E. V. Slivinskiy, E. A. Suzdalskaya, T. E. Mitina
Mechanical Technological Faculty, Elets State University I.A. Bunin, Elets, 399770, Russia
Correspondence to: E. V. Slivinskiy, Mechanical Technological Faculty, Elets State University I.A. Bunin, Elets, 399770, Russia.
Email: |  |
Copyright © 2012 Scientific & Academic Publishing. All Rights Reserved.
Abstract
In this article considers the issues on the development of perspective design of the Parking brake at the level of inventions for railway rolling stock. The offered design allows in an automatic mode in case of exhaustion of a brake to exclude possibility of self-movement of a railway rolling stock. As a result of the carried-out researches the design procedure of parameters of not direct-action pneumatic brake on an example of the freight car is developed by loading capacity of 60 t. The analysis of the conducted studies allowed us to substantiate the constructive characteristics of the proposed technical solution, in relation to other rail vehicles. The results of the studies are recommended design, scientific-research and engineering structures for possible use them in practice.
Keywords:
Brake Pad, Additional Cylinder, Auxiliary Cylinder, Brake Master Cylinder, Rod, Piston, Spare Tank, Valve
Cite this paper:
E. V. Slivinskiy, E. A. Suzdalskaya, T. E. Mitina, "The Development of the Parking Brake for Freight and Passenger Cars with Control from the Driver's Cab", International Journal of Traffic and Transportation Engineering, Vol. 1 No. 4, 2012, pp. 77-83. doi: 10.5923/j.ijtte.20120104.04.
1. Introduction
It is known[1, 2, 7, 8] that the most important part of the technical facilities of railway transport is rolling stock, which is designed for the transport of goods and passengers by rail. One of the most important criteria for the evaluation of the rolling stock operation is traffic safety. Therefore, all of the organizational-technical actions on the railway transport are directed on maintenance of the constant working order all railway structures, paths, rolling stock, equipment and mechanisms, SCBD (Signaling,Centralization and Blocking Devices) and connection by means of their examinations, preventive maintenance, and, of course, their constant modernization at the expense of introduction of achievements of science and technology. Modern passenger and cargo carload Park includes a variety of types and designs of this kind of rolling stock, which is conditioned by the necessity to satisfy the various requirements imposed on him. All types and kinds of the rolling stock should have a high slash ability to provide comfortable conditions for passengers, have the flexibility to have a high coefficient of use, etc. These factors determine the number of requirements to the structure of the cars, which are in equipping them automatically applicable brakes, using automatic coupling devices, improvement and unification of the chassis, in the application of modern systems of heating, air-conditioning, sanitary-technical equipment, electrical equipment, ventilation, etc.At the present time in the construction of cars have found wide application of pneumatic brake devices. Such devices are called indirectly acting pneumatic brake, because when you break the train or brake lines, as well as at the opening of the crane emergency braking is automatically come into effect. Thanks to a more rapid and efficient action, auto brakes increase safety of traffic and allow to significantly increase the speed of movement of trains. However, during prolonged braking, or Parking of train, or single cars in detached position from the engine the air pressure in the brake cylinders and spare tanks gradually decreases, due to available leaks, which leads to depletion of the brakes. This is a significant disadvantage of indirectly acting automatic brakes[1, 6].Analysis of existing brake systems of domestic and foreign rolling stock[9, 16] shows, that for today there are no technical means to enable in the case of leakage of compressed air from the spare tank locomotives or wagons and the absence of brake shoes, laid on the tracks under their wheels, exclude its independent movement as in these ways, and the routes to points of the season.
2. Objectives
For a number of years (in the period of 2008-2011 ys.) in the Department of Applied Mechanics and Engineering Graphics of Bunin Elets State University by the order of the Elets Railway Department and the Administration of the South-Eastern Railway, a branch of OJSC «Russian Railways», carried out research aimed at improving the efficiency and safety of a rolling stock and its modernization. One of the sections of this scientific-research work is a theme connected with the development of technical means, excluding an independent movement of rolling stock, owned as on the trunk and station tracks, as on the ways of their settling.The aim of work is to conduct a patent search, preparation of application materials for inventions on the design and synthesis, and the definition of some structural parameters of the Parking brake for freight and passenger cars.Taking this into account and analyzing numerous bibliographic sources and domestic and foreign patents, we developed a number of advanced technical solutions aimed at the exclusion of independent motion of railway rolling stock in the case of depletion of the brakes, recognized inventions №№ 2255872, 2374111, 2391240, 2397898, 2397900, 2397899, 2391238, 2402443, 2399526, 2399525, 2412074, 2412843, 2412844, positive solutions FIIP (Federal Institute of industrial property) from 22.05.12, on the patents of the Russian Federation for inventions to applications No. 2011118300/11, 2011118298/11, 2011118302/11, 2011118308/11.
3. Methods
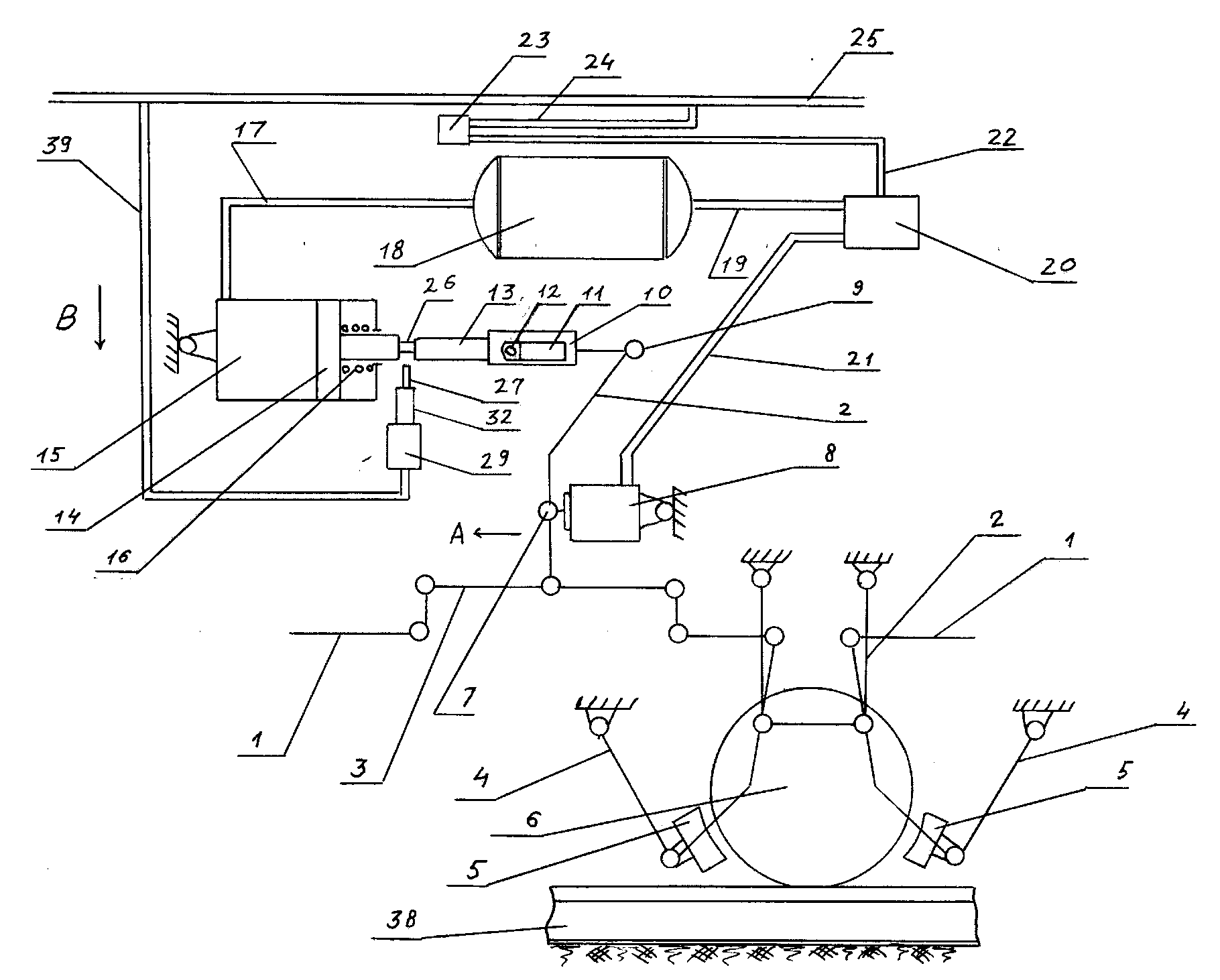 | Figure 1. The principle of the brakes |
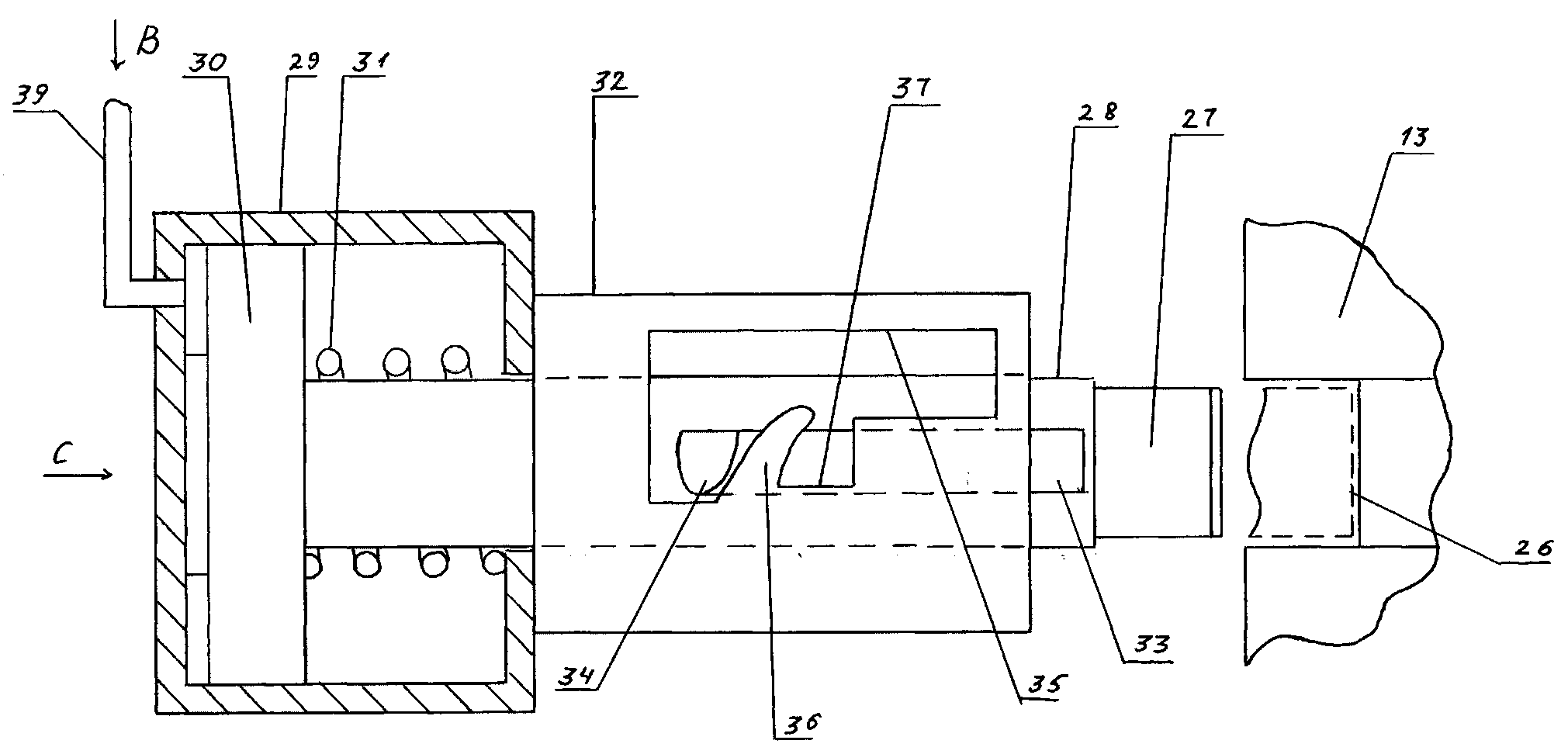 | Figure 2. Fortified node of the fixing device |
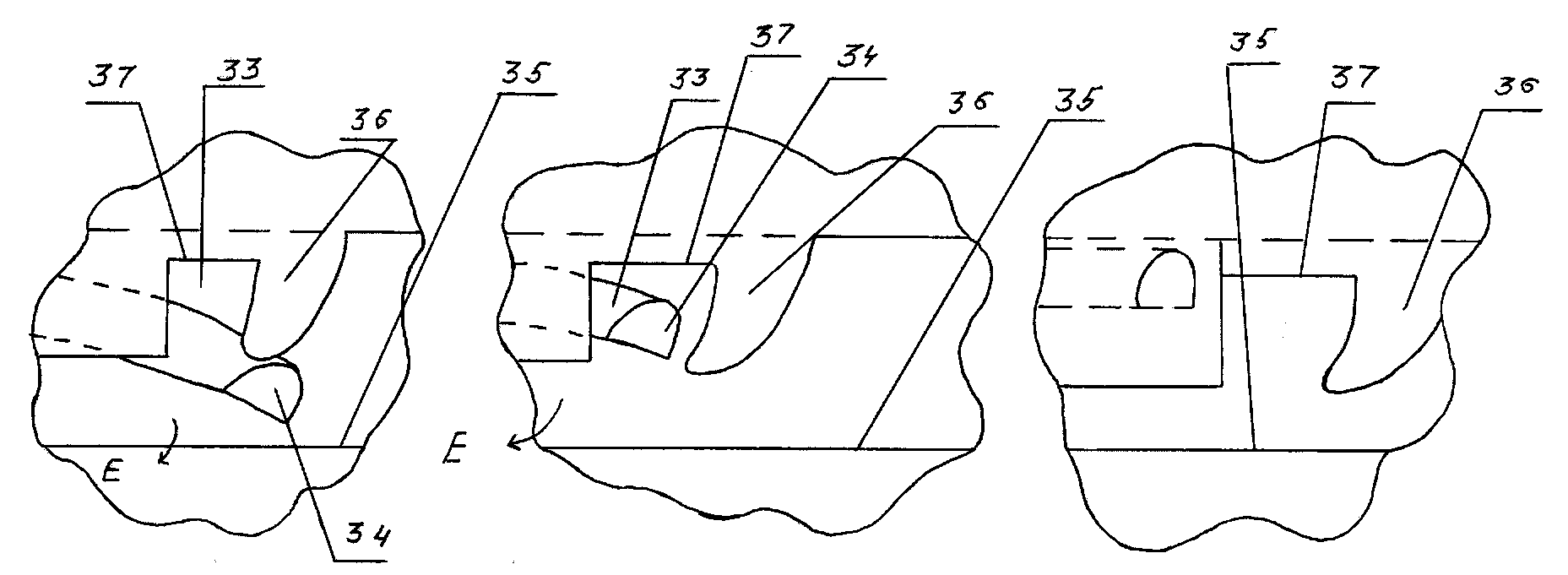 | Figure 3. Part of its cross-section vertical plane |
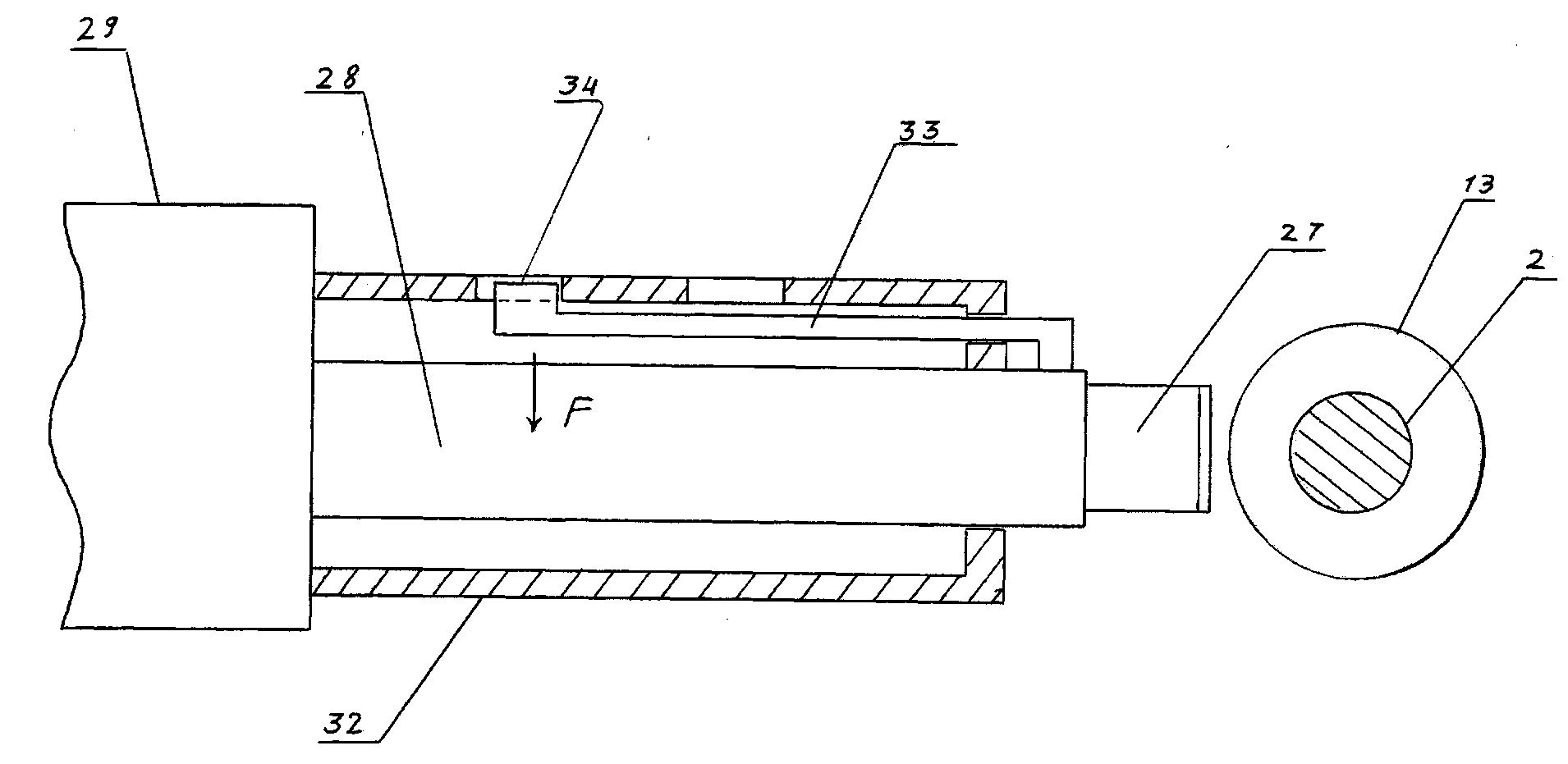 | Figure 4. Points triggering of the fixing device |
Cylinder 15 with the help of the pipeline 17 is connected to a spare tank of 18, and he in turn is linked pipeline 19 with air distributor 20, which is associated pipeline 21 with the main brake cylinder 8 and pipeline 22 with overlapping crane 23. The latest one is also connected pipeline 24 with a brake highway 25. The tuck 26 interacts with the rod lock 27 of the stem 28 of the auxiliary cylinder 29 performed on the stem 13 of the piston 14 additional cylinder 15. Piston 30 auxiliary cylinder 29 is spring loaded compression spring 31. Rod 28 auxiliary cylinder 29 mobile is situated in the hub of 32 rigidly connected to the auxiliary cylinder 29 and is equipped with a «D» shaped elastic element 33 on the free end of which is made cam 34. In the Bush 32 is made a longitudinal groove 35 having a guide of a curvilinear form 36, as well as transversal groove of 37. Wheel 6 is located on the railway track 38. Auxiliary cylinder 29 using the pipeline 39 connected to the brake highway 25.The rail crew brake works in the following way. If necessary, the service braking crew in the brake highway 25 widely known in the field of technology way to reduce the pressure of the compressed air and then the last, located in the spare tank 18 through fit the separate air distributor 20 pipeline on 21 is fed to the main brake cylinder 8. The stem of the last extends on the arrow A, which contributes to the translational and angular displacement associated with the vertical lever 2. Such transfers contribute to the movement of adjustment levers 3 and pendants 4, which allows the brake blocks the 5 enter in contact with the wheel 6 crew and thereby reduce its forward speed. At the same time, the aforementioned vertical lever 2 moves earring 10 also in the direction of the arrow and therefore finger 12 stem 13 additional cylinder 15 freely slipping on channel 11 and thus has no axial pressure on the stem 13. In the case of rod 13 cannot move the arrow A due to the fact that over the piston cavity additional cylinder 15 is located above the pressure of the compressed air entering permanently in the additional cylinder 15 by pipeline 17 from the spare tank 18. As soon as the need for braking crew disappears, the air pressure in the brake highway 25 raise, which excludes supply of it in the pipeline 21 and the latter via fit the separate air distributor 20 connects to the atmosphere, thus ensuring that the above details take the starting position, such as that shown in figure 1. If long term Parking of the crew without a locomotive equipped with the device of the production of the compressed air, or in the case of trains on the rise, the air pressure in the brake highway 25 is sharply reduced and the latter via fit the separate air distributor 20 from the spare tank 18 is fed to the main brake cylinder 15 and as it was described above, leads the crew or the band wagon to a stop. However, in practice, this Parking (especially long) may lead to leakage of compressed air from the main brake cylinder, 15 as well as other devices, brakes and then the crew or a group of cars will not be able to be more withheld brake pads 5. As soon as this happens (pressure of compressed air in the piston crown-cylinder head cavity additional cylinder 15 will decline), the piston 14 and his rod 13 will move under the influence of a compressed spring compression 16 also on the arrow A, putting in motion the lever system of brakes and pursing the brake pads 5 to the wheels 6. As a result of motion of the crew will be excluded. In practice there are cases when, for example, freight cars, equipped with the presented brake, be liable to be dissolved or the formation of the sorting plants with the use of slides. In this case, it is desirable actuation of the brake pads 5.Therefore, in order to fix the stock 13, and to his piston 14 not brought into action levers 2, before detaching locomotive from the train, on a signal of them, the driver increases the pressure of the compressed air in the brake highway 25, for example, to a value of 0.75 MPa (it is known that the pressure of the compressed air in the brake highway 25 trains is 0.53 – 0.55 MPa) then, due to the inflow of compressed air through the pipeline 39 in auxiliary cylinder 29 on the arrow B his piston 30 elastically deform the compression spring 31 move the arrow C the joint with a rod 28 and rod lock 27, which enter the tuck 26 stem 13 additional cylinder 15. It should be noted, that the geometrical parameters of the piston 30 and hardness compression spring 31 selected such that the stem 28 will receive a movement on the arrow C only at a pressure not lower than 0.75 MPa. But as the «D» shaped elastic element 33 rigidly fixed on the rod 28, and then he will move in this direction and it Cam 34 will move from the first position shown in Figure4 first in the position shown on the right, and then and in other positions are also shown on the right, with the «D» shaped elastic element 33 will be elastically deformed by the arrow E. After that, the driver reduces the pressure of the compressed air again, for example, to train, which is 0.53-0.55 MPa, and in this case the rod 28 will be securely fixed «D» shaped elastic element 33 ledge of a curvilinear form 36 executed for one whole with bushing 32, which also is rigidly fixed to the cylinder 20. Therefore, after that in case of disconnection of the braking highway 25 of the locomotive and then in the subsequent depletion of the brake rod 13 additional cylinder will always be securely fixed the pivot of the lock 27, which will freely give sorting operations on the hill. The locomotive lead to the train after drawing up the cars in it and brake highway 25 trains charged with compressed air under the pressure of the order of 0.6-0.65 MPa. The pressure value recommended also in analogue and for removing the lock rod 13 of the additional cylinder 15, in the brake line, then fall even more pressure 0.75-0.8 MPa. In this case, already drifted piston 30 auxiliary cylinder 29 on the arrow C continue to move in that direction, the «D» shaped elastic element 33 under the influence of the efforts of the created штокам 28 elastically deformed by the arrow F, and in the plan will take the position as it is shown in Figure4, and the core lock 27, selecting fully your move, take the position that, as shown in figure 4 as a dotted line. As Cam 34 «D» shaped elastic element 33 would be «recessed» on the wall of the sleeve 32, then after that the driver again reduces the pressure of the compressed air to the recommended 0.53 - 0.55 MPa and then under the action of compression springs 31 piston 30 together with the rod 28 and rod lock 27 will receive a movement in the opposite direction of the arrow C moving until Cam 34 «D» shaped elastic item 33 does not «pass» under the guide of a curvilinear form 36 and under the action of elastic properties will make movement in the direction of the arrow F. In the end, rod 13 additional cylinder will be released and the unit will again be ready to work on braking in the case of depletion of the brakes. Further described processes can be repeated many times.The constructive feature of the braking device for rolling stock, as it was noted above, is that in order to put a brake in effect, it is necessary to reduce the pressure in the brake highway to a certain value. It is clear that the pressure drop and the pace of its lowering in slow, service and emergency braking, differ significantly from the Parking regime, when such a decline is associated with accidental leaks of compressed air from the brake cylinder. And so, for the calculation of the parameters for this mode and the analysis of them, for example, with respect to four-axle gondola cars a lifting capacity of 60 t, in which the axle load is 20.0 tons developed scheme (figure 5), which includes the device, as described above. On the diagram shows two wheels wheel pairs carts, located on the rail and brake pads, compressed to him with the force of pressing K creating the braking force Fтр when the wheels on the slope at a certain value of the angle of γ in relation to the horizon.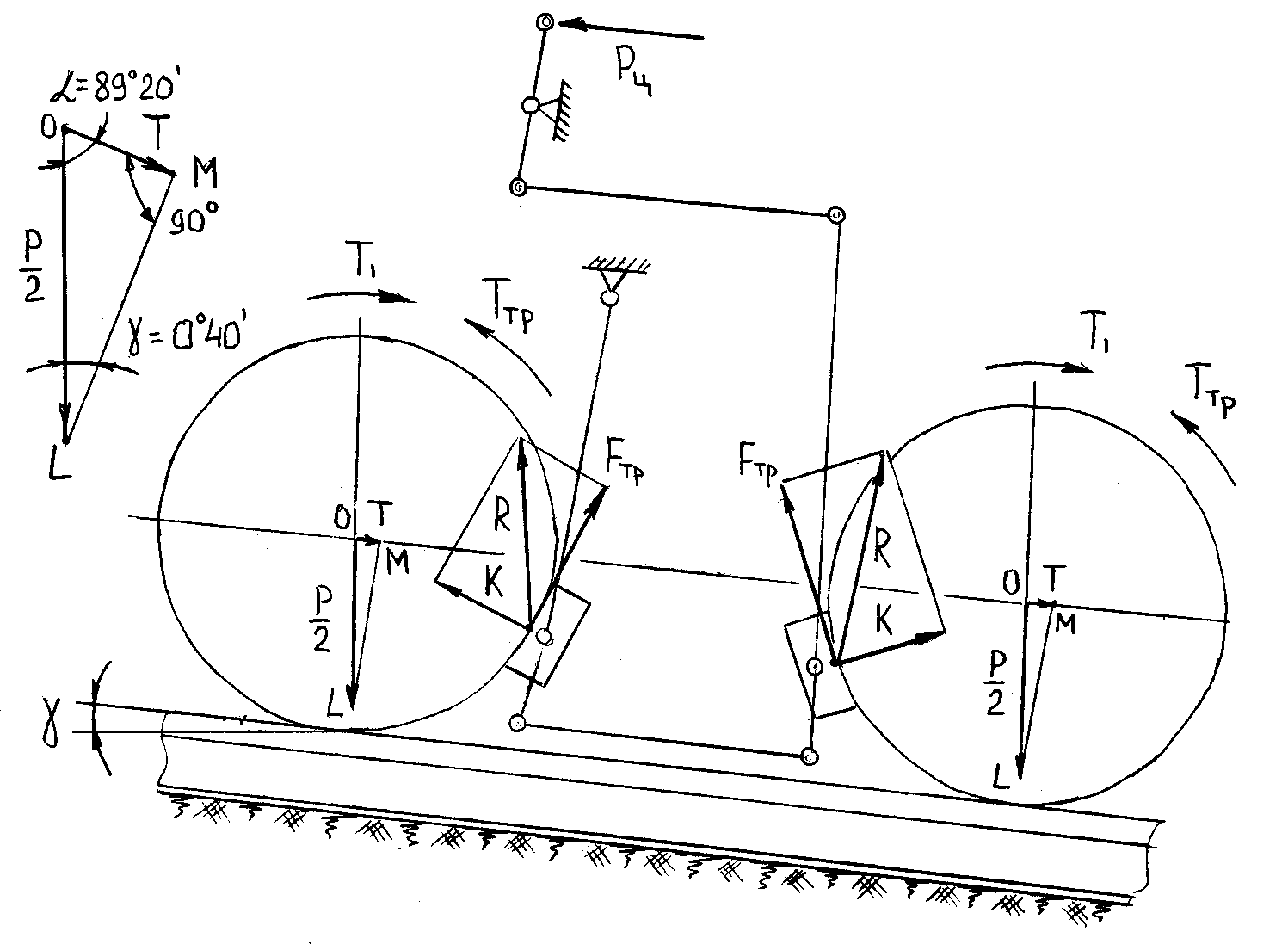 | Figure 5. Settlement scheme of the device |
Suppose that the gondola is in unhooked condition from the locomotive on a site of the station road with a bias ‰, when the pressure of the compressed air in the brake cylinder (on the scheme he had not shown) is p = 0,35 MPa at this, let us assume that the coefficient of pressing of brake blocks is equal to δ = 0,45, then the power of tension K on one axis will be: K = P∙δ = 20∙0,45 = 9t, and on one of the wheels of 4.5 tons. Therefore, the force of friction Fтр between each wheel and the brake Shoe will be equal to:
where: fsl coefficient of friction of pig-iron in steel equal to 0.18 in[2].Consider, that under such pressure of the compressed air in the brake cylinder with a diameter of 12" (304.8 mm) with the total area of the piston S = 730 cm2 his rod develop the effort Py = pS = 3,5∙730 = 2,5 t. Then, knowing the power of pressing ∑K all four axis of wheel pairs of carriages gondola ∑K = 9∙4 = 36 t, we can define the gear ratio of brake slack Adjuster.
.Suppose that the pressure of the compressed air through a variety of leaks fell to 0.15 MPa, then Py = 1.5 ∙ 730 = 1.1 tons and ∑K = Py ∙U = 1.1∙14.4 = 15.8 t, therefore, in this case the force clicking on one wheel K is K = 15.8 / 8 = 1.9 tons, and the friction force is equal to Ffr = K∙ fск = 1.9∙0.18 = 0.35 t.If the gondola is located on the slope of visitors ‰, as it is described above, it is clear that independent movement its the same as and at a pressure of compressed air 0.35 MPa possible. Now, suppose that for the first case, when p = 0.35 MPa slope of 10 ‰ that is, the angle of γ = 0º 40’ (Figure 5) and then to the wheel will be applied force T, defined from a rectangular triangle ∆LOM as:
Define now the moment T1 on the wheel, created by this power:
(where dk wheel diameter, is equal to 900 mm)The moment of friction forces Tfr generated by friction force Ffr will be equal to
= 0.36 t•m. It is seen that the Tfr > T1 therefore, gondola can't get an independent movement on the slope at a pressure of compressed air in the brake cylinder 0.35 MPa.To perform such calculations now at a pressure of compressed air 0.15 MPa at the same grade 10 ‰. Then, T1 = 0.16 t•m, and the Tfr = 0.35•0.45 = 0.16 t•m. This shows that T1 = Tfr and the subsequent reduction of pressure can lead to independent movement of the car.It is known[4] that screw springs of compression characterized by average diameter D, usually loaded at the ends, with current load is reduced to the forces P directed along the axis of symmetry of the spring and the pairs of points operating in face planes, perpendicular to the z axis.Using the method of cross-sections, suppose (Figure6) that in the favorites section A loaded spring specified loads of any internal components of efforts such as N - normal, Q-cutting in two planes and M - bending and twisting moments.
Usually in the practice of force N and Q are of secondary importance in comparison with the twisting and bending moment Мtu Мbu so they take as the estimated parameters in the study of stressed state of springs installed in the option cylinder brake. It is known[4] that in the process of deformation of the spring compression turns her move relative to each other steadily, and this testifies to the absence of a relative rotation of the cross sections of the spring. And therefore, given that the movement of spring are small compared with their respective sizes, as well as its ends are not turning you can use the following dependencies, allowing to calculate the axial displacement of the spring λ0 and moments
acting in the end planes, perpendicular to the z-axis by the following formulae: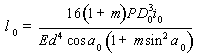
where E is the modulus of elasticity of the material;μ - Poisson ratio;d - diameter of bar springs.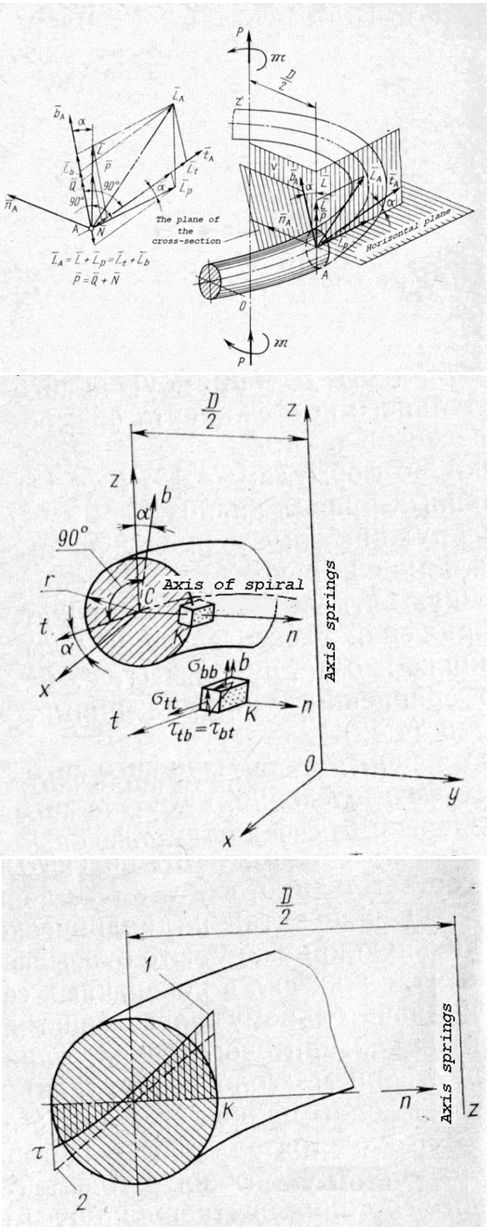 | Figure 6. Settlement scheme of a spring |
To the ends of the spring, Laden with moments that are not moving in the axial direction, axial force P0 and angular displacement θ the ends of the springs determined respectively by the following formulae:
Earlier it was noted that the loading of the cylindrical spring at the ends of the axial forces and a couple of moments, it turns working simultaneously on torsion, bending and stretching-compression, and with such an approach the normal and tangential stresses in the cross sections of turns can be determined by the known dependencies:
where, β – coefficient that depends on the form of the cross section of a coil.But as the coils of cylinder springs usually have a large curvature, and that significantly influence on the law of distribution of internal forces in the cross sections of turns, which leads to a significant increase of stress. Therefore, the calculation of stresses arising in the domestic fiber turns in dangerous points (point K on the figure 6) are recommended to be defined by the formulas obtained using methods of the theory of elasticity N.A.. Chernyshev[4], which have the form:
where, kbp, ktp , kp – ratios, depending on the angle of the coil α and the spring C the Poisson's ratio of μ = 0,3.On figure 6 as a representative example of the power of loading coil screw springs of compression of a solid line shows the graph of the distribution of tangential stresses on the diameter of the cross-section of its spire, built with the use of formulas obtained by the method of the theory of elasticity, and the dashed line shows the stresses arising in the direct beam of circular cross-section in its pure torsion. It is seen that the numerical values of tangential stresses in the first case, more than in the second, and therefore the definition of their using these formulas is the most important.The calculations showed that the motion for the exclusion of the car in case of depletion of brake spring compression 16 additional cylinder 15 (Figure 1) should develop the force of the order of 1.32 tons (coefficient of stock takes 1,2). This spring should have the following characteristics: Dout = 160 mm; Dav = 138 mm; diameter of bar 22 mm, step t = 44 mm, the height of the Hfr = 407 mm, material steel 60С2 according to standard 2590-51. The working effort this spring is 1.4 tons. For the spring calculate the numerical values of normal and tangential stresses arising in the this spring on the above formulae:
where, kbp, ktp, kp when C = D/d = 138/22 ≈ 6 and α = 150 respectively selected in table 4.5[4] is equal 0,002, 0,014 and 0,054.The results show that the condition of the strength is performed for the material steel 60С2 according to the standard 2590-76, from which is made plain spring and has a tensile strength of σВ = 6760 kg/cm2 = 676 MPa.At the same time, analyzing the design of the brake and his work can be seen that the most crucial part is the corner of the form of elastic element 33 with Cam 34 (see figure 4), the essence of which is a flat spring, working with small movements in the linear or angular displacement of the spring determine the methods of resistance of materials. Usually in the design of such springs decide not direct problem, which we know its geometry and the desired values are displacements and stresses, and the opposite associated with the preliminary selection of material and in accordance with the terms of their work shall appoint the allowable stress. In the end, they calculate the strength and stiffness of the definition of the geometrical characteristics of the springs. Let us consider a numerical example the design of flats, duplexes spring, which is the elastic element 33 angular form with Cam 34 (see Figure4). Take as the working load acting on Cam spring will take P = 200 N, at that, which should be moving Δl = 20 mm. As a material accept steel 60С2А with modulus E = 2•105 MPa and with a limit of fluidity σТ = 1400 MPa. In the responsibilities of the parts working in the brake system of railway rolling stock choose factor of nT = 2.0, and then the permissible bending stresses will be:
Let us ask ourselves the ratio l/h = 40, where the numerator spring length of 160 mm, and in the denominator of the thickness of 4 mm and then the width of the spring b will be determined by the formula[3]:
Ultimately accept the width of the spring equal 14.0 mm.Define now the normal stresses arising in the spring when the load is her effort 200 N, while constructively thickness of spring will increase up to 5 mm, depending on:
Condition strength performed.
4. Results
The carried-out researches allowed to develop a perspective design of not direct-action pneumatic brake for a railway rolling stock which in an automatic mode allows to carry out self-retardation of the last and to exclude thereby the emergencies connected with self-movement of locomotives and cars. Such design of a pneumatic brake has world novelty and is protected by the patent RU2397900. The carried-out analytical researches of such design allowed to calculate the geometrical characteristics of its element base allowing at pressure decrease of compressed air in the spare tank less than 0,15 MPa, at the expense of existence of the heat-sink device executed in the form of a screw cylindrical spring of compression, to create necessary pressure force on brake shoes about 13000 N and to exclude thereby a pro-collar of wheel pairs of rather rail way with a bias less than 10 ‰. As a result of the carried-out calculations numerical values of the tension arising in rounds of springs at their compression by nominal pressure in brake system of equal 0,65 MPa which don't exceed allowed values for this chosen material of 700 MPa are also received. The developed settlement schemes and techniques of carrying out analytical researches of power loading of constructional elements of the device are recommended for practical application at design and designing of a railway rolling stock of various type and appointment.
5. Discussion and Conclusions
In conclusion it should be noted that different types of freight and passenger cars may be equipped with the above-mentioned devices and with consideration of their mass and structural characteristics were calculated, using the method presented above, as well as the developed computer program in Delphi, and have the design parameters of the system of self, which correspond to their scope and purpose. The results of the study submitted to the heads of Administration of the South-Eastern Railway, a branch of OJSC «Russian Railways» in the form of an Express statement on the part of the above research, and are also recommended to use the relevant research institutes, specialized design bureaus and industrial enterprises, designs and manufacturing passenger and freight rolling stock, both in our country and abroad.
References
[1] | The cars. The design, theory and calculation / Under Ed. L. A. Shadur. M.: Transport, 1980 - 439 p. |
[2] | Krylov V.I. Locomotive brakes. - M.: Transzheldorizdat, 1983. – 461 p. |
[3] | Brake equipment of a railway rolling stock: Directory / V.I. Krylov, V. V. Krylov, V. N. Efremov, etc. – M: Transport, 1989. – 487 p. |
[4] | Inozemzev V. G., Kazarinov V. M., Yasentsev V. F. Automatic brakes: The textbook for higher education institutions. – M: Transport, 1981. – 464 p. |
[5] | Krylov V. I., Krylov V. V. Automatic brakes of a rolling stock. – M: Transport, 1983. – 360 p. |
[6] | Zapletokhin V.A. Construction of parts of mechanical devices: Handbook. - L.: Mechanical engineering. 1990. – 669 p. |
[7] | Ponomarev S.D., Andreeva L.E. The calculation of the elastic elements of machines and devices. - M.: Machinery, 1980 – 326 p. |
[8] | The calculation of the cars for stability/ Under ed. L.A. Shadur. M.: Machinery, 1978 - 432 p. |
[9] | Vorshinsky S.V. and etc. Dynamics of cars. M.: Transport, 1982 - 303 p. |
[10] | Technical guide of the railway. Volume 6. Rolling stock. Under ed. V.N. Sologubov. Gostranszheldorizdat. - M., 1962. - 955 p. |
[11] | Kazarinov A.V., Malikov, N.V. On the classification of automatic parking brake. The works of RSRIET (Russian Scientific-research Institute of Railway Transport), 2003. –p. 32. |
[12] | Nikitin G.B., Nazarov I.V., Goryunov G.N. Brake system platform for transportation of large-capacity containers with a maximum speed of up to 140 km/h. The works of RSRIET (Russian Scientific-research Institute of Railway Transport), Vol. 16, 2006. – p. 34. |
[13] | Feodosiev V.I. Resistance of materials. M.: Science, 1986. - 342 p. |
[14] | Patent RU 2255872, 7В61Н, 11/02 Brake cart rail crew. Slivinsky E.V., Teslin V.V. Kurnosova O.V. |
[15] | Patent RU 2232094, 7В61Н, 11/02 Braking equipment of a railway wagon. Slivinsky E.V., Klokov D.A. |
[16] | Slivinsky E.V., Teslin V.V. Investigation of the kinematic parameters of the device for automatic rolling stock with the computer. Computer science, concepts, modern condition, prospects of development. Materials of the scientific- methodological seminar. BYSU. Yelets, 2006, - p. 38. |
[17] | Railways. The General course. Fifth edition. Under ed. M.M. Uzdin. - M., Transport, 2000. |
[18] | Gundareva E.P. Technical means of Railways. A textbook for technical schools and colleges of rail transport. M., Route, 2003. |
[19] | Railway transport: Encyclopedia /ed. N.S. Konarev - M., The Great Russian Encyclopedia, 1994. |
[20] | Guzenkov P.G. Details of machines. Textbook for Institutes of higher education. - M., Higher school, 1975. |
[21] | Reshetov D.N. Details of machines. Textbook for students of engineering Universities. 4th ed. - M.: Machinery, 1980. |
[22] | Dunaev P.F. Designing of machines unites and components. - M.: Machinery, 2001. |