A K Bhakat1, P K Maini1, M K Pradhan2, C Muthuswamy2
1Steel Authority of India Limited (SAIL), Research & Development Centre for Iron & Steel (RDCIS), Ranchi, 834 002, India
2Steel Authority of India Limited (SAIL), Rourkela Steel Plant, Rourkela, 769011, India
Correspondence to: A K Bhakat, Steel Authority of India Limited (SAIL), Research & Development Centre for Iron & Steel (RDCIS), Ranchi, 834 002, India.
Email: |  |
Copyright © 2012 Scientific & Academic Publishing. All Rights Reserved.
Abstract
High strength low alloy steels are used now-a-days commercially with increased strength, toughness, formability and weldability for a variety of critical applications such as long and cross members of auto chassis, pre-engineered building (PEB) structures, high mast lighting poles, wind poles, welded pipes etc. To meet these requirements, special quality hot rolled formable grades such as HSFQ (High Strength Formable Quality) 350/ 450, IS 10748 Gr. V & IS 5986 Fe 510 have been developed at Rourkela Steel Plant (RSP) that combine micro-alloying with controlled processing considering customer’s requirement and plant’s capability for producing these grades. The newly developed HSFQ hot rolled steel possess an attractive combination of strength and formability property which is typically quantified as high elongation (25 % min) and hole expansion ratio (145 % min) coupled with lower YS/UTS ratio (0.80-0.85). This has been possible as a result of innovative alloy design and synergistic effect of Nb & Si during controlled processing. In case of IS 10748 Gr. V & IS 5986 Fe 510 grades, the unique feature was the combination of very high strength (UTS: 500-600 MPa and YS: 310-400 MPa) along with reasonable % EL (20-30) for its forming properties. Micro-alloying with Nb helps to achieve the desired properties by obtaining the required microstructures in the hot rolled coils. The application of these steel demands good internal soundness and cleanliness to arrest the cracking susceptibility of the finished products during forming / welding operations.
Keywords:
High Strength, Formable, HSFQ, IS 10748, IS 5986, Fine Grains, Strength, Niobium
Cite this paper: A K Bhakat, P K Maini, M K Pradhan, C Muthuswamy, Development of High Strength Hot Rolled Coils with Enhanced Formability Property, International Journal of Metallurgical Engineering, Vol. 2 No. 3, 2013, pp. 249-253. doi: 10.5923/j.ijmee.20130203.01.
1. Introduction
In the fast changing market scenario, value added steels with enhanced quality, properties and performance capabilities are getting more thrust day by day due to their specific end applications. In India, the cold reducers segment is growing very fast and their quality requirements for hot rolled coils are more and more demanding. Initially IS 10748 Gr. V & IS 5986 Fe 510 grades are selected for development at an Integrated Steel Plant. These difficult to cast grades have been developed by optimizing casting parameters through BOF-VAR-LF-CC route. The hot rolling parameters were optimized by maintaining mill load within the finishing mill capacity by giving adequate slab soaking time in the reheating furnace. Critical issues for development of these grades were selection of suitable alloy chemistry and hot rolling practices[1], which were established through extensive trials both at plants and customer premises. These materials are required for a variety of critical applications such as high mast lighting poles, wind poles, camera poles, welded pipes, tubes etc. In case of IS 10748 Gr. V & IS 5986 Fe 510 grades the unique feature was the combination of very high strength (UTS: 500-600 MPa and YS: 310-400 MPa) along with reasonable % EL (20-30) for its forming properties. Micro-alloying with Nb helps to achieve the desired properties by obtaining the required microstructures in the hot rolled coils.HSFQ grades with YS 350/ 450 MPa min. are used mainly for application in auto components after cold forming. These high tensile coils with higher forming properties are better substitute of SAILMA 350/ 450 due to its economical as well as competitive edge. Also HSFQ 450 grade is gradually replacing BSK 46 for chassis long members due to its inherent advantages of superior forming properties along with high strength. Higher yield strength allows user to increase strength of the finished component or to reduce thickness. The higher strength and formability property also allows the user to manufacture the end products by press forming. The formability of the steel is adjudged by high hole expansion ratio, low YS/UTS ratio and higher elongation. By judicious micro alloying finer grain size has been achieved which in turn enhances the strength and toughness of the material. The newly developed HSFQ hot rolled steel possess an attractive combination of strength and formability property which is typically quantified as high elongation (25% min) and hole expansion ratio (145 % min) coupled with lower YS/UTS ratio (0.80-0.85). This has been possible as a result of innovative alloy design and synergistic effect of Nb & Si during controlled processing. The synergistic effect of silicon in presence of Nb has contributed to greater availability of carbon for enhanced precipitation of Nb(CN) during hot rolling resulting into formation of fine ferrite grains[2]. The grain size was found 6.7 to 7.8 microns equivalent to ASTM No. 11-12 and these fine grains are very much suitable for forming applications like long and cross members of auto chassis, pre-engineered building (PEB) structures etc.
2. Materials & Experimental Procedure
Characterization of developed grades is very important to validate process design and its impact on various attributes of the desired product. Performance trials at customer’s end were also conducted to evaluate mechanical properties with adequate cold reducibility. The effect of Silicon on grain refinement was investigated in industrially produced Nb-microalloyed steel. Synergistic effect of Si in presence of Nb has been found to favour grain refinement in hot rolled strip. Evolution of such a fine grain has been related to the enhanced precipitation of Nb(CN) in presence of silicon. As a result the concept of effective (Nb+Si) has been introduced for commercial production of these grades.Initially trial heat of IS 10748 Gr. V with Nb was made at Steel Melting Shop (SMS) through BOF-VAR-LF-CC route and hot rolled successfully in the Hot Strip Mill (HSM). The process cycle was optimized and desired properties of HR coil (UTS: 490 MPa min.; YS: 310 min. & %EL: 15 min.) was achieved by adding Nb in the range of 0.015-0.020%. Based on the encouraging results obtained trial heat of IS 5986 Fe 510 grade was also made using Nb in the range of 0.020-0.025% to achieve the desired mechanical properties. While processing these materials, the mill load was maintained well within the finishing mill capacity by maintaining adequate slab soaking time in the reheating furnace. Earlier experiences of rolling high strength steel[1,3] was incorporated during development of these grades as there is limitation of rolling very high strength materials due to higher mill load envisaged in an underpowered mill. Similarly high strength formable quality (HSFQ 350) steel was developed with innovative alloy chemistry with lower Nb: 0.020-0.025% as the properties are more or less similar to IS 5986 Fe 510 grade. Development of high strength formable quality (HSFQ 450) steel was really a technical challenge due to the requirement of unique combination of properties such as increased strength, toughness, formability and weldability in the HR strips. Alloy chemistry was designed considering the application and processed industrially to achieve the desired properties in the hot rolled strips. High strength formable quality (HSFQ 450) steel was developed with innovative alloy chemistry (lower Nb: 0.040-0.050% and higher Si: 0.25-0.35%) which resulted into superior formability properties in terms of higher El (28-30%) and hole expansion ratio (λ>145 %) coupled with lower YS/UTS ratio (0.82-0.86). The hot rolled coils in the sizes of 4.9 & 6.1 mm were cold formed to manufacture the long chassis members of the vehicles.Detailed characterizations of all the products developed were carried out in detail. Metallographic specimens were prepared as per ASTM E3-2001 standard and the etchant used was 2% nital solution for microstructural examination. Microstructural examination was carried out as per ASTM E45-2005 standard using a Olympus X-71 microscope. A further investigation was also carried out using scanning electron micrograph (SEM) JEOL JSM 840A.
3. Results & Discussions
It is generally perceived that silicon is detrimental to forming behavior of steel as it increases hardness and also silicates inclusion act as crack initiation sites during forming. With the advancement of steel making facilities, aluminium is predominantly used as deoxidiser and silicon can be added when oxygen levels are very low. It results in minimization/elimination of silicates inclusions thereby reduction in incidence of crack. As silicon is a cheap alloying element and it also improves the castability with better desulphurization, addition of Si with Nb in optimized percentage has been considered for development of these grades.It is well known that carbonitride precipitation influences microstructural evolution during the hot rolling of microalloyed steels[4,5]. It therefore plays a key role in determining the final mechanical properties of a wide range of steel products. Despite extensive studies carried out during the past decades, many details regarding the precipitation behaviour remain unclear. One such example is how the addition of a third element, such as Si, influences the precipitation kinetics of Nb(C, N) in austenite during hot working. The effect of Si on the thermodynamics of precipitation was taken into account much early but it has attracted more attention recently. It was also suggested that Si addition should increase the precipitation rate, but there has been no direct experimental confirmation of this effect to date. Recent investigations,[6-7] indicate that the addition of Si may be responsible for accelerating Nb(C, N) precipitation in Nb-bearing microalloyed steels and therefore for preventing the occurrence of softening during hot strip rolling. These indirect observations indicate that there is a clear need for fundamental information regarding the effect of Si on the thermodynamics and kinetics of Nb(C, N) precipitation. Table 1. Chemical Composition of the Grades  |
| |
|
Before commercial production detailed laboratory experiments and investigations were carried out to study the effect of Nb and Si contents on ferrite grain size in hot rolled coils and the concept of effective Nb emerged. The effective Nb was computed by taking into account combined effect of Nb and Si,[Nb (wt%) + Si (wt%)/ 20]. However, the factor Si/20 has been further adjusted based on large-scale industrial trials. Conventional hot rolled high strength formable grades are produced with higher Nb (> 0.06 %) and restricted Si (< 0.05 %). For better formability property and specified application a new alloy design concept with lowr Nb and higher Si was used. The steel with lower Nb (0.04%) and higher Si (0.33 %) contents produced superior formability properties in terms of higher elongation (32 %) and hole expansion ratio (145 %) coupled with lower YS/UTS value (0.86). It has been found that in case of newly developed steel, Nb content (0.04%) was 30% lower than that of conventional steel and yet there was no appreciable increase in ferrite grain size, indicating positive role of Si in Nb containing steel towards enhanced precipitation of Nb(CN) and thus grain refinement. The chemical composition and mechanical properties of all these grades is illustrated in Table-1 & 2. Table 2. Mechanical Properties of the Developed Grades 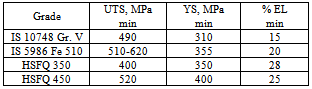 |
| |
|
3.1. IS 10748 Grade V
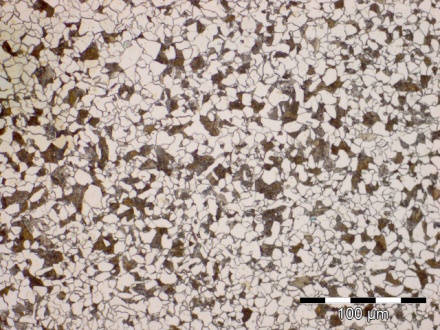 | Figure 1. Typical Ferrite Pearlite microstructure of IS 10748 Gr. V HR Coil |
Alloy chemistry was designed by addition of Nb in the range of 0.015-0.020% along with reduction in Mn in the range of 1.00-1.20% to achieve the desired properties in HR coils. The extra cost due to addition of Nb has been compensated by the reduction in Mn % in the steel (1.00-1.20% from 1.10-1.30%). The process cycle was optimized and desired properties of HR coil (UTS: 490 MPa min.; YS: 310 min. & %EL: 15 min.) was achieved. Fig. 1 shows the typical ferrite pearlite microstructure in the hot rolled coil. The material was supplied to various customers in the size range of 4.8x950; 5.9x1250; 3.6x1040; 3.2x1040 & 4.8x1040 mm HR coils. The main application of this grade is for electric poles, tubes & pipes.
3.2. IS 5986 Fe 510
Alloy chemistry was designed by keeping Nb in the range of 0.020-0.025% to achieve the desired mechanical properties. Chemistry was designed and the process cycle was optimized to develop a high strength formable quality variant of steel. The unique feature of this difficult to cast grade was the combination of very high strength (UTS: 510-620 MPa; YS: 355 MPa min) along withreasonable %EL (20 min) for its forming properties. Fig. 2 shows the typical ferrite pearlite microstructure in the hot rolled coil. The material was supplied to various customers in the sizes of 3.1x1030; 3.8x1030; 6.0x1410; 6.3x1410 & 5.6x1060 mm HR coils. 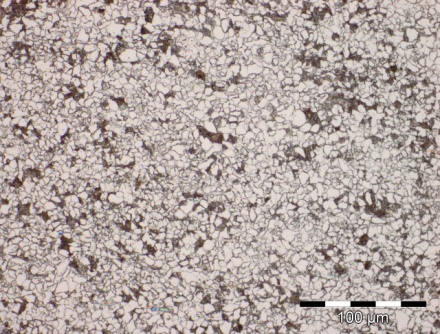 | Figure 2. Typical Ferrite Pearlite microstructure of IS 5986 Fe 510 Grade HR Coil |
The material has been successfully used for fabrication of high mast lighting poles, wind poles, camera poles etc. The high mast poles manufactured from this grade has been used in India as well as exported to Middle East countries such as Saudi Arabia, Jordan etc.
3.3. High Strength Formable Quality (HSFQ 350)
SAIL forming grades with YS 350 MPa min. are used mainly for application in auto components after cold forming. These high tensile coils with higher forming properties are better substitute of SAILMA 350 due to its economical as well as competitive edge. The mechanical properties achieved are very encouraging with respect to lower YS/UTS ratio (0.77 to 0.80) and close bend which are very much suitable for forming operations. Fig. 3 shows the typical ferrite pearlite microstructure in the hot rolled coil. The grain size was found 7.0 to 8.0 microns and these fine grains are very much suitable for forming applications due to presence of Nb & Si in this type of steel. 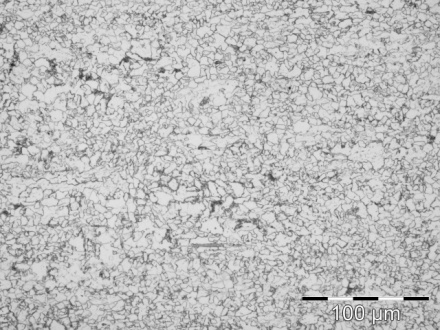 | Figure 3. Typical Ferrite Pearlite microstructure of HSFQ 350 Grade HR Coil |
3.4. High Strength Formable Quality (HSFQ 450)
HSFQ grades with YS 450 MPa min. are used mainly for application in auto components after cold forming. These high tensile coils with higher forming properties are better substitute of SAILMA 450 due to its economical as well as competitive edge. Also HSFQ 450 grade is gradually replacing BSK 46 for chassis long members due to its inherent advantages of superior forming properties along with high strength. The material was cold reduced from 4.6 mm to 2.05 mm and annealed successfully at the customer’s end. Cold rolled and annealed material met the high UTS requirement (520 MPa min) to cater automotive segment in high tensile applications. Addition of silicon in HSFQ grade has improved ease of casting due to increased flowability, better desulphurization at secondary refining stage leading to reduction of cost. The synergistic effect of Si in presence of Nb resulted in ferrite grain size of 6.7 to 7.8 microns equivalent to ASTM No. 11-12. Such a fine grain with 0.04 % Nb and 0.33 % Si has potential to meet the stringent quality requirements of high strength (>520 MPa) and good formability property in commercially produced hot rolled steel. The typical microstructure is shown for HSFQ 450 (Fig. 4a) & BSK 46 (Fig. 4b) and it was found that finer grain size in HSFQ 450 grades lead to higher formability property i.e. hole expansion ratio (λ) was 145% compared to 130% obtained in case of BSK 46 material. The yield strength of the HSFQ 450 HR Coil was in the range of 455-488 MPa with % elongation in the range of 27-30. The YS /UTS ratio was found to be in the range of 0.82-0.87. The automotive industry from all over the world has been constantly pursuing development of new design and materials for achieving reduced weight and improved crash performance of vehicles. High strength steels owing to their higher strength with moderate forming capacity favour application of thinner gauge sheets, reducing overall weight of car and saving in fuel consumption. In line with global development, high strength formable quality (HSFQ 450) was developed in recent past with innovative alloy chemistry where synergistic effect of niobium and silicon led to an attractive combination of strength and forming properties. This newly developed grade has a wide range of applications such as auto-chassis, load bearing structural components and wheel, roll formed section specially suited forPre-Engineered Building (PEB) manufactures etc. Pre-engineered buildings are cost-effective infrastructure solutions that provide design flexibility plus abridged construction time. Some of the advantages of these buildings include reduced construction time, lower cost, flexibility of expansion, quality control, low maintenance, energy efficient roofing and wall systems, and architectural versatility. These are used in warehouses, factories, workshops, offices, gas stations, vehicle parking sheds, gas stations, aircraft hangers, schools etc. HSFQ 450 grade has been successfully used for various end products e.g Pre-engineered building structures and auto chassis members. 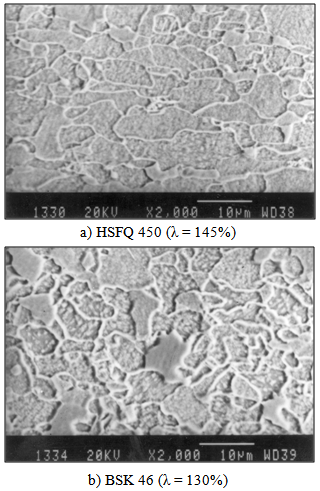 | Figure 4. Typical Scanning Photograph showing Ferrite Pearlite microstructure in HSFQ 450 & BSK 46 Grade HR Coil (λ designates hole expansion ratio) |
4. Conclusions
Based on the above findings the concluding remarks are as follows:i) Depending on market opportunity for various end applications, several new grades of special steel products have been developed. Customer’s requirement has been assessed and the grades have been developed considering the plant capability. Necessary changes in alloy design and processing conditions nave been incorporated from time to time to satisfy the specific requirements of the customer. ii) The micro alloyed developed grades (IS 10748 Gr. V, IS 5986 Fe 510, HSFQ 350/ 450) which are difficult-to-cast, have been fully developed and commercialized by optimizing product chemistry, casting and rolling parameters. Extensive customer interaction in different regions and continuous monitoring resulted in achieving & maintaining desired quality for these medium carbon grades. The performance feedback from various customers was found to be very good and developmental efforts have been well appreciated by the customers. iii) Positive role of Si in Nb for grain refinement has been achieved during development of hot rolled steel with lower Nb (0.040 wt%) & higher Si (0.33 wt%) contents resulting higher elongation (32%) and hole expansion (145%) values maintaining lower YS/UTS ratio (0.85) & fine grain size (< 8 microns).iv) Based on the encouraging results through laboratory investigation and commercial production along with performance trial at customers end a new series of HSFQ grades has been formulated, fine tuned and commercialized.
ACKNOWLEDGEMENTS
The authors wish to acknowledge the management of Steel Authority of India Limited (SAIL) for giving permission to publish this work.
References
[1] | John J Jonas, ISIJ International, 2000, Vol. 40, No. 8, pp 731-738. |
[2] | J. X. Dong, F. Siciliano, J. J. Jonas, W. J. Liu and E. Essadiqi, ISIJ International, 2000, Vol. 40, No. 6, pp 613-618. |
[3] | A. K. Bhakat, Journal of Failure Analysis and Prevention, ASM International, 2010, Vol. 10, No. 6, pp. 463-467. |
[4] | Pereloma E.V., Crawford and Hodgson, Material Science and Engineering, 2001, A299, pp. 27. |
[5] | Dutta B., Palmiere E. J. and Sellars C. M., Acta Materialia, 2001, Vol.49, pp.785. |
[6] | Takehide Senuma, ISIJ International, 2001, Vol. 41, No. 6, pp. 520-532. |
[7] | David San Martin, Francisca G. Caballero, Carlos Capdevila and Carlos Garcia De Andres, Materials Transactions, The Japan Institute of Metals, 2004, Vol. 45, No. 9, pp 2797-2804. |