Ndubuisi I. Mbada1, Pethuel O. Atanda2, Ola Aponbiede3, Abiodun A. Abioye2, Michael I. Ugbaja4, Ayo S. Alabi3
1Department of Transport Technology, Nigerian Institute of Transport Technology (NITT), Zaria Nigeria
2Department of Materials Science & Engineering, Obafemi Awolowo University, Ile-Ife, Nigeria
3Department of Metallurgical & Materials Engineering, Ahmadu Bello University, Zaria, Nigeria
4Department of Polymer Technology, Nigerian Institute of Science and Leather Technology (NILEST), Zaria, Nigeria
Correspondence to: Ndubuisi I. Mbada, Department of Transport Technology, Nigerian Institute of Transport Technology (NITT), Zaria Nigeria.
Email: |  |
Copyright © 2016 Scientific & Academic Publishing. All Rights Reserved.
This work is licensed under the Creative Commons Attribution International License (CC BY).
http://creativecommons.org/licenses/by/4.0/

Abstract
Methods: PKS were carbonised in other to drive off the organic matter, and obtained a clean solid fuel. Leco 350 Bomb Calorimeter was used to determine the heating value of the fuel; while adiabatic flame temperature and mass of air/ Kg of fuel were calculated for different conditions of excess air ratio ‘n’. The carbonised PKS was used to melt aluminium. Results: The higher heating value of PKS was 26541.204KJ/Kg. The lower heating value of PKS was 24457.9592KJ/Kg. The adiabatic flame temperature at n = 1 and 1.3 were 2082°C and 1679°C respectively. The air/fuel ratio is directly proportional to n. Discussion: The higher heating value of carbonised PKS was comparatively higher than those of firewood, peat and lignin but less than bituminous and anthracite coals.
Keywords:
Adiabatic flame temperature, Carbonisation, Heating value, Palm kernel shell, Crucible furnace
Cite this paper: Ndubuisi I. Mbada, Pethuel O. Atanda, Ola Aponbiede, Abiodun A. Abioye, Michael I. Ugbaja, Ayo S. Alabi, Performance Evaluation of Suitability of Carbonized Palm Kernel Shell (PKS) as a Veritable Alternative to Coal and Charcoal in Solid Fuel Fired Furnaces, International Journal of Metallurgical Engineering, Vol. 5 No. 1, 2016, pp. 15-20. doi: 10.5923/j.ijmee.20160501.03.
1. Introduction
Many activities of men including driving, power generation and production of equipment, in the modern age are fuels dependent [1, 2]. Consequently, the insatiable demand for fuels, fuel efficiency and performance guarantee and calls for environmental friendly alternative fuels sources, while not over relying on fossil fuels [1-3]. Literature is replete with alternative fuels, biomass content, carbon content and calorific values. Palm Kernel Shell (PKS), as a waste product of oil mill which poses considerable environmental problem in terms of disposal, has been employed in a number of applications [4-7]. PKS is an economic and environmentally sustainable raw material with potential for renewable energy industry [5]. A study by Okoroigwe [4] on the bio-energy potential of PKS found higher heating value of PKS on a dry and dry ash free basis using bomb calorimetric method as 22.94 and 25.75MJ/Kg. Similarly, other researchers have reported the heating values of PKS [6, 7]. Palm kernel shells are waste products of oil palm. The two major species of oil palm are the Dura and Pisifera [8]. However, there are currently, various species resulting from genetic modifications of the two traditional species . Historically, the origin of the oil palm could be traced to West Africa, with Nigeria, as the leading growers of oil palm in the 1950s and late 1960s [9]. Other countries, especially in the Asia sub-region, such as, Malaysia and Indonesia now cultivate oil palm as a chief cash crop produce [9]. The production of palm oil from the fruit bunch generates a lot of solid waste product on a large tonnage. These wastes may come from the palm fruit fibre, the palm kernel shell and the empty fruit bunch [10]. The utilization of palm kernel shell for thermal energy production by combustion of the palm kernel as a solid fuel mass is well documented in the literatures [10]. Okoroigwe [4] highlighted three thermo chemical processes that can be used to convert PKS to renewable energy, these methods includes- gasification, torrefaction and fast pyrolysis. Carbonisation is the term used for the conversion of organic substances to carbon or carbon containing residues through pyrolysis, the process liberates hydrogen, tar and other gaseous substances [12, 13]. Ogbimi [14] advocates that the design and construction of crucible furnace using carbonized PKS as an intermediate technology, is a step towards localization and institutionalization of technology in Africa. Crucible furnaces are the oldest and cheapest type of furnace, employed in foundry. Basically the crucibles are made of high temperature resisting materials for instance graphite crucible, the furnace can be fired by solid fuels, liquid and gaseous fuels several works have been done on evaluation and performance of some of these fuels for crucible furnace [15]. Olalere et al [16] and Osarenmwinda [17] constructed crucible furnace fired with spent engine oil, while Ighodalo et al [18] carried out a performance evaluation study of charcoal-fired furnace for recycling of aluminum. This study was aimed to evaluate the suitability of carbonised PKS fired crucible furnace for non-ferrous melting. In other to assess the suitability of PKS as a viable solid fuel, its calorific value, adiabatic flame temperature, excess air ratios, and the mass of air per Kg of fuel at different combustion ratios were determined.
2. Materials and Methods
2.1. Materials
The following materials were used for the construction of the crucible furnace: Refractory (fire clay), steel crucible, steel pipe, blower (bellow), carbonized palm kernel shell, thong, mould, hose connector.
2.2. Methods
The furnace outer shell is made of cylindrical metal. A circular opening was cut out on the side of the cylindrical metal shell, to serve as the inlet of the blower pipe. The basic function of the pipe was to supply oxidant or air for combustion of the fuel mass. The inner wall of the furnace was lined with pre-baked or pressed clay, a locally sourced refractory material. The refractory was a fire clay material basically of an alumina-silicate compound. The clay was sourced from Omoshio quarry site in Ado-Ekiti, Ekiti-State, Nigeria. The clayey masses were prepared by finely grinding and sieving the mass to obtain good particle distribution, which was then mixed with little amount of water to obtain a thick pasty solid that was moulded unto the inner wall of the cylindrical shell. The furnace chamber was allowed to dry and then fired. With this stage completed the furnace chamber was now ready for use.
2.3. Carbonization
The basic procedure in carbonizing the fuel is as follows: the shells were packed in steel rectangular compartment called retort or coke oven. The shell was heated in the absence of air to decompose the organic matter in the shell. The carbonized shell was subsequently quenched and left to cool in the compartment.
2.4. Determination of Calorific/ Heating Value and Ultimate Analysis
The determination of heating value was carried out at National Metallurgical Development Centre, Jos, Nigeria. The instrument used for the determination was Leco 350 Bomb Calorimeter. The calorific value of the PKS obtained in this study was 6343.5cal/g or 26541.204KJ/Kg. Table 1. Ultimate Analysis of Palm Kernel Shell (PKS) 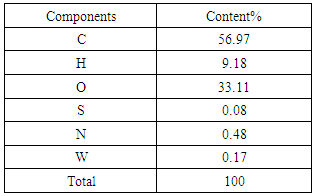 |
| |
|
2.5. Determination of Adiabatic Temperature of Burning
Adiabatic temperature was found under the assumption that all the heat evolved through combustion is spent only to raise the temperature of combustion product, in other words, calorimetric temperature of combustion was determined for adiabatic conditions only [19]. The Stoichiometric equations of combustion product are as follows: | (1) |
 | (2) |
 | (3) |
From the stoichiometric equations above: 1Kmol of Carbon reacts with 1Kmol of Oxygen to form 1Kmol of CO2 therefore,
4.75KmolO2, similarly we have 2.295KmolO2 + 0.0025KmolO2 -1.035KmolO2 from H2, S and O2 respectively. The Number of Mole of CO2=4.75Kmol, while that of
4.5994Kmol and SO2=0.0025Kmol, total mole of Oxygen = 6.0125KmolO2.Dry air contains 21 percent Oxygen while Nitrogen accounts for almost all the remaining 79 percent. Thus, the content of Nitrogen in air is 79/21 = 3.762 times the amount of Oxygen. Hence Kmole N2 = 3.762 × 6.0125 = 22.619Kmole plus 0.017KmolN2 from the fuel.The total mole of combustion product was 31.9879Kmole. It follows from the fact that 1mole of any gaseous substance occupies
thus the volume of combustion product is found by multiplying 31.9879Kmole by
= 716.5290m3 = 7.1653m3/Kg.To determine the Calorimetric Flame Temperature the following assumptions were made: i. We neglect the SO2 component of the combustion product as the SO2Kmole is negligible.ii. We assume that the stoichiometric equation of combustion is complete, that is, there is no CO as a result of incomplete combustion.iii. Theoretical Air-Fuel ratio (least required amount of air) is used for the calculation of the calorimetric flame temperature.iv. We also assume that there is no heat loss to the surroundings and the system, that is, the combustion products, does not work on the surroundings.The adiabatic temperature of combustion
that is when there is no heat exchange with the surrounding is given by the formula: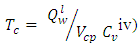 | (4) |
Is the lower heating value of fuel, KJ/m3 or KJ/Kg
Volume of combustion products per unit of fuel, 
Is the volume specific heat of combustion product, KJ/(m3.°C).The higher heating value,
of the palm kernel shell is given as 26541.204KJ/Kg, the lower heating value,
of the fuel is calculate from the relationship: 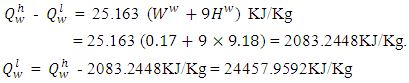 | (5) |
The specific heat of 1m3 combustion products (KJ/ (m3.°C)) is:
Therefore, the adiabatic flame temperature is estimated by substituting all the parameters into the equation:
at n >1 this condition is known as excess air, the adiabatic flame temperature is calculated by multiplying 6.0125KmolO2 by n and repeating the steps for calculating the adiabatic flame temperature. The crucible furnace was operated at 30% excess air this implies n= 1.3; thus O2 in the air supplied gives 6.0125 ×1.3 = 7.8163KmolO2 and the O2 in flue gas gives (7.8163-6.0125) Kmol = 1.8038KmolO2 which is entrained in the combustion products. Figure 1 gives the variation of adiabatic flame temperature with Excess Air Ratio (n) Table 2. Percentage Composition and Volume Specific Heat (Cv) of Combustion Products 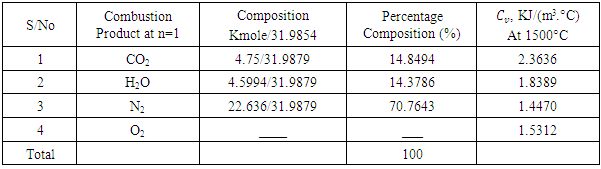 |
| |
|
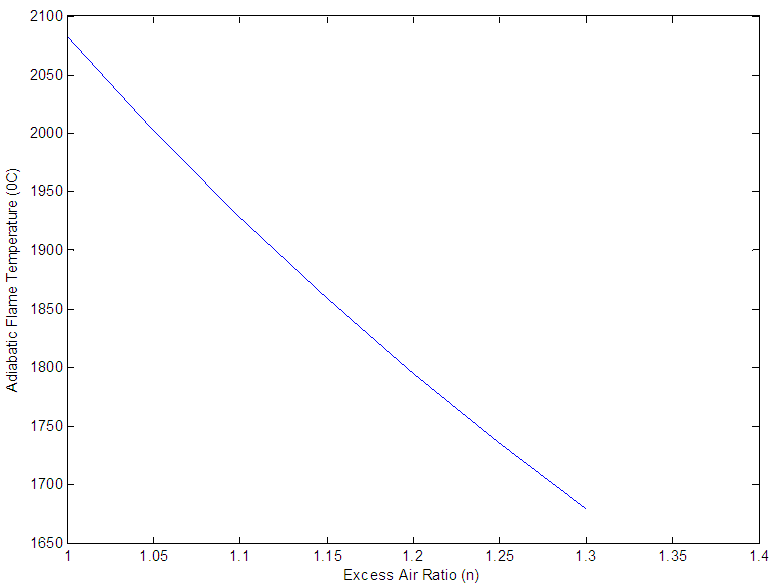 | Figure 1. Variation of Adiabatic Flame Temperature with Excess Air |
2.6. Furnace Operation
The furnace set-up is shown in figure 2 on charging the furnace with the carbonised palm kernel shell the fuel is ignited with an ember; after ignition the crucible is lowered into the combustion chamber with the charge inside, the bellow is operated continually until the charge becomes molten and the crucible is lifted out with a thong and the molten metal is poured into the mould.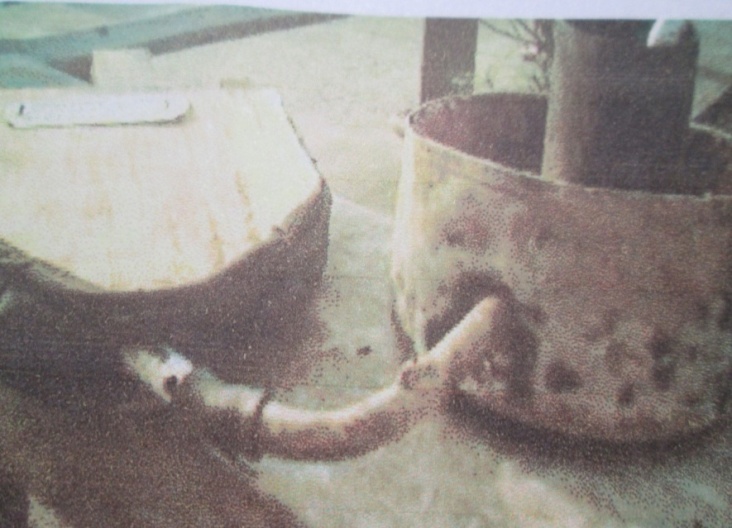 | Figure 2. Bellow and Crucible furnace set-up |
3. Results and Discussion
3.1. Carbonization
The thermal degradation of coal or any other organic matter that yield high carbon in the absence of air is known as carbonization or pyrolysis. The process is also commonly called coking because of its large volume use to prepare coke for blast furnaces. The Main objective for carbonizing is to produce a fuel with a smokeless flame, remove part of the moisture content of organic matter; and drive off some of the other organic matters that hinder combustion process, palm kernel shell are amenable to carbonization with a fuel mass that could be used for non-ferrous firing . The dull brownish shell of the PKS on carbonisation gives a brittle, black mass of solid eventuated by the pyrolitic action under a controlled atmosphere. Figure 3 below shows the carbonized PKS.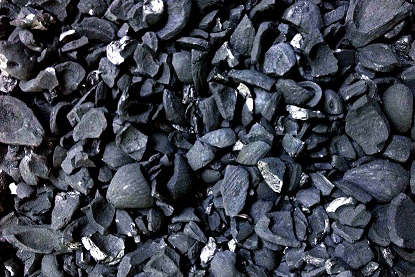 | Figure 3. Carbonized Palm Kernel Shell (PKS) |
3.2. Heating Value of Palm Kernel Shell
The calorific value/Higher heating value of the carbonized PKS as determined for the fuel mass was 26541.204KJ/Kg while the lower heating value as calculated from equation v was 24457.9592KJ/Kg. The heating value of the PKS is considerably greater than those of fire wood, peat, and lignite, and very much close to that of bituminous coal. Thus it suggests that it could be used effectively as solid fuels both for non-ferrous and ferrous foundry practices, boiler heating. Figure 4 below compares the calorific value of the PKS to those of some major types of solid fuels as culled from Khurmi [15].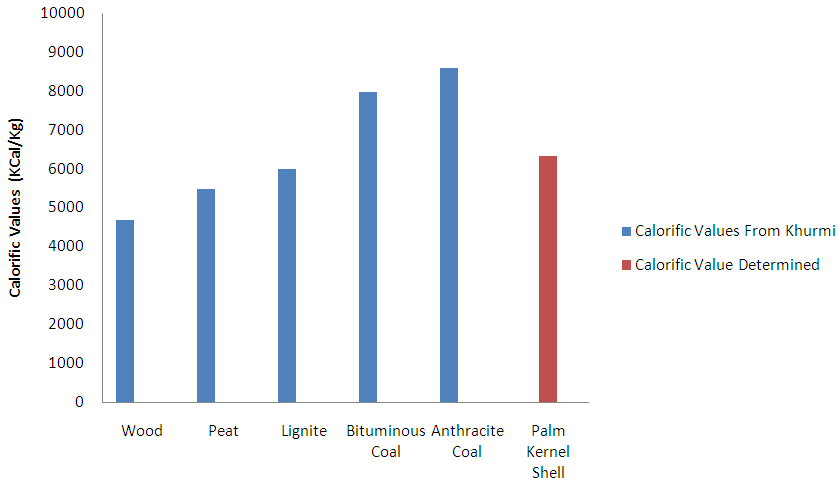 | Figure 4. Calorific Values of Some Selected Solid Fuel |
3.3. Fuel Energy Content and Flame Temperature
Energy content represents possibly the single most relevant property of a fuel. The standard measure of fuel energy content is the heating value or the calorific value. The heating value is of practical importance as it gives the basis for comparison of all fuel types irrespective of the source. The heat released from a system is consequently used to judge the efficiency of such system. Standard heating value analysis measures the heat released from the fuel when burned with enough air to fully oxidize the fuel (carbon forms CO2, H2 forms H2O). The Air/Fuel ratio which gives the masses of air/Kg of fuel required for combustion is directly proportional to excess air ratio ‘n’, which also leads to reduction in adiabatic flame temperature as shown in table 3. Adiabatic flame temperature, defines the temperature of products after all chemical reactions has reached equilibrium, and when no heat is allowed to enter or leave the combustion chamber. Each fuel has a unique adiabatic flame temperature for a given amount of air, as the ratio of fuel to air is varied the adiabatic flame temperature varies. The highest value generally occurs at an air- to-fuel ratio with slight less air than required to convert all of the carbon to CO2, and hydrogen to H2O. The lower heating value,
of the fuel was used in the calculation of the adiabatic temperature because of the fact that
mirrors the actual condition of combustion, since water vapour are entrained in the gaseous state by the combustion products formed on fuel combustion [19]. The adiabatic flame temperature of PKS at n =1 gives a value of 2082°C, while at n = 1.3 the temperature of burning was 1679°C. In practice the oxidizer is normally used at n>1 in other to fully oxidize the fuel. The flame produced by the palm kernel shell at n = 1.3 gives a bluish and luminous, and smokeless flame. The recorded flame temperature is typical of those of solid fuels that were used for crucible furnace firing and other heating applications [20]. The melting temperature of Aluminium is 660°C, while that of Copper is 1083°C; this implies that the fuel would be well suitable for non-ferrous melting and heating applications in boilers.Table 3. Spread Sheet Solution of Combustion Parameters as a Function of Excess Air Ratio 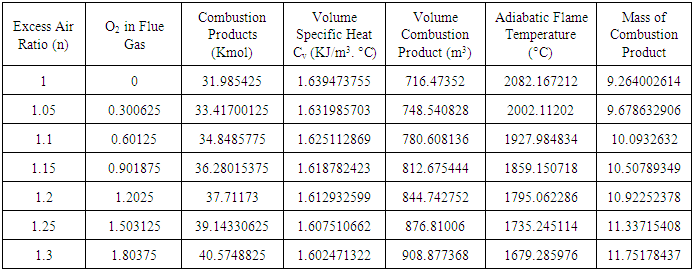 |
| |
|
3.4. Furnace Firing
The carbonized PKS was used to melt scraps of aluminium metal, using a bellow operated locally fabricated crucible furnace. The result showed that the carbonized PKS produced good heat for the melting of aluminium scrap plate I: shows the bellow and the crucible furnace set up.
3.5. Materials, Energy and the Environment
The over bearing influence of materials development and advances in energy utilization on the environment is fast becoming a thing of alarming concern to environmentalist and experts in this field. It is obvious that the environment is both the source and sinks for materials and energy; it is inevitable that development in both areas would have profound effect on the environment; in this case it would be a negative influence “No energy source is free, completely safe or limitless” [1]; “Energy must be used more wisely, in other to minimize the environmental hazards, and optimize the efficiency with which it is produced” [1].The overbearing demands for fossil fuels especially coal from the mines and the high and prohibitive cost of energy is leading to a negative impact on the environment; causing destruction of the landscape and the vegetation as well as other negative environmental hazards such as erosion, pollution, earth quake etc the global energy expenditure of fossil fuel was estimated to be about 1.3 billion in 1990 according to Davies [3].The use of PKS as an alternative fuel will relieve the high demand for fossil fuel as the main source of energy requirement for solid fuel firing of crucible furnaces and other heating needs; PKS provides alternative to high prohibitive cost of fossil fuel, and also help to offset the shift in environment-energy-materials equilibrium. It will also remove some of the negative influences caused by the over reliance on the major fossil fuels. From this study, the performance evaluation of suitability of carbonized palm kernel shell as a veritable alternative to coal and charcoal as solid fuels for crucible furnace melting of non-ferrous metals and other heating needs showed that the PKS can be deployed for the aforementioned purposes based on the findings of this research. On carbonisation, PKS were observed to burn with clean flame. The higher heating value,
of the PKS as measured by Leco 350 Bomb Calorimeter gives a value of 26541.204KJ/Kg while the lower heating value,
which was obtained by calculation using values from the ultimate analysis of the PKS, gives a value of 24457.9592KJ/Kg. Comparison of the heating value of PKS to those of coal and charcoal suggest that the
is well suitable for crucible furnace firing. The Adiabatic flame temperature at n = 1 gives a value of 2080°C, which is considerably high, the variation of adiabatic flame temperature as a function of n is shown in figure 1, while table 3 gives some of the combustion parameters it could also be inferred that the mass of air required also followed the same trend as those of adiabatic flame temperature.
3.6. Conclusions
The higher heating value of carbonised PKS was comparatively higher than those of firewood, peat and lignite but less than those of bituminous and anthracite coals. Hence, PKS is a veritable and cheap alternative to fossil fuel with good thermal properties in terms of the heating value and adiabatic temperature.
References
[1] | K. T. Pickering, L. A. Owen. An Introduction to Global Environmental Issues, London: Routledge, 1994. |
[2] | I. Dryden. The Efficient Use of Energy, London: Butterworth Scientific & Co (Publishers) Ltd, 1982. |
[3] | G. Davis, Energy for Planet Earth. 1990. |
[4] | E. Okoroigwe, C. Saffron. Determination of Bio-Energy Potential of Palm Kernel Shell by Physicochemical Characterization. Nigerian Journal of Technology 2012; 31(3): 329-335. |
[5] | M. Husin. Utilization of Oil Palm Biomass for Various Wood-Based and Other Products. In Advances in Oil Palm Research. Malaysia. 2000. |
[6] | G. Ezeike. Determination of Calorific Values of Some Nigerian Bio-Mass Solid Materials. Nig Journal of Tech. 1983; 7(1). |
[7] | A. Olufayo. Combustion-Related Characteristics of Some By-Products of Agricultural Processing Industries. Biomass. 1989; 69-72: 18. |
[8] | Cobley. An Introduction to Botany of Tropical Crops. Bristol: Western Printing Series Ltd., 1962. |
[9] | B. P. Elham. Production of Palm Kernel Shell Charcoal by the Continuous kiln Method. Faculty of Forestry. Universiti Putra Malaysia. Serdang, Selangor Darul Ehsan, 2001. |
[10] | H. D. Rozman, Z. A. Mohd Ishak, U. S. Ishiaku. Oil Palm Fiber-Thermoplastic Composites. In Natural Fibers, Biopolymers, and Biocomposites. Boca Raton, FL: CRC Press Taylor & Francis Group, 2005; 407-411. |
[11] | R. Kumar, H. Rozman, A. Abusamah, T. Chin. Sheet Moulding Compounds Based on Palm Fruit Pressed Fibre. In National Seminar on Utilization of Palm Tree and Other Palms. 1994. |
[12] | A. Afonja. Fluidized Bed Carbonization of Nigerian Coals. Proc. Nig. Soc. Chem. Engrs..1981; 52-62. |
[13] | D. Kaegi, V. Addes, H. Valia, M. Grant. Coal Conversion Processes. John Wiley & Son, 2000. |
[14] | F. Ogbimi. The Nature of Technological Development: Implication for Engineering Education and technology transfer. In ASEE Annual Conference, Toronto, Canada, 1990. |
[15] | R. Khurmi. A Textbook of Thermal Engineering: Mechanical Technology. New Delhi: S. Chand, 2006. |
[16] | A. Olalere, O. dahunsi, M. Akintunde, M. Tanimola. Development of A Crucible Furnace Fired With Spent Engine Oil Using Locally Sourced Materials. International Journal of Innovations and Applied Studies, pp. 281-288, 2015. |
[17] | J. Osarenmwinda. Fabrication and Performance Evaluation of Oil-Fired Crucible Furnace Using Locally Sourced Materials. Int. Journal of Engineering Research and Application. 2015; 5(3): 29-33. |
[18] | A. Ighodalo, E. Akue, J. Oyedoh. Performance Evaluation of the Local Charcoal-Fired Furnace for Recycling of Aluminum. Journal of Emerging trends in Engineering and Applied Sciences. 2011; 2(3): 448-450. |
[19] | A. Afonja, Materials Energy and the Environment: Inaugural Lecture Delivered at the University of Ife. 1986. |
[20] | L. Khitrin. Physics of Combustion and Explosion. Moscow: Moscow State University Publishing House. 1957. |