A. K. Bhakat1, M. K. Pradhan2, C. Muthuswamy2
1Steel Authority of India Limited (SAIL), Research & Development Centre for Iron & Steel (RDCIS), Ranchi, 834 002, India
2Steel Authority of India Limited (SAIL), Rourkela Steel Plant, Rourkela, 769011, India
Correspondence to: A. K. Bhakat, Steel Authority of India Limited (SAIL), Research & Development Centre for Iron & Steel (RDCIS), Ranchi, 834 002, India.
Email: |  |
Copyright © 2012 Scientific & Academic Publishing. All Rights Reserved.
Abstract
Medium carbon steels are having large demand for wide range of engineering applications. Selected difficult-to-cast medium carbon grades e.g. MC 40, MC 55 & MC 60 have been successfully developed and subsequently commercialized at integrated steel plant. MC 40 grade have good market demand for application like two wheeler chain links, industrial chain links, hair clips, binder clips, stapler parts, sprockets etc. whereas MC 55 grade have demand for application like hacksaw blade, drop pin for textile industry, dowel pins, clutches, seat buckles etc. Similarly, MC 60 grade is used for manufacturing circlips, spring washers, band saw blades for wood cutting, circular saws, cross cut saws etc. The identified medium carbon grades have been developed by optimizing casting and hot rolling parameters. The mill load was maintained well within the finishing mill capacity i.e. 25 MN at hot strip mill by maintaining adequate slab soaking time in the reheating furnace. The application of these steel demands good internal soundness and cleanliness to arrest the cracking susceptibility of the finished products during cold rolling/ forming operations. The metallurgical factors contribute for development of these grades are control of Al (< 0.04 %) & N content (~ 60 ppm) along with control of excessive segregation of carbon in the steel and presence of inclusions like aluminium oxide and MnS which are mainly responsible for inadequate cold reducibility.
Keywords:
Medium carbon steel, MC 40, MC 55, MC 60, Metallurgical factors, Strength, Hardness
Cite this paper: A. K. Bhakat, M. K. Pradhan, C. Muthuswamy, Metallurgical Factors Influencing the Performance of Medium Carbon Hot Rolled Coils Developed in Underpowered Mill, International Journal of Metallurgical Engineering, Vol. 2 No. 1, 2013, pp. 111-115. doi: 10.5923/j.ijmee.20130201.16.
1. Introduction
In the fast changing market scenario, value added steels with enhanced quality, properties and performance capabilities are getting more thrust day by day due to their specific end applications. In India, the cold reducers segment is growing very fast and their quality requirements for hot rolled coils are more and more demanding. It has been found that customers have preference for medium carbon grades with wide range of carbon (0.35-0.65%) for specific end applications. Hot rolled coils of these grades are input materials used for cold reduction to thinner gauges, which subsequently cater to the needs of different segment like cycle industry, auto components and general engineering applications. The manufacturing process involves three stages: (1) the conversion of concast slabs to coils by hot rolling, (2) reduction in thickness by pickling & cold rolling and (3) conversion of finished products by slitting and machining. The first stage involves conversion of cast slabs into coils through hot rolling operations. The second stage involves cold reduction of coils to desired thickness by pickling & cold rolling and the final stage involves slitting and manufacture of finished product by machining operations. Final heat treatment depends on the nature of product and required properties. The requirement of medium carbon grades is mainly for cold reducing and engineering fabrication segments. The objective was to develop customer specific medium carbon grades hot rolled coils in an underpowered mill where there is a limitation of maximum load (< 25 MN) in F1 strand. Accordingly the pass design and rolling schedules for hot rolling have been modified. The hot rolled coils supplied are subjected to a series of processing steps at the customers end and are used for a variety of end-applications. The major quality requirement of the hot rolled coils was moderate to high strength levels (YS: 400 to 700 MPa and UTS: 600 to 1000 MPa) with good cold reducibility (% EL: 12 to 22% in 50 mm GL) and adequate surface quality. These product attributes are achieved by major steel producers through a combination of measures such as better composition control (uniformity throughout the slabs), use of secondary refining in the steel making (to achieve a low sulfur and low inclusion content steel) and controlled rolling. All these measures will help the secondary producers to achieve desired properties and quality of the finished products.
2. Experimental Procedure
The developmental exercise in case of MC 40 grade steel involved rolling of lower thickness of hot rolled strip i.e. < 2.5 mm as it helps re-rollers to minimise number of passes at their rolling mills and thereby increases their mill productivity. Rolling of medium carbon steel with carbon ranging from 0.36 to 0.45% and thickness < 2.5 mm leads to higher rolling loads in the finishing stand of the hot strip mill. A number of trials were conducted by selecting combination of various processing parameters at hot strip mill i.e. soaking duration of slab, temperature of exit roughing, transfer bar thickness and draft schedule. Rolling load in the finishing stand (maximum load bearing capability: 25 MN) was regulated by rescheduling drafts and thermal regime. Strict control of rolling parameters (exit roughing temperature: ~1100oC; Finish rolling temperature: ~880oC; Coiling temperature: ~670oC) led to production of thinner gauges (2.20-2.50 mm + 0.10 mm) without overloading the mill when rolling load in F1 was significantly lower (19-22 MN). The modified practice succeeded in regulating the strip thickness within specified norms even with higher input slab thickness of 210 mm. The typical properties achieved in the hot rolled coils[YS: 430 MPa, UTS: 620 MPa, Elongation (50 mm GL): 19% and Hardness: 90 HRB] were adequate for the product and accepted by the customers. As medium carbon grades are difficult-to-cast due to tendency of segregation and occurrence of breakouts, casting parameters were selected judiciously. The heats of MC 55 & MC 60 were made in the basic oxygen furnace converter through BOF-VAR-LF-CC route and 210 x 950 x 8000 mm concast slabs were produced. The casting speed was stabilized around 0.7-0.8 m/ min The concast slabs were hot rolled into 2.5/5 x 940 mm coil in the hot strip mill with optimized rolling parameters and gauge control. While processing this material at hot strip mill, the mill load was well within the finishing mill capacity i.e. 25 MN. Metallographic specimens were prepared as per ASTM E3-2001 standard and the etchant used was 2% nital solution for microstructural examination. Microstructural examination was carried out as per ASTM E45-2005 standard using a Neophot-30 optical microscope. Hardness of the samples was measured in a Rockwell hardness tester as per ASTM E18-2005 standard. Nature and chemical composition of inclusion present in the surface was ascertained via EDX (Energy Dispersive X-ray) analysis and scanning electron micrograph (SEM) JEOL JSM 840A.
3. Results and Discussions
Medium carbon steel is normally classified on the basis of chemical composition (in terms of % carbon contents) and is used when higher strength and hardness is required in as rolled condition. This material can be used for all range of application i.e. rolling, forging and wire drawing. The heat treated steel gives good balance of ductility and strength and it can be frequently hardened and strengthened by heat treatment or cold working. Medium carbon steel is predominantly pearlite microstructure with good strength, good wear resistance, high hardness and moreover it is cheaper than alloy steel and are commercially attractive. The material can be used with or without heat treatment depending upon the application and level of properties required. The hot rolled material should have good cold reducibility (ability of a material to be reduced in desired thickness through single or double stage cold reduction) for its end use. Good cold reducible material implies that the strip should not break e.g. no edge cracking, no over-loading of mill and higher reduction per pass. It largely depends on its ductility, cleanliness level, hardness and bendability. Customized requirement fully depends on the processing conditions, product form, applications and its end usage. In the first phase, hot rolled coils of MC 40 quality was taken up for its development and soon after establishing its acceptability in the market place, this product was commercialized. The hot rolled coils supplied are subjected to a series of processing steps at the customers end and are used for a variety of end-applications such as links plates for motorcycle and industrial chains, hair clips, binder clips, stapler parts etc. Some of the customers’ source medium carbon hot rolled coils in higher thickness (7-8 mm), which is pressed to fabricate products like sprockets. The components fabricated using MC 40 grade steel is shown in Fig. 1 a & b.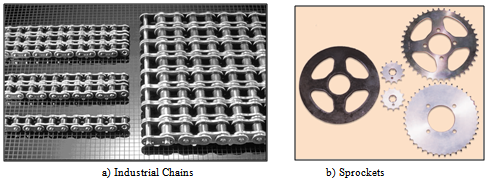 | Figure 1. Items fabricated using MC 40 grade steel |
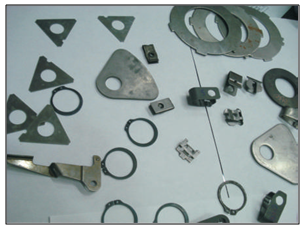 | Figure 2. Items fabricated using MC 55 grade steel |
Subsequently, another higher version i.e. MC 55 (C: 0.51-0.60) grade was also developed through BOF-VAR-LF-CC route. The casting speed was stabilized around 0.7-0.8 m/ min. Cast slabs were hot rolled by controlling finishing and coiling temperatures. While processing this material at hot strip mill, it was observed that the mill load was well within the finishing mill capacity i.e. 25 MN. This has been possible by maintaining adequate slab soaking time in the reheating furnace. This product enjoys good market demand for application like hacksaw blade, drop pin for textile industry, dowel pins, clutches, seat buckles etc. The components fabricated using MC 55 grade steel is shown in Fig. 2.Similarly, MC 60 grade steel was developed through BOF-VAR-LF-CC route. Cast slabs were hot rolled without much difficulty by maintaining proper finishing and coiling temperatures. While processing these materials, the mill load (22-25 MN) remained within the limit of the mill capacity (25 MN). This grade is used for manufacturing circlips, spring washers, band saw blades for wood cutting, circular saws, cross cut saws etc. and the components fabricated is shown in Fig. 3 a & b.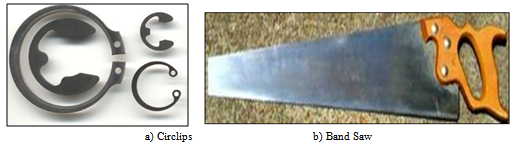 | Figure 3. Items fabricated using MC 60 grade steel |
The chemical composition of the developed grades is given in Table 1. The mechanical properties in terms of yield strength (YS), ultimate tensile strength (UTS), percentage elongation (EL %) and surface hardness at room temperature were evaluated and shown in Table 2. It can be deduced that in case of medium carbon steel, hot rolled coil properties conform to the desired value. Table 1. Chemical Composition of the Developed Grades  |
| |
|
Table 2. Mechanical Properties of Medium Carbon Grades  |
| |
|
Optical microscopy of the samples for different medium carbon grade steel was carried out for its characterization and is shown in Fig 4 a & b. The optical microstructural examination illustrates the presence of ferrite and pearlite phases in hot rolled condition. It was found that presence of % pearlite was 57-58 % in case of MC 40 grade steel as against 78-79 % in case of MC 55 grade steel. The predominantly present pearlite plays a useful role in increasing tensile strength and imparting a measure of wear resistance[1].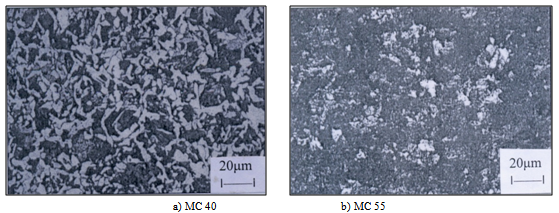 | Figure 4. Microstructures of Hot Rolled Medium Carbon Grades Steel |
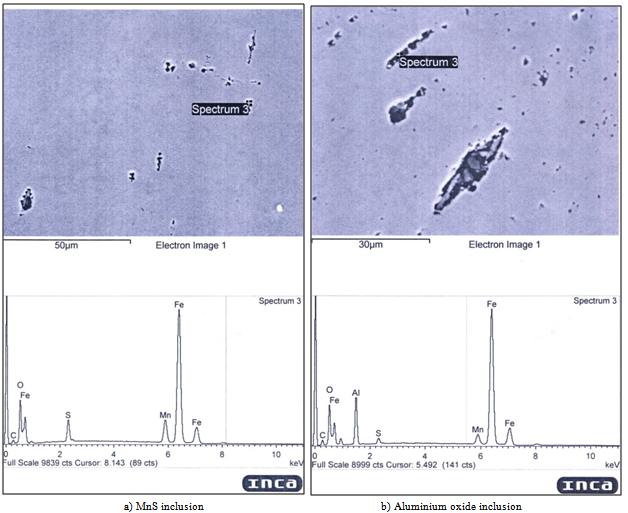 | Figure 5. EDX spectrum of the inclusion analysis |
Four types of inclusions commonly found present in steels i.e. sulphide, alumina, silicate and globular oxide. Sulphide inclusions normally present in the form of MnS have a high deformability index over a wide range of temperature. Cold and hot deformation elongates the MnS inclusions in the form of stringers and adversely affects the transverse ductility of the steel[2,3]. Silicates and alumina inclusions are products of deoxidation process of steel[4]. The deformability index of alumina is the lowest, followed by silicate and sulfide. Due to their poor deformability, silicates and alumina tend to fragment into smaller pieces leading to formation of voids and subsequent crack formation during cold working processes such as cold forming, cold forging, wire drawing etc. Thus the efforts are basically directed towards steel making with proper deoxidation practice for minimization of inclusions in the steel. Surface cracks normally create more of a problem than any type of internal cracks on a slab due to its exposure to air where the same is oxidized and unable to be re-weld during rolling[5,6]. Excessive secondary cooling and high casting temperatures are also responsible for crack formation[7,8]. To find out the nature of inclusion and its chemical composition, EDX analysis was carried out in various locations using scanning electron microscope. Fig. 5 a & b exhibits the EDX spectrum of the inclusion analyzed along with the elemental analysis of the same inclusion. The plots show prominent peaks of Mn, S, Al, O etc. besides other elements present. This clearly states the presence of MnS and Aluminium oxide inclusions in the steel. However, it was found that the total volume fraction of inclusion present in the medium carbon grades is limited to 0.20% and no problem has been encountered at the customer’s end during further processing of these hot rolled coils.
4. Conclusions
Medium carbon grades (MC 40, MC 55 & MC 60) are being considered as difficult-to-cast grades due to presence of high carbon and medium manganese. Optimization of chemistry, casting and rolling parameters have been carried out for its commercial production. The Al & N content in the medium carbon grades should be controlled within reasonable limit (0.02-0.04 wt %) and 60 ppm respectively to avoid any chances of crack formation during cooling of slab. Extensive customer interaction and continuous monitoring resulted in achieving & maintaining desired quality for these medium carbon grades. The performance feedback from various customers was found to be very good and developmental efforts have been well appreciated by the customers.
ACKNOWLEDGEMENTS
The authors wish to acknowledge the management of Research & Development Centre for Iron and Steel (RDCIS) and Rourkela Steel Plant (RSP), Steel Authority of India Limited (SAIL) for giving permission to publish this work.
References
[1] | B. A. Cots et al., The Relationship Between Structures and Mechanical Properties of Metals, NPL Symposium, HMSO, London, 2003, pp 455-456. |
[2] | R. Rungta, A. J. Skidmore and R. D. Buchheit, Inclusion and their Influence on Material Behavior, ASM International, Materials Park, OH, 1988, pp. 1. |
[3] | G. F. Vander Voort, Inclusion and their Influence on Material Behavior, ASM International, Materials Park, OH, 1988, pp. 49. |
[4] | M. K. Pradhan, et al., Investigation of Crack Formation in Continuous Cast Slabs & Remedial Measures taken for Improving Productivity at Rourkela Steel Plant, IIM Metal News, Vol. 11, No. 2, 2008, pp. 8-14. |
[5] | J. K. Brimacombe and K. Sorimachi, Crack Formation in Continuous Casting of Steel, The Iron and Steel Society, Vol. 8, 1997, pp. 57-58. |
[6] | O. O. Daramola et al., Effects of Heat Treatment on the Mechanical properties of Rolled Medium carbon Steel, Journal of Minerals & Materials Characterization & Engineering, Vol. 9, No. 8, 2010, pp. 693-708. |
[7] | W. F. Smith and J. Hashemi, Foundations of Materials Science and Engineering, 4th Edition, Mcgraws-Hill Book, 2006, pp 28-36. |
[8] | A. K. Bhakat, A Typical Failure Analysis of Medium Carbon Hot Rolled Strips, Journal of Failure Analysis and Prevention, ASM International, Vol. 10, No. 6, 2010, pp. 463-467. |