Santosh Kumar1, S. K. Shukla1, S. K. De1, Atul Saxena1, B. K. Jha1, B. Mishra2, Alok Verma2, S. Mallik2
1R&D Centre for Iron & Steel, Steel Authority of India Limited, Ranchi,
2Bokaro Steel Limited, Steel Authority of India Limited, Bokaro Steel City
Correspondence to: Santosh Kumar, R&D Centre for Iron & Steel, Steel Authority of India Limited, Ranchi,.
Email: |  |
Copyright © 2012 Scientific & Academic Publishing. All Rights Reserved.
Abstract
For supply of API 5L Grade X70 (PSL 2) 1610 mm wide hot rolled (HR) coils of 10.4, 11.2 and 12.8 mm thickness, trial rolling was undertaken at Bokaro Steel Limited (BSL). Two heats were made and cast into 200 x 1630 mm section slabs with designed alloy chemistry. Rolling parameters of exit roughing (R5) temperature, finish rolling temperature (FRT), and coiling temperature (CT) were kept in the range of 1080 – 1100 °C, 860 – 890 °C, and 600 – 630 °C respectively. Coiling of high strength 10.4, 11.2 and 12.8 mm thick coils of 1610 mm width at such low temperature was carried out for the first time in SAIL. Microstructure of hot rolled coils comprised ferrite and pearlite. Average grain size for ferrite varied between 6.3 – 9.2 micron. Microstructure of Centreline segregated zone of cast slab showed presence of primary carbides of microalloying elements. Optical micrograph clearly shows formation of coarse primary carbides at inter dendritic region. SEM and EDAX examinations confirmed presence of Nb and V in these coarse carbides. Genesis of these coarse primary carbides rich in Nb & V is attributed to segregation and subsequent slow cooling. To ensure complete dissolution of coarse primary carbides of Nb and V, a suitable time-temperature combine was adopted during reheating. Elimination of primary carbides in the rolled stock was testified through microstructural evaluation. High yield strength (~ 540 MPa) could be achieved accordingly. Excellent YS / UTS ratio (< 0.85) has been achieved. Charpy impact properties of HR coils has been > 100 J even at – 40°C . Lowering of FRT and CT led to a concurrent increase in strength and toughness. At ambient temperature, 100% shear area was observed after drop weight tear test (DWTT) whereas at 0 °C, shear area was above 95%.After pipe forming, tensile properties of the parent material and that of fusion-line were found satisfactory. Toughness of parent material were found to be adequate (> 200 J at 0 °C and > 170 J at – 30 °C). There had, however, been a few cases of inferior impact resistance of weld-seam. Metallurgical investigation established the genesis of inferior impact toughness of fusion line to be linked with incidence of penetrators. Originating crack on the detrimental flow lines propagate easily in presence of non-fusion / penetrators resulting from improper selection of welding parameters viz. heat input, pressure and speed of welding etc. During process of ERW pipe making, these inclusions must be ejected. Modified alloy design of API X 70 ensures liquid state of silicates at the end of ERW process which ejects out easily to provide penetrators free seam leading to adequate toughness of the weld seam. With modified alloy design, more than 4000 T of API X 70 grade HR coils have been supplied for successful production of pipe, meeting all the metallurgical requirements. The process technology for production of API X 70 grade HR coil has been established. API X 70 is now being regularly made against the commercial order at BSL.
Keywords:
Linepipe Steel, Microallying, Impact Toughness, Microstructure, Precipitates, Electrical Resistance Welding (ERW), Penetrators
Cite this paper: Santosh Kumar, S. K. Shukla, S. K. De, Atul Saxena, B. K. Jha, B. Mishra, Alok Verma, S. Mallik, API X 70 Grade HR Coils for ERW Pipes, International Journal of Metallurgical Engineering, Vol. 2 No. 2, 2013, pp. 179-187. doi: 10.5923/j.ijmee.20130202.09.
1. Introduction
High volume transportation of crude, oil and gases necessitate use of larger diameter linepipes and higher-pressure booster pumps. In addition to meeting the operational engineering requirements like weldability, recent generation high strength linepipe steels having guaranteed impact toughness, provide a superior option for pipe-laying projects owing to substantial material and cost savings when compared with linepipe steels of yester years1. In line with recent developments, Bokaro Steel Limited (BSL) initiated development program on high strength line pipe steels which included development of API X 70 grade HR coils for linepipes.Alloy DesignAlloy chemistry was designed not only to achieve the aimed properties of API X – 70 HR coils as shown in Table 1 which ensured meeting the end properties required in a API X – 70 grade linepipe, but also it ensured that the operating window of steel processing for API X – 70 grade is suitable for BSL conditions of steel making, casting and the hot rolling processes. Table 2 summarises the approach of alloy design. In view of strong tendency of Mn to segregate, Mn content was kept range bound between 1.3 – 1.5%, while content of C, S, P and N was adjusted in the alloy in accordance with the steel making practices of BSL. Addition of small amount of Ti (0.01 – 0.02%) was proposed in view of earlier experience of lamination originating from the pre-existing subsurface defects / cracks in slab. Addition of Ti was intended to tie up N in steel and reduces AlN / Nb(CN) precipitation along austenite grain boundary. TiN precipitates as large sized precipitates within the grains and thereby reducing chances of cracking caused by nitride formation at grain boundaries of prior austenite leading to reduction in hot ductility of cast structure. Addition of V (0.04-0.05%) was proposed for V provides precipitation hardening without increasing the mill load. Table 1. Aim Properties of API X – 70 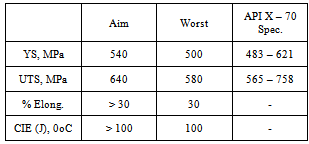 |
| |
|
Table 2. Alloy Design Considerations 2-8 of API X – 70 grade 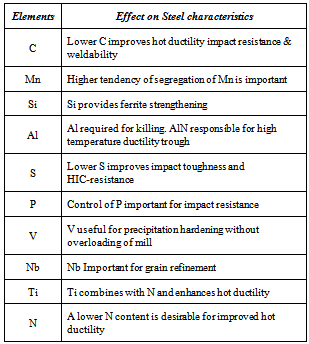 |
| |
|
2. Experimental
2.1. Heat making & Casting
BOF-LF-CC Route was followed for making of API X – 70 grade steel using combined blowing technology. Two heats were made and cast into 200 x 1630 mm section slabs. A typical chemical analysis is shown in Table 3. Typical casting parameters comprised controlled and steady casting speed of 1.2 M/min., super heat < 20 C and soft secondary cooling practice. The cast slab section was 200 x 1630 mm. these slabs were stack cooled for 60 hours. Slab surfaces and cast structure were inspected for assessing slab quality.
2.2. Hot Rolling
Central portion of slab and corresponding earlier processed rolled plates were examined metallographically for primary carbides. SEM-EDAX analysis was used to confirm the primary carbides. In view of the observations, temperature of soaking was selected on the basis of the temperature of dissolution of primary Nb(CN) precipitates. Thickness of slab was reduced from 200 mm to ~38 mm in 5 passes with individual reduction > 24%. Rolling parameters of exit roughing (R5) temperature, finish rolling temperature (FRT), and coiling temperature (CT) were kept in the range of 1080 – 1100 C, 860 – 890 C, and 600 – 630 C respectively. Coiling of high strength 10.4, 11.2 and 12.8 mm thick coils of 1610 mm width at such low temperature was carried out for the first time in SAIL.
2.3. Characterisation of HR coil
Samples were drawn from HR coils. Tensile, impact, ductile brittle transition temperature (DBTT), drop weight tear test (DWTT) and bend properties were evaluated. Optical and SEM examination were carried out on longitudinal section. Standard procedures of polishing were adopted. 2% natal was used as etchant. Samples for TEM were prepared by jet polishing of 3mm disc cut from thin foil made from the hot band in 95 : 5 acetic & perchloric acid at 10 – 15 C temperature. TEM study was carried out in a 120kV transmission electron microscope (HITACHI 7600 Model).Table 3. Chemistry (Ladle Analysis in wt.%)  |
| |
|
2.4. Performance Trial
After edge preparation though milling and online ultrasonic testing over 100% surface of the material, ERW pipe of 18” dia ERW line pipes was formed. Figure 1 depicts the processing steps of pipe making and various testings. Post high frequency induction resistance welding welding, seam was induction heated for normalizing treatment of seam and HAZ. When the seam temperature dropped below ~ 200 °C, samples were drawn for quality assessment as shown in Figure 1.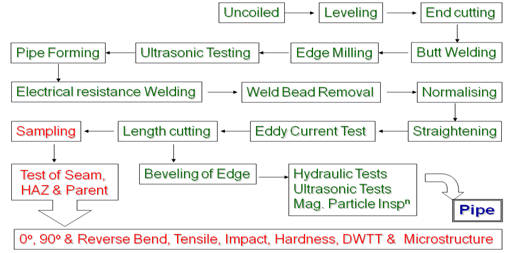 | Figure 1. Schematic Depiction of the processing steps of Pipe Making and various testings of pipe |
2.5. Quality Assessment of Formed Pipe
Besides ultrasonic testing of the HR Coil before pipe rolling and eddy current test, formed pipes were subjected to drop weight tear testing of parent material of the pipe, impact testing of parent and fusion line portion, tensile testing of parent and weldment seam, 0℃, 90℃ and reverse bend tests (flattening tests).
2.6. Investigation of ERW weld seam
Weld seams having inferior impact toughness was examined through both optical and scanning electron microscope. Presence of penetrators and their qualitative chemical analysis was ascertained to arrive at the genesis of the inferior impact toughness of weld-seam.
3. Results and Discussion
3.1. Primary Carbide
In the mid-thickness area of rolled stocks, coarse broken carbides of Nb were observed (Figure 2) in a Nb micro-alloyed steel. As these carbides donot contribute to strengthening process, these are drain on expensive ferro-Nb added to API X70 grade steels. To confirm their genesis to these coarse carbides, microstructure of Centreline segregated zone of cast slab was examined, which showed presence of primary carbides of microalloying elements. Optical micrograph (Figure 3a) clearly shows formation of coarse primary carbides at inter dendritic region. SEM and EDAX examinations confirmed presence of Nb and V in these coarse carbides (Figures 3 b&c). 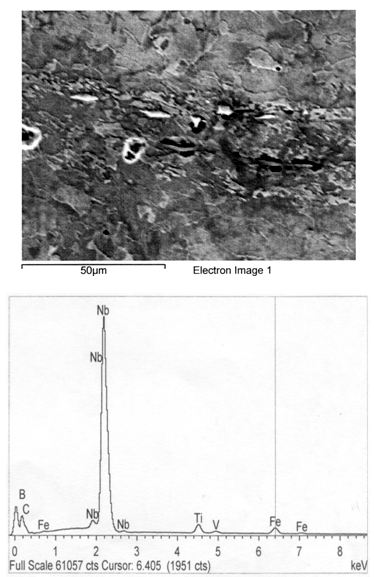 | Figure 2. (a) Scanning Electron Micrograph depicting white coarse Nb rich phase (b) EDAX of the the white coarse phase confirming presence of Nb carbide |
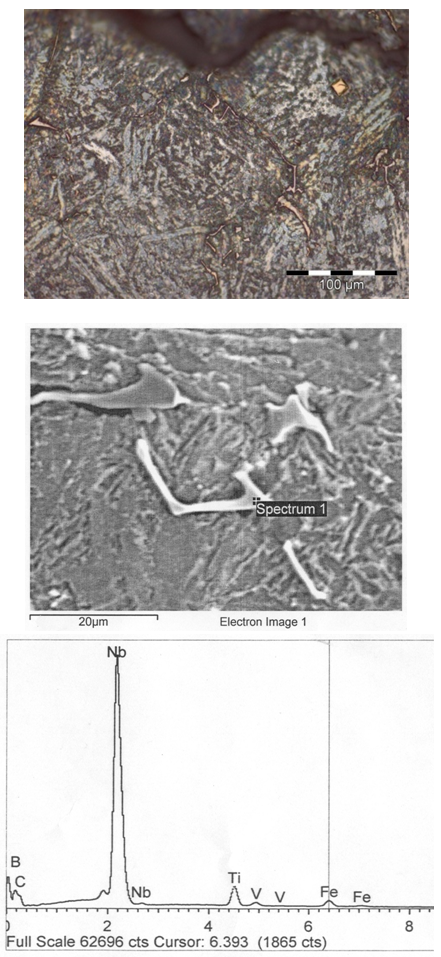 | Figure 3. Primary carbides in central segregated zone of slab (a) Optical Micrograph, (b) Scanning Electron Micrograph and (c) EDAX Analysis on point 1 marked in Scanning Electron Micrograph |
Genesis of these coarse primary carbides rich in Nb & V is attributed to segregation and subsequent slow cooling. To ensure complete dissolution of coarse primary carbides of Nb and V, a suitable time-temperature combine is therefore vital to microalloyed highstrength steels.
3.2. Characterisation of HR Coil & Performance after Pipe Making
Microstructure of hot rolled coils comprised ferrite and pearlite. Average grain size for ferrite varied between 6.3 – 9.2 micron. A typical microstructures and ferrite grain size distribution are depicted in Figure 4. Elimination of primary carbides in the rolled stock using proper soaking conditions was testified through microstructural observation across thickness. TEM observation (Figure 5) shows presence of nano-sized Nb-rich precepitates. Epitaxial growth of Nb rich area on the TiN coarse precipitate are also observed in Figure 5.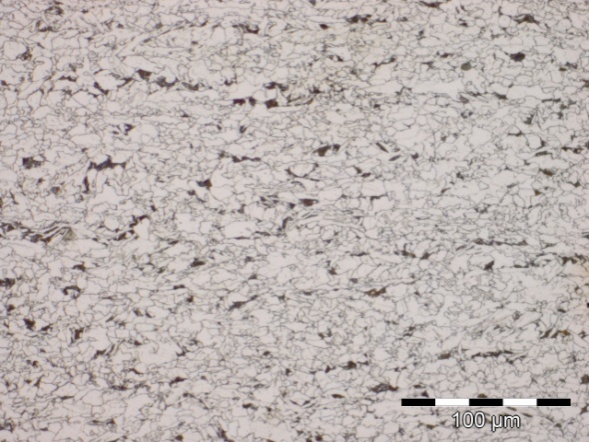 | Figure 4. Typical Microstructure of hot rolled HR coils |
Table 4. Typical Mechanical Properties of Parent Material  |
| |
|
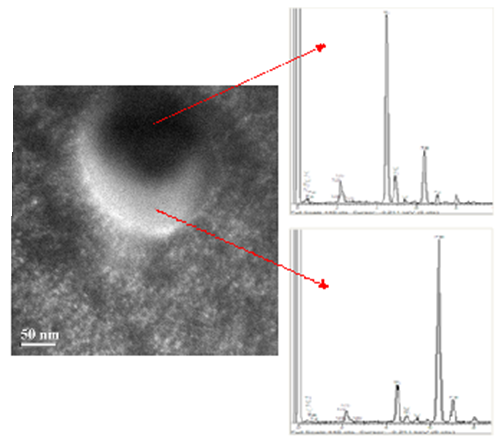 | Figure 5. Evidence of presence of nano-sized Nb-rich precipitates |
Table 3 summarises mechanical properties of some of the HR coils. Yield strength varied between 519 – 542 MPa whereas tensile strength is observed to vary between 621 – 635 MPa with excellent YS / UTS ratio (< 0.85). Percent elongation of more than 36% is indicative of excellent ductility needed for pipe forming. Accordingly bend results have been satisfactory at 2T (Figure 6).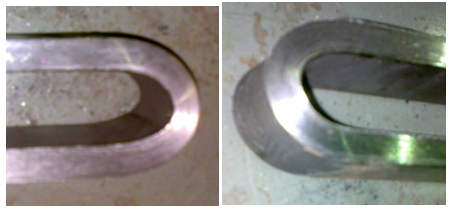 | Figure 6. 2T Bend Tested Specimen |
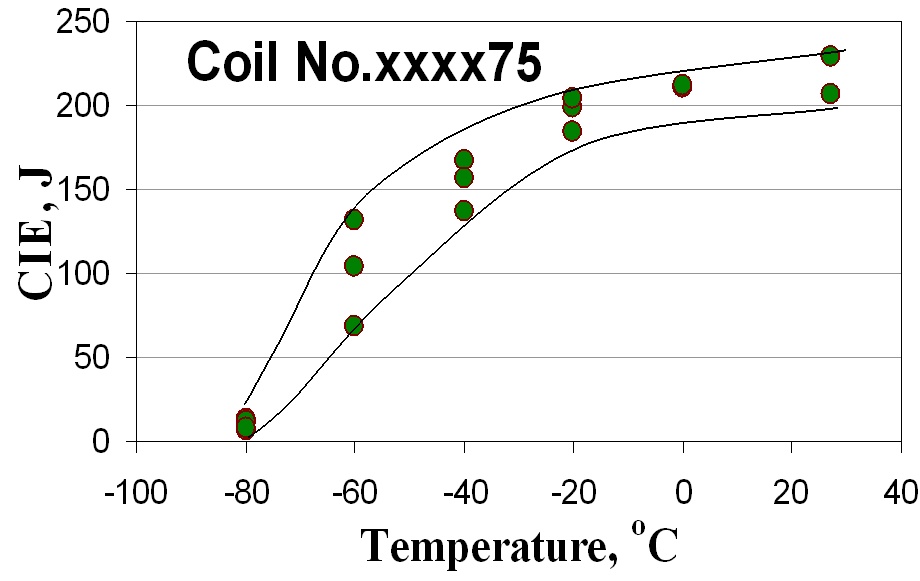 | Figure 7. A typical Plot of Ductile Brittle Transition Temperature |
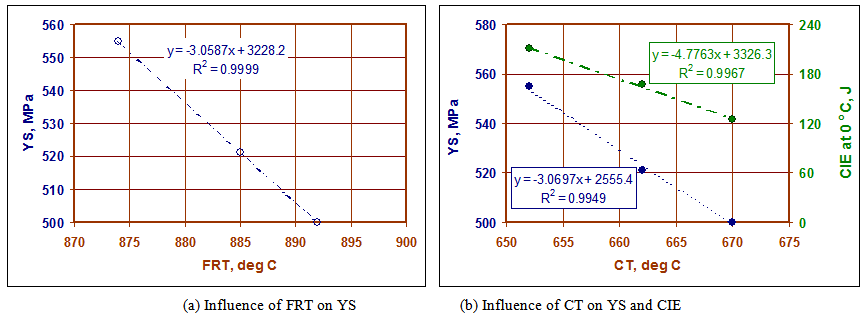 | Figure 8. Plots depict influence of FRT and CT on YS and CIE values |
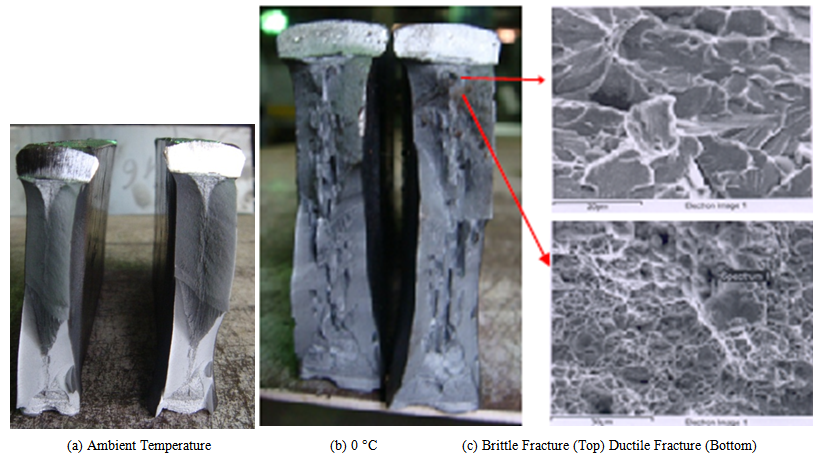 | Figure 9. Fractured surfaces of Drop Weight Tear tested Specimen |
Charpy impact properties of HR coils are varied between 102 – 210 J and even individual observations were > 100 J at – 40℃ indicating that ductile brittle transition temperature is adequately low (~ – 60℃) (Figure 7). Lowering of FRT and CT led to a concurrent increase in strength and toughness (Figure 8a & b). Drop weight tear test (DWTT) is an important test for linepipe steels. As per quality requirements of the final pipe, the test pieces are drawn after pipe forming and the parent material flattened prior to DWT test. DWTT at 0℃ should show more than 85% shear area which is indicative of ductile mode of failure. Even in cases of 12.8 mm thick HR coils, 100% shear area is observed at ambient temperature (Figure 9a) after DWTT whereas at 0 oC, shear area is above 95% (Figure 9b).Table 5 shows tensile properties of formed pipe- parent material and seam whereas Table 6 depicts two cases : first case shows typical impact toughness at fusion and HAZ while another relates to inferior results observed in some pipes. Tensile properties of the parent material and that of fusion-line were found satisfactory. Toughness of parent material were found to be adequate with Charpy impact energy values of > 200 J and > 170 J at 0 °C and – 30 °C respectively. Although, toughness of weld seam and HAZ were found to be largely satisfactory as shown in case 1 of Table 6, there had been some cases of inferior impact resistance of weld-seam which were also found associated with inferior bend properties (Case 2 in Table 6). Weld seams having inferior impact toughness was examined through both optical and scanning electron microscope. Presence of penetrators and their qualitative chemical analysis was ascertained to arrive at the genesis of the same.Optical microscopy revealed presence of about 40 micron wide decarburized band parallel to seam (as evident from absence of any pearlite). Metallurgical investigation established the genesis of inferior impact toughness of the fusion line to be linked with incidence of penetrators (Figures 10 & 11). Eccentric seam normalizing of weld seam which allows non-homogeneity and high propensity of flow lines in structure near seam are detrimental. Originating crack on these flow lines propagate easily in presence of non-fusion / penetrators resulting from improper selection of welding parameters viz. heat input, pressure and speed of welding etc. At the time of ERW process, Mn and Si having higher affinity for oxygen, oxidises in preference to iron in absence of protective atmosphere of weld seam during ERW process. Thus forms Mn silicates at weldment. During process of ERW pipe making, this oxide phase must be ejected from fusion line through proper selection of ERW parameters like heat input, welding speed etc. to ensure a good impact toughness of weldment in ERW pipes. Wherever, the suitable ERW parameters has been there, fusion line has been free from such silicate stringers leading to acceptable impact toughness of weld seam (case 1 of Table 6). Also it is observed that absence of the penetrators, concurrent acceptability in various flattening tests results.Table 5. Tensile Properties of API X – 70 linepipe 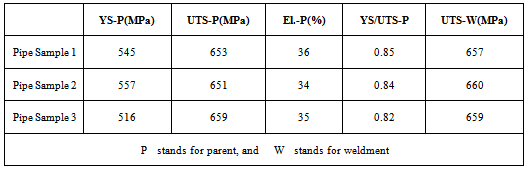 |
| |
|
Table 6. Results of impact and bend test of formed Pipes 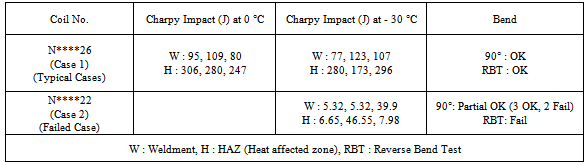 |
| |
|
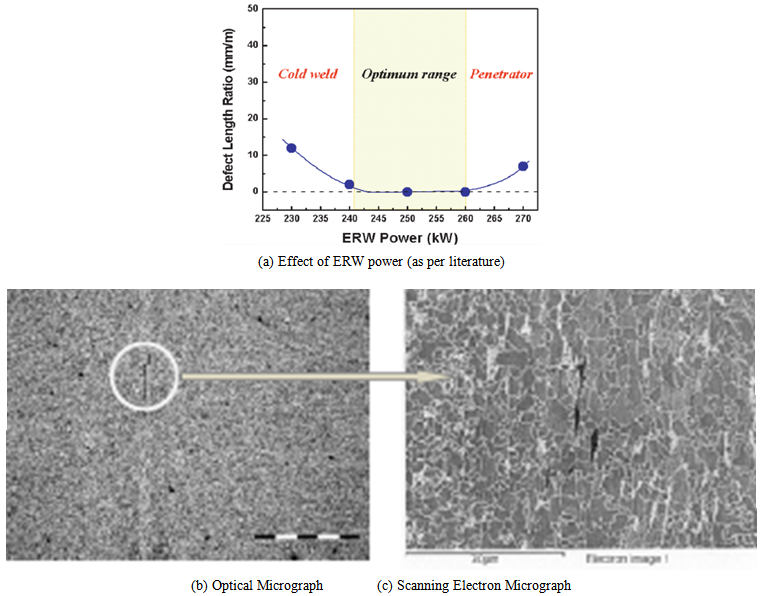 | Figure 10. Penetrator at fusion line of ERW pipe |
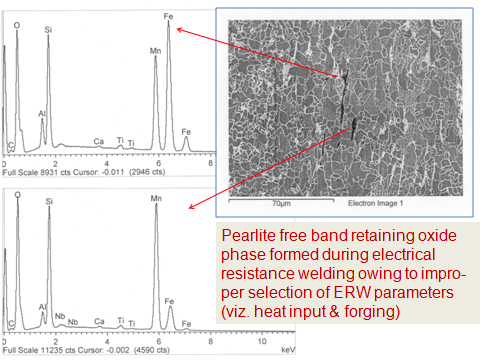 | Figure 11. SEM & EDAX analysis of penetrators found at fusion line of ERW pipe |
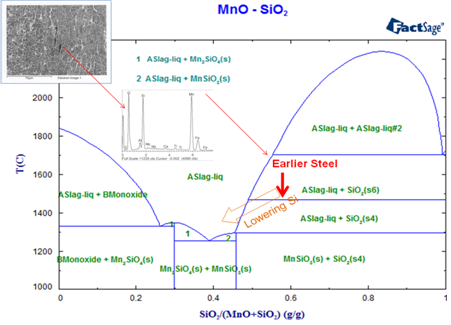 | Figure 12. Pseudo-binary diagram with indicative position of penetrator (oxide phase)-composition before and after innovation (depicted by broad arrow) |
3.3. Fine Tuning of Alloy Design for ERW Pipe
Innovative solution to improve impact toughness of weld seam in ERW pipes through modified alloy design was achieved. Liquefying oxide phase at the time of steel solidification through lowering of Si content has been the innovation that facilitated its escape during ERW pressing operation which ensure a perfect seam with good impact toughness and bend-characteristics. Based on theoretical calculation using thermodynamic software package ‘FactSage’, it has been observed that inclusion composition forming in earlier steel corresponds to vertical down arrow in Figure 12 whereas lowering of Si in steel alters the inclusion chemistry which enables it to be liquid at solidus temperature of steel during ERW process (as shown by broad arrow). Adoption of this modification led to total elimination of failure at weld seam and more than 4000 T of API X 70 grade HR Coils could be rolled into ERW pipes. In view of the occasional incidence of failure in achieving toughness properties because of improper ERW parameters, alloy design of API X 70 grade HR coil was fine tuned to ensure that the oxide phases forming during the welding process are liquid in state at the time of metal squeezing taking place at the end of ERW process. Based on the modified alloy design, more than 4000 T of API X 70 grade HR coils have been commercially supplied and the same have been rolled into ERW pipes successfully. All metallurgical parameters of finally pipe were met and customer feedback had been satisfactory.
4. Conclusions
1. Trends of variation in yield strength and Charpy impact toughness underlined significance of lower FRT (< 880 °C) and CT (< 680 °C).2. Suitably tailored alloy design and selected process parameters ensured excellent microstructural features both at optical (fine ferrite size) and TEM level (nano precipitates) in HR coils of thicker gauge.3. Properties achieved have been well above the lower limits of the specification of API X – 70 for HR coils up to 14.4 mm thickness. HR Coils of BSL meet all quality requirements of API X 70 specification after pipe making. Developing microstructure of hot band underlines suitability of alloy design and proper selection of process parameters.4. Eccentric seam normalizing of weld seam which allows non-homogeneity and high propensity of flow lines in structure near seam are detrimental. Originating crack on these flow lines propagate easily in presence of non-fusion / penetrators resulting from improper selection of welding parameters viz. heat input, pressure and speed of welding etc. Under suitable operating window of ERW process, meeting all properties of seam is possible.5. Processing technology for production of API X-70 grade HR coils at Bokaro Steel Limited has been established. More than 4000 T of API X 70 grade HR coils have been commercially supplied to roll ERW pipes successfully.
ACKNOWLEDGEMENTS
Authors are grateful to the management of SAIL for providing opportunity to work for development of API X 70 grade HR coil. We acknowledge help received from BSL collectives of SMS, HSM and RCL who helped in implementing the requisite suggestions. Help and support received from M/s Maharastra Seamless Pvt. Ltd, Nagothane, Mumbai and M/s Jindal India Pvt. Ltd., Kolkata towards pipe making are acknowledged with pleasure. Last but not the least, our sincerest thanks are due to RDCIS laboratory staff for characterization of material.
References
[1] | Hiroo Akasaki, “Progress in Pipe and Tube Technology and Its Future Prospect – Application and Manufacturing, Nippon Steel Technical Report No. 90 July 2004, pp 75 – 88 |
[2] | F.B. Pickering: Microalloying 75, Union Carbide Corp., New York, NY, (1977), 9. |
[3] | L. Meyer, “Grundlagen der Werkstoffentwicklung durch Verknüpfung thermischer und mechanischer Vorgänge beim Warmumformen”, Stahl und Eisen, 101 (7) (1981), 483 – 491. |
[4] | A.J. DeArdo, “The Physical Metallurgy of Thermomechanical Processing of Microalloyed Steels, “Thermec ‘97, eds. T. Chandra and T. Sakai, (1) (12) (TMS publications, 1997), 13-30. |
[5] | T. Gladman, “Precipitation hardening in metals”, Materials Science and Technology, 15 (1999), 30 – 36. |
[6] | L. J. Cuddy: Thermomechanical Processing of Microalloyed Austenite, TMS, Warrendale, PA, (1982), 129. |
[7] | K. Fujiwara, S. Okaguchi and H. Ohtani: ISIJ Int., 35 (1995), No. 8, 1006. |
[8] | D. Russwum & P. Wille, Microalloying 95 Conf. Proc., Iron and Steel Society, Pittsburgh, USA, June 1995, p 37 |