Yehia Abdel-Nasser1, Jasem Alrajhi1, Mohsen Alardhi1, Khalid Alkhulaifi2
1Department of Automotive and Marine, The Public Authority for Applied Education and Training, Kuwait (College of Technological Studies)
2Department of Power and Air Conditioning, The Public Authority for Applied Education and Training, Kuwait (College of Technological Studies)
Correspondence to: Jasem Alrajhi, Department of Automotive and Marine, The Public Authority for Applied Education and Training, Kuwait (College of Technological Studies).
Email: |  |
Copyright © 2012 Scientific & Academic Publishing. All Rights Reserved.
Abstract
Kuwait suffers from severe and fatal crashes that result from vehicles collision with street columns such as lighting columns. These crashes cause extremely high impact forces and deformation on the frontal area of the car. The objective of this study is to investigate the effect of vehicle frontal crash with lighting columns on vehicle deformation and deceleration after impact using finite element model simulation. In this research, Abaqus explicit code is used to numerically simulate the crash of the vehicle with the present lighting columns in Kuwait using a new suggested material. The acceleration, contact force and the energy required to deform the frontal area of the vehicle are all investigated. It was found that the lighting columns with the new suggested material have impact properties capable of decelerating the vehicle and absorbs high energy during impact.
Keywords:
FEM, Crash Simulation, Lighting Columns, Kuwait, Acceleration
Cite this paper: Yehia Abdel-Nasser, Jasem Alrajhi, Mohsen Alardhi, Khalid Alkhulaifi, Frontal Crash Simulation of Vehicles Against Lighting Columns in Kuwait Using FEM, International Journal of Traffic and Transportation Engineering, Vol. 2 No. 5, 2013, pp. 101-105. doi: 10.5923/j.ijtte.20130205.02.
1. Introduction
In Kuwait there are a lot of utility poles such as lighting columns and street signs. These may cause many severe and fatal injuries that result from vehicles colliding with these utility poles. The existing lighting columns are made from steel with high yield strength. The characteristics of the lighting columns material have a high static strength and low absorbing energy which causes the vehicle to absorb most of the kinetic energy resulted from the crash. This causes an extremely high impact forces on such small area of the car and in turn causes high risk of injury to the vehicle occupants. Although modern cars are made with composite materials that can absorb most of the impact energy, however, the risk of injury is still high. A new design of lighting columns would absorb dramatically most of the energy that the vehicle absorbs during impact. Lighting columns are made from a variety of composite materials[1]. Passive safety lighting columns are suggested to reduce possibility of injury crash[2]. Many companies and organizations have carried out studies to improve passive safety of lighting columns[3]. Further research indicates the importance of material selection such as Fibre-reinforced polymer composite materials[4]. Valin et al proposed anchorage system of non-energy absorbing system[5]. It allows the vehicle to continue moving after impact with a limited reduction in speed. Elmarakbi[6] developed five different support structures including a brake away base supported with anchor bolts fixed in a concrete base.Computer simulation of vehicle collisions has improved significantly over the past few years. Polytechnic university computational mechanics laboratory performed crash test simulations for several types of composite columns at different speed values[7]. Frontal collisions using various finite element models (FEM) are used to perform contact–impact nonlinear dynamic analysis of lighting columns with vehicle[9]. FEM crash simulations have been primarily focused on the vehicle models and their crash characteristics. In this research, Abaqus explicit code is used to numerically simulate frontal crash of the vehicle with lighting columns. The main parameters influencing the deceleration and deformation of the vehicle such as column shell thickness, outer diameter and material properties are all investigated. The acceleration, deformed energy and contact force for each model after impact are calculated using the FEM. The results and trends of the analysis are all presented in this work.
2. Model of Analysis by FEM
This research addresses a numerical simulation of vehicle impact with lighting columns using FEM ABAQUS/Explicit Version 6.9-4 code. The FEM simulation encompasses a number of considerations which should be given an appropriate attention. These considerations are the selection of a mesh and type of element which should be made of fine mesh especially at the frontal contact areas to acquire accurate results and to represent real simulation during impact. The vehicle and lighting columns are modelled using four nodes thin shell double curved elements (S4R) where S refers to shell element, 4 refers to the number of nodes in each element and R is the reduced integration. About 6200 elements have been generated in the entire model in which the smallest size of the element is about 0.01 m at the front contact area (bumper–radiators–hood and front doors). Coarse mesh may be applied for areas located far from collision region to reduce CPU time. The contact surface during collision and elements based surface are applied to define contact region.
3. The Case Study
Today's standard lighting column has a length of 8 meters with diameters at base and top of 200mm and 100mm respectively while shell thickness is 4mm. The selected dimension is a typical case of a lighting column in Kuwait City. The column material has yield strength of 355 N/mm2 with isotropic hardening with strength of 490 N/mm2 and plastic strain of 0.025. It is assumed that the column dimension has sufficient static strength against other environmental loads. The lighting column is assumed to be fixed at its base while the vehicle is free to move at a right angle with a translational velocity along the -y-axis of 14 m/sec. The velocity is applied at all nodes of the vehicle. Point masses are assumed to represent masses of mechanical and transmission components. In this study the vehicle weight is not considered as a variable. Therefore, a vehicle gross weight of 980 kg is used in this analysis. The main investigation of this work is to study the effect of lighting columns materials on deformation and energy absorption of vehicles during impact. During the crash, two stages occur simultaneously. The first stage results in maximum peak of deceleration of the vehicle while the second stage is passing with low values of deceleration up to vehicle stop. The first phase of impact is mostly considered because of its importance. Therefore, a partial dynamical explicit analysis up to a time 0.05 sec is used.
4. Analysis of Impact Results
4.1. Absorbing Energy of Vehicle
Figure 1 shows undeformed and deformed shape of vehicle crash when using standard lighting column.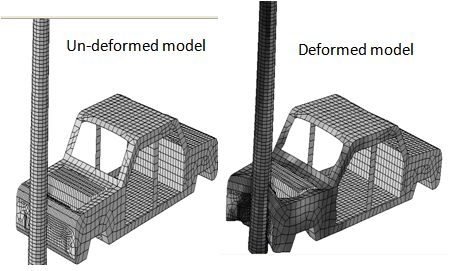 | Figure 1. FEM of impact vehicle with the present lighting column |
It is apparent that the existing column absorbs small energy while small deformation has happened to the column. The remaining impact energy is absorbed by the frontal area of the vehicle. Various analyses are carried out by using a new material property and different shell thicknesses for the lighting column. Light columns thicknesses of 4, 3, and 2mm respectively are used in this work. History of deformations of the lighting column is shown in Figures 2 and 3.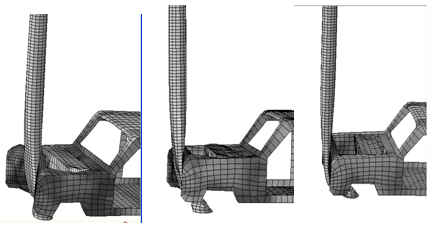 | Figure 2. Deformation history of the lighting column made from a new material |
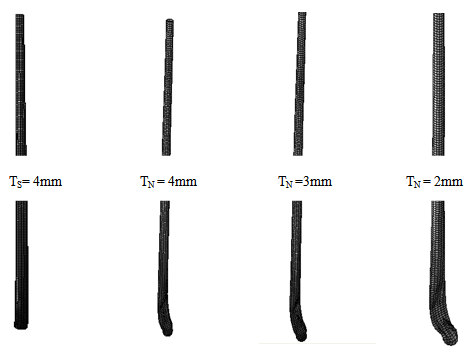 | Figure 3. Deformation of the lighting column with different shell thicknesses |
It is noticed that the crash against the lighting column using the new suggested material shows high deformation while small deformation occurred at the frontal area of the vehicle. The lighting column with the small shell thickness shows high absorbing energy which results in more safety for the vehicle occupant. Figure 4 shows the deformed energy versus time. It is clear that vehicle crash with the present standard light column causes the highest vehicle deformation while the new material absorbs more energy than the present column. At collision, the velocity of the vehicle reaches zero with the present column while it continue running with a small reduction of speed when colliding with the new lighting columns as shown in Figure 5.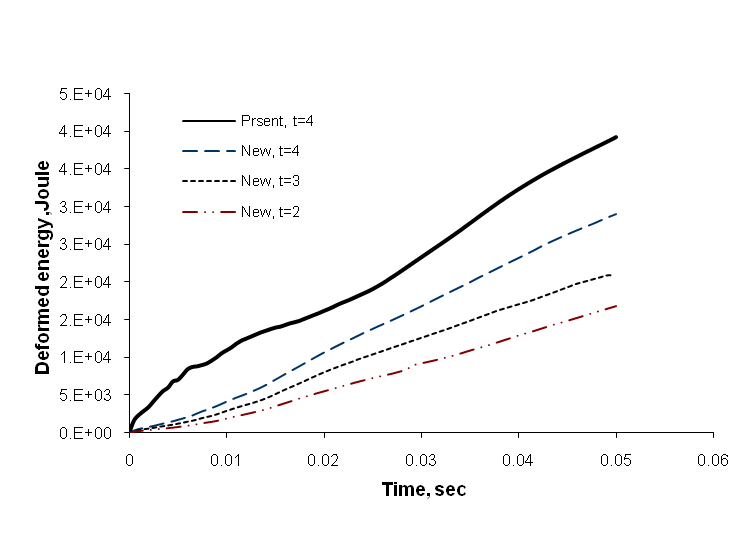 | Figure 4. Deformed energy vs. time |
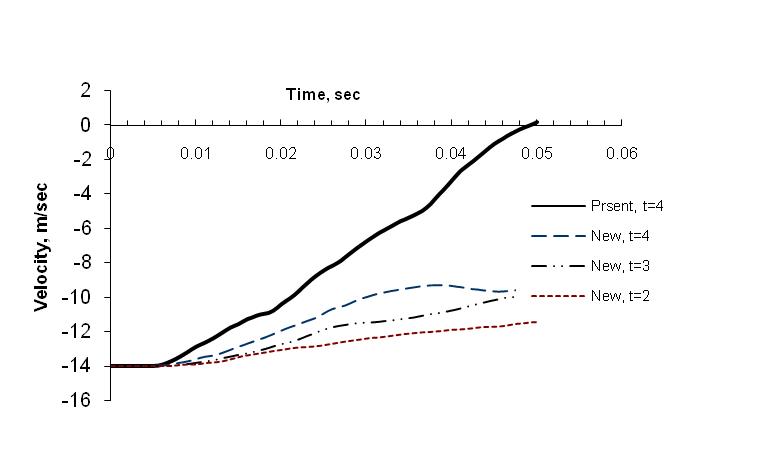 | Figure 5. Vehicle velocity vs. time |
4.2. Acceleration of Vehicles
Figure 6 shows vehicle acceleration versus time relationship for the present and new lighting columns. The acceleration is measured at the frontal area of the vehicle. It is shown that the new material of light column decelerated the vehicle. The column with the smallest thickness shows maximum deceleration than other lighting columns. These results has the same trend with other numerical results[10], however, the FEM here is a bit rigid than it should be. The peak of the acceleration value has happened at a time less than expected. This is because the model lacks of details and additional material parts in the interior of the vehicle. Figure 7 shows contact force versus time for all models. The force-time relationship has the same behavior for the new material lighting. Two peaks of the force value for the behaviour of present lighting column.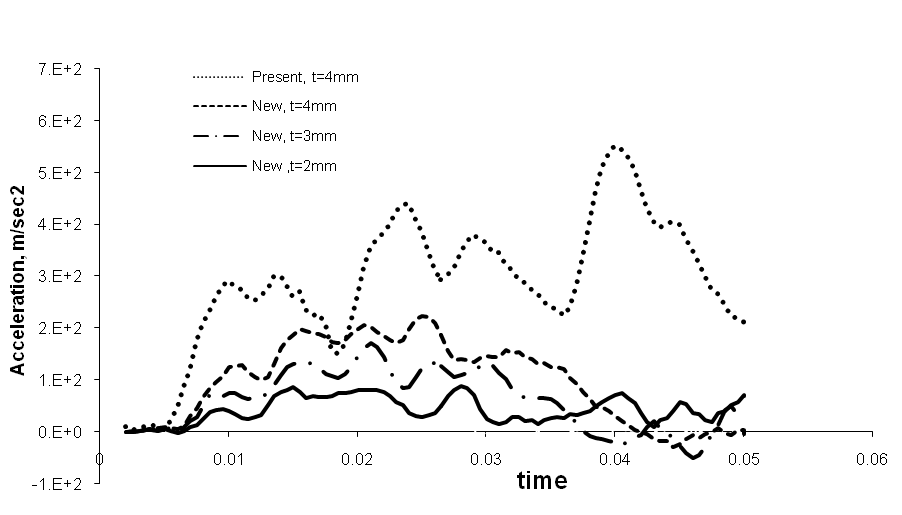 | Figure 6. Acceleration versus time |
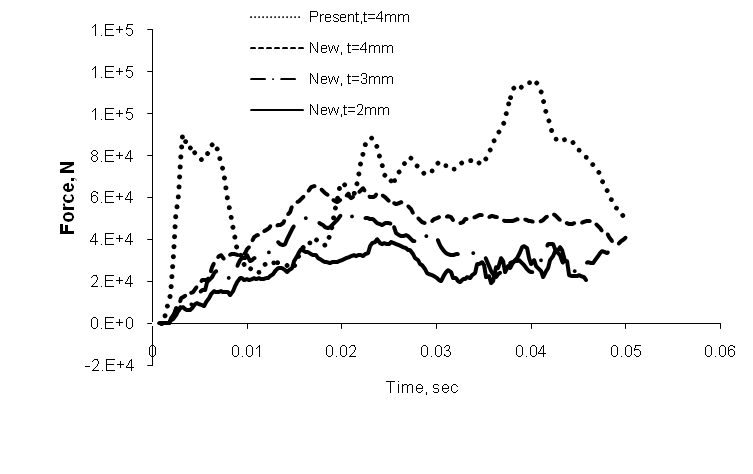 | Figure 7. Force versus time |
5. Conclusions
The objective of this study was to investigate the effect of vehicle frontal crash with lighting columns on vehicle deformation and deceleration after impact using finite element model simulation. FEM Abaqus explicit code was used to numerically simulate the crash of the vehicle with the present lighting columns in Kuwait using existing and new suggested material. The acceleration, contact force and the energy required to deform the frontal area of the vehicle were all investigated. It was found that the present lighting column with high yield strength of material absorbs little impact energy which could results in high injury risk. On the other hand, the lighting column made from new material decelerated the vehicle and absorbed higher impact energy which is expected to increase the safety of vehicle occupants. The peak of the acceleration value happened at a time less than expected due to the fact that the model lacks of details and additional material parts in the interior of the vehicle. The validation of this study need to be checked with real crash test using different vehicles weights and velocities.
ACKNOWLEDGEMENTS
This research was carried out as a part of (research No. TS-08-06) of PAAET (The Public Authority for Applied Education and Training, Kuwait). The authors are grateful for PAAET for their financial support.
References
[1] | G. L. Williams, J. V. Kennedy, J. A. Carrol and J. R. Beesley, "The use of passively Safe Sign Post and Lighting Columns", Publ. Report PPR342, Transportation Research laboratory, 2008. |
[2] | B. Ferrer, S.Tvorra, E. Segovia and R. Irles, "Impact Load in Parking Steel Column", COMPDYN Conference 2009, Greece. |
[3] | B. Pipkorn and J. Haland, "Proposed Variables Stiffness of Vehicle Longitudinal Frontal Members", IJ Crash Vol.10No6, pp.603-608, 2005. |
[4] | S. KOkkula, O. Hopperstad, O. Lademo, T. Berstad and M. Langseth, "Offset Impact Behaviour of Bumper Beam-Longitudinal Systems: Numerical Simulations", IJ CrashVol.11No.4 pp.317-336, 2006. |
[5] | M. Poanco ,S. Kellas and K. Jackson, "Evaluation of Material Models within LS-DYNA for a Kevlar/Epoxy Composite Honeycomb”, Report by the National Aeronautics and Space Administration |
[6] | J. Vlian, A. Segade and C. Casqueiro, "Development and Testing of a Non-Energy-Absorbing Anchorage System for Roadside Poles", IJ Crash Vol.11 No.2 pp.143-152, 2006. |
[7] | A. Elmarakbi and N. Fielding, "New Design of Roadside Pole Structure: Crash Analysis of Different Longitudinal Tubes Using LS-DYNA", 7Th European LS-DYNA Conference, 2009. |
[8] | D. Marzougui, C. kan and N. Bedewi, "Development And Validation of An NCAP Simulation Using LS-DYNA3D", FHWA/NHTSA National Crash Analysis Center, George Washington University,, Virginia, USA, 2000. |
[9] | O. Klyavin, A. Michailov and A. Borovkov, "Finite Element Modelling of The Crash-Tests for Energy Absorbing Lighting Columns", ENOC-2008, Saint Petersburg, Russia, June, 2008. |
[10] | E. Schuller , M. Schönpflug, N. Praxl and J. Adamec, "Potential of Virtual Crash Simulation to Examine Crash Injury and Crash Safety", Institute for Legal Medicine, Munich University (LMU), Munich, Germany. |