Md Israr Equbal1, Parwez Alam1, Rajkumar Ohdar2, Kumar Aniket Anand3, Md. Serfraj Alam3
1Department of Mechanical Engineering, Cambridge Institute of Technology, Tatisilwai, Ranchi, India
2Department of Forge Technology, National Institute of Foundry and Forge Technology, Ranchi, India
3R&D Centre for Iron and Steel, Steel Authority of India Limited, Ranchi, India
Correspondence to: Md Israr Equbal, Department of Mechanical Engineering, Cambridge Institute of Technology, Tatisilwai, Ranchi, India.
Email: |  |
Copyright © 2016 Scientific & Academic Publishing. All Rights Reserved.
This work is licensed under the Creative Commons Attribution International License (CC BY).
http://creativecommons.org/licenses/by/4.0/

Abstract
Medium carbon steel is being widely used for machinery structural parts. The microstructure, tensile and impact behaviour of a commercial medium carbon forging steel (AISI 1035) have been determined before and after forging with respect to different cooling conditions in a hydraulic press at 950°C. Final microstructures and mechanical properties were evaluated by optical microscopy, hardness, tensile and impact tests. The results indicated that the microstructures of all forging and cooling conditions are dominated by ferrite and pearlite phases with different morphologies and grain sizes according to various cooling rate. Oil quenching leads to a formation of relatively fine ferrite and pearlite grains in comparison to normal air and forced air cooling. Relatively fine ferrite, pearlite increase strength but decrease ductility. The cooling rate has a remarkable effect on the microstructure and mechanical properties at room temperature.
Keywords:
Forgeability, Hydraulic press, Ferrite, Pearlite
Cite this paper: Md Israr Equbal, Parwez Alam, Rajkumar Ohdar, Kumar Aniket Anand, Md. Serfraj Alam, Effect of Cooling Rate on the Microstructure and Mechanical Properties of Medium Carbon Steel, International Journal of Metallurgical Engineering, Vol. 5 No. 2, 2016, pp. 21-24. doi: 10.5923/j.ijmee.20160502.01.
1. Introduction
Medium carbon steels are widely used for many industrial applications and manufacturing on account of their low cost and easy fabrication [1]. Mechanical properties of these steels are strongly connected to their microstructures obtained after various thermo-mechanical treatments, based on controlled cooling after hot deformation. Among hot deformation processes, forging has become a competitive technique for processing such steels. Forging technology is known for producing parts of superior mechanical properties with minimum waste. It is a manufacturing process where metal is pressed, pounded or squeezed under great pressure into high strength parts. In hot forging a heated up billet is pressed between a die set to a nearly finished product [2]. Large numbers of solid metal parts are produced in aluminium alloys, copper alloys, steel or super-alloys where irregular shapes need to be combined with good mechanical properties. In metal forging process the quality and performance of the forged product is heavily dependent on various parameters. The cooling rate after finishing deformation stage has a significant effect on the mechanical properties through engendering a variety of microstructure constituents that alter significantly the mechanical properties. Higher cooling rates lead to a decrease of ferrite grain size and formation of high strength, hardness, dislocation density, and fine phases because it suppresses the atomic diffusion. Whereas slow cooling rates lead to transformation into soft, coarse and less dislocated phases like polygonal ferrite. The size and percentage distribution of ferrite and pearlite within the microstructure play an important role on the final mechanical properties [3]. A variety of microstructures in medium carbon steels can be obtained depending on the forging parameters utilized and the post-forging cooling rate [4-7]. The present investigation is aimed to study the effect of cooling rate after controlled hot forging on the microstructure and mechanical properties of medium carbon steel 35C8 (AISI 1035). The different mechanical properties like yield strength, ultimate tensile strength, percentage elongation, impact strength and hardness obtained are correlated with microstructure using high magnification optical microscope.
2. Experimental Procedure
The chemical composition and mechanical properties of medium carbon steel samples used for present investigation is listed in Table 1 and 2 respectively. The steel was supplied in the form of 75 RCS billets of 100mm in length. Prior to the hot forging the specimens have prepared for required size 60×90 mm by a power hack saw machine. The prepared stocks were heated to 950°C in an electrical muffle furnace. All forgings have been completed in between flat dies of 150 ton hydraulic press by a thickness reduction (40% strain induced, respectively) at constant strain rate. Two to three times heating were required during the process of forging to get the required reduction. The forged steel samples have been cooled in normal air (NA), forced air (FA) and quenching oil (OQ) respectively.Table 1. Chemical Composition of Experimental 35C8 steel in (wt. %)  |
| |
|
Table 2. Mechanical Properties of Experimental 35C8 Steel  |
| |
|
Specimens for metallographic analysis were cut from the hot forged samples in the transverse direction. The specimens were polished for microstructure observations. The microstructural characterization was carried out by optical microscopy (OM) under polarized light. Mechanical properties were measured using tensile, charpy impact and brinell hardness tests. Figure 1 shows schematic of samples for tensile and charpy impact test.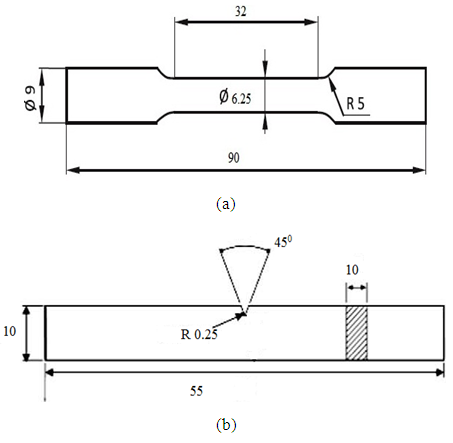 | Figure 1. A schematic of test specimens: (a) tensile testing specimen and (b) Charpy testing sample. Dimensions in mm |
Tensile strength and Charpy impact energy value has measured at room temperature according to the standard ASTM A 370-05 [8]. Tensile tests were performed on a Universal tensile-testing machine (INSTRON 1195), equipped with a 100 kN load cell and a clip-on extensometer at a crosshead speed of 2 mm/min. Test pieces of round cross-section, with original gauge length l0 = 30 mm and original diameter d0 = 6 mm, were used for the tests. Yield strength (YS), Ultimate tensile strength (UTS) and Elongation to failure (%El) were measured. Charpy impact test were carried out in an instrumented charpy impact testing machine (M/S Tinius Olsen, USA). Charpy impact specimens of 10 x 10 x 55 mm3 dimensions, with 2 mm V-notch were used for the tests. Hardness measurements were also carried out using the Rockwell hardness tests under the application of 100 kg laod (HRB).
3. Results and Discussion
Microstructure The microstructures of as received sample as well as samples deformed at 950°C and followed by normal air cooling, forced air cooling and oil quenching are shown in Fig. 2. It is observed that depending on the different thermo-mechanical conditions, a variety of microstructures may be obtained. The variation in mechanical properties in AISI 1035 medium carbon steel can be explained in terms of microstructure obtained after forging followed by different cooling rates. Table 3 shows volume fraction of ferrite and pearlite and grain sizes (ASTM No.) in as-received, normal air, forced air and oil cooled samples. Microstructural analysis indicates that volume fraction of ferrite is decreased with increasing cooling rate (Table 3). These effects are generally associated with the influence of cooling rate on the coalescence and growth rates of ferrites [5]. Microstructure of as received material (Fig. 2a) mainly consists of coarser ferrite and pearlite structure. Normal air cooled sample (Fig. 2b) reveals coarse ferrite and pearlite grains with volume fraction of pearlite content of around 40%. Forced air cooled sample (Fig. 2c) reveals finer ferrite and pearlite grains than normal air cooled sample with higher amount of pearlite. Whereas OQ sample (Fig. 2d) reveals relatively finner ferrite and pearlite grains than normal and forced air cooled samples with maximum amount of pearlite content. With increase in cooling rate the grains become finer due to faster cooling rate. An increase in the cooling rates lowers transformation temperature and ferrite-pearlite form at lower temperature resulting in finer ferrite and pearlite grains [9].Table 3. Volume fraction of ferrite and pearlite and grain size (ASTM No.) of as received, normal air, forced air and oil cooled samples 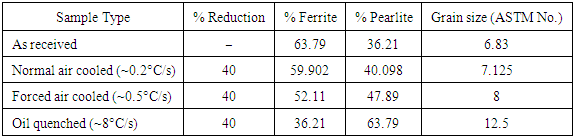 |
| |
|
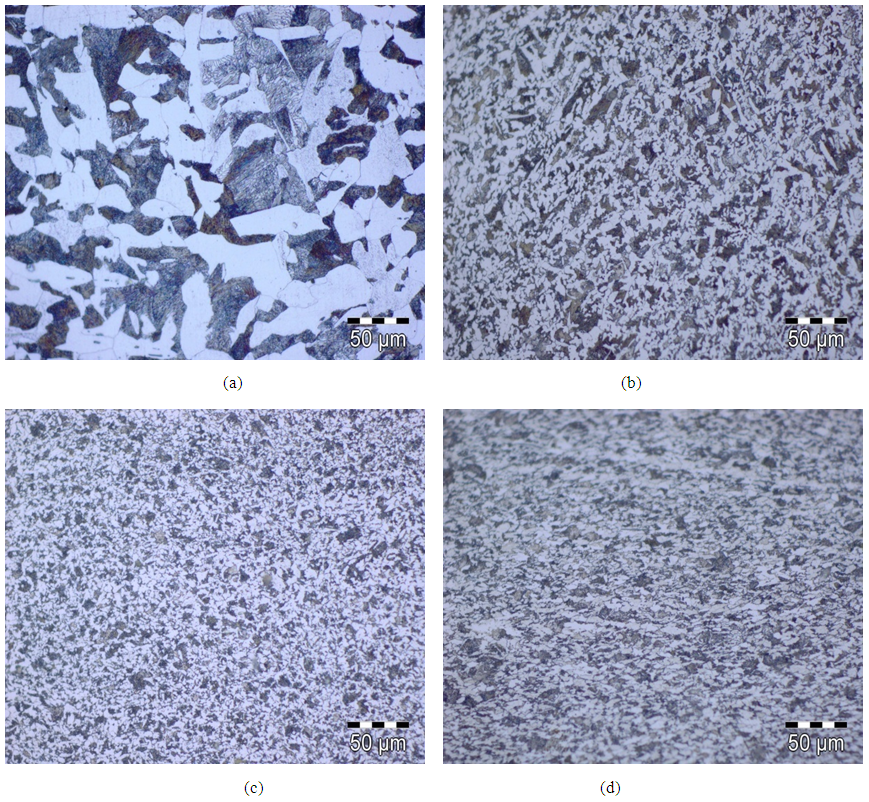 | Figure 2. Microstructures of 35C8 steel under conditions of (a) as-received, (b) normal air, (c) forced air and (d) oil cooled |
MECHANICAL PROPERTIESIt is seen from Fig. 3a that the tensile and the yield strength increase with increasing cooling rate (from NA to FA to OQ). The hardness measurement indicated that water quenched samples had higher hardness compared to normal air and forced air cooled samples. It was also found that forced air-cooled samples had higher hardness than normal air cooled samples due to higher cooling rates. Fast cooling rate was anticipated to give a fine dispersion of small particles in the pro-eutectoid ferrite and pearlitic ferrite which make dislocation movement more difficult and increase hardness. As the strength increase there is a corresponding decrease in percentage elongation and impact energy values (Fig. 3b). The UTS and YS values increase from 649.77 to 722.69 MPa and 406.05 to 519.09 MPa respectively as the cooling rates increase from NA to OQ. Whereas, the increase in strength from NA to FA was evident, the oil quenched sample showed a significant increase in terms of UTS/YS with marked decrease in elongation value comparison to NA and FA samples. This is due to the presence of finer ferrite pearlite structure. The lowest value of UTS/YS achieved in NA sample is due to the presence of microstructure that is dominated by coarser ferrite and pearlite structure. With faster cooling rate (from NA to FA), the transformation temperature is lowered there by resulting in finer ferrite - pearlite structures. Moreover, the lamellae produced through faster cooling are finer. This in turn increases the strength. With the increase in cooling rate from NA to FA to OQ, the charpy impact energy value decreased. The drop in the impact energy value between NA and FA was smaller than between FA and OQ. The increase in cooling rate led to the formation of finer and harder phases in the microstructure with a consequent decrease in ductility values as well as CIE. Whereas, the OQ samples exhibited least CIE value because of harder micro constituents, the NA samples reflected the highest CIE values on account of the softer and coarser ferrite-pearlite structures.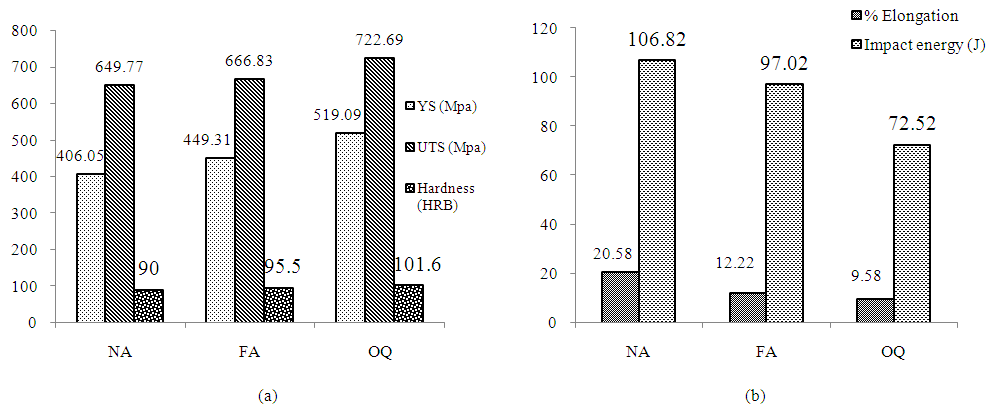 | Figure 3. A comparison of mechanical properties of different cooling mediums after forging: (a) yield strength, tensile strength and hardness and (b) % elongation and impact energy |
4. Conclusions
In the present study the effect of cooling rate after hot forging on the final microstructure and mechanical properties of AISI 1035 medium carbon steel was investigated. Based on the results and discussions, the following conclusions are made:Ø By increasing the cooling rate after hot forging, the effective yield strength, UTS, and hardness are increased. However, the effective impact energy as well as percentage elongation to failure is significantly decreased by increasing the cooling rate.Ø Although the strength of the steel is high, a drastic fall in elongation to fracture values is obtained when the steel is cooled in oil. Oil quenching leads to a formation of relatively fine ferrite and pearlite.Ø Normal air cooling from forging temperature results in a decrement of strength (yield and tensile strength) in above mentioned steel. This is because of the lower cooling rate resulted in coarse ferrite and pearlite structure.Ø The maximum percentage increased after forging followed by oil quenching for UTS and YS are 24.5% and 72.3% respectively whereas for percentage elongation the maximum percentage increased after forging followed by normal air cooling is 2.5% with respect to as received material.
ACKNOWLEDGEMENTS
The Topic of research is supported by National Institute of Foundry and Forge (India), by providing facilities for Research work.
References
[1] | Tukur, S.A., Usman, M. M., Muhammad, Isyaku and Sulaiman, N.A., 2014, Effect of Tempering Temperature on Mechanical Properties of Medium Carbon Steel. International Journal of Engineering Trends and Technology, 9, 798-800. |
[2] | T. Altan, G. Ngaile and G. Shen, Cold and hot forging fundamentals and applications, ASM International, 2005. |
[3] | Gunduz, S. and Capar, A., 2006, Influence of forging and cooling rate on microstructure and properties of medium carbon microalloy forging steel. J MATER SCI, 41, 561–564. |
[4] | Babakhani, A., Kiani-Rashid, A. R. and Ziaei, S. M. R., 2012, The microstructure and mechanical properties of hot forged vanadium microalloyed steel. Materials and Manufacturing Processes, 27, 135-139. |
[5] | Ceschini, L., Marconi, A., Martini, C., Morri, A. and Di Schino, A., 2013, Tensile and impact behaviour of a microalloyed medium carbon steel: Effect of the cooling condition and corresponding microstructure. Materials and Design, 45, 171–178. |
[6] | Rasouli, D., Khameneh, A. S., Akbarzadeh, A. and Daneshi, G.H., 2008, Effect of cooling rate on the microstructure and mechanical properties of microalloyed forging steel. Journal of materials processing technology, 206, 92. |
[7] | Jahazi, M., and Eghbali B., 2001, The influence of hot forging conditions on the microstructure and mechanical properties of two microalloyed steels. Journal of materials processing technology, 113, 594-598. |
[8] | ASTM A 370-05, Standard Test Methods and Definitions for Mechanical Testing of Steel Products, ASTM International, West Conshohocken, PA, 2005, www.astm.org. |
[9] | Kaynar, A., Gunduz, S. and Turkmen, M., 2013, Investigation on the behaviour of medium carbon and vanadium microalloyed steels by hot forging test. Materials and Design, 51, 819–825. |