Robert J. Glodowski
Evraz - East Metals (NA) Pittsburgh, PA, USA
Correspondence to: Robert J. Glodowski, Evraz - East Metals (NA) Pittsburgh, PA, USA.
Email: |  |
Copyright © 2012 Scientific & Academic Publishing. All Rights Reserved.
Abstract
Several prediction models of V-N strengthening have been published and used over the course of many years of vanadium microalloying experience. The basis and origin of a proven strength model previously distributed is reviewed and explained. Inherent in the prediction accuracy of the model is the assumption of the amount of nitrogen actually available for VN precipitation. This paper discusses various situations where the amount of nitrogen available can be significantly altered by the presence of other alloy elements, particularly Ti, Nb, and Al. Of these, the effect of the Al content (and prior processing history) seem to be most widely overlooked when evaluating and predicting the expected strengthening of the VN precipitate in polygonal ferrite. The possible interactions of Al and N that can affect nitrogen availability are reviewed, and the unintended effects of specification Al requirements are explained.
Keywords:
Steel, Vanadium, Effective Nitrogen, Precipitation, Strengthening Model
Cite this paper: Robert J. Glodowski, An Empirical Prediction Model of the Incremental Strengthening of Ferrite/Pearlite Steels with Additions of Vanadium and Nitrogen, with Emphasis on the Effective Nitrogen Level, International Journal of Metallurgical Engineering, Vol. 2 No. 1, 2013, pp. 56-61. doi: 10.5923/j.ijmee.20130201.09.
1. Introduction
Since the advent of microalloyed steels it has been recognized that vanadium precipitation strengthening is enhanced by the presence of nitrogen. Perhaps this was most widely announced in several papers included in the now classic “Proceedings of an International Symposium on High-Strength, Low-Alloy Steels”, perhaps better known as MA ‘75.[1] However, at that time many of the products were heat treated, either normalized or quenched and tempered. As a result, conclusions about the strengthening factors for vanadium and nitrogen tended to vary significantly. The relative effects of austenitizing temperature, nitrogen and aluminum contents that control the availability of V and N for precipitation strengthening during subsequent transformation were generally unrecognized. For the as-rolled situation, the need to control austenite recrystallization and growth during the rolling process was just being recognized. While the advantages of control rolling with higher recrystallization stop temperatures were just being exploited, the benefits of recrystallization controlled rolling were not promoted to any degree. Grozier [2] presented an extensive review of results from the production of VAN-80, vanadium-nitrogen bearing hot rolled strip steel produced with controlled cooling first introduced in 1968. The graphical model used by Grozier to describe the effect of vanadium and nitrogen content on incremental yield strength was first published by Korchynsky and Stuart[3] and is reproduced again here as Figure 1. This information, confirmed by numerous researchers, has been widely referenced. Also widely used from Grozier’s work is Figure 2, showing the effect of coiling temperature on the precipitation strengthening of 0.12% vanadium steel at increasing nitrogen levels.One problem with Figure 1 is that it predicts no strengthening of vanadium at zero nitrogen. This is not likely to be true except in the most extreme cases, as there should be some VC precipitation strengthening. Also, the slope of strengthening with increasing nitrogen increases with higher V contents. At sub-stoichiometric levels of nitrogen, the amount of VN precipitation is controlled by the nitrogen available, not the amount of V. Because of this, N strengthening slopes at different V levels are more likely to be parallel, but starting at different strengthening levels due to possible VC precipitation. The VC precipitation strengthening would logically be assumed to be relatively constant for constant processing conditions. Only the nitrogen level is changing. Thus, the strengthening curves at sub-stoichiometric levels of N would be expected to be slightly displaced by higher V contents, but parallel up to stoichiometric VN levels. As the nitrogen level exceeds stoichiometric V:N, the strengthening effect will be significantly reduced. 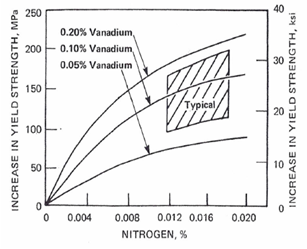 | Figure 1. Increase in yield strength from nitrogen and vanadium as a result of the precipitation of vanadium nitride. Control-cooled coil product, with a coiling temperature of 593 C[3] |
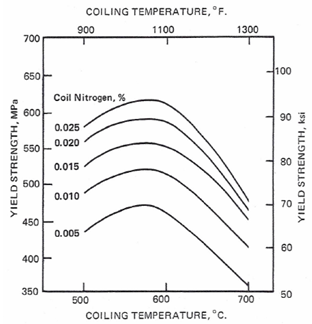 | Figure 2. Effect of coiling temperature and total nitrogen content on the yield strength of 6.3 mm strip with a FRT of 900 C and cooled at 17 C/sec. 0.13% C, 1.40% Mn, 0.5% Si, 0.12% V[2] |
Perhaps a good demonstration of this effect was published by Siwecki et.al. in 1981.[4] Figure 3 shows the contribution of V-N precipitation strengthening to a 0.12% C, 1.35% Mn, 0.09% V steel produced by either control rolling (CR) or recrystallization controlled rolling (RCR). For all processing conditions, the contribution of additional nitrogen was linear, consistently at 7 MPa for every additional10 ppm of nitrogen. For all nitrogen levels, the nitrogen is sub-stoichiometric to the vanadium level, so the linear nitrogen response is expected and consistent with the logic that the amount of addition VN precipitation is controlled by the additional N.
2. Developing a Different Model
To clarify some of the issues stated, a method was needed to generate a descriptive graphical model of V-N strengthening that would have a visual impact demonstrating the strengthening potential of the VN precipitation, and yet reflect the other strengthening processes that may be contributed by the presence of VC precipitation as well as interstitial nitrogen. As shown in Figure 3, there will always be the possibility of induced variation from processing variations. An empirical fit to a mechanical property data obtained from multiple production mills was chosen as the basis for the model. Next, for functionality and for ease of visual recognition, it was decided to use incremental yield strength as the Y axis, and vanadium content, the primary controlled variable, as the x axis. Different but fixed nitrogen levels would be represented by multiple curves on this graphical representation. 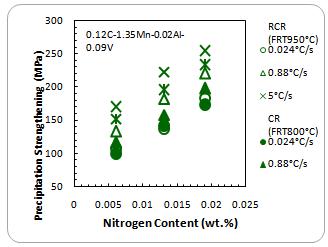 | Figure 3. Effect of nitrogen on precipitation strengthening[4] |
What is required to build this kind of graphical model is the strength contribution of three different situations. First, the effect of interstitial or free nitrogen is needed to predict the starting points. Second, the strengthening rate for V additions must be determined when there is a hyper-stoichiometric level of nitrogen available and VN precipitation is predominant. Third, the strengthening rate for V additions when no nitrogen is available (hyper-stoichiometric additions of V to N) must also be determined. It is presumed that VC will form at this time and be the primary precipitate for strengthening. For the base data set, a previously published compilation of test results from three different thin-slab direct-rolled strip mills was used.[5] The as-rolled properties were used for the regression model, as the simulated coil-cooled samples may have had addition VC precipitation that may not happen in production coils. Given the minimum amount of data available, only linear regression was considered. Since the N strengthening coefficient would be very different depending on the presence of vanadium, only data from V containing heats were used. Also, almost all of those heats were sub-stoichiometric in N for the V level, meaning that sufficient nitrogen was available to tie up all V as VN. A number of different dependent variable configurations were investigated in linear regression analysis, finally settling on the simplified version as follows: | (1) |
A brief review of the literature to estimate a value of the strengthening coefficient for interstitial or “free” nitrogen suggested that the effect is quite small. In MA’75, Pickering[6] reported a typical value of 350 MPa per 1% N, based on a survey of several different authors. Compared to the N coefficient in V steels, this value is insignificant, but not zero. This value is used to determine the starting (0% V) point of the different strength curves representing different nitrogen levels, providing separation in the initial portion of the graph. Since the practical levels of nitrogen variation in ferritic steels is only from 50 to 200 ppm, the strength increase for the additional 150 ppm of interstitial N would only be slightly over 5 MPa. The initial section of each strengthening curve would represent the initial V addition, which would by necessity be nitrogen rich assuming a starting N level of at least 50 ppm. Since the data set was essentially a constant carbon level (.05% to .06%) a C coefficient could not be determined. As previously discussed, the interstitial N strengthening is considered to be relatively insignificant. The N coefficient is assumed to represent the N contribution to strength, therefore predicting the VN precipitation strengthening. In line with that assumption, the V coefficient is assumed to represent the V strengthening due to VC precipitation. While these assumptions are tenuous at best, the end results proved to be very credible. Finally, we know that only precipitation in the ferrite during or after transformation provides strength. We also know that VN precipitation takes precedence over VC precipitation. Therefore, for the purposes of this model it is assumed that all VC precipitation takes place in the ferrite after transformation. The maximum solubility of carbon in ferrite immediately after transformation is considered to be about 0.02% C, and decreases rapidly as it cools further. That means the maximum VC precipitation that can be expected is that which forms from a maximum of 0.02% C, which stoichiometrically translates to 0.085% V. (V:C = 4.24:1) Vanadium added above the amount needed to form VN and VC from all of the N and C available will not contribute to precipitation strengthening. The result is a strength prediction curve for increasing V additions consisting of three lines with three distinct slopes – the first line having a higher slope with N available for VN precipitation, and the second line representing VC precipitation having a smaller slope when V is added beyond the stoichiometric V:N ratio (3.64:1). After the available C in ferrite is consumed, presumed to be a maximum of 0.02% C, the strengthening slope for vanadium additions approaches zero. The first inflection point of the Strength-Vanadium curve is at a V level of 3.64 x N content. The second inflection point is .085 V above the first break point, where all C in the ferrite is consumed. The result is as shown in Figure 4.Since the assumption is that all available nitrogen and all available carbon in the ferrite are consumed, there are no interstitial elements left to form strengthening vanadium precipitates. Since the level of vanadium is low, less than 0.2%, no further alloying effect is expected. The microalloying (precipitation strengthening) effect of vanadium has been exhausted because of the consumption of the available interstitial elements in the ferrite. 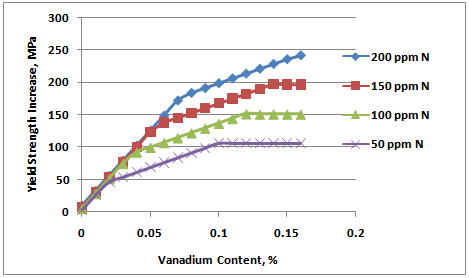 | Figure 4. Linear representation of strengthening model of ferritic steels with V and N |
3. Reality Check
The relationship of yield strength increase with vanadium addition can be affected by a number of variables. First, all VC and VN (or V[C,N]) must be in solution in the austenite prior to the final transformation to ferrite. This usually limits this analysis to either as-rolled or as-forged products. Second, there should be no re-precipitation in the austenite during rolling or forging. At high levels of vanadium and nitrogen, this is likely to be some deformation-induced precipitation which, while it can contribute to intragranular ferrite formation, does not contribute directly to strength. Secondly, most or all of the V should be precipitated in the ferrite, but we know that is unlikely to be true as well. The data used to derive this empirical description likely did not have much VN precipitated in the austenite, but it is likely that only a portion of the V was precipitated in the final as-rolled ferrite. This incomplete precipitation was demonstrated by the simulated coil-cooling strength increase that occurred in these materials and is reported elsewhere.[7] The strengthening shown in Figure 4 is not likely to contain all of the potential vanadium precipitation, but it does represent strength achieved in a variety of actual hot strip mill production processes. Since the VC precipitation is the last vanadium precipitation to occur and at a slower rate than the VN precipitation, it is subject to more dependence on process variation. Strengthening can be significantly less when a continuous cooling practice is used well beyond the austenite to ferrite transformation temperature. This reduction of V strengthening by rapid cooling to below 600°C is demonstrated by effect of lower coiling temperature as shown in Figure 2. For these situations where VC precipitation is limited, it is expected that the vanadium strengthening rate (slope of the line) in the intermediate region can be significantly less. On the other hand, some authors(8) have proposed that the precipitation strengthening of VC can be enhanced at intermediate carbon levels by super-saturation of the ferrite. Deduced values of precipitation strengthening for isothermally transformed 0.12% V steels at 650°C indicated a strong carbon effect. However, the nitrogen effect on enhancing VN precipitation strengthening was equally strong at all carbon levels. And finally, the rate of precipitation of VN and VC are controlled by various time-temperature parameters (solubility, diffusion and precipitation). As a result, different degrees of precipitation completion would be expected as process conditions changed. Besides affecting the actual amount of incremental strengthening, it would also cause difficulty in verifying with production data any of the inflection points suggested in Figure 4. Perhaps a better representation would be much more of a continuous curve. To reflect this reality, the model was modified as shown in Figure 5. Many years of experience has proven the model to be very useful in predicting the trade-off in V and N content in the final strength level. Because of the process dependence of the relationship, it is only an estimate of the actual strength achieved. So while quantitatively, the actual strength increments can be variable, there is always a qualitative relationship of the type shown in Figure 5.Even with the qualifications just mentioned, and the indirect derivation of the initial coefficients, this prediction of precipitation strengthening has proven to be very useful. In particular, an increase of yield strength by 7 MPa for each 10 ppm nitrogen added (when N is less than stoichiometric V:N) has been extremely consistent as reported by multiple investigators. 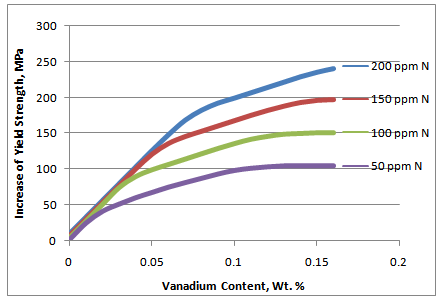 | Figure 5. Modified strengthening model of ferritic steel with vanadium and nitrogen |
4. Effective Nitrogen
With the understanding that the effectiveness of precipitation strengthening with vanadium is largely controlled by the available nitrogen, it is important to review the concept of “effective nitrogen”. From the previous discussion, it is apparent the VN precipitation in ferrite will occur in preference to VC precipitation. There may be some co-precipitation of V(C,N), but most investigators have found that the first to form is VN, then followed by VC precipitation around the VN particle. So the effectiveness of the vanadium addition is primarily a function of the nitrogen available. The problem is that, even if the nitrogen is in the steel, it may not be available for VN precipitation in the ferrite. Any nitride former that has a thermodynamic “preference” for nitrogen is capable of reducing the beneficial strengthening effect of VN precipitation. The “Effective” nitrogen, as defined as the nitrogen available for formation of VN precipitates, may be much less than the total nitrogen reported by standard analysis.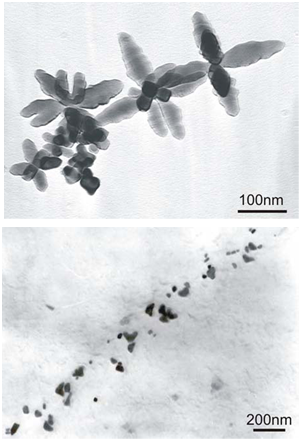 | Figure 6. TEM micrographs showing cruciform particles in a V-Ti-N steel (left), and cuboid particles in a V-Nb-Ti steel (right) after equalization at 1100℃.[8] |
The first, and most well know of the nitrogen scavengers, is titanium. TiN will form at very high temperatures, even before solidification, and will not typically dissolve to any significant extent during the reheat operation. So it can be assumed that for any Ti addition to the steel, a stoichiometric amount of nitrogen will be removed from availability. While Ti additions are desirable in some situations to provide grain refining precipitates for high temperatures grain growth control, the loss of N available for VN precipitation must be considered. For small amounts of Ti addition, additional nitrogen added can reduce the negative effects of effective N reduction. Niobium additions can complicate the issue. NbN is usually in solution during conventional reheating, but in CSP mills the reduced reheat temperatures may be insufficient to fully dissolve NbN. Also, because of the lower solubility of NbN vs. VN, the possibility of NbN precipitation during rolling is much higher than VN precipitation. Add to this the possibility that a Nb bearing steel is likely to be finish rolled at lower temperatures to take advantage of the higher recrystallization stop temperature. The combination creates a real problem in designing a V-Nb alloy system that takes advantage of the austenite conditioning properties of niobium while allowing the maximum VN precipitation. At this point there does not seem to be a desirable solution to this problem.
5. Aluminum Content
This leaves one more nitride forming element that is often overlooked, but almost always present. Aluminum is routinely added to steels for deoxidation and for grain refinement. The soluble Al, that amount that is not oxidized, can form AlN. Aluminum does not form AlC. The solubility of AlN is lower than VN, making it a competitor to V for the available N. Grozier recognized this problem, and discussed it at length[2]. He pointed out that when vanadium-nitrogen heats are produced with high aluminum contents, adequate reheating temperatures must be maintained to avoid deterioration in strength properties. Numerous other authors have identified the same issues. Similar problems exist with the new thin-slab direct-roll mills that use tunnel furnaces with limited heating capability. Fortunately, even with the low solubility of AlN, it is kinetically very sluggish to precipitate during the cooling cycle. As long as the temperature is in a decreasing mode in normal production processing cycles, AlN precipitation is minimized. Any reheating, however, can cause rapid precipitation. Problem areas include the traditional slab/billet reheating as discussed. One place where this reheating can occur is at the surface during casting, where discontinuous but repeating water sprays can create repeated thermal cycling. These cool and reheat cycles are ideal for precipitating AlN. While these AlN precipitates may be re-dissolved during conventional reheat cycles, they can cause hot short issues at the caster, resulting in cracking problems.[9] Very recent work reported by Rothleutner and Van Tyne[10] demonstrated the problem of Al effects in V-N microalloyed air-cooled forging steels. Again, the problem is getting the AlN in solution during the reheat cycle for forging. Air-cooled forging alloys rely heavily on VN precipitation, so the amount of effective nitrogen available is critical. His work demonstrated a loss of 50 MPa when reducing the forging reheat temperature from 1200 to 1100°C in a 0.37% C, 0.088% V, 0.031% Al, 153 ppm N steel. 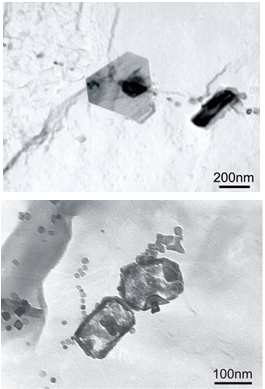 | Figure 7. TEM micrograph showing AlN + MnS in a V-N steel (left), and complex particles in a V-Ti-N steel (right) after equalization at 1050°C.(8) |
Modern steelmaking practices are capable of adequately deoxidizing steels with substantially less Al than in the past. Clean steel practices using reducing slag and other techniques are now widely used. There is little need to maintain high Al contents to minimize steel reoxidation from high oxygen slags. While fine ferrite grain size is a desirable trait for microalloyed steels, the method to achieve these fine grains in an as-rolled or as-forged microstructure is completely independent of the presence of aluminum. Rolling and cooling practices primarily determine the final grain size in microalloyed steels. Aluminum additions to meet specification grain size requirements are of no value in as-rolled steels. Neither is the reheat testing of these steels for subsequent austenite grain size. Since the as-rolled product will not be heat treated, the austenite grain size achieved on reheating is irrelevant to the performance of the steel in the as-rolled condition.
6. Summary
A graphical model showing the interactions of V and N on the precipitation strengthening of polygonal ferrite steel is developed using a combination of empirical data and expected thermal-mechanical response. The resulting model has been shown to be very useful in predicting the effects of nitrogen on the effectiveness of vanadium precipitation strengthening. The importance of the effective nitrogen level is developed, considering the possible competing effects of the presence of alternate nitride forming elements. In particular, the importance of considering the competition of aluminum and vanadium for the nitrogen content is reviewed. When using the vanadium-nitrogen alloying system, it is highly recommended that the aluminum additions be limited to that necessary for the desired metallurgical function required of the aluminum addition. Since microalloyed steels were designed to be used in the as-rolled or as-forged condition, the presence of aluminum has no bearing on the grain size of the steel as used.
References
[1] | Micro Alloying 75 Proceedings, Oct. 1975, Washington, D.C. USA |
[2] | J.K. Grozier “Production of Microalloyed Strip and Plate by Controlled Cooling”, MA’75, pp. 241-250 |
[3] | M. Korchynsky, H. Stuart, Symposium-Low Ally High-Strength Steels, Nuremberg, May 1970, pp.17-27 |
[4] | T. Siwecki, A. Sandberg, W. Roberts, and R. Lagneborg. “The Influence of Processing Route and Nitrogen Content on Microstructure Development and Precipitation Hardening in Vanadium-Microalloyed HSLA-Steels”, Thermomechanical Processing of Microalloyed Austenite, Pittsburgh Pa. Aug. 1981. Pp. 163-194. |
[5] | R.J. Glodowski, “Effect of V and N on Processing and Properties of HSLA Strip Steels Produced by Thin Slab Casting”, 42nd MWSP Conf. Proceedings, ISS, Vol. XXXVIII, 2000, pp. 441-449. |
[6] | F.B. Pickering “High-Strength, Low-Alloy Steels – A Decade of Progress”, MA’75, 1975, pp 9-30. |
[7] | R.J. Glodowski, “Nitrogen Strain Aging in Microalloyed Steels”, ISS Tech 2003 Conference Proceedings, pp.763-7711. |
[8] | Y. LI, J.A. Wilson, D.N. Crowther, P.S. Mitchell, A.J. Craven, T.N. Baker, “The effects of Vanadium, Niobium, Titanium and Zirconium on the Microstructure and Mechanical Properties of Thin Slab Cast Steels”, Vanitec Publication, Westerham, Kent. UK. |
[9] | R.J. Glodowski, “Fine Grain Practice - Revisited” Proceedings, AISTech May 2010, Pittsburgh. |
[10] | L.M. Rothleutner and C.J. Van Tyne, “Mechanical Properties of a Vanadium Microalloyed Air-cooled Forging Steel with Various Aluminum Additions”, Proceedings, MS&T’12, Oct. 7-12, 2012. |