S. Srikanth1, P. Saravanan1, Vinod Kumar1, D. Saravanan2, L. Sivakumar2, S. Sisodia2, K. Ravi1, B. K. Jha1
1R&D Centre for Iron and Steel, Steel Authority of India Limited, Ranchi-834 002, India
2Salem Steel Plant, Steel Authority of India Limited, Salem-636 013, India
Correspondence to: S. Srikanth, R&D Centre for Iron and Steel, Steel Authority of India Limited, Ranchi-834 002, India.
Email: |  |
Copyright © 2012 Scientific & Academic Publishing. All Rights Reserved.
Abstract
Metastable austenitic stainless steel type 301LN is widely used for fabrication of structural components of Metro Coaches. The steel exhibits both high strength and enhanced plasticity due to strain hardening as well as formation of strain-induced martensite (α′) during cold deformation (TRIP effect). The current market requirement, as projected by many of the ongoing Metro Rail Projects in India, calls for manufacture of this steel with ultimate tensile strength (UTS) in excess of 1000 MPa and yield (YS/UTS) ratio of less than 0.8, as this would facilitate substantial reductions in tare weight and crash-worthiness of metro coaches. The typical property requirements in high temper (HT) as per one typical Metro Coach specification are: Yield Strength (YS) ~ 751-921 MPa, Ultimate Tensile Strength (UTS) ~ 1001-1151 MPa, Elongation ~ 22% min, Hardness ~ 36 HRC max and YS/UTS ratio <0.8. Previous plant experience has shown that the maximum attainable UTS in this grade through cold rolling is only to the tune of 970 MPa and any excess deformation severely impairs both ductility (< 22%) and hardness (> 36 HRC) beyond acceptable limits. In the present work, an innovative thermomechanical processing (TMP) methodology has been evolved for the attainment of this seemingly unlikely combination of properties through experimental cold rolling and short annealing simulations in Gleeble 3500 C thermomechanical simulator. The novel process methodology entails imparting heavy cold reductions (CR) of 45-50% in Sendzimir Mill followed by brief/ short reversion annealing treatments (80-160 s) by means of single furnace operation at 750 oC at standard line operating speeds for 300 series in Annealing Pickling Line-1 (AP Line-1) of Salem Steel Plant (SSP) in India. The improvement in properties (strength-ductility combination) has been attributed to grain refinement through formation of submicron grained austenitic (γ) microstructure by controlled reversion of strain-induced martensite (α′) during the short annealing treatment. The process is distinct from conventional long annealing treatments (300-360 s), which are employed to soften the steel after cold rolling by means of recovery and recrystallization processes.
Keywords:
Austenitic Stainless Steel, Cold Rolling, Strain-Induced Martensite, Reversion Annealing, Grain Refinement
Cite this paper: S. Srikanth, P. Saravanan, Vinod Kumar, D. Saravanan, L. Sivakumar, S. Sisodia, K. Ravi, B. K. Jha, Property Enhancement in Metastable 301LN Austenitic Stainless Steel through Strain-Induced Martensitic Transformation and its Reversion (SIMTR) for Metro Coach Manufacture, International Journal of Metallurgical Engineering, Vol. 2 No. 2, 2013, pp. 203-213. doi: 10.5923/j.ijmee.20130202.12.
1. Introduction
Austenitic stainless steels (ASS) are traditionally used in various applications requiring good corrosion resistance and formability. However, their biggest demerit is that the yield strength is quite low, e.g., 230-260 MPa for EN 1.4301 (AISI 304), and 350-380 MPa for EN 1.4318 (AISI 301LN) steel. This limits their use for structural applications. The tensile strength of these steels is in the range of 600 to 800 MPa and total elongation varies between 45 to 60%. With respect to the ratio of strength and elongation, however, stainless steels are located well above the ranges of carbon steels[1,2].In recent years, there has been a growing interest in developing the “third generation” of advanced high strength steels, including stainless steels, for light weight constructions. These steels possess nano/ultrafine grained microstructures with excellent combinations of strength and ductility[3,4]. Since austenitic stainless steels (ASSs) do not undergo any transformation during hot deformation, the grain refinement may be achievable only through the occurrence of recrystallization in the microstructure[5]. According to literature, the level of grain refining achieved by these processes is very limited (about 5 μm)[6]. Fig.1 depicts the classical “Banana Curve” showingstrength-ductility combinations of various advanced high strength steels (AHSS) including typical property range for conventional annealed as well as temper-rolled metastable austenitic stainless steels.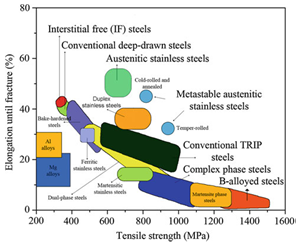 | Figure 1. “Banana Curve” showing strength-ductility combinations of various AHSS including austenitic stainless steels[7] |
Metastable austenitic stainless steels (ASS) are important grades of the austenitic family in which γ-austenite can be transformed to α´-martensite during cold deformation due to their relatively lower Ni equivalents. Hence, metastable grades exhibit higher tensile strength and better formability than the stable austenitic grades. Metastable ASSs are employed in various structural applications, such as railway and automotive structural components, due to the necessity of weight reduction and crash safety of automobiles and coaches. The martensite formation, resulting from plastic deformation of metastable austenite, is of great interest for producing high strength and ductility combinations as well as TRIP effect in austenitic stainless steels (delay in onset of necking). Such steels exhibit high strength and enhanced plasticity due to both strain hardening (increase in dislocation density, twins, stacking faults, or the Suzuki locking) and formation of strain-induced martensite (α′) during cold deformation (TRIP effect). Substantial strengthening can be obtained by plastic deformation below Md temperature (Md is the highest temperature at which the martensitic transformation can be induced by plastic deformation) to produce bcc α´ and hcp ε martensite. The transformation of fcc austenite γ to α´ and ε martensite depends on the alloy composition, stacking fault energy, degree of deformation, plastic strain, strain rate, grain size, temperature, etc.[8,9].A novel processing route of controlled reversion annealing of the heavily cold-deformed martensite in metastable Cr-Ni austenitic stainless steels has been employed resulting in highly refined austenite grain size by a number of researchers[2,10-13]. In the first stage, the deformation of austenite in the vicinity of room temperature (RT) leads to strain-induced shear transformation of austenite to martensite, and then upon annealing, this heavily deformed martensite transforms back to fine-grained austenite either through a martensitic shear or diffusional reversion mechanism. An optimized annealing schedule leads to the formation of ultrafine (nano- or submicron) grained structure leading to dramatic improvements in strength-ductility combinations[2,10-13].Fig.2 illustrates the thermo-mechanical processing (TMP) used to obtain ultrafine grained (UFG) or nano-grained (NG) austenitic structure through controlled reversion of deformation-induced martensite in metastable ASS.Amongst the wide variety of austenitic stainless steels (ASS) produced at Salem Steel Plant (SSP) in India, the metastable austenitic stainless steel type 301LN is widely used for manufacture of rail car structural components and automotive trim applications. Currently, there exists a substantial demand for this grade for fabrication of Metro Coaches suited for urban rail transportation. The steel has relatively low yield strength of 350-380 MPa and tensile strength of 600-800 MPa with total elongation of 45-60% in annealed condition. However, the current market requirement, as projected by many of the ongoing Metro Rail Projects in India, calls for the manufacture of this steel with UTS in excess of 1000 MPa and yield (YS to UTS) ratio of less than 0.8 as this would facilitate substantial reductions in tare weight and crash-worthiness of the metro coaches. The cold rolled coils (CRC) of the steel are manufactured in a wide variety of thicknesses and temper designations (namely, high temper (HT), medium temper (MT), standard temper (ST), deadlight temper (DLT) and light temper (LT)) through cold rolling and concurrent annealing cycles. Table 1 gives the nominal chemical composition of 301LN metastable austenitic stainless steel (in wt%).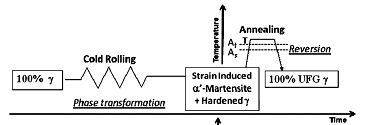 | Figure 2. TMP to obtain UFG austenitic structure through reversion of deformation-induced martensite in metastable ASS |
Table 1. Chemical composition of 301LN metastable austenitic stainless steel (in wt%)  |
| |
|
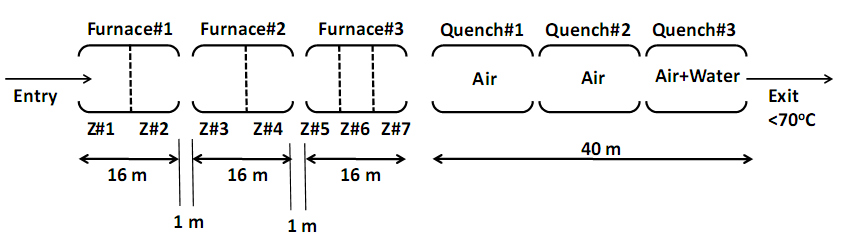 | Figure 3. Schematic layout of annealing section of AP Line-1 at Salem Steel Plant |
The cold deformation step is employed to increase the strength/ hardness by virtue of strain hardening (resulting from increased dislocation density, twins, stacking faults, or the Suzuki locking) with concomitant formation of strain-induced martensite (α′) from metastable austenite (Md30/50 = 35oC; Ms = −115oC). The steel, thus, exhibits both high strength and enhanced plasticity due to strain hardening as well as formation of strain-induced martensite (α′) during cold deformation (TRIP effect). Normally, annealing cycles are subsequently employed to attain properties in all the tempers except high temper (HT), where the steel is produced in as-cold rolled condition.The salient combination of properties required in HT temper for coil thickness of 4/ 4.5 mm as per prevalent specification for Metro Coach manufacture are: YS ~ 751-921 MPa, UTS ~ 1001-1151 MPa, Elongation ~ 22% min, Hardness ~ 36 HRC max and YS/UTS ratio <0.8. Practical experience has revealed that the maximum attainable UTS in this grade through cold rolling is only to the tune of 970 MPa and excess deformation severely impairs both ductility (< 22%) as well as hardness (> 36 HRC) beyond stipulated limits for HT temper. Accordingly, the present work was taken up to develop a suitable processing methodology for manufacture of 301LN coils with UTS > 1000 MPa, YS/UTS ratio < 0.8 and maximum hardness of 36 HRC at SSP.
2. Experimental
2.1. Base Period Study
The operational capability of Sendzimir Mill and Annealing Pickling Line-1 (AP Line-1) were studied to explore the feasibility of employing severe plastic deformation and short duration reversion annealing treatments for effecting grain refinement and property enhancement in 301LN ASS. Cold reductions to the tune of 45-50% are achievable in Sendzimir Mill; the limiting factors for higher reductions being the mill capacity and resulting strip flatness and hardness. For these reasons, thinner gauges of coils facilitate even higher reductions. The viability of short annealing treatments in AP Line-1 was also similarly examined. Fig.3 shows the schematic layout of annealing section of AP Line-1 at SSP with its discrete three-furnace arrangement and strip cooling/ quenching section. It was observed that: (1) the lowest achievable annealing temperature in AP Line-1 was around 730-750 oC, (2) the line speeds could be varied between 6 to 45 mpm (metre per minute) for coil thicknesses ranging from 4.0 to 0.3 mm, and (3) the three furnace arrangement of AP Line-1 proffers the flexibility to operate one, two or all the three furnaces, each furnace being 16 m in length. By restricting the annealing treatment to single furnace operation, short annealing cycles could be effected involving time scales of 80-160 s.
2.2. Material
Commercial 301LN austenitic stainless steel for experimentation was provided by Salem Steel Plant (SSP). Hot rolled strip samples of size 300 mm (length) x 275 mm (width) x 8.5 mm (thickness) were sourced from an solution-annealed and pickled hot rolled coil (HRC) with No.1 finish. The chemical composition of the steel is given in Table 2.
2.3. Experimental Cold Rolling
The strips were cold rolled in Hillé, UK laboratory rolling mill by imparting overall cold reductions of 45 and 50% through multipass, accumulative cold rolling in as many as 60-80 passes. Roll gap was progressively set in the mill to achieve effective thickness reductions between 3-8% in each pass. The overall thickness reduction was accomplished using progressively decreasing 10 to 12 roll gap settings. The cold rolled strips were adequately lubricated with cold rolling oil and intermittently cooled under running water to control the adiabatic heating in between passes. During rolling, the roll gap, rolling load and output thickness of the strip were continuously monitored for controlled rolling.Table 2. Chemical composition of annealed and pickled 301LN HRC sample (in wt%) 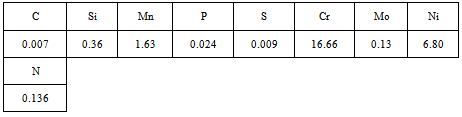 |
| |
|
2.4. Strip Annealing Simulation
Specimens of size 190 x 25 mm were sectioned transverse to the rolling direction from cold rolled strips, subjected to 45 and 50% overall cold reductions. The reversion annealing experiments were conducted in Gleeble 3500C thermomechanical simulator by imparting relatively short duration annealing treatments of 80-160 s. Two annealing temperatures viz. 750 and 800 oC were chosen for the strip annealing simulation and a single furnace length of 16 m was assumed. The annealing times were so chosen as to simulate line speeds of 6-12 mpm to comply with the requirement for 4 mm coils concomitant with single furnace operation in AP Line-1. From a practical perspective and to accord the simulation a more pragmatic approach, it was further assumed that the peak annealing temperature is attained just at 16-metre furnace exit.The uniform temperature zone in the middle of the rectangular strip specimens was estimated to be about 25 mm in length in contrast to that reported by previous researchers[2,12,13], given the fact that thicker specimens exhibit a wider uniformly heated zone at the centre. Post annealing, the strip samples were cooled in an air-mist blow, down to about 50-100 oC at a cooling rate of 200 oC/s. Fig.4 shows a schematic illustrating the annealing cycle employed in Gleeble simulations.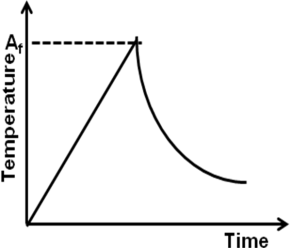 | Figure 4. Schematic illustrating annealing cycle employed in Gleeble simulation |
2.5. Metallurgical Characterization
The mechanical properties of as-received, cold rolled and reversion annealed specimens were essentially determined through tensile testing in 10-ton static tensile testing machine, INSTRON 1195. All tensile specimens were machined and prepared to dimensions according to ASTM A370-07a. While standard sized tensile specimens of 50 mm gauge length were prepared from as-received and cold rolled stainless steel samples, subsized specimens with 25 mm gauge length were machined from steel strips reversion annealed in Gleeble simulator. The subsize specimens were used owing to the limitation of narrow uniformly-annealed zone at the middle in Gleeble tested specimens. All tensile specimens were extracted transverse to the rolling direction except for as-received material, in which case the tensile specimens were machined in both rolling as well as transverse directions, to examine the variation in mechanical properties. Fig.5 depicts a schematic illustrating the location of tensile and metallographic samples in Gleeble test specimen.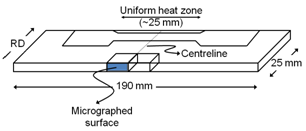 | Figure 5. Schematic illustrating the location of tensile and metallographic samples in Gleeble test specimen |
The microstructures of as-received, cold rolled and reversion annealed steels were examined both under Olympus optical microscope and JEOL JSM-840A scanning electron microscope (SEM) for qualitatively resolving and imaging the annealed, cold worked and reverted submicron austenite grain structures. In each case, metallographic specimens were sectioned and prepared carefully using conventional grinding-polishing procedures and electrolytically etched in 10% oxalic acid solution at 6 V for 30 s for microscopic observation. The volume fraction of strain-induced martensite (α′) at each stage was determined using a Helmut Fischer MP3 ferritescope. The ferritescope readings were converted to α′-martensite volume fractions by multiplying with a correction factor of 1.71, as suggested by previous researchers[14]. For further corroboration of results, Rockwell hardness measurements were also effected on as-received, cold rolled and reversion annealed specimens in INSTRON Wolpert hardness tester.
3. Results and Discussion
3.1. Initial Microstructure and Properties of As-received Material
Table 2 gives the chemical composition of as-received annealed and pickled 301LN hot rolled coil (HRC) sample (in wt%) supplied with No.1 finish. The austenite stability index in terms of Md30/50 temperature as proposed by Angel works out to be 35 oC, which is sufficiently above room temperature, and the Ms temperature calculated according to Eichelmann and Hull equation is -115 oC, which is well below the room temperature. The steel fulfills the basic pre-condition for austenitic metastability and grain refinement through “Strain-induced MartensiticTransformation and Reversion to Austenite” (SIMTR) technique, as proposed by Tomimura et al[11].Fig.6 shows the microstructures of as-received hot rolled, solution-annealed and pickled stainless steel as observed under optical microscope and SEM. The grain size of the annealed microstructure was considerably coarse and varied over a wide range of 10-40 μm. Table 3 gives the corresponding tensile properties, hardness and α′-martensite content of the as-received material. The steel did not exhibit any marked variation of tensile properties in longitudinal and transverse directions. The yield strength of annealed stainless steel is quite low at 331-352 MPa, from the standpoint of engineering requirement of 751-921 MPa for a Metro Coach. The tensile strength is in the range of 812-831 MPa, also well below the requirement for HT temper viz. 1001-1151 MPa. However, the overall elongation to fracture and the strain hardening characteristics of the steel are quite superior, well corroborated by elongation and strain hardening exponent (n) values of 62-64% and 0.62-0.64, respectively.The steel was found to exhibit an increase in strain hardening exponent during the course of tensile straining signifying the transformation-induced plasticity (TRIP) effect associated with strain-induced martensite (α′) formation. This property renders the steel capable of absorbing higher amounts of plastic energy before the onset of necking, a property of vital importance for crash worthiness of Metro Coach structural members. Incidentally, the annealed steel exhibited hardness of 96 HRB and low α′-martensite content of 1.6%.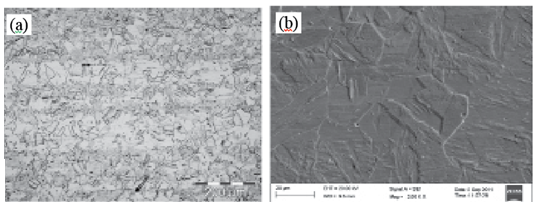 | Figure 6. Microstructures of as-received hot rolled, solution-annealed and pickled 301LN stainless steel: (a) Optical image (b) Secondary electron image |
Table 3. Tensile properties and hardness of as-received solution-annealed and pickled 301LN HRC samples 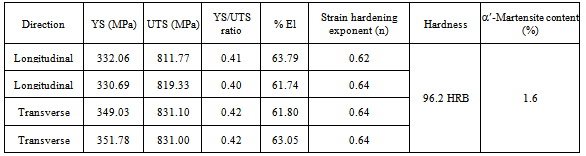 |
| |
|
3.2. Findings From Experimental Cold Rolling
Fig.7 graphically depicts the variation in rolling load with passes for an overall cold reduction (CR) of 45%. It is evident that there is an abrupt increase in rolling load after about 22% cold reduction, which presumably signifies the onset of formation of strain-induced martensite (SIM) in the steel. The formation of SIM saturates at around 39% cold reduction and at a saturating strain (εs) of about 0.39 with present chemistry and grain size of steel and for present set of rolling conditions (temperature, strain and strain rate).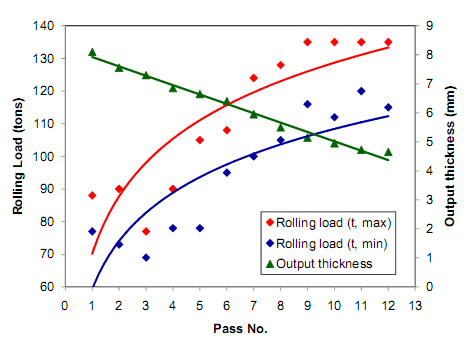 | Figure 7. Variation in rolling load with passes (Overall cold reduction: 45%) |
Since the cold deformation was continued beyond the saturating strain (εs) by about 5 and 10% for 45 and 50% reductions respectively, it is safe to presume that the martensite was effectively conditioned and heavily dislocated through crushing and fragmentation during cold rolling. The formation of heavily-dislocated martensite is one of the essential precursors for accomplishing effective and successful reversions of SIM to ultrafine grained austenite for enhancement in mechanical properties in 301LN austenitic stainless steel[3,12,15].Metastable austenitic stainless steels such as 301LN contain thermodynamically metastable austenite at room temperature, which can be transformed to α′-martensite (strain-induced martensite, SIM) by deformation below the Md30 temperature. The volume fraction of SIM increases with increasing strain. The martensite formation becomes saturated at a specific strain called “saturating strain” (εs). The martensite crushes subsequently during deformation, increasing the concentration of lattice defects (dislocations, dislocation cells and stacking fault bundles) inside the SIM[3,12,15].
3.3. Microstructure and Properties After Cold Rolling
Fig. 8 depicts the microstructural evolution in 301LN austenitic stainless steel with 45 and 50% cold rolling of the solution-annealed hot rolled steel. The light optical micrographs and the secondary electron images of the cold reduced steels revealed pronounced fibering/ texturing in the microstructure, resulting from heavy cold rolling of the annealed stainless steel. | Figure 8. Microstructures of cold rolled 301LN stainless steel: (a) Optical image after 45% cold reduction (b) Secondary electron image after 45% cold reduction (c) Optical image after 50% cold reduction (d) Secondary electron image after 50% cold reduction |
Table 4 gives the tensile properties of 301LN coil samples after 45 and 50% cold reductions performed in Hillé experimental cold rolling mill. The steel exhibited an yield strength (YS) of 1260-1324 MPa and an ultimate tensile strength (UTS) of 1476-1488 MPa after 45% cold reduction. In comparison, the 50% cold reduced steel revealed YS of 1180-1201 MPa and UTS of 1548-1557 MPa.It appears from the results that with a 5% increase in cold reduction, the yield strength is marginally lowered while the tensile strength is somewhat improved. Understandably, both steels revealed very inferior elongations of 3.7 to 6.3%, very low strain hardening exponents ranging between 0.22-0.43 and high hardness values of ~46 HRC due to excessive strain hardening and strain-induced martensitic transformation in the steel as a result of very heavy cold reductions. The overall elongations of the cold rolled steels are well below the stipulated requirement of 22% minimum in HT temper for Metro Coach application. Likewise, the hardness values are also well beyond the acceptable limit of 36 HRC maximum as stipulated by specification for HT temper. The cold rolled steels exhibited near complete transformation of austenite to α′-martensite content of 98 and ~100%, respectively, after 45 and 50% cold reductions. One of the other precursors for grain refinement by Strain-Induced Martensitic Transformation and its Reversion to austenite (SIMTR) is the near complete SIM transformation of the austenite during cold rolling[11,16].The volume fraction of martensite and εs markedly influence the achievement of nano/ ultrafine structure in Strain-Induced Martensitic Transformation and its Reversion to austenite (SIMTR). These two parameters also depend on other process variables including deformation conditions (strain, strain rate, strain path, rolling temperature), austenite stability (composition and initial grain size) and primary dislocation density[17-21].It is imperative that the metastable austenite be almost completely transformed to α’-martensite during cold deformation for effective reversion of martensite to austenite with marked grain refinement. Therefore, processing parameters in cold rolling must be carefully chosen and controlled in order to obtain more than 90% α’-martensite from cold deformation[22].As mentioned, the formation and the amount of strain-induced martensite depends on the austenite stability (chemical composition and initial austenite grain size) and the cold deformation conditions (the deformation temperature, strain and strain rate). The strain-induced martensitic transformation is suppressed with increasing deformation temperature. This has been attributed to an increase in the stacking fault energy (SFE) and decrease in the available chemical driving force for the transformation. It has also been mentioned that the SIM transformation is suppressed with increasing strain rate. This latter effect was primarily attributed to a decrease in the chemical driving force of the transformation due to adiabatic heating[1]. The martensite content is increased when the amount of deformation is high or the deformation temperature is low. Moreover, by increasing the ASTM austenite grain size number, the amount of strain-induced martensite is reduced[22]. Thus, a coarse grain size would be preferable from view point of strain-induced martensitic transformation and its reversion (SIMTR).The following observations can be made from the table:1. The 301LN ASS exhibits YS of 617-777 MPa, UTS of 1000-1197 MPa, overall elongation of 39-47%, YS/UTS ratio of 0.61-0.71 and hardness of 28-35 HRC for starting cold reduction of 45%, annealing temperature of 800 oC and simulated line speeds of 6-12 mpm assuming the furnace length of 16 m in Gleeble simulation.2. The steel shows YS of 637-809 MPa, UTS of 1068-1125 MPa, overall elongation of 35-39%, YS/UTS ratio of 0.59-0.72 and hardness of 31-37 HRC for cold reduction of 45%, annealing temperature of 750 oC and simulated line speeds of 6-12 mpm..3. The steel reveals YS of 645-798 MPa, UTS of 1013-1057 MPa, overall elongation of 38-43%, YS/UTS ratio of 0.62-0.76 and hardness of 29-37 HRC for cold reduction of 50%, annealing temperature of 800 oC and simulated line speeds of 6-12 mpm.4. The steel displays YS of 682-842 MPa, UTS of 1042-1101 MPa, overall elongation of 32-36%, YS/UTS ratio of 0.63-0.77 and hardness of 30-38 HRC for cold reduction of 50%, annealing temperature of 750 oC and simulated line speeds of 6-12 mpm.Fig. 9 shows light optical micrographs of some of the Gleeble tested 301LN specimens including the micrograph of the as-received, solution-annealed and pickled 301LN stainless steel for comparison. The micrographs of the Gleeble tested 301LN specimens reveal composite microstructures comprising very fine, partially recrystallized austenite grains generated through partial reversion of strain-induced martensite (α′) formed during cold rolling. The occurrence of fibering in the microstructures is presumably the remnant textural feature of prior cold rolling and is indicative of partial reversion of strain-induced martensite (α′) that is attributable to the short annealing treatment conferred to the steel at relatively lower annealing temperature. The presence of untransformed strain-induced martensite (α′) was subsequently corroborated through ferritescope measurements. Table 5 also gives the measured α′-martensite content in the reversion-annealed steels, which was found to vary in the range of 2-9%.Table 4. Tensile properties of 301LN coil samples after cold rolling in Hillé experimental cold rolling mill  |
| |
|
3.4. Microstructure and Properties after Short Reversion Annealing Treatments
Table 5 summarizes the properties achieved in 301LN austenitic stainless steel samples through experimental cold rolling and short reversion annealing simulations in Gleeble 3500 C thermo-mechanical simulator.Table 5. Properties achieved in 301LN ASS strips through experimental cold rolling and short annealing simulations in Gleeble 3500 C thermo-mechanical simulator (based on single furnace length of 16 m in AP Line-1) 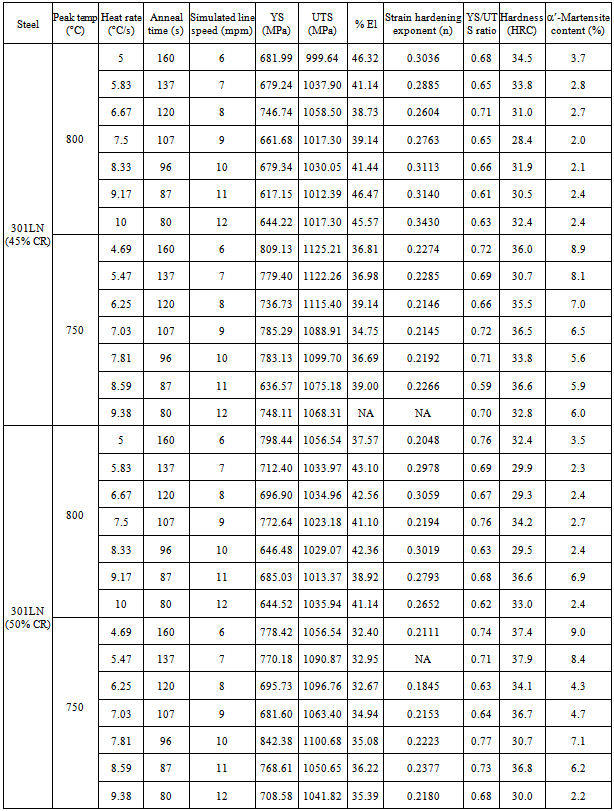 |
| |
|
Fig.10 depicts the secondary electron images (SEIs) of some of the Gleeble tested 301LN specimens. The electron micrographs clearly reveal the nucleation of sub-micron sized austenite (γ) grains formed through controlled reversion of strain-induced martensite (α′) by means of thermo-mechanical processing (TMP) comprising 45 and 50% cold reductions followed by short reversion annealing treatment at 750 and 800oC at simulated line speeds of 6-12 mpm (annealing time: 160-80 s) assuming single furnace operation (Furnace length: 16 m) in AP Line-1 of SSP. The SEI of as-received, solution-annealed and pickled 301LN stainless steel is also included for comparison.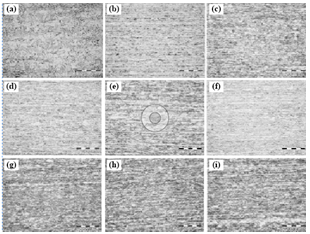 | Figure 9. Light optical micrographs of Gleeble tested 301LN ASS specimens showing refinement in reverted austenite grain size with thermo mechanical treatment: (a) Solution annealed (b) 45% CR/ 800 oC/ 6 mpm (c) 45% CR/ 750 oC/ 6 mpm (d) 45% CR/ 800 oC/ 9 mpm (e) 45% CR/ 750 oC/ 9 mpm (f) 50% CR/ 800 oC/ 7 mpm (g) 50% CR/ 750 oC/ 7 mpm (h) 50% CR/ 800 oC/ 11 mpm (i) 50% CR/ 750 oC/ 11 mpm |
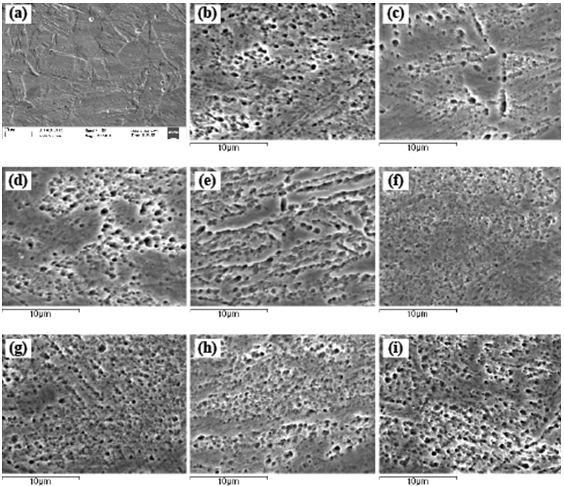 | Figure 10. Secondary electron images of Gleeble tested 301LN ASS specimens showing sub-micron sized austenite (γ) grains obtained through controlled reversion of strain-induced martensite (α′) by means of thermo-mechanical processing (TMP): (a) Solution annealed (b) 45% CR/ 800 oC/ 6 mpm (c) 45% CR/ 750 oC/ 6 mpm (d) 45% CR/ 800 oC/ 9 mpm (e) 45% CR/ 750 oC/ 9 mpm (f) 50% CR/ 800 oC/ 7 mpm (g) 50% CR/ 750 oC/ 7 mpm (h) 50% CR/ 800 oC/ 11 mpm (i) 50% CR/ 750 oC/ 11 mpm |
Fig.11 graphically depicts the variation in hardness of 301LN samples after experimental cold rolling and reversion annealing treatments in Gleeble 3500C. Most of the measured hardness values lie well within the stipulated limit of 36 HRC for Metro Coach specification in HT temper, underlining the reproducibility of the thermomechanical processing (TMP) methodology. Fig.12 graphically presents the strain-induced martensite (α′) contents in as-received No.1 finish, laboratory cold rolled and reversion annealed 301LN samples determined through Ferritescope measurements. The graph illustrates the near complete transformation of austenite (γ) to strain-induced α′-martensite with 45% cold reduction and the rapid kinetics of near complete reversion back to austenite (γ) at 750 and 800 oC at simulated line speeds of 6 and 9 mpm (Annealing time: 160 and 107 s) assuming single furnace operation (Furnace length: 16 m) in AP Line-1 (Annealed value refers to the α′-martensite content in as-received, solution-annealed and pickled 301LN HRC sample with No.1 finish).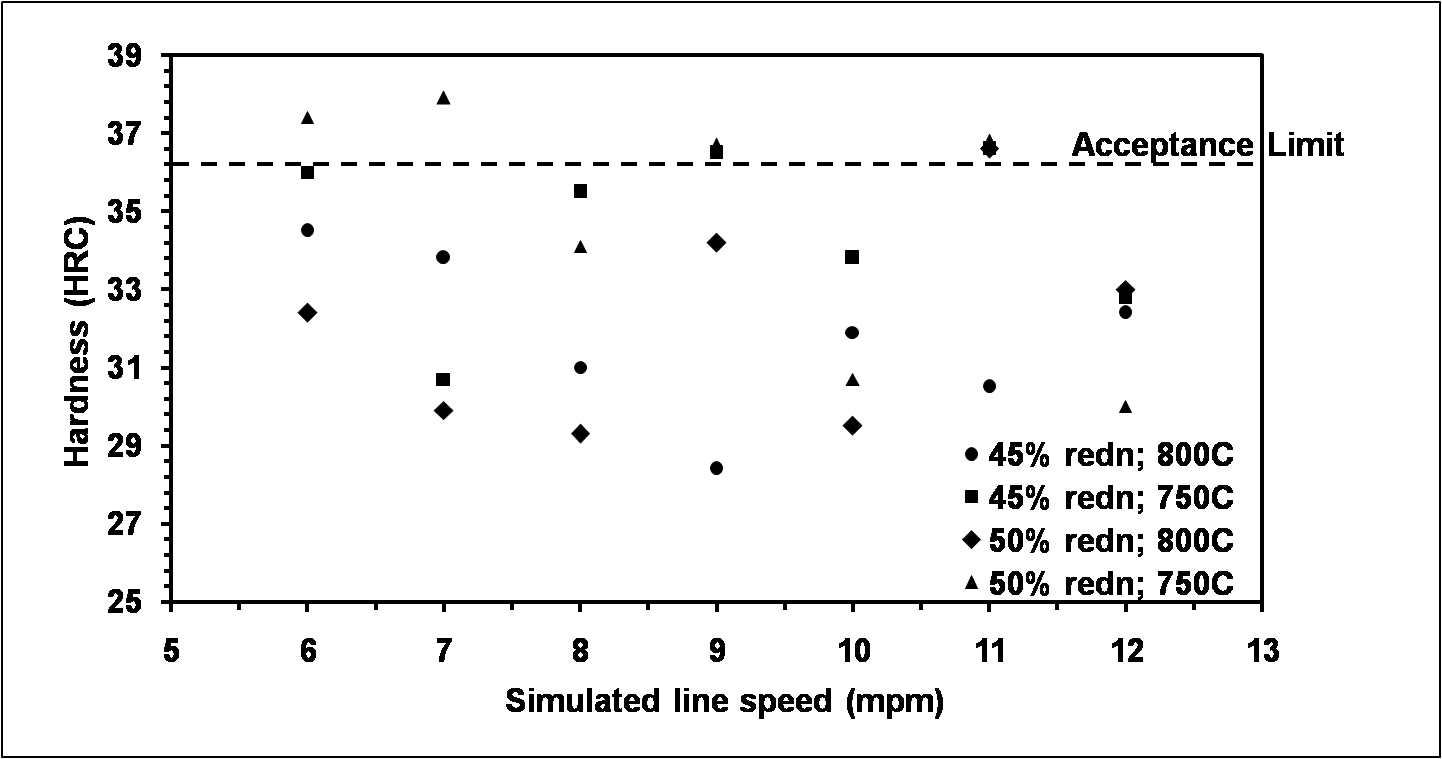 | Figure 11. Variation in hardness of 301LN ASS samples after experimental cold rolling and reversion annealing treatments in Gleeble 3500C |
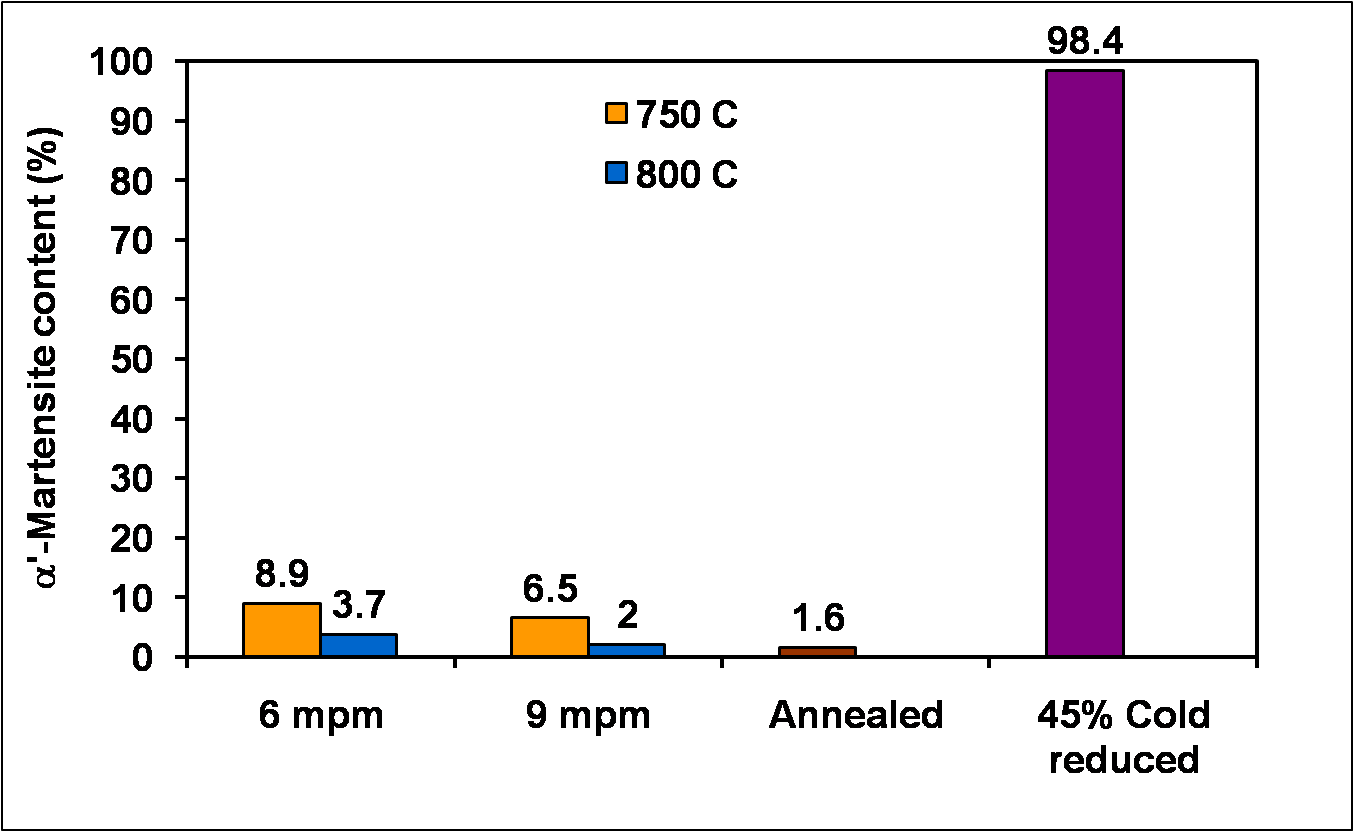 | Figure 12. Strain-induced martensite (α′) content in as-received No.1 finish, laboratory cold rolled and reversion annealed 301LN ASS samples determined using Ferritescope |
The results from the annealing simulations clearly show that the seemingly unlikely combination of properties stipulated by Metro Coach specification in HT temper viz. Yield Strength: 751-921 MPa, Ultimate Tensile Strength: 1001-1151 MPa, Elongation: 22% min, Hardness: 36 HRC max and Yield (YS/UTS) Ratio: <0.8 can be achieved in 301LN grade austenitic stainless steel by imparting heavy cold reductions to the tune of 45-50% in Sendzimir Mill followed by brief/ short annealing treatments at 750 oC using single furnace (F/c #3) operation (16 m furnace length) at normal line speeds followed as per standard operating practice (SOP) for 300 series in Annealing Pickling Line-1 at SSP.The thermomechanical process (TMP) methodology involving heavy cold rolling and short annealing treatment serves to revert the deformation/ strain-induced martensite (α′), formed during heavy cold rolling/ deformation, to strain-free, sub-micron sized austenite grains, which contribute to improvement in mechanical properties through grain refinement/ grain boundary strengthening mechanism. The strength, ductility and toughness of such ultra fine-grained austenitic microstructure is undoubtedly superior to that achieved through deformation-induced martensitic strengthening of metastable austenite accomplished through mere cold rolling.
4. Conclusions
Combination of properties viz. YS: 751-921 MPa, UTS: 1001-1151 MPa, Elongation: 22% min, Hardness: 36 HRC max and Yield ratio: <0.8 can be attained in 301LN grade coils by imparting heavy cold reductions to the tune of 45-50% in Sendzimir Mill followed by brief / short annealing treatments (80-160 s) by means of single furnace operation at 750 oC at standard line operating speeds stipulated for 300 series in Annealing Pickling Line-1 (AP Line-1) at SSP.Short annealing treatment would serve to revert strain-induced martensite (α′), formed during heavy cold rolling, to strain-free, sub-micron sized austenite grains, which contribute to improvement in mechanical properties (strength-ductility combination) through grain refinement/ grain boundary strengthening mechanism.Strength, ductility and toughness of ultra fine-grained austenitic microstructure are superior to that achieved through deformation-induced martensitic strengthening of metastable austenite.The acceptable combination of properties in HT temper, especially those stipulated by Metro Coach specification, necessitate the achievement of composite microstructure comprising ultrafine grained austenite and some amount of untransformed strain-induced martensite (SIM less than about 10 vol%) through partial reversion.The process is distinct from conventional long annealing treatments (300-360 s), which are conventionally employed to soften the steel after cold rolling by means of recovery and recrystallization processes. Thus, conventional annealing softens the ASS whereas reversion annealing serves to strengthen steel through grain refinement.
ACKNOWLEDGEMENTS
The authors wish to acknowledge the whole-hearted support and encouragement of managements of R&D Centre for Iron and Steel and Salem Steel Plant of Steel Authority of India Limited for pursuing and publishing this work.
References
[1] | L.P. Karjalainen, T. Taulavuori, M. Sellman and A. Kyröläinen: Steel Res. Int., 79 (2008), No. 6, pp. 404-412. |
[2] | M.C. Somani, P. Juntunen, L.P. Karjalainen, R.D.K. Misra and A. Kyröläinen: Metall. Mater. Trans. A, Vol. 40a, March 2009, pp. 729-744. |
[3] | M. Eskandari, A. Najafizadeh, A. Kermanpur and M. Karimi: Mater. Des. 30 (2009), pp. 3869-3872. |
[4] | A. Rezaee, A. Najafizadeh, A. Kermanpur and M. Moallemi: Mater. Des., 32 (2011), pp. 4437-4442. |
[5] | T. Maki: Curr. Opin. Solid State Mater. Sci., 2 (1997), pp. 290-295. |
[6] | A.D. Manshadi, M.R. Barnett and P.D. Hodgson: Mater. Sci. Eng. A, 485 (2008), pp. 664-762. |
[7] | S. Rajasekhara, L. P. Karjalainen, A. Kyröläinen and P. J. Ferreira: Advanced Steels, Eds. Y. Weng, H. Dong and Y. Gan, Metallurgical Industry Press, Springer, p.372. |
[8] | M. Moallemi, A. Najafizadeh, A. Kermanpur and A. Rezaee: Mater. Sci. Eng. A, 530 (2011), pp. 378-381. |
[9] | A.A. Lebedev and V.V. Kosarchuk: Int. J. of Plast., Vol. 16 (2000), No. 12, pp. 749-767. |
[10] | K. Tomimura, S. Takaki, and Y. Tokunaga: ISIJ Int., Vol. 31 (1991), No. 12, pp. 1431-1437. |
[11] | K. Tomimura, S. Takaki, S. Tanimoto, and Y. Tokunaga: ISIJ Int., Vol. 31 (1991), No. 7, pp. 721-727. |
[12] | R.D.K. Misra, S. Nayak, S.A. Mali, J.S. Shah, M.C. Somani and L.P. Karjalainen: Metall. Mater. Trans. A, Vol. 41a, Jan 2010, pp. 3-12. |
[13] | R.D.K. Misra, S. Nayak, S.A. Mali, J.S. Shah, M.C. Somani and L.P. Karjalainen: Metall. Mater. Trans. A, Vol. 40a, Oct 2009, pp. 2498-2509. |
[14] | J. Talonen, P. Nenonen, G. Pape, and H. Hänninen: Metall. Mater. Trans. A, Vol. 36a, Feb 2005, p.423. |
[15] | A. Rezaee, A. Kermanpur, A. Najafizadeh and M. Moallemi: Mater. Sci. Eng. A, 528 (2011), pp. 5025-5029. |
[16] | B. Ravi Kumar, Sailaja Sharma, B. Mahato: Mater. Sci. Eng. A, 528 (2011), pp. 2209-2216. |
[17] | J. Talonen and H. Hanninen: Acta. Mater., 55 (2007), pp. 6108-6118. |
[18] | K. Nohara, Y. Ono and N. Ohashi: ISIJ Int, 63 (1977), pp. 212-222. |
[19] | V. Shrinivas, S.K. Varma and L. Murr: Metall. Trans. A, 26 (1995), pp. 661-671. |
[20] | T. Angel: Iron Steel Inst, 177 (1954), pp. 165-174. |
[21] | M. Shimojo, T. Inamura, T.H. Myeong and K. Takashima: Metall. Trans. A, 32 (2001), pp. 261-265. |
[22] | H. Mirzadeh and A. Najafizadeh: Mater. Charac., 59 (2008), pp.1650-1654. |