S. O Seidu1, B. J Kutelu2
1Department of Metallurgical and Materials Engineering, Federal University of Technology, Akure, Nigeria
2Department of Mineral Resources Engineering, Federal Polytechnic Ado-Ekiti, Nigeria
Correspondence to: S. O Seidu, Department of Metallurgical and Materials Engineering, Federal University of Technology, Akure, Nigeria.
Email: |  |
Copyright © 2012 Scientific & Academic Publishing. All Rights Reserved.
Abstract
This study investigates effects of mould additives on the hardness property of grey cast iron. Five moulds with 25% iron dust, 25% coal dust, 25% saw dust and 25% iron dust, coal dust and saw dust additives were prepared respectively with silica sand using bentonite as a binder in wooden mould boxes. The melt was prepared with selected scraps which after superheated to 1555℃ were tapped while 0.2% inoculant (Fe-Si) was added to the stream to allow uniform dissolution of the inoculant in the melt. Thereafter, the melt was quickly poured into the prepared moulds to avoid gasification of the inoculants where cooling and solidification occurred. Hardness measurement was made using standard approach with Rockwell hardness (HRc). Specimens for microscopy studies were prepared from the samples by machining to appropriate dimensions. Etching for eutectic cells photography and microstructure were done by using Stead’s reagent and nital respectively. The microstructures were examined. Results obtained revealed microstructures with varied amount of eutectic cells and different graphite morphologies. Also, highest hardness value of 61.10 HRC was revealed by mould with saw dust additive and lowest with coal dust additive with 42.10HRC.
Keywords:
Keyword Mould Additives, Inoculation, Hardness, Microstructure, Eutectic Cell, Grey Iron
Cite this paper: S. O Seidu, B. J Kutelu, Effects of Mould Additives on Hardness Property of Grey Cast Iron, International Journal of Metallurgical Engineering, Vol. 2 No. 2, 2013, pp. 238-242. doi: 10.5923/j.ijmee.20130202.16.
1. Introduction
Cast iron is the common metallic materials used for numerous applications in different industries. The use of cast iron for structural purposes began in late 1770s, it was used in constructing bridges and railways notable examples includes Holyhead railway river Dee in Chesterand toy rail bridge. Regrettably, these structures were found to ail, and one possible cause was traced to inappropriate material selection[1]. There is a wide commercial application of cast alloy treatments that modify the initial solidification characteristics to provide a means for effective control of grain size and morphology, prominent among these is inoculation.[2], defined inoculation as the process of modification of cast structure by the addition of substance to the melt for the purpose of nuclei formation during crystallization, the success of inoculation approach has been established by past researchers. Apart from the use of inoculants, foundry sand are equally expected to satisfy some requirements among which are chemical compatibility with the process or processes employed, consistency, satisfactory development of strength and where applicable the rate of strength development and the ability of manufactured molds and cores to produce the desired casting quality[3]. Among the various types of cast iron for engineering applications, grey cast iron is the most commonly used iron and the most widely used cast material base on weight[4]. Although, it has less tensile strength and shock resistance as compared to steel, its relative cheapness, ease of melting and casting, very good machinability, high damping capacity, good resistance to wear, good compressive strength and high fluidity which makes it easy to form into intricate shapes and melting point of between 1147 and 1250℃, which is considerably lower than that of mild steel are derivable advantages that make it a preferred material of choice for a number of engineering applications including engine blocks, flywheels, cylinder heads, machine beds and brake drums[5].In the recent years, the importance of the relative versatility of this attractive engineering material (grey cast iron) as compared to the other types of cast iron has been widely applauded. However, very scanty information is available in the literatures on how the qualities of products from this material can be enhanced through other means different from the conventional inoculation method. It is well understood that the solidification process by which a liquid metal freezes in a mold plays a critical role in determining the microstructures and mechanical properties of the as-cast alloy[6] and since properties can also be developed in as- cast products by blending sand or other refractory’s with bonding materials, water and special additives[7]. Therefore, a consideration of an alternative means by which the condition of the mold can be modify for optimum solidification structures through special additives is imperative if the desired improved service performance of products from grey cast iron is to be adequately realized. To this end, effects of some additives including saw dust, iron filling and coal dust on the microstructures and hardness property of grey cast iron was investigated in this work. Consequently, known quantities of the additives were added to the silica sand that was used to produce the molds with mold boxes of steel material.
2. Materials and Method
2.1. Materials
The materials used were scrap (automobile part), silica sand, bentonite, coal dust, iron dust and saw dust. And The equipment used include molding box, rammer, vent wire, weighing scale, sledge hammer, metallurgical microscope Model-Axio with camera attached, shovel, electronic weighing scale and oil fired rotary furnace of 100kg capacity.The chemical composition of the scrap is depicted in Table 1Table 1. Chemical composition of scrap from auto parts (wt.%) |
| C | Si | Mn | P | S | 3.97 | 1.94 | 0.87 | 0.088 | 0.131 | Cr | Ni | Al | Cu | Mo | 0.163 | 0.058 | 0.058 | 0.137 | 0.015 |
|
|
2.2. Method
A wooden pattern of 50 mm length, 30 mm breadth and 20 mm thickness used for producing the experimental samples was machined to shape with wood lathe machine with contraction allowance of 1.5% introduced. Thereafter, the silica sand and bentonite (binder) were manually mixed together and water was added to the mixture to fill into the pores, to form a sort of microfilm and to impart the desired strength to the sand. The resulting mould which serves as control for the experiment was labeled sample A. Subsequently, other moulds labeled samples B to E with additives were also produced. The procedures involved is stipulated in Table 2 Table 2. Procedures for Mould Preparation |
| | Additives | Percentage composition in the mould | A | Control | 0 | B | Iron dust | 25% | C | Saw dust | 25% | D | Charcoal dust | 25% | E | Saw dust, charcoal dust and Iron dust | 25% |
|
|
The quantity of melts required to cast the moulds were determined with relevant design calculations, and the obtained scraps carefully selected and cleaned to avoid melt contamination during melting. During tapping of the resulting liquid metal from the furnace at the temperature of 1520℃, 0.2% inoculant (Fe-Si) was added to the stream to allow uniform dissolution of the inoculant in the melt. Thereafter, the melt was quickly poured into prepared moulds to avoid fading of the inoculants after which cooling and solidification occurred. The chemical analysis of the Fe-Si inoculants and of the cast are shown in Tables 3 and 4 respectively Table 3. Chemical composition of the Fe-Si inoculants used |
| Element | Si | Ca | Al | Zn | % Composition | 74.22 | 2.44 | 1.21 | 1.21 |
|
|
Table 4. Chemical composition of 0.2% inoculated sample |
| C | Si | Mn | P | S | 2.783 | 3.252 | 0.313 | 0.158 | 0.063 | Cr | Ni | Mo | Al | Cu | 0.110 | 0.050 | 0.011 | 0.002 | 0.162 |
|
|
2.3. Metallography
Specimens for microscopy studies were prepared from the scrap (automobile part) and cast samples by machining to dimensions of 10 mm length, 10 mm breadth and 8 mm thickness; they were mounted on thermosetting material known as Bakelite in order to make them convenient for handling. Thereafter, the surfaces of the specimens were then flattened by filing and grinding using laboratory grinding and polishing machines with a set of emery papers of 240, 320, 400, 600, 1000 and 1200 microns. The grinding was done in order of coarseness of the papers. As each specimen was change from one emery papers to the other, it was turned through an angle of 90o so as to remove the scratches sustained from the previous grinding. After grinding, the specimens were polished using rotary polishing machine, to give it mirror like surface, and in conformity with[8] a polishing cloth was used to polish the surface of the specimens. However, during the course of grinding and polishing, water was added on the samples and papers to prevent heat build-up and wearing away of the grit on the papers. Etching for eutectic cells photography was performed first, by using Stead’s reagent of composition 2g of CuCl2.2H20; 8g of MgCl2.6H20; 4ml of HCl; and 100ml of grain alcohol, while that of the microstructure was done using Nital solution (2% nitric acid and 98% alcohol). The microstructures were examined at a magnification of 100xx.
2.4. Hardness Test
Samples of dimensions 10 mm length, 10 mm breadth and 6 mm thickness were cut and machined to standard hardness specimens, they were properly ground to ensure flat and stable surface using a hand grinder. Thereafter, hardness measurement was made using Rockwell hardness testing machine with 16 inches indenter and 60gf indenting load with a dwell time of 10s. Hardness measurements were made in three different locations and the average value was taken [9], the results are shown in Table 5.
3. Results and Discussion
3.1. Eutectic Cell and Microstructure Characteristics
The cast samples were prepared and testing was carried out according to ASTM testing specification throughout the experiment. The results were compared with the standard [10].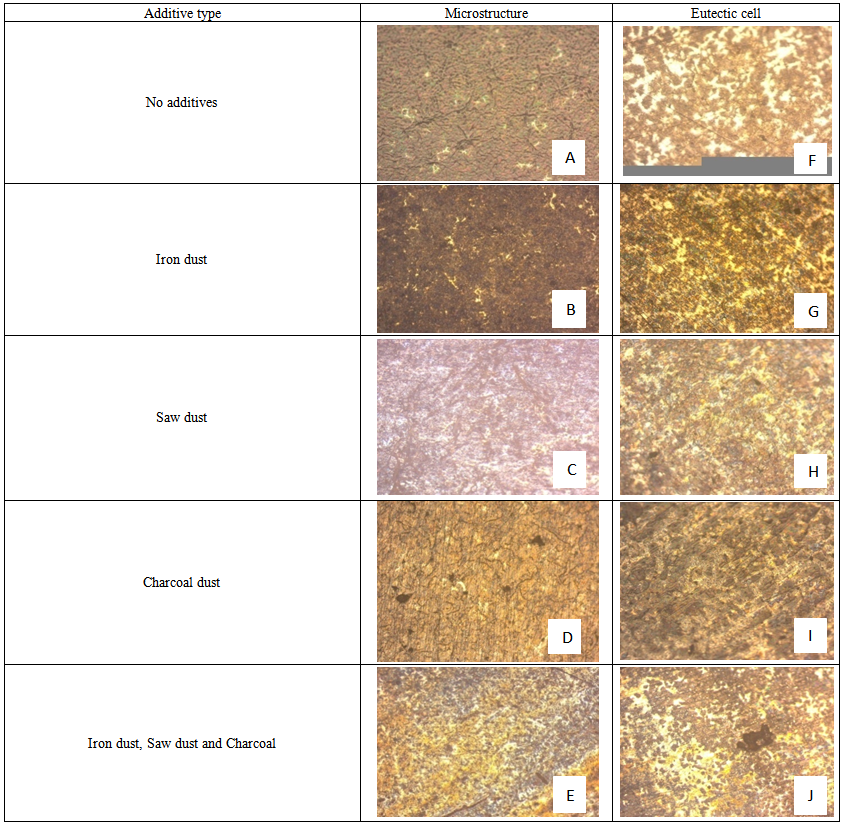 | Figure 1. A-E and F-J: Microstructures and Eutectic cells of inoculated gray cast iron with no and with 25% mould additives etched in 2% nital solution and Stead’s reagent respectively at a magnification of 100xx |
Table 5. Hardness Results of Gray the Grey Cast Iron Samples |
| S/N | Sample | Sample Description | 1st | 2nd | 3rd | Average Hardness (Hrc) | 1 | A | No Additive | 58.6 | 58.8 | 59.2 | 58.90 | 2 | B | 25% Iron Dust | 59.6 | 59.7 | 59.4 | 59.60 | 3 | C | 25% Saw Dust | 61.2 | 61.1 | 61.0 | 61.10 | 4 | D | 25% Coal Dust | 42.0 | 42.1 | 42.2 | 42.10 | 5 | E | 25% Iron, Saw and Coal Dusts | 51.1 | 51.0 | 51.3 | 51.10 |
|
|
In general, Fig. 1(F) through 1(J) was found to be composed majorly of eutectic cells (white patches) in between austenite (dark portion) and ferrite (white portion).[6], reported that in flake graphite cast iron, the austenite-graphite eutectic solidification process is concomitant with the formation of eutectic cells that are more or less spherical. These eutectic cells consist of interconnected graphite plates surrounded by austenite, and according to[3], on the concave surface of graphite rosettes, an austenite nucleates and surrounds the central part of the rosette, rising along its branches and leading to the creation of eutectic cells, and from each nucleus, a single eutectic cell is formed. From the characteristic feature of the inoculated grey cast iron sample with no additive depicted by Fig.1(F), the sample revealed low eutectic cells which may have resulted from lack of sufficient nuclei, also the corresponding microstructural features of the sample revealed by Fig. 1(A), showing graphite morphology (graphite type D) with a rosette graphite flakes in a dendritic structure may have been influenced by low eutectic cells. Also, the observed reduction in graphite flakes formation may be due to lack of mould additives[11].The large percentage of eutectic cells obtained with inoculated grey cast iron sample with 25% iron dust depicted in Fig. 1(G) could have resulted from a relatively large number of nuclei for graphite formation in the eutectic iron melt, and according to[12], mould additives are found to increase eutectic cell count in a given cast iron. The obtained corresponding microstructural feature of the sample given in Fig.1(B), showing an inter-dendritic structure with a uniform distribution of graphite flakes in a complete ferritic matrix may be due to full graphitization, which may have resulted from decomposition of cementite to ferrite and graphite[7]. Some advantages of increased eutectic cell count includes: increased strength through a reduction in ferrite and an increase in graphite type A, improved machinability due to a reduced chill of cast iron, free from the high hardness carbide eutectic, and increasing pre - shrinkage expansion[3].[12], revealed that the number of nuclei also represents the number of eutectic cells. Therefore, the more eutectic cells observed in inoculated grey cast iron sample with no additive relative to inoculated grey cast iron sample with 25% of sawdust as revealed in Fig. 1(F) and (H) respectively, may have been due to formation of more nuclei in the later, while the obtained corresponding microstructure of the inoculated grey cast iron sample with 25% of sawdust in Fig. (C), showing graphite morphology (graphite type A) in an inter-dendritic structure with a uniform distribution of graphite flakes in a complete pearlitic matrix may have be influenced by the properties of the molding sand[12]. The increased percentage of eutectic cells in inoculated grey cast iron sample with 25% of charcoal dust as compared with inoculated grey cast iron sample with 25% of sawdust depicted by Fig. 1(I) and (H) respectively, may be accounted for by the relative effects of the additives on the cooling rate of the eutectic iron melt, and in which the former may have showed more effect. The microstructure, Fig. 1(C), which revealed graphite morphology (graphite type A) in an inter-dendritic structure with a uniform distribution of graphite flakes in a complete ferritic matrix may have be due to full graphitization resulting from the decomposition of cementite to ferrite and graphite[7]. Fig. 1(J), which depicts inoculated grey iron sample with 25% of iron dust, saw dust and charcoal dust revealed a significant amount of eutectic cells as compared to Fig. 1(F). This observation may be due to the combined effects of the additives on the cooling rate in which rapid cooling and hence more nuclei are formed.
3.2. Hardness Property of the Cast Samples
[12], reported that if the mould lacks sufficient rigidity, expansion of the casting during solidification can cause unsoundness in the form of internal porosity. Hence, the relative low hardness value of 42.10 HRC of the inoculated grey cast iron sample with 25% charcoal dust additive as compared to sample with no additive (control) with hardness value of 58.9 HRC may have among other factors be due to low solidification resulting from low internal porosity. The observed improved hardness property of the inoculated grey cast iron samples with additives in the respective increasing order of 25% coal dust, 25% iron dust, 25% saw dust, coal dust and iron dust, and 25% saw dust may have resulted from relative amount of eutectic cells produced in the solidified samples[2]. Also, variations in graphite morphology in the final microstructures may have contributed to the observed hardness characteristics[12]. The observed superior hardness property of sample with saw dust additive as compared to samples with other additives may be due to the resulting small grain size of the phases[7]. Due to high combustibility of saw dust relative to iron dust and coal dust, more pores are produced in the mould, a tendency that favours increased cooling and solidification rates with concomitant small grains formation.[13], has associated low porosity, high bulk density, high compressibility strength, high shear strength and low hardness with increase in grain size of phases, a consequence which he said allows for easy movement of the dislocation in the molten metal during solidification Hence, the relative low hardness value of the inoculated sample with 25% of coal dust may have resulted from increased grain size of the phases.[14], has attributed moulding sand with increased permeability and porosity, and decreased bulk density, compressibility strength and shear strength to rapid cooling, a situation that leads to increase in the amount of grain particles (fine grains) which are known to hinder movement of dislocation, and according to[1], rapid cooling prevents graphitization and encourages cementite formation.[12], revealed that large percentage of eutectic cells can lead to unsoundness of cast products.[5], reported that there is improvement in the graphite morphology with increase in eutectic cells, and according to[7], low graphite flakes aids high tensile strength and high hardness while excess graphite flakes in morphology encourages low tensile strength and low hardness (maximum machinability). Therefore, the significant improved hardness of the inoculated sample with 25% saw dust over inoculated sample with 25% saw dust, 25% coal dust and 25% iron dust may have been due to increasing amount of eutectic cells which may have resulted from the synergic effects of these additives, while the revealed relative high hardness of both the inoculated sample with no additive and inoculated sample with iron dust additive over the inoculated sample with 25% saw dust, 25% coal dust and 25% iron dust may equally be accounted for by more eutectic cells in the former.
4. Conclusions
The mould additives were found to control essentially cooling and solidification rates of casting in the respective moulds investigated, and since the rates were found to vary from mould to mould, microstructures with different morphologies were obtained. Hence effects of these additives on hardness characteristic of the cast iron were found to be equally different with the highest hardness value revealed by mould with saw dust additive and lowest with coal dust additive. However, the synergic effect of saw dust, iron dust and coal dust was found to be a disadvantage as excessive eutectic cells which are detrimental to improved hardness are produced.
References
[1] | Degarmo, E. Paul; Black, J.T. and Kohser, Ronald A (2003): Materials and processes in manufacturing (9th ed.), wiley, ISBN 0-471-65653-4. |
[2] | Seidu, S.O.(2009) : Inoculant’s effect on chilling tendency in ductile iron, WTF Ph.D International Conference, Brno Czech Republic |
[3] | Alexander B, (2011): Graded coal-its role in iron casting production from greensand systems, james durrans & sons ltd, phoenix works, penistone, sheffield s36 9qu, England. |
[4] | S.Strobi, (2000) Fundamentals of green sand preparation and control, modern casting |
[5] | Mukherjees P.C (2003): Mould section material, properties and testing fundamental of metal casting technology, pp703-754. |
[6] | Scott D.A (1991): Metallography and microstructure of ancient and historical metals. marina del rey, the getty conservation institute in association with archetype books. |
[7] | C.Deepak, (2008): Green sand management – role & application of carbonaceous additives and concept of total carbon in a green sand system, 68th world foundry congress, pp. 127-132 |
[8] | Beno J, Jelinek P (2009): Solution of negative impact of carbonaceous additive to bentonite mixtures, international PhD foundry conference. |
[9] | Donald B., Wagner (2008): Science and civilisation in china: volume 5, chemistry and chemical technology, part 11, ferrous metallurgy. cambridge university press, 8, ISBN 978-0-521-87566-0, pp 159–169. |
[10] | Properties and selection: Irons, steels and high performance Alloys selection: Cast iron, ASM Hand book vol. 1 Sept. 2005, pg 37-47. |
[11] | Paul Aondona (2011): Effects of the moisture content on the foundry properties of Yola natural sand. leonardo electronic journal of practices and technologies ISSN 1583-1078, 19 July – Dec., 2011, pp 85-96. |
[12] | Adedayo A.V. 2010 Effects of addition of iron fillings to green moulding sand on the microstructure of grey cast iron, Journal of Brazilian society for mechanical and Engineering, Vol. XXXII, No 2, pp 171-175. |
[13] | Cast iron inoculation (the technology of graphite shape (control) booklet, Elkem foundry products,www.foundry.eElkem.com,march 2007 |
[14] | Higgins, R.A (2004): Engineering metallurgy: applied physical metallurgy”, 6th ed. viva books, new delhi, pp. 355-356. |