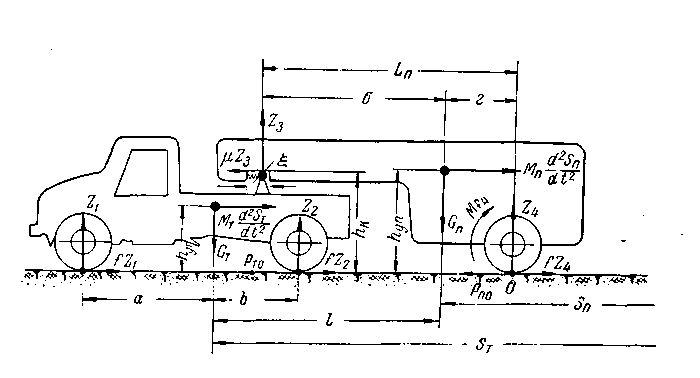 | Figure 2. Settlement scheme of the road train |
2. Research Objective
Practice of operation of heavy-load road trains shows that the design of the last is still far from perfect, and especially it is shown in high accident rate on roads. Considering it, and also above-mentioned materials, the purposes and problems of this research are:1. Development of the perspective technical solutions, allowing to warn, and in some cases and to exclude folding of links of road trains at their braking, change of modes of movement, and also other unpredictable situations arising on roads.2. Development of design models and methods for calculating the structural parameters of devices linked to heavy articulated trucks.3. Development of the computer program, allowing to determine rational parameters of the devices increasing longitudinal stability of road trains of a various design and appointment.
3. Research Technique
Given the above it in Elets State University I.A. Bunin for a number of years at the Department of Applied Mechanics and Engineering Graphics conducted research on "Dynamics, durability and reliability of transport, road-building and agricultural machinery, as well as industry-standard and non-standard equipment in relation to the Black Earth region of Russia" and one of its sections through the NIRS is a scientific field that is associated with the development of advanced technological solutions that increase driving stability trucks.The analysis of considerable number of bibliographic sources, and also domestic and foreign patents allowed to develop at the level of the invention the technical solution, allowing to prevent folding of links of the road train at its sharp braking (RU2368528).In fig. 3 the part of a longitudinal section of the road train in a sedelno-coupling device zone in the vertical plane and in fig. 4 a view of the sedelno-coupling device from above is shown.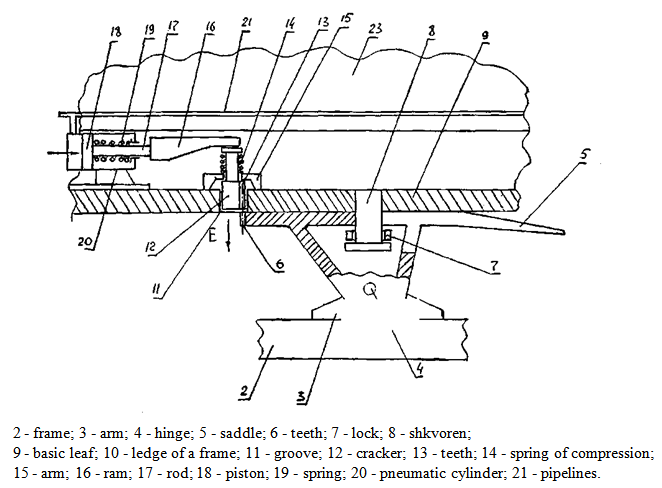 | Figure 3. Longitudinal section of the road train in a sedelno-coupling device zone |
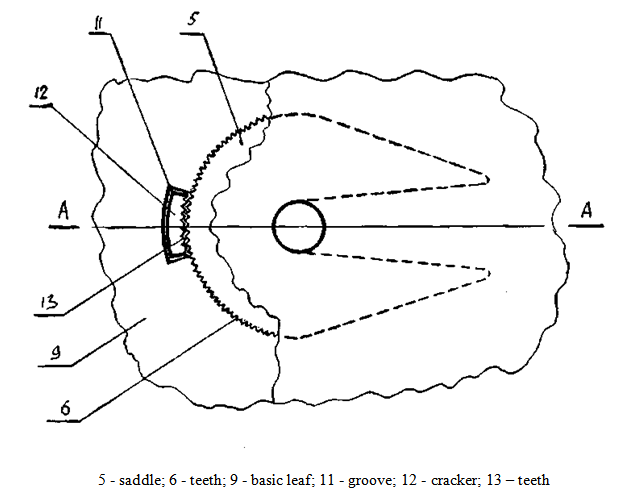 | Figure 4. Sedelno-coupling device top view |
The road train consists of the car tractor, on a frame 2 who is rigidly fixed an arm 3. The saddle 5 supplied on the face surface with a teeth 6 is attached to an arm 3 by means of the hinge 4. The saddle 5 by means of the lock 7 is interconnected with shkvorny 8, fixed on basic sheet 9 of a ledge of a frame 10. In basic sheet 9 the groove 11 is executed a bow-shaped form in which the cracker 12 is movably placed supplied with a teeth 13. The cracker 12 is sprung by a spring of compression 14 concerning an arm 15 fixed on basic sheet 9. The cracker 12 contacts to the ram 16 which has been rigidly attached to a rod 17 of piston 18, the compression sprung by a spring 19 placed in a pneumatic cylinder 20. The pneumatic cylinder 20 is attached to the pipeline 21 feeding brake cameras of a brake mechanism of wheels 22 semi-trailers.At road train movement with a forward speed of V the provision of details of the basic coupling device has such appearance as it is shown in drawings. In case of sharp braking for a number of reasons caused, for example, unevenness of creation of brake forces applied to wheels 22 semi-trailers possibly folding of links of the road train. However it doesn't occur for the following reason. As soon as the driver of the car will begin the braking process, the compressed air arrives in the pipeline 21, thus it at the same time will arrive in a pneumatic cylinder 20 which piston 18 will start moving on an arrow C, squeezing a spring of compression 19. But as the rod of the piston is supplied with the ram 16 with an inclined surface, the last, influencing a boot 12 will force it to squeeze a spring of compression 14 and will move in the direction of an arrow E, having contacted the teeth 13 with the teeth 6 executed on a saddle of the 5th car tractor. It will exclude possible angular turn of the semi-trailer caused by drift of its back part. Therefore, the car tractor and the semi-trailer in this case represents uniform "rigid" system in the longitudinal plane of the road train. After the driver will stop braking process, pressure in the pipeline 21 right there to become equal atmospheric and then the piston 18 under pressure of the squeezed spring of compression 19 comes back to a starting position, moving the ram 16 in the direction the antiput arrow C. At the same time and the boot 12 under the influence of elastic forces created by a spring of compression 14 will start moving in the direction the return to an arrow E uncoupling gearing formed by teeth 6 and 13. As a result road train links receive again freedom of angular movements from each other. Further the described processes can will repeat repeatedly.The settlement scheme (fig. 5) which represents two mass system
the mass of the semi-trailer and
mass of the car tractor is developed for calculation of the key kinematic and geometrical parameters of the offered device.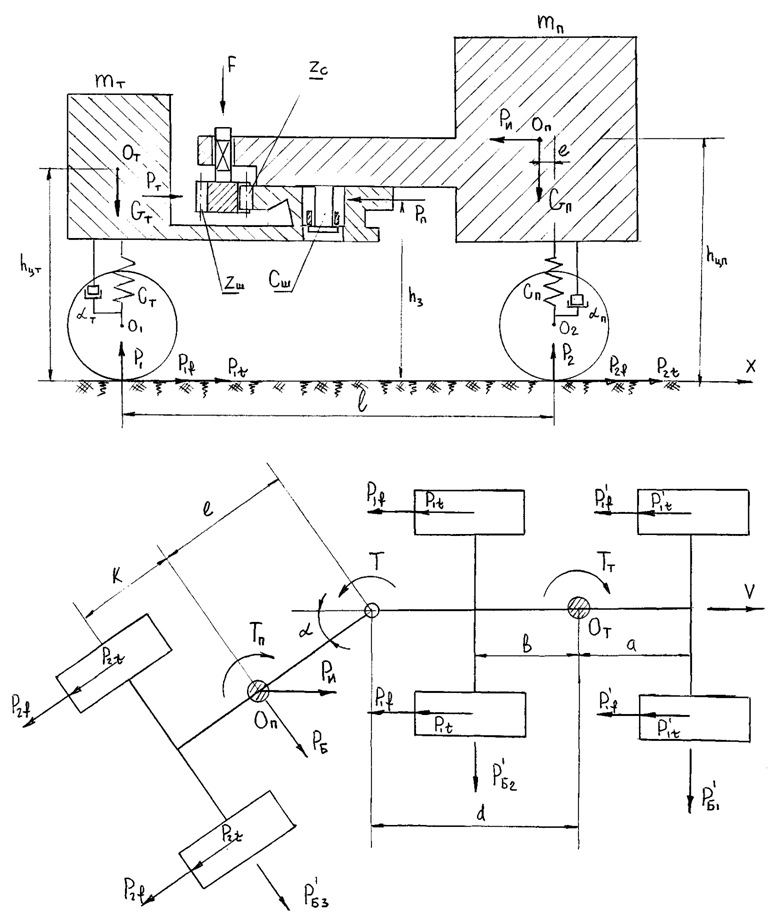 | Figure 5. Settlement scheme of the road train |
From action of static loadings
and
on back wheels of the car tractor there will be a reaction
, and on semi-trailer wheels –
. The specified masses are connected among themselves shkvorny with flexural rigidity
and the last is rigidly fixed on a semi-trailer frame. On a semi-trailer frame, movably in its vertical plane the gear Zш, boot interconnected with gear sector Zc executed on a saddle of the saddle device of the tractor is established. To a gear boot force F created by the mechanism of its management located on a trailer frame is applied. Reactions of communications
and
are attached to weight
and, operating on shkvoren in the horizontal plane located at height
from the plane of the road. When braking road train to the center of gravity of the semi-trailer inertial force
is applied, and in a zone of contact of wheels with the road arise from friction force
and braking force
. The centers of gravity Оп and От of masses
and
also are located respectively at height
and
from a road surface. It is obvious that vertical reactions
and
can be determined by dependences[3]:
Analyzing the system of equations, it is clear that if
and
, then their influence on the redistribution of loads on the wheels of the towing vehicle and trailer, if
then
(
can be positive or negative) then the run-up to the semi-trailer tractor units stretching or train. At the same time, it is clear that such a redistribution of loads is significantly affected by the magnitude
and its relation
with the greater the ratio, the wider the scope of congestion fifth-wheel towing vehicle and drive wheels. This phenomenon helps to block the rear wheels of the towing vehicle when braking[2,3]. In order to take into account the damping force train
, project the horizontal components of the forces on the axis XX, and then the equation of motion becomes:
Assuming that
and
, can be calculated according to the force of inertia:
.Determining the force of inertia can be calculated toothing on the strength of the stabilizing device. Here is an example of such a criterion for calculating road train consisting of a towing vehicle MAZ-5432 total weight
= 7050 kg and a car trailer container truck MAZ-9397 model with
= 26800 kg. At the same time as the initial data we adopt the following measures using the data of[1].
- distance from the road surface to the center of mass of the towing vehicle, 1,2 m;
- distance from the road surface to the center of gravity of the semitrailer, 1,8 m;
- distance from the road surface to the horizontal plane of the longitudinal forces
and
;
- distance from center of gravity of the semitrailer to the vertical symmetry axis of the rear wheels of the semitrailer suspension, 3,2 m;
- static vertical reaction to the rear wheels of the tractor trailer 88000 N and from the tractor 24400 N,
= 88000 + 24400 = 112400 N;
- static vertical reaction of rear-wheel trailer, P2 = 180000 N;
- rolling resistance rear wheels truck
= 11240 ∙ 0,02 = 2248 N;
- rolling resistance wheels of the semitrailer
= 18000 ∙ 0,02 = 3600 N.Suppose[2,3] that the inhibition occurs when trains its speed of 40 km/h (such a velocity is set to GOST 22895-77 Limits vehicle braking distance), the braking force and
will be equal
and
, where
the coefficient traction is assumed to be 0,5[3] when moving train on dry roads with asphalt concrete pavement. Then the force of inertia
is determined by:
We compute for a given force
acceleration deceleration
.Then the stopping distance trains will be:
where
- the brake actuator response time
[3].It is known[ 2,3 ] that the stability of the motion train evaluated from the size of the critical speed, which , in practice , in the case of the semi-trailer skidding when braking is quite low and averages
. When braking force acting in the plane of the road are large and at the same time are different in magnitude for each of the wheels, in this case a turning moment which causes a reversal in semi heading angle ψ. Since in our example, made the speed of movement
, it is possible for instability when braking trains. Therefore, to ensure reliable stabilization of the semi-trailer towing vehicle relative to define the torque T arising in connection gear when subjected to forces of inertia
= 120118 N braking trains. We use the recommendations in[3], according to which in accordance with GOST 22895-77 in order to ensure the safety of folding angle α trailer braking must not exceed 150, therefore, РБ lateral force applied to the center of gravity of the ОП (Fig. 5) in this case is equal to РБ = РИ cos(900-α) = 12011,8· cos750 = 12011,8·0,2588 = 31086 N. Given that the distance between the center of gravity of the semi-trailer to the teeth , according to the nameplate data on the semi-trailer models MAZ - 9397 is 9350 mm[1] torque of the tooth will be Т = РБ ·е = 3108,6·9,350 = 290654 N·m. We define a module gearing the known dependence of the strength condition of the teeth in bending:
where K - coefficient taking into account the conditions of the transfer;γи – coefficient taking into account the dust and corrosive environment;Yу - the shape factor of the tooth;[σ0] - flexural endurance limit;Analyzing the above it is clear that the practice of folding units can train at its various speeds ranging from 20 km/h or more and actions on the brake forces are in a very wide range. On this basis in order to enhance the operational capabilities of the proposed device, which eliminates folding, filling the air cylinder control locking device cooperating with a toothed sector performed in the seat of the saddle device of the truck must be carried out as quickly as possible to engage the teeth occurred at angles of rotation of the semi-trailer is not greater than 50. Therefore it is constructive choose a small inner diameter, for example equal to 30 mm. At the same time, for the rational selection of the geometric characteristics of the air cylinder requires a wide range of testing full-scale models in operational conditions, and only then finally justify the optimal geometric and kinematic settings for each train consisting of different models of trucks and automobile trailers.At the same time, the analysis of a large number of bibliographic sources, as well as domestic and foreign patents (RU2009932, SU1169872, DE4429986, WO90/03297, SU1172811, SU1230911, US5620195, RU2175927, US3825089, etc.) led to the development of inventions at a number of technical solutions, help prevent folding units train when braking (RU2255018, RU2254246, RU2255017). Let us consider the design of such devices attached to trucks.So Pat RU2255018 described heavy-truck (Fig. 6), consisting of a tractor 1, in frame 2 is fixed saddle device 3. Saddle device 3 is interconnected with pivot 4, and lockable lock 5 slidably disposed in the longitudinal groove 6 formed in the supporting plate 7 and frame 8 of semi-trailer 9. Pivot 4 is connected via hinge 10 with the cylinder 11 and its rod 12 as by a hinge 13 fixed to the frame 8 of the semi-trailer 9. The cylinder 1 via a conduit 14 connected to conduit 15, the feed brake cylinders 16 of wheels 17 of semi-trailer 9. In the groove 6 between the frame 8 and the pivot 4 is placed a compression spring 18 and the rod 12 is provided with a piston 19.When driving train according to arrow B, and its abrupt deceleration occurs folding trailer 9 relative to the towing vehicle 1 as shown in Figure 6, but the proposed design does not happen for the following reason. As soon as the driver of the tractor 1 will make a sharp slowdown, semitrailer tractor 9 will have one as the longitudinal force inertial force P applied and the angular momentum M, caused, for example, uneven brake force applied to the braking devices of wheels 17 semitrailer 9, the influence of micro Profile the road, the difference tire pressure wheels 17, etc. At this time, under the action of the force P pivot 4 moves to the groove 6 by the arrow C, elastically deforming the compression spring 18 while pulling the rotation into the same cylinder 11. Since the conduit 15, a pressure air (such trailer braking process is widely known in the art), exerted by the arrow Д to the brake chamber 16 and the cylinder 1 moves in the arrow C, then at a certain time due to immobility rod 12 and therefore and the piston 19, the latter blocked by conduit 14 (as shown in Figure 6) engages with the left cylinder space above the piston 11 and the compressed air from conduit 15 enters this said cavity. At this time, the compression spring 18 is fully compressed and then the compressed air piston 19 will move together with the rod 12 by the arrow E, as well as the rod 13 is connected to frame 8 of semitrailer 9, the latter will move into the same direction. This movement promotes the trailer of 'waste' it from the towing vehicle 1 in the direction opposite to the movement of trains, which will create conditions for reducing torque M as the wheels 17 inhibited their brake chambers 16 as a "stretched" road train , and, consequently , the rotation angle α of semitrailer 9 relative to the tractor 1 significantly reduced. Once the truck stops the movement and the driver will translate the tractor brake release mode, the pipeline 15 is connected to the atmosphere (such a process is also well known in the art), and in the left cylinder chamber 11, the pressure will disappear. Once this occurs, cylinder 11 begins to move under the action of a spring 18 according to arrow F, as well as brake chamber 16 is also connected with the atmosphere and the trailer wheels 17 disinhibited were then semi 9 moving on wheels 17 return to the original position. Such a phenomenon will occur in cases where a sharp braking or emergency train will occur at the location of the tractor 1 and semitrailer 9 on one longitudinal axis of symmetry, i.e. when angle α = 0. In this case, the longitudinal stresses resulting from exposure tractor 1 to the semitrailer 9 will be damped as a compression spring 18 and the cylinder 11, as was the case in describing the operation of the apparatus above.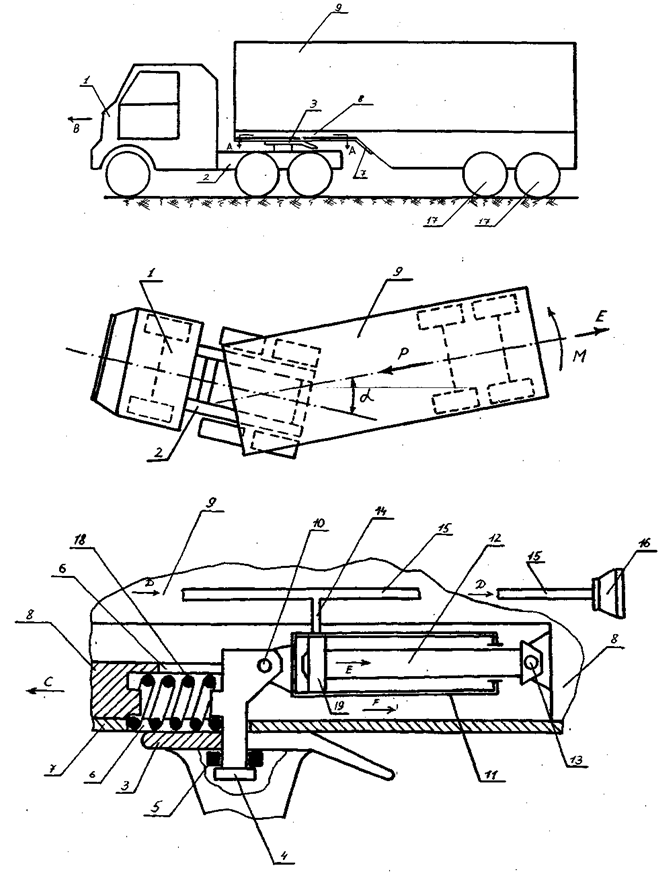 | Figure 6. The device according to the patent RU2255018 the excluding folding of links of the road train when braking |
Another solution (RU2554246), excluding storage units train (Fig. 7) is tied to a car trailer, which consists of a frame 1, and her body set 2. The frame 1 is in contact with the saddle device 3 of truck 4. The frame 1 is fixed thrust brackets 5 of spring 6 which is movably placed on the pins 7 is rigidly attached to the plates 8. Plates 8 are secured in the areas axles 9 of wheels 10. Each of the sections 9 is provided with a bracket axle 11 in which the connecting pins 12 are located, arranged in the grooves 13, formed in the plug 14 of rod 15 of the air cylinder 16. On rod 15 is piston 17, spring-loaded compression spring 18 relative to the air cylinder 16, and the latter by a hinge 19 mounted on the thrust arm 20 is rigidly attached to the frame 1. The ends of the axle sections 9 respectively have a groove 21 and projection 22 which are curved. The cylinder 16 is connected by the brake pipe 23 with cameras braking device of wheels 10.When traveling by train in the direction by the arrow B may be a situation when the driver of the towing vehicle 4 will brake sharply. In this case, simultaneously with the supply of compressed air to the brake chambers (on fig. pneumatic brake system and its parts are not shown) as is the case in the prior art semi- wheel braking device 10 is then triggered simultaneously and braking the towing vehicle 4 and trailer. However, due to the forces of inertia trailer puts additional pressure on the towing truck 4 by the arrow C. Then, and perhaps folding train links. But this does not happen for the following reason. Simultaneously with the supply of compressed air to the brake chambers latter also receives the arrow Д through the conduit 23 into the cylinder 16, which provides movement of the piston 17 by the arrow E with the compression spring 18. Since the rod 15 of piston 17 connected by the connecting pins 12 with brackets 11 and are rigidly secured to the axle parts 9, the latter will turn the corner of the arrows F, occupying a position as shown in figure 7. Of course, in practice, an angular rotation axes and portions 9 and the light can be from 3° to 5°, and therefore, first, the axle portions 9 can not escape from the interface with each other, since the projection 22 is fixed to the groove 21 and the secondly, the spring 6 will receive the linear displacement of the amount Δl, and the angular turning on fingers 7, occupying a position as shown in figure 5. Corner portions rotation axis 9 and will turn with them the wheels 10, which, being rotated at an angle β to the longitudinal axis of the trailer, the additional resistance will move in conjunction with the locked wheels 10 of trailer air brake system. Consequently, semi will resist movement in the direction opposite to the arrow C, which eliminate its "drift" relative to the towing vehicle 4 to the left or right side of the latter. Once braking ceases and the compressed air will go out to the atmosphere. Simultaneously, via line 23, the latter will go out in a direction opposite to the arrow Д. The pressure drop in the compressed air cylinder 16 provides the action of the compressed spring 18 returning the piston 17 and rod 15 to its original position, which creates conditions for the wheels 10 return to the position when the angle α = 0 and the angle β = 0. Then train can be carried out subsequent motion. The process described above may be repeated many times.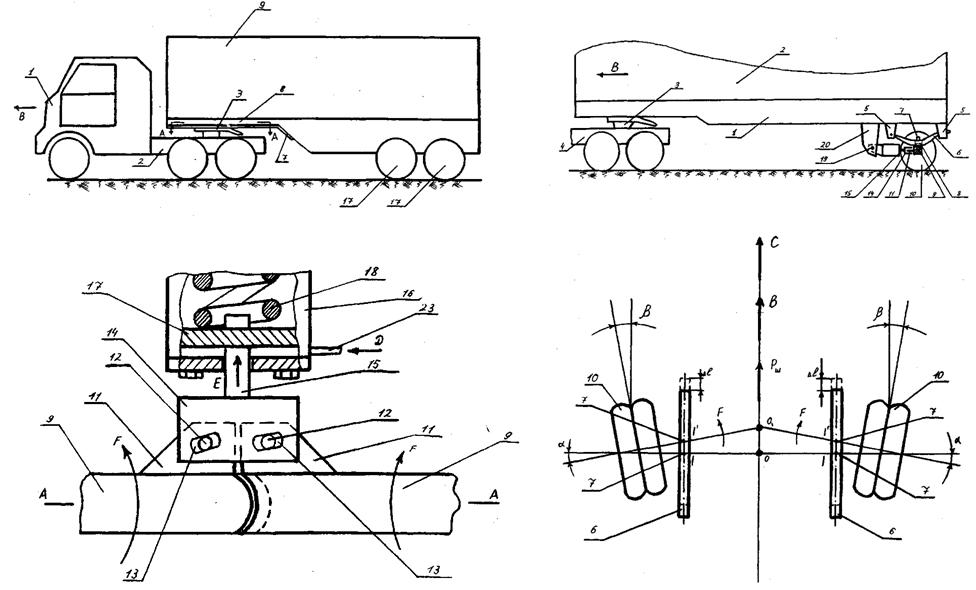 | Figure 7. The device according to the patent RU2554246 the excluding folding of links of the road train when braking |
The third solution (RU2255017), as shown in Fig.8 is a combination consisting of the towing vehicle 1, the frame 2 is set saddle device 3, interconnected with the backsheet 4 of frame 5 of semitrailer 6. On the supporting plate 4 is rigidly fixed pivot 7 through hole 8 provided with a shut-off valve 9. Shut-off valve 9 is in contact with the shut-off valve 10 placed in the cup 11, which is installed in the saddle device 3, a sealing member 12 and is biased by a compression spring 13 relative to the saddle device 3. Cup 11 via a conduit 14 connected to air cylinder 15. On the exterior of the saddle device 3 side of the support plate 4 of frame 5 of trailer 6 in the guide 16 is movably mounted slide 17, wherein the semi-elliptical shape formed slot 18 connected by a flexible conduit 19 to a conduit 20 connected to the brake chambers 21 of wheels 22 of semitrailer 6. The slider 17 is biased on one side by a compression spring 23 on the guide 16 and the other pivotally connected to the rod 24 of air cylinder 25 which is also pivotally mounted on the same rail 16. The air cylinder 25 via a conduit 26 connected to conduit 20. Pipe 20 and air conduit 27 of air cylinder 15 connected to the air distributor 28 which, through manual control valve 29 is connected to a conduit 30 connected to conduit 31 of air brake system of the towing vehicle 1. Semi- 6 has a supporting device 32. Pivot 7 is fixed on the saddle device 3 with lock 33.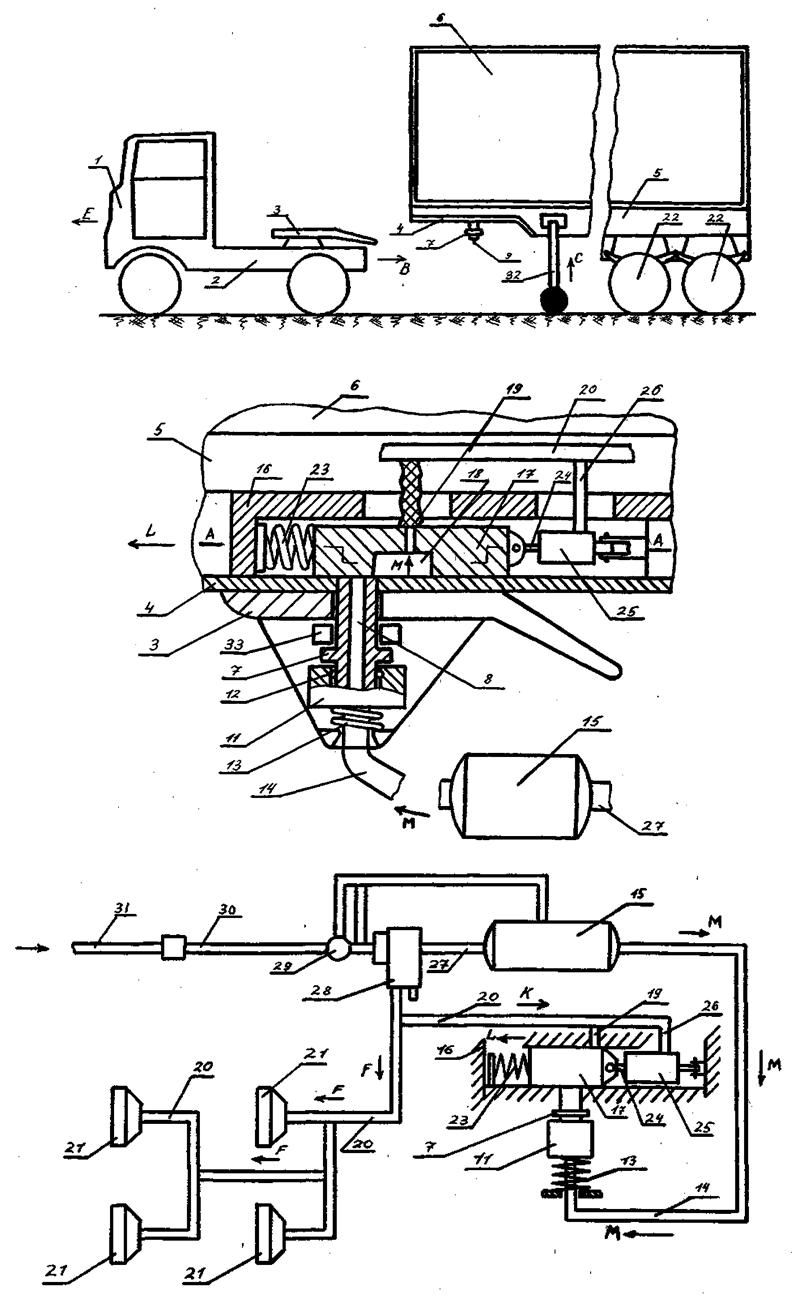 | Figure 8. The device according to the patent RU2255017 the excluding folding of links of the road train when braking |
Tractive connection to the towing vehicle 1 with the semitrailer 6 which is mounted on the supporting device 32, as shown in fig. 8, the towing vehicle 1 is moved according to arrow B, and the vertical axis as the saddle device 3 coincides with the vertical axis of the pivot 7, commonly known in the art bearing device 32 raises the arrow C, whereby semi 6 its backsheet 4 is located on the surface of the saddle device 2, and pivot 7 enters into the cup 11 and occupies a position as shown in fig. 8. Such conjugation pivot 7 and cup 11 simultaneous elastic deformation of the compression spring 13, which provides a tight connection between these components and the connection hole 8 in the cavity conduit 14 as shut-off valves 9 and 10 to retract the arrows Д. Once this happens, compressed air from the air cylinder 15 to the line 14 will fill the hole 8 of pivot 7. Thereafter, widely known in the art lock pin 33 is fixed the pivot 7 relative to the saddle device 3. Thereafter manually connect conduits 31 and 30, which eventually brings air brake system of the towing vehicle 1 (in the figure it is not shown) such trailer 6. Subsequently the rectilinear movement of trains along arrow E and a situation arises in which it is necessary to brake sharply train, commonly known in the art the driver of the towing vehicle 1 decreases the air pressure in its air brake system, which also contributes to reducing the air pressure in conduit 31 and therefore, in line 30. The pressure drop in the air conduit 30 facilitates its side lap air distributor 28 from the atmosphere (the process of air brake system semi widely known in the art) and the entry of compressed air from the air cylinder 15 through the diffuser 28 into the conduit 20 by the arrow F and further to the brake chamber 21, and the arrow K through the conduit 26 into the pneumatic cylinder 25. Since there is an abrupt braking trains, under the action of inertial forces on the slider 17 moves in the direction L of the guide 16, elastically deforming the compression spring 23, which ultimately provides a compound of the through hole 8 with the cavity recess 18. Such a combination of these elements allows the compressed air in the air cylinder 15, the arrow M to enter into the flexible conduit 19 and hence in the duct 20. The increased air pressure in the conduit 20 will create a greater braking force brake chambers 21, considerably more than the force of the brake chambers of the towing vehicle 1. Consequently, the rear wheels are locked trailer 6, which will create a condition can not be "rolling" on his car - tractor 1, then there will be excluded knifing. It should be noted that the slider 17, the termination or attenuation of action on it of inertia during braking trains can not return to its original position, as the cylinder 25 through conduit 26 connecting it to conduit 20 will force the piston precluding its movement according to arrow N. As soon as the driver of the tractor 1 releases the pedal brake control valve, the pressure of the compressed air in the lines 31 and 30 instantly increases, which permits operation of the air diffuser 28, which connects the line 20 to the atmosphere. This connection leads to the release of the brakes and release of compressed air from the cylinder cavity 25 and through conduits 26 and 20 and then under the action of compression spring 23, the slider 17 moves in a direction opposite arrow L, blocking the through hole 8 of pivot 7, the starting position is.When operating the train is also possible abrupt braking when driving in his path curve. In this case, the slider 17 as in the first case by the action of inertial forces to move the arrow L, and that creates the conditions for locking the rear wheels 22 of the semi-trailer 6, and, therefore, would eliminate storage units trains. For given normal operating conditions braking trains (no hard braking) in straights and in curves, movement of the slide 17 is not due to selection of the elastic characteristics of the compression spring 23 and the force exerted by the cylinder 25 such that they would provide a fixed position slide 17 when subjected to a small value by inertia forces. When disconnection units train support apparatus 32 is moved in the direction opposite the arrow C, thus dissolving the lock 33, which eventually promotes the release pivot 7 of the cup 11 and, as soon as this happens, the stop valves 9 and 10 overlap the delivery of compressed air from conduit 14 the through hole 8 and the atmosphere in general. After that the towing vehicle 1 is removed from the trailer 6 relative to each other which occupy a position as shown in fig. 8. Next foregoing process can be repeated many times.On all three of the development allowed the calculations to justify their design parameters, which ultimately allows us to recommend them to both domestic and foreign research institutes, engineering and production structures of the automotive industry to further study and refinement of the proposed device for possible introduction in his practice.
4. Results
Based on the above, the following conclusions and suggestions:1. The analysis of both domestic and foreign construction trucks shows that the latter have a significant disadvantage that in case of sudden braking or service at different speeds, they have a high ability to folding. This phenomenon is dangerous not only for the trains, but also for other vehicles moving after him or meet him. Experience in operation of motor trains shows that the consequences of accidents that occur on the roads for this reason, make up more than 5% of all accidents recorded by the world practice.2. Given the above us on the level of inventions (RU2255017, RU2254246, RU2255018) developed technical solutions devices allowing prevent folding units trains when they move at different speeds and in particular when they are exploited in the autumn and winter time.3. To establish a rational geometric and kinematic parameters of one of these devices developed a physical model and proposed a method for their calculation. Thus, our calculations as applied to train consisting of car MAZ-6422 trailer and container models MAZ-9389, showed that as the elastic coupling can be used compression spring made of steel bar Steel 602S 22mm diameter with a work force and rigidity, working together with the pneumatic cylinder. To automate the calculations developed a computer program in the language of Delphi, which allows to calculate these parameters for different designs trains.4. Results of the study are recommended for domestic and foreign transport companies, automobile industry, science and engineering, both domestic and foreign entities operating in the automotive industry for the study and analysis of the proposed designs for possible further put them into practice.
References
[1] | A short car handbook. 10th ed. rev. and add. - Moscow: Transport, 1983. - 220 p. |
[2] | Vysotsky M.S. etc. Car and tractor trailers. M. Mashgiz, 1962. – 161 p. |
[3] | Zakin Ya.Kh. Car trains, development of vehicle design, Proceedings of the NAMI, vol. 12. Mashgiz, 1955. |
[4] | Chudakov E.A. The theory of the car. M. Mashgiz. 1950. – 272 p. |
[5] | Theory and design of the car. Tutorial for motor colleges /V.A. Ilarionov, etc. - M.: Mechanical Engineering, 1985. – 368 p. |
[6] | RU 2009932 C1, 30.03.1994 |
[7] | SU 1169874 A, 30.07.1985 |
[8] | DE 4429986 A1, 18.05.1995 |
[9] | WO 90/ 03297 , 05.04.1990 |
[10] | SU 1172811 A1, 15.08.1985 |
[11] | SU1230977 A1, 15.05.1986 |
[12] | US 5620195 A1, 15.04.1997 |
[13] | RU 2175927 C1, 20.11.2001 |
[14] | US 3825089 , 23.07.1974 |
[15] | Shchukin M.M. Hitches cars and trucks . M-L.: Mashgiz, 1961. – 207 p. |
[16] | Smirnov G.A. The theory of the movement of wheeled vehicles. Textbook for students of mechanical engineering specials universities - 2nd ed., ext. and rev. - M.: Mechanical Engineering, 1990. – 352 p. |
[17] | Ellis D.R. Handling. Mashinostroyeniye. 1975 – 216 p. |
[18] | Glushchenko A.D., Slivinskiy E.V. Dynamics and strength of the transport system for the transport of freight cars. Publishing house Fan, Tashkent. 1988. – 116 p. |
[19] | Ponamarev S.D., Andreeva L.E. The calculation of the elastic elements of machines and devices. Mashinostroyeniye 1980. – 326 p. |
[20] | Rothenberg R.V. Car suspension Mashinostroyeniye 1972. – 392 p. |
[21] | Bukharin N.A. Brakes Car L-M.: Mashgiz. 1950. – 135 p. |
[22] | Zakin Ya.Kh. Applied theory of train movement. M.: Transport 1967. - 215 p. |
[23] | Rozanov V.G. Braking of the car and the train. M.: Mashinostroyeniye, 1964. – 276 p. |
[24] | Slivinskiy E.V., Zelyh A.N. Calculation of basic parameters of devices that exclude folding car trains on the computer. Computer Science: Concepts, current state and prospects for development. Materials Interuniversity scientific-practical conference. Issue 3. Elec 2007. – 89 p. |