Mahesh C. Somani1, David A. Porter1, L. Pentti Karjalainen1, Devesh K. Misra2
1University of Oulu, Department of Mechanical Engineering, Centre for Advanced Steels Research, Post Box 4200, 90014 Oulu, Finland
2University of Louisiana at Lafayette, Dept. of Chemical Engineering & Centre for Structural and Functional Materials, P.O. Box 44130, Lafayette, LA 70504-4130, USA
Correspondence to: Mahesh C. Somani, University of Oulu, Department of Mechanical Engineering, Centre for Advanced Steels Research, Post Box 4200, 90014 Oulu, Finland.
Email: |  |
Copyright © 2012 Scientific & Academic Publishing. All Rights Reserved.
Abstract
A novel concept of direct quenching and partitioning (DQ&P) processing route has been explored with the specific aim of producing ultra-high strength structural steels with yield strengths ≈1100 MPa combined with good uniform and total elongations and impact toughness. The approach used was to design suitable compositions based on high silicon and/or aluminium content, establish the DQ&P parameters with the aid of physical simulation on a Gleeble simulator and finally, design the DQ&P processing route for trials on a laboratory rolling mill. Dilatation experiments were made on a Gleeble simulator to determine the appropriate cooling rates and quench stop temperatures for obtaining martensite fractions in the range 60-90%. Two types of dilatation tests were conducted starting with either strained or unstrained austenite prior to quenching to roughly simulate industrial rolling with low and high finish rolling temperatures, respectively. Laboratory rolled samples were direct quenched in water to desired quench stop temperatures followed by partitioning in a furnace held at the quench stop temperature. Some samples were cooled very slowly thus simulating the cooling of the coiled strips in industrial rolling. Metallographic studies showed that the desired martensite-austenite microstructures were achieved. Besides high strengths, the ductility (including uniform elongation) and impact toughness were significantly improved. Straining of austenite prior to DQ&P led to extensive refinement of martensite packets/blocks and laths and hence resulted in improved mechanical properties, particularly impact toughness. No adverse effect of prolonged partitioning simulating coiling has been noticed suggesting new possibilities for developing tough ductile structural steels both for strip and plate products.
Keywords:
Direct Quenching, Quenching and Partitioning, Thermomechanical Processing, Martensite, Retained Austenite, Finish Rolling Temperature
Cite this paper: Mahesh C. Somani, David A. Porter, L. Pentti Karjalainen, Devesh K. Misra, Evaluation of DQ&P Processing Route for the Development of Ultra-high Strength Tough Ductile Steels, International Journal of Metallurgical Engineering, Vol. 2 No. 2, 2013, pp. 154-160. doi: 10.5923/j.ijmee.20130202.07.
1. Introduction
There has been an ever-increasing demand for developing ultra-high strength steels with excellent combinations of mechanical properties such as high strength, ductility, toughness and formability. This, however, requires optimal design of new, inexpensive compositions and/or thermomechanical processing (TMP) routes to meet the new challenges. Conventionally, quenching and tempering is employed to realize high-strength structural steels with good impact toughness. Generally, the ductility of these steels in terms of their elongation or reduction of area to fracture in uniaxial tensile testing is acceptable, but their uniform elongation, i.e., the work hardening capacity is relatively low. Such a deficiency limits the wider application of these steels, because strain localization during fabrication or as a result of overloading can be detrimental to the integrity of the structure. In recent years, a novel concept of quenching and partitioning (Q&P) has been proposed as a potential processing route for improving the balance of elongation to fracture and tensile strength for advanced high-strength steels[1-3]. In essence, the Q&P processing of a cold-rolled sheet involves austenitization at a desired temperature, followed by quenching to a temperature between the martensite start (Ms) and finish (Mf) temperatures and holding at a suitable temperature for an appropriate time to allow the partitioning of carbon from martensite to austenite, which can thereby be partly or fully stabilized down to room temperature. The formation of iron carbides and the decomposition of austenite are intentionally suppressed by the use of Si, Al or P alloying[3-6] unlike in the case of tempering.In a recent study, the potential use of thermomechanical rolling combined with DQ&P to improve the work hardening, uniform elongation and impact toughness of a high-strength hot-rolled structural steel has been presented[7]. The specific aim was to establish a direct quenching and partitioning (DQ&P) route for the production of a steel with a yield strength ≥ 1100 MPa combined with good ductility and impact toughness. A martensitic matrix has the potential to provide the required high strength, while a small fraction of finely divided retained austenite stabilized between the martensitic laths through carbon partitioning was expected to provide the desired uniform elongation and improved work hardening via TRIP effect. Dilatometer measurements and electron microscopy studies were combined with published information in a fresh attempt to understand the possible microstructural mechanisms operating during Q&P and thereby get closer to the thorough understanding needed to design optimized compositions and/or DQ&P processing routes[8]. This paper presents a brief account of the salient results encompassing the dilatation behaviour, hot rolling aspects, various microstructural mechanisms and mechanical properties.
2. Experimental Procedures
Two experimental compositions were designed for the DQ&P experiments, one based on a high Si content and one on a high Al content, in wt.% respectively Fe-0.2C-1.5Si-2.0Mn-0.6Cr andFe-0.2C-0.5Si-1Al-2.0Mn-0.5Cr-0.2Mo, hereinafter referred as High-Si and High-Al steels. The chosen compositions were cast as 70 kg slabs. Pieces of 200 x 80 x 60 mm from these castings were homogenized and hot rolled to a 14 mm thick plate from which cylindrical specimens Ø6x9 mm or Ø5x7.5 mm were cut with the axis of the cylinders transverse to the rolling direction in the rolling plane. These were used for thermomechanical treatment and dilatation measurements on a Gleeble 1500 simulator. Preliminary CCT measurements suggested that cooling at 30°C/s would be appropriate to avoid transformation prior to reaching the Ms temperature. Two austenite states were investigated prior to quenching, recrystallized and strained, in order to roughly simulate industrial rolling with high and low finish rolling temperatures.In the case of High-Si steel, for undeformed austenite, samples were reheated at 20°C/s to 1150°C, held for 2 min prior to cooling at 30°C/s to a quench-stop temperature (TQ) below the Ms temperature giving initial martensite fractions in the range 60-85%. The samples were then partitioned for different times (Pt) in the range 10 - 1000 s at TP (
TQ), followed by cooling in air to room temperature (RT) at ~10-20°C/s down to 100°C. In the case of deformed austenite, samples were cooled at 2°C/s to 850°C, held 10 s, and then compressed with three hits each having a strain of ~0.2 at a strain rate of 1 s-1. The time between hits was 25 s. The specimens were then held 25 s prior to cooling at 30°C/s to a quenching temperature below Ms giving initial martensite fractions of 75-85%, Fig. 1.In case of High-Al steel, the difference was essentially in reheating conditions of the specimens (10°C/s to 1000°C, held for 2 min) prior to subjecting to Q&P schedules for both unstrained and strained specimens. As compared to a more detailed evaluation of Q&P processing in the case of High-Si steel, the study was restricted to roughly determine appropriate rolling conditions for High-Al steel and hence, specimens were partitioned for 10 - 1000 s only at the quench stop temperature, i.e., TP = TQ giving initial martensite fractions of about 70-90%. | Figure 1. Thermomechanical simulation schedule |
Vickers hardness measurements were made on all dilatation specimens using a 5 kg load. This was followed by microstructural characterization using a light optical microscope (LOM). The volume fraction and mean carbon content of the retained austenite in the dilatation specimens was determined using X-ray diffraction (XRD; 18.5°
2θ
42°, MoKa radiation, 40 kV, 40 mA). Selected specimens were subjected to more detailed metallographic examination using transmission electron microscopy (TEM) and scanning electron microscopy combined with electron backscatter diffraction (SEM-EBSD).Based on the results of dilatation experiments, rolling trials were made on both the steels in a two-high, reversing laboratory rolling mill with blocks of 110 x 80 x 60 mm cut from cast ingots. The temperature of the samples during rolling and quenching was monitored by thermocouples placed in holes drilled in the edges of the samples to the mid-width at mid-length. The samples were heated at 1200°C for 2 h in a furnace prior to two-stage rolling. In the first stage, hot rolling was carried out in the recrystallization regime in 4 passes to a thickness of 26 mm with about 0.2 strain/pass with the temperature of the fourth pass at about 1030-1050°C. The second stage comprised waiting for the temperature to drop to ≈900°C and then rolling to a thickness of 11.2 mm with 4 passes of about 0.21 strain/pass and a finish rolling temperature (FRT) at 800-820°C. Immediately after rolling, the samples were quenched in a tank of water close to desired TQ and then subjected to partitioning treatment in a furnace at the same temperature for 10 min (i.e., TP = TQ), Fig. 2. Some rolled samples were cooled very slowly over 29-30 hours by switching off the furnace in order to simulate the cooling of the coiled strips in actual industrial rolling.In order to compare the mechanical properties of the laboratory rolled DQ&P samples with those obtainable on a composition giving similar strength properties, a steel containing0.14C-1.13Mn-0.2Si-0.71Cr-0.15Mo-0.03Ti-0.0017B was also laboratory rolled in the same way as described above and directly quenched to room temperature in water.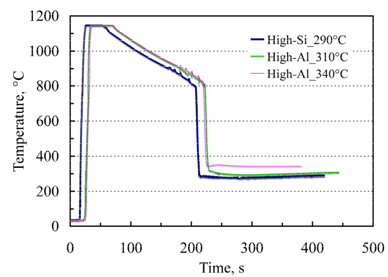 | Figure 2. Examples of recorded rolling and cooling cycles during DQ&P processing |
3. Results and Discussion
3.1. Retained Austenite and Hardness
The dilatation curves of specimens cooled at 30°C/s to RT showed that there was no transformation on cooling prior to reaching the Ms temperature at about 395 and 405°C respectively, for High-Si and High-Al steels, respectively. A simple analysis of the dilatation curves for High-Si steel indicates that quenching at 340, 320 and 290°C should produce initial martensite fractions of 60, 75 and 84%, respectively. Likewise, for High-Al steel, quenching at 340, 310 and 290°C gave initial martensite fractions of 70, 86 and 91%, respectively. Subsequent partitioning of High-Si Q&P specimens at the quenching or higher temperatures up to 450°C resulted in various measured fractions of austenite, but the variations in the retained austenite fractions were greater than the expected accuracy of the XRD measurements (about 2%), see Fig.3 for instance. Likewise, no systematic variations were observed for High-Al steel held for different partitioning times at the quenching temperature. A detailed explanation for the variations could be decomposition of austenite into bainite and/or isothermal martensite or due to carbide precipitation despite the high Si content in the steel[1-6]. Further work carried out to understand the microstructural mechanisms operating during partitioning treatment is published elsewhere[8] and will be briefly presented in subsequent section.Table 1 shows that as expected mean retained austenite contents increase as TQ and TP increase, however prior strain has only little effect. It is, therefore, expected that the amounts of retained austenite will generally be low in rolled DQ&P samples, as partitioning temperatures would normally be ≤ TQ and for long durations, such as in case of coiled strips. The mean carbon content of the retained austenite as estimated from lattice parameter measurements does not show any systematic dependence on holding time for both steels, Table 1. The average carbon content of the Gleeble tested Q&P specimens (0.7-1.2%, irrespective of the steel type and/or austenite state) is much lower than would be expected from simple calculations suggesting that not all carbon is partitioning into austenite. Moreover, the dilatation curves of Q&P specimens showed that there is a gradual expansion during partitioning and required systematic study owing to widely differing opinions in literature, cf. [2,9,10,11].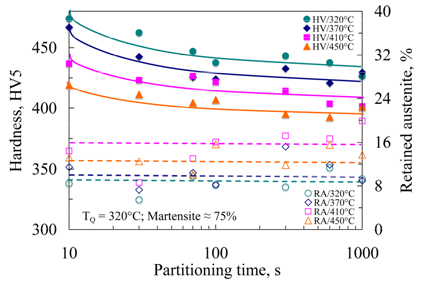 | Figure 3. Hardness (HV5) and retained austenite (RA) vs. partitioning time in unstrained Gleeble specimens quenched to 320°C |
Table 1. Average retained austenite and corresponding carbon contents of Q&P specimens partitioned 10-1000 s 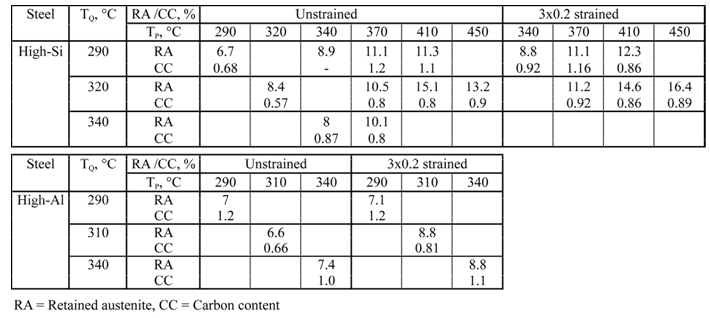 |
| |
|
An example of hardness vs. partitioning time for unstrained austenite in the case of High-Si Q&P specimens is given in Fig. 3. As expected, holding at the partitioning temperatures, particularly at high temperatures leads to softening, i.e., tempering of the martensite, with the rate of softening decreasing with holding time (note the logarithmic scale). As expected, lower quenching temperatures produce higher hardness due to the higher initial martensite fractions. It is interesting to note that prior straining of the austenite had only little effect on final hardness[7].
3.2. Microstructural Mechanisms
An example of gradual expansion during partitioning is depicted in Fig. 4, which shows how the specimen diameter varies with time up to at least 1000 s after reaching TQ = 320°C. After 1 s at TQ, heating to TP occurs at 30°C/s, which explains most of the expansion immediately after 1 s. Apart from this, on a logarithmic scale, the diameter increases slowly (region I) and then more rapidly (region II). In some cases, a third region can be identified (region III), in which the steel contracts.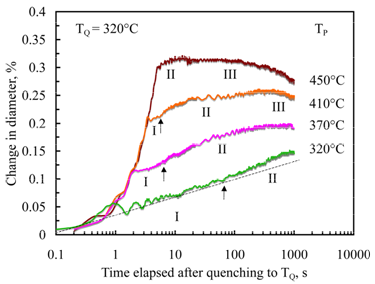 | Figure 4. Change in specimen diameter with time at different partitioning temperatures (TP) following quenching at TQ = 320°C |
Carbon partitioning begins immediately below Ms during cooling to TQ and continues thereafter. It can be shown that the linear dilatation caused by complete partitioning for the present steel will only be 0.027-0.033%[12]. Therefore, other microstructural changes are also affecting the dilatation apart from thermal expansion on heating from TQ to TP and carbon partitioning into austenite.One of these changes is probably the formation and migration of ledges that allow the martensitic laths to grow into the austenite isothermally, thus producing the irregular laths with ledge-like protrusions and constitutes together with carbon partitioning, the expansion observed in region I of Fig. 4[8,9]. With time, some austenite pools transform to lower bainite, i.e., ferrite laths containing carbides aligned in the same direction, marked as region II in Fig. 4. The time required for this to initiate decreases as TP is increased indicating that the chosen values of TP are largely below the lower bainite nose of the TTT diagrams. The austenite pools into which lower bainite grows will tend to be the alloy-rich regions of the original dendritic structure, and they will see developing carbon concentration profiles due to the carbon leaving the untransformed regions. In effect, there will be a range of “C-curves” for bainite that will vary with positions and time. It is also expected that the C curves will be shifted to earlier times than would be predicted on the basis of the local composition, due to the accelerating effect of the martensite on the nucleation of bainite[13].The concentration seen in region III in Fig. 4, especially at the highest partitioning temperatures suggests that martensite is contracting due to tempering. No evidence for carbide precipitation in martensite was found in TEM study indicating that carbon in the martensite laths is perhaps clustering, but this needs further investigation.During the final cooling at about 20°C/s, some bainite formation is possible in the case of high TP, followed by the formation of untempered, in some cases, twinned, high carbon martensite starting at temperatures close to 200°C. The corresponding carbon contents (0.7-0.9%) computed from standard equations given in literature are comparable with the estimated carbon contents of the average retained austenite of the Q&P samples partitioned for 10-1000 s, Table I[8].
3.3. Microstructures of Dilatation Specimens
It has earlier been presented in the case of High-Si steel that 3x0.2 straining in austenite prior to Q&P processing resulted in finer packers and blocks of fine martensite laths[7]. Similar effects of prior straining on the microstructural refinement were noticed in the case of High-Al steel too. A typical example of the optical microstructures of the unstrained specimens following the Q&P process is presented in Fig. 5a, which shows mainly coarse packets and blocks of martensite laths. Specimens that were compressed at 850°C and subjected to a similar Q&P process typically showed finer packets and blocks of fine martensite laths, shortened and randomized in different directions, Fig. 5b. Such a microstructure should enhance the impact and fracture toughness due to the need for more tortuous crack path propagation[14]. Since the martensite / austenite interface is effectively constrained, LOM does not show much change in microstructure following holding at high temperatures and/or long times except for slight truncation of the martensite laths.Select Q&P specimens from High-Si steel without prior straining were examined in a FEG-SEM. Fig. 5c presents an example of a phase contrast image taken on an unstrained specimen quenched to 290°C and partitioned at 410°C for 100 s. Elongated pools of austenite can be seen between the martensitic ferrite laths. TEM investigations also showed the presence of fine interlath austenite. A typical example is shown in Fig. 5d for a specimen quenched at 320°C and partitioned at 410°C for 600 s. The dark field image at the same location further reveals the interlath austenite clearly, Fig. 5e. Further microstructural characterization of strained specimens is yet to be completed.
3.4. Property Evaluation of Rolled DQ&P Samples
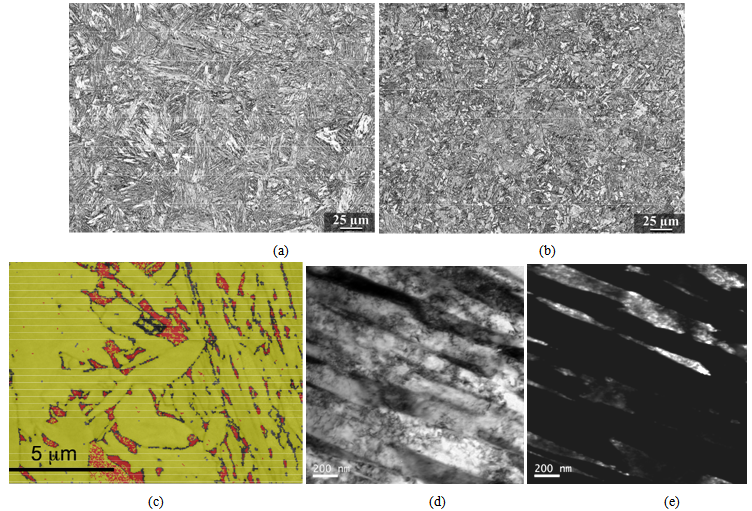 | Figure 5. Typical microstructures of Gleeble simulated DQ&P specimens. Light optical microscopy showing microstructures of unstrained (a) and strained (b) specimens in High-Al steel. Interlath austenite revealed in High-Si steel by FESEM-EBSD (c) and TEM (d and e) |
Microstructural features in respect of martensite packets and block sizes were carried out on select samples from both High-Si and High-Al steels following laboratory rolling and DQ&P processing. The structural features were quite similar to those seen in optical microstructures of Gleeble simulated specimens, suggesting possibilities of controlling fairly accurately the deformation conditions in rolling as well as direct quenching at high rates (average cooling rates about 30-35°C/s up to about 400°C) close to partitioning temperatures. Typical austenite contents as measured by XRD were in the range 6-9% and 4.5-7% for High-Si and High-Al steels, respectively, irrespective of partitioning temperature. As mentioned earlier, some of the rolled samples were subjected to long time partitioning, while being cooled extremely slowly over 29-30 hours by switching off the furnace thus simulating the cooling of the coiled strips in industrial rolling. Hardness measurements made on rolled samples showed closely similar levels of hardness as compared to those observed in Gleeble specimens, particularly for High-Si steel (about 440-450 HV). However, some High-Al steel samples showed hardness values as low as 390 HV, as a consequence of very fine strain induced ferrite noticed in some sections of the rolled plates suggesting drop in local temperatures during controlled rolling and the need for slightly increasing the FRT in the case of High-Al steel.Examples of typical engineering stress-strain curves recorded at room temperature on controlled rolled, direct quenched and partitioned samples are given in Fig. 6. For comparison, typical tensile curves from the lab-rolled 0.14C DQ martensitic steel of similar yield strength have also been plotted. The advantages of DQ&P processing over simple DQ in respect of total ductility and uniform elongation are evident, even though the tensile strength of High-Al steel is somewhat lower and may require further improvement. However, there was no significant influence of coiling simulation (long time slow cooling over 29 hours in furnace) on tensile properties of either steels, as will be shown later. XRD measurements near the fractured ends of some tensile specimens of High-Si steel revealed that the retained austenite content had dropped during straining from the original 7.5% to about 3.5% showing that a large fraction of the original retained austenite transformed during straining.Fig. 7 presents Charpy impact energy as a function of test temperature for both High-Si and High-Al steels lab-rolled down to low finish rolling temperature, followed by direct quenching and partitioning at 320°C. In the case of High-Al steel, the DQ&P sample was subjected to coiling simulation (CS; cooled slowly in furnace allowing non-isothermal partitioning to occur over long time). For comparison, the impact toughness data obtained on specimens from a High-Si steel sample rolled at a high finish rolling temperature (recrystallized unstrained austenite) followed by direct quenching and partitioning at 320℃ are also presented in the same graph. As can be discerned from Fig. 7, both the steels have shown comparable impact toughness properties at sub-zero temperatures. However, the upper shelf energy of High-Al steel is significantly lower than that of High-Si steel.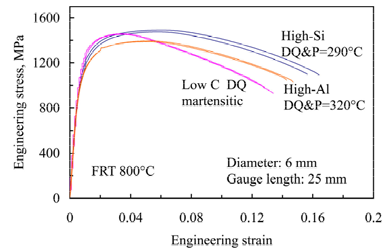 | Figure 6. Typical engineering stress-strain curves; specimens transverse to rolling direction |
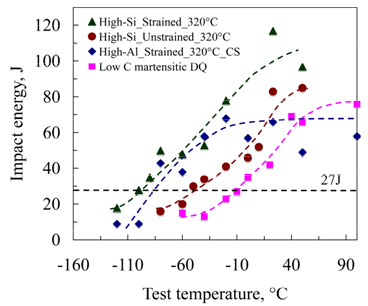 | Figure 7. Typical Charpy V impact energy as a function of test temperature (10 x 10 mm specimens; transverse to rolling direction) |
The advantage of rolling at low temperatures in the no-recrystallization temperature range on impact toughness is clearly evident: the 27J transition temperature (T27J) is lowered by about 55℃ in the case of High-Si steel. This is consistent with the observed refinement of the martensite packet and block sizes, and the shortening and randomization of the lath structure caused by straining of the austenite prior to quenching. It is also possible that retained austenite has a beneficial effect on the transition temperature. Fig. 7 also shows that DQ&P processing improves the transition temperature compared to that of the lower carbon fully martensitic DQ steel. Results presented in Figs. 6 and 7 show that good combinations of strength, ductility and impact toughness are possible with laboratory rolling, despite the fact that the total hot rolling reduction is much lower than that available in an industrial process. Optimization of the hot rolling and cooling conditions should allow even better combinations of properties to be produced on an industrial scale. The Q&P concept has recently been considered in literature in context of hot-strip mill processing, whereby a desired fraction of martensite forms during cooling to the coiling temperature, followed by non-isothermal partitioning of carbon from supersaturated martensite to remaining austenite, thereby stabilizing it to room temperature[15].Table 2 presents a summary of mechanical properties obtained on rolled DQ&P samples from both the steels. Also included are the tensile and impact property data of the lower carbon, fully martensitic DQ steel. The 0.2% yield strength (Rp0.2) is marginally lower than the target level (1100 MPa) but for example temper rolling should be able to raise the yield strength to the required level (e.g. 1.0% proof strength (Rp1.0) values are of the order of 1300 MPa). Referring to the High-Si DQ&P samples, both yield and tensile strengths obtained on recrystallized DQ&P specimens (FRT =1000℃) are marginally lower than those finish rolled at the lower FRT of 800°C. While the total elongation (A) and reduction of area to fracture (Z) vary in a narrow range, the total uniform elongation (Agt) and the plastic uniform elongation (Ag) are somewhat better at the lower quenching temperature of 290℃ (5.5% and 4.7%, respectively). Even the sample quenched to 290℃, followed by long-time non-isothermal partitioning during cooling in furnace (coiling simulation) too did not show any significant change in properties, except marginally lower uniform elongation (Agt = 4.6%, Ag = 3.9%). The elongation to fracture with a proportional gauge length (A) is the standard value (EN 10002-1) used for hot rolled materials in Europe. The temperatures corresponding to 27J impact energy (T27J) and 50% shear fracture (T50%) are quite low and distinctly improved over those of the low C martensitic DQ steel (see also Fig. 7). For the plates with FRT 800C, the reasons for the lower tensile strength and uniform elongation values obtained with TQ/TP=320℃ compared to 290℃ need further investigation.Referring to High-Al steel, the DQ&P samples quenched at 340 and 360℃ showed relatively lower tensile strength as compared to that obtained on DQ martensitic steel. Even the total and plastic uniform elongations were at the same level as the DQ steel or even lower. However, the properties were better at lower quenching temperatures of 320 and 270℃. Despite long-time non-isothermal partitioning (coiling simulation) at these temperatures, the tensile properties including the total uniform elongation (Agt) and plastic uniform elongation (Ag) were reasonably improved. In particular, the temperatures corresponding to 27J impact energy (T27J) and 50% shear fracture (T50%) are quite low and comparable to those obtained on High-Si DQ&P steel and distinctly improved over those of the martensitic DQ steel. Tiny fractions of strain-induced ferrite noticed in some locations of a few High-Al plates may have influenced the mechanical properties and calls for adjusting the chemical composition or modifying the thermomechanical processing conditions prior to DQ&P processing. An attempt to raise the finish rolling temperature to 890℃, however, was counterproductive and marginally reduced the uniform elongation (Agt = 3.0%, Ag = 2.3%) as well as raised the T27J temperature (-67°C), possibly as a consequence of deformation in partial recrystallization regime. This needs further investigation.Table 2. Tensile* and Charpy impact properties of laboratory rolled DQ&P plates 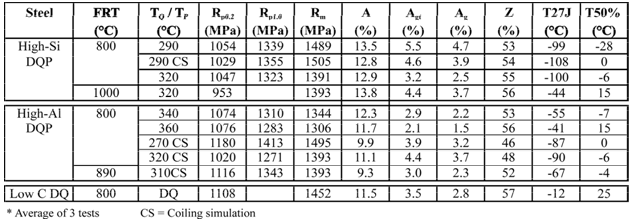 |
| |
|
4. Summary and Concluding Remarks
Preliminary results in respect of microstructures and mechanical properties of two experimental High-Si and High-Al steels processed through direct quenching and partitioning processing schedules have been presented. On the basis of Gleeble simulations, laboratory rolling experiments were designed to achieve either recrystallized or non-recrystallized austenite prior to direct quenching and partitioning in a furnace at the quenching stop temperature. Metallographic and XRD studies revealed clearly the presence of extended pools of retained austenite between martensite laths. Also, the advantage of straining in austenite in respect of the refinement of martensite packets/blocks and lath structure was clearly evident and resulted in significant improvement in mechanical properties, particularly the impact toughness. Dilatometric measurements and electron microscopy have shown that besides carbon partitioning, isothermal martensite and bainite form at or close to the partitioning temperature. At high partitioning temperature, martensite tempering competes with the partitioning process. Bainite as well as high carbon martensite can form on cooling from the partitioning temperature. Promising results in respect of microstructures and mechanical properties as compared to those of a lower carbon, fully martensitic DQ steel, indicates that there are possibilities for developing tough ductile structural steels through the DQ&P route.
ACKNOWLEDGEMENTS
The authors would like to express their gratitude to the FIMECC Oy (Finnish Metals and Engineering Competence Cluster Ltd.), Tekes (Finnish Funding Agency for Technology and Innovation) and Rautaruukki Oyj for funding this research activity under the auspices of Light and Efficient Solutions Program.
References
[1] | J.G. Speer, D.V. Edmonds, F.C. Rizzo and D.K. Matlock, Current Opinion in Solid State Mater. Sci., Vol. 8 , 2004, p. 219. |
[2] | H.Y. Li, X.W. Lu, W.J. Li and X.J. Jin, Metall. Mater. Trans. A, Vol. 41A, 2010, p. 1284. |
[3] | E. De Moor. S. Lacroix, A.J. Clarke, J. Penning and J.G. Speer, Metall. Mater. Trans. A, Vol. 39A, 2008, p. 2586. |
[4] | J.G. Speer, F.C.R. Assunção, D.K. Matlock and D.V. Edmonds, Mater. Research, Vol. 8, No. 4 , 2005, p. 417. |
[5] | A.J. Clarke, J.G. Speer, M.K. Miller, R.E. Hackenberg, D.V. Edmonds, D.K. Matlock, F.C. Rizzo, K.D. Clarke and E. De Moor, Acta Mater., Vol. 56, 2008, p. 16. |
[6] | D.V. Edmonds, K. He, F.C. Rizzo, B.C. De Cooman, D.K. Matlock and J.G. Speer, Mater. Sci. Eng. A, Vol. 438-440, 2006, p. 25. |
[7] | M.C. Somani, L.P. Karjalainen, D.A. Porter and D.K. Misra, Mater. Sci. Forum, Vol. 706-709, 2012, p. 2824 . |
[8] | M.C. Somani, D.A. Porter, L.P. Karjalainen and D.K. Misra, Proc. Int. Symp. on Recent Developments in Steel Processing, MS&T’12 Conf. & Exhibition, Pittsburgh, PA, 2012 (in press). |
[9] | D. Kim, J.G. Speer and B.C. De Cooman, Metall. Mater. Trans. A, Vol. 42A, 2011, p. 1575. |
[10] | J. Speer, D.K. Matlock, B.C. De Cooman and J.G. Schroth, Acta Materialia, Vol. 51, 2003, p. 2611. |
[11] | S.M.C. van Bohemen, M.J. Santofimia and J. Sietsma, Scripta Mater., Vol. 58, 2008, p. 488. |
[12] | M.J. Santofimia, L. Zhao and J. Sietsma, Mater. Sci. Forum, Vol. 706-709, 2012, p. 2290 . |
[13] | V. Smanio and T. Sourmail, Solid State Phenomena, Vol. 172-174, 2011, p. 821. |
[14] | K. Takahashi and M. Hashimoto, Int. Conf. on Thermomechanical Processing of Steels and Other Materials (THERMEC’97), Wollongong, Australia, The Minerals, Metals & Materials Society, 1997, pp. 395 – 401. |
[15] | G.A. Thomas, J.G. Speer and D.A. Matlock, Proc. Int. Conf. on New Developments in Advanced High Strength Sheet Steels, Orlando, Florida, AIST, 2008, pp. 227 – 236. |