C. Subramanian1, K. Palaniradja2
1Research Scholar, Department of Mechanical Engineering, Pondicherry Engineering College, Puducherry, India
2Professor, Department of Mechanical Engineering, Pondicherry Engineering College, Puducherry, India
Correspondence to: C. Subramanian, Research Scholar, Department of Mechanical Engineering, Pondicherry Engineering College, Puducherry, India.
Email: |  |
Copyright © 2015 Scientific & Academic Publishing. All Rights Reserved.
Abstract
The present work deals with the formation of Ni–P/Ni–B duplex coatings by electroless nickel coating process and evaluation of their microhardness, surface roughness and weight gain of the substrate. The Ni–P/Ni–B duplex coatings were prepared using dual baths (acidic hypophosphite and alkaline borohydride) with both ionic and non-ionic surfactant duplex coating. Scanning electron microscopy (SEM) was used to assess the suface morphology of duplex interface. The microhardness, surface roughness and weight gain of electroless nickel duplex coating were compared with thallium acetate and tri sodium citrate stabilizers. The study reveals that the Ni–P/Ni–B duplex coatings without surfactant is amorphous rather than Ni-P/Ni-B duplex ionic surfactant coating. The duplex coatings are uniform and compatibility between the layers is good.
Keywords:
Duplex coating, Surfactant, SEM, Surface roughness, Micro hardness
Cite this paper: C. Subramanian, K. Palaniradja, Effect of Surfactant on the Electroless Ni-P/Ni-B Duplex Coatings on Aluminium 7075, International Journal of Metallurgical Engineering, Vol. 4 No. 2, 2015, pp. 25-32. doi: 10.5923/j.ijmee.20150402.01.
1. Introduction
In order to improve the corrosion resistance, electroless nickel phosphorous is considered as one of the most efficient surface treatment methodology due to its effective comprehensive properties such as good corrosion and wear resistance, uniform deposition on difficult geometries [1]. Nowadays, lot of research work was done on aluminium and its alloys because of their exclusive properties such as high strength to weight ratios, high thermal conductivity and good corrosion resistance. High strength aluminium alloys, such as 7075-T6, are widely used in aircraft structures due to their high strength-to-weight ratio, machinability and low cost [3]. Electroless coating developed by Brenner and Riddell is a chemical reduction process, in which the catalytic reduction of a metallic ion from an aqueous solution, and the subsequent deposition of the metal without the use of electrical energy. Except for the life of the bath, electroless has several advantages over electroplating technique in terms of deposit quality as well as the physical and mechanical properties. In electroless method, a sharp edge as well as a blind hole receives equivalent deposit thickness. Coating can be developed for desired properties by choosing the compositions of coating alloy/composite to suit specific requirements. As nickel melts around a temperature of about 1480°C and is unaffected by oxidation up to 500°C, electroless alloy/composite coatings can be applied for high operating temperatures based applications [14]. Ni–P coatings on aluminium-based alloys may be prepared using various procedures. Structure and properties are significantly dependent on phosphorus content, bath composition, temperature and pH [10]. Incase of electroless Ni-B plating, sodium borohydride or dimethyl amine borane are the common reducing agents present in boron. Hardness and superior wear resistance are the foremost benefits of borohydride reduced electroless nickel deposits in as-deposited condition [2]. The main need of duplex-layer or multi-layer coating with layers having different corrosion potential was an effective solution to develop the corrosion-resistance of anodic substrate. Electroless Ni-B coating is more wear resistant than tool steel and also it can replace gold in electronic industries [4].The purpose of electroless plating is to confer the mechanical properties of aluminium. Since the technique for plating of aluminium is not easy, a primary protective coating usually electroless Ni-P or Wood’s nickel is required before the plating of aluminium. After that, sodium borohydride is used for plating over electroless Ni-P because of its unstability along with pH value of more than 9 [5]. Metal coatings applied by electro-coating can match the uniform thickness of electroless nickel finish. Because these protective coating are chemically made and they create deposits of highly consistent depth all over the surfaces [8]. Among the various types of electroless plating, electroless nickel has become very popular due to their ability to provide a hard, wear and corrosion resistant surface. Hypophosphite-reduced electroless nickel plating has proved its supremacy in providing improved hardness, corrosion and wear resistance. Recently, much attention is being paid towards borohydride-reduced electroless nickel plating. The properties of sodium borohydride-reduced electroless nickel coatings are often superior to those of deposits reduced with other boron compounds or with sodium hypophosphite [7]. Borohydride electroless nickel coatings find extensive applications in aerospace, automotive, chemical and electrical industries especially because of their solderability, high hardness, wear and abrasion resistances. Similar to nickel–phosphorus, the deposition characteristics of nickel–boron change with boron content. Obviously, electroless Ni–B coatings are naturally lubricious [13]. The present work aims to prepare Ni–P/Ni–B duplex coating using dual bath technique and to evaluate its micro hardness, surface roughness and weight gain of the substrate.
2. Experimental Details
A heating bath is used in the laboratory to allow the chemical reaction to occur at an elevated temperature around 100°C. The beaker is a glass vessel which contains the chemical solutions for the purpose of coating. It is placed in the electroless bath where the chemicals are being heated up. The glass rod is used to stir the chemical where the magnetic stirrer is not necessary. The tongs are used to lift the bath after the coating is completed. Tri-sodium citrate and thallium acetate are the chemicals used during coating process which acts as a stabilizer for the bath [5-7]. It stabilizes the reaction occurring in the bath. Laboratory grade distilled water is used for the cleaning process and also to mix up with the chemicals. Nickel chloride acts as the source for the coating process as the nickel is being coated upon the surface of the substrate. Ethylene di amine is used as a complexing agent which creates a bond between the nickel and aluminium and causes the coating [9]. Thallium acetate is used as the stabilizer. Sodium borohydride is the reducing agent which removes the hydrogen ions which are being formed up inside the bath during the coating process [12].The nickel chlorides are absorbing moisture from the air and made into it as a solution. Nickel salts are carcinogenic. Sodium borohydride, also known as sodium tetrahydrido borate, and sodium tetrahydroborateis an inorganic compound usually encountered as a powder, and also it is a versatile reducing agent that finds wide application in chemical industry. Ethylenediamine is the organic compound with an ammonia-like odor is a strongly basic amine. Ethylenediamine readily reacts with moisture in humid air to generate a caustic, noxious and irritating film, to which even short exposures can cause serious damage to health. Ammonium chloride, an inorganic compound is a white crystal-like salt, highly doable in water. Sodium hypophosphite is the sodium salt of hypo phosphorous acid and is often encountered as the monohydrate which is solid at ambient temperature, appearing as odorless white sparklers. Ammonia or azane is a compound of nitrogen and hydrogen with the formula NH3.Surfactant is used for reducing the surface tension of the liquid, which is classified as non-ionic surfactant and ionic surfactant. Non-ionic surfactant does not contain any charge in it hydrophobic position. Ionic surfactant contain positive and negative charges, they are classified into two types namely anionic and cationic surfactants. The anionic surfactant contain negative charge in hydrophobic position and the cationic surfactant contain positive charge in hydrophobic position.Aluminium 7075 was used as the substrate for the preparation of electroless Ni–P/Ni–B duplex coatings. The aluminium 7075 are attract easily with oxygen, hence the fine layer is allow to form on the surface. Generally, aluminium has negative kinship towards nickel coating and hence it needs preliminary processes for coating nickel on the aluminium surface [5]. Their high chemical reactivity with air will result in the establishment of an oxide film on their surface that has an unfavorable effect on the coatings adherence and uniformity. Therefore, air interaction of specimens must be minimized throughout this process. The acidic solution oxidizes the surface, making it rougher but more chemically vigorous, providing surface pits to turn as spots for automated meshing of the EN coating [1].Initially, the substrate was made to polish by various emery sheets in order to obtain the fine smooth surface. After the motorized polishing of substrate it was cleaned using the acetone, then rinsed it with de-ionized water and pickled in nitric acid for 30 sec. Furthermore, the substrate was thoroughly washed with de-ionized water and then dipped in zincate solution for 1 min. The composition of solutions used for zincate process was given in table. 1. Table 1. Composition of Zincate 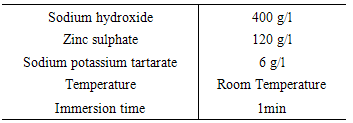 |
| |
|
After following this first zincate process, the substrate was rinsed with de-ionized water and again dipped the same in nitric acid for 30 sec and clean it with the use of de-ionized water. Finally, the substrate was dipped in zincate solution for 30 sec followed with cleaning process. The purpose of double zincate conversion is to improve electroless deposit adhesion on the coating surface [6]. The step by step procedure for carrying out the zincate pre-treatment process was given in fig. 1.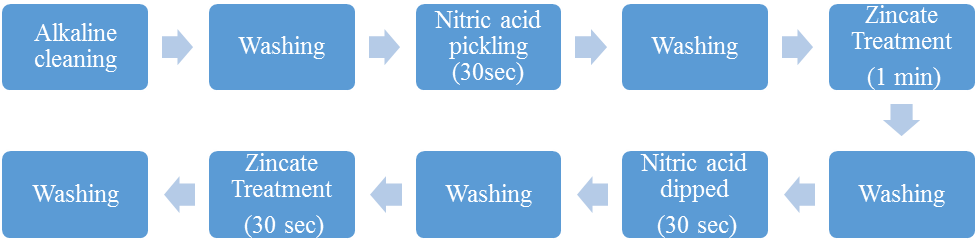 | Figure 1. Zincate pre-treatment process |
Immediately after the zincate pre-treatment process, the substrate was carefully placed in electroless nickel phosphorous solution bath, which is readily prepared and maintained at a temperature of 85°C. The composition of NiP bath along with conditions are given in table. 2. The substrate (sample A) was slowly dipped and placed on the NiP bath with desired position, so that the deposition ofnickel around the surface becomes good. The temperature should be kept as constant for better reaction in between metal surfaces and solutions. The pH level was frequently checked with the aid of pH indicator paper for fine coating thickness. Likewise the sample A with non-ionic surfactant (Polyethylene glycol hexadecyl ether) was coated with composition 1. Table 2. Nickel phosphorous and Nickel boron composition and conditions 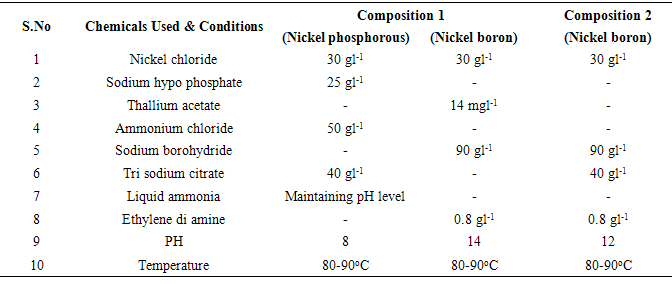 |
| |
|
After coating of the first layer (nickel phosophorous) for 15 mins, the sample A was made to react in nickel boron bath for the deposition of boron which is acting as second layer. Here, the pH of 14 is maintained for better deposition of nickel boron. After the desired time given in table. 3, the sample A was taken from the bath and rinse it with de-ionized water. The weight difference of sample before and after coating was determined using precision weighing machine. Likewise, the sample B was coated without using any surfactant on both nickel phosphorous and boron bath.Table 3. Coating time and Weight difference for composition 1 & 2 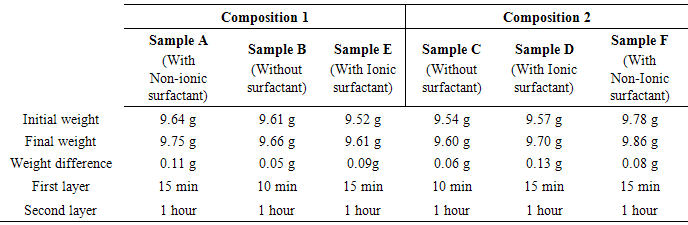 |
| |
|
The purpose of using surfactant was clearly identified in weight difference of the samples. However, the sample E was coated using ionic surfactant (sodium lauryl sulphate) along with bath composition and conditions were given in table. 2. Similarly, the coating was carried out on sample C, D and F using the composition 2 given in table. 2. The duplex coating resembles that the sample which is using ionic or non-ionic surfactant possesses better deposition rate than without using any surfactant on nickel solution. The weight gain after coating on various sample was listed in table. 3. In sample A we used non-ionic surfactant, in which we get weight difference of 0.11g. The thickness of the Sample A is much higher when compared to the other samples. Sample B without surfactant is allow to be coated for 10 min for the first layer and 1 hour for the second layer and the final weight difference of the sample is 0.05g. The sample E with ionic surfactant is allow to be coated for 15min for the first layer and 1 hour for the second layer and the final weight difference is 0.09g. In sample C, no surfactant was used and the sample D is carried out through ionic surfactant and sample F is carried out with non-ionic surfactant where the innermost layer is nickel phosphorous and the outermost layer is nickel boron for all the coated samples. The sample C coating time for the first layer is 10 min and for the second layer is 1 hour and the final weight difference of the sample is 0.06 g. Sample C has the less weight gain when compared to the other samples, the sample is coated without using the surfactant. Hence the thickness of the sample is less due to without using the surfactant. The sample D which is coated with ionic surfactant having a coating time for the first layer is 15min and for the second layer is 1 hour and the weight difference for the sample is 0.13 g. The sample F coating time for the first layer is 15 min and for the second layer is 1 hour and the weight difference is 0.08 g. we use non-ionic surfactant for this sample F. Comparatively, sample D possess more weight gain over all the substrates coated.
3. Results and Discussion
The plating rate of the electroless Ni–P/Ni–B deposits is evaluated by measuring the gain in weight after plating and using the density of the deposit. The thickness of the Ni–P/Ni–B deposits increases with increase in plating time. However, the extent of increase in thickness is not linear throughout the entire duration of plating and it saturates after some time. This is due to the accumulation of oxidation products of hypophosphite and borohydride in their respective baths [7].
3.1. SEM Analysis
The surface morphology of the electroless Ni-P/Ni-B deposits was shown in Fig.2, which fully covered the aluminium alloy substrate and shows typical spherical nodular structure. But the subsequent Ni-B coating shows more smooth surface morphology with good uniformity and exhibits metal luster like rhodium. This structure gives to the deposit the naturally property of autolubricious and thus increases the wear properties. The surface morphology of the duplex coatings indicates the formation of well-developed crystallites. The regions, which appear spherical nodules, are due to the precipitation of crystalline nickel and nickel borides (Ni3B) in the coatings. Some pores in the coatings at the initial deposition stage may result from the evolution the hydrogen during the electroless Ni-P deposition, which is corresponding to the surface morphology result. It is evident from the figure that the duplex coatings are uniform and the compatibility between the Ni-P and Ni-B layers is good. Meanwhile, the coatings are connected closely to the substrate and hence should exhibit good adhesion to the substrate [14].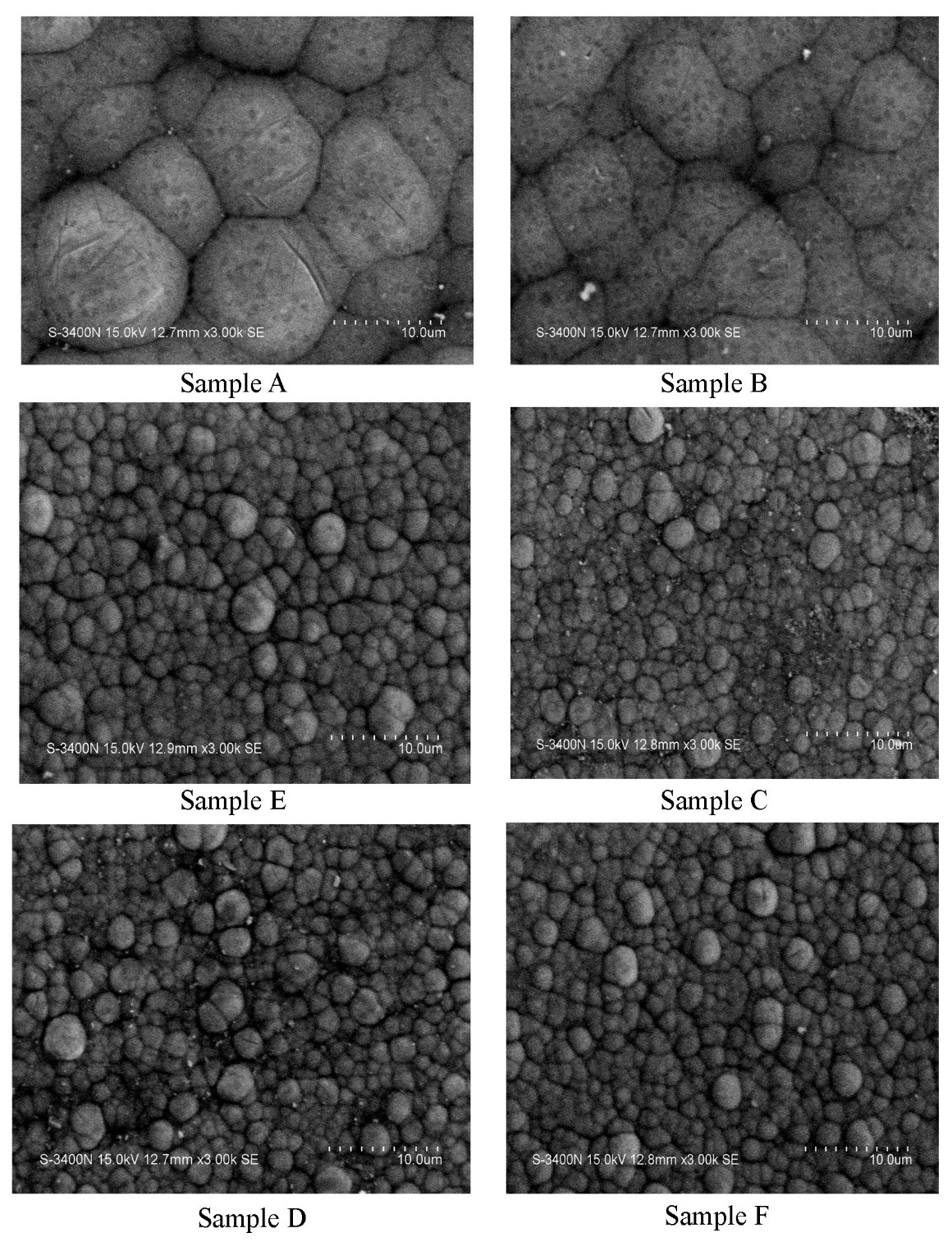 | Figure 2. SEM image for various coated samples with different composition |
The morphologies of electroless Ni-P/Ni-B coating deposition on aluminium alloy surface resembles that amount of nickel deposition in both ionic and non-ionic surfactant are very well enriched with nickel rather than without using surfactant. After one hour of immersion in the Ni-B bath without replenishment, a relatively uniform Ni-B deposit was obtained with a characteristic ‘cauliflower’ like structure. The cauliflower structure is arranged more uniform in ionic surfactant, when compared to non-ionic surfactant. The samples without surfactant are not arranged in uniform manner when compared to sample with surfactant.The above images represent the SEM analysis for the given samples. The sample A is coated with the non-ionic surfactant. The morphological analysis shows that the sample A has coated well. This is because the structure obtained is so uniform. The presence of nickel is identified with the help of pyramidal structure obtained from the analysis. The sample B is coated without the surfactant. The absence of surfactant reduces the thickness of the coating during coating process. Hence the sample B does not get the uniform structure. The sample E is coated with ionic surfactant. The ionic surfactant increases the coating thickness to get a great extent. This results in good coating on the substrate. Hence the identical structure is being obtained in this sample. The sample C is coated without the surfactant. So that the structure is not even in this sample. Also the amount of nickel deposition is very low. The sample D is coated with the ionic surfactant in which the amount of nickel deposits is high and also the structure is more uniform. The sample F is coated with the non-ionic surfactant. The structure obtained from this sample is rather uniform but the rate of nickel deposit among these is low. But the sample A is uniform when compared with the remaining coated samples with low deposition of nickel than sample D.
3.2. Micro Hardness Test
Micro hardness test is taken for each sample, the value of each sample is given below, and the figure.3 represents the micro hardness for the various samples. The hardness which we measured is expressed in terms of hardness vickers. The load applied for the hardness test is of about 0.05 kilogram with dwell time of 10 seconds. From the figure we come to know that the sample D has high hardness value of about 1079.25 hv. This is because the sample D is coated with ionic surfactant. The sample coated with this composition has high hardness value in an average. The sample B has the least hardness value due to coating without any surfactant. This reduces the thickness of the coating. It has the thickness value of about 343.85 hv. Hence the sample coated without the surfactant has least hardness value.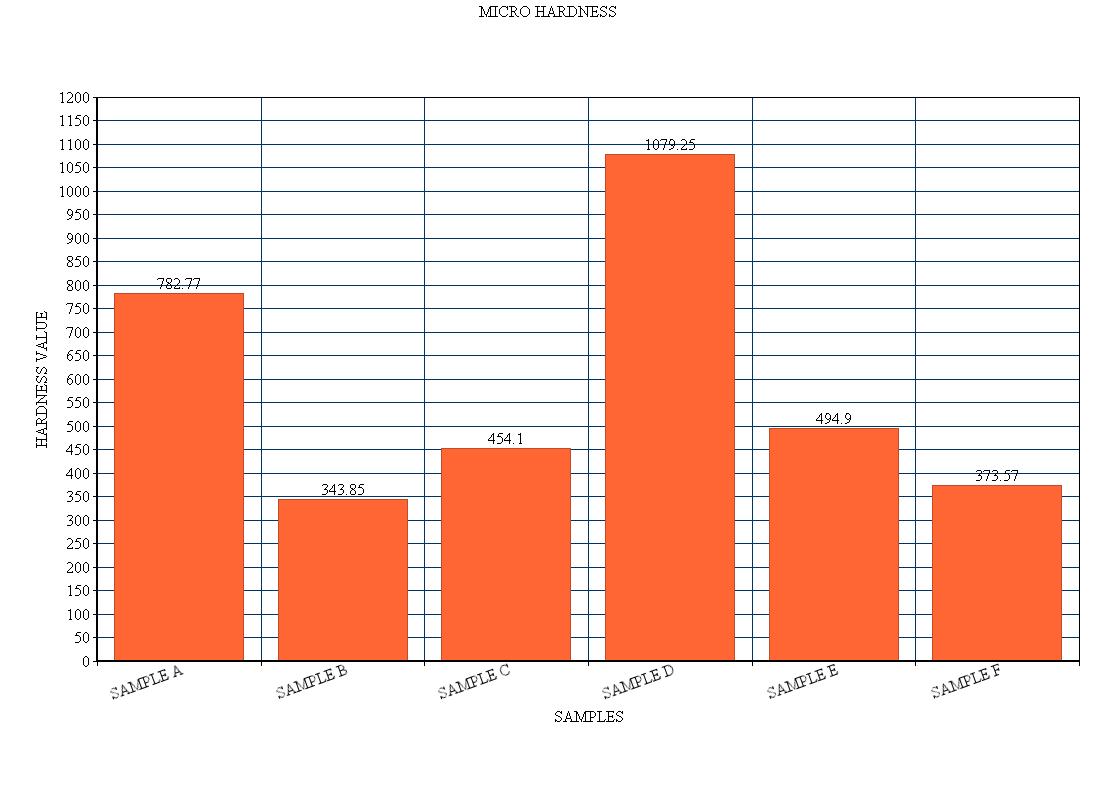 | Figure 3. Bar chart for Micro-Hardness test |
Table 4. Average Microhardness value 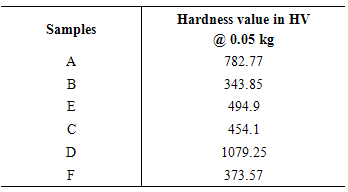 |
| |
|
In chart the hardness value for the sample D is much more higher and for the sample B has less hardness which is shown in fig. 3. Hence nickel boron has high hardness in case of sample D due to rich deposition of boron on the substrate.
3.3. Surface Roughness
Roughness plays a substantial role in defining how an existent object will interact with its atmosphere. The surface roughness of the sample to be plated should be considered before the beginning of any other plating process. The primary roughness plays an important role in the thickness and adhesion of the deposits as well as in their wear properties. In a polished substrate with a very low surface roughness, a thinner, less adherent coating will grow in contrast with a rougher substrate that favours an enriched interlocking force. On the other hand, on a rough substrate, coatings of high friction coefficient will be produced. Therefore, the coupons of this study were grinded down to improve the average surface roughness (Ra) reached to 0.126 μm.The surface roughness values for the coated samples were given in table.5. As per the specification Ra is the average surface roughness of the sample, Rq is the height of the root travels on the sample and Rz is the total travelling length on the specimen. In this the sample A has a roughness value of about 0.44µm by measuring about 8000 plots and finally it gives the average value of 3.289µm. The sample B has a roughness value of about 0.156µm as shown in fig.4. The roughness value of this sample is less when compared with the sample A. The sample C has a roughness value of about 0.126µm. This is relatively higher when compared with the sample B, due to the influence of the surfactant. The sample D has a roughness value of about 0.376µm at a point in it. This sample has high roughness value when compared with other samples. The sample E has roughness value of about 0.310µm which is said to be higher among one of the poor surface sample. The sample F has the roughness value of about 0.186µm as a crowning value at a specific point which is nearer to the fine surface finish.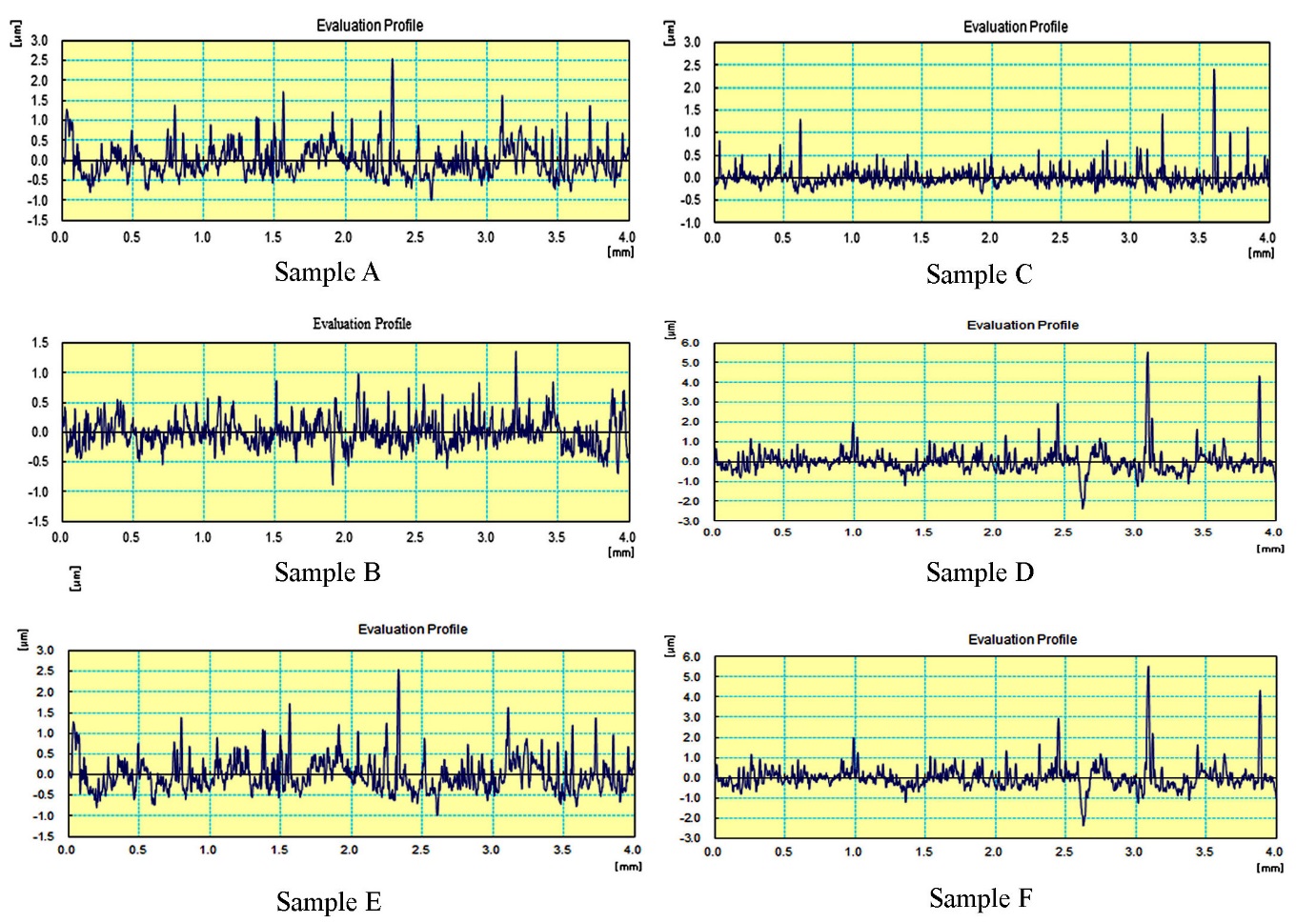 | Figure 4. Surface roughness graph for the samples |
Table 5. Surface Roughness value of coated samples 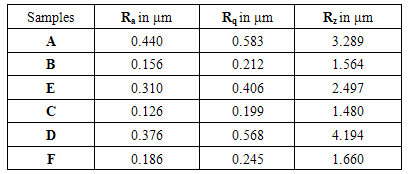 |
| |
|
4. Conclusions
The plating rate of the electroless Ni–P and Ni–B deposits is evaluated by measuring the gain in weight after coating and using the density of the deposit. The thickness of the Ni–P and Ni–B deposits increases with increase in plating time. However, the extent of increase in thickness is not linear throughout the entire duration of coating and it saturates after certain stage. This is due to the accumulation of oxidation products of hypophosphite and borohydride in their respective baths.i. The study reveals that electroless Ni–P/Ni–B duplex coatings could be prepared using dual baths (acidic hypophosphite- and alkaline borohydride-reduced electroless nickel baths). The Ni–P and Ni–B coatings are amorphous in their coated condition. The weight gain of the duplex coating has average weight gain of 0.13g.ii. SEM analysis of the substrate without surfactant, ionic surfactant and non-ionic surfactant of the electroless nickel duplex coatings reveals that the coatings are uniform and the compatibility between the layers are good.iii. The microhardness of the coating sample are tested using the hardness Vickers, and its shows that the hardness is high for the sample D which has tri-sodium citrate with ionic surfactants.iv. The surface roughness of the various sample is allow to be tested, the graph shows that the roughness of the each sample are uniform. Sample C has less roughness value and the Sample A has high roughness value.
References
[1] | Elsa Georgiza, Jelica Novakovic, Panayota Vassiliou, Characterization and corrosion resistance of duplex electroless Ni-P composite coatings on magnesium alloy, Surface & Coatings Technology 232 (2013) 432–439. |
[2] | K. Krishnaveni, T.S.N. Sankara Narayanan, S.K. Seshadri, Electroless Ni–B coatings: preparation and evaluation of hardness and wear resistance, Surface & Coatings Technology 190 (2005) 115–121. |
[3] | Mohan Kumar. S, Pramod. R, Shashi Kumar. M.E, Govindaraju. H.K, Evaluation of Fracture Toughness and Mechanical Properties of Aluminium Alloy 7075, T6 with Nickel Coating, Procedia Engineering 97, 2014, 178-185. |
[4] | W.X. Zhang, Z.H. Jiang, G.Y. Li, Q. Jiang, J.S. Lian, Electroless Ni-P/Ni-B duplex coatings for improving the hardness and the corrosion resistance of AZ91D magnesium alloy, Applied Surface Science 254 (2008) 4949–4955. |
[5] | V. Vitry, A. Sens, A.F. Kanta, F. Delaunois, Wear and corrosion resistance of heat treated and as-plated Duplex NiP/NiB coatings on 2024 aluminum alloys, Surface & Coatings Technology 206 (2012) 3421–3427. |
[6] | M. Vijayanand, R. Elansezhian, Effect of Different Pretreatments and Heat Treatment on Wear Properties of Electroless Ni-B Coatings on 7075-T6 Aluminum Alloy, Procedia Engineering 97 ( 2014 ) 1707 – 1717. |
[7] | T.S.N. Sankara Narayanan, K. Krishnaveni, S.K. Seshadri, Electroless Ni–P/Ni–B duplex coatings: preparation and evaluation of microhardness, wear and corrosion resistance, Materials Chemistry and Physics 82 (2003) 771–779. |
[8] | Prasanta Sahoo, Suman Kalyan Das, Tribology of electroless nickel coatings – A review, Materials and Design 32 (2011) 1760–1775. |
[9] | Mohammed Sahal, Characterization of NieP coating on AZ91D magnesium alloy with surfactants and nano-additives, Journal of Magnesium and Alloys 2 (2014) 293-298. |
[10] | M. Novak, D. Vojtech, T. Vıtu, Influence of heat treatment on tribological properties of electroless Ni–P and Ni–P–Al2O3 coatings on Al–Si casting alloy, Applied Surface Science 256 (2010) 2956–2960. |
[11] | CHEN Xiao-ming, LI Guang-yu, LIAN Jian-she, Deposition of electroless Ni-P/Ni-W-P duplex coatings on AZ91D magnesium alloy, Transactions of Nonferrous Metals Society of China 18 (2008) s323-s328. |
[12] | Jothi Sudagar, K. Venkateswarlu, and Jainshe Lian, Dry Sliding Wear Properties of a 7075-T6 Aluminum Alloy Coated with Ni-P (h) in Different Pretreatment Conditions, Journal of Materials Engineering and Performance, 2009. |
[13] | F. Delaunois, P. Lienard, Heat treatments for electroless nickel–boron plating on aluminium alloys, Surface and Coatings Technology 160 (2002) 239–248. |
[14] | Sanjib Kundu, Suman Kalyan Das and Prasanta Sahoo, Properties of electroless nickel at elevated temperature-a review, Procedia Engineering 97 (2014) 1698 – 1706. |