S. V. Subramanian1, Md Kashif Rehman1, H. Zurob1, J. M. Gray2
1Department of Mat. Sci. and Engg., McMaster University, Hamilton, Canada
2Microalloyed Steel Institute, 5100 Westheimer, St. 540, Houston, Texas 77056, USA
Correspondence to: S. V. Subramanian, Department of Mat. Sci. and Engg., McMaster University, Hamilton, Canada.
Email: |  |
Copyright © 2012 Scientific & Academic Publishing. All Rights Reserved.
Abstract
Quantitative modeling of (a) strain induced precipitation of NbC and its interaction with recovery and recrystallization, (b) solute drag effect of Nb on boundary mobility have contributed to understanding the evolution of microstructure during thermo-mechanical rolling and accelerated cooling of plates or strips. While a fully integrated model is yet to be developed based on multi-variants associated with time evolution of local chemistry, deformation effects on precipitation and recrystallization and their mutual interactions influencing the microstructure, a modular approach has been developed to control the microstructural evolution at different stages of processing, based on current metallurgical understanding the underlying phenomena controlling the structure at each stage. The key concept is based on integrating modules of upstream austenite conditioning with downstream austenite transformation to control the morphological microstructure, and density and dispersion of high angle boundaries associated with crystallographic structure to which strength and fracture properties of the steel are related. The microstructural control at each of the various stages of hierarchical evolution is captured and integrated in “Through Process Modeling” based on modular approach. The application of process modeling of microstructure evolution based on modular approach for successful development of higher grade line steels based on high niobium (0.1wt%) is the focus of this paper.
Keywords:
Niobium Microalloying, Process Modeling, Recrystallization, Line Pipe Steel
Cite this paper: S. V. Subramanian, Md Kashif Rehman, H. Zurob, J. M. Gray, Process Modeling of Niobium Microalloyed Line Pipe Steels, International Journal of Metallurgical Engineering, Vol. 2 No. 1, 2013, pp. 18-26. doi: 10.5923/j.ijmee.20130201.03.
1. Quantitative Modeling of Solidification Behaviour of Microalloyed Steels (Module-1)
The precipitation behavior of microalloyed steel is influenced by solute redistribution from dendritic solidification of steel in the caster and the post-solidification cooling schedule.Dendritic solidification of the steel causes a concentration variation on a local scale, which is of the order of the interdendritic spacing. The interdendritric spacing ranges typically from ten to a few hundred µm, depending on the local solidification rates occurring in industrial slabs. During the solidification of steels, the dendrite spacing is empirically related to the local solidification time (the resident time between the liquidus and solidus) raised to an exponent ranging between 0.5 to 0.33; the faster the cooling rate, the finer the interdendritic spacing. If the steady state dendritic solidification is disturbed by fluid flow, the solute enriched liquid may be transported over a large distance, resulting in macro-segregation, notably centreline segregation. While macrosegregation can be prevented by the control of fluid flow in the caster, microsegregation is inherent in the mechanism of dendritic solidification.A quantitative model has been developed to predict the solute redistribution from dendritic solidification for multi-component micro-alloyed steels[1]. A finite difference method is used to predict the microsegregation at a given location (node point) in the slab. The diffusion equation is represented by the Crank-Nicholson implicit method of a finite difference equation. Local equilibrium is assumed at the solid–liquid interface. Multi-component phase equilibria are rigorously calculated from thermodynamic data for the case of Fe-Mn-C because of the large Mn concentration in the steel. The effects of other alloying elements are taken into account as a first order correction to this base. The slab thermal history used in the analysis is typical of an industrial caster. The algorithm results in the computation of the interdendritic microsegregation during freezing (including the effects of solid state diffusion during freezing) at stage-I and modifies this result by accounting for post-solidification homogenisation in the delta ferrite (stage-II), in the delta and gamma field (stage-III) and in the single phase gamma austenite region (stage-IV), see Fig. 1. Quantitative results of microsegregation in a typical high Nb, Ti bearing line pipe steel (0.03 C, 0.003 N, 0.09 Nb, 0.014Ti in wt%) solidifying at a location 5 mm from the slab surface with an interdendritic spacing of 70 µm are analyzed for the typical cooling schedule of the industrial caster. The solute redistribution of C and N exhibits a negligible variation in the concentration in the solid as a function of fraction solidified. The interstitial solutes exhibit negligible micro-segrgation, suggesting that the diffusion of the interstitial solutes is able to keep pace with the rate of advance of the solid-liquid interface during solidification. In contrast, the substitutional solutes give rise to significant microsegregation that persists to lower temperatures. Fig. 2 and 3 respectively show the redistribution of solute Nb and Ti as a function of interdendritic spacing. The reduction in the intensity of microsegregation as defined by Cmaximum/Cminimum from Stage-I to Stage-II, corresponding to the delta phase field (BCC structure) is far more significant than those of stage-III and stage-IV. The diffusion coefficients of Nb and Ti in the delta BCC phase are about 20 times greater than in those in the gamma phase (FCC structure). An increase in the temperature window of the delta phase field, corresponding to a decrease in the carbon content, brings about a significant homogenisation of the substitutional solutes. By comparison, the degree of homogenisation is not significant in austenite at a lower but wider temperature range corresponding to stage-IV. The effect of decreasing the carbon content in a given base chemistry was found to decrease the degree of microsegregation of Nb and Ti. The effect of lowering carbon is to increase the temperature window in the delta phase field, where significant diffusional homogenisation of substitutional solute occurs. Thus, a distinct advantage of low carbon design is to reduce the intensity of the microsegregation of the substitutional solutes, thereby promoting a more homogeneous microstructure. The reduced tendency of microsegregation in microalloyed steels with low carbon has been confirmed by Taira et al.[2] using mill data, which is consistent with the foregoing analysis. The microsegregation and precipitation models are used to design the base chemistry and temperature window required to prevent surface cracking during the bending and straightening of the slab. The base chemistry is designed to reduce the intensity of microsegregation using a low interstitial design. Ti additions are made to the stoichiometric requirement to tie up all the nitrogen at high temperatures as TiN. This is possible only if the nitrogen content of the steel is controlled to low levels (<40 ppm). A significant thermodynamic potential for NbCN in the temperature window corresponding to bend and unbend regions of caster is known to cause surface cracks. A low carbon design ensures less intensity of microsegregation of Nb, which allows high Nb design in the base chemistry.Thus, quantitative analysis of both the solidification and precipitation behaviour of a Ti-Nb microalloyed steel has underscored the scientific merits of low nitrogen as well as low carbon design in order to obtain sound slabs without surface cracking, which can be thermo-mechanically processed to obtain the required microstructure with enhanced strength and fracture toughness at low temperature.Summary: Quantitative modeling of solidification processing of slab shows that in order to obtain a homogeneous microstructure in the slab without surface cracks, the design of base chemistry warrants interstitial control. A low nitrogen design (30- 40ppm) is required coupled with stoichiometric Ti addition to tie up all nitrogen as TiN upstream ( 0.015%). A low carbon design (0.03 to 0.04%) is required to minimize microsegregation of Nb and Ti. A low carbon (0.03) design is coupled with high Nb (0.09%) addition which allows thermo-mechanical processing in high temperature window to gain increased productivity.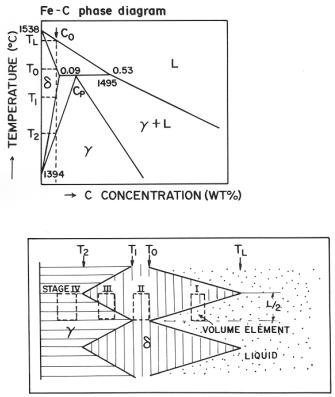 | Figure 1. A schematic diagram representing the various stages of microsegregation during solidification (Stage I) and post-solidification homogenization (Stages II, III and IV)[1] |
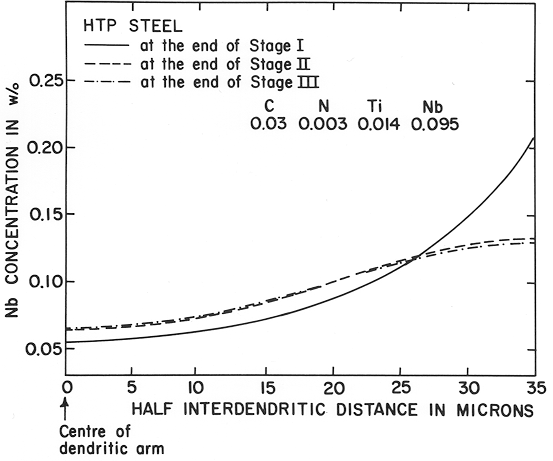 | Figure 2. The distribution of niobium as a function of interdendritic distance at the end of Stage I, II and III respectively[1] |
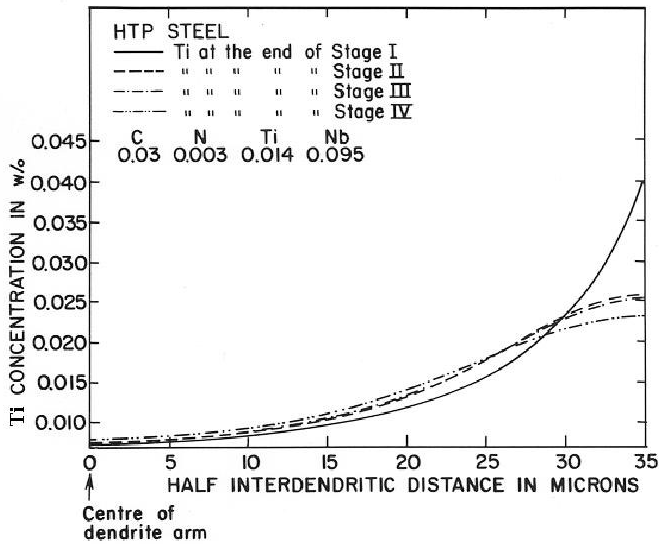 | Figure 3. The distribution of titanium as a function of interdendritic distance at the end of Stage I, II, III and IV (1200ºC) respectively[1] |
2. Thermodynamic Modeling to Predict Mole Fraction and Composition of Precipitates in Microalloyed Steels (Module-2)
Quantitative modeling based on Hillert and Staffanson’s regular solution model is used for predicting the equilibrium mole fraction and the microchemistry of the precipitates of the compound (TixNb1-x) (CyN1-y) as a function of base chemistry and temperature[3]. TEM characterization of precipitates of Ti-Nb microalloyed steel has confirmed that the precipitates are mixed Ti-Nb carbo-nitrides.These precipitates are described by sub-regular solution, in which the substitutional sites in cubic lattice are interchangeably taken by Ti and Nb, the interstitial sites are taken by N and C, with a certain amount of vacancy concentration as quantified by statistical thermodynamic approach. Thermodynamic model predictions were validated in HTP steel by TEM characterization of precipitates of samples equilibrated at different temperatures and quenched. Fig. 4 shows a typical plot of thermo-dynamic potential for precipitation of mixed carbo-nitrides of Ti and Nb occurring in low interstitial high niobium base chemistry (HTP). The high temperature precipitates are essentially mixed nitrides, enriched in TiN. The low temperature precipitates are essentially mixed carbides enriched in NbC. It is well known that while the kinetics of nitride precipitates are relatively rapid, the nucleation of NbC precipitates is sluggish and requires large undercooling even when their nucleation is aided by dislocations (strain induced). A quantitative understanding of the relative contribution of solute niobium, coherent and in-coherent precipitation of NbC on boundary mobility, recovery and recrystallization processes during hot rolling of niobium microalloyed steel is essential for microstructure control in thermo-mechanical rolling. This can be gained by quantitative modeling.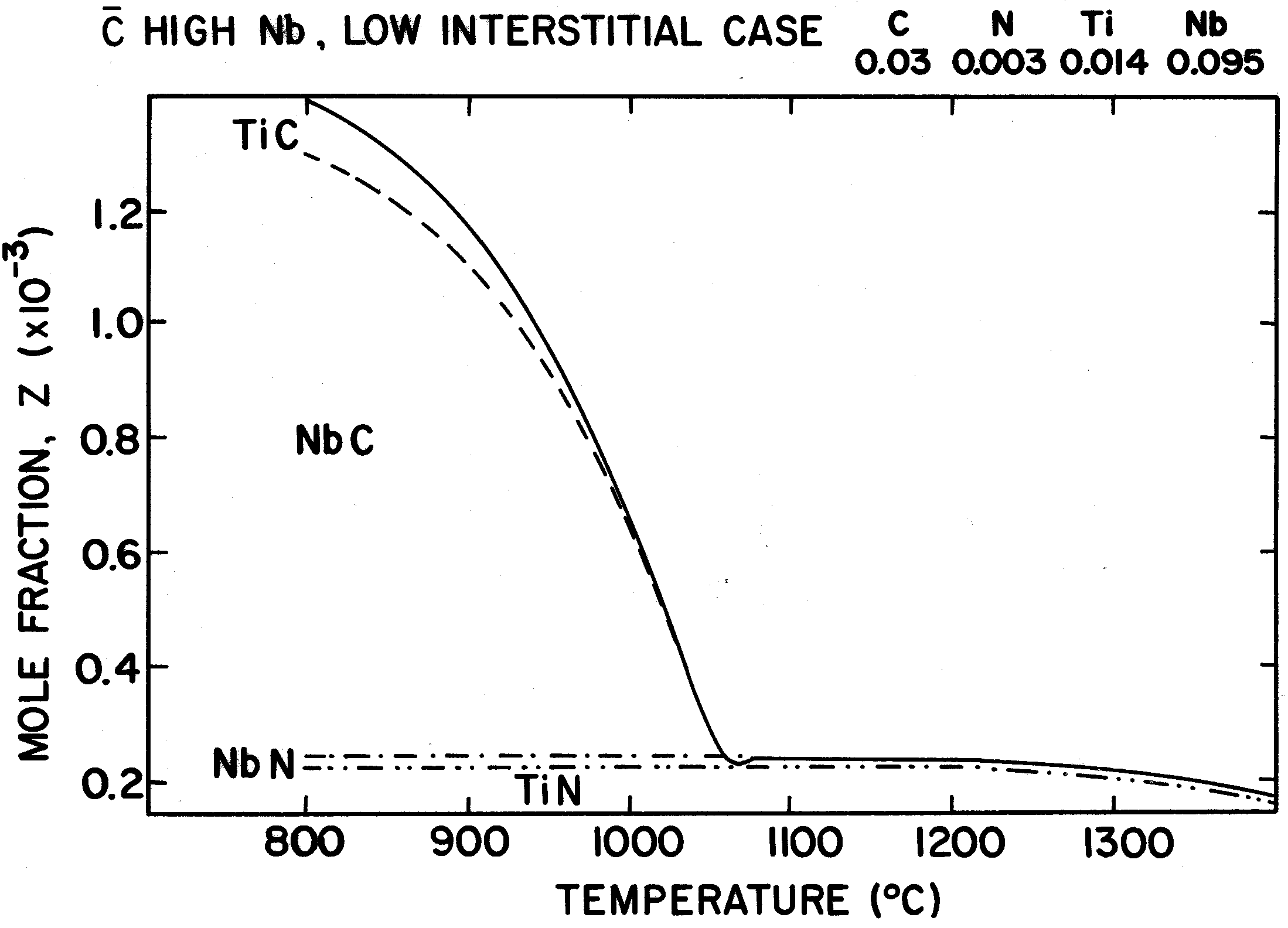 | Figure 4. Precipitate evolution curve for the high niobium low interstitial steel HTP. Thermodynamic potential for the precipitation of mixed carbides starts at 1060ºC |
Summary: Mixed carbo-nitride formation is predicted in Ti-Nb microalloyed steel. Mixed nitrides enriched in TiN are promoted that are stable at high temperature during high temperature excursion in HAZ region in high heat input welding. Strain induced precipitation of NbC is promoted during thermo-mechanical rolling to retard static recrystallization in finish rolling. Refinement of austenite grains before pancaking should be carried out by rough rolling in high temperature window where there is little thermodynamic potential for precipitation of mixed carbides enriched in NbC.
3. Refinement of Austenite Grain Size by Recrystallization during Rough Rolling and Prevention of Coarsening of Grains between Roughing and Finish Rolling (Module-3)
A typical rolling schedule with softening kinetics pass by pass during hot rolling of high niobium microalloyed steel (HTP) is given in Fig. 5. The model is based on quantitative database generated by Lutz Meyer and coworkers on softening kinetics based on total niobium. Rough rolling (the first 5 passes in Fig. 5) is carried out in a regime where there is no potential for thermodynamic precipitation of NbC or NbCN. Refinement of austenite grains by breaking down the as-cast structure is brought about by static recrystallization [4]. While the models for recrystallization process tend to focus on percentage softening, the critical information required is number density and grain size distribution of austenite grains, for which one still has to rely on actual experimental data-base. This requires metallographic techniques to reveal prior austenite grains. Modeling of recrystallization nucleation kinetics of austenite is still at a stage of infancy.The recent trend is to introduce another intermediate processing step in between roughing and finish rolling, where austenite grain size can be significantly refined by accelerating the kinetics of recrystallization nucleation. Though the modeling is yet to capture this aspect fully, experimental results on austenite grains are presented that demonstrate this concept[5].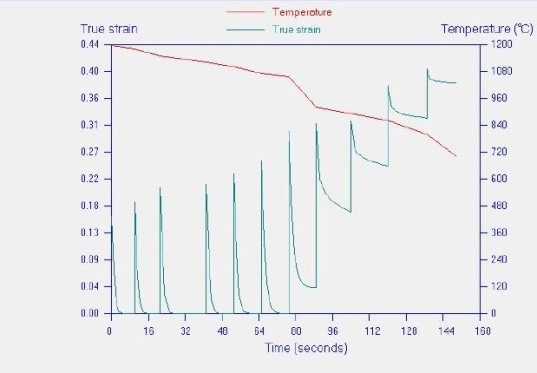 | Figure 5. Softening kinetics of high niobium microalloyed steel for a typical hot rolling schedule comprising of roughing ( first six passes) and finish rolling (last 5 passes) |
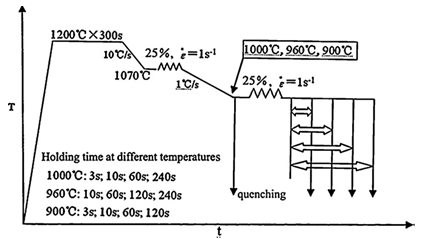 | Figure 6. A schematic of experimental rolling simulation investigations on niobium microalloyed steel |
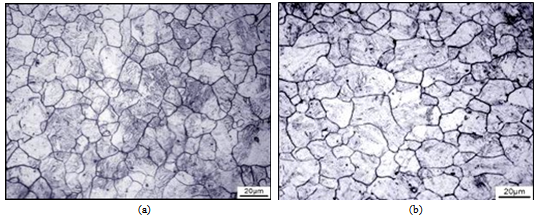 | Figure 7. a and b: Austenite grains quenched at the end of 3 s (5a) and 60 s (2b) respectively after deformation at 1000oC |
A metallographic technique was developed to reveal the prior austenite grain size in low interstitial- high Nb microalloyed steel sample interrupted by quenching at different stages during static recrystallization. This allowed time evolution of austenite grain size and distribution to be determined after single and multi-pass deformation. Conventional double compression test, stress relaxation test, plane strain experiments were also used along with the new etching technique of prior austenite grain to investigate static (SRX) and dynamic (DRX) recrystallization behavior of low interstitial, high Mn ( >1.5%) and high Nb (0.1wt%) pipeline steel[6,7].After single pass deformation of 25% reduction at 1070oC, the austenite grain size coarsened to 80 microns upon cooling at 1K/s to 1000oC. Upon 25% reduction at 1000oC, steel exhibited uniform grain size of 13 microns at the end of 3 seconds. Austenite grains did not coarsen for 60 s, see Fig. 6, 7a, and 7b. The coarsening kinetics of austenite was relatively slow up to 240s. The effect of prior deformation is to accelerate recrystallization nucleation kinetics, which can be related to the number density of austenite grains. More importantly, solute niobium was effective in retarding the grain coarsening of austenite at 1000oC compared to 1070oC. These two findings turned out to be the key to introduce an intermediate processing step in optimizing the rolling schedule to refine the austenite grains before pancaking in optimized rolling of HTP for X-80 referred to as OHTP process in a modern mill to roll 5 meter wide plate of thickness up to 25 mm[5]. Analysis of basic science aspects of recrystallization nucleation kinetics shows that the dislocation density is the driving force for recrystallization nucleation, which increases with applied strain. In consequence, the critical radius for recrystallization decreases, which, in turn, decreases the incubation time for recrystallization nucleation.Summary: Refinement of austenite grain size by static recrystallization is the key to refining austenite grain size before pancaking.The as-cast austenite grain which is between 800 to 1500 microns can be refined to less than 25 microns by static recrystallization.A large pass reduction at the end of roughing will increase the nucleation sites for static recrystallization, thereby reducing the austenite grain size in the range of 10-15 microns.
4. Prevention of Grain Coarsening of Austenite before Pancaking in Finish Rolling (Module-4)
The fine austenite grains will coarsen by the driving force, determined by reduction in surface energy accompanying coarsening of grains. The coarsening kinetics of grain refined austenite is a significant problem under industrial processing, which is examined in further detail by using quantitative modeling.
4.1. Modeling of Coarsening Kinetics of Austenite
The driving force for grain coarsening is the reduction in surface energy associated with grain boundary, expressed as: | (1) |
The boundary mobility for plain C-Mn steel as determined by Zhou et al.[8] is: | (2) |
This is modified to incorporate solute drag effect which was modeled using Cahn’s equation[9] | (3) |
where, | (4) |
and
refer to the intrinsic grain boundary mobility of the C-Mn steel and the concentration of Nb in solution respectively,
is the grain boundary width
is the number of atoms per unit volume,
is the solute-boundary binding energy and D is the trans-interface boundary diffusion which is equal to twice the bulk diffusion coefficient of Nb in austenite[10].
Finally the grain coarsening is expressed as: | (5) |
where
and
are the initial and final grain size corresponding to initial and final time
and
respectively. According to model predictions, the effect of adding 0.09 wt% Nb in retarding the coarsening kinetics of plain Fe-Mn-C steel ( solute drag effect of Nb) is more pronounced at 1000oC compared with any higher temperature (>1100oC), which is consistent with the experimental observations. Even without Nb, diffusion is too low at low temperature (<900oC) to cause any significant coarsening. The effect of Nb addition in retarding the coarsening kinetics of austenite is plotted for a starting austenite grain size of 15 microns in Fig. 8. There is significant potential for grain coarsening of austenite between the end of roughing and start of finish rolling, which can be controlled by combining high solute Nb with rapid cooling between roughing and finish rolling.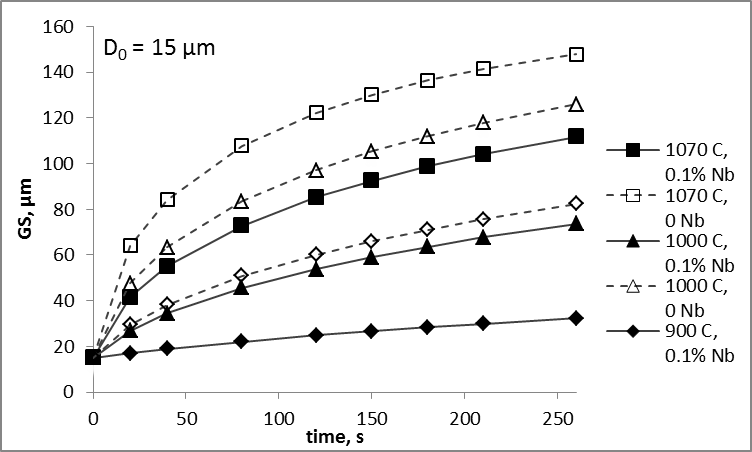 | Figure 8. Effect of 0.1%Nb on grain coarsening at different temperatures and time |
The model predictions of austenite grain size at entry to finish rolling are summarized in Fig. 9 for typical case histories. In order to achieve a target austenite grain size of 25 microns, high solute niobium and rapid cooling rate have to be coupled for a typical temperature window of 1000-910oC for a typical hot strip mill processing.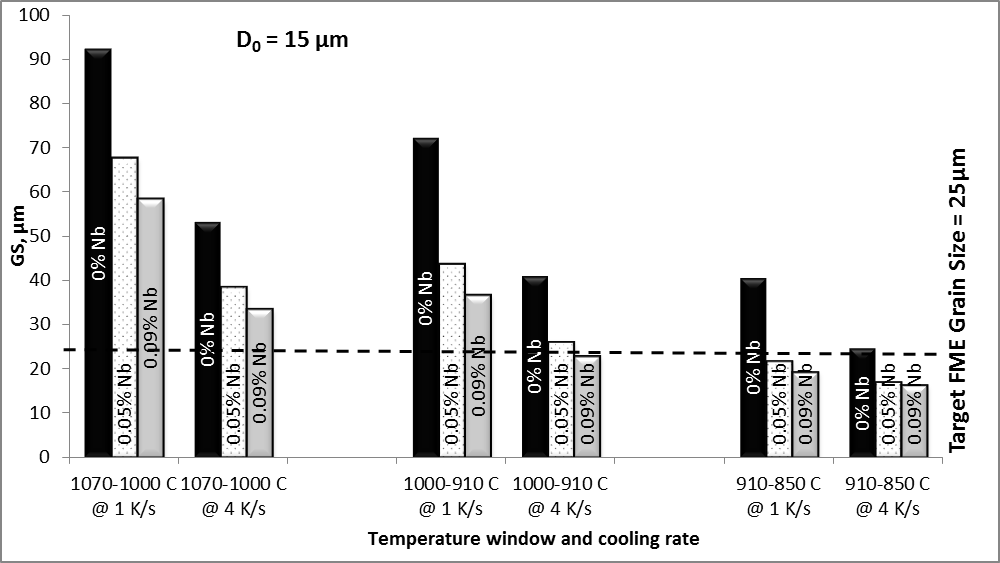 | Figure 9. Effect of cooling rate, temperature window and %Nb on grain coarsening kinetics. The starting GS= 15 µm |
Summary: High solute niobium and rapid cooling rate between roughing and finishing (1050-910oC) are shown to the key parameters to minimize grain coarsening of austenite. At low temperature (<900oC), grain coarsening is not a significant problem, which is used to advantage during pancaking of austenite in finish rolling of strips, where there is inadequate time for Zener pinning of precipitates.
5. Recrystallization Control for Strain Accumulation in Finish Rolling (Module-5)
Quantitative model for time evolution of strain induced precipitation of NbC was developed by Dutta, Palmiere and Sellars[11] and strain induced precipitate interaction with recovery and recrystallization after single pass deformation was quantitatively modeled by Zurob et al.[12]. Attempts have been made to refine the site saturation assumption for recrystallization nucleation in single pass deformation. The model is being refined to capture fresh continuous nucleation of strain induced precipitation with each new pass in multi-pass rolling. Zurob’s model captures time evolution of recovery, which decreases the driving force for recrystallization. Precipitates nucleating on dislocations pin the dislocations which impedes the recovery until coarsening unpins the dislocations. Zurob’s analysis[12] has confirmed that it is only at relatively large time when the precipitate volume fraction is large, Zener effect is effective in pinning the grain boundary, and the recrystallization is effectively retarded.Summary: Time evolution of strain induced precipitation occurs within seconds of deformation pass but time evolution of growth of precipitates takes tens of seconds before the precipitate volume fraction is adequate to exert significant pinning pressure on boundary to retard recrystallization.Solute drag due solute niobium is essential to prevent boundary break away and prevent potential for abnormal grain growth.
5.1. Prevention of Mixed Grain Size due to Rolling in Partial Static Recrystallization Regime
Physically based models are developed based on time evolution of strain induced precipitation and interaction of Zener drag and solute drag with recrystallization. Experimental results have confirmed the window of partial static recrystallization is not fixed. Temperature of no recrystallization (TNR) is sensitive to both chemistry and processing parameters, which means that there is no fixed TNR for HTP but it is also sensitive to mill processing parameters[4]. Pass No-6 in Fig. 5 exhibits partial recrystallization. The experimental results on the effect of strain on partial static recrystallization window are given in Fig. 10. It is imperative to avoid rolling in partial static recrystallization in order to avoid mixed grain size.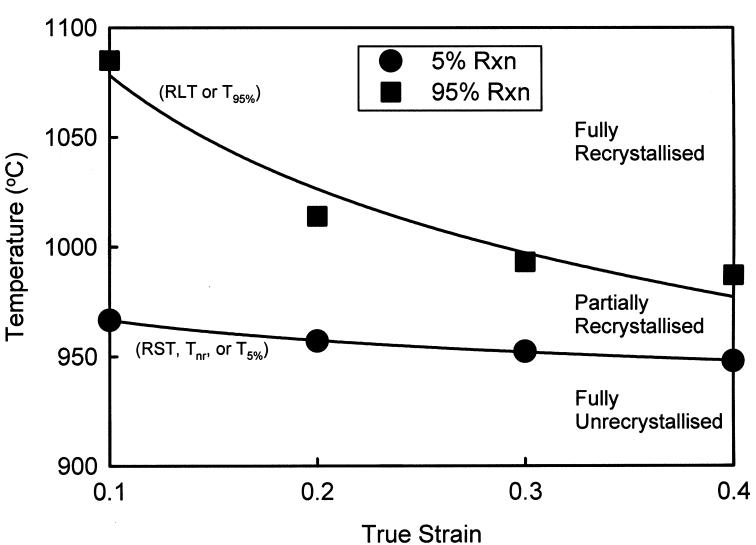 | Figure 10. Map showing the start and finish of recrystallization as a function of temperature and strain[4] |
Summary: Rolling should be avoided in partial static recrystallization zone. Otherwise, mixed grain size would occur, which will impair toughness as measured by DWTT results.Roughing should be done well above partial static recrystallization regime for a given chemistry and austenite conditioning. Finish rolling should start below temperature of partial static recrystallization region in the region of no recrystallization. This window is sensitive to both chemistry and mill rolling parameters!
5.2. Prevention of Mixed Grain Size due to Partial Dynamic Recrystallization
In finish rolling, large strain accumulation is required without any partial dynamic recrystallization at any stage[13]. Modeling is used to predict the strain accumulation from pass to pass without exceeding the critical strain for dynamic recrystallization.In strip rolling of HTP, there is inadequate time for adequate Zener drag to develop, which implies that there is significant potential for partial dynamic recrystallization to occur unless the temperature window is adequately lowered[12]. Experimental results have confirmed that mean flow stress can used to monitor and control the time-temperature-deformation schedule of finish rolling to prevent partial dynamic recrystallization, see Fig 11 and 12.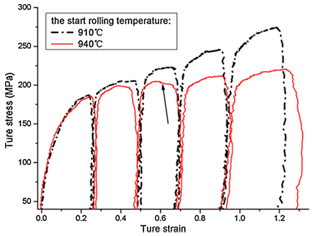 | Figure 11. Map showing the drop in mean flow stress due to recrystallization[6] |
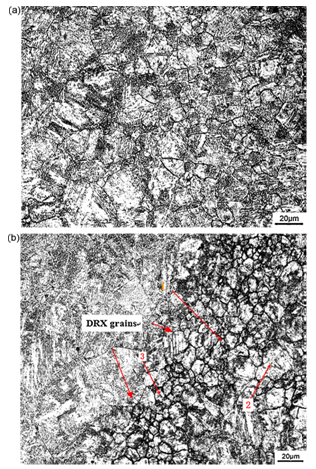 | Figure 12. Micrographs of the two cases shown in Fig. 11 demonstrating that the drop in flow stress is due to dynamic recrystallization[6] |
Summary: Partial dynamic recrystallization will give mixed grain size and therefore should be avoided. Increase in mean flow stress from pass to pass can be used for on-line monitoring to prevent partial dynamic softening during mill rolling.
6. Structure-property Correlation Studies (Module-6)
While the morphological microstructure control is used to enhance toughness associated with resistance to ductile fracture, the competition from brittle fracture as manifested by decrease in percentage shear area in DWTT is controlled by density and dispersion of crystallographic high angle boundaries[14], see Fig. 13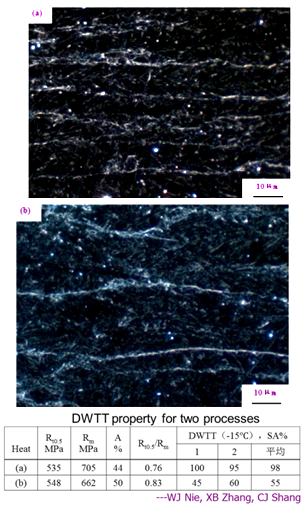 | Figure 13. Micrographs showing the effect of Sv on DWTT |
6.1. Control of competition from brittle fracture
Studies based on EBSD characterization of crystallographic high angle boundaries in higher grade line pipe steels have confirmed that control of density and dispersion of crystallographic high angle boundaries is essential to control ductile to brittle transition temperature[15]. Crystallographic high angle boundaries act as microcrack arresters that prevent brittle crack initiation. Acicular ferrite structure with high density and dispersion of high angle boundaries can be promoted in niobium microalloyed steel. The domain size is determined by high density (number count) of high angle boundaries. This, in turn, is found to be a strong function of prior austenite grain size before pancaking as well as the degree of pancaking. A large strain accumulation in a relatively fine grained austenite when accelerated cooled through the transformation to promote coherent transformation to form acicular ferrite, and interrupted and held well above martensite start temperature to complete the transformation is shown to be the key to obtain the required domain size in higher grade line pipe steels. A coarse austenite grain exhibits a low density of high angle boundaries within the austenite grain. The large interspacing between high angle boundaries is weak zone to resist brittle fracture initiation, see Fig. 14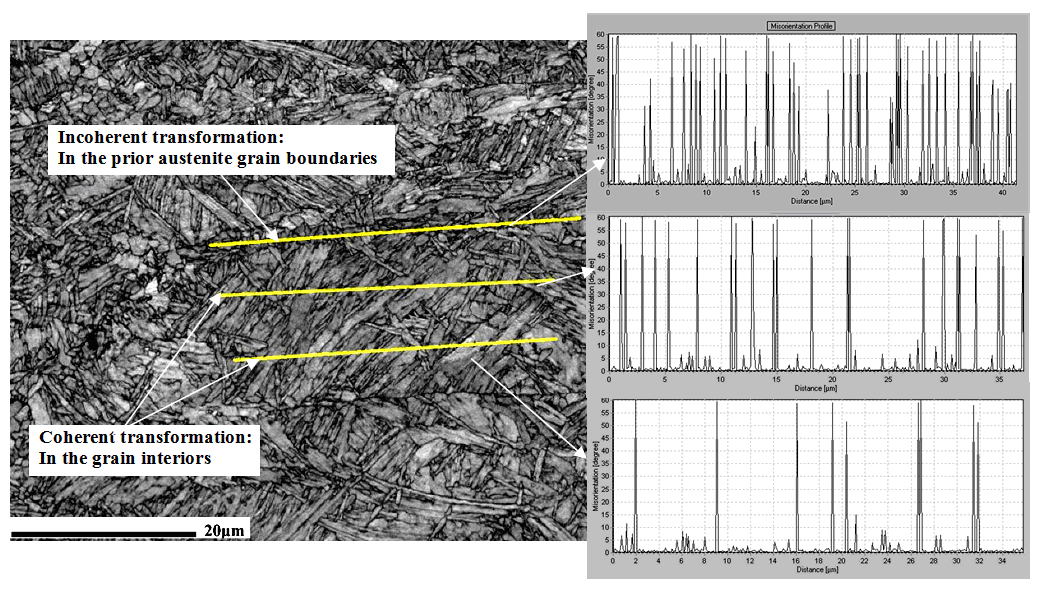 | Figure 14. Micrographs showing the density and dispersion of high angle grain boundaries |
The effect of prior austenite grain size on the density of high angle boundaries in austenite is illustrated in Fig. 15 X-120 exhibits typically a pancaked austenite thickness of 6 microns, which implies that for 75% total reduction the austenite grain size before pancaking is less than 20 microns.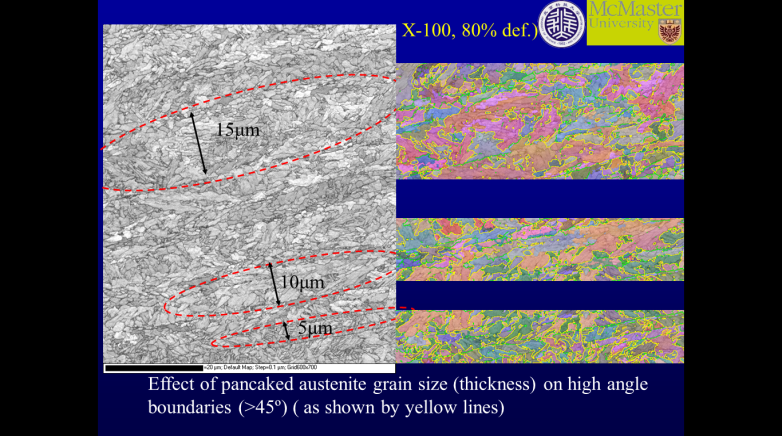 | Figure 15. Effect of pancaked austenite grain size on high angle grain boundaries |
High niobium steel has turned out to be a cost effective option over V-Nb microalloyed grade with high Mo to produce X100.Summary: Control of density and dispersion of high angle boundary is essential to prevent competition from brittle fracture, that lowers ductile to brittle transition temperature. Acicular ferrite structure is promoted by high niobium, which gives high density and dispersion of high angle boundaries. Refinement of austenite grains before pancaking, large strain accumulation and high cooling rate are key parameters that influence density and dispersion of high angle boundaries. High strength austenite transformed at low temperature increase the density and dispersion of crystallographic high angle boundaries.
7. Conclusions
A modular approach is used to control upstream processing of austenite with downstream transformation product, to which strength and fracture properties are related in high niobium microalloyed steel of HTP design. The evolution of HTP as the workhorse for line pipe steel owes its success to the concept of product-process integration by “through process modeling” approach.
ACKNOWLEDGEMENTS
The authors wish to thank CBMM- Brazil, NSERC- Canada and Chinese Government Scholarship agencies for funding support. Research contributions from Prof. C.S. Shang, Dr. Miao Chengliang and You Yang of USTB, China are gratefully acknowledged.
References
[1] | S.V.Subramanian et al., Technology and Applications of HSLA Steels (Beijing), (Materials Park: ASM International, 1985), p. 151. |
[2] | T.Taira et al., Technology and Applications of HSLA Steels (Philadelphia), (Metals Park: ASM, 1983), p. 723. |
[3] | S.V.Subramanian, J.D.Embury and G.R.Purdy, “Solidification and Precipitation evolution analyses for Ti-Nb bearing line pipe steels” Proc. Int. Conf. Pipe Technology, Rome Nov 1987 AIM/CEC Publication, p. 153-170. |
[4] | E.J.Palmiere, C.M.Sellars, and S.V.Subramanian, “Modeling of thermomechanical rolling”, The International Symposium Niobium 2001, AIME-TMS, Dec. 2-5, 2001, p. 501- 526, Orlando, U.S.A |
[5] | Nie, W. et al., Enhancing the Toughness of Heavy Thick X80 Pipeline Steel Plates by Microstructure Control, Adavanced Materials Research Vol, 194-196 (2011) p 1183. |
[6] | Miao, C.L., et al. Materials Science and Engineering: A, 2010. 527(18–19): p. 4985. |
[7] | Shang, C. and C. Miao, Refinement of Prior Austenite Grain in Advanced Pipeline Steel, Advanced Steels, 2011, Springer Berlin Heidelberg. p. 341. |
[8] | Zhou, T., R.J. O’Malley, and H.S. Zurob. Metallurgical and Materials Transactions A, 2010. 41(8): p. 2112. |
[9] | Cahn, J.W. Acta Metall Mater, 1962. 10(9): p. 789. |
[10] | Zurob, H.S., et al. Acta Mater, 2002. 50: p. 3075. |
[11] | Dutta, B., E.J. Palmiere, and C.M. Sellars, Acta Mater, 2001. 49: p. 785. |
[12] | Zurob, H.S., et al. ISIJ Int, 2005. 45(5): p. 713. |
[13] | S.V.Subramanian and H. Zou, Processing, Microstructure and Properties of Microalloyed and Other Modern High Strength Low Alloy Steels (Pittsburgh), (Warrendale: ISS-AIME, 1991), p. 23. |
[14] | S.V.Subramanian et al. Microalloyed Bar and Forging Steels (Hamilton), M. Finn Ed., (Montreal: CIM, 1990), p. 120. |
[15] | S.V.Subramanian et al, Microstructural development for brittle fracture control in Nb microalloyed line pipe steel. HSLA Beijing 2011, june 1st. |