Somnath Kumar, K. K. Keshari, S. Kumar, A. Chatterjee, S. Ghosh, A. K. Bhakat, B. Sarkar
R & D Centre for Iron and Steel, Steel Authority of India Ltd., Ranchi, India
Correspondence to: Somnath Kumar, R & D Centre for Iron and Steel, Steel Authority of India Ltd., Ranchi, India.
Email: |  |
Copyright © 2015 Scientific & Academic Publishing. All Rights Reserved.
Abstract
Spring steels are used for making leaf springs for automotives, elastic rail clips (ERC) for railways, and coil springs for various applications. No residual plastic deformation is permissible even under heavy static or cyclic loads and springs must return to its original state after removal of external loads. The present paper relates to Si-Mn alloyed rolled spring steel billets and a process for its production through twin hearth furnace (THF) – top poured (TP) ingot – blooming and billet mill route, suitable for making elastic rail clip (ERC). A selective alloy design and process control for successful commercial production of rolled spring steel billets free from surface defects and internal defects like, subcutaneous pin/blow holes, off corner cracks and central piping or looseness to make it suitable for making elastic rail clip (ERC) and leaf springs favoring wide industrial application is described in the paper.
Keywords:
Spring Steel, Elastic Railway clip, Twin Hearth Furnace, Ingot casting, Ferro-alloys, Deoxidation
Cite this paper: Somnath Kumar, K. K. Keshari, S. Kumar, A. Chatterjee, S. Ghosh, A. K. Bhakat, B. Sarkar, Development of Si-Mn Alloyed Spring Steels Suitable for Elastic Rail Clip (ERC) Application, International Journal of Metallurgical Engineering, Vol. 4 No. 1, 2015, pp. 1-5. doi: 10.5923/j.ijmee.20150401.01.
1. Introduction
All Spring steel grades viz. 55Si7, 60Si7, 65Si7, SUP 9, SUP 11A etc. are used for making of helical and leaf springs which find application in auto sectors and railways.Si-Mn alloyed spring steels suitable for elastic rail clip (ERC) need to have high fatigue resistance in addition to high modulus of elasticity and resilience defined as energy absorbed during elastic deformation depicted by area under stress – strain plot upto elastic limit. In view of the properties required in spring steel, it is necessary to engineer a tempered-martensitic microstructure typified by high hardness (> 360 BHN) [1]. Further, it is critical to ensure absence of any surface / sub-surface cracks or matrix inclusion interface larger than a critical size where fatigue failure originate. In view of above, stringent requirement for inclusion rating in the final product assumes significance in addition to defect free macrostructure of cast billets. Usually top poured (TP) ingots have limitation in restricting the defect free surface in form of rolled scabs which is unacceptable for ERC.Stringent quality requirements are major deterrents against production of ERC grades billets through TP ingot route. In view of problem of yield on one hand and chances of non-compliance to inclusion rating, hardness, and other requirements relating fatigue and impact associated with surface defect and surface decarburisation on the other hand, usually twin hearth furnace (THF) – top poured (TP) ingot – blooming and billet mill route billets have not been considered ideally suited for applications like elastic rail clip or leaf spring. Absence of secondary refinement makes it all the more difficult in meeting the critical inclusion ratings. To meet the stringent metallurgical requirements of ERC, either bottom poured ingots or continuously cast steels have conventionally been in vogue.Si-Mn grade spring steel is high alloy steel aiming at eutectoid composition through high amount of carbon (C in the range of 0.47 – 0.63%), manganese (Mn in the range of 0.76 – 1.04%) and silicon (Si in the range of 1.45 – 1.95%). As there were no secondary refining facilities at IISCO Steel Plant (ISP), it was a difficult task to ensure carbon and silicon pick up to a requisite levels. Overall there has been no facility of correcting the chemistry once tapped from THF.There has been thus a need in the art to developing Si-Mn alloyed spring steel through top poured ingot route overcoming the conventional limitation in respect of surface and sub surface defects as well as compliance to the desired stringent inclusions rating suitable for ERC or leaf spring application by careful selection and trial of the alloy design and control on key process parameters. The above said technological difficulties were overcome by way of the present work exploiting metallurgical concepts and developing a process technology for the first time for producing ERC grade billets through twin hearth furnace (THF) – top poured (TP) ingot – blooming and billet Mill route in absence of secondary refining facilities at ISP, Burnpur.
2. Literature Review
Spring steel is a low alloy, medium carbon steel or high carbon steel with very high yield strength. This allows objects made of spring steel to return to their original shape despite significant bending or twisting. The steels used for spring making depend on the application and type of spring. They range from plain carbon grades in the range 0.5% to 1.00% C to Chromium, Chromium-Vanadium, Nickel-Chromium-Molybdenum, Silico-Manganese and Silicon-Manganese-Chromium-Molybdenum types. The chemical composition as per Indian standard of various spring steel grades is mentioned below in table 1.Table 1. Chemical composition of some common spring steel grades 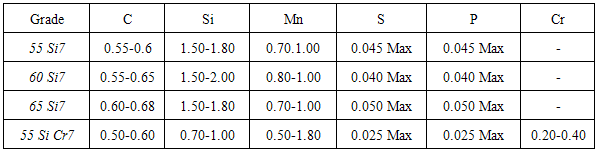 |
| |
|
2.1. Elastic Railway Clip
55Si7 Grade of spring steel is used for making Elastic Railway Clips (ERC) (Figure 1). A brief review regarding ERC, their function, production, specification and inspection standards set by the Indian Railways is given below.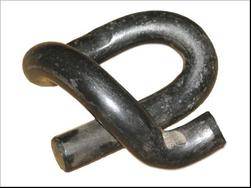 | Figure 1. Elastic railway clip |
2.1.1. Types of ERC
At present four types of ERCs are in trend:1. ERC MK III- toe load of 850-1100 kg2. ERC J clip –used at joint sleeper having a toe load of 300 kg3. Anti theft ERC used in theft prone area having toe load of 850-1100 kg4. ERC MK V- these are at trial stage to be used in toe loads of 850-1100 kg
2.1.2. Functions of ERCs
1. Withstand vibration induced in tracks2. Sustain static and dynamic cyclic stresses3. Provide creep and torsional resistance and keep the tracks in position.4. Able to resist lateral forces5. Long life and economic maintenance
2.1.3. Production Process
• Heating in furnace: 900-950°C• Forming of Clips: After heating the clips are formed in three stages of strokes• Quenching: After forming the ERCs are passed through a quenching oil tank in a conveyor belt for a period of 12 minutes at a temperature of 70°C. The maximum time specified in taking out the bars from the heating furnace to dipping in the quenching oil (including forming) is 20 seconds. The quenching oil bath is cleaned and the oil is filtered after every one lakh clips.• Tempering: After quenching, the ERCs are tempered at 400-500 C for a period of 55-60 minutesThe ERCs are finally oiled and packed. 100 % of the ERCs must have hardness between 40 and 44 Rc [1].
3. Twin Hearth Furnace
A twin hearth steelmaking furnace, THF(Figure.2) is the first industrial structure representing a proper steelmaking unit without regenerators, designed for intensive oxygen blowing into the bath; the fundamental principle of its operation is the utilization of the physical and chemical heat of gases formed during blowing for direct of solid charge materials [2], [3].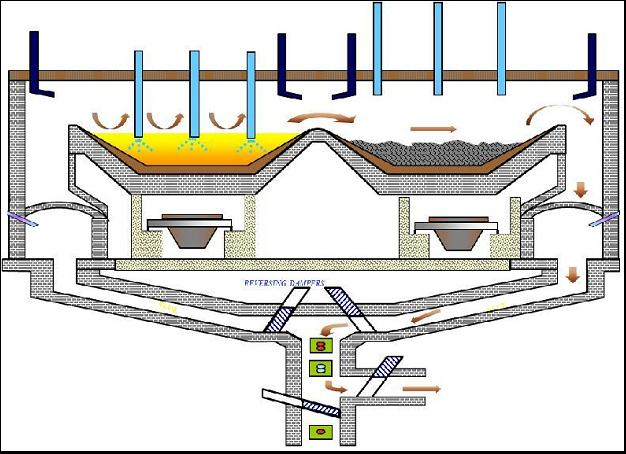 | Figure 2. Schematic diagram of twin hearth furnace |
The normal operational practice in THF includes fettling/repair of hearth, charging of fluxes scrap and iron ore, heating of solid charge, hot metal pouring, flushing of initial siliceous slag, melting of scrap, refining and then tapping. The normal charge consists of 85% hot metal and 15% scrap. The design duration of the whole cycle is 5 hours, with tapping at every 150 minutes. Impurities like phosphorus and sulphur etc. are removed by entrapping them in a high basicity slag. The slag basicity is aimed at around 2.0 [4]. After fettling, sandwich type charging sequence is adopted. Refining time varies between 2.5 to 3.0 hours depending on the refining load. The heat is tapped in the ladle after attaining desired levels of carbon, phosphorous and temperature.
4. Experimentation
4.1. Investigation of Defect Genesis
Spring steel of 60Si7 grade when earlier trial-processed incidence of rejections at bloom stage was reported by ISP on account of surface cracks. Typical cracks observed on the rolled blooms are shown in Figure 3. Prior to taking fresh initiative with respect to heat making and rolling of 55Si7 grade billets, thorough investigation aimed at finding out root cause of these types of surface defects were carried out.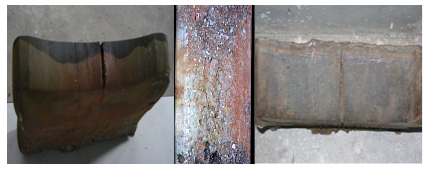 | Figure 3. Typical cracks observed on the rolled blooms |
Optical metallography (Figure 4) showed silicate and MnS type inclusions. Thin lines of inclusions aligning in the rolling direction are normal for steels having chemistry rich in Si (1.74%) and Mn (0.89%). Figure 5 shows the decarbed area present near the crack. Depth of the decarbed area is found to ~ 90 micron.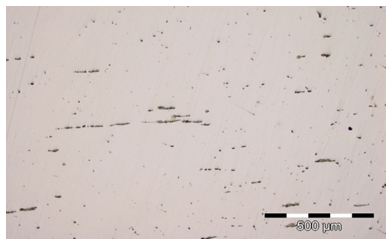 | Figure 4. Inclusions in 60Si7 grade spring steel bloom |
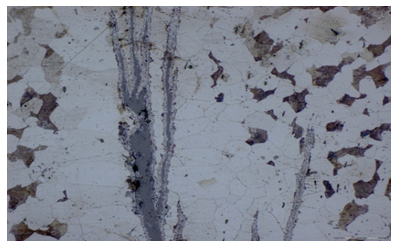 | Figure 5. Decarburisation near crack and entrapment of minute oxide particles in ferrite phase |
Electron Probe Microanalysis revealed that there exist evidences of internal oxidation of Si. Enriched Si spots (Figure 6a) relate to the inclusion (Figure 6b). Oxygen penetrated through pre-existing cracks and diffused within the matrix leading to not only decarburisation but also caused oxidation of Si which has higher affinity for oxygen compared to that of iron. 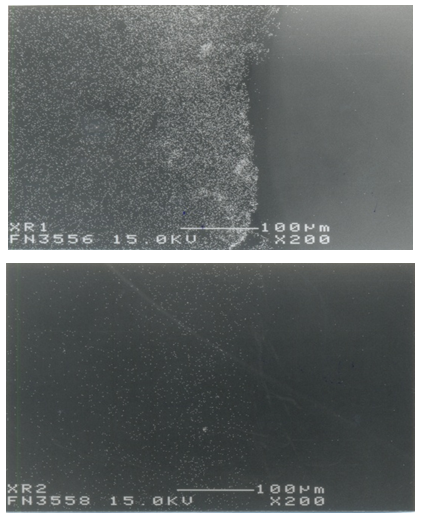 | Figure 6. a & b: EPMA analysis, X-ray mapping of Si & Mn |
The investigations revealed that surface cracks during rolling resulted from pre-existing cracks in ingot. Inferior thermal conductivity entails slow heating and slow cooling of 60Si7 grade spring steels for lowering the detrimental thermal stresses which cause surface cracking under severe conditions.
4.2. Spring Steel Heat Making
IS 55Si7 grade spring steel is high alloy steel aiming at eutectoid composition through high amount of carbon (C in the range of 0.47 – 0.63%), manganese (Mn in the range of 0.76 – 1.04%) and silicon (Si in the range of 1.45 – 1.95%). As there are no secondary refining facilities at ISP, Burnpur, it was a difficult task to ensure carbon and silicon pick up to a requisite levels. Overall there has been no facility of correcting the chemistry once tapped from THF.Since composition of spring steel grade 55Si7 has high levels of alloy content as is mentioned above, huge amount of (~6 t) ferro-alloys needs to be added. In normal cases the addition of ferro alloys is done in the ladle bottom, but for making spring steel it was felt necessary to divide the ferro alloy addition into two parts; ladle bottom as well as direct addition to the bath during tapping. This was done mainly to obtain desired recoveries of ferro alloys.Due to ~6 t addition of ferro alloys in spring steel during heat making on one hand and non-availability of any secondary refining facility on the other, it has been very critical to achieve desired tapping temperature in single attempt. The desired tap temperature was estimated on the following basis:Estimated tap temperature = Liquidus Temp (~1463°C) + Temperature drop due to Fe-alloy addition (~72°C) + Ladle Soaking (~70°C) + Superheat (~60°C) = ~1665°CHeats were made at steel melting shop through THF-Rinsing Unit-TP ingot route. Tapping temperature with proper charge balance was maintained at around 1680°C. Slag basicity ensured in the range of 2.5–3.0. Specific oxygen consumption was restricted to 60 Nm3/tcs. During tapping carry over slag was controlled. Teeming start temperature was controlled to ~1560°C, by adopting suitable purging regime. Efficient purging also helped in floatation of inclusions [5]. Keeping surface temperature of ingots just after stripping at ~ 885°C and ~705°C just before charging in soaking pits also helped in prevention of any thermal shock and better heating and soaking of ingots.Typical chemistry achieved for the trial heats along with specified chemistry for 55Si7 is depicted in Table-2. It can be seen that weight % of all the elements were found to fall within the range of aimed chemistry.Table 2. Chemical composition of some common spring steel grades 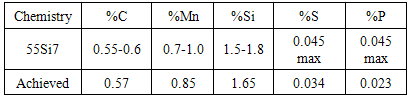 |
| |
|
4.3. Rolling of Spring Steel Ingots into Billets
The ingots were hot rolled keeping in view the characteristics of Si-Mn spring steel. Initial soaking pit temperature was kept ~ 300°C above the ingot temperature at the time of charging to avoid thermal shock and facilitate slow heating. Since spring steel contains Si ~1.7% slow heating / cooling is required [6] because of its lower thermal conductivity thus maintaining a minimum time period of 5 hours of heating plus 2 hours of soaking time for ensuring desired temperature-homogenization. The soaking pit temperature was raised slowly at the rate of 100°C / hr max. maintaining soaking temperature at ~ 1270°C and maintaining entry temperature to blooming mill > 1250°C whereas exit-temperature of 225 x 225 mm bloom > 1100°C. Finish rolling temperature of > 900°C was maintained for 96 x 96 mm (6M length) billets of spring steel.
5. Result & Discussion
Adopting of above mentioned controlled process parameters led to production of billets with sound macro. Performance trial was conducted with the billets with desired macrostructure. No edge crack was observed on the rolled rounds obtained of these billets. Microstructure, inclusion rating, depth of decarburisation and hardness conformed to the stipulated norm. Table 3 shows different stages of processing of billets into ERC and final surface hardness of ERC and figure 7 depicts microstructures at different stages of making of ERC. Flats were experimentally rolled from the 96 x 96 mm billet rolled billets and after heat treatments simulating austenitising, oil-quenching and tempering. Step hardness measurements of the flats as shown in Figure 8 met all the requirements stipulated for elastic railway clip as well as leaf spring also. Si-Mn alloyed rolled spring steel billets made through twin hearth furnace (THF) – top poured (TP) ingot – blooming and billet mill route are suitable for both ERC and leaf spring applications.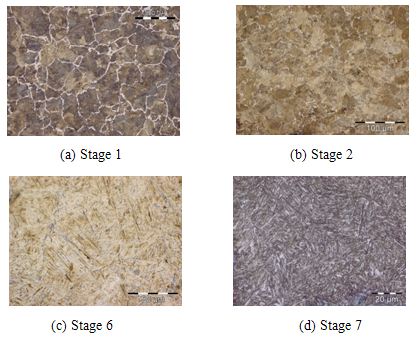 | Figure 7. Microstructures at different stages of making of ERC |
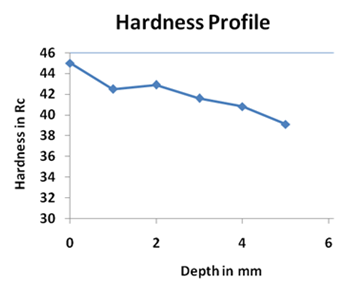 | Figure 8. Typical hardness profile of the stepped samples from the plates |
Table 3. Different Stages of processing of Billet into ERC 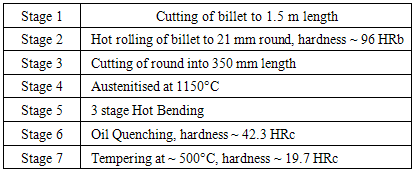 |
| |
|
6. Conclusions
Due to very rich chemistry and stringent quality requirements making of Si-Mn spring steel billets through THF - TP Ingot – Blooming & Billet Mill route was a critical issue especially in absence of secondary refining facility at ISP, Burnpur.Selective alloy design and precise control of process parameters helped in control of inclusion ratings in final product and meeting all other metallurgical requirements like surface hardness, step hardness, grain size in rolled flats, controlled decarburised depths etc., especially in absence of secondary refining facility. Advantageously, the macrostructure of billets produced according to the present work conform to ASTM 381 C2R2S2 specification, i.e. macrostructure of the transverse section of the cast billet must be defect free with respect to central looseness, pin holes or blow-holes and off corner cracks, so that the final product does not fail prematurely due to fatigue induced failure. The billets so produced were free from surface defects and internal defects making it suitable for making elastic rail clip (ERC).
ACKNOWLEDGEMENTS
The authors of the paper are grateful to the management of IISCO Steel Plant and RDCIS for extending the support to pursue the work. Extensive support provided by the personnel of Steel Melting Shop and R&C Lab. ISP during execution of the present investigations is thankfully acknowledged. The authors express their gratitude to all who directly or indirectly supported this technical work during execution of the project.
References
[1] | Dietrich Schreiber, et.al, “Spring Steels”. A Handbook for Materials Research and Engineering, Vol.2: Applications, Edited by Verein Deutscher, P. 468-477. |
[2] | G. Oiks, Converter and Open Hearth Steel Manufacture pp-350. |
[3] | I. Bornatsky, M. Kotrovsky, Y. Yargin, Open –Hearth Practice a Handbook. |
[4] | A.I. Borodulin, K.M. Trubetskov, et. al. “Operation of Twin bath steel making”, Metallurg, No.1, pp16-18.1968. |
[5] | Rob Dekkers, Ph.D. Thesis, Katholieke Universiteit Leuven, Leuven, Belgium (2002). |
[6] | J.H. Ai, et.al, “Effect of controlled rolling and cooling on the microstructure and mechanical properties of 60Si2MnA spring steel ”, Journal of Materials Processing Technology, Vol. 160, Issue 3, March 2005,, P. 390-395. |