D. Karmakar1, A. K. Bhakat1, Anjana Deva1, B. K. Jha1, K. K. Keshri1, S. Biswas2, R. K. Banerjee2
1RDCIS, SAIL, Ranchi, India
2ISP, SAIL, Burnpur, India
Correspondence to: A. K. Bhakat, RDCIS, SAIL, Ranchi, India.
Email: |  |
Copyright © 2014 Scientific & Academic Publishing. All Rights Reserved.
Abstract
High strength IS 2062 E410 grade structural were being produced at ISP by micro alloying with Nb (0.03-0.04%). To circumvent higher mill load experienced during rolling (Finish Rolling Temperature 850°-900℃), Nb was substituted by V (0.03-0.04%). Further to develop high tensile structural with leaner chemistry, addition of less Nb (~0.01%) and higher silicon (~0.20%) was tried to reduce the cost of production without sacrificing the properties. Successfully rolled material reveals that ferrite grain size with lower Nb and Si was found to be comparable with that of higher Nb steel and finer than that of V bearing steel. Synergistic effect of silicon in presence of niobium has resulted in refinement of grain size.
Keywords:
Fine grains, Micro alloyed steel, Grain refinement, High strength structural
Cite this paper: D. Karmakar, A. K. Bhakat, Anjana Deva, B. K. Jha, K. K. Keshri, S. Biswas, R. K. Banerjee, Niobium-Silicon Microalloyed High Strength Structural Steel, International Journal of Metallurgical Engineering, Vol. 3 No. 1, 2014, pp. 1-5. doi: 10.5923/j.ijmee.20140301.01.
1. Introduction
All over the world, the present technological trend is to explore usage of new material for construction with higher strength to weight ratio to make the design more efficient. There exists demand for high strength structural steel for construction and railways. IISCO Steel Plant, Burnpur (ISP) was regularly producing semi-killed variety structural conforming to IS 2062 E 250 and E 410 grade for construction and railways. As per IS 2062:2011 it has been made mandatory to supply the killed variety steel with guaranteed impact property at RT (room temperature), 0℃ and -20℃ for B0 and C grades respectively. High strength structural E 410 grade semi-killed variety were being produced at ISP by micro alloying with Nb (0.03-0.04%) through THF-RU-TP (Twin hearth - rinsing unit - top pouring) route. But very high mill load was experienced during rolling of this high strength structural due to low temperature (850-900℃) rolling caused by delay in entry and delivery of mill. Besides this, lower productivity due to generation of cobbles owing to the bent at delivery and excessive pass wear noticed in final stand. Although niobium is extremely effective grain refiner and has greatest influence on strength and toughness properties, it precipitates during rolling process within the temperature range of 1200℃ to 900℃ which leads to an increase in mill load substantially. In view of these, steel conforming to IS 2062 E 410 with leaner chemistry were designed to mitigate the problems associated with rolling and to make it cost effective. In the present work it was explored to develop high tensile structural first by micro-alloying with vanadium and secondly with leaner chemistry using less niobium and increased silicon to reduce the cost of production without sacrificing the properties.
2. Experimental
Critical issue for this developmental work was to produce killed high tensile (Hiten) IS 2062 E410 grade structural using existing steel making facilities at ISP by aluminium or in combination with silicon and aluminium. Alloy chemistry was designed primarily by micro-alloying with vanadium in place of niobium and secondly with leaner chemistry using less niobium and increased silicon. Accordingly trial heats were made at ISP and rolled into high strength structural.
2.1. Processing of Vanadium Bearing IS 2062 E 410 Grade Steel Structural
The following parameters were considered while designing the alloy chemistry to meet the targeted mechanical properties as per IS 2062:2011:YS (Yield Strength) = 410 MPa minimum UTS (Ultimate Tensile Strength) = 560 MPa minimumElongation = 20 % minimum While rolling Nb bearing Hiten Z bar by maintaining finish rolling temperature at around 850℃ in the old Heavy Structural Mill at ISP, mill load experienced was considerably high (motor load ~5500A as against 4000A for normal). It was observed by Dutta & Sellars [1] that lower rolling temperature increase mill load due to niobium effect which leads to significant retardation of austenite recrystallization due to Nb carbides precipitation. Hence, it was decided to use V in place of Nb because in case of V, precipitation [2] takes place in between 875 to 900℃ and so it was assumed that the mill load will remain within specified norms. To achieve the desired properties, the alloy chemistry (by wt %) was designed and shown in Table-1.Table 1. Designed alloy chemistry (by weight %) of V bearing Z bar  |
| |
|
Average heat size in twin hearth furnace of steel melting shop at ISP was 110t. Tapping temperature with proper charge balance was maintained at 1680℃. Slag basicity ensured in the range of 2.5–3.0. Developmental heats were made initially with V in the range of 0.04-0.05, but subsequently it was reduced gradually to the level of around 0.03-0.04 to achieve the required properties of Hiten Z bar to make it cost effective. Chemical analysis of the trial heat samples for Z bar is given in Table-2.Table 2. Typical chemical analysis (by weight %) of V bearing steel for Z bar  |
| |
|
Z-bar is a special asymmetrical structural section mostly used for manufacture of railway wagons in India. Two grades of Z bar namely normal Z bar (IS 2062 E250 grade A with Cu), Hiten Z bar (IS 2062 E410A, with Cu and micro alloyed) were being produced at ISP, SAIL regularly. Certain general problems were associated with production of Nb bearing Hiten Z bar during rolling such as inducing side sweep on delivery of the bar and axial shifting of the rolls towards long leg due to large difference in leg thickness between short leg and long leg of Z bar. This behaviour not only induced delivery trouble but also affected the sharpness of Apex. Further, any imbalance in drafting between short leg and long leg in final pass twisted the bar from short side and made the rolling even more difficult. However, all the necessary measures were taken during roll turning and rolling to minimise above mentioned troubles. Following are the salient observations while rolling V bearing Hiten Z bar i.e. troubles associated with entry and delivery got eliminated to a great extent, shearing at leader pass eliminated due to maintenance of adequate rolling temperature, mill load decreased substantially from 5000A to 4200A, relegation due to variation in long leg appreciably decreased (could be maintained between 171-174 mm) thereby improving the product quality, yield and reduction in cobble generation.
2.2. Processing of Low Nb and High Si Bearing Al killed E410 Grade Steel
In a recent study carried out on hot rolled strip [3] the effect of silicon on grain refinement has been investigated in industrially produced Nb-microalloyed steel. Synergistic effect of silicon in presence of Nb found to have favoured grain refinement in hot rolled strip and has resulted in very fine ferrite grains of less than 3 micron. Evolution of such a fine grain has been related to the enhanced precipitation of Nb(CN) in presence of silicon. It is well known that Nb(CN) precipitation influences micro structural evolution during hot rolling of micro alloyed steels [4-6]. The complexity of thermo mechanical processing is such that it is difficult to deconvolute the contribution of various microalloying elements and processing variable in influencing its precipitation kinetics. Despite extensive studies carried out during the past decades, many details regarding the precipitation behaviour remain unclear. One such example is how the addition of a third element, such as silicon, influences the precipitation kinetics of Nb(CN) in austenite during hot working. Traditionally, silicon has been effectively being used for the development of Dual Phase and TRIP (Transformation Induced Plasticity) steels wherein Si addition has inhibited carbide precipitation and resulted in cleaner ferrite [7, 8]. Silicon is considered to be an effective element in partitioning of carbon from ferrite to austenite. This attribute can also be exploited in enhancing strain induced precipitation of carbonitrides in micro alloyed steels. The effect of silicon on thermodynamics of precipitation was taken into account as early as 1971 [9], but it has attracted more attention recently wherein it has been suggested that silicon addition should increase precipitation rate. Recent investigations indicate that addition of Si may be responsible for accelerating Nb(CN) precipitation in Nb bearing steel [4, 10, 11]. This precipitation depends on chemistry and the hot rolling parameters such as strain, strain rate and interpass time. It was envisaged earlier that silicon addition promotes grain refinement in Nb micro alloyed hot strip steel [3, 12]. In the present work the concept has been used for production of high tensile structural.
2.2.1. Steel Making for Low Nb and High Si Bearing Steel
Heats were made at steel melting shop through THF-RU-TP route. Tapping temperature with proper charge balance maintained at around 1680℃. Slag basicity ensured in the range of 2.5–3.0. Specific oxygen consumption was restricted to <60 Nm3/t. During tapping carry over slag was controlled. FeSi was added in the ladle and aluminium shots were added during top pouring. Typical chemistry achieved for the trial heats along with specified chemistry for this grade is depicted in Table-3. It can be seen that weight % of all the elements were found to fall within the range of aimed chemistry. Silicon was found to be on lower side. Niobium in the product analysis was 0.01%.Table 3. Chemical composition (wt%) of Al-Killed Nb+Si variety steel for Z bar  |
| |
|
2.2.2. Rolling of High Strength IS 2062 E 410C Grade Channels
The channels ISMB 250 (Figure 1) were produced in Heavy Structural Mill as per high tensile variety (IS 2062 E410 C grade) with guaranteed impact value of 25J at -20℃ as stipulated in the Standard.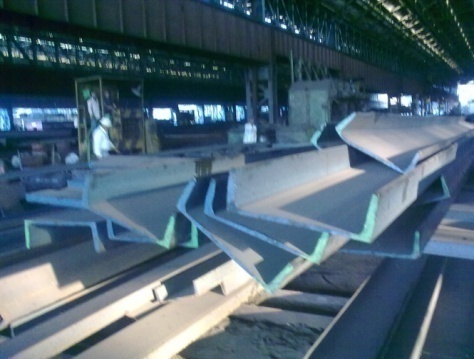 | Figure 1. ISMB 250 Channels of IS 2062 E410 grade B steel at Heavy Structural Mill, ISP |
The product was characterized and the properties evaluated are discussed below.
3. Experimental Results
3.1. Microstructural Evolution
A few specimens were prepared from the representative samples of Nb, V and Nb+Si bearing Hiten (E 410C) Z bar. Microstructures taken in optical microscope are reproduced in Figure 2. 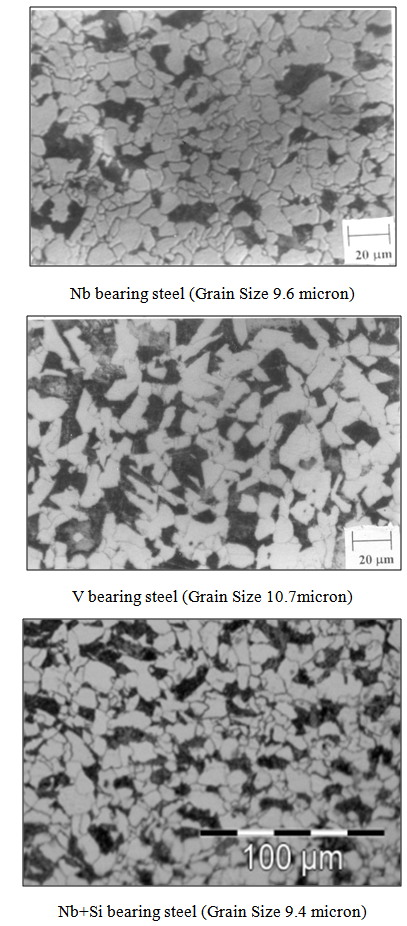 | Figure 2. Microstructure of IS-2062 E 410 grade B Z bar of three different compositions |
3.2. Mechanical Properties
Tensile and Charpy specimens were prepared from the representative samples of all the three grades of steels and the test results are shown in Table-4 along with the specified limit of yield strength, tensile strength and elongation values. Table 4. Mechanical properties of IS 2062 Al-Killed E 410C grade steel 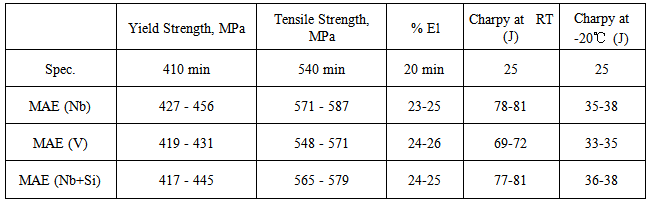 |
| |
|
4. Results and Discussions
4.1. Micro-alloyed Structural Using V in Place of Nb
Niobium is considered as an effective grain refiner and has greatest influence on strength and toughness properties. It precipitates during rolling process within the temperature range of 1200℃ to 900℃ which leads to an increase in mill load substantially. Hence it was decided to use vanadium in place of niobium. Vanadium is moderate grain refiner but good precipitation strengthener. In case of V, precipitation takes place below finish rolling temperature around 850℃, and hence it is not supposed to increase mill load significantly. Considering this, IS 2062 E410 grade Z bar structural was made with V addition in the range of 0.035–0.040%. Operating parameters at Heavy Structural Mill were maintained with bloom soaking temperature in the range of 1050-1100℃ and Finish rolling temperature in the range of 850-900℃. Natural tendency of twisting and bending in Z bar gets aggravated in Hiten with Nb because of developed stiffness of the bar due to the process of precipitation on grain boundaries which takes place within above mentioned temperature range during rolling. Many of the problems faced during rolling could be mitigated by the use of V as micro-alloy. V is characterized by starting the process of precipitation on grain boundaries at the temperature below 850℃. As a result, stiffness of the bar during rolling got reduced and Hiten grade Z bar structural could be rolled successfully at much lower mill load.
4.2. Micro-alloyed Structural Using Nb-Si in Place of Nb
Further experimental heats were made and processed using Nb+Si alloyed grade. The chemistry was designed using lower Nb and higher Si and the properties were found to be comparable. In the newly conceptualised grade niobium addition was reduced from 0.039% to 0.010% but simultaneously silicon percentage was increased to 0.186% from 0.08%. It was also found that all the three grades with varying chemistry conform to the specification. Yield strength of Nb steel was found to be slightly higher (427–456 MPa) as compared to the other two i.e. V microalloyed steel (419–431 MPa) and Nb+Si alloyed steel (417-445 MPa). For all the three grades Tensile Strength were greater than specified 540 MPa and elongation values were varied between 23 to 26%. Charpy impact value of Hiten IS 2062 E-410 Grade Z bar at Room Temperature and -20℃ for all the three micro-alloyed steel are found comparable (Table 4). The production of Nb+Si micro-alloyed steel grade resulted in minimisation of the problems like higher mill load during rolling, tendency of twisting and bending associated with rolling etc. It was also revealed that an optimum temperature range of 900 to 950℃ was desirable as finish rolling temperature. Ferrite grain size of E 410 with Nb+Si variety and Nb variety was found 9.4 and 9.6 micron respectively but finer than V variety (10.7 micron). This is due to the synergistic effect of silicon in presence of niobium which has resulted in the refinement of grain size.
5. Conclusions
a) Two types of new alloy chemistry were tried for development of Hiten IS 2062 E-410 Grade Z bar at ISP. The properties were compared with the conventional Nb bearing grade. Both V bearing and Nb+Si bearing steel were found suitable for this application.b) Properties for all the three grades conform to the specification (IS 2062 E410C). The synergistic effect of silicon in presence of niobium has resulted in refinement of grain size. c) The leaner chemistry with lower niobium and higher silicon resulted in saving of ferro-alloy and is economically more viable than V bearing and Nb bearing HITEN Z bar.d) The mill parameters like higher mill load during rolling, tendency of twisting and bending associated with rolling etc. has been minimised substantially in case of V bearing steel and Nb+Si bearing steel. However, Nb+Si bearing steel is preferable over V bearing steel due to its economic advantages.
ACKNOWLEDGEMENTS
The authors thankfully acknowledge with gratitude for the guidance and support extended by the management of RDCIS and ISP during the course of this work.
References
[1] | B Dutta & C M Sellars, Material Science and Technology, Vol 2, Issue 2, 1986, pp. 146-153. |
[2] | Rune Lagneborg, Tadeusz Siwecki, Stanislaw Zajac and Bevis Hutchinson, Book on the “Role of vanadium in micro alloyed steels”. |
[3] | Anjana Deva, B K Jha and N S Mishra, Material Science and Technology, Vol 27, No.3, March 2011, pp. 710 – 712. |
[4] | J. X. Dong, F. Siciliano Jr, J. J. Jonas, W. J. Liu and E. Essadiqi, ISIJ International, 2000, 40, p 613. |
[5] | E. V. Pereloma, B. R. Crawford, P.D. Hodgson, 2001, A 299, pp. 27. |
[6] | A, S. S. Hansen, J.B. Vander Sande, Morris Cohen, Metallurgical Transactions, March 1980, Volume 11, Issue 3, pp. 387-402. |
[7] | Takehide Senuma, ISIJ International, 41, pp. 520. |
[8] | B. K. Jha, Ram Avtar and V. S. Dwivedi, Trans ISIJ,1988, 28, pp. 125. |
[9] | S. Koyoma, T. Ishii and K. Narita, Japan Inst. Met. J, 1971, 35, pp. 1089. |
[10] | L. Jiang, A. O. Humphreys and J. J. Jonas, ISIJ International, 2004, 44, pp. 381. |
[11] | F. Siciliano Jr and J.J. Jonas, Metall. Mater Trans A, 2000, 31, pp. 511. |
[12] | C. Garcia-Mateo, B. Lopez, J. M. Rodriguez-Ibabe: Mater. Sci. Eng. A, 2001, A303, pp. 216–225. |