Liu Shangtan1, Wu Xiaochun1, Mao Zhengdong2
1Materail Science and Engineering School, Shanghai University, Shanghai, China
2Manufacturing Department, Baosteel Special Metals Co, Ltd, Shanghai, China
Correspondence to: Liu Shangtan, Materail Science and Engineering School, Shanghai University, Shanghai, China.
Email: |  |
Copyright © 2019 The Author(s). Published by Scientific & Academic Publishing.
This work is licensed under the Creative Commons Attribution International License (CC BY).
http://creativecommons.org/licenses/by/4.0/

Abstract
Steel manufacturers have been paying more attentions to burning loss prevention to increase yield rate and lower cost for the last decade. For high carbon content steel, the application of anti-oxidation coating is a truly effective way, but various coatings matter totally different. Some experimental practices have been done and the most appropriate coatings for hign carbon steel have been confirmed. So the detailed burning loss performance experiments in one hot rolling plant in Baosteel Special Metals Co, Ltd of two anti-oxidation coatings have been successfully discussed and analyzed. The results shows the original burning loss percent without billets-coating stays at 1.705%, and the two anti-oxidation coatings do significantly decrease the burning loss, with coating TL0001 lowering the loss percent to 1.24% whereas coating TL0002 to 0.20%. As a result, the application of coating TL0002 will bring a huge economic benefit of 135.20 RMB per ton.
Keywords:
High-carbon high-manganese steel, Anti-oxidation, Coating, Burning loss
Cite this paper: Liu Shangtan, Wu Xiaochun, Mao Zhengdong, Application Research of Anti-Oxidation Coating on High-Carbon High-Manganese Steel, International Journal of Metallurgical Engineering, Vol. 7 No. 1, 2019, pp. 6-12. doi: 10.5923/j.ijmee.20190701.02.
1. Introduction
High-carbon high-manganese billets are very much easily oxidated because of the carbon oxygen reaction
=3Fe2O3. In 2007, a new plate line with annual output 280,000 tons was built to supply various kinds of high-manganese alloy plates such as 20Mn23AlV, 45Mn17Al3, Mn13, Mn8 etc., high alloys stainless plates such as S30403, S30408, S30492, S31254, S31603, S31608, S31803, S310S, S32253, S32205, S32304 etc., high alloy die plates such as H13, D3, SKD11, SKD61, SKD5, 1.2316 etc., high performance alloy plates such as N07718, N07750, S66286 etc., corrsion resistant high alloy plates such as N08800, N08810, N06600, N06601, N06690, N10001, N10276, N06625 etc., Titanium alloy plates such as GradeF1, GradeF2, GradeF3, GradeF4, GradeF5 etc., For high--carbon high-manganese steel, it has been always an economical consideration to prevent it from burning too much. The most effective burning -loss controlling way is coating brushing on the surface of billets. But the results varies a lot for various kinds of coatings, So the performance experiment of two kinds of anti-oxidation coating were arranged in Baosteel Special Steel Co,. Ltd to finally confirm the application the right coating in the manufacturing practice.
2. Approach and Materials for Experiments
2.1. Experimental Approach
The way to apply in the experiment includes weighing all four billets before burning, heating four billets to a temperature of 1200°Cand holding 60 minutes, then pulling out two billets but rolling the other two, and weighing all four billets after burning if the billets all cooled to ambient temperature [1].
2.2. Experimental Materials
The sizes of the four billets of high-carbon high-manganese steel are 200**1300*2000-2500mm and the applied two anti-oxidation coatings were marked TL0001 and TL0002.The billets were put into the walking-beam furnace with heat capacity of 2850m3/h, 27000mm length, 6900mm width and 7900mm height.
3. Experiment Processes
The research process constitutes roughly four steps showing in Figure.1.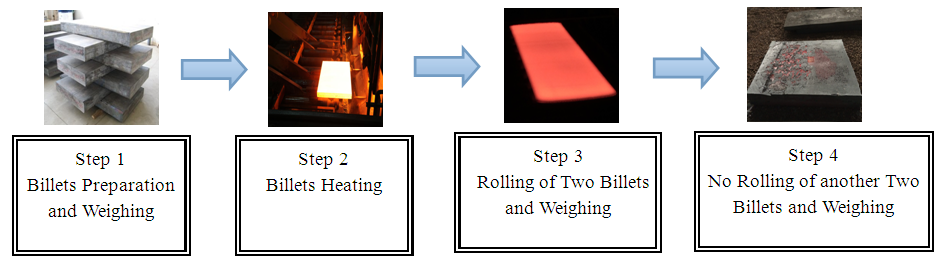 | Figure 1. Burning Loss Experimental Process |
Firstly four billets of high-carbon high-manganese were prepared with size of 200*1300*2000-2500mm, serial numbers of BP0001, BP0002, BP0003 and BP00004 were recorded respectively. They were weighed by 20 tonnes electronic hoist scale with weights recorded. Secondly, BP0001 and BP0002 were covered by coating TL0001 and TL0002 respectively, but no coating covering BP0003 and BP0004. Coating were only sprayed on upper surface and two sides with down surface no coating spraying for the convenience of operation, so roughly half the overall surface of the two billets were covered with coating.Next, the above four billets were loaded into walking-beam furnace for heating with soaking time of 1 hour and soaking temperature 1200°C. Billet BP0001 and BP0002 were rolled into plate size of 30*1820*6500mm and 30*1820*7500mm respectively, whereas BP0003 and BP0004 not committed rolling. The above plates and billets were cooled in air and got rid of scales, with weights counted by electronic hoist scale and recorded. The above process was repeated triple times and the average data were recorded for the following discussion and analyse.
4. Data Analysis and Results
4.1. Data Sheet
The collected data were showed in Table 1 to Table 4.Table 1. Billet Weights Before and After Heating 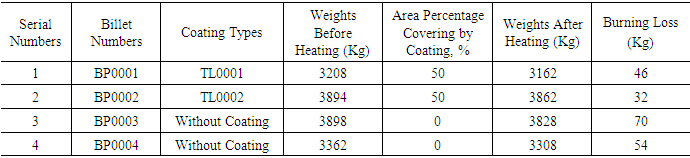 |
| |
|
Table 2. Burning Loss Percentage on Actual Circumstance 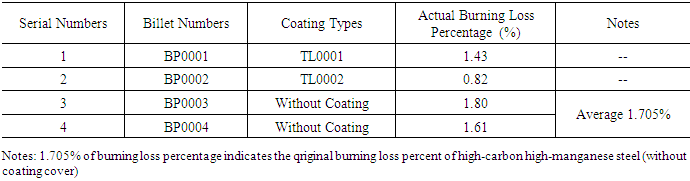 |
| |
|
The theoretical burning loss percentage in terms of 100% percent surface coating can be calculated as following.Table 3. Theoretical Burning Loss Percent With 100% Surface Coating  |
| |
|
Table 4. Comparative Results of the Two Coating on Anti-oxidation Capability  |
| |
|
4.2. Burning Loss Characteristics Discussion of High-Carbon High-Manganese Steel
A gradual oxidation process as FeO→Fe3O4→Fe2O3 features the oxidation of billets, creating three layers oxidation chemicals from billet surface to inside. The outerest layer Fe2O3 accounts 10% the whole thickness, medium layer Fe3O4 takes 50% thickness, whereas the innerest FeO hold 40% the whole thickness. The scales react chemically as following equations [2]. | (1) |
 | (2) |
 | (3) |
Figure.2 presents the three layer of scales layout produced when the billets are heated.Figure.3 indicates the original burning loss value of high-carbon high-manganese steel.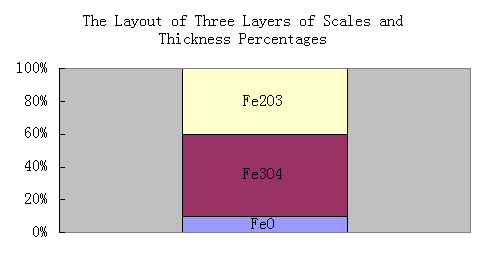 | Figure 2. The Layout of Three Layers of Scales and Thickness Percentages |
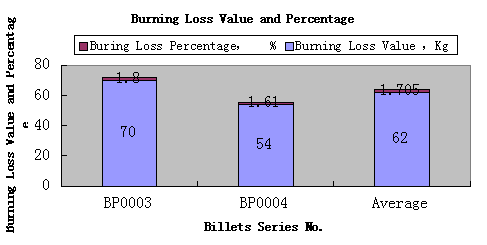 | Figure 3. Original burning loss value of high-carbon high-manganese steel |
Several major factors to affect the process of chemical burning on billet surface, ranking in terms of their contributions level, include burning temperature, soaking duration, oxygen content as well as air-feul ratio in furnace [3], etc.The formation amount W(g) of scale per area has close connection with soaking temperature(T) and soaking period(Г) [4]: | (4) |
Herein Г means soaking period(min), T indicates soaking temperature(K), and ‘a’ stands at 6.30, ‘b’ is a constant value of 900. So soaking temperature plays the most important role on burning loss, see Table 5.Table 5. The correlation between the burning loss values and soaking temperatures  |
| |
|
Figure.4 displays the significant effects of soaking temperature on burning loss value.Figure.5 shows how soaking period affects burning loss value.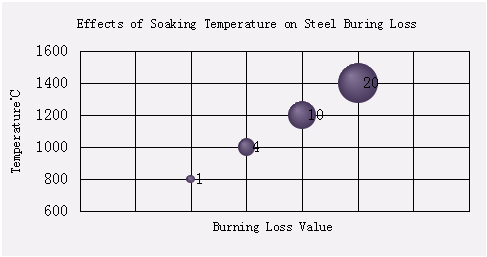 | Figure 4. How soaking temperature affects burning loss value |
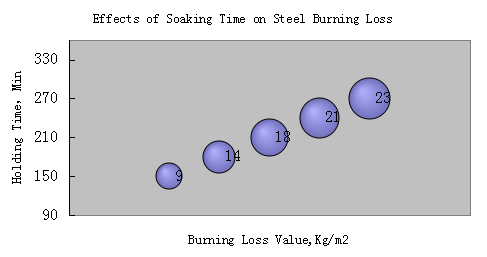 | Figure 5. Effect of soaking period on burning loss value |
4.3. Anti-Burning Performance Comparison between the Two Anti-Oxidation Coatings
The burning loss value of high-carbon high-manganese billets plummets after they are covered with any of the two coating, with coating TL0002 having the most positive anti-burning result. The good results of the two anti-oxidation coating are showing in Figure.6 and Figure.7.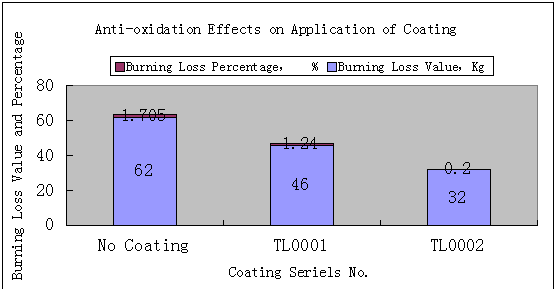 | Figure 6. Positive result showcase of the two anti-oxidation coating |
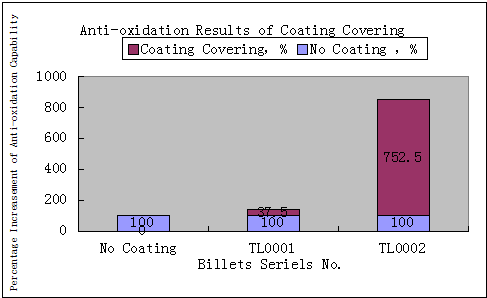 | Figure 7. Positive result showcase of the two anti-oxidation coating |
It shows that application of coating TL00001 on high-carbon high-manganese steel decreases the burning loss percentage from the original 1.705% to 1.24%, with anti-oxidation efficiency improvement of 37.5%, whereas that of coating TL0002 on high-carbon high-manganese steel lower the burning loss percentage from 1.705% to 0.20%, with an anti-oxidation improvement of significantly 752%.
4.4. Advantage of the Two Coatings
• Melting temperature as high as 1800°C and excellent chemical stability.• Relatively low Oxygen diffusion coefficient, so effectively prevent the oxygen from intruding into billet surface. Fewer coating defects, so decrease the billet oxidation.• Strong combing ability with billets, fabulous wetability as well as high density.• Prone to be peeled off in quick cooling process, so avoid of hurt on plate surface by remnant coating during rolling.• Dry fast and easy to paint.
4.5. Economic Benefit Calculation of Application of the Two Coatings
4.5.1. Cost Discussion
Table 6 is coating-related cost [5] per ton steel (labour cost and facility cost included).Table 6. Coating-related cost per ton steel  |
| |
|
4.5.2. Economic Return
Table 7 displays the ecnomic return per ton steel in application of coating.Table 7. Ecnomic return per ton steel in application of the two coatings  |
| |
|
Figure.8 demostrates the per ton economic benefit of high-carbon high-manganese steel by application of the two anti-oxidation coatings.Figure.9 indicates the economic return by application of coating TL0002 on high-carbon high-manganese steel in a scale production.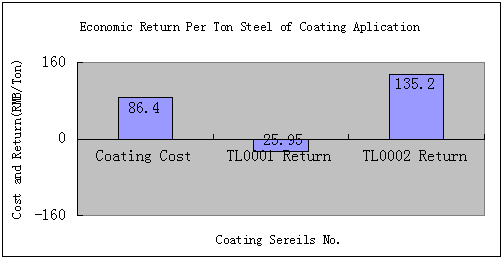 | Figure 8. Economic Return Per Ton Steel of Coating Application |
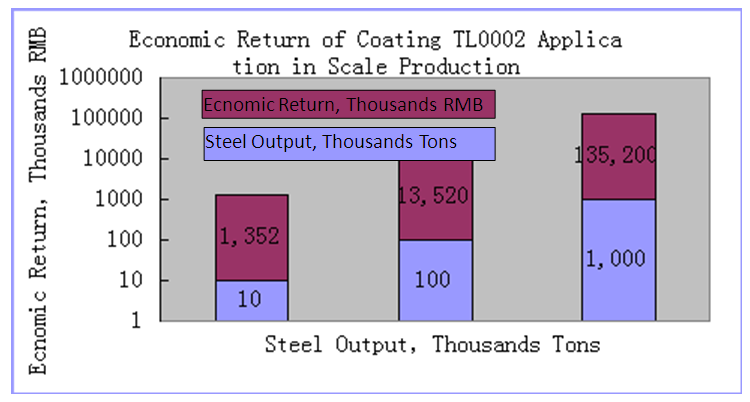 | Figure 9. Economic Return of Coating TL0002 Application in scale production |
5. Conclusions
The experiment results show it has a solid burning loss percentage for high-carbon high-manganese steel with average burning loss percentage of 1.705%. Application of coating TL0001 and TL0002 both effectively retards the burning loss process of high-carbon high-manganese steel, with burning loss percentage lowering down to 1.24% and 0.20% respectively and much better anti-burning loss performance in TL0002.There is an 135.20RMB/ton economic benefit by application coating TL0002 on high-carbon high-manganese steel. In an scale production level, it means a 13.52 millions and 135.2 millions RMB economic return with an scale production of 100,000 tons and 1,000,000 tons respectively.
References
[1] | Wang Minghu, Discussion and Practice on Measuring Method of Burning Rate of Steel Billet in Heating Furnace, Gansu Metallurgy[J], 2015, (4), 29. |
[2] | Wang Liyu, Jin Xinxi, etc. Discussion on the Technology of Reducing Slab Oxidation Loss,Wide and Heavy Plate[J], 2012, 18(6), 32. |
[3] | Zhang Yukun, Wen Zhulan, Practice of Billet Burning Reduction, Jiangxi Metallurgy[J], 2012, 32(3), 23-24. |
[4] | Liu Zhanzeng, Zhen Zhaoping, etc. Causes and Countermeasures of Oxidation Burning in Heating Furnace, Energy for Metallurgical Industry[J], 2014, 23(2), 30-31. |
[5] | Xu Xiaolian, Liu Dong, etc. Development of Anti-oxidation Coating in high temperature for nickel-chromium alloy steel billet, Materials Protection[J], 2013, 36(4), 53. |
[6] | ZHANG Lili, ZHOU Chenhui, etc. The Research of Solving the Problem of Thickness and Uniformity of the Steel Billet Anti-Oxidation Coating by Applying the ARIZ Algorithm, The seventh international conference proceedings on refractories[J], 2016, 55-59. |