T. Sreenivas , R. R. Venkatkrishnan
Mineral Processing Division, Bhabha Atomic Research Centre, AMD Complex, Begumpet, Hyderabad, 500 016, India
Correspondence to: T. Sreenivas , Mineral Processing Division, Bhabha Atomic Research Centre, AMD Complex, Begumpet, Hyderabad, 500 016, India.
Email: |  |
Copyright © 2012 Scientific & Academic Publishing. All Rights Reserved.
Abstract
Studies on pre-concentration of molybdenum values from a primary molybdenum ore deposit located in Harur of Dharmapuri district, Tamilnadu were carried out by physical beneficiation techniques. Inspite of being a primary deposit, the Mo content in the ore is very low, being 0.06% only. Mo is present as molybdenite (MoS2) and the other sulfide minerals in the ore are pyrite, galena and traces of chalcopyrite. Quartz constitues the bulk gangue phase. Based on detailed mineralogical studies, two alternative process schemes, a ‘multi-stage flotation route’ and a ‘flotation cum gravity separation’ route were investigated. The “flotation - gravity” separation route gave a final Mo concentrate analyzing Mo 44.21%.
Keywords:
Molybdenum, Primary molybdenum, Flotation, Molybdenite
Cite this paper:
T. Sreenivas , R. R. Venkatkrishnan , "Preconcentration of Molybdenum from a Low-grade Primary Mo Ore by Physical Beneficition", International Journal of Metallurgical Engineering, Vol. 1 No. 5, 2012, pp. 96-101. doi: 10.5923/j.ijmee.20120105.05.
1. Introduction
Molybdenum is a versatile metallic element used in variety of applications ranging from those of strategic nature to general industrial purposes. The special properties of molybdenum bearing alloys like high-temperature resistance, non-corrosive nature and relative strength makes it a critical metal in nuclear applications[1,2,3]. Owing to its strategic applications determined efforts are being made in India to develop process routes for the recovery of this metal from various resources. At present majority of the requirements of molybdenum, amounting to about 940 tonnes, are met through imports only, either in the form of roasted concentrate, oxide or as ferro-molybdenum[4].The total molybdenite resources in India are reported to be about 12640 tonnes[4,5]. They are present predominantly in three states namely, Tamilnadu, Madhya Pradesh and Karnataka. Molybdenum deposits also occur in copper porphyries of Singhbhum Shear Zone (SSZ) in Jharkhand. The Rakha copper deposit in SSZ assays 45 to 48 ppm Mo. The Malanjkhand copper deposit in Madhya Pradesh contains 0.04% recoverable Mo. The lead-zinc sulphide deposit in Dariba-Rajpura, Rajasthan also contains molybdenum. The multi-metal deposit at Umpyrtha in Khasi and Jaintia Hills, Meghalaya, reportedly contains molybdenum in association with copper, lead and tungsten. Occurrence of a low-grade primary molybdenum ore deposit in Harur of Dharmapuri district, Tamilnadu is also well known[6]. The ore reserves in Harur is about 1.84 million tonnes with an average Mo content of 0.098% at 0.03% as cut-off grade. This deposit is located in Harur – Alangayam area of Velampatti south block in the southern end of the Harur-Uttangarai zone. Epidote – hornblend gneiss is the dominant host rock type and is sporadically exposed with conformable bands of quartzo-felspathic gneiss and enclaves of meta-gabbro and metal pyroxenite. Quartz veins with associated mineralisation cut across the formation and form low north-south trending reefs in the central and southern parts of the block. Within the mineralised shear zone molybdenum occurs as mineral molybdenite in the quartz vein as well as in the sheared and sericitised gneiss on either side of it. It occurs as fine flakes, granular aggregates and disseminated grains occupying hair line fractures in the quartz veins.Though extensive beneficiation and metallurgical extraction work was reported on molybdenum resources of Jharkhand [7], similar work on the newly discovered Harur deposit is scanty. This paper gives details of bench-scale and pilot-scale beneficiation studies carried out on the Harur molybdenum ore.
2. Experimental
2.1. Materials
The complete mineralogical composition of a representative ore sample is given in Table 1 and the partial chemical composition in Table 2. Molybdenite is the only molybdenum mineral and pyrite is the predominant sulphide mineral. Other sulphides such as chalcopyrite and galena occur in minor quantities. Quartz, feldspar and sericite constitute the major gangue. Chemically the sample analyses Mo 0.06%, Cu 0.0055% and Fe 3.8%. All the chemicals used in the studies like potassium isopropyl xanthate (KIPX), soda-ash, lime, sodium silicate, starch, potassium dichromate and pine oil were of commercial grade. The experiments were conducted with water analyzing CaO 135ppm and MgO 90 ppm.Table 1. Mineralogical Composition of Harur molybdenite Ore  |
| |
|
Table 2. Partial Chemical Composition of Harur Ore 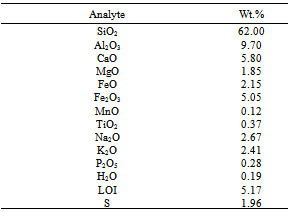 |
| |
|
2.2. Methods
The “as-received” ore was stage crushed in jaw and roll crushers to 25 mm size and representative lots were sampled for further size reduction in rod-mill to desired particle size. The pre-concentration studies were carried out on ground ore using the froth flotation and gravity separation techniques. The bench scale flotation tests were conducted on laboratory Denver sub-aeration flotation cell. The procedure followed for rougher flotation consisted of (i) conditioning of the ground ore with pre-defined quantity of dispersant (sodium silicate) for 3 minutes at 50% solids by weight at agitation rate of 1500 rpm, (ii) addition of collector reagent (KIX) followed by conditioning for pre-set time duration, (iii). re-pulping the reagentised slurry to 35% solids and addition of frother (pine oil), (iv) opening of the aeration valve and collection of froth for predefined time at reduced impeller speed (1200 rpm). The gravity separation tests were carried out on Mozley Mineral Separator (UK) and Bartles Mozley Shaking Table. The metallurgical balance is based on wet chemical analysis of Mo, Pb, Fe, S and other desired species in ore and stream products. Benificiation experiment was repeated thrice and only the mean value was considered for data evaluation.  | Figure 1. Flotation response of Harur molybdenite ore as a function of grind size. Potassium isopropyl xanthate 0.25 g/kg, sodium silicate 0.075 g/kg ,pine oil, flotation time 4.5mimutes ,pH 9.2 |
3. Results and Discussion
Molybdenite is a naturally hydrophobic sulphide mineral [1]. It is floated using simple hydrophobic chain extender type collector reagents like kerosene oil, furnace oil, creosotes or pine oil[8,9]. However, the oil type collectors are unselective in nature resulting in indiscriminate flotation of both valuable and other gangue. Unlike them the alkyl xanthate reagents are known for their high selectivity for sulphide minerals. The process strategy adopted in the present investigations consists of flotation of all the sulphide minerals as bulk float with alkyl xanthates, followed by separation of individual minerals either by flotation or gravity separation. The possibility of using gravity separation exists due to large specific gravity difference between molybdenite and galena.
3.1. Bench Scale Test Work - Parametric Variation Studies for Bulk Flotation of Sulfide Minerals
3.1.1. Mesh-of-grind
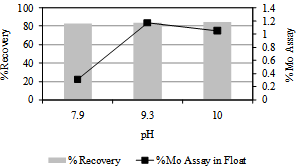 | Figure 2. Flotation response of Harur molybdenite ore as a function of pH. Potassium isopropyl xanthate 0.25 g/kg, sodium silicate 0.075 g/kg , pine oil, grind size 46% by weight finer than 200 #, flotation time 4.5mimutes, pH 9.2 |
The crushed ore was ground for different time intervals to obtain mill products with varying particle sizes, ranging from 33% to 54% by weight passing 200#. The results of the flotation experiments on feed ground to different sizes are given in Figure 1 along with the experimental conditions followed. The recovery of molybdenum values in the float fraction was practically invariant with the fineness of grind, in the range of 80-83%. Nevertheless minor variations in the Mo assay of the float products were noticed at different grinds studied. The float grade was 1% and 1.08% Mo when the grind was 33 and 46 % by wt finer than 200# and it dropped to 0.78% Mo for feed having 54% by weight in –200# fraction. Microscopic analysis of various float fractions indicated presence of entrained slimes in the float when the particle size of the feed is finer. 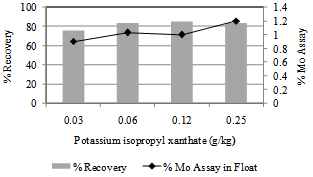 | Figure 3. Flotation response of Harur molybdenite ore as a function of collector-Potassium isopropyl xanthate dosage, sodium silicate 0.075 g/kg , pine oil, grind size 46% by weight finer than 200#, flotation time 4.5mimutes , pH 9.2 |
3.1.2. Effect of Pulp pH
The flotation response of molybdenite as a function of pulp pH was studied at insitu pH, about 7.9 and, at two other higher levels, 9.3 and 10.0. The pulp pH was modified using appropriate dosages of soda ash. Results of the flotation tests are given in Figure 2. At insitu pH, the flotation response was indiscriminate, both molybdenum and other gangue minerals reported in the float resulting float Mo assay of 0.38%. The flotation selectivity improved when the pulp pH was in the range of 9.0 to 10. In this range the float products analysed about 1.0% Mo with nearly 85% recovery. The pattern of selectivity observed in Figure 2 is in agreement with earlier reported results. Dixanthogen is the principle collector species imparting hydrophobicity to pyrite or galena[9]. In alkaline conditions these minerals become less hydrophobic due to (i) hydrolytic decomposition of xanthate collectors leading to reduced concentration of dixanthogen for sorption on mineral surface and (ii) formation of hydrophilic metal hydroxides on sulphide minerals.
3.1.3. Effect of Collector Dosage
Optimization of the collector dosage was carried out by varying of potassium isopropyl xanthate dosage from 0.03 g/kg to 0.25 g/kg of ore. Results are illustrated in Figure 3. Both the recovery and the grade of float product was relatively lower, 76% and 0.9%Mo respectively, when the collector dosage was 0.03g/kg. The recovery increased to 84% with simultaneous improvement in the float grade to Mo 1.03% upon increasing the KIPX dosage to 0.06g/kg. Flotation tests carried out at 0.12g/kg and 0.25g/kg did not yield any further improvements either in the grade or in the recovery of Mo in the float fraction.
3.1.4. Effect of Nature and Dosage of Modifier
As the flotation of molybdenite was more selective at alkaline pH, two different modifiers were investigated for regulation of pulp pH to about 9.5. They are commercial grade sodium carbonate (soda ash) and calcium oxide (lime)[10,11]. Amongst the two modifiers tested, soda ash gave better quality floats (Table 3).Addition of 1 g/kg of soda ash to the flotation pulp gave float product assaying 1.03% Mo assay with 84% recovery. Unlike this, the performance with lime was poor. The Mo assay in the float was mere 0.24% and the recovery being about 74% when 0.3g/kg of lime was added to the flotation pulp. The absence of selectivity with lime reagent could be due to activation of siliceous gangue during flotation due to sorption of surface active CaOH+ species [9,10,11]. Table 3. Effect of nature and dosage of pH modifier. KIPX 0.12 g/kg, sodium silicate 0.075 g/kg, pine oil 2 drops, pH 9.-10, conditioning time 15 minutes and flotation time 4.5 minutes |
| Modifier (g/kg) | Float | Wt. % | Mo % | Dist. % | Soda ash 1g/kg | 4.9 | 1.03 | 84.0 | Soda ash 2g/kg | 5.6 | 0.98 | 83.7 | Lime 0.3 g/kg | 17.2 | 0.24 | 71.4 | Lime 0.3 g/kg | 15.4 | 0.28 | 71.8 |
|
|
3.1.5. Kinetics of moly flotation
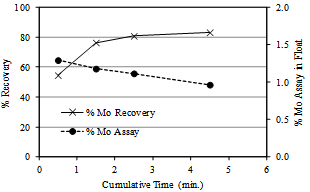 | Figure 4. Flotation kinetics of Harur molybdenite ore. Potassium isopropyl xanthate dosage 0.25g/kg, sodium silicate 0.075 g/kg ,pine oil, pH 9.2 |
The kinetics of flotation of molybdenite during rougher flotation stage is illustrated in Figure 4. About 80% of Mo values were recovered in the float in the initial 2.5 minutes of flotation time. Increasing the froth collection time beyond 2.5 minutes resulted in dilution of the float assay due to collection of slimy gangue. For instance the float collected in a typical experiment with feed of grind size 46% by weight finer than 200# gave float assaying 1.29% Mo in the initial 0.5 minute, 1.2% Mo at 2.5 minutes flotation time and the cumulative grade at the end of 4.5 minutes was 0.96%. The froth ceased after 4.5 minutes of flotation time. The recovery profile too indicates almost insignificant improvement, about 3%, during the flotation time interval of 2.5 minute to 4.5 minute.
3.2. Separation of Sulfide Minerals from Combined Float
3.2.1. Multi-stage Flotation Scheme
The three sulphide minerals present in the combined float – molybdenite, pyrite and galena, were separated from each other by multi-stage flotation comprising of (i) regulation of pulp pH to 10 using soda ash for the depression of pyrite mineral followed by (ii) differential flotation of galena and molybdenite. The differential flotation in step (ii) was carried out by using depressant for galena. Figure 5 shows the Mo assay and recovery of the float product obtained in various stages flotation.The Mo content in the combined sulfide minerals float at bulk flotation stage was 1.03%. The flotation stages aimed at pyrite depression enhanced the Mo content in the float to about 18% after two stages of plain cleaning. The mineralogical composition of the float obtained after pyrite depression indicate dominant presence of galena, about 52% by weight stage-wise, 17% of pyrite and 25% of molybdenite. 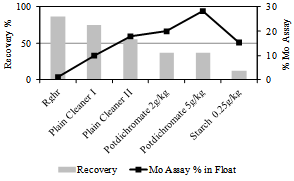 | Figure 5. Grade and recovery of Mo during various flotation stages |
The differential flotation of galena and molybdenite was carried out by adding two well known depressants for galena namely, potassium dichromate and soluble starch[12]. Potassium dichromate was added in solution form at two dosage levels–2 & 5 kg/ton (stage level dosages). The depression of galena was relatively better when the dichromate dosage was 5 kg/ton in comparison to that noticed upon addition of 2kg/ton. The Mo content of float improved to 28.2% at this higher dosage. No tests were carried out at further higher level dosages of dichromate due to the adverse toxic impact of chromium ions on the environment. Attempts made with starch depressant, a non-toxic modifier for galena, resulted in depression of both molybdenite and galena. Starches are known to adsorb on minerals primarily by weak hydrogen bonds and vander Wal bonding. The hydrophobic surface of molybdenite enhanced the affinity for starch leading to depression of molybdenite along with galena.
3.2.2. Flotation cum Gravity Separation Scheme
Taking advantage of the significant specific gravity difference between molybdenite (sp.gr. 4.7 – 5.0) and galena (sp.gr. 7.5), the separation of the two sulfide minerals in the intermediate grade moly float obtained after pyrite depression was carried out on Mozley Mineral Gravity Separator. The results of these experiments are given in Table 4. Table 4. Separation of molybdenite and galena on Mozley Mineral Gravity Separator, a). Flat Tray Setting: Amplitude 101.6 mm, Frequency 80 rpm, Slope 44.5 mm, Irrigation water 2 lpm |
| Stream | Flat tray Setting | Mo% | Pb% | Mo Dist.% | Pb Dist% | Conc.Tails | (a) | 34.22.10 | 17.057.4 | 91.708.3 | 16.883.2 | Conc.Tails | (a) | 45.6709.08 | 6.347.9 | 49.650.4 | 2.597.5 | b). Flat Tray Setting: Amplitude 101.6 mm, Frequency 100 rpm, Slope 44.5 mm, Irrigation water 2 lpm | Conc.Tails | (b) | 32.051.42 | 11.164.7 | 94.805.2 | 12.487.6 |
|
|
Apparently the separation was better on gravity separators than by flotation. The contamination of galena in molybdenite concentrate depends on the target recovery. The best results were obtained on a flat tray operated at a frequency of 80 rpm. The moly rich concentrate obtained with flat tray operated at a frequency of 80 rpm analysed 45.67% Mo and 6.7% Pb with about 50 and 2.5% distribution respectively.
3.3. Integrated Flowsheet - Large-scale Experiment
The generic flowsheet followed in the large-scale studies consists of crushing–grinding–bulk flotation of sulfide minerals followed by differential separation of molybdenite from pyrite and galena (Figure 6). Bulk flotation comprising of the rougher and scavenger, was carried out in Dorr-Oliver No.15 cells and differential flotation in No.12 cells using: collector - potassium isopropyl xanthate collector (0.06 g/kg), dispersant – sodium silicate (0.075g/kg) and frother – pineoil, at pH 9.2.The kinetics of flotation of molybdenite in the batch scale experiments indicated scope of floating about 85% of molybdenum values in 5 minutes flotation time. In the pilot-plant scale tests a scale-up factor of 2 was taken for residence time of pulp in the flotation cell during bulk sulfides flotation. About 90% of the molybdenite values were concentrated in the rougher float analysing 1.12% Mo. The mass rejection was about 95% by weight carrying about 10% of moly values. During the plain cleaning stages, there was no improvement in Mo grade but the tailings were practically pyrite only. The plain cleaning stages did not yield any appreciable up-gradation of Mo content in the float. The loss of about 10% of moly values at this stage is mainly due to slimes present in the rougher float. As high as 10% by weight (stage-wise) of the material in the rougher float was in size finer than 2.8µm. These very-fine size particles disturb the froth structure and were found to prevent the liberated molybdenite values reaching the froth zone of the floatation cell. The slimes in the plain cleaning stage were removed by processing on a 2” hydrocyclone operated at 30 psi pumping pressure. The deslimed coarse stream containing moly and galena was treated on wet shaking gravity tables. The “flotation - gravity” separation route gave a moly concentrate analysing Mo 44.21% with about 37% distribution. Interestingly the Pb content here is 8.7% only. Other contaminants are: Cu 0.33, Fe 4.33 and SiO2 1.35. Another off-grade moly concentrate assaying 7% Mo with 19% distribution was also obtained but the Pb content was very high, about 49%. The concentrate has more than permissible levels of lead, which can be removed only by hydrometallurgy route[13,14,15]. 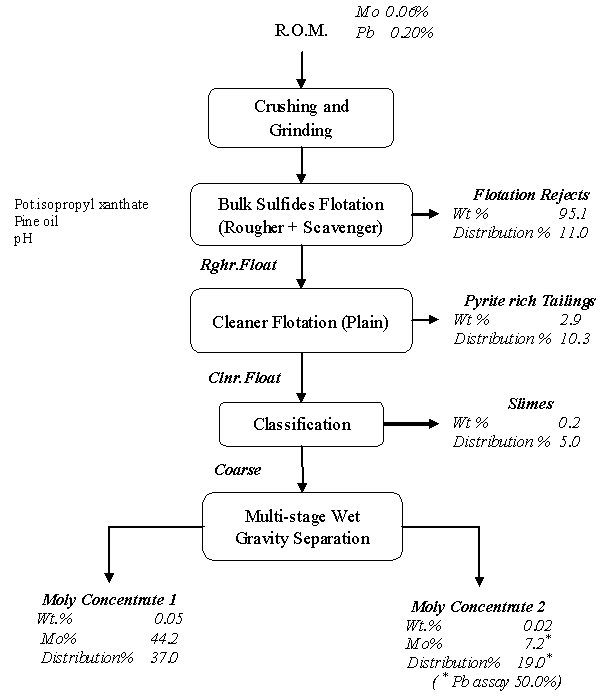 | Figure 6. Recovery of Mo from Harur ore. Material balance of large-scale test |
4. Conclusions
Process flowsheet development studies were carried out on a low-grade primary molybdenite ore assaying 0.06% Mo from Harur of Tamilnadu. The main sulphide minerals besides moly are pyrite and galena. Two process alternatives were investigated an “all flotation” route and a “flotation cum gravity separation” route. Though both the routes gave similar recovery, the “flotation cum gravity” processing route gave a moly rich product with less of galena. About 60% of the molybdenite values can be recovered from this ore at an average grade of about 16% Mo. Any attempt to improve the grade of molybdenum in the float results in loss of recovery. The lead impurities in moly concentrate can be removed only by hydrometallurgy route.
ACKNOWLEDGMENTS
The authors are thankful to Dr.A.K.Suri, Director, Materials Group, Bhabha Atomic Research Centre, for his constant encouragement and interest in the studies. Thanks are also due to M/s.Mineral Exploration Corporation Limited, Nagpur, for providing the sample for studies.
References
[1] | C.K.Gupta, Extractive Metallurgy of Molybdenum, CRC Press, 1992. |
[2] | C.R.F. Azevedo, Selection of fuel cladding material for nuclear fission reactors, Engineering Failure Analysis, 18, 1943–1962, 2011. |
[3] | F. Ditrói, A. Hermanne, F. Tárkányi, S. Takács, A.V. Ignatyuk Investigation of the α-particle induced nuclear reactions on natural molybdenum, Nuclear Instruments and Methods in Physics Research B, 285,125-141, 2012. |
[4] | Indian Mineral Year Book 2009, Indian Bureau of Mines, Nagpur. pp. 58-1 to 58-6, 2011. |
[5] | Monthly summary on non-ferrous minerals and metals, Ministry of Mines, Government of India, March 2012.. |
[6] | Detailed information on molybdenum ores of India, Geological Survey of India, 1994. |
[7] | N.P.H.Padmanabhan, T.Sreenivas and N.Krishna Rao, Processing of Ores of Ti, Zr, Hf, Nb, Ta, Mo, Re and W: International Trends and Indian Scene J.High.Temp.Metals and Materials, 9. 217-247, 1990 |
[8] | M. Peart, D.R. Nagaraj, S.A. Ravishankar and R. Capanema, Optimization of Reagents in Sulfide Flotation, in Cytech Solutions for Hydrometallurgy and Mineral Processing, 15, 22-29,Sept 2010. |
[9] | Liu Guang-yi, Lu Yi-ping, Zhong Hong, Cao Zhan-fang, Xu Zheng-he, A novel approach for preferential flotation recovery of molybdenite from a porphyrycopper–molybdenum ore Minerals Engineering, 2012 (in press). |
[10] | Zohir Nedjar, Djamel Barkat, Mustapha Bouhenguel, Study of sulphide mineral flotation with xanthates: control parameters of flotation. TOJSAT: The Online Journal of Science and Technology -1(2), April 2011. |
[11] | Ferihan G¨Oktepe, Effect of pH on Pulp Potential and Sulphide Mineral Flotation, Turkish J. Eng. Env. Sci. 26, 309- 318, 2002 |
[12] | Jan Drzymalaa, Janusz Kapusniak, Piotr Tomasik Removal of lead minerals from copper industrial flotation concentrates by xanthate flotation in the presence of dextrin. Int. J. Miner. Processing. 70, 147– 155, 2003. |
[13] | A.M. Amer, Hydrometallurgical recovery of molybdenum from Egyptian Qattar molybdenite concentrate, Physicochem. Probl. Miner. Process. 47, 105-112, 2011. |
[14] | Yan Liu, Yifei Zhang, Fangfang Chen, Yi Zhang, The alkaline leaching of molybdenite flotation tailings associated with galena, Hydrometallurgy (in press) 2012. |
[15] | S. Aydoğan, M. Erdemoğlu, G. Uçar, Kinetics of galena dissolution in nitric acid solutions with hydrogen peroxide. Hydrometallurgy 88, 52-57,2007. |