Srinivas Dwarapudi1, Chandra Sekhar1, Indrajit Paul2, Kapil Modi2, Atanu Ranjan Pal1, Ujjal Chakraborty2, B. K. Das2
1R&D, Tata Steel Jamshedpur, India
2Iron Making Division, Tata Steel Jamshedpur, India
Correspondence to: Srinivas Dwarapudi, R&D, Tata Steel Jamshedpur, India.
Email: |  |
Copyright © 2017 Scientific & Academic Publishing. All Rights Reserved.
This work is licensed under the Creative Commons Attribution International License (CC BY).
http://creativecommons.org/licenses/by/4.0/

Abstract
Indian iron ore fines with high alumina content (~2.5% Al2O3) resulted in poor quality pellets and a study was under taken to establish suitable pellet chemistry through proper fluxing agents. Limestone fluxed pellets were prepared at varying basicity (0 to 0.8) and pyroxenite fluxed pellets at varying MgO contents (0 to 3%) to study their effect on the metallurgical properties. Fired pellets were tested for their strength, RDI, reducibility and swelling. Microstructural studies, optical and SEM-EDS were carried out to quantify different phases and their chemistry. Acid pellets exhibited poor quality whereas limestone pellets at 0.8 basicity and pyroxenite pellets at 1.5% MgO exhibited optimum metallurgical quality. Formation of widely distributed silicate melt in limestone pellets and high melting point slag & magnesioferrite in pyroxenite pellets found to improve their quality. However, commercially produced pyroxenite fluxed MgO rich pellets exhibited better high temperature properties but inferior low temperature properties; whereas limestone fluxed CaO rich pellets exhibited the quality vice versa. To yield the benefits of both CaO (for good strength and RDI) and MgO (for low swelling and high softening), a dual flux combination was established, using both the fluxes, that resulted in optimum metallurgical properties.
Keywords:
Pyroxenite, Olivine, Swelling, Magnesioferrite, RDI, Iron ore pellets
Cite this paper: Srinivas Dwarapudi, Chandra Sekhar, Indrajit Paul, Kapil Modi, Atanu Ranjan Pal, Ujjal Chakraborty, B. K. Das, Effect of Fluxing Agents on the Quality and Microstructure of Hematite Pellets, International Journal of Metallurgical Engineering, Vol. 6 No. 1, 2017, pp. 18-30. doi: 10.5923/j.ijmee.20170601.03.
1. Introduction
Iron ore agglomerate quality plays a vital role in decreasing the reducing agent consumption and increasing the productivity of blast furnace. In most of the integrated steel works, the burden mix for blast furnace is decided as per the availability of the iron ore agglomerates like sinter and pellets. More attention has been given in recent years to the use of fluxed pellets in blast furnace due to their good strength and improved reducibility, swelling and softening melting characteristics. Generally, quality of pellets is influenced by the nature of ore or concentrate, associated gangue, type and amount of fluxes added and their subsequent treatment to produce pellets. These factors in turn result in the variation of physicochemical properties of the coexisting phases and their distribution during pellet induration. Hence properties of the pellets are largely governed by the form and degree of bonding achieved between ore particles and the stability of these bonding phases during reduction of iron oxides [1].Some researchers have recently studied the effect of fluxing agents on the pellet quality. Zhu et al [2] studied the effect of limestone and magnesite on pellet quality prepared from Brazilian specularite. They stated that RI and RDI were improved with increased basicity and MgO helped in decreasing the SI and RDI while improving the reducibility. Iljana et al [3] studied effect of limestone on the pellets prepared from Karelian region of Russia. They observed that with the addition of limestone, reducibility, swelling and cracking were increased whereas softening temperature, CCS and LTD indices were decreased. Mandal et al [4], studied the effect of lime addition on pellet quality and found out that lime addition resulted in the formation of calcium-alumino-silicate phases thereby increased the CCS, TI, AI and shatter index. It is important to note that conditions and parameters of pelletizing are specific to given ore or concentrate; the present study is undertaken for typical Indian hematite ore fines high in alumina. Except authors earlier work on quality of pellets from Indian iron ore [5, 6], there is no considerable literature reported on the effect of pellet basicity and MgO content in the basicity range of 0 to 0.8 for Indian hematite ore. In the present study, limestone fluxed pellets were prepared at varying CaO and basicity (0 to 0.8) and pyroxenite fluxed pellets at varying MgO contents (0 to 3%) to study their effect on the metallurgical properties. All the fired pellet were tested for the metallurgical properties viz., cold strength, reduction degradation index, reducibility and swelling. Optical microscope studies with image analysis software were carried out to estimate the amount of different phases. SEM-EDS analysis was done to record the chemical analysis of oxide and slag phases. X-ray mapping was also carried out to understand the distribution of CaO, MgO, SiO2 and Al2O3 in different phases. It was attempted to establish correlation between pellet chemistry (in terms of basicity & MgO) and quality.
2. Experimental
The following materials were used for preparing the green pellets: iron ore fines (-10 mm size); bentonite (-75 microns); anthracite coal (-10 mm); limestone (-50mm) and pyroxenite (-50mm). Iron ore fines, coal, limestone and pyroxenite were ground separately in laboratory ball mill to get the required fineness for pelletizing. Chemical analysis and particle size distribution of the all the materials are given in Table 1 and Table 2 respectively.Table 1. Chemical composition of materials used for pelletizing 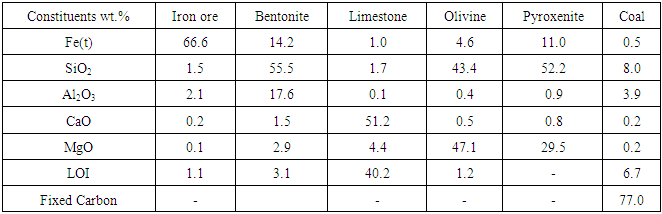 |
| |
|
Table 2. Particle size distribution of the ground materials used for pelletizing 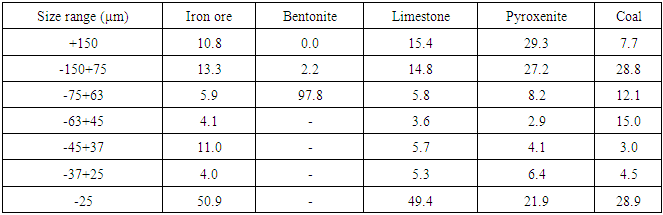 |
| |
|
Green pellets were prepared using a laboratory balling disc with a diameter of 600 mm, an edge height of 200 mm and a tilting angle of 45 degrees at 27 rpm. During balling, green pellets were screened with 10 mm and 12.5 mm screens to get 10-12.5 mm pellets. The amount of ingredients added for preparing green pellets with varying limestone and pyroxenite and their quality parameters is shown in Table 3 and Table 4 respectively. In the limestone fluxed pellets, to adjust the basicity of pellets from 0 to 0.8, flux was varied from 0 to 3%. In the pyroxenite fluxed pellets, to adjust the MgO content of pellets from 0 to 3.0%, pyroxenite was varied from 0 to 10% in the green pellets. Before firing, pellets were dried in the hot air oven at 150°C for 5 to 6 hours to ensure that all the moisture is removed.Table 3. Ingredients of green pellets with varying amount of limestone and their quality 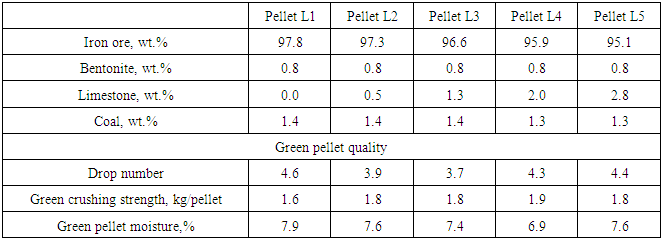 |
| |
|
Table 4. Ingredients of green pellets with varying amount of pyroxenite 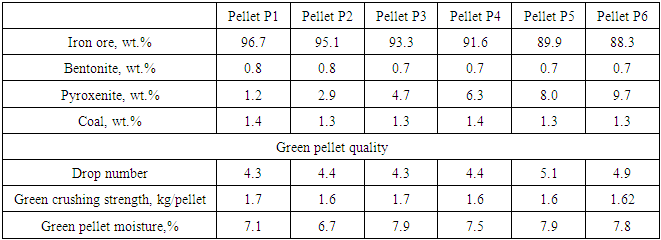 |
| |
|
Firing of the pellets was carried out using electrically heated rotary hearth furnace (RHF) mentioned elsewhere by the author in their earlier work [6]. The RHF consists of 5 heating zones and 1 cooling zone. All the zones were provided with air inlet nozzles to inject ambient air for creating oxidizing atmosphere during induration. During firing, air was injected from zone-6 (cooling zone) and was vented from the exhaust hood in zone 1 to ensure hot air circulation from zone 6 to zone 1 while pellet sample travels from zone 1 to zone 6. The counter-current movement between the hot pellets and air facilitates the complete oxidation of admixed coal in the green pellets. Temperature profiles in each zone were maintained to simulate the firing conditions in the industrial pellet indurating machine. Temperature in zone-1 & 2 was maintained at 800°C & 1100°C respectively to simulate preheating, zone-3 & 4 at 1300°C to simulate firing and zone-5 & 6 at 1100°C & 800°C respectively to simulate cooling zones of indurating machine. Inconel baskets, that can accommodate 500gms of pellets, were used to firing the pellets in the RHF. In each batch 3 kg of pellets were fired to generate required number samples for the test work.
2.1. Physical and Metallurgical Testing of Pellets
Fired pellets were tested for their cold compression strength (CCS) as per ISO 4700 and swelling index as per ISO 4698. While reporting CCS, standard deviation was also measured. Reduction degradation index (RDI) and reducibility index (RI) were tested as per ISO 4696-2 and ISO 7215 respectively. For micro structural studies, CCS and swelling, pellets from each batch were collected from top layer of Inconel basket as they are exposed to uniform heat from top and sidewalls of RHF. Pellets with cracks and irregular shape were avoided as they experience uneven heat treatment across their cross section. To normalise the experimental error, experiments are repeated for 3 times and an average value is taken for each data point.
3. Results and Discussion
3.1. Limestone Fluxed Pellets
Table 5 shows the chemical analysis of limestone fluxed fired pellets with varying basicity.Table 5. Chemical analysis of limestone fluxed pellets with varying basicity 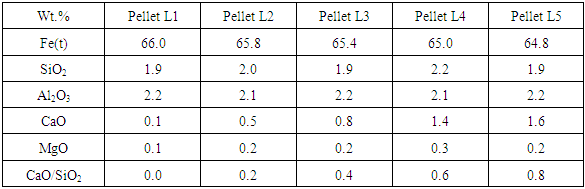 |
| |
|
3.1.1. Quantitative Measures of Microstructure through Image Analysis
Image analysis studies of these pellets revealed that hematite, magnetite and silicate melt are the major phases in the pellets. Amount of silicate melt, which acts as a bonding phase, was found to increase with increasing basicity, as shown in Fig.1. Porosity was found to decrease with increasing basicity due to impregnation of pores with the melt phase.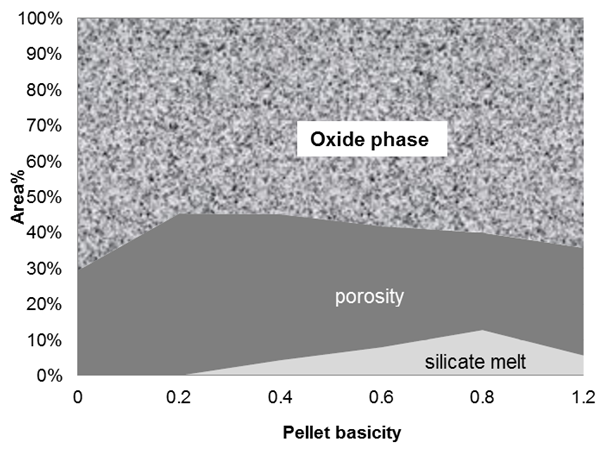 | Figure 1. Image analysis of limestone fluxed pellets showing the amount of different phases |
3.1.2. SEM Study with EDS Analysis
Figure 2 shows the SEM image of Pellet L1 & L5 with EDS analysis of all pellets (L1, L2 L3, L4 & L5). From the results it was evident that chemistry of iron oxides is uniform in all pellets irrespective of their basicity. But chemistry of slag phase found to be varying with increasing basicity. FeO content of the slag phase decreased considerably with increased basicity as shown in the EDS analysis of Fig.2. X-ray mapping studies of the fired pellet samples, as shown in Fig.3, revealed that CaO from the limestone was distributed only in silicate melt.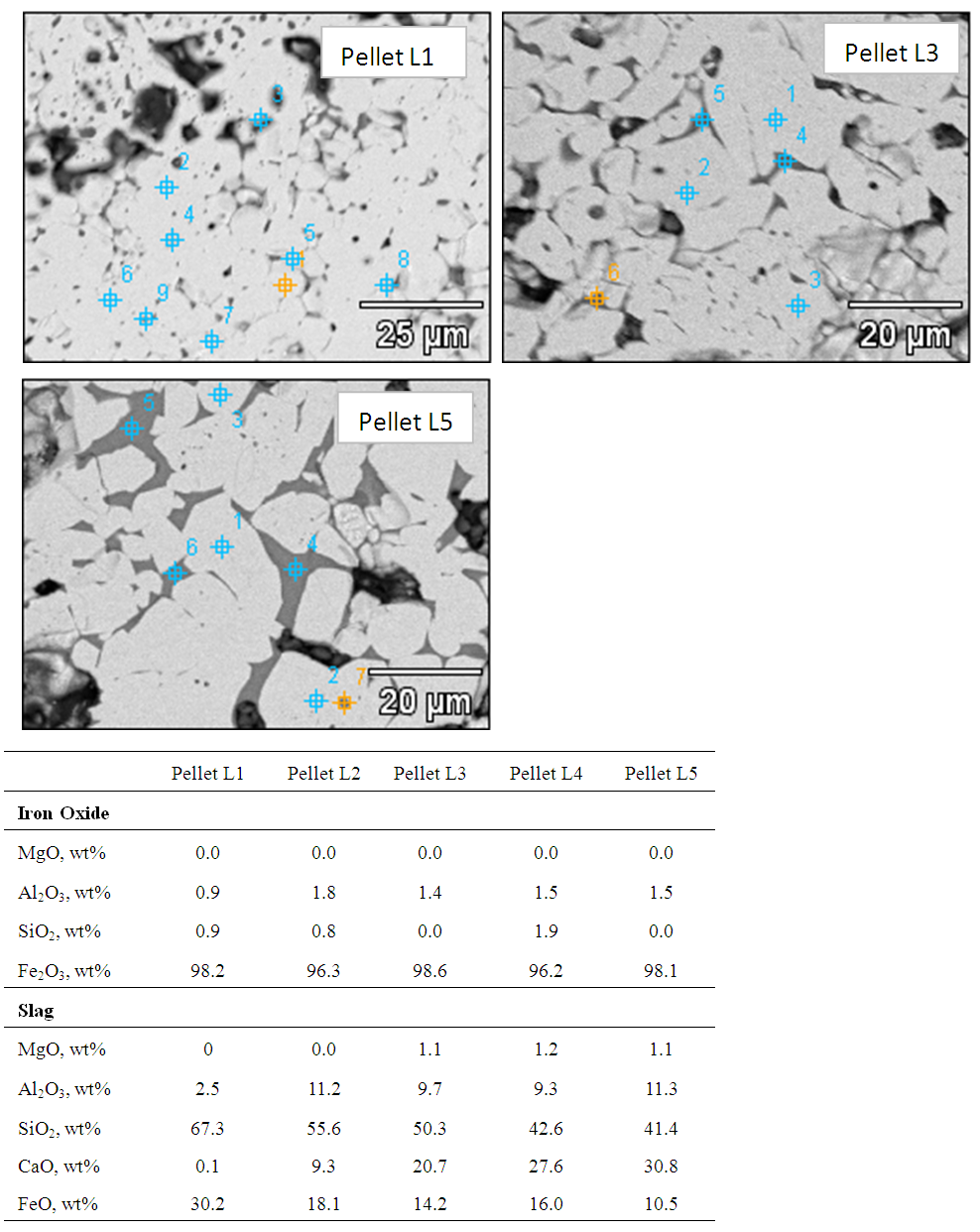 | Figure 2. SEM image of pellet L1, L3 & L5 with EDS analysis of all pellets (L1, L2, L3, L4 & L5) |
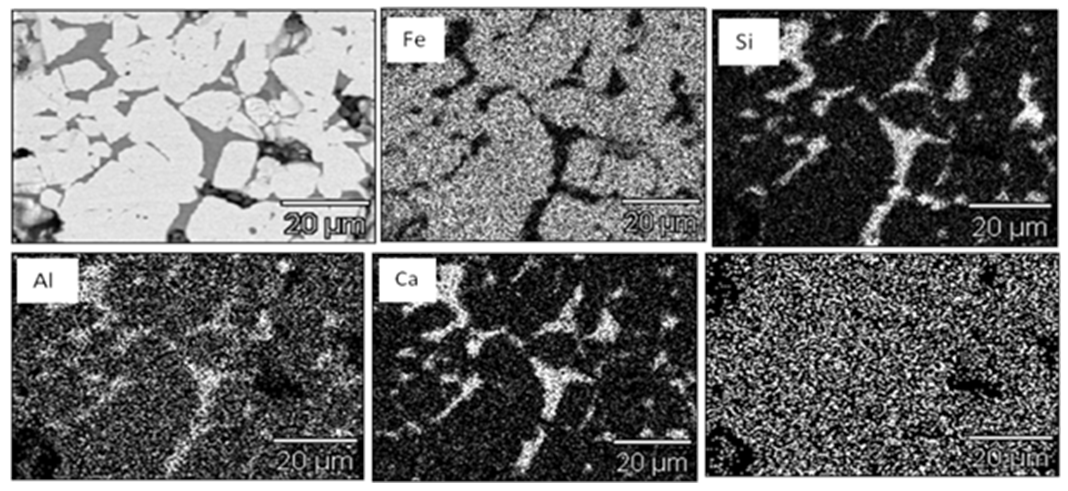 | Figure 3. Distribution of Fe, Si, Ca and Mg in 0.8 basicity pellet (Pellet L5) |
3.1.3. Cold Compression Strength
Cold compression strength (CCS) indicates the ability of pellets to withstand the load during their storage & handling and the load of burden material in the reduction furnace. Blast furnace needs pellets with CCS values in the range of 200-230 kg/pellet. Pellet strength found to increase upto 0.4 basicity (CaO/SiO2) in limestone pellets and decreased thereafter, as shown in Fig.4 (a). This high strength at 0.4 basicity could be attributed to decreased porosity with increased basicity. Addition of basic flux resulted in the formation of more amount of low strength silicate melt phase, Fig.1. Silicate melt fills up the pores between solid particles and exerts pressure to pull them together due to interfacial forces thereby reducing the porosity. But, beyond 0.4 basicity, the positive effect of low porosity is counteracted by the increased amount of low strength silicate melt, thereby resulting in lower strength.
3.1.4. Swelling Index
Swelling index indicates volume change of pellets during reduction. Higher swelling index reduces the strength of pellets after their reduction thereby causing irregularities in the blast furnace like high resistance to gas flow, burden hanging and slipping. Maximum allowable swelling of pellets for blast furnace ranges from 14-16%. Figure 4 (b) shows the swelling index of limestone pellets with varying basicity. From the results it is evident that acid pellets (without any added flux) exhibited highest swelling among all the pellets. In case of limestone pellets, high swelling was observed at 0.6 basicity and decreased thereafter.Volumetric expansion of iron ore pellets takes place during their reduction from hematite to magnetite and wüstite. It can be mainly attributed to the increased volume requirements for the anisotropic growth of magnetite (111) planes parallel to the hematite (0001) planes 5. Swelling is related to the ability of gangue or slag phase to withstand the reduction stresses of independent oxide particles. High melting point slag would produce sufficient bonding strength to limit swelling and low melting point slag enhances swelling. In acid pellets, reduction is accompanied by the reaction between Fe2+ and SiO2 to form low melting point phase, fayalite (Fe2SiO4) that melts at 1175°C [6, 7]. High swelling index of these pellets can be attributed to the plastic or mobile nature of low melting point fayalitic slag that provides a medium for absorption of the reduction stresses by increased distances between the particles. In the limestone pellets, high swelling values at 0.6 basicity can be compared to the studies of on different iron ore fines. They reported that maximum swelling on reduction occurs in the basicity range of 0.2-0.8. In case of our pellets, maximum swelling at 0.6 basicity can be attributed to the formation of low melting point calcium olivines between Fe2SiO2 and Ca2SiO4, with lowest melting point of 1115°C [8].
3.1.5. Reduction Degradation
Reduction degradation (RDI) of pellets indicates their tendency to generate fines during reduction. From the results it is evident that acid pellets exhibited highest RDI whereas limestone pellets in the basicity range of 0.2-0.8 showed low RDI as shown in Fig.4 (c). RDI of pellets is an undesired phenomenon that occurs at low temperatures in the upper part of blast furnace. The primary cause of low temperature disintegration is due to crystalline transformation from hexagonal hematite to cubic magnetite accompanied by volume expansion to an extent of 25 percent and lattice distortion [1]. The anisotropic dimensional change due to the transformation leads to severe stresses in certain planes, resulting cracks in brittle matrix. The effect is particularly severe in the grain boundaries. It is very clear that iron oxide in the indurated pellets is mainly in the form of hematite; therefore, generation of internal stress, in principle, is unavoidable. The disintegration can be reduced by increasing the amount of stable bonding phases, which are less brittle at lower temperatures, with homogeneous distribution. Bonding which forms during induration can be divided into three main groups: Iron oxides bonds (hematite, magnetite), silicate bonds and local bonds (calcium ferrite, magnesioferrite) that are close to particular mineral phases. Iron oxide bonds are common and strong, but they are not stable during reduction due their phase change. Unlike iron oxide bonds, silicate bonds remain unaltered during reduction and they soften and melt later [9]. Acid pellets showed high reduction degradation due to the presence of more hematite bonds and less silicate bonds. Limestone pellets exhibited considerably less reduction degradation due to the presence of silicate melt, as shown in Fig. 1, which is more stable compared to hematite. In the earlier studies by the author, it was observed that uniformly distributed silicate melt improves the RDI of iron ore pellets [5].
3.1.6. Reducibility
Reducibility of the pellets may be defined as the ease with which the oxygen combined with the iron oxide can be removed. A higher reducibility indicates more indirect reduction in the blast furnace resulting in lower coke rate and high productivity. Results indicated that acid pellets reduced more compared to limestone pellets, as shown in Fig. 4(d), due to the presence of more amount of low melting point silicate melt between the iron oxide grains in the later. During reduction at high temperature, the slag softens and impedes the flow of reducing gas within the pellet thereby retarding the reduction.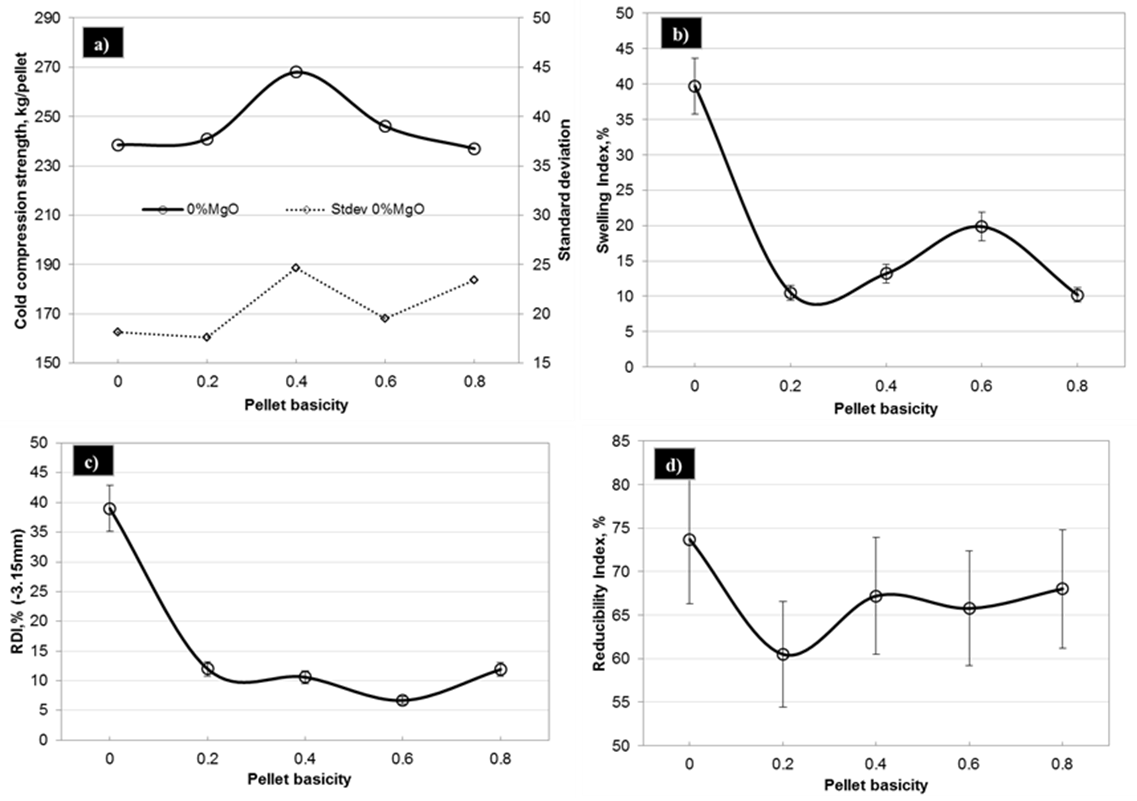 | Figure 4. Metallurgical properties of limestone pellets with varying basicity |
3.2. Pyroxenite Fluxed Pellets
Table 6 shows the chemical analysis of fired pellets with the pyroxenite addition varying from 0% to 10%. Pyroxenite increased the MgO content of the pellets from 0% to 3%.Table 6. Chemical analysis of pyroxenite pellets with varying amounts of MgO 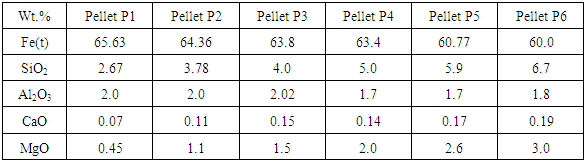 |
| |
|
3.2.1. Quantitative Measures of Microstructure through Image Analysis
Image analysis of these pellets, as shown in Fig.5, revealed that hematite, silicate melt and magnesioferrite are the major phases with some amount of relict or partially assimilated magnesium silicate phase. The amount of relict magnesium silicate phase was found to increase considerably beyond 1.5% MgO content in the pellets. Porosity of pellets decreased with increasing amount of pyroxenite due to the formation of more silicate melt from the silica in pyroxenite.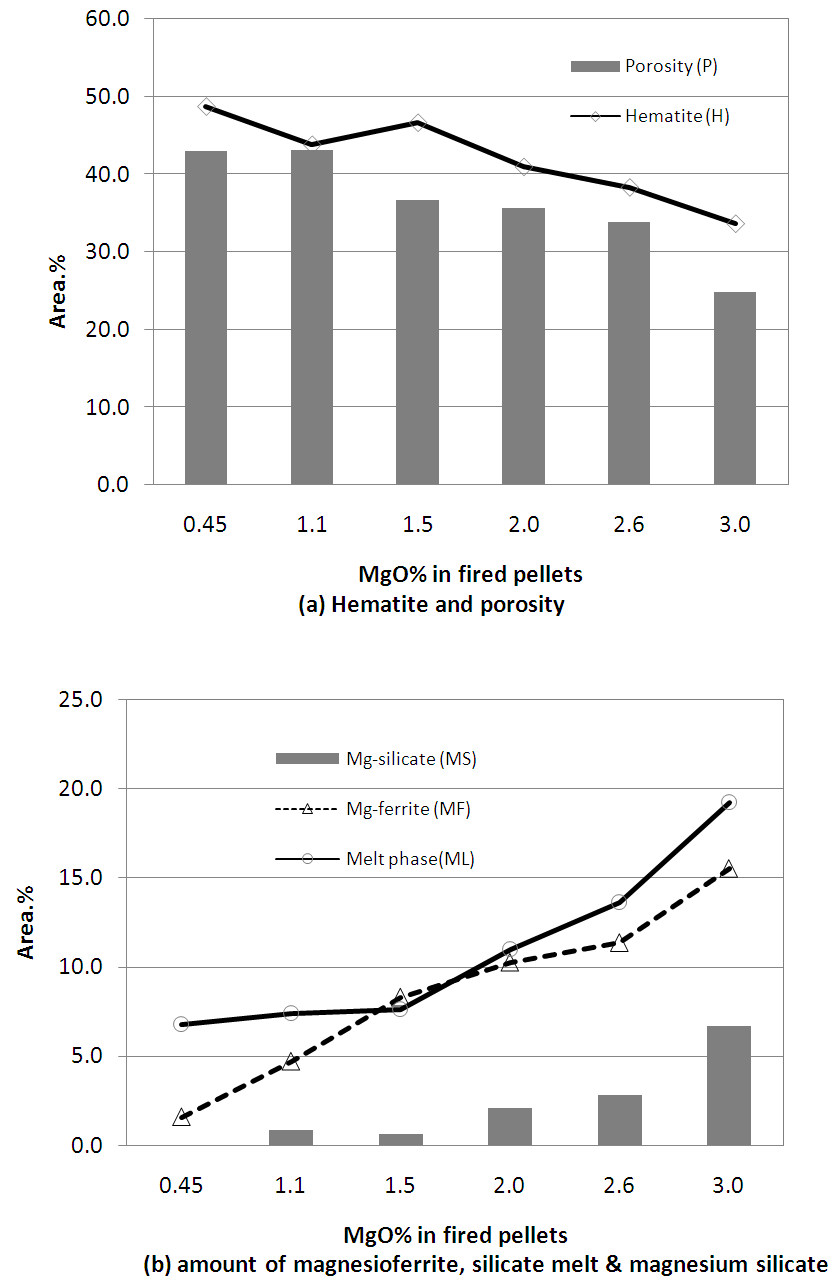 | Figure 5. Image analysis of pyroxenite fluxed pellets showing the amount of different phases varying MgO content |
3.2.2. SEM Study with EDS Analysis
Figure 6 shows the SEM image of Pellets P1 & P3 with EDS analysis of all pellets (P1, P2, P3, P4, P5 & P6). From the results it was evident that chemistry of iron oxide and magnesioferrite phases is uniform in all pellets irrespective of MgO content. But chemistry of slag phase found to be varying with the addition of pyroxenite. FeO content of the slag phase decreased considerably with increased MgO content up to 1.5% (Pellet P3) and thereafter less drop was observed as shown in the Fig.7. X-ray mapping studies of fired pellet samples, as shown in Fig.8, revealed that the MgO from the pyroxenite was distributed only in magnesioferrite and not joined the slag phase. Decreased FeO content of the slag phase by increasing the MgO content (up to 1.5% MgO or 5% pyroxenite) can be attributed to the formation of magnesio-wüstite, which upon cooling leads to the formation of magnesioferrite. Beyond 5% pyroxenite addition, assimilation of pyroxenite into the pellet matrix is poor, as indicated by the increasing amount of relict magnesium silicate phase shown in Fig.5 (b), resulting in no further drop in FeO.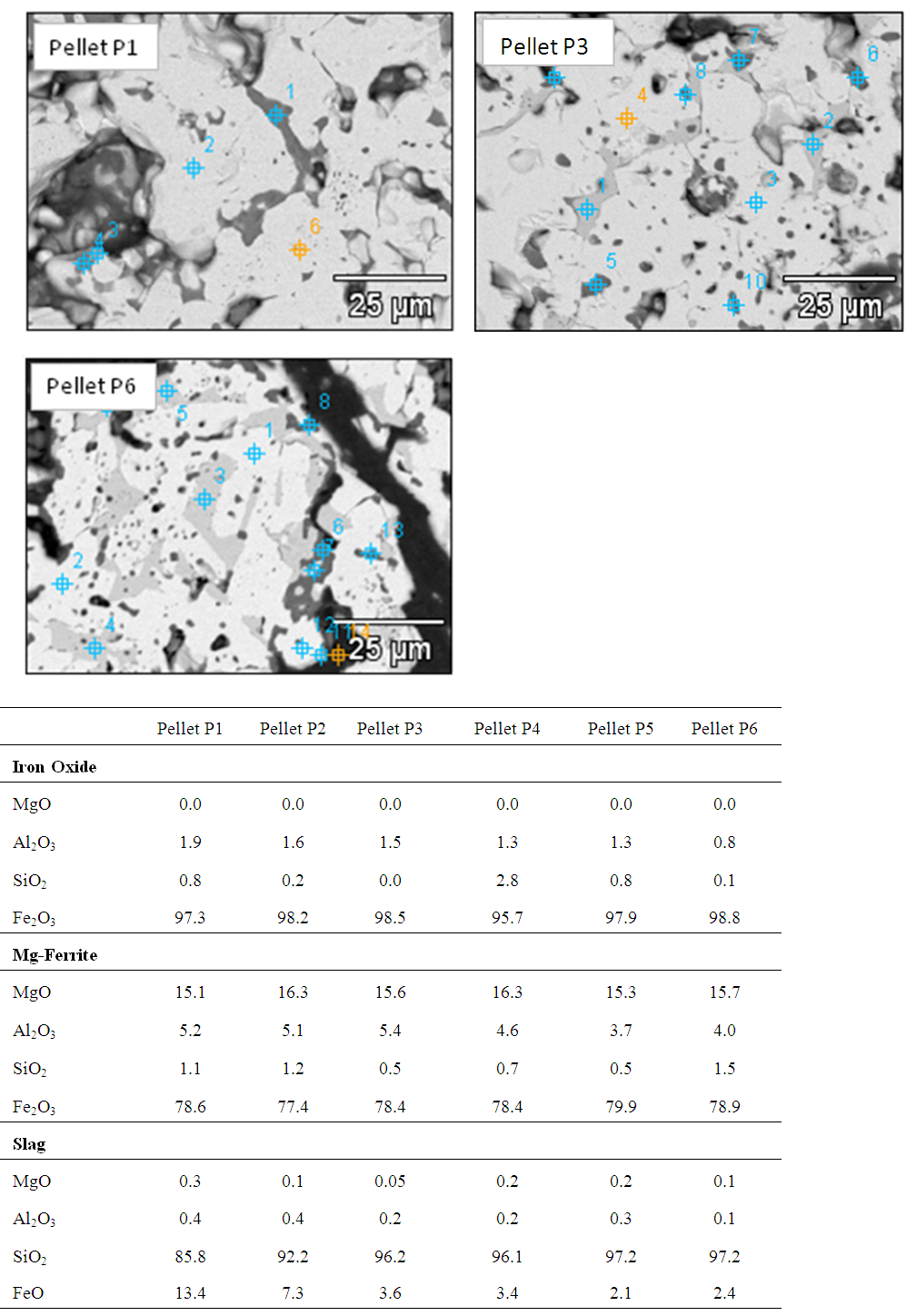 | Figure 6. SEM image of Pellet P1, P3 & P6 with EDS analysis of pellets (P1, P2, P3, P4, P5 & P6) |
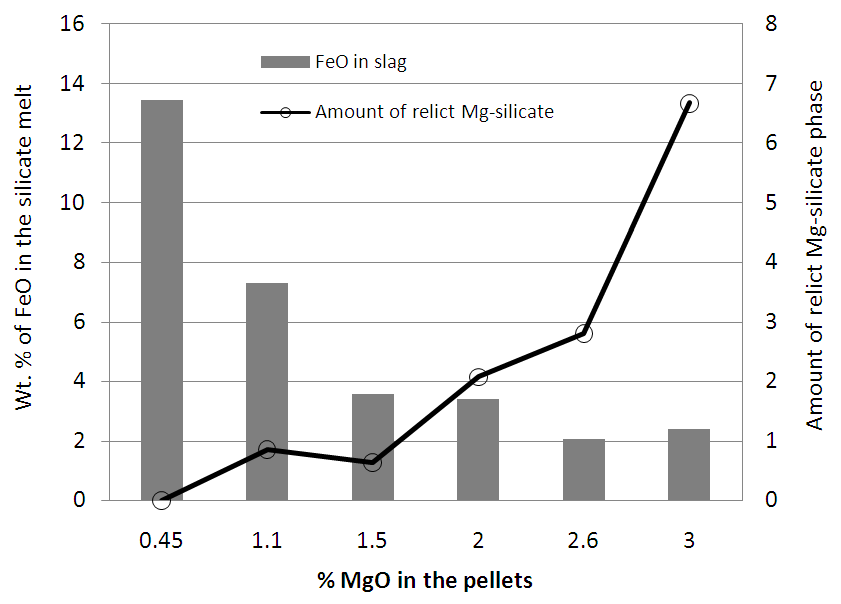 | Figure 7. Effect of MgO on the FeO content of slag phase in the fired pyroxenite pellets |
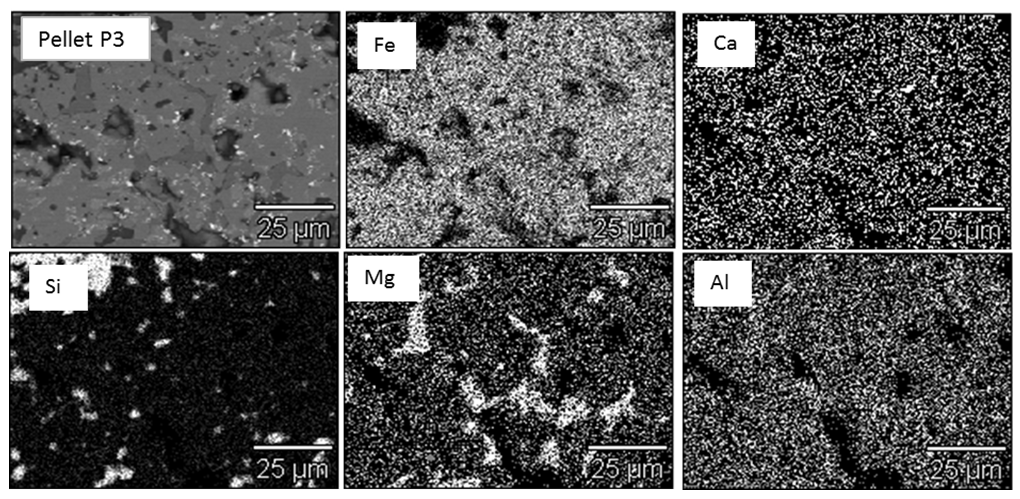 | Figure 8. Distribution of Fe, Si and Mg in 1.5% MgO pyroxenite pellet (Pellet P3) |
3.2.3. Cold Compression Strength
Fig.9 (a) shows the CCS of pyroxenite fluxed pellets. In spite of increased slag phase, CCS of the pyroxenite pellets is comparable to acid pellets and exhibit adequate strength as desired by blast furnace. Porosity of acid pellets is considerably high and decreased with increasing amount of pyroxenite, as shown in Fig.5 (a). In spite of high porosity in the acid pellets, adequate strength is obtained due to the low amount of low strength gangue or slag phase and more sintering between the hematite grains leading to oxide-to-oxide bond or hematite bond. Hematite bonds are strong but they are not stable during their reduction in blast furnace [9]. Addition of pyroxenite resulted in the formation of magnesioferrite and more amount of low strength silicate melt phase, Fig. 5 (b). Silicate melt fills up the pores between solid particles and exerts pressure to pull them together due to interfacial forces thereby reducing the porosity. The negative effect of silicate melt on pellet strength is counteracted by the reduced porosity of pyroxenite pellets.
3.2.4. Swelling Index
Figure 9 (b) shows the swelling index of pellets with varying MgO content. From the results it is evident that swelling index was found to decrease with increase in pellet MgO and a minimum of 1.5% MgO is required to curtail the swelling as desired by blast furnace.During firing, MgO diffuses into the wüstite phase and increases its melting point and also increases melting point of the slag [10]. Increasing the MgO content increases the melting point of wüstite. Low swelling of pellets with increasing MgO content, could be due to the high melting point slag that gives sufficient bond strength to withstand the reduction stresses [8].
3.2.5. Reduction Degradation
Pyroxenite pellets exhibited less degradation with increasing MgO content, as shown in Fig.9 (c). This lower RDI could be due to the formation of magnesioferrite and silicate melt, as shown in Fig. 5 (b), which are more stable phases compared to hematite. Lower FeO content of the melt phase, as shown in Fig.7, also helped in improving its bond strength to withstand the reduction stresses. In addition to silicate melt, magnesioferrite formed between the iron oxide grains also acts as a strong bonding phase that counteracts the reduction degradation [11].
3.2.6. Reducibility
Addition pyroxenite improved the reducibility of pellets, Fig. 9(d), as it increases the MgO and decreases the FeO content of the slag formed inside the pellets, as shown in Fig. 7, thereby increasing its melting point. This kind of slag does not soften at reduction temperatures and keeps the pores open for reducing gas thereby enhancing reduction.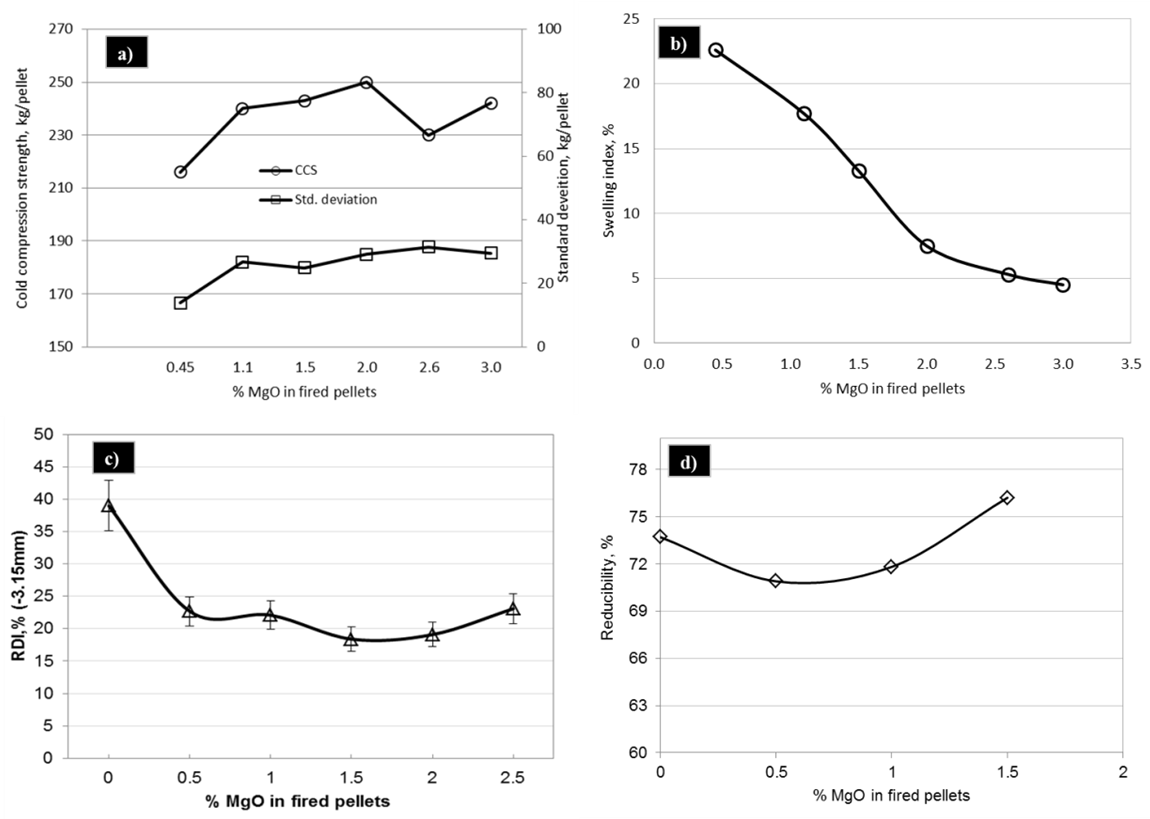 | Figure 9. Metallurgical properties of pyroxenite pellets with varying MgO content |
3.3. Dual Flux Pellets
After commercially implementing the pyroxenite pellets (with around 1% MgO) in the Tata Steel’s 6 MTPA pellet plant, it was observed that their quality was not as expected with poor strength, more dust generation and very high RDI, as shown in the Table 7. It was realized that these pyroxenite pellets were very sensitive to thermal cycle and wide variation in firing profile of indurating machine resulted in poor quality pellets. In addition to this, high grinding energy requirement, wide chemistry variation of iron ore fines, especially high alumina also contributed to the poor quality of pyroxenite pellets. Pellet quality, as desired for blast furnaces, has become a major concern during ramping up of Pellet Plant. For some duration, pyroxenite pellets were discontinued and limestone pellet production was started with CaO levels ranging from 0.4 to 0.8% in the fired pellets. These pellets exhibited good RDI and less dust generation, but very high temperature metallurgical quality viz., softening- melting properties were still not up to the mark, Table 7.Table 7. Quality of pyroxenite, limestone and dual flux pellets produced in the plant 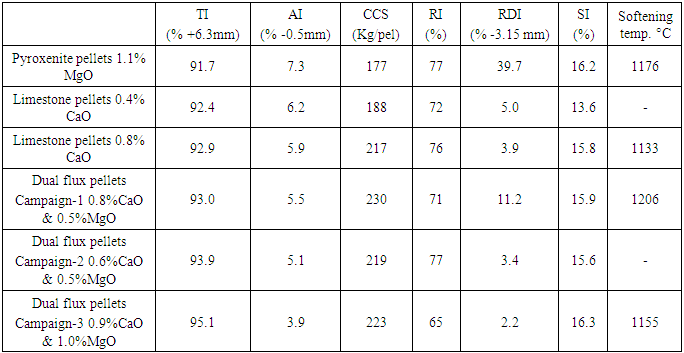 |
| |
|
To understand the reasons behind the poor quality of pyroxenite & limestone pellets, thermodynamic modelling was done for estimating the slag formation inside the pellets during firing. Fact-Sage simulations revealed that in pyroxenite pellets, inadequate melt formation resulted in poor assimilation between gangue and flux, as shown in Fig.10. Bed temperature gradient in the plant firing profile aggravated the problem further leading to poor quality. In limestone pellets, melt formation was adequate to flux the gangue minerals but the lower melting point of the melt resulting in poor softening-melting behaviour of pellet at high temperature in the blast furnace.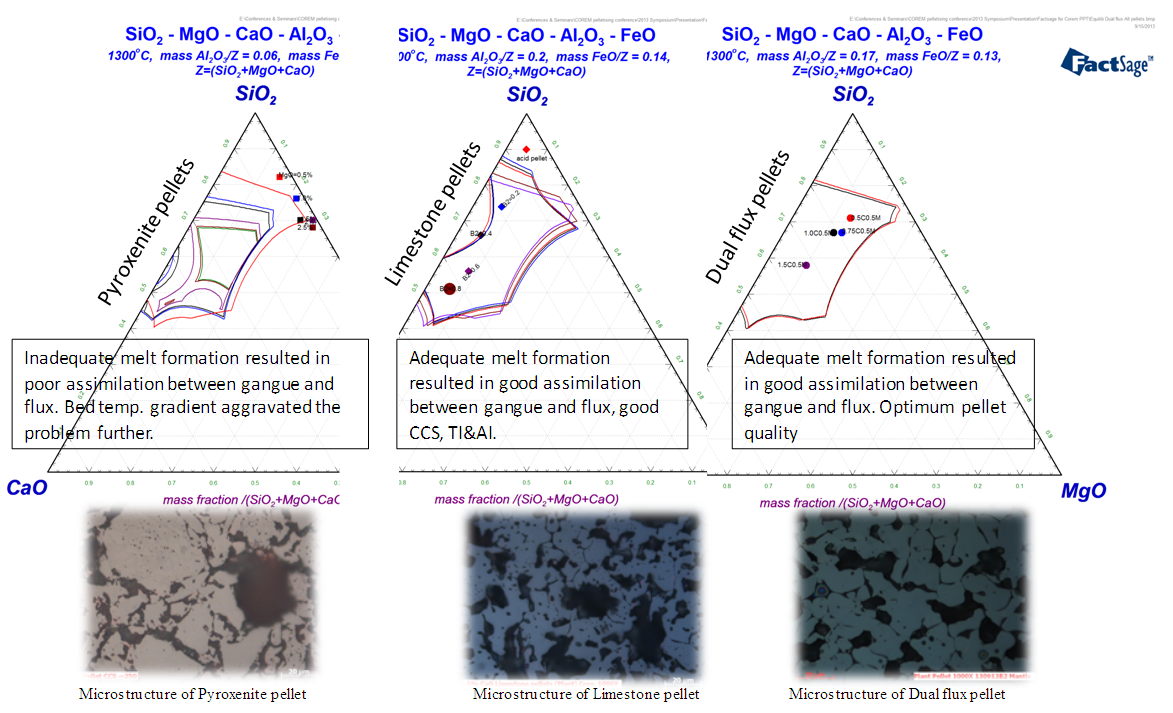 | Figure 10. Fact-Sage thermodynamic simulation of limestone pellets, pyroxenite pellets and dual flux pellets |
To yield the benefits of both CaO (for good strength and RDI) and MgO (for low swelling and high softening), a dual flux combination was established through Fact-Sage simulation. This innovative flux combination consists of carbonate (limestone) and silicate (pyroxenite or olivine) minerals to improve the amount of bonding phases in pellets. This was implemented at the pellet plant in October 2012, which resulted in significant improvement in the cold crushing strength, reduction degradation index and softening temperature of pellets, as shown in Table 8. Additionally, fines generation during pellet making reduced from 7% to 3.3% resulting in ~12% improvement in pellet productivity. Coke rate at the blast furnaces found to be reduced by 1kg for every1% increase of dual flux pellets in the burden.
4. Conclusions
The following conclusions can be drawn from the results of this work:1) Type and amount of flux is vital for pellet quality as it influences the formation of bonding phase during pellet induration and its stability during reduction.2) In the present study limestone and pyroxenite fluxes were studied for their suitability to produce quality pellets for blast furnace.3) With increasing basicity, the amount of melt phase, which acts bonding phase, was found to increase in the fired pellets. FeO content of the silicate melt was decreased with increased basicity of the pellets.4) Acid pellets exhibited highest swelling, whereas maximum swelling in the limestone pellets was observed at 0.6 basicity.5) Pyroxenite /olivine addition to the pellets increased the melting point of slag, due to the presence of MgO and helped in improving the high temperature properties.6) Limestone pellets at 0.8 B2 and pyroxenite pellets at 1.5% MgO exhibited optimum quality.7) During commercial production of pyroxenite pellets, it was observed that pellets were very sensitive to firing temperature due to very narrow range of melt formation which resulted in less amount of melt phase leading to poor quality, especially CCS and RDI.8) Limestone pellets exhibited good RDI and less dust generation, but very high temperature metallurgical quality viz., softening- melting properties were not satisfactory9) To combine the benefits CaO that increases the melt formation and MgO that increases the melting point of the melt phase, dual flux combination was established comprising both limestone and pyroxenite/olivine through Fact-Sage simulation.10) Dual flux pellets resulted in significant improvement in the cold crushing strength, reduction degradation index and softening temperature of. Further fine tuning is under progress at Tata Steel to establish right CaO: MgO ratio for optimum melt formation.
ACKNOWLEDGEMENTS
Author wishes to thank the management of Tata Steel, especially Dr. Sanjay Chandra (Chief R&D and SS), for permitting to use necessary data in this publication. Thanks are also due to Prof. A K Lahiri, (Visiting Scientist, Tata Steel) and Mr. Ashok Kumar (CTO Process) for their valuable inputs towards this project.
Abbreviations

References
[1] | Panigraphy, S.C., Jena, B.C., Rigaud, M., 1990. Characterization of bonding and crystalline phases in fluxed pellets using peat moss and bentonite as binders. Metall. Trans. B. 21B, 463-474. |
[2] | Deqing Zhu, Tiejun Chun, Jian Pan, Jinliang Zhang, 2013. Influence of basicity and MgO content on metallurgical performances of Brazilian specularite pellets, Int. J. Miner. Process. (125), 51-60. |
[3] | Mikko Iljanaa, Antti Kemppainena, Timo Paananenb, Olli Mattilab, Erkki Pisiläb, Mikhail Kondrakovc, Timo Fabritiusa, 2015. Effect of adding limestone on the metallurgical properties of iron ore pellets, Int. J. Miner. Process. (141), 34-43. |
[4] | Arup Kumar Mandal Email author Alok Sarkar Om Prakash Sinha, 2016. Utilization of Lime Fines as an Effective Binder as well as Fluxing Agent for Making Fluxed Iron Ore Pellets, J. of Inst. of Engineers, V97 (1), 69-75. |
[5] | Dwarapudi, S., Devi, T.U., Rao, S.M., Ranjan, M., 2008. Influence of pellet size on quality and microstructure of iron ore pellets. ISIJ Int. 48 (6), 768–776. |
[6] | Dwarapudi, S., Ghosh, T.K, Shankar, A., Tathavadkar, V., Bhattacharjee, D., Venugopal, R., 2010. Effect of pyroxenite flux on the quality and microstructure of hematite pellets, Int. J. Miner. Process. (96), 45-53. |
[7] | Dwarapudi, S., S.M. Rao, J. Murthy, D. D. Parida and K.S. Raju: ‘Effect of activated bentonite on properties of green and fired chromite pellets’, Ironmaking Steelmaking, 2008, 35 (4), 308-314. |
[8] | Frazer, F.W., Westenberger, H., Boss, K.H., Thumm, W., 1975. The relation between basicity and swelling on reduction of iron ore pellets. Int. J. Miner. Process. 2, 353-365. |
[9] | Niiniskorpi, V., 2004. Development of phases and structures during pelletizing of kiruna magnetite ore. PhD thesis, Abo Akademi University, Finland. |
[10] | Onoda, M., Tsuchiya, O., Sugiyama, T., Fujita, I., 1980. Quality improvements of lime fluxed pellets. Proc. of ISS-AIME 40th Iron making conference, Toronto, Ontario Canada, 286-298. |
[11] | Narita, K., Maekawa, M., Shigaki, I., 1977. On the permeability resistance of pellets containing MgO in the softening and melting zone of blast furnace. Trans. ISIJ. 18, 712-720. |