Sri Endah Susilowati, Didit Sumardiyanto
Department of Mechanical Engineering, 17 Agustus 1945 University, Jakarta, Indonesia
Correspondence to: Sri Endah Susilowati, Department of Mechanical Engineering, 17 Agustus 1945 University, Jakarta, Indonesia.
Email: |  |
Copyright © 2017 Scientific & Academic Publishing. All Rights Reserved.
This work is licensed under the Creative Commons Attribution International License (CC BY).
http://creativecommons.org/licenses/by/4.0/

Abstract
This research have been conducted by making of one type of bronze bearing materials Cu-Sn-Zn-C alloy by powder metallurgy method. Powder Metallurgy enables the manufacture of products with controlled levels of porosity in their structure in which the interconnected porosity in the sintered structure is used to hold a reservoir of oil. A self-lubricating sintered bearing is a metallic component with high porosity (20-25% in volume), impregnated in a lubricant oil. The oil contained in the porosity provides a constant lubrication between bearing and shaft, so the system does not need any additional external lubricant. The aim of this research was to determine the effects of sintering temperature on the mechanical properties of a Cu-Sn-Zn-C alloy. The result of this research showed that in 700°C, 750°C and 800°C sintering temperature, the hardness, density, and yield strength values increased, but the rate of wear and porosity values decreased. Meanwhile, at the temperature 825°C, 850°C, 875°C and 900°C, the hardness, density, and yield strength values decreased but the rate of wear and porosity values increased. It happened because at the temperature above 800°C there was rapid diffusion of Sn and Zn to Cu and C alloy which then left a large pore (swelling). Thus, the best value of mechanical properties for a Cu-Sn-Zn-C alloy occurred at the temperature of 800°C with the hardness, rate of wear, density, porosity and compressive strength values were as respectively following 52 BHN, 4.76 x 10-6 mm3/mm, 7.08 gr/cm3, 18,23% and 440 MPa.
Keywords:
Cu-Sn-Zn-C Alloy, Metal Matrix Composite, Sinter, Graphite, Mechanical Properties
Cite this paper: Sri Endah Susilowati, Didit Sumardiyanto, Effect of Sintering Temperature on the Mechanical Properties for a Cu-Sn-Zn-C Alloy Produced by Powder Metallurgy, International Journal of Metallurgical Engineering, Vol. 6 No. 1, 2017, pp. 10-17. doi: 10.5923/j.ijmee.20170601.02.
1. Introduction
Powder metallurgy is the study of the manufacture process of products from metal powder with these following stages: characterization, mixing powders, compacting, until sintering (heating) [1]. Powder metallurgy (P/M) might be chosen as the preferred route for the manufacture of a product. In broad terms, these reasons separate into two categories: (i). Cost effectiveness, P/M is the most cost effective of a number of possible options for making the part and (ii). Uniqueness, some characteristic of the product (e.g. combination of chemical constituents, control over microstructure, control over porosity etc.) can be created by starting from a powder feedstock, which would be very difficult or sometimes impossible in conventional processing [2].Journal bearings are machine elements which provide relative rotational movement between components through sliding movement. Journal bearings must have the expected features, such as low coefficient of friction, high wear resistance, high load capacity and corrosion resistance, good thermal conductivity, low thermal expansion and embedding foreign particles, easy workability and low cost [3]. To obtain high mechanical and tribological properties, journal bearings are produced by alloying in powder metallurgy method [4-6]. To produce porous metallic products, powder metallurgy is the most common method by which the level of porosity and the size distribution of pores are controlled. These properties of the produced parts depends on material composition, pore size and porosity distribution. Pore type, amount, distribution and shape of powder are important to improve the conditions for self-lubricating bearings and regulate the amount of oil impregnated [7]. Porous sliding bearings, due to their oil deposition advantage of about 25% of their volume in the pores, are produced by sintering of metal powders compressed under a certain pressure [8, 9]. During service, oil in pores comes to the surface for lubrication. This is one of the most desired features in bearings. Therefore, P/M techniques are utilized to impregnate oil into machine parts having no possibility of continuous lubricating. Journal bearing materials which are made from copper-based materials have been widely due to properties such as good corrosion resistance, high thermal and electrical conductivity, self-lubrication and good abrasion resistance [10-12].Graphite is always added to improve lubrication. Bronze bearing with the addition of graphite suitable for conditions with heavy loading, high load and high temperature. Graphite added in the process of making bearings serves as lubrication [1]. For bronze bearing, the material composition has 90% Cu-10% Sn with the addition of graphite to 1.5% [2]. Addition of graphite is used to modify friction during application [13]. Additionally, the addition of graphite to copper-tin alloys is also used to control dimensional changes [14].The type of bearing to be made in this study was a type of bronze bearing using weight fraction of 88% Cu, 9% Sn, 3% Zn, and 1.5% C graphite with the different sintering temperature 700°C, 750°C, 800°C, 825°C, 850°C, 875°C and 900°C. The bronze bearing materials has pores, which serves as a storage place lubricant (oil reservoir) so that once inserted into the bearing lubricant, the bearing lubricant needs not be given back because the lubricant is already in the pores of the bearing.
2. Experimental
Copper, tin, zinc powders with a particle size of 65 μm, 65 μm and 42 μm, respectively were used as bronze bearing or as a matrix and graphite powder with 50 μm size was mixed in the blender for 5 minutes. The composition of Cu: Sn: Zn is 88: 9: 3 and the addition of graphite with 1,5% weight fraction. All the powders were prepared then compacted with a pressure of 200 bars for 30 seconds. Green compact with 10 grams of weight each was then sintered in Carbolite furnaces with sintering temperatures varied from 700°C, 750°C, 800°C, 825°C, 850°C, 875°C and 900°C for 5 minutes then furnace cooled. To prevent thermal shock, heating rates were set at 100°C per minute, and held for 10 minutes at 500°C. All samples were characterized both mechanical properties and microstructural analysis.
3. Result and Discussions
3.1. Hardness Test
The hardness testing results that the hardness values increased with the increasing sintering temperature and achieved the optimum hardness at temperature 800°C, which amounted to 52 BHN, then the value of hardness decreased significantly with the increased sintering temperature are shown in Figure 1.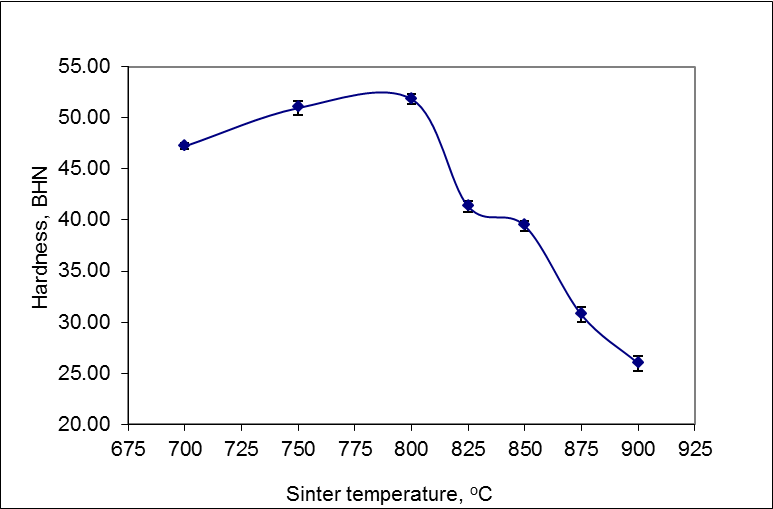 | Figure 1. Effect of sintering temperature on the hardness |
The increased of hardness values occurred due to the liquid phase sintering mechanism through diffusion of atoms in which the liquid phase of Sn and Zn filled the pores between Cu powder or graphite so that the pore was reduced then moistened the grain boundaries of Cu forming a strong bond [13-16]. At the time of liquid phase sintering, mass transfer occurred between Cu or C graphite powder through solid state diffusion so that the density increased. The strong bond and increasing density also caused increasing hardness.The presence of Sn and Zn became crucial due to between Cu and graphite that resulted in poor wetting properties [17], particularly Cu as the matrix that did not undergo a liquid phase. The presence of Sn and Zn in a liquid phase allowed the damping in three ways, namely: (i) by reducing the surface tension between the Cu and Graphite, (ii) by reducing energy interfacial solid-liquid, and (iii) to promote chemical reactions in interface of the solid-liquid [18].However, in temperature above 825°C hardness values decreased significantly. It happened because at high temperatures ranging from 825°C rapid diffusion of Sn and Zn to Cu and graphite then left a large pore (swelling), it also resulted in decreased hardness value [16]. When fast diffusion, there was graphite that was not wetted completely by Sn and Zn so as to form a pore that caused the hardness decreased. When the sintering temperature was raised, the atoms vibrated with greater energy and atoms had enough energy to break the bond and jumped to a new position, a process was called diffusion [19]. There were several kinds of diffusion mechanism during the process of sintering and each diffusion mechanism would give effects to changes in the physical properties of the material after the sintering process, such as changes in density, shrinkage and enlargement granules [16]. The large grains gradually started to increase with increasing heating temperature. Metals with large crystals (coarse grains) the number of crystal grain boundaries were not as much when compared to metal with fine-grained crystals. Coarse granules that had the least amount of grain boundaries than metal with smooth item, so that little hurdle rate also happened to dislocation movement which meant the strength of these metals also declined [19].Crystal boundary or grain boundary of the metal was the junction between the crystals, so that in these areas, the atomic structure became random. As a result, those atoms in the crystal boundaries had a higher mobility than the atoms in the crystal. Therefore, in case of plastic deformation, the dislocation generally occurred in the crystal boundary and then moved into and finally stopped at the next crystal boundary. This meant as well as a beginning point of dislocation, crystal grain boundaries also act as a barrier/obstacle dislocation [19].
3.2. Wear Test
The test result that the rate of ware decreased until the minimum limit. That was 4,76 x 10-6 mm3/mm in temperature 800°C, then increase from 4,78 x 10-6 mm3/mm in temperature 825°C until 6,70 x 10-6 mm3/mm in temperature 900°C (Figure 2).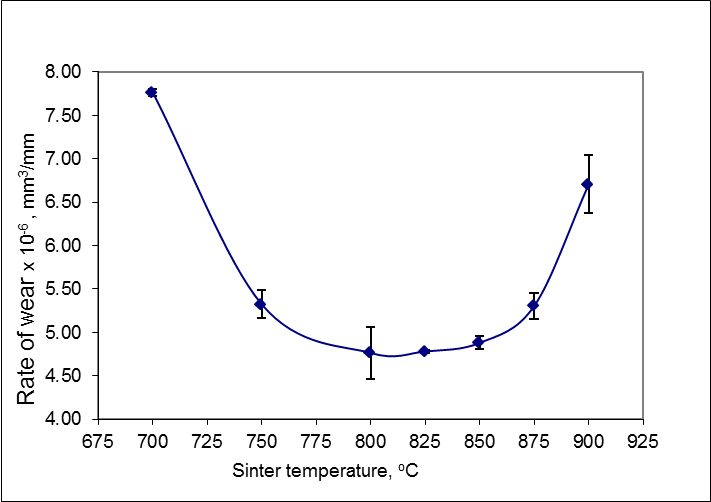 | Figure 2. Effect of sintering temperature on the rate of wear |
The rate of wear value was inversely proportional to the value of the material hardness. The harder a material is, the more wear resistance also increased or the lower rate of wear was low [17]. The rate of wear value decreased to the temperature of 800°C, it was due to their strong bond and the increasing density as a result of the liquid phase sintering and solid state diffusion [13-16]. However, an increase in the rate of wear from the temperature of 825°C (4.78 x 10-6 mm3/mm), 850°C (4.88 x 10-6 mm3/mm), 875°C (5.30 x 10-6 mm3/mm), to the temperature of 900°C (6.70 x 10-6 mm3/mm), it was caused by the declining value of hardness.
3.3. Density Test
Based on density test, the value of density had increase untill at the temperature of 800°C at 7.08 gr/cm3, and the density decreased from the temperature of 825°C at 6.80 gr/cm3 to the temperature of 900°C amounted to 6.27 gr/cm3 (Figure 3).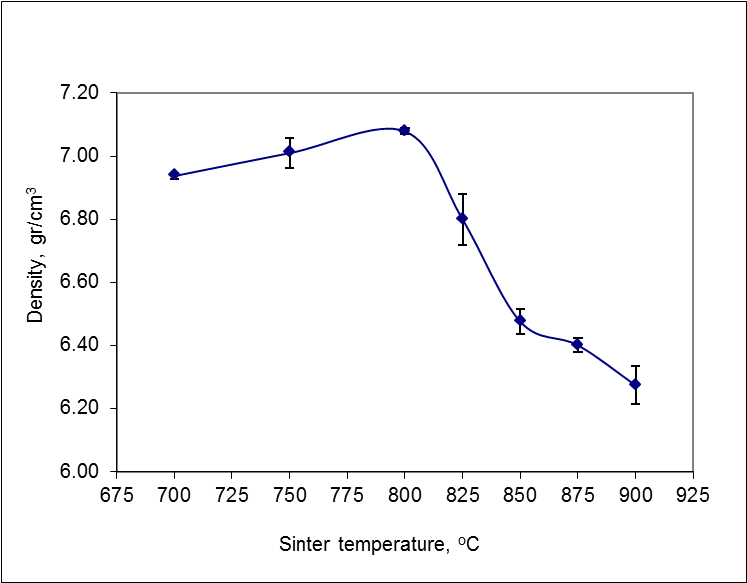 | Figure 3. Effect of sintering temperature on density |
Products made from metallurgy powder process are considered good products if they have high density and low porosity values. It means that the products have experienced good densification so that it increases their mechanical properties. However, because the bronze bearings were applied to porous materials that wear-resistant, the porous was needed as a place to store a lubricant to reduce friction between components [1, 2]. The higher sintering temperature made the tendency of mechanical properties such as density also increased [16]. From the Figure 3, it can be seen a relationship between density and sintering temperature in which the density increased to the optimum temperature (800°C). It was because when liquid phase sintering, there was rearrangement in liquid phase of Sn and Zn which filled the pores between grains of Cu or graphite as well as the displacement of masses through solid state diffusion starting from the point of contact between the particles, the growth of the neck, the unification of the powder so that the density increased. However, the density values decreased significantly from the temperature of 825°C to 900°C. The decreased density is attributed to the swelling as well as the graphite that was not wetted perfectly to form the pore. The decreased density was followed by a decrease in hardness and compressive strength of the material.
3.4. Porosity Test
Porosity value was inversely proportional to the density. The increase of density was followed by the decrease in porosity. Figure 4 shown the relationship of porosity and the sintering temperature indicating the decrease in porosity values from 700°C up to 800°C. This happened because the pores between grains of Cu or graphite were filled by liquid phase Sn and Zn so that the pore was reduced. Before sintering, many pores closed by the point of contact between the particles and pore surface gathered around grains. Then, as a result of the sintering process with sintering temperature 800°C, there was rearrangement of Sn and Zn liquid phase filling the pores between Cu or graphite so that the pore was reduced.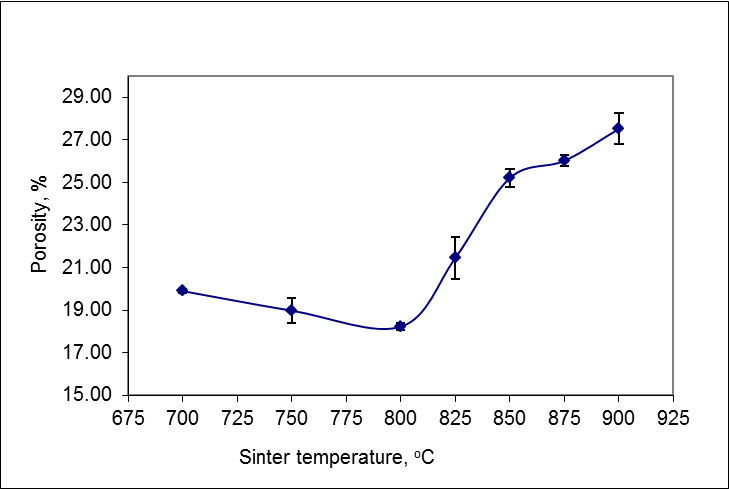 | Figure 4. Effect of sintering temperature on porosity |
Porosity values increased significantly from the temperature of 825°C to 900°C. This occurred because there was rapid diffusion of Sn and Zn to Cu and graphite leaving a large pore (swelling) [5]. Besides, the increase in the number of pores was also caused by incomplete wetting of graphite by Sn and Zn, thus it formed pores in the graphite area. While the sinter 900°C, half of the samples experienced distension. It was because Zn which already began to evaporate at the temperature of 900°C leaving a large pore (Zn’s boiling point 906°C).According to the standard ASM, the porosity value of bronze bearing material is ranged between 25-35% [13] and some references also mention for certain applications porosity values ranging between 10-35% [20]. So one type of bronze bearing materials Cu-Sn-Zn-C alloy have been conducted with porosity values obtained in this study is still in the range of standard value (safe condition) as a storage place for the application of lubricant wear resistant material.
3.5. Compressive Strength Test
The compressive strength increased up to a temperature of 800°C with a value of 440 MPa, then decreased from 825°C temperature of 419 MPa at the temperature up to 900°C amounted to 275 MPa (Figure 5).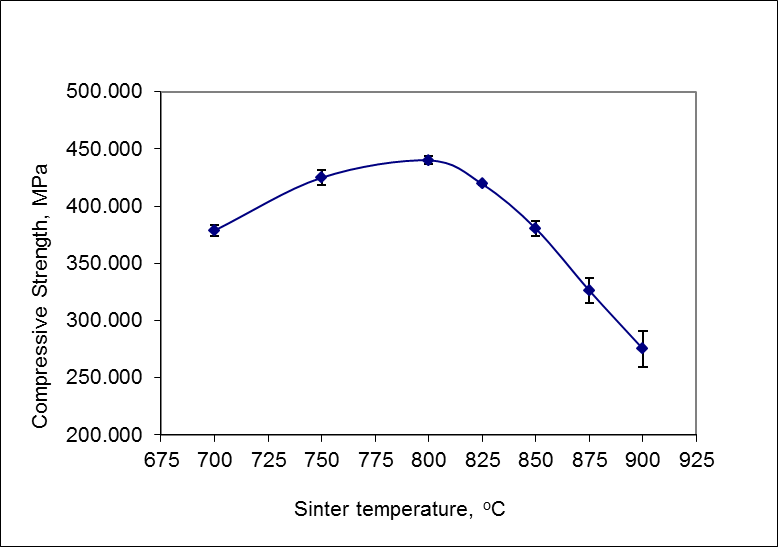 | Figure 5. Effect of sintering temperature on compressive strength |
This happened because of their strong bond and increase in density along with the increase of temperature up to 800°C through liquid phase sintering and mass transfer through solid state diffusion which involved diffusion of atoms or particles, but above the sintering temperature 800°C the compressive strength decreased significantly. The compressive strength was positively correlated with the hardness and density, but negatively correlated with porosity values.
3.6. Microstructure Observation
The result of microstructural photograph can be seen that with increasing of sinter temperature from 700°C to 800°C happened pore reduction (Figure 6a,b) then with sinter temperature rise 850°C to 900°C happened pore enlargement (Figure 6c,d). This might indicate a densification followed with downsizing as the pore was filled by pore liquid phase up to the temperature 800°C. Meanwhile, at the temperature of 850°C up to 900°C (Figure 6c,d) the size of the pores got larger due to their swelling.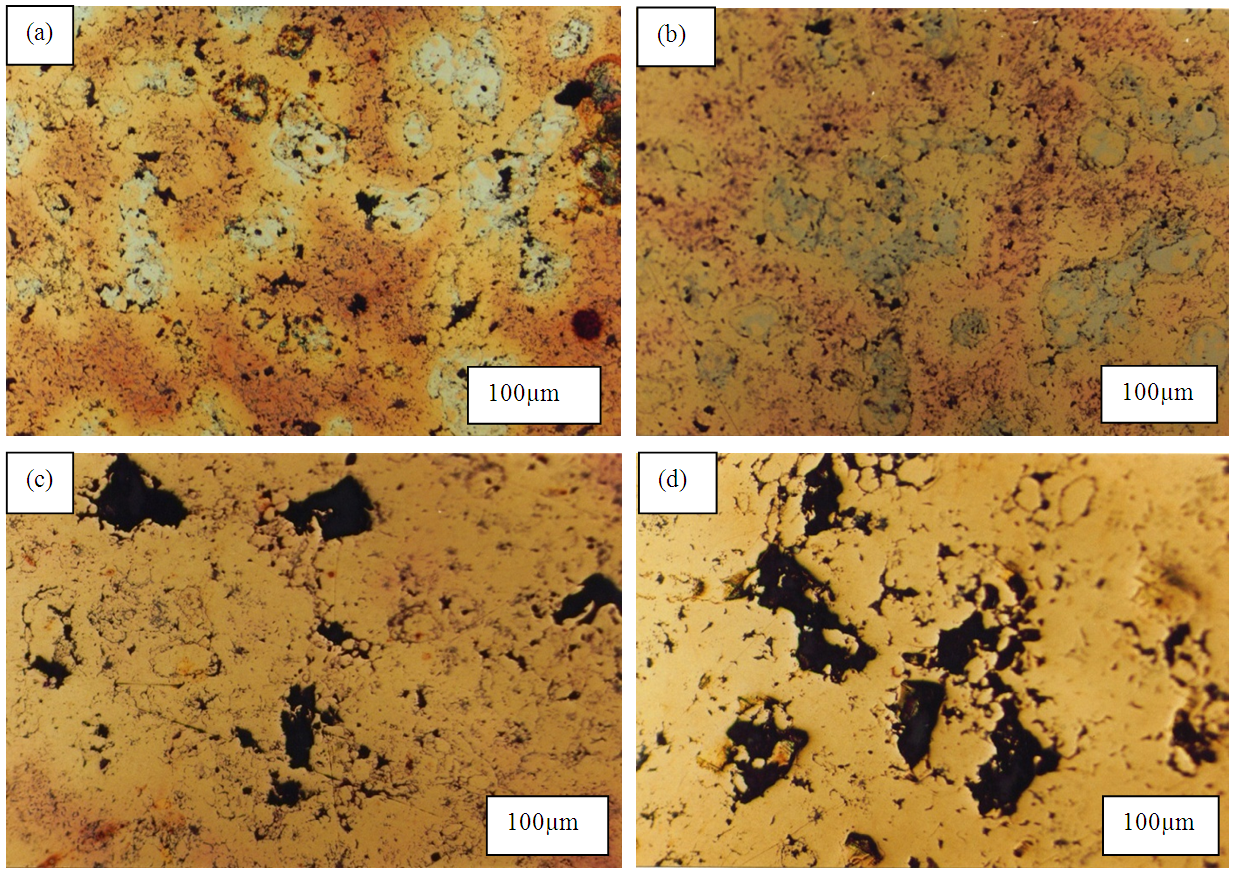 | Figure 6. Microstructure sample with sintering temperature at (a) 750°C (b) 800°C (c) 850°C (d) 900°C |
Although the mechanical properties of the test material in the sintering temperature 825°C up to 900°C decreased, the pores could also function as a store of lubricant (oil reservoir) for the application of the bearing material. Oil stored in the pores pads would function as self - lubricant when the bearing was used. Therefore, the material self - lubricated bearings had a percentage of porosity with the range of 25 to 35% of course while considering the required mechanical properties [2].
3.7. SEM Observation
Observation with SEM showed non sinter graphite sample packs and evenly spread with a lot of void around the graphite (Figure 7). In the observation by using an optical microscope, it was not apparent yet.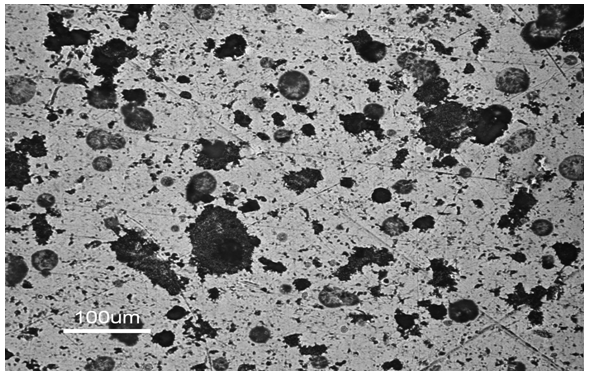 | Figure 7. Non sinter microstructure sample with SEM |
The microstructure particles after sintered was different from the microstructure before sintering, with the increasing sintering temperature of 700°C to 800°C a reduction in pore and pore distribution even than non-sintered samples (Figure 8a). This is indicated by the densification followed by the reduction of the pore due to the pore fillings by the liquid phase of Sn and Zn [18]. With increasing sintering temperature 850°C the pores appeared larger (Figure 8b).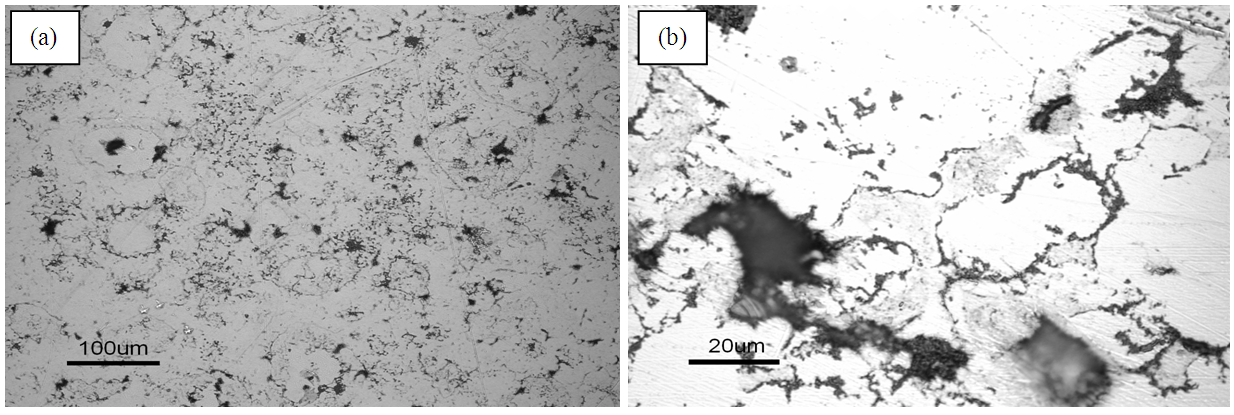 | Figure 8. Microstructure sample sintering with SEM at (a) 800°C (b) 850°C |
3.8. EPMA (Electron Probe Micro analyzer) Observation
Microstructure results in compaction which still formed the bulk of green, not yet sintered, as observed by EPMA showed that they gathered Sn concentration (Figure 9a). This was due to the condition of non sinter Sn and Zn which served as a wetting agent had not experienced the liquid phase. The strength properties of the material non-sinter powder metallurgy products were more affected by their mechanical strengthening (cold weld and mechanical interlocking) [21].The results of EPMA with sintering temperature 800°C showed Sn melted and diffused into the Cu forming CuSn phase (Figure 9b). At the sintering temperature above 800°C up to 900°C the size of the pores got larger and the number of pores significantly increased. This pore enlargement signified rapid diffusion of Sn to Cu and resulted in decreased material strength [16].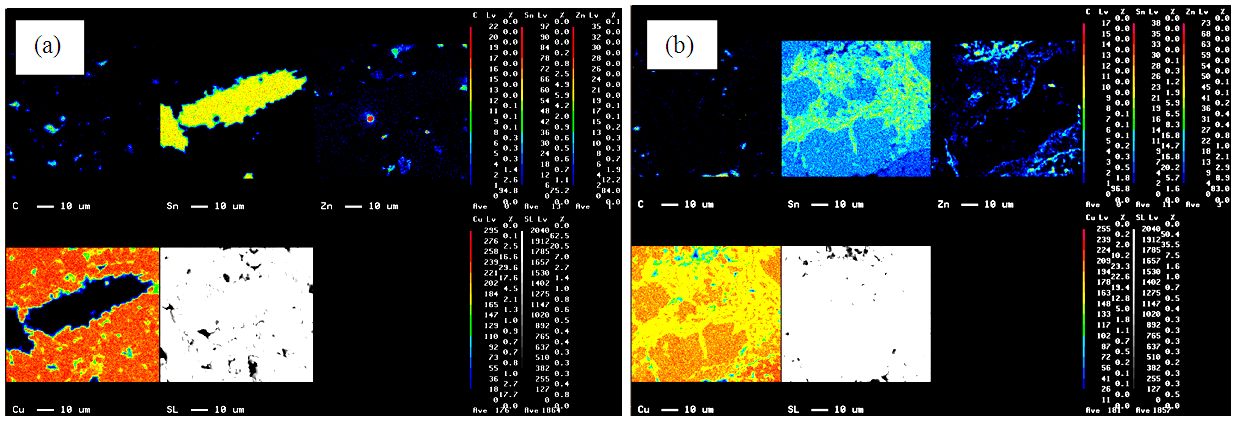 | Figure 9. Microstructure sample EPMA at (a) Non Sinter (b) 800°C |
The microstructure particles after sintered was different from the microstructure before sintered. Sintering process required heating so that the fine particles could be transformed into the solid ones. It required a high temperature below its melting point temperature. The result showed that with the increasing sintering temperature of 700°C to 800°C there was a reduction in pores and pores evenly distributed compared to the non-sintered sample. This showed that there was densification followed by pore shrinkage because the pores were filled by the liquid phase of Sn and Zn [18]. During the sintering process, the pores became smaller and the size of grains changed. In addition, the high heat raised the recrystallization process that was the process of formation of new crystals followed by grain growth process. Microstructure gradually started to be coarse with the increase of heating temperature [22].
3.9. Characterization by XRD
The diffraction pattern sample Cu-Sn-Zn-C alloy with non sinter treatment resulted in two phases, namely Cu and Sn (Figure 10a). For Zn phase that was not identified, this occurred because the concentration of Zn was small (only 3%). In the non-sintered samples, the alloy has yet to form so that there were only pure phases as in their constituent particles. Cu phase was indicated by the diffraction peaks with orientation hkl (111), (200), (220), (311) and (222), the space group F - centered cubic (Fm-3m) and the lattice parameters a = b = c = 3.615 °A. For Sn, it was indicated by the orientation hkl diffraction peak (200) and (411), the space group I - centered tetragonal (141 / amd) with lattice parameters a = b = 5,819 °A and c = 3.175 °A.Diffraction Patterns and Crystal Structure for Sinter Sample 700°CSample identification with sintering temperature of 700°C, identified the dominant Cu phase and just a few of Cu3Sn phase (Figure 10b). The visible Cu phase is still the same as the phase in the non-sinter sample and is shown by the diffraction peaks with the hkl orientations (111), (200), (220), (311) and (222) with the F-centered cubic space group (Fm-3m ) and lattice parameters a = b = c = 3.615°A. For Cu3Sn phase represented by diffraction peak with hkl orientation (0160), (002) and (2120)) with group space Cmcm and lattice parameter a = 2.749°A, b = 2.749°A and c = 4.322°A.At sintering temperature 700°C there is still Cu phase and there is a few of Cu3Sn. This is because at that temperature there is only a small amount of Sn and Zn diffusing into Cu, especially with a short sinter resistance time (5 minutes) has not formed alloy.Diffraction Patterns and Crystal Structure for Sinter Sample 800°CThe process of sintering the Cu-Sn-Zn and graphite with a sintering temperature of 800°C produced Cu20Sn6 dominant phase, besides there was still Cu phase (Figure 10c). For Cu20Sn6 phase, it was indicated by the orientation of the field hkl peak (300), (113) and (106) with the space group P63 and lattice parameters a = b = 7.330 °A and c = 7.864 °A. While the Cu phase was indicated by the orientation hkl diffraction peak (111), (200) centric space group F - centered cubic (Fm-3m) and the lattice parameters a = b = c = 3.615 °A. At sintering temperature of 800°C a liquid phase sintering mechanism takes place through the diffusion of atoms where the liquid phase Sn and Zn fill the pores between Cu and graphite powder and also moisten the Cu grain boundary to form a bond [13, 16]. Sn diffuses with Cu to form Cu20Sn6 alloys, in the presence of these alloys also causing increased hardness of material properties.Diffraction patterns and Crystal Structure for Sinter Sample 850°CThe diffraction pattern of samples Cu-Sn-Zn and graphite with sinter treatment of 850°C can be seen in Figure 10d. Samples with sintering temperature of 850°C, they produced dominant Cu39Sn11 phase and there was still Cu phase. For Cu39Sn11 the phase was indicated by the orientation of the field hkl peak (660), (844) and (888) centric space group F - centered cubic (F43m) and the lattice parameters a = b = c = 18.01 °A. While the Cu phase is indicated by the orientation hkl diffraction peak (111), (200) and (220) centric space group F - centered cubic (Fm-3m) and the lattice parameters a = b = c = 3,607 °A. At 850°C there is a phase change from Cu20Sn6 to Cu30Sn11. At this temperature Zn starts to evaporate (boiling point Zn = 906°C) to form Zn oxide on the sample surface.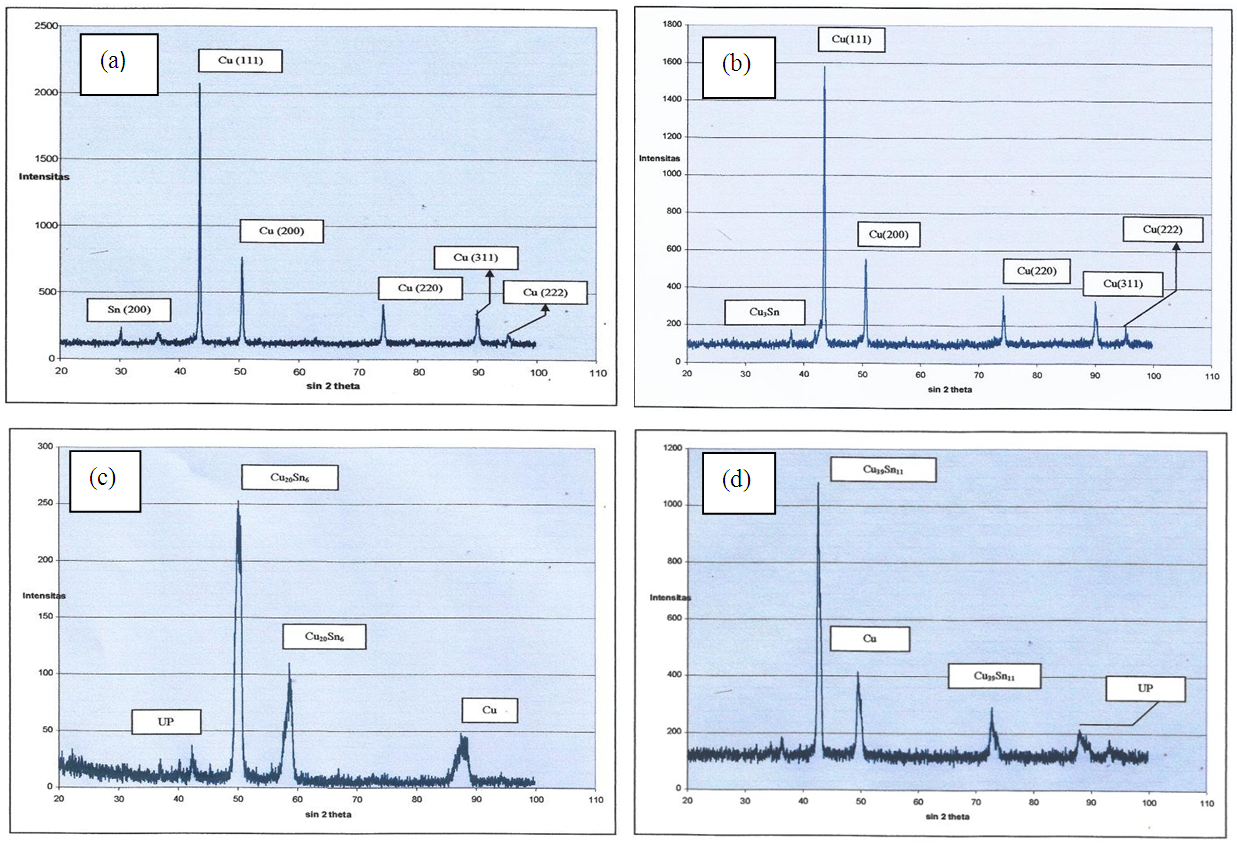 | Figure 10. Diffraction patterns and crystal structure at (a).non sinter (b) 700°C (c) 800°C (d) 850°C |
4. Conclusions
This study concluded that:1. One type of bronze bearing material Cu-Sn-Zn-C Alloy can be made by powder metallurgy method.2. Sinter temperatures affect on the mechanical properties of Cu-Sn-Zn-C Alloy material.3. At sinter temperature 800°C, the mechanical properties of Cu-Sn-Zn-C Alloy reach optimum value. At this temperature, the values of hardness, density, compressive strength, porosity and wear rate are respectively: 52 BHN, 7.08 gram / cm3, 440 MPa, 4.76 x 10 -6 mm3 / mm and 18.23%.4. However, the increase in the sintering temperature above 800°C (in this research 825°C, 850°C, 875°C and 900°C) cause the hardness value, density and compressive strength decrease but the rate of wear and porosity value increase.5. From the results of microstructure photo observations, visible pore size is getting smaller with the increasing temperature up to 800°C. After 800°C, the size of pores gets larger. This is due to densification occurs and the diffusion between Sn and Zn (liquid phase) in Cu and graphite. The function of Sn and Zn is as a wetting. From the results of XRD, it shows that Sn diffuses into Cu, it is shown by the appearance of Cu20Sn6 phase at the temperature of 800°C and Cu39Sn11 phase at the sintering temperature above 800°C. The Cu20Sn6 phase is suspected of causing the material strength to increase.6. At the sintering temperature above 800°C, Sn diffuses quickly and leaves the pores causing swelling (enlarged pore size) and the material strength to decrease.
References
[1] | Metal Powder Industries Federation, Powder Metallurgy Design Manual 2nd Edition, Priceton USA, 1995, pp. 74-76. |
[2] | ASM Handbook Volume 2, Properties and Selection: Nonferrous Alloy and Special-Purpose Materials, USA: ASM International, 1990, pp. 392-530. |
[3] | Unlu B.S, Journal Bearings Powder Metallurgy, Vol. 54, 2011, pp. 338-342. |
[4] | Kumar A & Kumar P, Indian Journal of Engineering & Material Sciences, Vol. 3, 1996, pp. 57-62. |
[5] | Eksi A & Kurt A, Nat Powder Metallurgy Conf, Turkey, 1999, pp. 565-557. |
[6] | Kadir Gungor et.all, Indian Journal of Engineering & Material Sciences, Vol. 22, 2015, pp. 288-296. |
[7] | Durak E & Duran F, International Journal Fatigue, Vol.30, 2008, pp.745-755. |
[8] | Morgan V.T, Porous Metallurgy Bearings, 1970. |
[9] | Improving performance from self-lubricating bronze bearings, Metal-Powder.net, 2007. |
[10] | Schmidt R F, Schmidt D.G, ASM Handbook (II), 1993, pp. 346-357. |
[11] | Eisen W B & German R.M, ASM Handbook, vol 7, 1998, pp.1051-1057. |
[12] | Prasad B K, Metall Trans A, A-28, 1997, pp. 809-815. |
[13] | German, Randall. M, Sintering Theory and Practice, New York: John Willey & Sons, Inc., 1996 pp.8-534. |
[14] | ASM Handbook Volume 2, Powder Metal Technologies and Applications, USA: ASM International, pp. 863-1054. |
[15] | Goetzel, Claus G, Treatise on Powder Metallurgy Volume I-a, Technology of Metal Powders and Their Products, pp. 198-199. |
[16] | German, R.M, Powder Metallurgy Science, United States of America, 1984, pp. 2-192. |
[17] | ASM Handbook, Composite, USA: ASM International, 1990, pp. 169-170. |
[18] | Zulfia, Anne, Jurnalteknologi: Effect of Processing Temperature on PureAl/SiC Metal Matrix Composites Produced by The Lanxide Process, Jakarta, 2001, p. 203. |
[19] | Wulpi, Donald. J, Understanding How Components Fail, American Society for Metals, Ohio, 1995, pp. 36-37. |
[20] | www.sdp-si.com/herb/spk/sdp-si/D200/PDF/D200_T16.pdf |
[21] | Chandrawan, Myrna Ariati, Powder Metallurgy, Theory and Application, Jakarta, 1999, pp. 5-67. |
[22] | Aghajanian M.K., Properties and Microstructure of Lanxide Al2O3-Al Ceramic Composite Material, Journal of Material Science, USA, 1989, pp. 658-670. |